Make The Case: Iron vs. Aluminum Engine Blocks
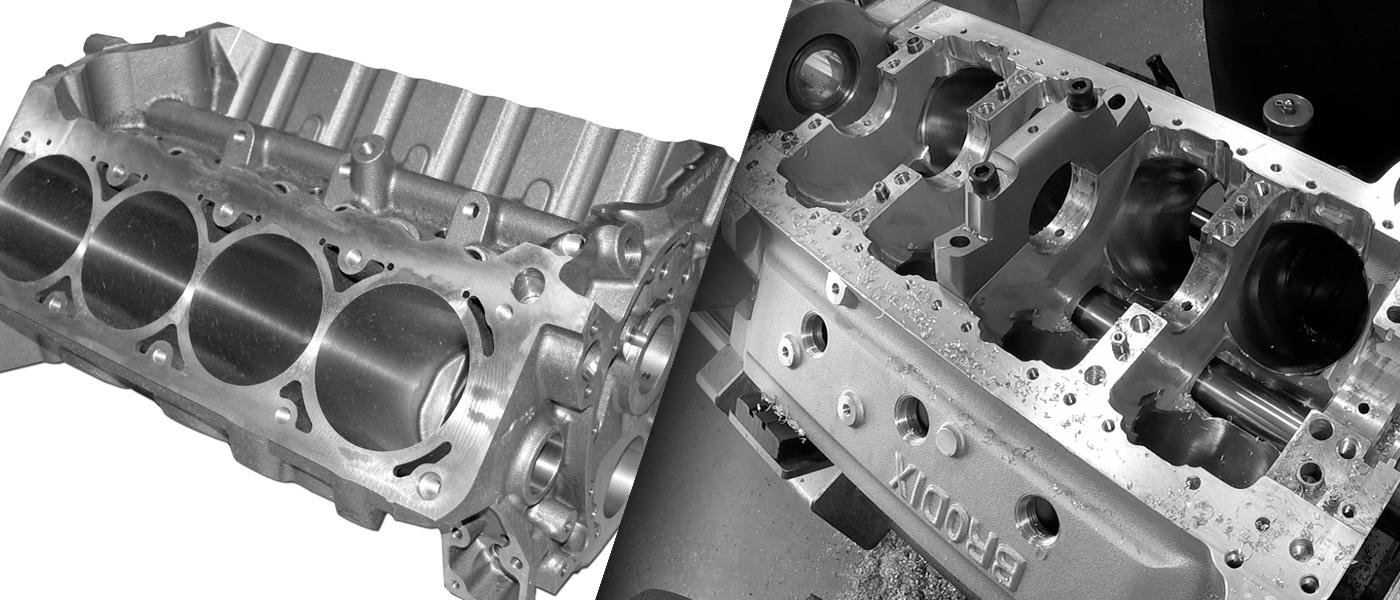
For many racers, choosing which engine block material to invest in often comes down to two factors: cost and strength. But as our two advocates in this month’s column explain, the science behind how these materials behave under the stresses of a motorsports environment—along with steady advances in block design and manufacturing—have introduced other important factors to consider when choosing between cast iron and aluminum.
IRON BLOCK ADVOCATE:
JACK MCINNIS,
WORLD PRODUCTS
–
Cost is a big factor, of course—you’re reducing the cost of the block by about 40% or more by opting for iron over aluminum. And that’s cast aluminum; a billet aluminum block would be an entirely different animal, where we’re talking about multiples of price.
People tend to focus on the weight difference, and obviously that’s a big deal, but it’s important to note that iron is generally going to give you more power because of better ring seal. Because iron is more rigid than aluminum, it won’t deflect and distort as much under high cylinder pressures. So if you were to do a direct comparison with all other variables being the same, you’re typically going to see a little more horsepower from an iron block engine than you would with an equivalent aluminum block. Of course, that’s more obvious in high-stress applications, but isn’t that what motorsports is all about?
Modern aluminum blocks are pretty strong, but a properly built iron block is still ultimately going to be stronger, and that strength offers some benefits that might be less obvious. For instance, if you have a catastrophic engine failure, an iron block is usually going to hold up better to it. We’ve seen instances where people have really seriously blown some stuff up, and while it leaves a few scars on the block, the block is still perfectly good to use without having to get into welding, re-machining, and that sort of thing.
And the rigidity and higher tensile strength of iron makes it inherently better at handling large amounts of power and large amounts of boost than aluminum is. There are plenty of people who’re making lots of power with aluminum engines, but when that threshold is lower, the tune becomes even more critical. Something that might be a bit unhappy in an iron block engine could be devastating in an aluminum one. The margin of error is smaller.
When you start really throwing a lot of boost or a lot of nitrous at it, the whole block can actually twist and move, and that can subsequently lead to other components failing because they don’t have the support they need at that instant. That’s one scenario where an iron block is generally going to allow components to live longer and provide better reliability.
While there are classes across a number of different racing disciplines where iron blocks are required by the rule set, there are also situations where it’s simply a better option for the given application. In classes where the cars are heavy anyway, or marine applications where wake is not a big consideration, what you lose in weight advantage can be compensated for in added power.
But one thing we’ve noticed is that a lot of racers make the mistake of ignoring the benefits of what aftermarket iron engine blocks offer. We see a lot of dirt track guys who will go out of their way to find old factory blocks because they’re a bit lighter, and then they blow up two or three of them over the course of a season, whereas an aftermarket iron block would probably have lasted them several seasons.
They might go that route because they’re saving 40 pounds or something like that, but that additional weight is there for a reason—it’s often additional material that’s strategically placed in the block to strengthen weak points in the block design.
With the old factory small blocks everybody was going after the four-bolt mains, but in truth, the two-bolt blocks are stronger. You’re securing the cap a little bit better with a four-bolt design, but you’re weakening the web in the process. The splayed bolts and thicker pan rails found in modern aftermarket blocks resolve that issue—and then some. And some of that additional weight can also be attributed to the use of higher grades of iron that are denser, and inherently stronger, than the factory iron material is.
ALUMINUM BLOCK ADVOCATE:
MARK FRETZ,
BRODIX
–
Perhaps the most important advantage of aluminum engine blocks over iron blocks is the weight—an aluminum block is going to weigh about half as much as its iron counterpart. That takes weight off of the nose of the car and gives you more freedom to move weight around in the car for better weight distribution. So while an aluminum block doesn’t provide a performance benefit in terms of horsepower, it lightens the overall engine package and provides more ways to optimize the car while meeting the minimum weight for the class you’re running in.
While there are some class rule sets that do not allow aluminum blocks, most provide the option, and the majority of the time the decision is driven by a team’s budget more than anything else. If you can afford an aluminum block and your class allows it, you’re going to run one.
There’s also the repairability factor. When you’ve reached the maximum bore at the end of the life cycle of the engine, you can replace the sleeves and start over with an aluminum block. With an iron block you can sleeve one or two cylinders, but if you need to sleeve the entire block, it’s usually better to simply replace it. The sleeving process is more labor intensive with an iron block, and between parts and labor, the cost savings usually isn’t worth the trouble: Re-sleeving an aluminum block engine might cost you $1,000 versus a $6,500 block replacement cost, but with an iron block, it could cost you $1,400 to $1,600 to sleeve a block that can be replaced for $2,000 to $2,500.
Customizability is also a big advantage you’ll find with aluminum engine blocks. Most iron blocks are manufactured on a large production scale, so you usually don’t have many options as far as configuration goes. But for us, the versatility of having an in-house foundry for our aluminum blocks allows us to make changes to meet a customer’s needs. When we take an order for an aluminum block, there’s about 15 options we provide for the customer—you can choose things like camshaft size, lifter size, and deck height—and that allows engine builders to really tailor an engine to the rule set of a class.
And although iron blocks can handle more power, well-built modern aluminum blocks can be pretty stout as well. So much of it comes down to the tune; some guys will break blocks at 1,800 horsepower, while others make 3,500 horsepower and have 700 passes on a block. Over the last 10 years or so, we’ve taken a lot of feedback from our customers and have improved our aluminum blocks to the point at which their power handling is nearly equal to an iron block.
There’s also a common misconception that aluminum blocks lose a significant amount of horsepower versus an iron block engine because the material isn’t as rigid and the engine moves around. But ring packages, ring materials, and the technology used to finish the cylinders has come a long way over the years. We have engine builders that say the difference they’re seeing between iron blocks and aluminum blocks is as little as 10 horsepower in these kinds of applications.