Stop Doing That…Do This Instead: Prepping Race Cylinder Heads
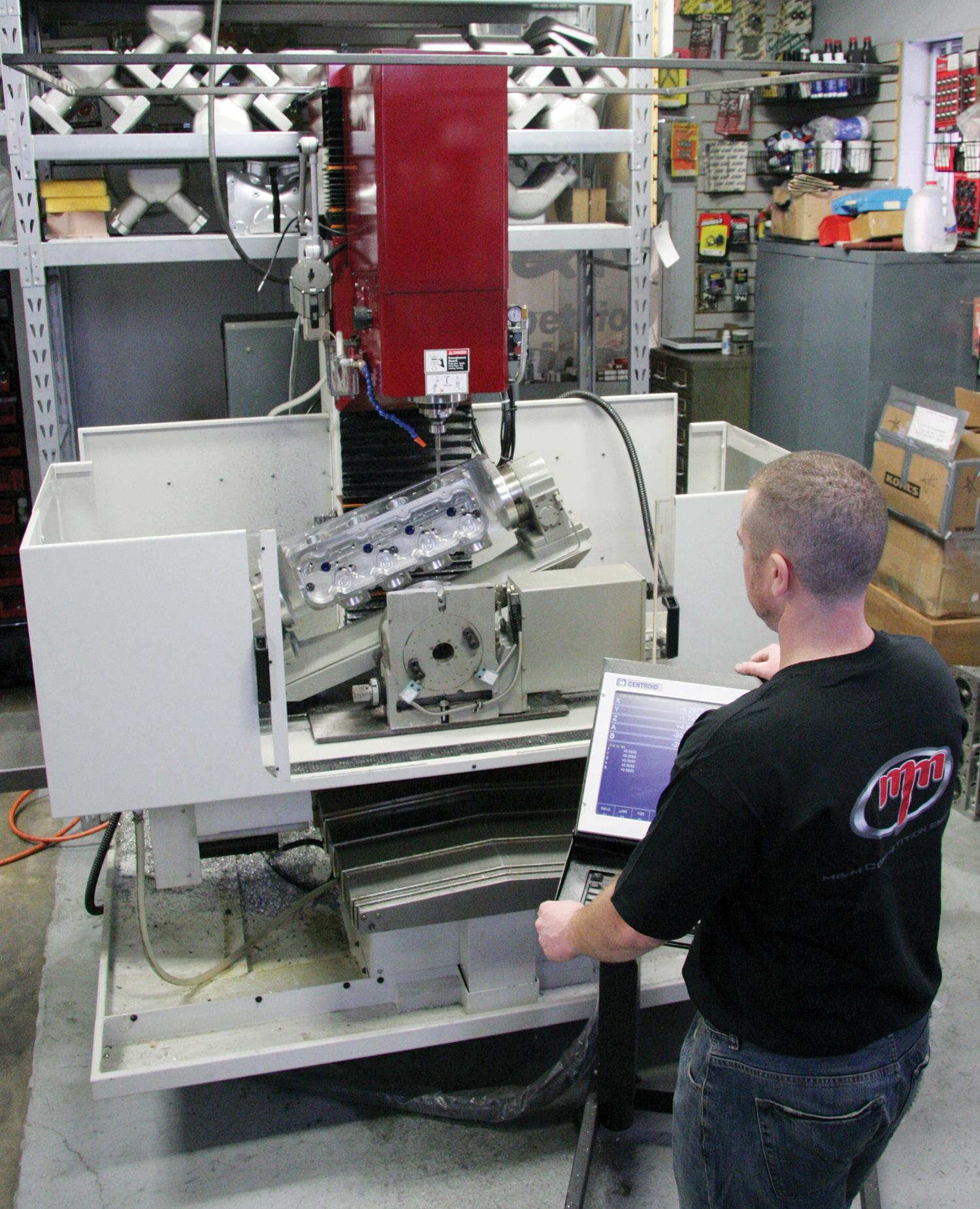
Successful cylinder head port development depends on several critical metrics, according to our source from M&M Competition Engines, whose shop is pictured at left. Valve-to-bowl area percentages, finish texture of the port, and cross-section were all cited as factors directly tied to head performance.
Several misconceptions have infiltrated the performance spectrum, so we called on a pair of industry veterans to separate the fact from fiction.
Engine builders today can take advantage of a variety of off-the-shelf cylinder heads that are specifically designed for the most popular engine platforms.
“That works for the majority of the market,” said Scott Patton of M&M Competition Engines, Franklin, Indiana. But the sheer number of head choices “can be overwhelming for some engine builders,” he noted. Plus, those off-the-shelf heads may not work for “the small percentage of racers who truly need ‘just a little bit more,’” he pointed out. “Engine builders whose clientele needs the cutting-edge advantage that custom cylinder heads provide start to see themselves heading down the proverbial rabbit hole.”
From Patton’s perspective, most engine builders “are not altering cylinder head port development as they once were. They are utilizing existing CNC-ported heads to complete their builds. It seems that the industry is transitioning with the times and segregating engine builders from cylinder head development companies. The two go hand in hand, though, and trying to be successful at one is impossible without at least a small understanding of the other. We try to bring the two worlds back together.”
Cylinder head education is also an important part of the service offered at 1 Way Technologies of Washington, Indiana, said Chris Grace. “Our customers run the gamut from real experienced guys to guys who are just starting out,” Grace explained. “Either way, we try to inform the people we deal with, because we want them to be armed with all the knowledge we can give them for their application.”
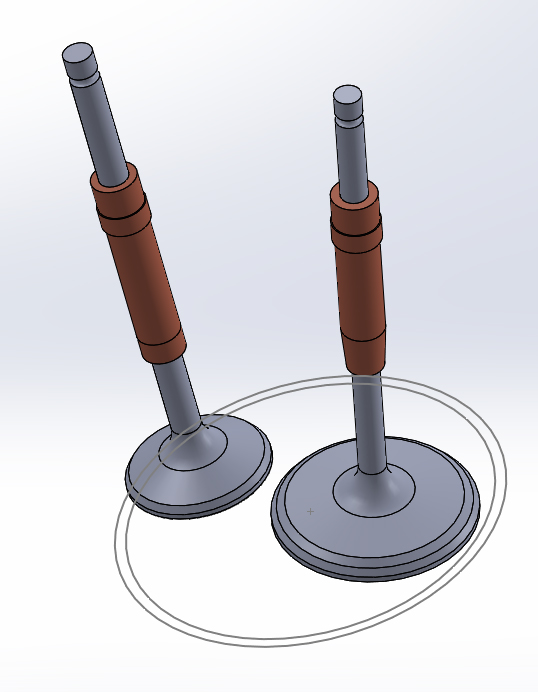
Among the recurring issues these companies have observed when it comes to cylinder heads:
Bigger is not always better. “The common thought process is that to make more power requires bigger valves,” said Patton. “But at times, a larger valve could create unforeseen problems that will decrease the engine’s power potential. A larger valve will come closer to the cylinder wall which, in many instances, will decrease airflow because it has a wall to contend with.”
Another issue with big valves, particularly in smaller-displacement engines, is the large valve pocket needed for piston clearance, Patton said. “Some engines—485-inch truck-pull engines are especially susceptible to this—with large cams and bigger head diameters on the valves, require a valve pocket in the piston that makes it next-to-impossible to get any sort of viable compression out of the engine. Just because a cylinder head flows big air doesn’t mean that it will translate into big power on the dyno or quicker ETs at the track.”
Beware the “freshen-up.” “Guys can hurt cylinder heads by doing a freshen-up where the valve job cutter spec is different than what we put on it brand new,” said Grace. “What we’ll see is that the combustion chambers have a big radius in them right above the valve job.” Whoever did the freshening “just used the basic cutter to go in and try to put a valve job on a seat ring. What that’s actually doing is hurting the design aspect and the flow characteristics of the port. We have spec sheets in our catalog of the cylinder heads that we offer, and they have a flow curve that we like to adhere to. That’s why they were designed that way.”
1 Way Technologies fixes the issue by putting the head back in the CNC machine “and re-running the combustion chamber program over the cylinder head,” Grace said. “We’ll do what we call dropping the chamber. We drop the chamber into the head, and it will get it back closer to the spec it was brand new.”
The techs then “analyze the valve job, where the valve actually sits on the valve seat, and the distance from the valve seat to the short turn, because we don’t want to see that distance change drastically,” said Grace. “If it does change drastically, then we will go in and apply a fix to the cylinder head—blend the seats differently, blend the short turns, blend the combustion chamber. Then we’ll put it back on a flowbench and compare that worked-over cylinder head to the brand-new aftermarket piece that we’d like to have sold in the beginning.”
Looks versus performance. Some engine builders “are more concerned with how a head visually looks than how it actually performs,” said Patton. “By that I’m referring to the shape and texture of a port. It is common for engine builders to take an out-of-the box CNC cylinder head and want to, for example, polish the intake to a mirror finish, or open up the bowl area to improve the airflow and power potential of a cylinder head. Only they’ll do the exact opposite. Cylinder head port development success depends upon critical metrics that many don’t quite understand. Valve-to-bowl area percentages, finish texture of the port, and cross-section are just a few areas that either make a head perform or not.”
Port volume versus cross-section. The “cross-section” Patton referred to is the way M&M prefers to measure and compare cylinder head size, as opposed to intake-port volume.
“When you compare different cylinder heads by the minimum cross-section of the port, it provides the end user with information that is more relative to what they are inquiring about,” he explained. “When utilizing volume as your benchmark, it does not take into consideration the port length. So ultimately you can have two heads with the same port volume but wildly different cross-sections. Engine builders using volume to make their cylinder head choices might end up with the incorrect cylinder head to start their project.”
SOURCES
–
1 Way Technologies
1way-tech.com
M&M Competition Engines
mmcompetitionengines.com