Stop Doing That…Do This Instead: Track Prep and Maintenance
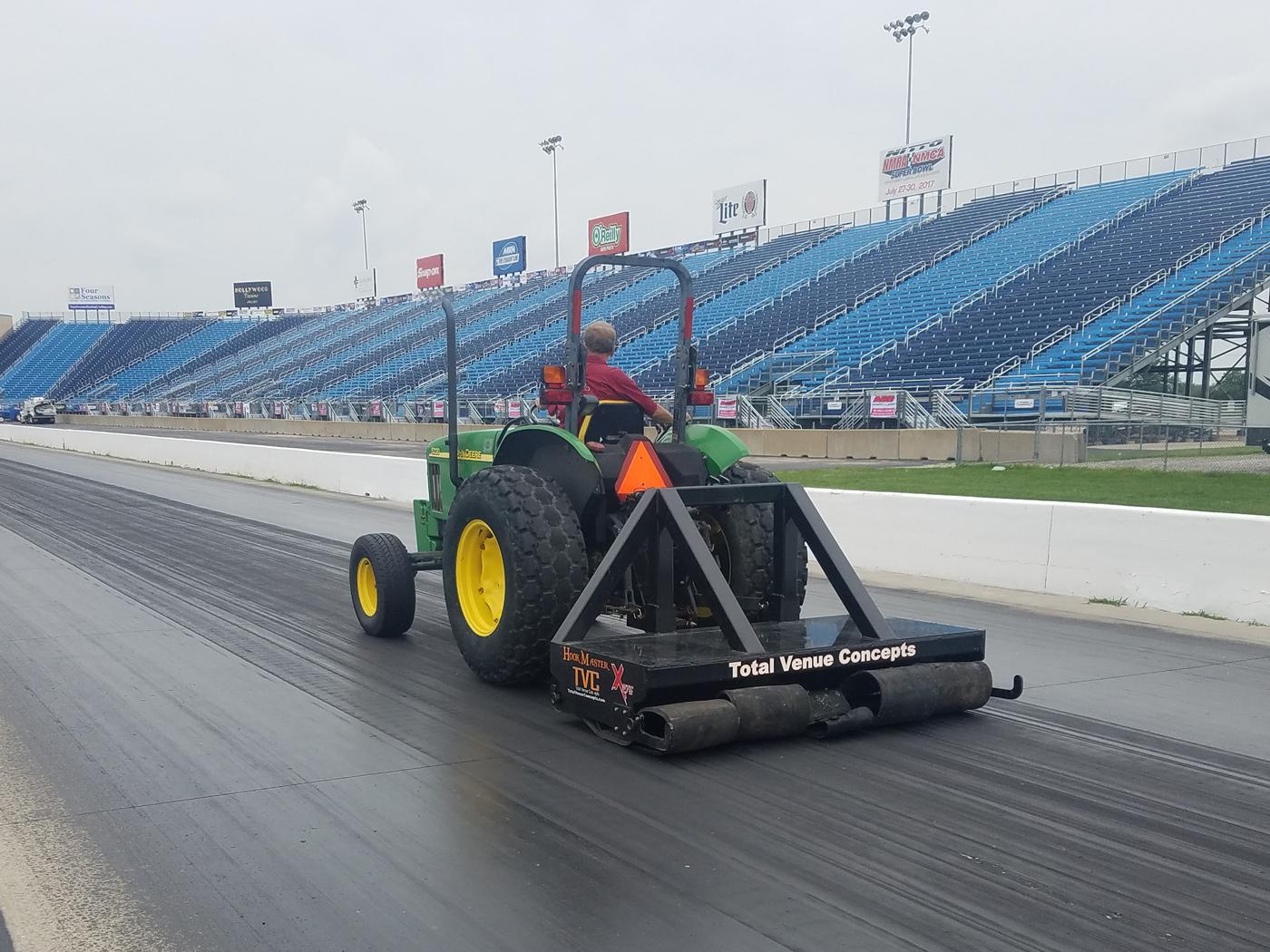
Proper track preparation often requires costly labor, but this static drag from Total Venue Concepts, which can easily lay rubber for weekly bracket events, makes the job easier and less expensive.
Managing your track’s “primary revenue generator” involves carefully choosing which equipment can effectively accomplish the task at hand.
“A good surface is the primary revenue generator of any motorsports facility,” said Kurt Johnson of Total Venue Concepts, Petersburg, Indiana. “Concessions, apparel, parking—that all relies on the piece of concrete and asphalt at the center of the facility that the race cars go down.” Keeping that in mind can give a track owner or operator some needed perspective on what can be “not inexpensive” track maintenance costs, Johnson said.
But, he noted, not every track requires the same level of maintenance.
“My company is usually called in by a track that wants to set records,” he explained. “If you want to set records, you should own a [tire drag] rotator, which my company sells for $35,000. But if you’re a week-in, week-out bracket track, a rotator is a waste of money. For weekly events, you can have just as good of a surface with a $5,000 static drag. Having the right tools for the right job is important when you’re watching cash flow. Instead of buying every cool piece in my inventory, have the key components you need to start with, then use the rest of your capital in other places.”
To Johnson, those key components start with a quality tractor “with a warranty, which can save thousands of dollars down the road. A tractor can be expensive to fix, and a warranty is money well spent.” Next is a “good quality static drag to put rubber onto the race track,” followed by “a good torch and rubber scraping device. Scraping the old rubber off the track is just as important as putting new rubber on.”
Scraping manually eliminates the up-front cost of buying a scraping machine. But “scraping is a labor-intensive process,” Johnson pointed out. “It’s hot, it’s physical, it sucks. Nobody likes to do it.” Looking to “build a better mousetrap,” Johnson put together TVC’s Zero Turn Track Scraper that can “scrape a quarter-mile race track with two guys in two days, and with almost no effort from either of the two people. It will still use about the same amount of propane, and you have some initial investment, but you don’t have the employee labor costs and employee toil.”
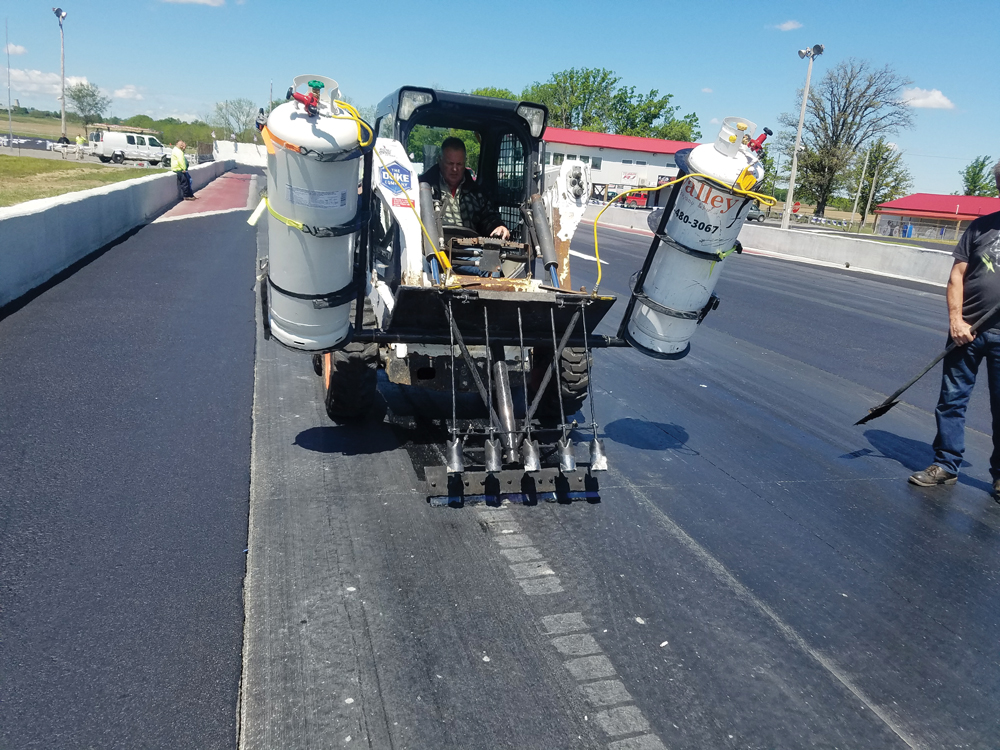
Johnson recommends a regular scraping interval: “The first 60 feet, from the burnout box to the 60-foot mark, needs to be scraped every week. After the first 60 feet, scrape 100 feet of the race track. Next week, after doing the first 60 feet again, start where you left down-track and do another 100 feet. In a matter of 13 weeks [for a quarter-mile], you’ve scraped the entire track. Then start the process over again.”
The final key component is a sprayer to apply traction compound. Whether it’s professionally built or a homemade rig, Johnson believes in “maximum effectiveness with the least amount of effort.” To that end, he recommends sprayers “that are really wide, so all you have to do is one or one-and-a-half laps” to cover the track. “Time is money. The less time you have employees working, the more time you can be racing.”
Plus, if the sprayer is too narrow, requiring more laps to cover the full track, “by the time you’re done with the outside the inside’s not near as good.”
In fact, Johnson’s goal is “to have consistency throughout the day, a surface that’s just as good from the moment we put the first car on it to when the last car leaves that night.” He can also deliver surface consistency from track to track, a valuable asset for racing series. In March he explained, “We just did the NMCA race in Bradenton, and I made that track exactly the same as I will in Atlanta, which is where we’re going next in the series. I want tuners to have the same surface at the tracks, so I repeat the same process for preparing the track.”
That process involves “a minimum of three hours before a race working on the track,” Johnson said, “and many times I’ll spend a half-day before, making sure the rubber is applied. Not including scraping, just dragging it and rotating it, using the static drag and the rotator together, and spraying it.”
Johnson said he’s seen “a lot of tracks that drag the track for 15 minutes, spray it and go race. If you want a good quality, consistent surface, that’s not enough. You’re going to get sporadic and inconsistent results when you do that.”
Proper track prep “takes quite a bit of labor, which is money out of the track operator’s pocket,” Johnson noted. “But if you look at any of the top-10 tracks in the country, they have a team that wants to see the track succeed. A track’s biggest asset is a good employee team that works together with a common drive to have as good and consistent a track surface as they can. That becomes their reputation, and the reputation of the track.”
SOURCES
–
Total Venue Concepts
totalvenueconcepts.com