PRI Tech: Coatings
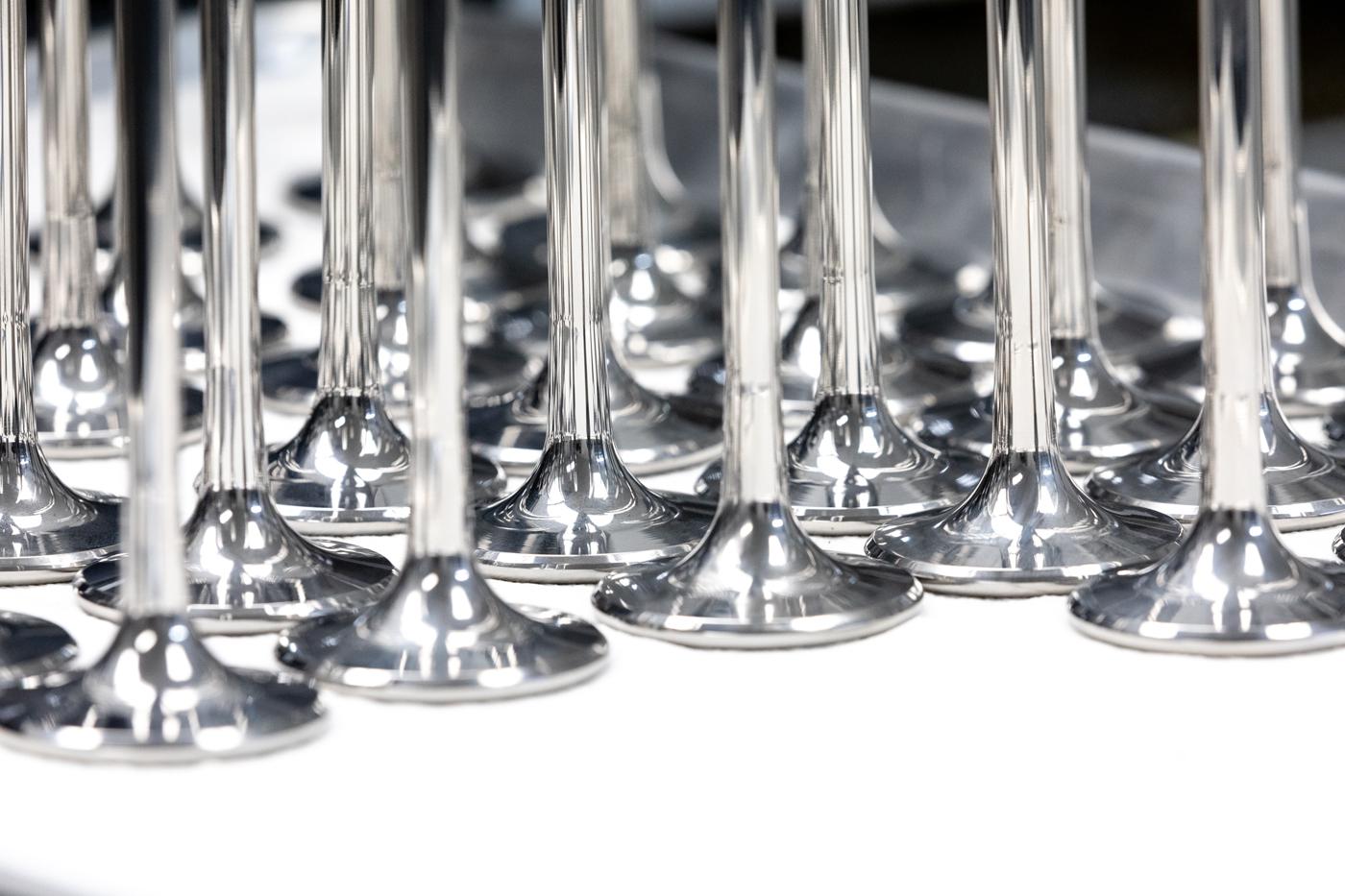
When should coatings be used and on which parts? This guide from Calico Coatings explains why coatings are considered “the hidden heroes of racing” and how they can enhance your racing program.
In an industry where performance is everything, coatings have stepped in to provide a performance advantage. Professionals in the racing industry use coatings on their engine components to provide various benefits, such as friction reduction, corrosion prevention, enhanced material compatibility, and improved overall engine performance. Coatings are used extensively for their ability to provide higher engine efficiency, durability, and reliability, making them the hidden heroes of the racing industry.
A wide range of components can benefit from performance coatings, everything from bearings to wrist pins. These powerful coatings are designed to modify the behavior of the substrate material, preventing various types of wear, including abrasive, adhesive, fretting, and surface fatigue. By mitigating these wear properties, the coatings improve the lifespan of engine components.
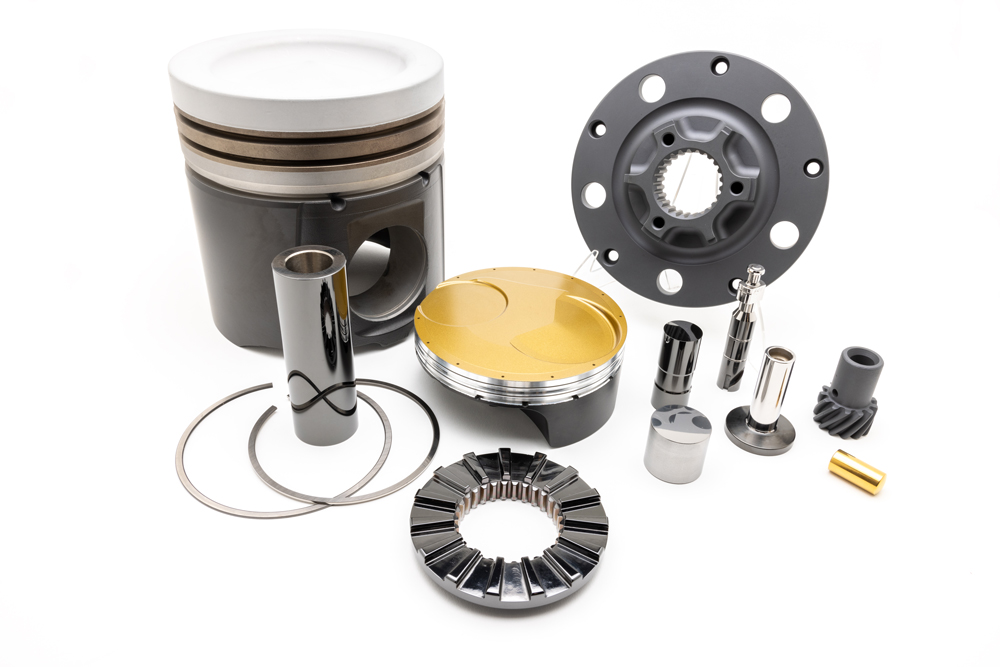
In addition to their performance benefits, coatings are also used in the racing industry to address environmental concerns. While the racing industry focuses on enhanced performance through lower friction, a secondary benefit is lower fuel consumption and reduced emissions due to increased lubricity provided by coatings—another valuable unseen benefit.
Following are the top-five reasons the racing industry chooses performance coatings:
1. Reduced friction. Coatings can be applied to various engine components to reduce friction and increase efficiency, improving engine performance and longevity.
2. Heat resistance. High-performance coatings help dissipate heat more effectively, keeping critical engine components from overheating during intense racing conditions.
3. Corrosion protection. In the demanding automotive racing environment, vehicles are often exposed to harsh elements such as moisture, salt, and chemicals. Coatings act as a tough protective barrier, shielding components from corrosion and significantly extending their lifespan.
4. Wear resistance. High speeds and intense forces make components prone to wear. Coatings with high wear-resistance properties can help prolong the life of these components, reducing the frequency of replacements and maintenance downtime.
5. Customization. From adjusting friction coefficients to modifying thermal conductivity, coatings can be tailored to specific racing applications, allowing teams to fine-tune their vehicles’ performance characteristics.
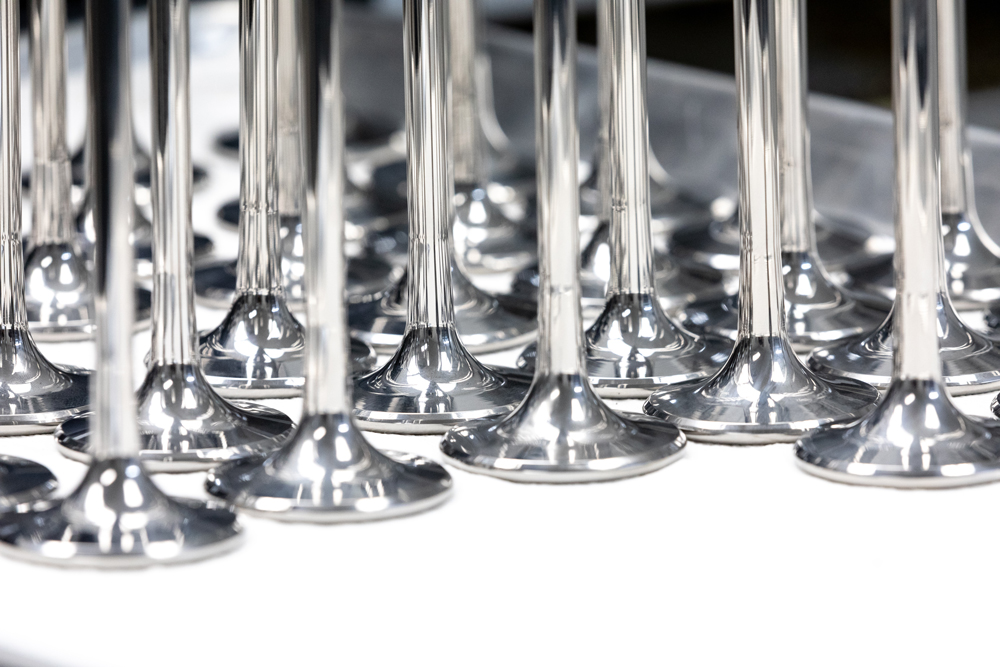
Which Coatings and Why?
While there is an arsenal of performance coatings from which to choose, Diamond-like carbon (DLC) and Physical Vapor Deposition (PVD) are top contenders for providing race teams with a performance advantage. Various factors, such as the application methods, substrate material, surface preparation, and performance properties, determine the effectiveness of DLC and PVD coatings.
Diamond-like carbon is a family of carbon-based coatings that have extreme hardness due to the diamond crystal (tetragonal) structure and is soft and lubricious due to the graphite crystal (hexagonal) structure. A technological advancement, DLC is a combination of PVD and Plasma Enhanced Chemical Vapor Deposition (PECVD) coatings. Combining these two structures reduces the coefficient of friction by 200%–500% compared to traditional tribological PVD coatings, making them an excellent choice for components that operate at high pressures.
Physical Vapor Deposition coatings offer several benefits across various applications due to their unique properties and characteristics, including hardness and wear resistance, low coefficient of friction, and temperature resistance. They also have a positive presence in a wide range of industrial, non-industrial, and cosmetic applications due to their increased hardness, low coefficient of friction, extreme temperature resistance, and a multitude of color ranges.
Depending on the specific issue the engine builder is trying to solve, there are various other coating solutions to choose from.
Dry-film lubricant coatings help reduce friction and abrasive wear. They provide intermittent dry lubrication, are not affected by dust or dirt, and are specifically engineered to withstand the extreme conditions of today’s high-performance engines. With increased embeddability, strength, and durability, dry-film lubricant coatings give professional engine builders a higher confidence level.
Titanium Nitride (TiN), the staple of thin film coatings, solves tribological problems with machine components that can be coated at temperatures of 425° C–450° C. TiN is normally applied to steels, hardened steels, and stainless steel materials where high wear resistance and lubricity are needed.
Chromium Nitride (CrN) provides lubricity, superior wear, and corrosion resistance, and a very low residual stress, which provides for the best adhesion and ductility of any PVD coating. High hardness, low coefficient of friction, and the low residual stress of CrN combine to resist abrasive, metal-on-metal wear, and galling.
Super Finishing is a precision surface prep process commonly applied to critical engine and drivetrain components to reduce friction, increase durability, improve fatigue resistance, and enhance overall performance. Super Finishing removes microscopic peaks, component stresses, and stress risers, leaving an isotropic or uniform surface finish of less than 2–3 micro-inch. Super Finishing prior to coatings can lead to improved power transfer, reduced energy consumption, and increased reliability, all of which are crucial in high-performance racing applications.
Coatings are the hidden heroes of the automotive racing industry, playing a vital role in enhancing performance, durability, and efficiency, making them indispensable for competitive teams seeking an edge on the track.
Calico Coatings has been a premier coatings provider to the automotive racing industry for more than 25 years. It has developed some of the industry’s most technologically advanced coatings—with the ability to withstand the extreme conditions of high speed and engine wear. Find out more at calicocoatings.com.