Ask the Experts: Parts Cleaning Media
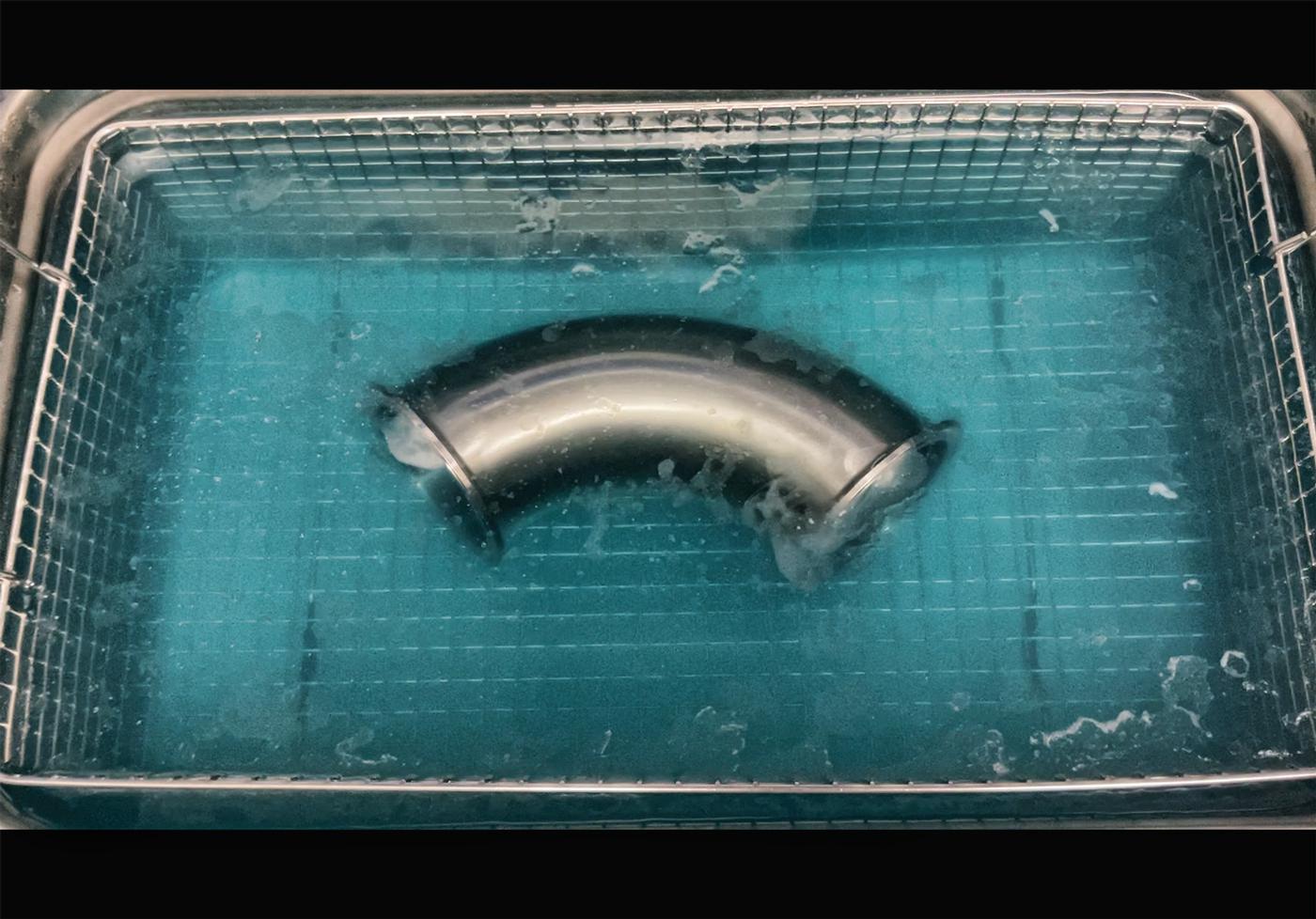
Ultrasonic cleaning is often thought of as a finishing step, said our source from UltraSonic LLC, as it won’t remove things like paint, rust, or corrosion. But its aqueous nature allows it to get into blind holes, cracks, crevices, and other places where other cleaning methods can’t reach.
When scrubbing down components, should blast media or aqueous solutions be used? Or, is a combination of both the preferred method?
Parts cleaners can make components with decades of grime and corrosion look brand new in just a matter of minutes, but they’re not one-size-fits-all solutions. Getting the most out of blast media and aqueous solutions means using the right tool for the job.
Blast Media
Although there are situations where blast media is a better option than the ultrasonic cleaning method, or vice versa, there are also situations where these cleaning methods can complement one another. As Ron Storer of ABS Products in Brea, California, noted, selecting the appropriate methods and media for a given task ultimately comes down to the job at hand and the parts involved.
“For instance, when I’m cleaning parts for race engines—trying to remove carbon buildup, gasket material, grease, and things like that—I’ll use soda. Soda is a one-time-use media, it’s biodegradable, and it’s a soft enough material that it will not change the substrate that you’re blasting.”
Storer pointed out that because soda doesn’t change the surface of the material it’s applied to, it’s mainly used to clean parts rather than change their surfaces. If you’re looking to take a part like an aluminum intake manifold back to a factory-fresh appearance, that’s a different situation with a different process. “In that case I might use dry glass beads because they would make that part look brand new.”
While glass bead media provides a deeper, more intensive clean, he said that it requires more care during the cleaning process, and additional steps may be needed after this process in order to prepare the part for use. “With dry glass beads you need to make sure it doesn’t wedge itself in cracks or crevices of the part. The last thing you want to do is have that material come out later on when the part is installed, and you usually can’t get it out by just blowing it off or rinsing it.”
These beads are ostensibly microscopic glass marbles. When the beads hit the part, they shatter into smaller pieces with sharp edges, and these shards provide a deep clean that can also polish the surface of the component. That means that dry glass beads can effectively take care of two steps in the parts cleaning process at once, but the media also necessitates an additional preparation step in order to get the part ready for use.
“In a situation where I’m using dry glass beads, I’d run the part through that process first and then I’d put it into an ultrasonic cleaner,” Storer said. “Ultrasonic cleaning will loosen up that material through vibrations and get it out of those nooks and crannies.”
He also offers hydroslurry, or wet blasting, as an option that can sometimes take care of both steps. “You might not need to use an ultrasonic process in that case because that’s a wet glass bead media, and the water becomes sort of a cushion, so the beads don’t impregnate themselves into the part. There’s less frictional heat because of the water, and it does yield a smoother finish when the process is completed. But it also takes about five times as long to clean something in comparison to the dry glass bead process.”
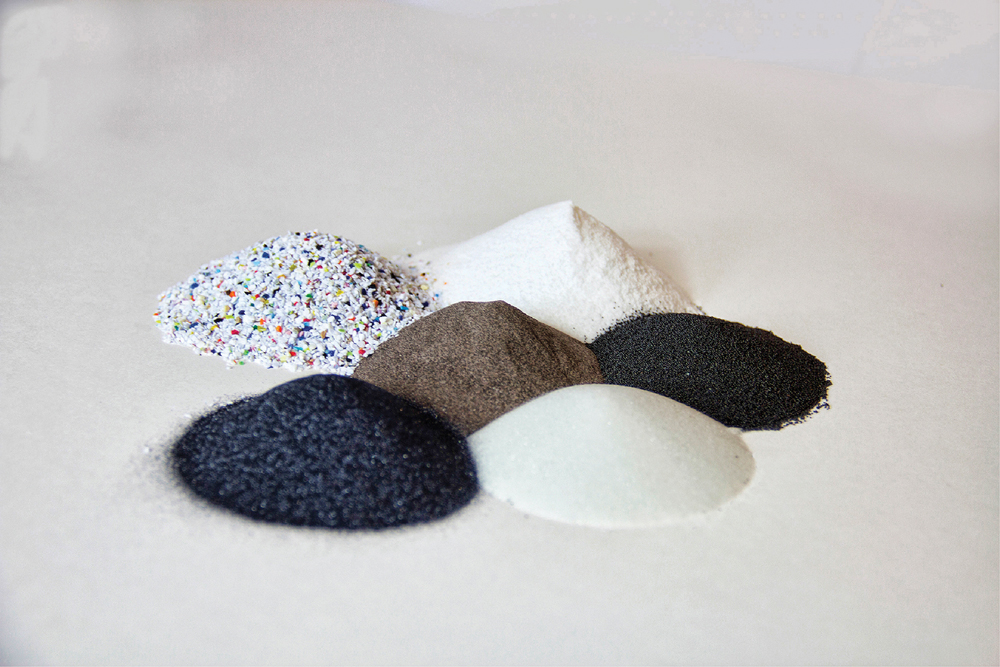
ABS Products also offers other blast materials like aluminum oxide, ceramic beads, and plastic, and each has a specialized use. “Aluminum oxide is great for cleaning out rust and corrosion, but you have to be careful with it because it can also remove material,” Storer explained. “A lot of companies we work with prefer ceramic beads for cleaning components because those beads don’t break down as fast, so the media can be reclaimed and used again. Meanwhile, plastic is great for stripping paint and powder coating, and we use steel shot for peening.”
With the variances in both materials and machines, he recommends that those who are new to these cleaning methods consult the machine manufacturers for their recommendations in order to achieve the results they’re looking for. “We build the machines around our customers’ applications and the media they need to use. And like anything, there’s a certain level of finesse involved in using parts cleaners. You run the risk of ruining a part if you use the wrong abrasive for the wrong amount of time. It pays to get some insight about how to use them properly for a specific set of circumstances.”
Aqueous Solutions
While ultrasonic cleaners can do things that blast media cleaning methods cannot, Jason Shaw of UltraSonic LLC in Amelia, Ohio, told us that it’s generally considered a finishing step in the parts cleaning process.
“Ultrasonic cleaning with our detergents is not going to remove things like paint, rust, and corrosion. In those situations, you’re going to need a solvent or media blaster. If you have very high concentrations of carbon buildup on exhaust ports of a cylinder head, for instance, ultrasonic cleaning can help get that carbon out, but you’d often start with media blast. The advantage of ultrasonic cleaning is that it gets where you can’t touch, see, or feel. It’ll get down into blind holes, cracks, and crevices—places where typical cleaning methods aren’t going to be able to get to. So if you’ve got a block coming out of the junkyard that’s got a bunch of paint, rust, and other nasty stuff on it, you might run it through a jet wash, then media blast, and then put it through the ultrasonic cleaner to remove that media.”
Since ultrasonic cleaning is often considered a finishing step, it’s also commonly used after machining processes. “We have customers who will use the ultrasonic machines on engines as a final clean before assembly,” Shaw said. “It will remove things like the gray dust inside a cylinder wall. It’s a precision clean that will remove those fine particulates that you’re not going to go after with a media blast.”
Ultrasonic cleaning machines put out a wave that creates a microscopic bubble. Wherever that fluid touches, those cavitation bubbles will impact, implode, and pull the dirt off of that surface. One of the key advantages of ultrasonic cleaning is that detergents like those offered by UltraSonic LLC don’t involve harsh chemicals or solvents, but Shaw noted that the appropriate cleaning agent must be used for the material being worked on.
“It’s important to use the right cleaning agents with motorsports components,” he said. “For instance, with certain billet parts, highly polished components, and especially non-ferrous metals, if you use too aggressive of a detergent, it can discolor that metal and etch it. It doesn’t necessarily hurt it, but it doesn’t make it look good. So you need to be aware of that, and that’s why we provide a chart that outlines what detergent you should use with what materials, how much time you should use it for, and at what temperature. It’s a great reference and starting point for those who’re new to the technology.”
SOURCES
ABS Products
abs-products.com
UltraSonic LLC
ultrasonicllc.com