Ask the Experts: Fuel Pump Performance
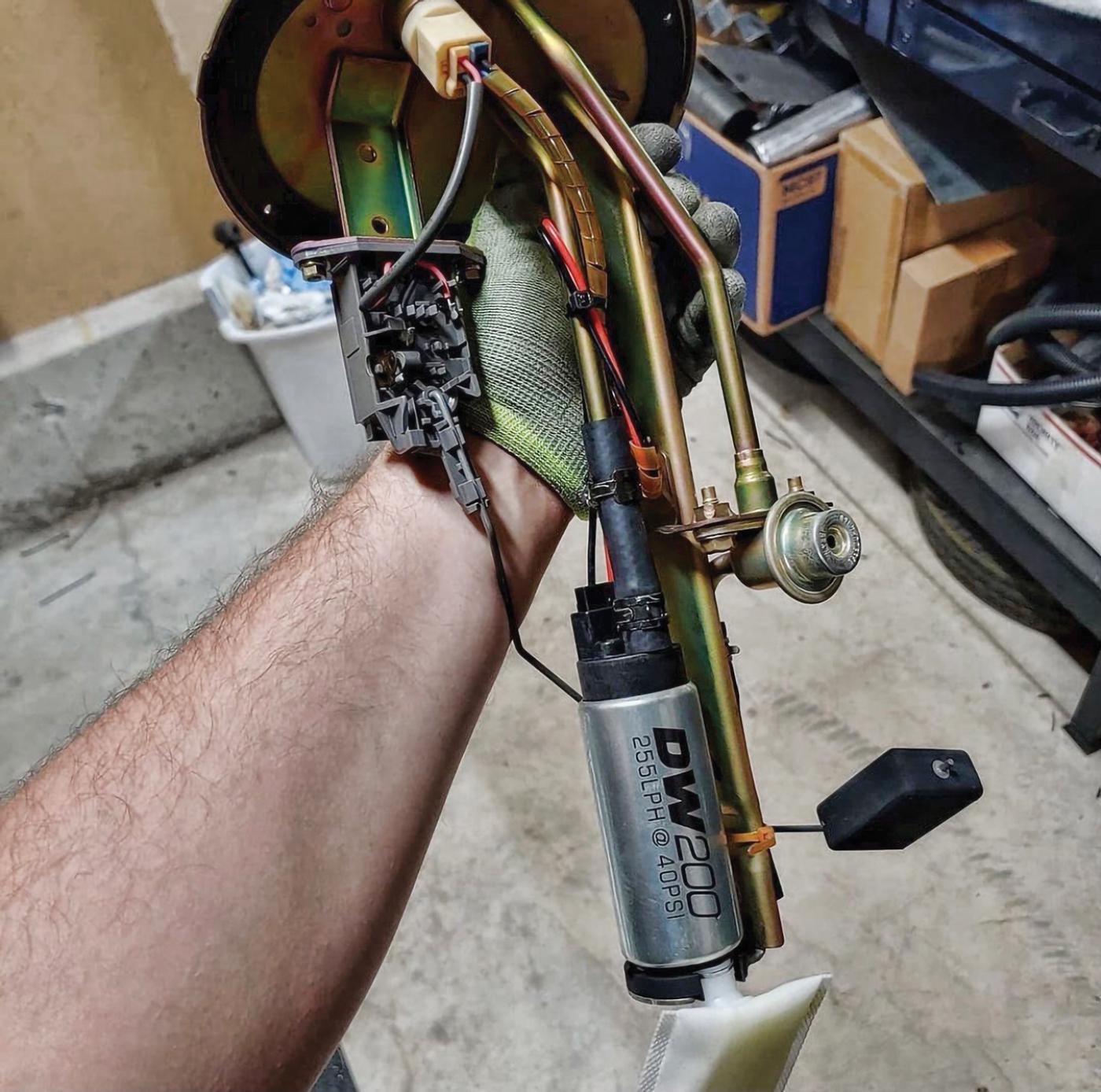
Voltage drop can be a problem if factory wiring is used in the installation of an aftermarket fuel pump, said Brandon McDaniel of DeatschWerks. With OE wiring, the pump could be “down on flow because the pump is not getting the voltage it needs to provide its full capability.”
Improper installation and setup can rob performance potential and even lead to catastrophic failures. While it’s easy to assume that higher numbers are better when it comes to flow rates and system pressure, there are situations where the opposite can be true, so we’re separating fact from fiction.
A fuel pump might not have the sex appeal of a cylinder head or a turbocharger, but it plays a pivotal role in an engine’s performance and durability. That’s especially true in motorsports, where fractions of a second often determine the finishing order and reliability can be the difference between a podium and a DNF. Inefficiencies in any system tend to be amplified out on track, and when it comes to fuel pumps, the consequences can be severe.
“It can go as far as taking out an engine,” said Sam Chaysavang of AEM Performance Electronics, Hawthorne, California. “These problems can be really frustrating if you’ve spent all this time, energy, and money getting the car ready only to end up fighting performance issues and rushing to fix failures once you get to the track.”
To avoid those potential headaches and extract all of the capability from the fuel system, the pump needs to be dialed-in for the application. This is a situation where overkill can actually be counterproductive.
Work Smarter, Not Harder
“One common mistake we see with external fuel pumps is people installing the pump too high relative to where the pickup is,” Chaysavang explained. “These pumps are typically designed to be gravity fed; to push the fuel rather than pull it. If the pump has to work harder to lift fuel to feed itself, it’s not going to be able to deliver as much on the output side. That can also lead to fuel cavitation, which can lead to pump failure. As the pressure drops, the vaporization point drops as well, so it’s critical to maintain good pressure.”
Brandon McDaniel of DeatschWerks in Oklahoma City, Oklahoma, pointed out that problems also often arise when builders purchase a pump without planning ahead.
“We generally focus on application-specific install kits, but sometimes people will just go buy a pump off eBay or something like that and try to figure out how they’re going to install it once it arrives. If that pump is a different design than what they were using previously, they might try to make room for it by deleting components that they assume are redundant or unnecessary, but are actually very crucial to the fuel system’s operation. So they might remove a factory filter to make some space, but there are instances where the pressure regulation is attached to that filter. So you have this pump in there now, and suddenly you have 80 or 90 psi instead of the 58 psi you’re supposed to have.”
DeatschWerks’ Dakota Bowman said that incorrect pressure has a tendency to throw the engine tune off. “And you’re going to be dumping the majority of the flow back into the tank because now you’re relying on the pump to regulate the pressure. That additional pressure is also creating more heat, so the end result is actually less flow.”
Bigger Doesn’t Necessarily Mean Better
Bowman also told us that people have a tendency to buy fuel pumps for the setup that they want rather than the one they have, and that leads to mismatched components that can negatively affect efficiency.
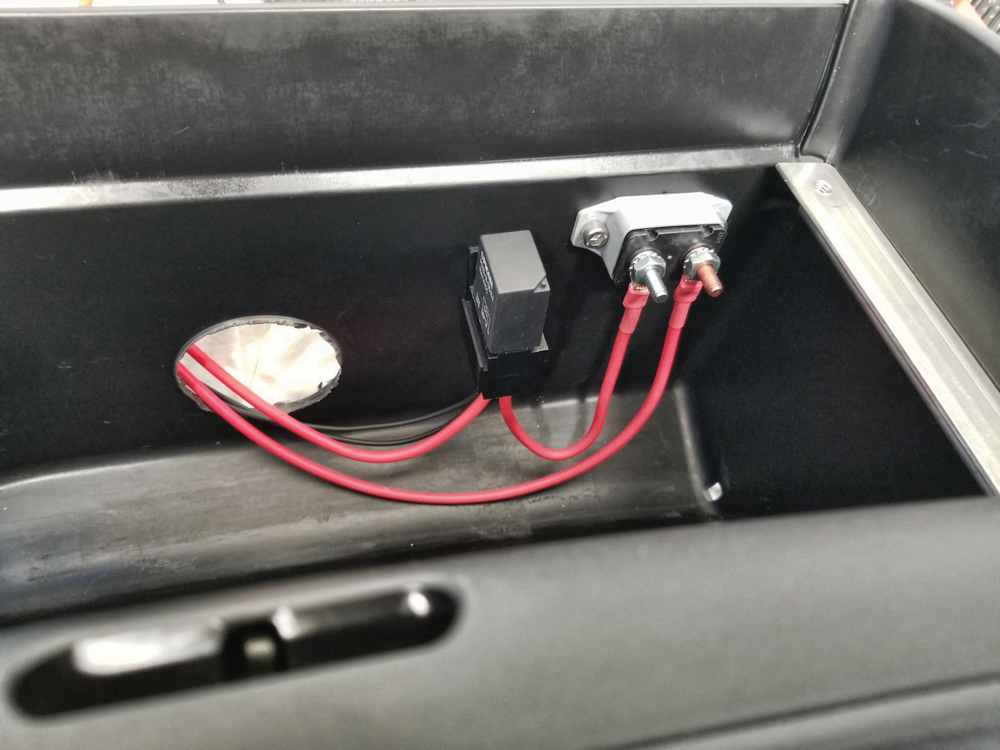
“A lot of people like to go too big—they’ll oversize the pump for the application because they want to size the pump for what they’re eventually planning to do rather than what they’re doing right now,” he said. “Maybe the car is making 500 hp now, but they’re hoping to get it over a thousand later on, so they select a pump that’s totally inappropriate for the application. In those instances, you also end up returning too much fuel, which compresses the fuel over and over, which in turn generates more heat and eventually ends up boiling the fuel.”
But Chaysavang noted that additional headroom can be beneficial to fuel pump performance when it comes to filter selection. “A filter’s maximum flow rate is typically based on what the filter flows when it’s brand new and clean, but that’s going to go down once it’s put into use and starts to get dirty. If you spec out a filter that’s right on the edge of what you need, it might not flow the fuel that’s required for that power level once the filter has captured any debris that has been going through the fuel system. So if you’re not planning to change that filter out regularly, it’s a good idea to spec out a filter that can handle maybe 20% or 30% more flow than you need.”
Wired For Success
McDaniel also explained that while the existing wiring can be convenient to use in order to make the necessary connections when swapping out a factory fuel pump for an aftermarket unit, it often will not stand up to the voltage demands of a larger aftermarket pump.
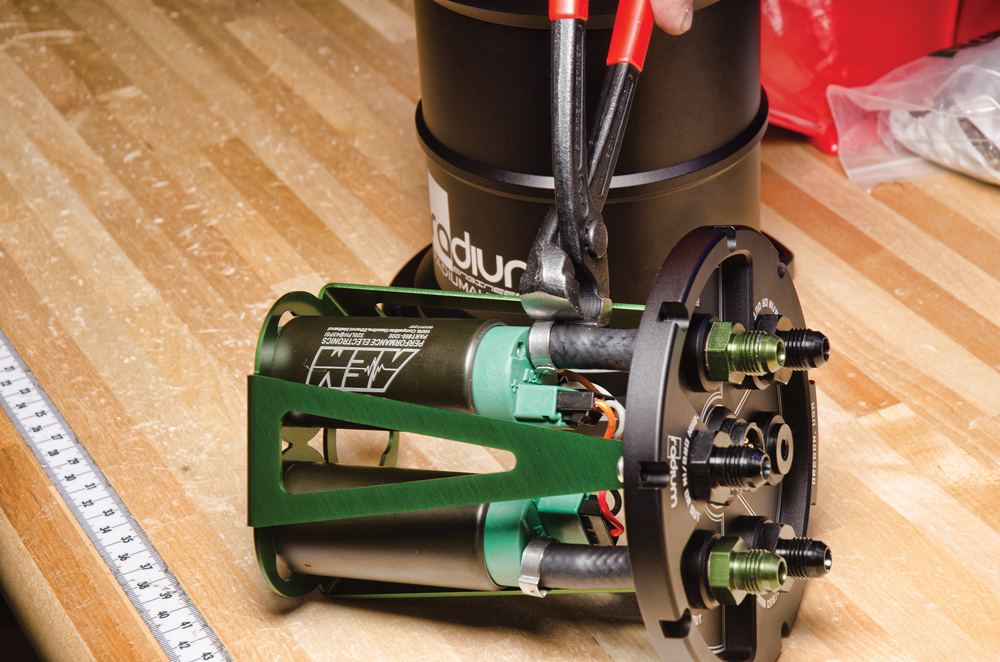
“Ideally you want to run brand new, large-gauge wire with a relay to the pump,” he said. “The big issue is voltage drop—you might be at 14 volts at the fuse box, but by the time it reaches the pump it could be down to 11 or 10 volts if you’re not using the proper wiring. Now you’re down on flow because the pump is not getting the voltage it needs to provide its full capability.”
Chaysavang added that amperage requirements for both the wiring and the associated connectors can vary based on the engine combination. “In a naturally aspirated application, the fuel pump will typically run at roughly a fixed pressure based on what the mechanical regulator is set to. But with a boosted application, the fuel pump pressure will vary with the boost pressure if you’re running a fuel pressure regulator that is referenced to manifold pressure. As the fuel pressure increases the amperage is going to increase as well, so you want to make sure the amperage rating of the wiring and the connectors matches the expected amperage draw based on your engine combination and setup.”
SOURCES
AEM Performance Electronics
aemelectronics.com
DeatschWerks
deatschwerks.com