PRI Tech: The Unexpected Value of Brake Fluid
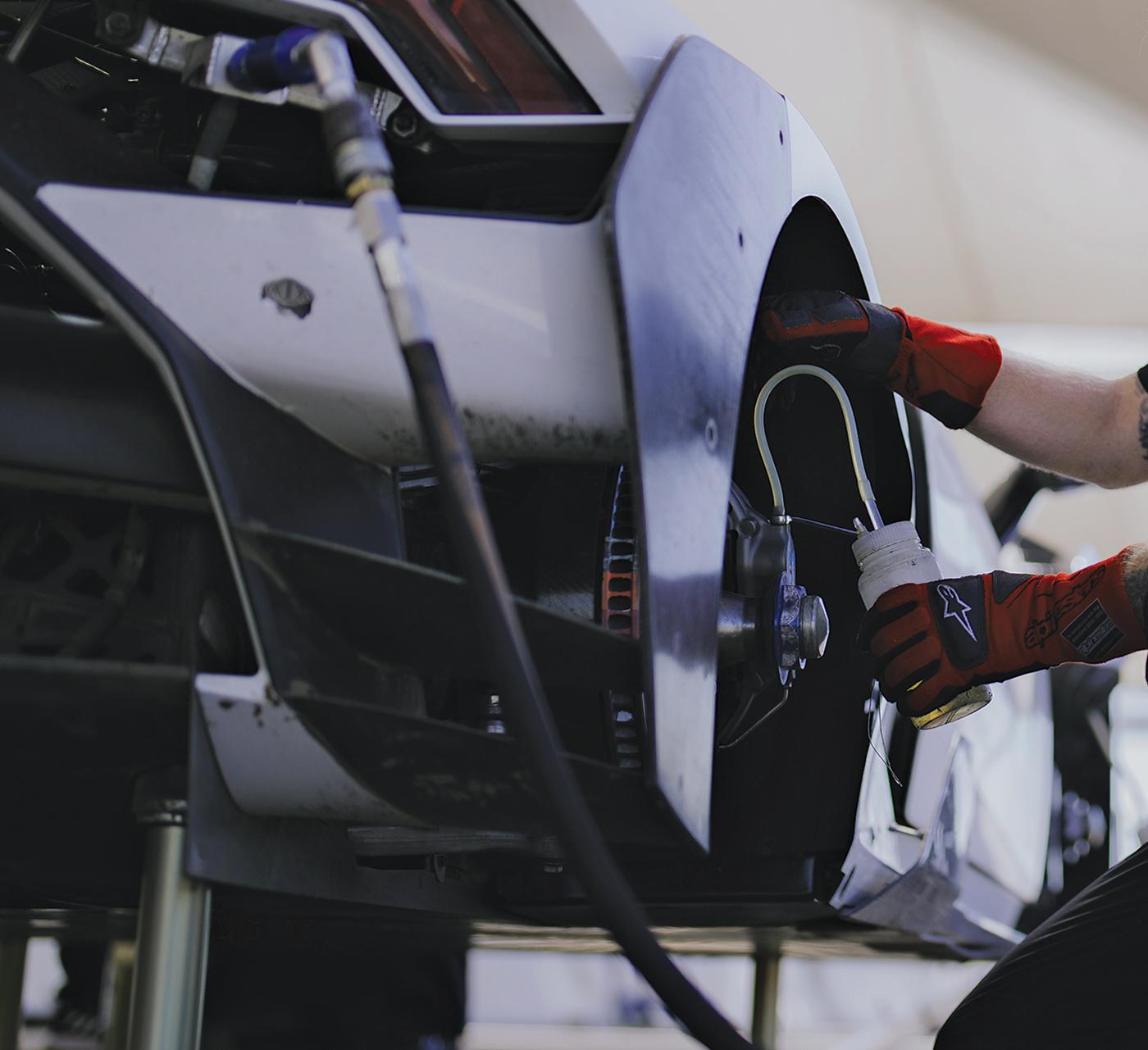
Don’t overlook this critical component of an optimal braking system.
Modern racing brake systems are a high-tech business. Sophisticated computer-aided design optimizes every component for peak performance. But what about the brake fluid? In many race series, the specifications of the rotors and calipers are prescribed so that race engineers have little scope to gain any meaningful advantage over their competitors. Typically, such restrictions do not apply to brake fluid, which means that there may well be an opportunity for a competitive advantage.
But brake fluid is just brake fluid, right? As brake fluid experts, Halo By Orthene would beg to differ. While even race engineers often think of brake fluid as little more than a commodity, the reality is far more complex and involves sophisticated chemical engineering.
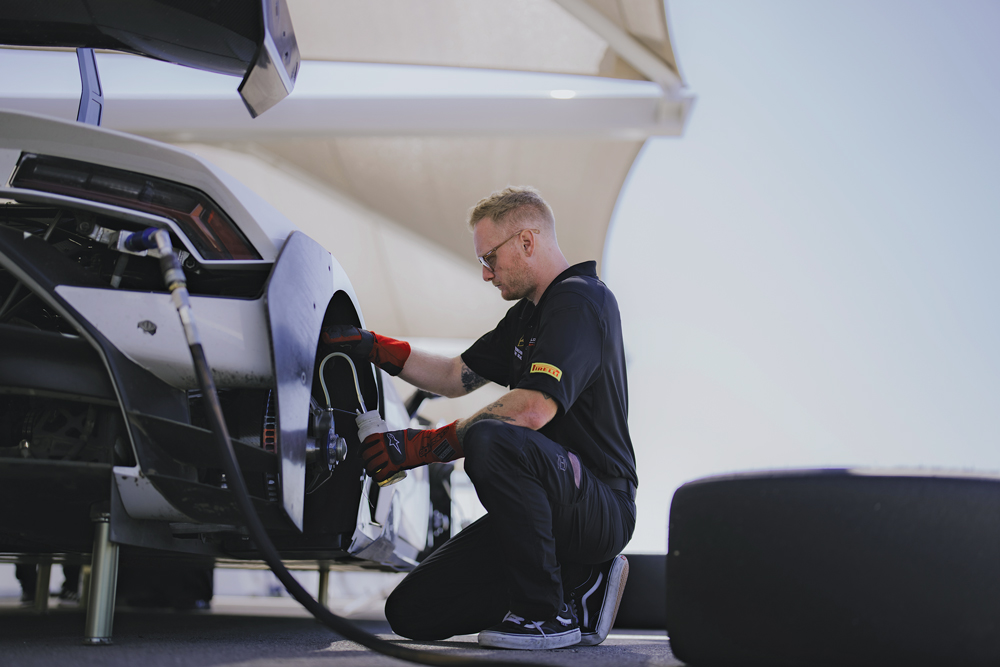
So, what is actually involved? At its most basic, brake fluid is the medium that transmits pressure force from the brake pedal to the brake caliper. At ambient temperatures it is no different than any other hydraulic fluid. But in racing conditions, brakes get hot, sometimes really hot, and this is where the challenge lies, and expert knowledge is needed. Simply put, if your brake fluid fails at high temperature, you will lose your brakes and your race will be over. So maybe your choice of brake fluid deserves a little more thought.
Brake Fluid Functions
Given its pivotal role in transmitting braking force, the first requirement of any brake fluid is that it is incompressible. You might assume that all fluids are incompressible, but they do vary, and certainly under the sort of pressures experienced within a brake system. A lot of effort goes into making sure that brake systems are as stiff as possible—from hard brake lines and braided hoses to mono-block machined calipers. The objective is to ensure that the stopping force is transmitted efficiently from the pedal to the caliper without any energy losses. But given its volume, the brake fluid itself is a significant element in this equation, especially as temperatures rise.
It might be assumed that the higher the dry boiling point of the brake fluid, the better the quality. While a high boiling point is necessarily important, it is the way that the brake fluid responds to temperature that is critical. Ideally you want as stable a compressibility profile as possible to give a consistent performance over the widest temperature range. This will give the driver a firm pedal feel, allow them to maintain the same braking points lap after lap, and give them confidence in the car. As the race goes on, heat buildup is the real enemy, and at higher levels it can adversely affect brake fluid in several ways, such as lowering the viscosity or by causing oxidative breakdown of the fluid itself. Most significantly, as the fluid approaches boiling point, it will start to form bubbles, which increase its compressibility—a phenomenon known as vapor lock, which will cause the driver to experience brake fade through longer pedal travel and sometimes to even lose the pedal completely. So, the higher the dry boiling point, or more specifically, the dry vapor lock, the better. At present, the best performing racing brake fluids, such as Halo P1, can achieve typical dry boiling points in excess of 640 degrees F. But, as always in racing, the limits are there to be pushed.
People sometimes refer to wet boiling point as well, which assumes a percentage of water in the brake fluid. But this has very little relevance to racing, certainly professional racing, as the brake fluid is changed so frequently, often after every race. In fact, the global standard for wet boiling point was established in the 1950s and so is way out of date in any case. Today the quality of component materials, especially brake hoses, has advanced to such an extent that moisture absorption in normal operating conditions is negligible. In reality, even during a 24-hour wet race, with a professional pit crew, using new brake fluid, you could reasonably expect moisture absorption of less than 0.005%.
The second critical function of brake fluid is lubrication. This is important for metal-to-metal lubricity but also for metal-to-rubber lubricity. Lubricity is important to protect against wear or excessive heat from friction and to avoid any catastrophic seizures.
In modern racing, high lubricity is also increasingly important to cope with fast reciprocating parts within ABS and ESP systems. When ABS systems were first introduced, it was estimated that the lifetime travel of a rubber seal (as it moves in operation) might be 5 kilometers. Today that estimate is more like 1,000 kilometers, as electronic control systems become more sophisticated and cycle times have become faster. Not surprisingly, lubricity has become a critical factor, so much so that it is likely to become part of the regulatory standards for brake fluid worldwide in the near future. While such standards only apply to road use, the implications for racing are equally clear, especially in longer duration and endurance racing.
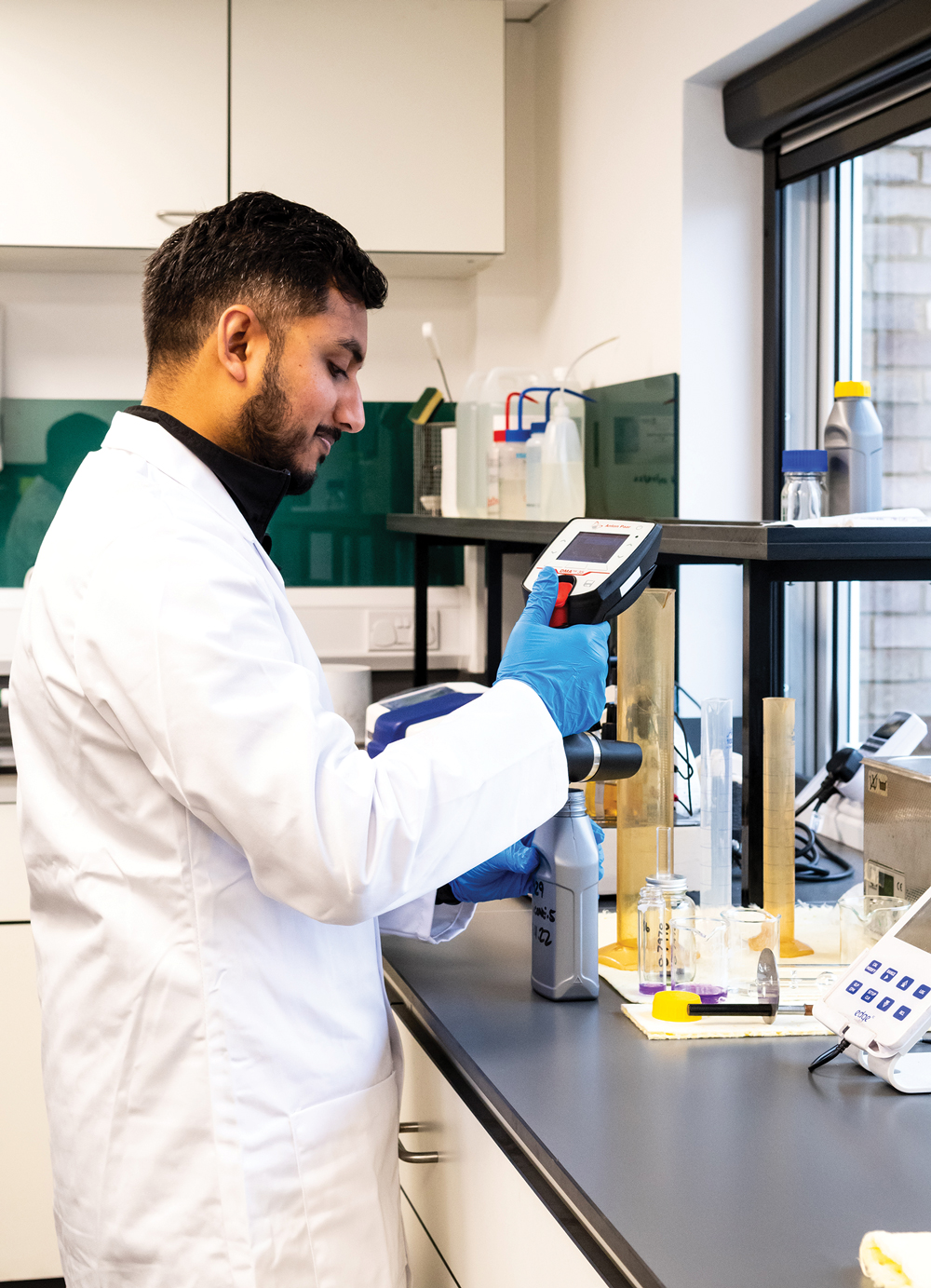
The level of lubricity can vary significantly between different chemical types of brake fluid, and this is a key reason Bosch specifies the exclusive use of glycol or glycol ether-based brake fluids (as opposed to mineral, silicone, or silicate ester-based fluids) within its racing ABS systems, as they provide a far better level of lubricity. In fact, Halo By Orthene recently developed a bespoke, high lubricity racing brake fluid for a performance OEM specifically to address issues that it was having with its ABS systems.
Finally, brake fluid needs to protect the system and avoid any adverse reactions with the component materials, such as oxidation where metal components might release gas. Just in terms of metals, a racing brake system may contain aluminum, various alloys, steel, cast iron, copper, brass, bronze, zinc, titanium, or even magnesium. There may be an equally wide range of rubbers. The brake fluid needs to be fully compatible with all these materials and not react with any of them, either individually or in combination.
Racing brake system design and development is essentially a mechanical engineering discipline. But the most advanced racing brake fluid brings an additional chemical engineering component into play, and one which is often overlooked. When racing margins are so narrow, and the opportunities to optimize mechanical brake system components so limited, ignoring the advantage that the best racing brake fluid can deliver would be foolish. Instead, choose the best, and precious tenths might never be so easy or so cheap.
Dan Stafford is the Chief Development Chemist for Halo By Orthene. Halo By Orthene is the racing division of Orthene, the world’s largest, specialist producer of brake fluid. Orthene has been the experts’ expert in brake fluid for almost 50 years, supplying many well-known brands. In December 2023, Halo By Orthene launched Halo P1, a professional-use, high-performance, low-compressibility racing brake fluid with the highest typical dry boiling point of 646 degrees F.