Ask the Experts: Parts Cleaning
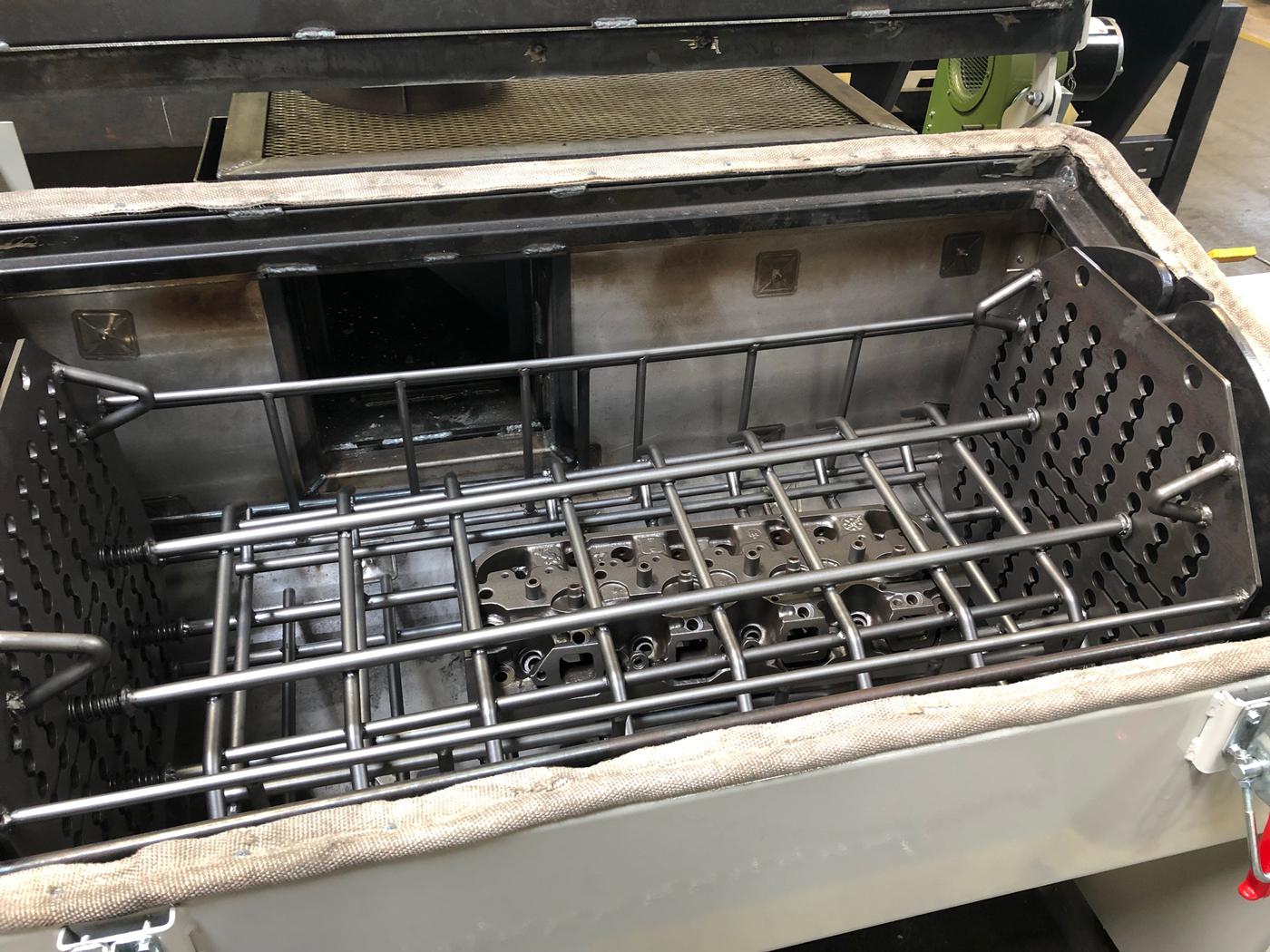
Effectively cleaning race components requires the proper equipment. Winona Van Norman recommends using its Thermal Cleaning Systems, which incorporates a three-part process that bakes off the grease and grime with its Eliminator Oven (seen here), followed by a shot blaster that blasts the ash and contaminants off the surface, and concluding with a shaker that removes the blast media.
Selecting the right equipment—and using it correctly—will help users avoid common mistakes and achieve optimal results.
Clean parts are important to ensure any sort of automotive assembly works properly. The high-stress environment of racing steps up that need considerably, to a point where the parts need to be “precision clean,” a term coined by the team at UltraSonic LLC of Amelia, Ohio. Yet there can be a disconnect between the desire for clean parts and the steps to get them there, despite the wide variety of cleaning machines and processes available to race shops and teams.
“One machine doesn’t do it all,” observed UltraSonic’s Phil Esz, who races a Top Alcohol Funny Car. “You need an arsenal of cleaning equipment.”
Dave Ward of ABS Products, Brea, California, agreed, adding, “The number-one issue we run into is using a machine not for the purpose it was intended for, or not using the proper machine for the proper results.”
Here, Esz, Ward, and other parts cleaning experts share their views about the different methods of cleaning and mistakes to avoid during the process.
The Right Tool
“Knowing the desired outcome is the key to getting the right machine,” said Ward. As an example, he compared cabinets: “If someone is looking for more of a factory look to cover up machining marks, that requires a blast cabinet with a heavier type of abrasive, such as steel grit or shot. That finish isn’t possible with a cleaning type of cabinet and media like soda or glass bead, which are more on the mild side.”
In some cases, he pointed out, “two machines may be needed. The job could start with an ultrasonic cleaning machine and finish with our HydroSlurry machine to create a clean, new-looking part. Or, for a crankshaft, a blast machine can be used to clean the crank, which then gets polished on a polishing lathe.”
Ultrasonic machines “really shine in the racing community because the parts are pretty clean to start with,” Esz explained. “It cleans the oil, grit, and dirt off in a matter of seconds.”
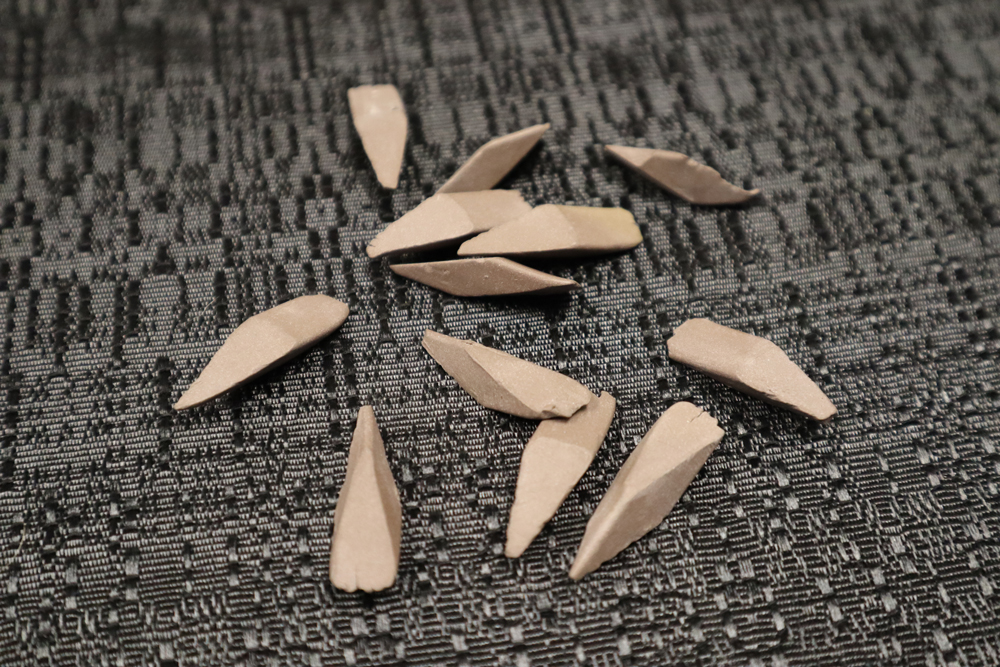
“With really dirty stuff, guys get good results using their spray cabinets and soda blasters in conjunction with an ultrasonic cleaner,” added UltraSonic’s Jason Shaw. “They can cut down on cleaning times with other equipment, and then use the ultrasonic cleaner for final clean before assembly.”
“The main question we ask the customer is, ‘Tell me about your project,’” said Mark Oryszczak of Giant Finishing, Addison, Illinois, which specializes in vibratory deburring and finishing machines. “After vibratory finishing, what is the next step in your manufacturing process? Is this final finish? Does it go to plating? Does it get painted? Are you looking to polish? Does it go to assembly? Does it get welded? What is the size of the largest part you envision putting into the machine? Those questions help us determine what type of process to give them.”
“The most difficult problem to clean is grease, especially grease that has been baked onto hot surfaces and collected other grime from the atmosphere,” said Lisa Hargrove of Winona Van Norman, Wichita, Kansas. “The most effective way to address this problem is with one of our Thermal Cleaning Systems. The three-part process bakes off the grease and grime, then blasts the ash and contaminants off the surface. Then a shaker removes the blast media and cools down the part for handling.”
The Wrong Way
The most common mistakes Hargrove sees with Thermal Cleaning Systems occur when an operator “assumes this can be done in just one process. Problems arise from skipping steps. You can’t go straight to blast or only bake if you expect to have a truly clean part.”
“One of the things people do wrong with an ultrasonic machine is put too many parts in,” Esz said. “They think they can fill the thing up like a hot tank. But when there’s a lot of weight in the tank, it sucks up all the ultrasonic power, and it’s not very effective.”
Operators also have the tendency to start the cleaning process before the water-based solution in the ultrasonic tank is up to proper temperature, Esz added. “It cleans better at the correct temperature—150 degrees—than it does at 100 or 110.”
Cleaning materials are often overlooked—and overworked—say our experts. “You have to keep that media clean,” said Oryszczak. “A lot of problems the guys have with the media come from the fact that they’ve had the same media for decades and it’s all glazed over. It’s not doing the job it was originally meant to do. Finding the right chemistry is also extremely important.”
Also, operators often “don’t have enough media in the machine, and they’re not getting the proper tumbling action,” he added. “When there’s more media in the machine, and the parts go down to the bottom of the machine, that’s when the work is getting done, when you have all that weight pushing down and grinding. If the parts are just sitting there vibrating on top, nothing’s getting done.”
Media selection has a big impact on the cleaning results as well and is “the biggest thing most people need to learn,” said Oryszczak. “There’s literally thousands of different combinations of sizes, shapes, and compositions of media. We’re creating new media all the time, coming up with new shapes for certain issues.” For example, media has been developed especially for gears, “to get into the valleys in between the teeth to make sure it gets cleaned. If you just put a general-purpose medium in it, it might be too big and won’t reach certain areas.”
The Best Thing
All of our experts encouraged engine builders or race teams to reach out with any questions they may have about parts cleaning.
“Pick up the phone and call us,” said Oryszczak. “I can get more out of a phone conversation than an email or text. You might divulge something you didn’t think is relevant that could have a huge effect on what I tell you to do.” He also invites customers to send sample parts. “Let us process them for you and get the results. We can potentially show you much better results more efficiently than what you’re doing now. Then you can come in and run sample parts with us in our lab.”
“When looking at any type of machine, especially one you’re spending big dollars for, you really should talk to people who know what they’re talking about within the industry, whether it’s the company you’re buying from or experts in that field,” said Ward. “Ask them what they’re using and how they’re using it. They won’t tell you their secrets about how they’re making their engines last longer or produce more horsepower, but they more than likely will talk to you about their cleaning equipment and how they use it.”
SOURCES
–
ABS Products
abs-products.com
Giant Finishing Inc.
giantfinishing.com
UltraSonic LLC
ultrasonicllc.com
Winona Van Norman
winonavannorman.com