Made To Slide
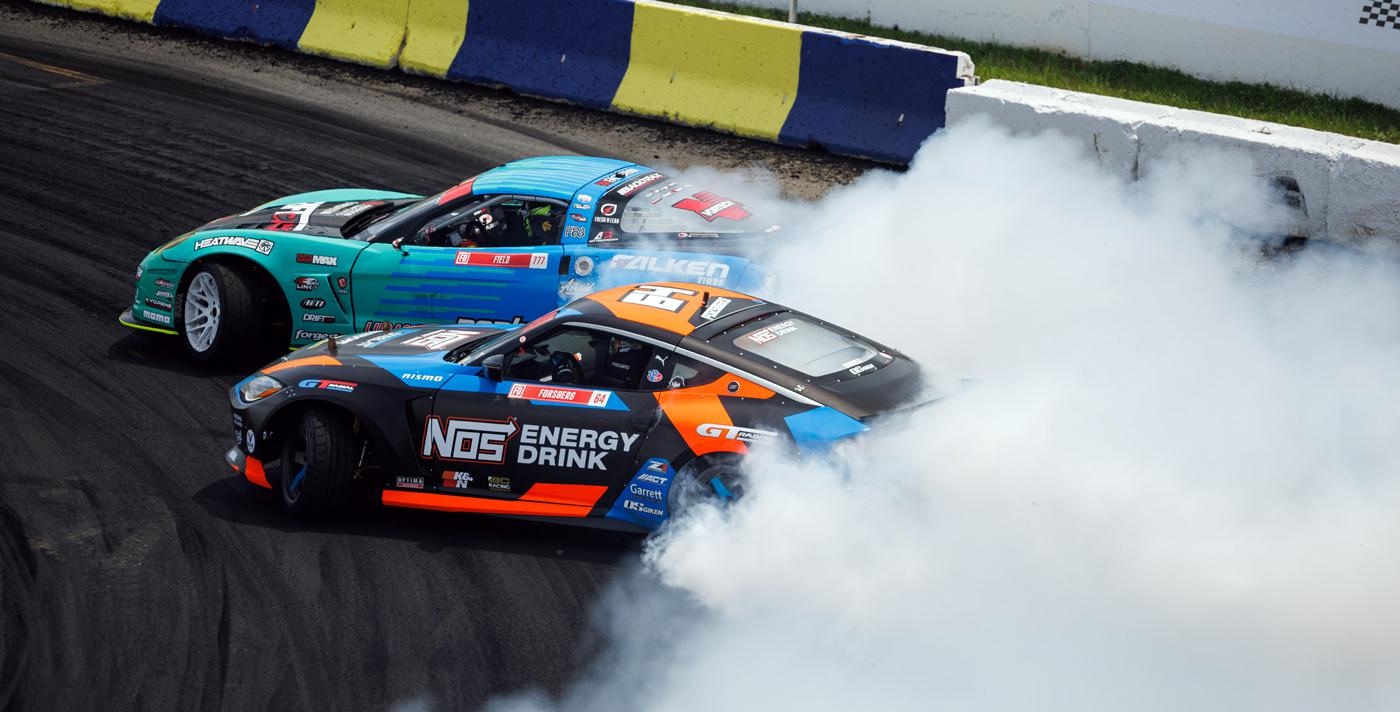
Photo courtesy of Larry Chen/Drift Cave Motorsports
While big horsepower, specialized suspension components, and quick-change solutions still epitomize these rowdy machines, reliability remains paramount in today’s drift sector.
Drifting continues to be one of the fastest-growing disciplines in motorsports. Attracting some of the youngest fans in racing, drifting has embraced the culture associated with it as well as the technology that has helped to define the look, feel, and competitive nature of the sport. It’s an approach that has helped the drifting segment mature rapidly over recent years, not only in terms of aftermarket support, but also its willingness to innovate and advance.
“In the grand scheme of things, drifting has evolved pretty quickly,” said Mike Skudlarek of Detroit Drifting, Livonia, Michigan. “One of the cool things about pro-level drifting is that there’s never really been any kind of limitation on horsepower. The playing field has always been leveled by limiting the grip that a vehicle can have by weight restrictions relative to tire size.”
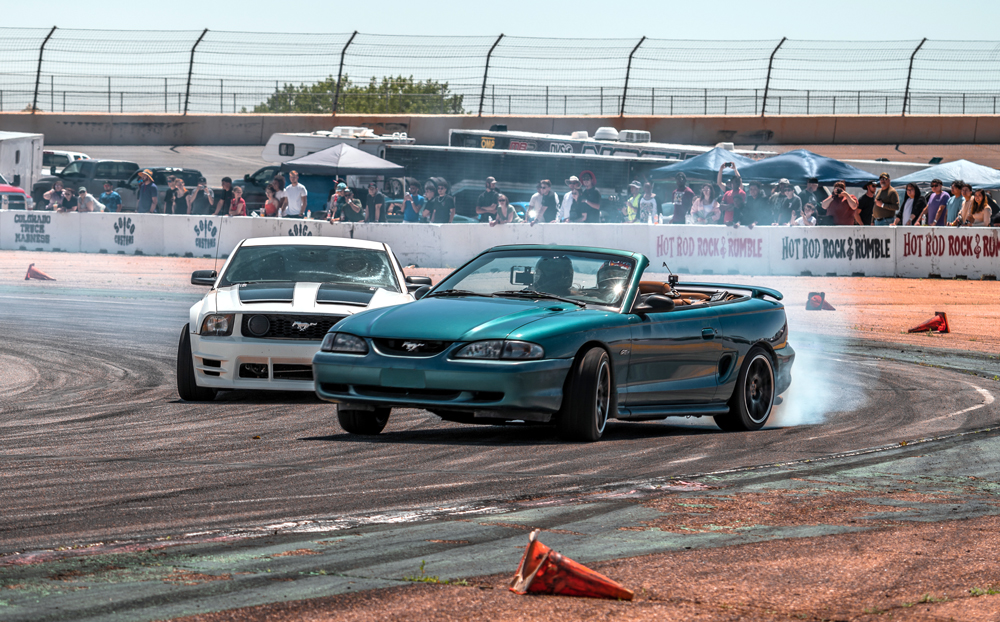
That tactic has fostered a horsepower arms race over the past decade that in turn sent competitors in search of ways to dial greater reliability into their cars. “Within a few years, 800 to 1,200 horsepower started to become commonplace, and so the supporting parts had to change as well,” Skudlarek explained.
“Suddenly the factory components that you might’ve been able to get away with a few seasons ago weren’t cutting it anymore. That led a lot of teams to engineer their own motorsports-grade hardware that was designed specifically for drifting,” he added.
Over time those development efforts have expanded far beyond angle kits and beefed-up clutches. To build a competitive drift car today, racers must take every aspect of the car’s performance into account while also considering the rule sets that can affect the eligibility.
Platforms
Rear-drive Japanese coupes have long been a staple in drifting, but as the prices and availability of many of these cars have skyrocketed recently, competitors have been seeking worthy alternatives. Although some grassroots series allow purpose-built tube chassis cars, larger organizations like Formula Drift require the vehicles competing at all levels to be production based with unmodified wheelbases. That makes starting with a capable and well-supported architecture key to establishing a solid build foundation for those who wish to pursue that series and other ones like it.
“A lot of the younger guys want to build a car that’s unique to them,” said Scott Umbreit of Drift American, Fort Collins, Colorado. “Many of the popular cars early on in the sport have either dried up or are getting cost-prohibitive, which has led to a more diverse field of vehicles. Cars like Mustangs, Nissan 350Zs, Corvettes, and BMW 3-Series have become the cost-effective, reliable alternatives.”
As Daniel Chow of Morgan Hill, California’s Drift Cave Motorsports pointed out, some platforms have inherent advantages that can streamline the build process.
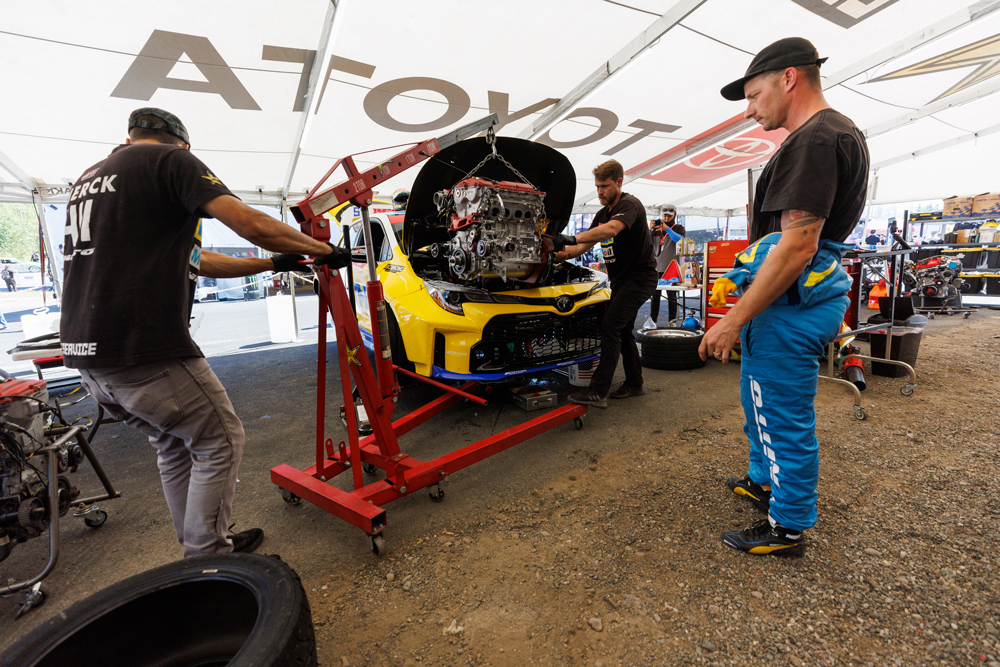
“We started off with a Nissan S chassis when we began competing in Formula Drift’s Pro series,” said Chow. “At that level you’re looking at a minimum of 200 to 300 hours of chassis fabrication to make the car competitive. We put an LS engine in it, and we were trying to adapt all of these different parts that weren’t originally designed for that chassis. The same applies for BMWs, 350Zs, and so on.
“When we were looking to build a new car about four years ago, we started thinking, ‘Why are we putting all of this effort into a 30-year-old platform when the Corvettes are engineered to be capable sports cars with good weight distribution, they’re relatively affordable, they have strong support, and they already have LS engines?’” Chow continued. “When we entered into the Pro series with our Corvette, I think it was a big eye-opener for a lot of people.”
Regulations in Formula Drift have made some popular performance platforms less appealing for drift builds, but competition director Kevin Wells told us they’re always looking for ways to make the series more accessible while keeping costs in check.
“You need the ability to add steering angle, and some cars just aren’t conducive to that,” explained Wells. “For example, the Fox-body Mustang has a spring perch built into the subframe, and the way that the lower arm is designed, you can’t get a lot of steering angle out of it with the factory subframe. While they can be modified according to the rulebook guidelines, we require the factory front and rear subframes on all of the vehicles. Right now that makes the Fox-bodies inherently more difficult to work with, but next year the plan is to allow competitors to use an aftermarket K-member from QA1 in the front of those cars.”
Powertrains
Since most series have no limitations on horsepower or engine combinations, competitors are free to use whatever solutions they prefer to achieve their ideal horsepower levels. While reliability is still the top priority for most teams, Wells said that this unrestricted aspect of the builds has led to a wide variety of engine combinations. “We have everything from four cylinders, V6s, straight sixes, and V8s to V10s and V12s competing today.”
In the interest of keeping costs under control, Formula Drift’s PROSPEC series prohibits more exotic hardware like sequential transmissions and requires a Link Engine Management ECU. “At a certain point you have to limit things a little bit because there’s always someone who wants to go further,” he said. “I don’t want to ruin the sport by making it too expensive.”
Since a vehicle’s minimum weight is directly tied to the tire width it can run in Formula Drift, it encourages teams to build heavier cars that compensate for the weight with a lot of horsepower. To that end, the LS remains the go-to option for a cost-effective grunt that can be relied on.
“At the sportsman level, the driver is often also the mechanic, so having something that’s going to be easy to maintain is really important,” said Skudlarek. “The obvious choice there is the LS family of engines. A naturally aspirated LS is a great option at that level, and if you need more power down the road, you can add forced induction at a pretty low cost without seriously jeopardizing reliability.”
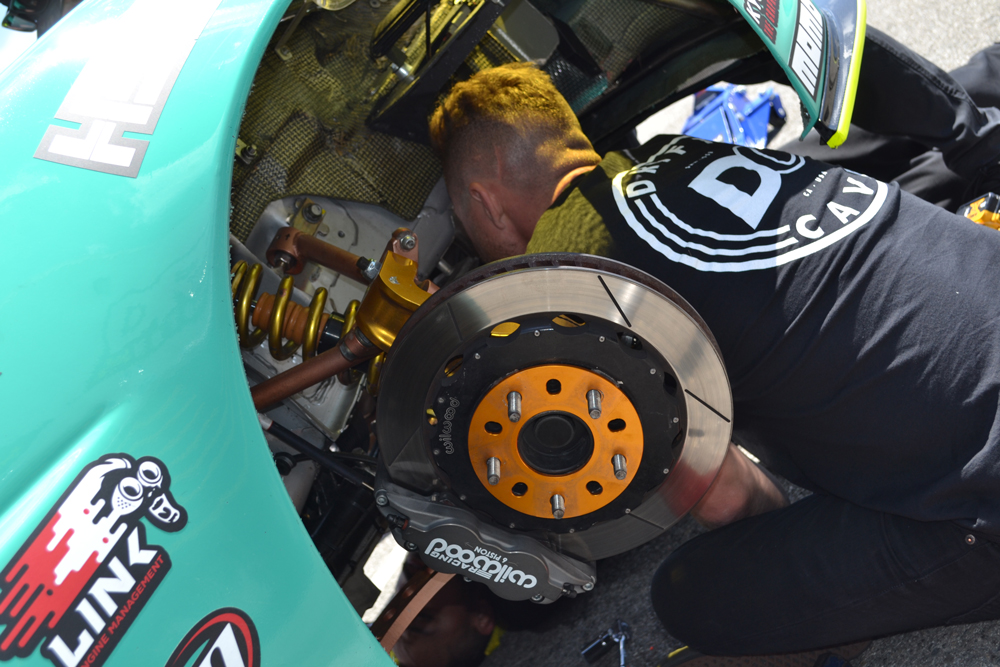
Many competitors run a nitrous system to provide additional response on demand as well. “On the courses we compete on, you can have everything from 20 to 30 mph corners to ones that you might take at close to 100 mph,” said Chow. “Because there’s so much fluctuation in rpm, you can see some lag in throttle response in some situations. We’re always looking for ways to improve that, and so initially the thought was that a 200-shot of nitrous could help get the cam lag out, or help the turbos spool up quicker. But at a certain point, it just became a desire for more horsepower for us, so we’re basically spraying all the way from 3,100 rpm to 7,700.”
When it comes to cooling, many teams use rear-mounted radiator setups that are similar to what you’d find in a Trophy Truck. “Most of these cars’ engine bays weren’t designed for the engines that are in them, so it’s often a situation where you just don’t have the room for the radiator and fans, or having them there would make working on the car much more difficult,” Wells said. “By moving it to the back you’re getting cooler air and adding water volume, and it also helps move the weight distribution toward the rear of the car.”
With big power and massive shock loads to contend with, transmission choice has also become an important consideration. Reinforced factory-style gearboxes might have been able to get the job done before quadruple-digit horsepower numbers became commonplace, but that’s no longer the case at the upper levels. NASCAR-style four-speed dogboxes like the G-Force RTS GSR and sequential transmissions like the six-speed offered by 6XD have become the standard of today, as they offer the strength and adjustability required to tolerate the abuse and maximize performance.
In that same spirit, quick-change differentials have also become a common sight at the upper levels of competition. “It allows you to do a final drive change in less than three minutes, and that’s a huge benefit,” said Chow. “We’ll make anywhere from four to eight gear ratio changes over the course of a weekend.”
Chassis and Suspension
Although series like Formula Drift require factory chassis and wheelbases, some modifications are allowed in order for teams to improve durability and make the cars easier to repair. According to Wells, 99% of the teams are using aftermarket bumper structures of some kind. “These are for the protection of vital engine parts and ease of service, and with the body work installed you’d never know they’re there. Most of these structures are removable, and teams bring spares to change out during the events—especially for the rear.”
Drift car suspension systems, meanwhile, have advanced significantly over recent years. Since Formula Drift requires suspension components to mount in the factory locations, in the early days many teams needed to figure out a custom solution to get the performance they needed. This too has changed. “There are full bolt-on systems for pretty much all of the common platforms in drifting now,” said Umbreit. “For folks who might be just starting out, there are now kits available that allow you to get more steering angle out of the car while keeping the stock spindles and things like that. Companies like Wisefab, Scotidi Race Development, and FDFRaceshop now have options that cover a wide range of applications.”
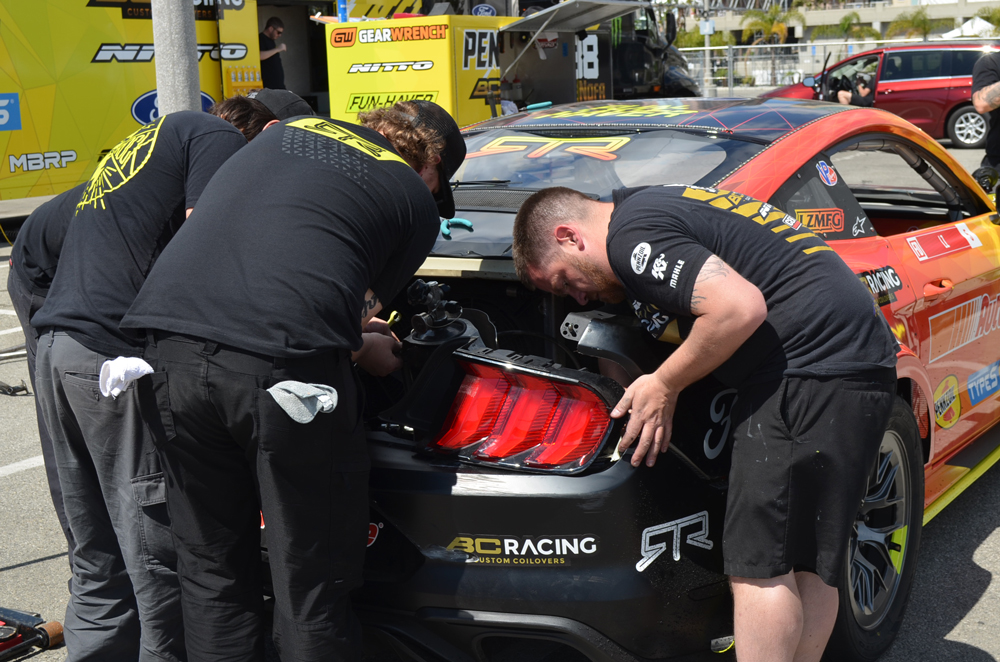
Skudlarek noted that the more comprehensive solutions tend to fix issues that typically cannot be addressed by basic angle kits. “At the grassroots level, people are often looking for the least expensive way to add more steering angle, and they’re willing to compromise on other aspects of the suspension’s performance to get it. More advanced kits are usually engineered to correct some of the issues that arise in the suspension geometry when you start swapping out factory components. These kits are CAD designed and include purpose-built components like steering knuckles, and oftentimes there’s a different camber plate or top hat for the strut that relocates the pivot point to be more conducive to the geometry of the kit. It’s more of an all-in-one solution.”
Of course, a hydraulic handbrake system is par for the course at virtually all levels. “Wilwood offers all of the components for these handbrake systems, and most of the handbrake handles are designed around their components,” Skudlarek added. “You’ll see a Tilton setup occasionally, but Wilwood has really become the go-to there.”
Bodywork
Contact—be it with a wall or another car—is pretty common in drifting. As such, teams have sought ways to minimize the damage and make repairs as quick and painless as possible. “Pretty much everything has gone to fiberglass or carbon fiber, and a few teams have done carbon Kevlar,” said Wells. “Carbon Kevlar is an interesting option because it’s flexible and will pop back into shape, whereas a piece of fiberglass isn’t going to do that. But about three-quarters of the field still run the factory metal doors—the doors just get hit so often that its cost prohibitive to use carbon there.”
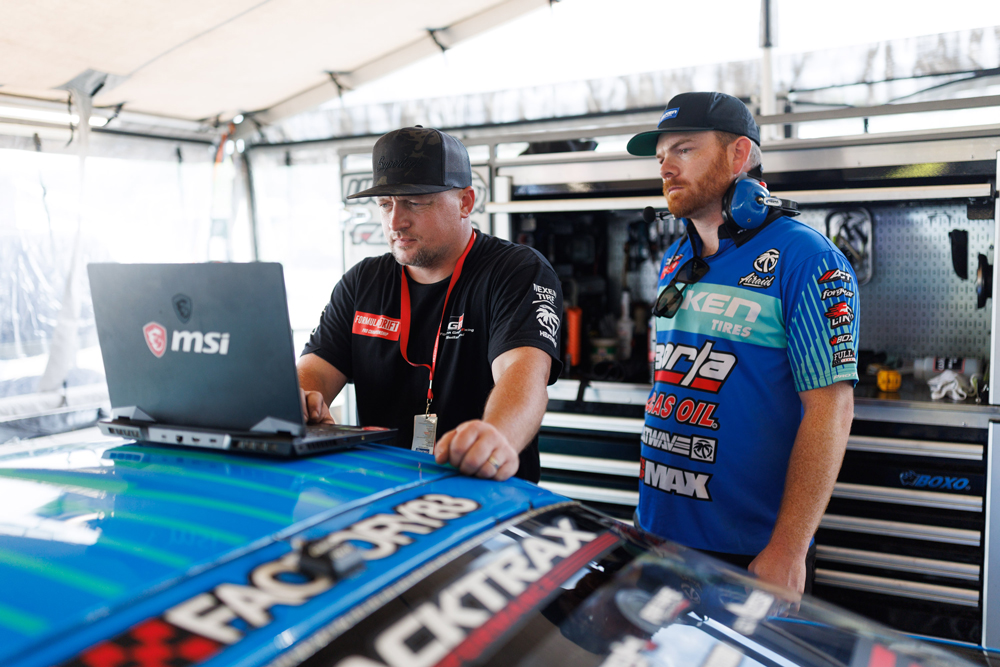
Many aftermarket kits have integrated front splitters, diffusers, fender flares, and other features that add both style and functionality to the car without bringing additional pieces into the mix that would make repairs more complicated. Wells said teams also utilize aftermarket mounts to make it less time-consuming to replace damaged panels. “For instance, with the rear quarter-panel, the teams are allowed to cut the whole thing off aside from a one-inch lip that goes all the way around the car, so the majority of teams use that lip to rivet in the aftermarket panel. Others will use quarter-turn fasteners, but it can be difficult to get the panel back on after you’ve gotten into damage with those. At the front end of the car, we only allow for modifications in front of the strut towers on the top side. So everything forward of the rail that the fender would attach to is usually aftermarket.”
Because of the format of competition, ease of replacement is really the highest priority here. “Some guys will just use really strong cable ties to hold it together,” said Chow. “These cars aren’t going to do 150 mph around a race track for long periods of time. The panels need to stay together for the 45 seconds that we’re on track and be easy to replace if there’s a collision.”
What’s Next
After a few years of big rule changes in Formula Drift, Wells said that the series is giving competitors some breathing room going into 2023 while the organization mulls over long-term considerations.
“There aren’t many rear-wheel drive cars left on the market at this point, so we need to make sure all of the ones that are out there are eligible to compete. We’re also trying to figure out what we can do with EVs. We’ve had electric drift cars in the series before, but it was challenging because some of the tracks weren’t set up for it, and they wouldn’t let them run. We want to figure out how to bridge that gap a bit without forcing it to be some kind of spec car.”
In the meantime, Skudlarek expects to see technology becoming a larger aspect of most teams’ programs over the next few years. “The use of data acquisition is definitely on the rise—it’s already huge at the pro level, and I think that’s only going to increase over time. In order to keep a handle on some of these really high-strung engine packages and maximize the capability of these cars, it kind of has to happen.”
Sources
Detroit Drifting
detroitdriftingco.com
Drift American
driftamerican.com
Drift Cave Motorsports
driftcave.com
Formula Drift
formulad.com