Build An Effective Fuel System

Between ever-increasing power levels and the variety of fuels racers are using, choosing the right fuel system components is more important than ever.
“Without fuel, you don’t go.”
Jeff Stacy of the Aeromotive Group, based in Lenexa, Kansas, distilled the importance of an effective fuel system down to that brief, five-word sentence. Even with all the best block prep, head work, and valvetrain science, an engine is a very expensive doorstop without fuel to make it run. We picked the brains of five fuel-delivery experts for their advice on how to choose the proper components and build the most effective fuel system for a variety of racing disciplines.
Best Results
We started our discussions with this question: How can racers get the best results from their fuel system? The question was purposely wide-open, as we hoped each would approach the notion of “best results” from a different perspective.
“Buy American-made, high-quality products,” said Stacy. “Fuel systems are not a place to try to save money. Waterman [what Stacy described as “predominantly a circle track and very high-end drag race company”] and Aeromotive build a premier product that is priced accordingly. We see people who figure they can do it cheaper by hobnobbing this to work with that, and it doesn’t work. It may work for a month, two months, or until it gets hot out. But the founder of Aeromotive, Steve Matusek, named the company Aeromotive Fuel Systems for a reason. We’re not just a fuel pump manufacturer. We don’t sell you a pump and say, ‘Good luck.’ We manufacture the complete system. We sell you a pump and provide you the inlet filter, outlet filter, fuel pressure regulator, whatever you need to make this work in the application that you’re trying to fuel.”
“In order to optimize fuel system performance, it is essential to ensure proper sizing and maintenance,” said Brandon McDaniel of DeatschWerks, Oklahoma City, Oklahoma. “Having a fuel system with 20 to 25% overhead is recommended for improved drivability and to avoid excessive heat buildup. However, oversizing injectors by more than 25% can negatively impact idle quality and throttle response, and oversizing fuel pumps beyond 25% more than you require to meet horsepower goals may result in heat buildup and vapor lock issues.” DeatschWerks, he said, “has painstakingly developed injector and pump sizing calculators to simplify the selection of the proper flow rates to meet a racer’s needs.”
Correctly sizing, locating, and maintaining fuel filters is “crucial,” McDaniel said, to prevent fuel pump and injector malfunction. “Debris can cause severe damage to fuel pumps, resulting in potential engine damage. Debris in injectors can disrupt cylinder-to-cylinder balance, causing issues such as lean or rich cylinders. DeatschWerks’ dual-stage magneto-mechanical filters are recommended to filter out any such debris that might be in your fuel system. Proper maintenance of fuel system components can avoid costly and damaging issues down the line. We recommend cleaning your fuel filter and injectors every racing season.”
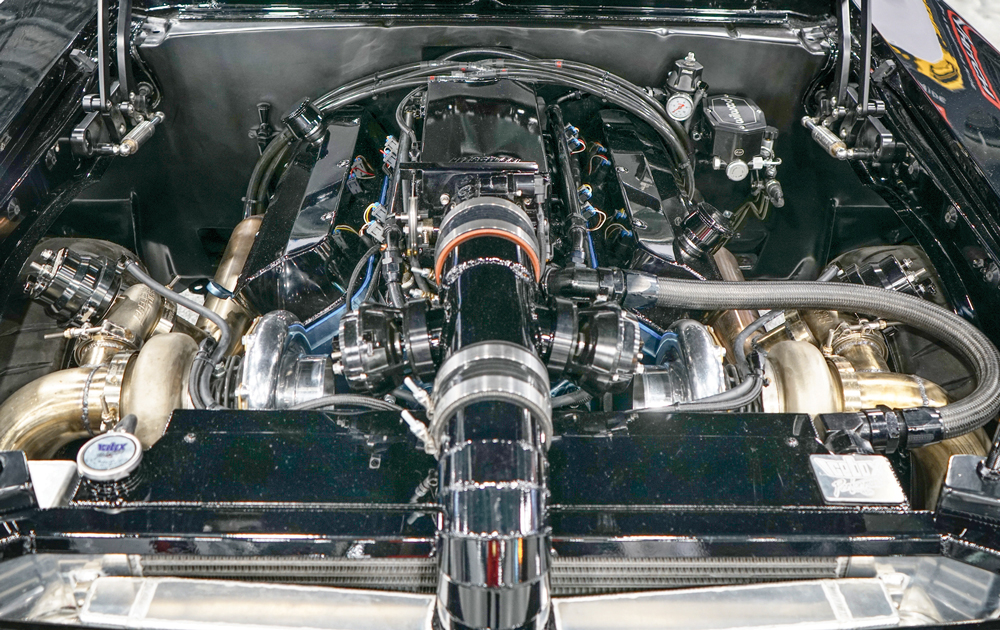
“The key to having a good running EFI system is consistent fuel pressure,” said Bryce Cegielski of FiTech EFI, Riverside, California. “The most foolproof way to achieve consistent fuel pressure, no matter what the vehicle is doing and experiencing, is an in-tank fuel pump. An EFI-rated gas tank has baffles inside of it that keep fuel next to the fuel pump. So when the pump always has access to fuel, you can anticipate that you’re going to have consistent fuel pressure.” Because a fuel pump pushes fuel rather than pulling it, in an application where the fuel pump has to be mounted outside the tank, “the most important thing is to get that pump gravity fed with fuel—putting it below the bottom level of the gas tank,” he added. He also advised “keeping the line sizes leading to the pump as large as possible and as short as possible. Anything that adds up as a restriction prevents fuel flow from getting to the pump.”
“One of the most important things, especially when assembling your fuel system, is to keep things as clean as possible,” said Nic Santarpia of Fuel Injector Clinic, Hobe Sound, Florida. He often sees people assembling a fuel system using “lines off the shelf that might have been sitting for some time. Dust and debris can accumulate in lines and other fuel system components. That tends to clog either their filters after they just started getting fuel flowing through their system, or even down into the injectors.” If a racer buys a complete system from a manufacturer, “that company should pack up everything and seal components into individual bags” so the components will be clean and remain that way, “even if you don’t put it in the vehicle right away.”
Matthew Sosa of Holley, headquartered in Bowling Green, Kentucky, said a fuel system’s best results rely on three pillars: “First you need to make sure you have enough volume or enough flow rate coming out of the pumps to support the horsepower of your engine. Second is the control aspect of the fuel system, which is mainly in the tank. Wherever those pumps are, or wherever the pickup is, it should always be submerged in fuel.”
This is one part of the fuel system equation that can be race-discipline-specific. “A drag racer only needs to think about acceleration in one axis,” Sosa pointed out. “When you take off, the fuel is going to go to the back of the tank. But it gets a little more complicated if you’re a circle track or road racer because you need to control the fuel in multiple axes. You could be braking and turning, or accelerating and turning, and the fuel could be sloshing around.”
Sosa’s third pillar is plumbing. “With plumbing, it’s really an efficiency question. What the pump flows at the pump at a certain pressure doesn’t matter. What really matters is how much flow you can get through your entire system.”
Building the System
Putting together an effective fuel system begins with determining your goals, Santarpia explained. “Typically, you want to have an idea of what your power output is going to be, because you are going to need enough pump. You are going to want the correct filtration and the correct injector size for the power you are trying to make. Fuel line size can create a restriction in flow if it is too small, so it is also important to choose the appropriate size fuel line for your power goals.”
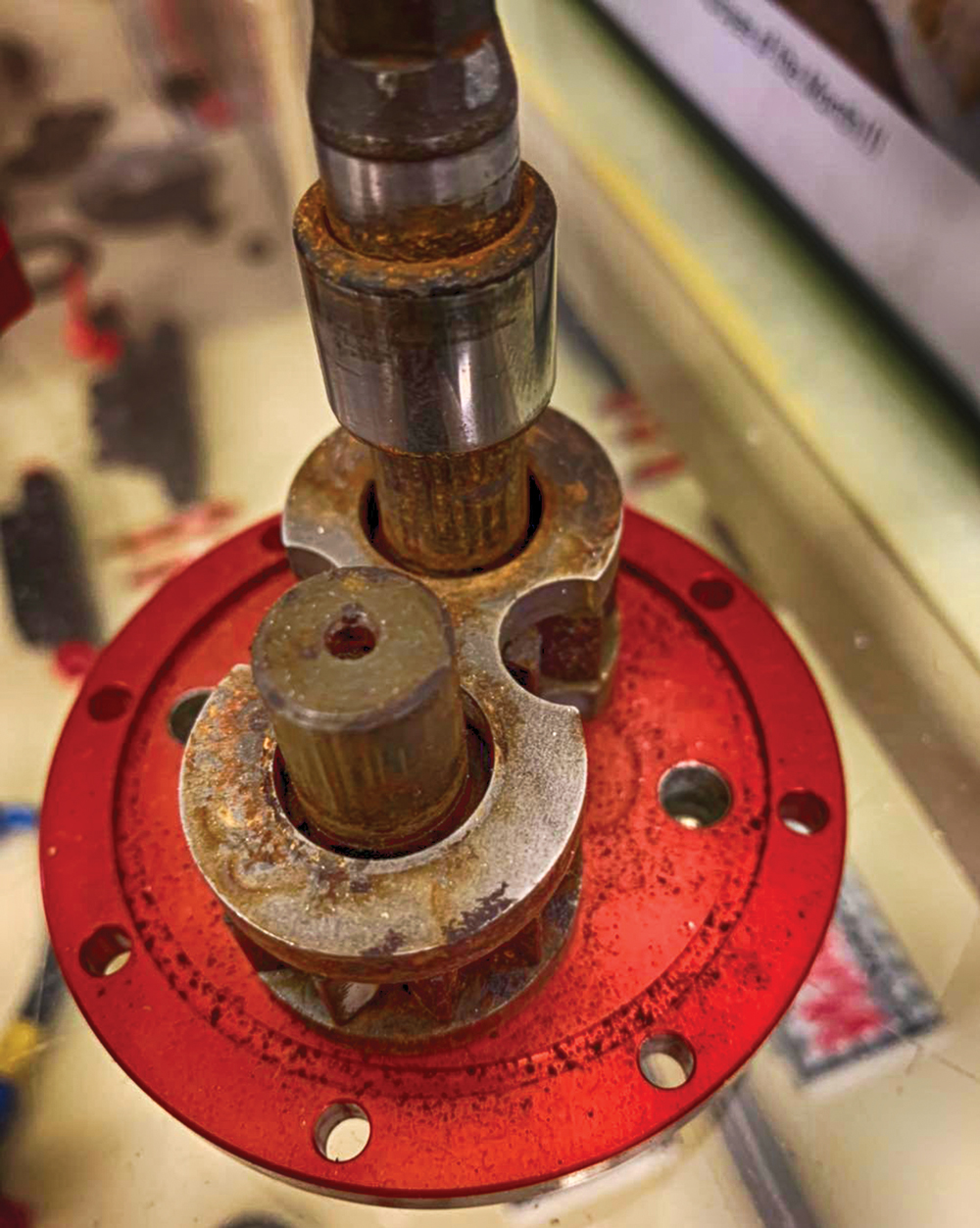
He also mentioned fittings as “an overlooked component of fuel systems in many cases. Cheap fittings can leak and cause fuel flow restrictions. My personal recommendation for fittings and fuel systems in general is Fore Innovations.”
McDaniel cited racing type and horsepower output as critical factors in building a fuel system, but he also said it’s important to identify “all the necessary components prior to purchasing. These include elements such as drivetrain loss, fuel pressure, fuel type, boost pressure, and whether the fuel system is return or returnless, as well as whether it is a rising or static pressure system. By having knowledge of these components, it will be easier to determine the appropriate flow rate, pressure, and plumbing required for selecting a suitable fuel system.”
Aeromotive takes a lot of the guesswork out of building a fuel system with its Power Planner, Stacy said, a tool on the company’s website. “It will have everything from our smallest, A750 pump all the way up to a mechanical pump, and it will show you inlet size fitting part number, outlet size fitting part number, post-filter, pre-filter, what regulator to use if we recommend one, and how to plumb it whether it’s a fuel-injected application or a carbureted application.”
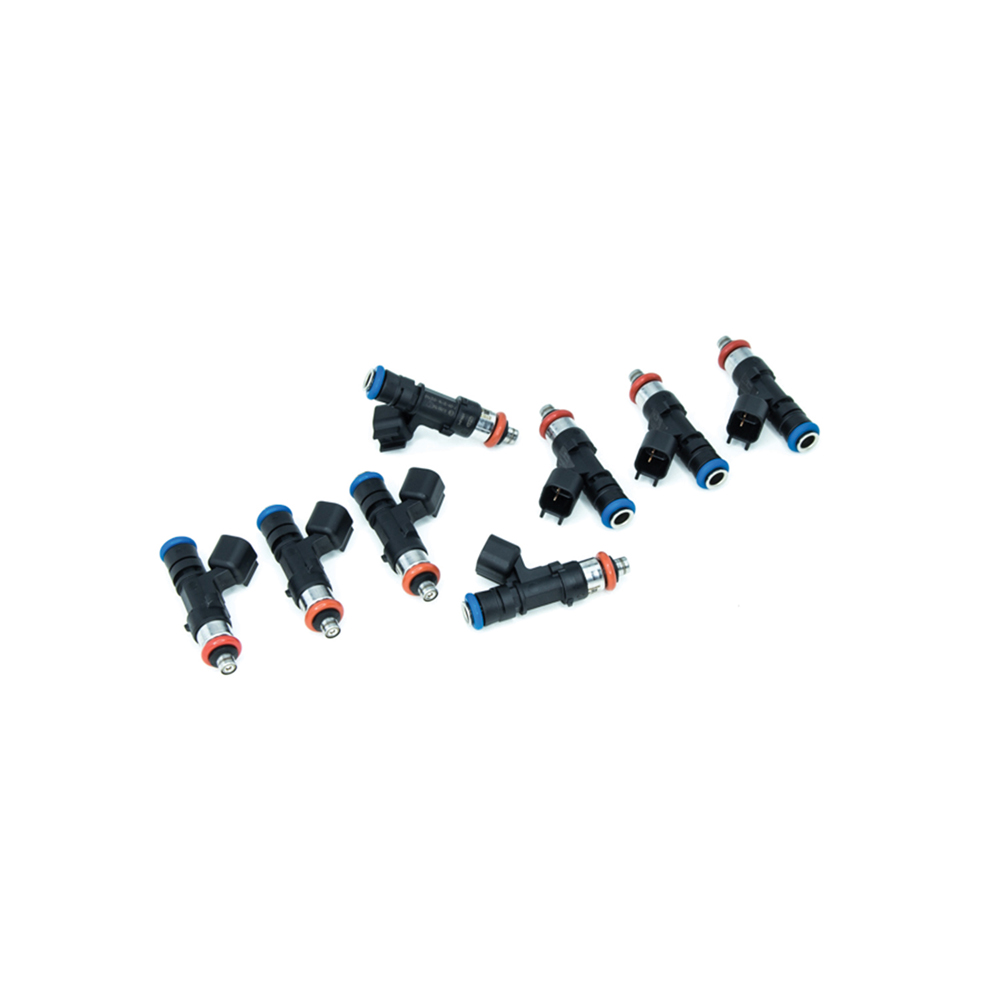
Should other questions arise, he advised calling Aeromotive’s tech department. “We’ve been building fuel systems for 30 years, and some of our tech people have been here for 25 of those 30 years. So we’ve seen everything and done most everything. Don’t email us, don’t message us on social media. Pick up the phone and call us. It’s so much easier. If the guy’s just looking for a part number, we’ll give him just the part number. But if he wants to learn, we will teach him the fluid dynamics of a fuel system so he will understand why we’re recommending what we’re recommending.”
Component Selection
It’s easy to get deep into the weeds when discussing which fuel system components to use and why, especially given all the different permutations of race engines and their output. We’ve collected some of the general concepts to point racers in the right direction when it comes to choosing pumps, lines, regulators, and other parts.
Regarding fuel pumps, several of our sources talked about having enough fuel volume to support the engine. “Support” refers to the amount of fuel, whether it’s measured in gallons, liters, or pounds, for the power level the engine is expected to make.
“It’s an equation based on the brake-specific fuel consumption and the weight of your fuel,” Sosa explained. His rule of thumb: “One gallon of gasoline per hour can support approximately 10 horsepower” for a naturally aspirated engine. It takes about 30% more E85 to support the same amount of power, and twice the flow rate if using methanol.
Fuel pressure will vary, too, depending on whether the engine is carbureted or fuel injected, and naturally aspirated or boosted.
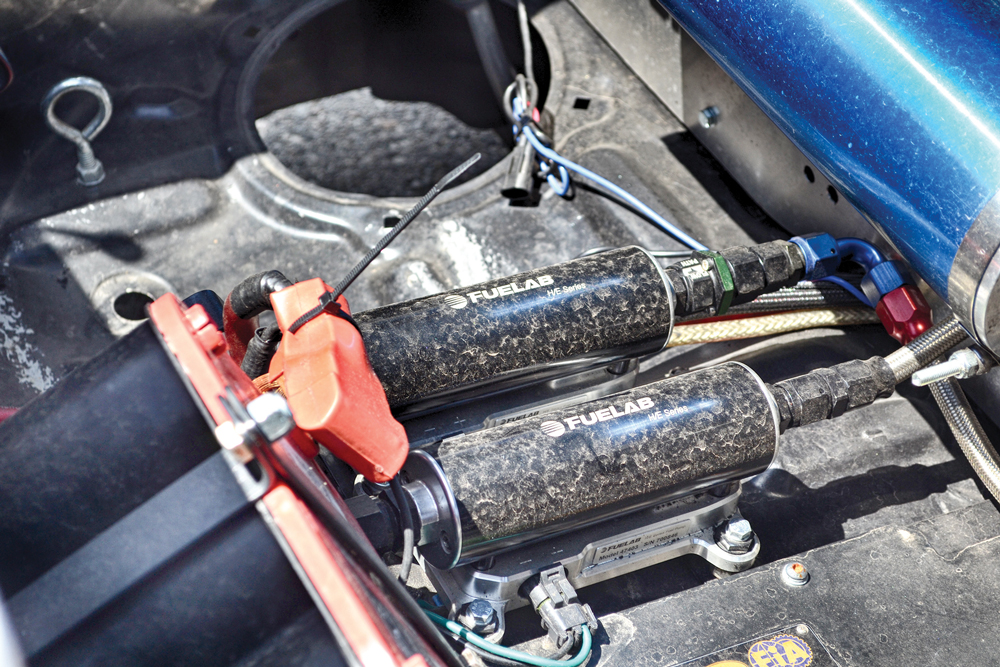
“The output of a pump for a carbureted application could be 15 psi, and we may regulate it down to 8,” Stacy said. “But fuel injection is rated at a much higher psi at the injector, typically 43 psi. People can get in trouble if they don’t look at the flow rate at pressure. We always ask, what’s your base pressure, and is it turbocharged, supercharged, or naturally aspirated? If it’s naturally aspirated, we can end our conversation there. If it’s turbocharged, we have to find out how much boost they’re going to make to make their peak horsepower. As you pressurize the intake manifold with your turbocharger or supercharger, you make it harder for that injector to fire enough fuel in at 43 psi. So we raise the fuel pressure. For every pound of boost we create, we raise the fuel pressure one pound, so that 43 always stays technically at 43.”
“Regulating fuel pressure is one of the biggest things in a fuel injection system,” Cegielski said. Where to mount a fuel pressure regulator varies depending on the application. In a street car, “a lot of people will use something like a C5 Corvette filter/regulator—it’s both in one—and they’ll put it back by the gas tank. That’s totally fine for a 400-hp small block or something like that, as you’re not creating too much heat. But when you start getting to higher performance engines, vehicles that have a lot of underhood heat, you want to be mindful of where the regulator is. When you start adding turbos under the hood, it’s better to run fuel through the fuel rails then to the regulator. This keeps fuel circulating so even if an air bubble gets in, it’ll pass the injectors, go to the regulator, and return back to the gas tank.”
Selecting the proper size fuel injector is similar to selecting the right fuel pump, Santarpia said. “Once you discern how much fuel you’re going to need for the amount of airflow you’re going to move or power you’re going to want to make, you can select the appropriate injector size for your application.” But “too much injector can definitely be a bad thing,” he noted.
“Let’s say a vehicle needs a 1,000cc injector to support its power goals. But some people think they should buy the biggest injector out there to have room to grow in the future. Well, the bigger the injector, the smaller the pulse widths are at idle and cruising. It’s a lot more difficult to control fueling and get consistent shot-to-shot consistency of fuel mass at those really small pulse widths.” His advice: “Pick the injector that’s appropriate for your power goals and gives you 15 to 20% headroom, so that way you don’t have an injector that’s super inconsistent at idle and is difficult to get dialed in down low.”
“The volume of the fuel rail is also very important,” Sosa said. “As fuel injector size increases, if the rail volume stays the same, then every time those injectors open, they’re going to have a higher local pressure swing. The pressure locally is going to drop, and those pressure swings may lead to stumbling or can make an engine more difficult to tune. It’s definitely worth the effort to make an upgrade to larger diameter fuel rails or high-volume fuel rails because you’ll be able to better control those pulses.”
All of our experts recommended installing filters at both the inlet and outlet sides of the fuel pump. Their mesh size recommendations were consistent, too. DeatschWerks’ McDaniel summed it up succinctly: “We recommend using a 100- to 200-micron filter before the fuel pump to protect it, and a 5- to 40-micron filter before injectors or carburetor—a 5-micron filter for direct injection, 10-micron for port injection, and 40-micron for carb applications.”
As fuel flow increases, “we have to increase the surface area of the filter element,” Stacy pointed out. “We don’t change the micron rating, but we go to a larger filter. If I were to take our filter that’s rated for 1,000 hp and put it on one of our mechanical pumps, one that could support 3,000 hp, we would crush that filter in the filter housing because it can’t pass the amount of fuel through that small surface area that the pump needs.”
Sosa also noted that the filter element “needs to be compatible with the type of fuel you’re running. When you get into methanol, a lot of guys will run stainless filters with stainless elements, so you don’t have to worry about compatibility.”
What Not to Do
After asking our experts about what racers should do for their fuel systems, we ended the conversations asking about mistakes they’ve seen and problem areas to avoid.
“With fuel pump sizing, you want to make sure that the fuel pump you select is large enough to support your horsepower, but there are downsides to flowing too much fuel through the system,” Sosa said. “One is because you’d need a larger regulator, but you’re also adding a lot of heat to the fuel every time you compress it.”
Sosa also cautioned against using the wrong kind of rubber hose for fuel lines. “To most guys, rubber is rubber. But it’s not. There are certain rubber lines that are meant to carry oil, and if you put fuel in them, they will work, but they’ll deteriorate very quickly.” Look for fuel lines with an SAE rating of J30, “which means it’s constructed with an inner tube made of a fuel-resistant rubber.” Fuel line specific to fuel injection carries an additional R9 rating, he added.
On the subject of lines, “keep fuel lines away from any type of heat source or moving source, like driveshafts or exhaust pipes,” said Cegielski. “Generally speaking, if you try to mindfully follow where the factory fuel lines were on a vehicle, a lot of them were put there because they are away from those types of situations.
“Another big one we run into is builders who want to run hard lines but don’t have the tools to bend stainless steel line, so they try to find a softer material like aluminum,” Cegielski added. Aluminum, though, is not rated for the same pressure as stainless. Plus, “certain metals do not perform well against fuel pulsation. When a pump is running, it creates small fluctuations of pressure, which can crack aluminum. We tell people to go with a high quality, stainless-steel-braided PTFE line or fuel injection hose. If you are going to use hard line, get the best quality parts you can, like stainless steel hard line.”
Santarpia at Fuel Injector Clinic and Stacy at Aeromotive talked about the damage that can be caused by leaving alcohol-based fuels in a system.
“We find when vehicles using E85 sit a long time without running, the alcohol tends to leave a residue on the tip of the injector that, when mixed with moisture in the air, creates this black tar-like substance,” Santarpia explained. “If the vehicle doesn’t run for a long time after that, it can congeal and stick the injectors shut. It’s acting like an adhesive between the valve and the valve seat, and the injector can’t create enough force to open up that valve after sitting for so long.”
“If you leave methanol or ethanol in your gas tank, in your fuel pump, and in your carburetor over the winter, or even over three or four weeks without being started, you will be a very unhappy camper,” Stacy said. “Methanol is very corrosive. People will leave methanol in their pump all winter long, and it will eat the bottom chamber of that pump. And E85 tends to jellify, I guess you would say. It gets thick and gooey. So don’t store any non-gasoline-based fuels over a winter.”
“When it comes to modifying your fuel system, it’s important to do your own research and not rely solely on what has worked for others,” McDaniel said. “While some may prefer to push the limits of injector and pump flow, others may opt for a more conservative approach. By understanding the specific needs of your fuel system, you can make informed decisions that will leave you satisfied with the results.
“Never cut corners,” McDaniel added, “as saving a few dollars on a fuel pump could ultimately lead to engine failure or missed opportunities on the track. If you lack experience in modifying fuel systems, seek the assistance of a professional to ensure that your modifications are properly designed and built.”
SOURCES
Aeromotive Group
aeromotiveinc.com
DeatschWerks
deatschwerks.com
FiTech EFI
fitechefi.com
Fuel Injector Clinic
fuelinjectorclinic.com
Holley
holley.com