PRI Show Report: Back To Business
The Indiana Convention Center and Lucas Oil Stadium in Indianapolis were once again jammed with new performance parts and technology covering all types and levels of motorsports competition.
Yes, new products returned to the 2021 PRI Trade Show.
Following a COVID-19-driven cancellation of the 2020 Show—which may have tabled many development projects—the Indiana Convention Center and Lucas Oil Stadium in Indianapolis were once again jammed with new performance products covering a wide spectrum of racer needs.
From large, multi-brand corporations to budding upstarts, these companies showcased new products for tens of thousands of attendees looking for ways to go fast, reduce costs and improve shop efficiency.
“The Show is going awesome,” reported Reggie Wynn of Precision Turbo & Engine and Turbonetics in Hebron, Indiana, who was on-site during the Show. “I didn’t think it would be this well attended. It has definitely surpassed my expectations, by far.”
“We learned about PRI while doing SEMA for the first time in 2021,” said Amanda Meeks of HC Pacific, which is based in Ontario, California. “I told my boss I’m going to Indy. We’ve got to exhibit at PRI. This has been an even more amazing show for us. We’ll be back next year. We’re hooked.”
HC Pacific has been manufacturing Cleco temporary fasteners for more than 20 years, mostly for aerospace. “But there’s a lot of crossover between aerospace and automotive,” said Meeks. “We haven’t really sold directly to the automotive market. In the past we’ve sold to distributors who sell to automotive. But we want to know this market. We want to know who’s using them in their shops in the race car industry. We’re here to support the industry.”
In past PRI Shows, there often was a prevailing theme that generated character and spirit into the aisleway conversations. One year it was all the billet products; another Show was dominated by large turbos and products built to withstand ample boost. For 2021, there were widespread discussions of the strong, if not record, sales and companies recovering from the COVID-19 hangover of slow supply chains and hard-to-find skilled labor. Other lively discussions focused on the growing EV presence, the RPM Act and, of course, racing rules.
“So by coming to this Show we learned a few things,” noted Dave Werremeyer of Frankenstein Engine Dynamics, Weatherford, Texas. “Like, we have a new small block Chevy product displayed, and we learned from the Show that there’s been a major rule change in dirt track racing. We would be totally unaware of it if we weren’t here. We would have probably never known about it.
“Also, our focus in the trade is basically drag racing and street racing. Now, we’ve had diesel guys and tractor pullers who are asking us about building heads for them,” added Werremeyer. “Market-wise, sometimes it’s easy to become so focused and have blinders on and not see the possibilities. That’s where this Show comes into play.”
New Materials
The COVID break certainly gave one company a chance to expand and fine-tune its disruptive yet relatively unsold product line. Almost three years ago, the industry first learned of AWA Forged Composites’ research into composite connecting rods. Since then, the company has added composite pushrods, rocker arms, lifters and pistons to its prototype lineup, in addition to continued development on the rods.
“We’ve refined the techniques and technology in our connecting rods,” said Bryan Gill of the Rolling Hills Estates, California-based company. “The biggest thing is the revised tooling. With composites, it’s all about the tooling and fiber placement. We’ve been able to do even more computer modeling, more load simulations, more thermal imaging to displace all the loads to the appropriate areas.”
Gill said the rod is stronger and lighter than any other material with higher life expectancy, even for Top Fuel or Pro Mod teams. He has been working discretely with sanctioning body officials on the approval process, emphasizing that even though the up-front costs would be very high to a team, the rods have the potential to last an entire season instead of one or two weekends of racing.
“We actually calculated the current cost is $250 a run, while our product would be about $150 a run if we cut it off at a year,” added Gill.
One of the company’s most pressing issues is sales and marketing. Gill freely admitted that he’s a scientist, not a business person. So he has entered into talks with CP-Carrillo in Irvine, California, to distribute the product. CP-Carrillo officials confirmed the distribution deal but also say extensive prototype testing is underway to ensure product viability in the racing market.
Gill said CP-Carrillo is best suited to determine market possibilities for not only the connecting rods but also the rocker arms, pushrods and other products. Then he would develop the tooling and production schedule to meet sales demands.
AWA’s newest innovation is a composite piston. It features a crown constructed from thermal-conductive material that can withstand 2,000 degrees F. It’s adhered to a titanium ring land that supports the top two rings. The oil ring groove is actually cut into the lower composite skirt section.
“We separate the rings because it can handle the heat better,” explained Gill, who pointed to a prototype composite wrist pin that will lower the reciprocating weight even more. “The rings are cut directly into the composite.”
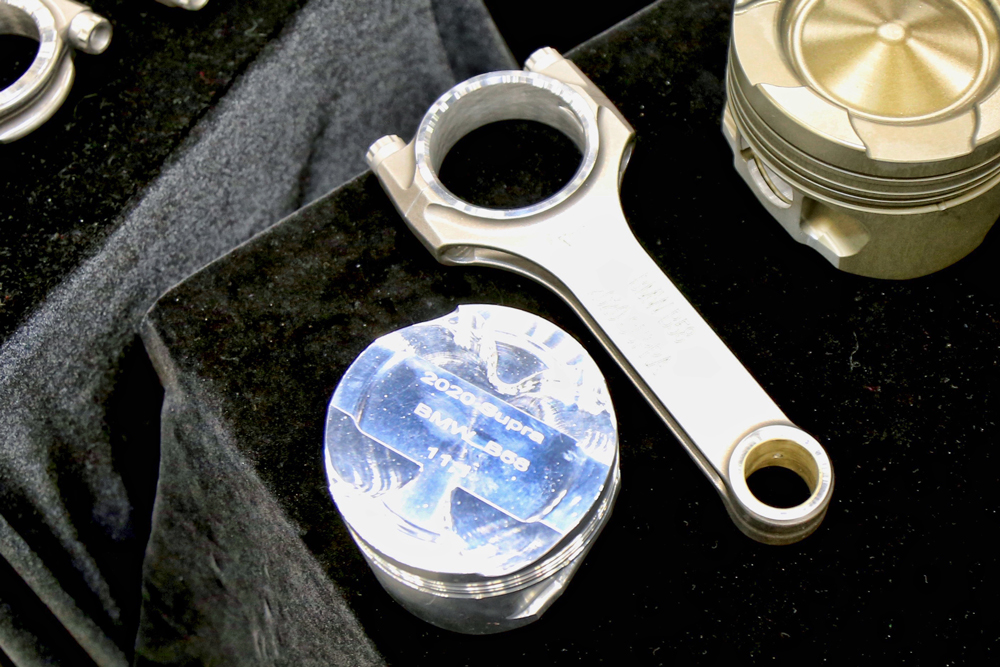
No doubt, high-end racers are eager to hear more about this technology and when product will be available for popular engines. On the flip side, CP-Carrillo already has new pistons for a number of applications, including the hot, new Toyota Supra with a BMW-sourced straight-6.
“That’s really taken off. It’s hard to keep those on the shelf,” said Tony Calvert. “We have a couple different compression ratios. Those blocks are pretty good from the factory, so a lot of people just want the standard bore setup. We also have an oversized bore available. Keeping up the inventory has been the biggest hurdle this year.”
Calvert said the company has brought in new machinery, but hiring skilled labor has been difficult, so adjustments in hiring strategy have to be made.
“In years past, we’ve always looked for experts in the industry, people with CNC experience who love the racing industry,” said Calvert. “Now we’re opening it up to people who really want to learn. If they have the right attitude, that’s primarily what we’re looking for. We can train people, but we can’t train attitude and coming to work every day with a smile and willing to help each other out.”
Hemi Nation
New products for high-demand applications drew some of the biggest crowds. There was a swarm around Dart Machinery’s new Gen III Hemi cylinder block. The industry has been eager for an upgraded block to develop more power parts for the Hemi platform. The block is available with or without VVT, deck height from 9.250- up to 9.285-inch and cylinder-bore options up to 4.250-inch diameter. With a 4.000-inch-stroke crank, that’s a displacement of around 454 cubic inches.
“We fixed a lot of the oiling issues,” reported Nick DiBlasi. “It will be priority main, like all of our race-series blocks. We’ve added material behind the lifter bores because of the shortcomings there on the factory block.”
The block still has the side skirts, but the center three main caps are a splayed four-bolt design—no cross bolts. It will be cast from high-nickel iron with a 220,000-psi tensile strength.
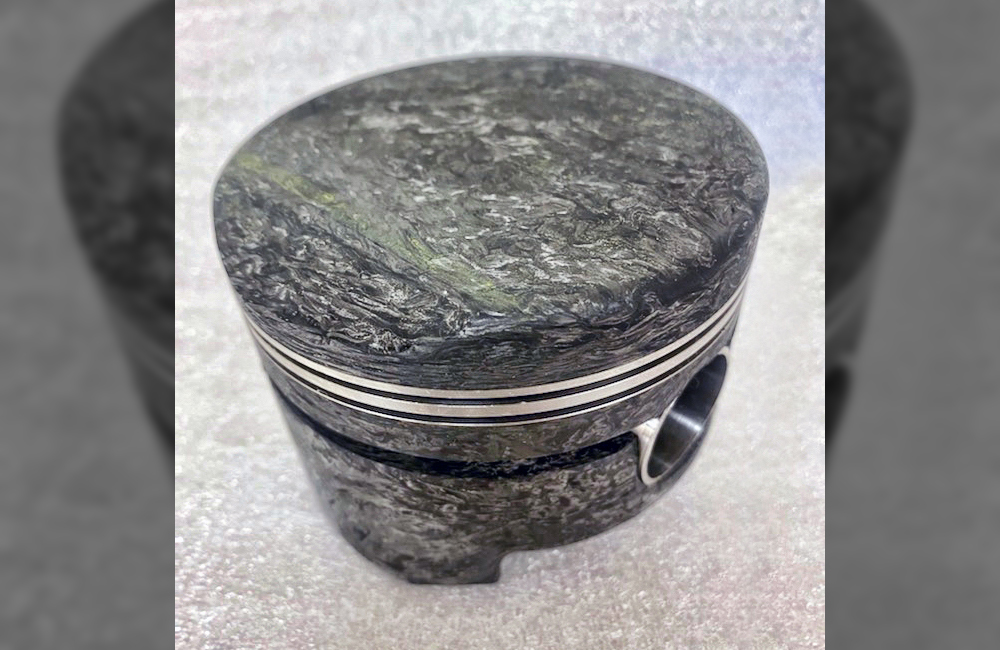
Dart Machinery is part of the Race Winning Brands portfolio, which showed its performance diversity by introducing new diesel connecting rods from BoostLine and powersports pistons from JE Pistons. The connecting rods required purpose-built 12-mm bolts from ARP, which are similar to those used in Top Fuel engines.
“These engines make so much power,” said DiBlasi. “They need more clamping force than a traditional 7/16-inch bolt. The rods are made from 4340 chromoly and have our patented three-pocket design.”
Test engines rated up to 2,200 horsepower were used to validate the rods in 50-hour dyno runs. On the piston side, JE now has Ultra Series pistons for Hayabusa, Kawasaki, Honda and Polaris powersports applications.
“We’re using the horizontal grain flow forgings, which provides about 20% more strength,” added DiBlasi. “People were already making 700 horsepower on a [Kawasaki] ZX14 as soon as we came out with these.”
Big power these days often starts with boost, and Precision Turbo showed off its new Gen II 8080 T4 with an 80-mm turbine and 80-mm compressor. It’s available in multiple housing options and rated at 1,375 horsepower.
“That’s very conservative,” added Wynn. “I wouldn’t be surprised if we could hit 2,000. Most guys need something larger than a 75 mm on the turbine side. We’ve also done the same combination in a mirrored housing setup.”
Twin 8080 turbos with mirrored housings can help with packaging issues and are also more aesthetically pleasing. This package will support up to 2,750 horsepower—also conservative.
Wynn said that even though turbos are getting larger every year, improved compressor aerodynamics allow racers to actually select a smaller turbo. “That is, compared to the wheels available 10 years ago,” he explained. “The smaller wheels today can make more power than a wheel we were selling 10 or 15 years ago because they’re more efficient. A smaller turbo gives the racers better response.”
More Spec Engines
Over at the Chevrolet Performance exhibit, the 572 COPO Camaro had Super Stock racers drooling as there is growing interest in factory racing. The good news is that the 2022 COPO Camaro won’t be sold out as in previous years, when only 69 units were built and there was a lottery system to purchase one. GM will build as many COPOs as are ordered. In fact, Chevrolet won’t offer the 572 as a crate engine in 2022 so that there will be enough for the COPO cars. But in the following year, watch for an announcement.
“When we introduced the 572 COPO, we had a tremendous surge of interest,” explained Bill Martens of the Detroit, Michigan, manufacturer, adding that the initial 35 cars built in the new year will have the 572, and then production of the other engine options will resume.
On the circle track side, Chevrolet Performance is a leading supplier of spec and sealed engines to a variety of dirt track organizations. COVID-19 related challenges had disrupted supply chains and engine assembly in 2021.
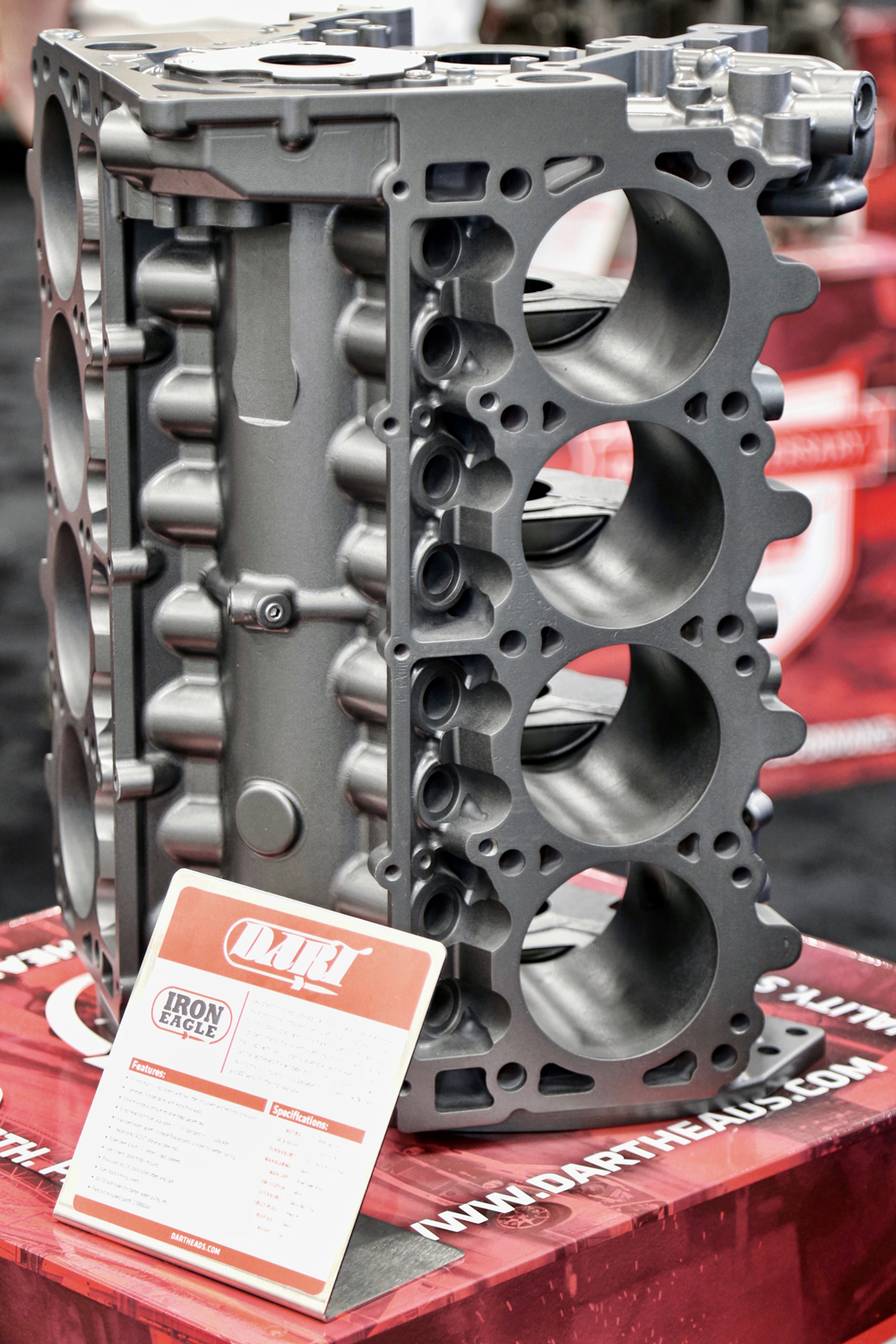
“Now we’re back in production,” said Martens. “We resumed production on the CT350s two weeks ago [in late November], and the CT525 is starting up next week. As far as internal content, we’ve stayed the course and purposely have not changed anything. We want to keep the playing field level.
“There are going to be more opportunities for the 525,” promised Martens. “We’ve got a couple of pending announcements right after the first of the year that some series will be taking the 525 on as their spec engine. That’s exciting, but there’s nothing I can say until the ink is dry.”
New Engine Components
The union of Edelbrock with the COMP Performance Group certainly offers the potential for new racing products over the upcoming years.
“It’s taken two engineering teams and put them together. It’s amazing the ideas that are starting to come up,” said Mike Campbell of Edelbrock Group, Olive Branch, Mississippi. “The Edelbrock Group was really focused on cylinder heads and manifolds. COMP was really focused on engine components, camshafts, valvetrain, fuel injection and transmission. The only real overlap that we have is in some fuel injection, but two totally different systems.”
Edelbrock’s new VRS-4150 carburetor stands out as it’s loaded with many features such as billet four-circuit metering blocks, mechanical secondaries and easily accessible adjustments.
“We looked at all the carburetors on the market and found that none had all of the features in them,” explained Campbell. “So we put in bigger capacity fuel bowls. We have more air bleeds. We got a built-in TPS on the carburetor, and we have a very unique design that allows a smoother transition of air into the carburetor. Just a lot of really unique features that we made better and put them all into one package for a very affordable price.”
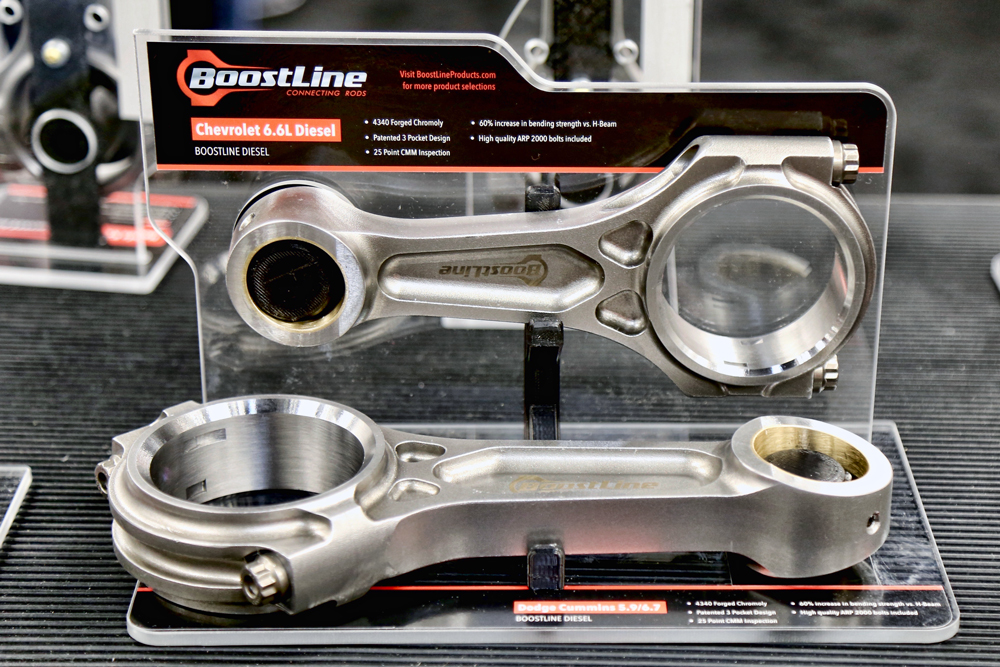
The new VRS line, with four models ranging in size from 650 to 950 cfm, expands Edelbrock’s presence in the carburetor market. The company’s longtime AVS line will not be phased out, as it’s designed for street use.
“The VRS takes it to the next level and fills a market we want service in,” said Campbell.
Holley Performance Products in Bowling Green, Kentucky, released two new low-profile LS intake manifolds, one for cathedral port heads and the other for rectangular port.
“We have engineers that are racers who designed these parts,” noted Mark Gearhart. “So these intakes are available in a single- or dual-injector setup. No welding or drilling or fabricating custom fuel rails. They’re also available with a burst panel.”
Holley also showed off a CAN I/O module that allows users to add multiple sensor inputs to a budget-minded Terminator X or HP ECU, instead of stepping up to the more expensive Dominator ECU. This means that if a racer wants to add shock sensors or before and after air-temp sensors on a boosted engine, they can use the module to expand the I/O capability of the existing ECU.
EVs are Coming
Another market that many of the leading companies are watching closely is electric vehicles.
“We’ve got some ideas, but I can’t say much. We’re certainly looking at it,” said Edelbrock’s Campbell, adding that gas engines are not dying out anytime soon. “We sold more carburetors last year than we did in 2019. Carb sales continue to climb. But, yes, we’re certainly looking at EVs.”
Holley is already aggressively addressing the EV potential by acquiring AEM Electronics, which has developed high-end motor and inverter controls for EV conversions. The company also sponsored the Holley High Voltage Experience in November, which drew as many, if not more, cars than the first LS festival a number of years ago.

“We want to be here to support whatever people do in the industry,” said Gearhart. “We want to help support people who want to go faster. We just want to be there to support enthusiasts. We feel like we accept everyone from truck people to gas, EV whatever, with open arms.”
AEM already has the electronics to swap Tesla drivetrains into just about any vehicle, and the company has been working with the development of newer EVs to stay on top of the technology. Elsewhere in the company, Holley subsidiaries are making wheels and suspension components for the Tesla.
For the first time at PRI, a special section of the Show was dedicated to EV racing. There were electric dragsters, EV conversions and some of the factory EVs from Ford. Lonestar EV Performance has been a pioneer in EV racing and displayed a motor-inverter-rear axle combination that was quite compact and ready for installation into a dragster chassis.
“It’s about two feet long and 1,500 horsepower,” said John Metric. “It can blow off 33-inch drag tires with 6,000 foot pounds of torque. I would say we could get someone into 1,500 horsepower for about $50,000. That would include everything: battery, motor, controller. We also have a 2,000-horsepower model.”
Racers have talked to Metric about the possibility of a 4,000-horsepower package. He’s heard from owners of drag boats and even monster trucks.
“They want to put them in all kinds of vehicles, like a sand rail,” said Metric, noting that exposure to EVs will convince an even larger crowd to consider the potential. “When somebody actually sits in an electric vehicle and drives it, then they get it immediately. It’s a big hit when they’re crushed into their seat from the acceleration. It’s like an out-of-control roller coaster ride. Next, they’re looking at a potential conversion or potential new EV car.”
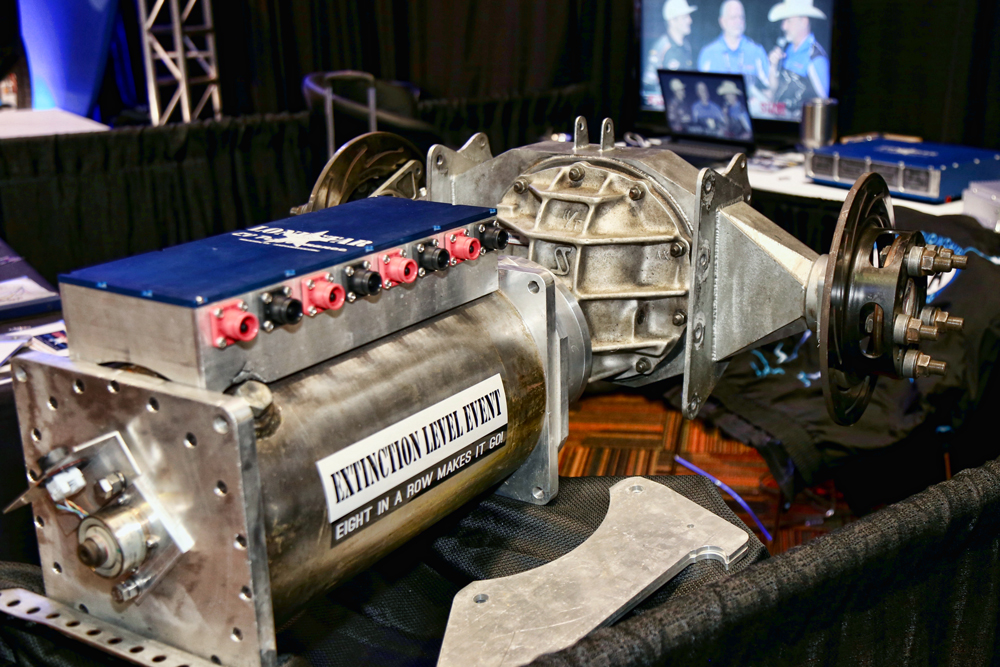
EVs weren’t the only technology representing the green movement. VP Racing Fuels of San Antonio, Texas, announced that advanced bio-renewable components are available for adaptation with its current race fuel portfolio. That means that renewable components may be used in spec fuels for certain sanctioning bodies. The company said there are 70 proprietary fuel blends in VP’s portfolio, and 23 already use some renewable components.
“There are a lot of series that are heading more and more in that direction,” explained Bruce Hendel. “We’re working on developing some of those fuels.”
Hendel said the technology is already available to use more sustainable components but shipping those components from global sources creates more CO2 in the atmosphere.
“We have to be smart, right? Does it make sense to buy them where they’re being produced and ship them over here? By the time the fuel gets to the track it may have created more greenhouse gasses than it will save in the race. So I try to focus on the whole chain of greenhouse gases and CO2,” he explained.
VP did have a new Trigger fluid control system to help racers transfer fuel from jugs to the racing cells. And it was heavily promoting recent products like the Stay Frosty coolant and water-methanol injection solutions.
Machinery Row
In some ways, Machinery Row is not only where the latest in CNC equipment, abrasive supplies, welders, cleaning systems and other race-related shop gear can be seen. It’s also a section of the PRI Show where exceptional fabrication and machine work created by those who use those tools is on display.
John Cowher of Centroid, based in Howard, Pennsylvania, was showing off the company’s upgraded A560 XL 5-axis CNC machine that handles both cylinder blocks and cylinder heads. It was whirling away on an Edelbrock big block Chevy casting as Cowher talked about the more rigid frame design.
“It weighs 23,000 pounds, which is a thousand more than the first version,” he said. “It’s got beefy sheetmetal all around. It’s a tank!”
Cowher said the machine is designed to work at a major manufacturer like Brodix or a trending mom-and-pop race shop because of its versatility in switching between heads and blocks. Then he was quick to introduce Centroid customer Jeff Smith of Late Model Throttle in Waukesha, Wisconsin, who had a well-rounded portfolio of billet items.
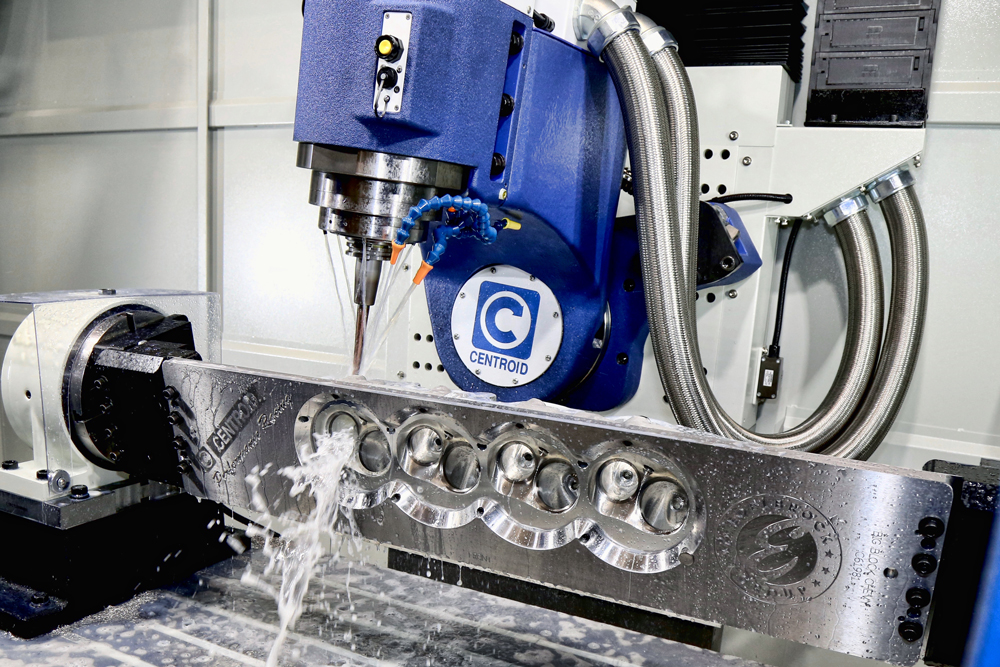
“It helps tremendously with the rigidity of that machine, so we can run it faster. And obviously, time is money,” said Smith, who favors billet parts over casting. “For me it’s the fit and finish of a billet part. I can control every aspect of the process. And it’s going to be stronger.”
One of Smith’s billet parts was an air-inlet housing for a Mopar application that achieved a 25% gain in airflow over a ported stock casting. It also boasted a unique honeycomb pattern that appears as if it were a mesh laid over all the curves of the piece. Another part on display was a supercharger lid for a Ford GT500 that helped give the car a 35-horsepower increase at the wheels.
“The problem with the factory one is that it’s very shallow, and the air doesn’t have the room to grow,” explained Smith. “By just adding the curve in there, it allows the air to move more efficiently.”
Over at the JD Squared exhibit, owner Bob Hughes brought only half of his new product from his Johnson City, Tennessee, headquarters. The XR6 Extreme Rotary tube cutter is adept at plasma cutting intricate details in square or round pipe. In addition to the main section on display, there is also another table that allows work on much longer pieces of pipe. Racers and fabricators are drawn to this equipment because an entire roll cage can be designed and cut in short order.
“A fabricator can wedge-cut the frame and never have to do any manual cutting,” said Hughes. “It’s fully automatic. Our machines will mark the pipe, show how much tube to use and where to bend it. It’s all about how fast we can accomplish each job.”
JD Squared has a goal of supporting its products for a minimum of 30 years, so the company handles all the software development and even makes its own computers. Ironically, the company has many racers as customers, but those customers often buy the machines to use in their businesses that support their racing activities.
“Out of the 12 machines we talked to customers about yesterday, three were race car builders and the others were drivers and owners with construction or similar operations,” said Hughes, adding that during one part of the pandemic he was selling more than 200 entry-level tube benders a month. “Everybody was building stuff at home.”
Machinery Row wasn’t all high-dollar, computer-controlled manufacturing gear. There were pneumatic tools, hand tools, power tools, welders and other assorted shop solutions and supplies. Giant Finishing of Addison, Illinois, provides a large assortment of blast systems, vibratory deburring equipment, tumbling bowls, industrial cleaners and other finishing gear. Racers have been turning to these types of products to achieve a clean finish on the metal.
“They want their parts cleaner and smoother,” said Mark Oryszczak. “Smoother is faster.”
Key to these velvety smooth surface finishes is a line of improved media and abrasives for the different types of equipment. “We have our BHD plastic to lower Ra surfaces in a shorter time,” said Oryszczak, noting that racers like to smooth out connecting rods, valves and other internal engine components. “Smoother will eliminate the stress risers that can lead to cracks or failure, but let’s be honest: Some racing guys just love the bling of a polished surface.”