Spin Doctors
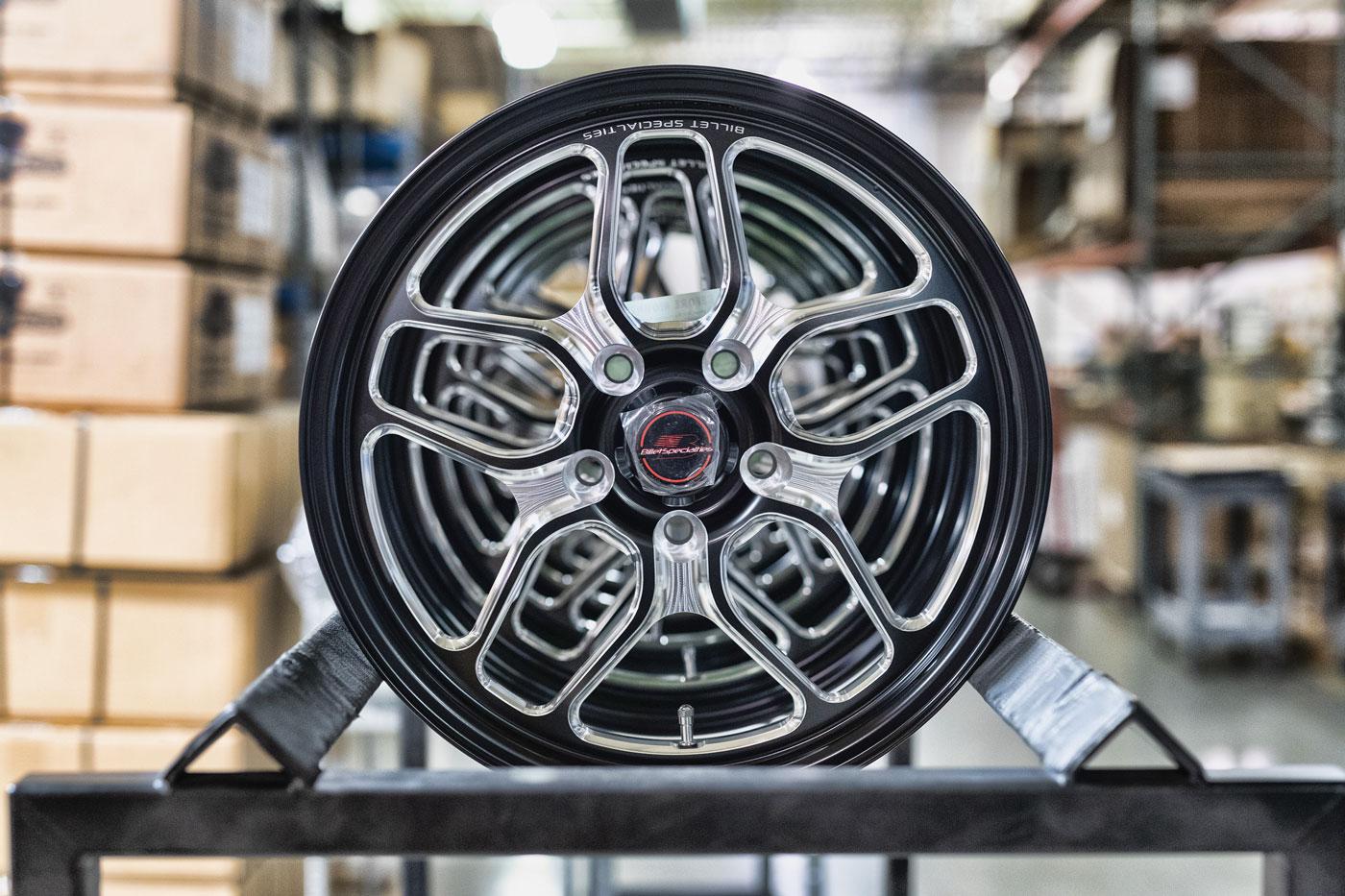
While the basic purpose of the wheel has not changed in more than 5,500 years, more recent advances in engineering, materials, and manufacturing have yielded the lightest, strongest, and stiffest wheels in motorsports history. These benefits carry over to the performance street market, where oftentimes the cars are more powerful and faster (and certainly heavier) than their competition counterparts. For a snapshot of the current performance wheel market, PRI talked to six manufacturers of all sizes. We found a landscape that seems ripe for small niche operations to carve out profitable slices of the market, even as the big players continue to innovate and prosper.
3030 Autosport
Keith Kern and Philip Watson launched 3030 Autosport in Terre Haute, Indiana, in 2020, seeing a need for high-quality forged drag racing and street wheels with direct factory sales. The company name comes from the pair’s 30-plus years of wheel industry experience.
Kern explained that each of the company’s four street and track wheel series is made with a specific manufacturing process to meet the needs of its particular market. Production and material sourcing are all in the US.
“Everything we do is forged 6061-T6,” Kern explained. “All of our stuff is ring-rolled—it comes from a log of billet. That retains the grain structure you get with a forging. After ring rolling comes precision spinning over a mandrel, which always produces the same shape. And we get to move the material, for example, making it thick only where we need to.”
The company’s Drag Ops two-piece 15-inch rear wheels are SFI 15.1 certified, and the monoblock FrontRunners are 15.2 certified. Kern said Autosport 3030 also subjects its FrontRunners to a rotary fatigue test that can account for the abuse that these wheels endure on the drag strip.
“Wheels don’t always come down straight on a launch,” he said. “And there’s a lot of correcting on the strip.”
Drag Ops wheels are certified for street and strip, and available in non-, single- and double-beadlock. “They’re street rated but light enough for drag racing,” said Kern. Beadlocks are also forged parts, which Kern said do not deform when in use like a machined-plate beadlock might. Heli-coil inserts are used for securing bolts.
The modern muscle car market presented different opportunities for street-and-strip applications.
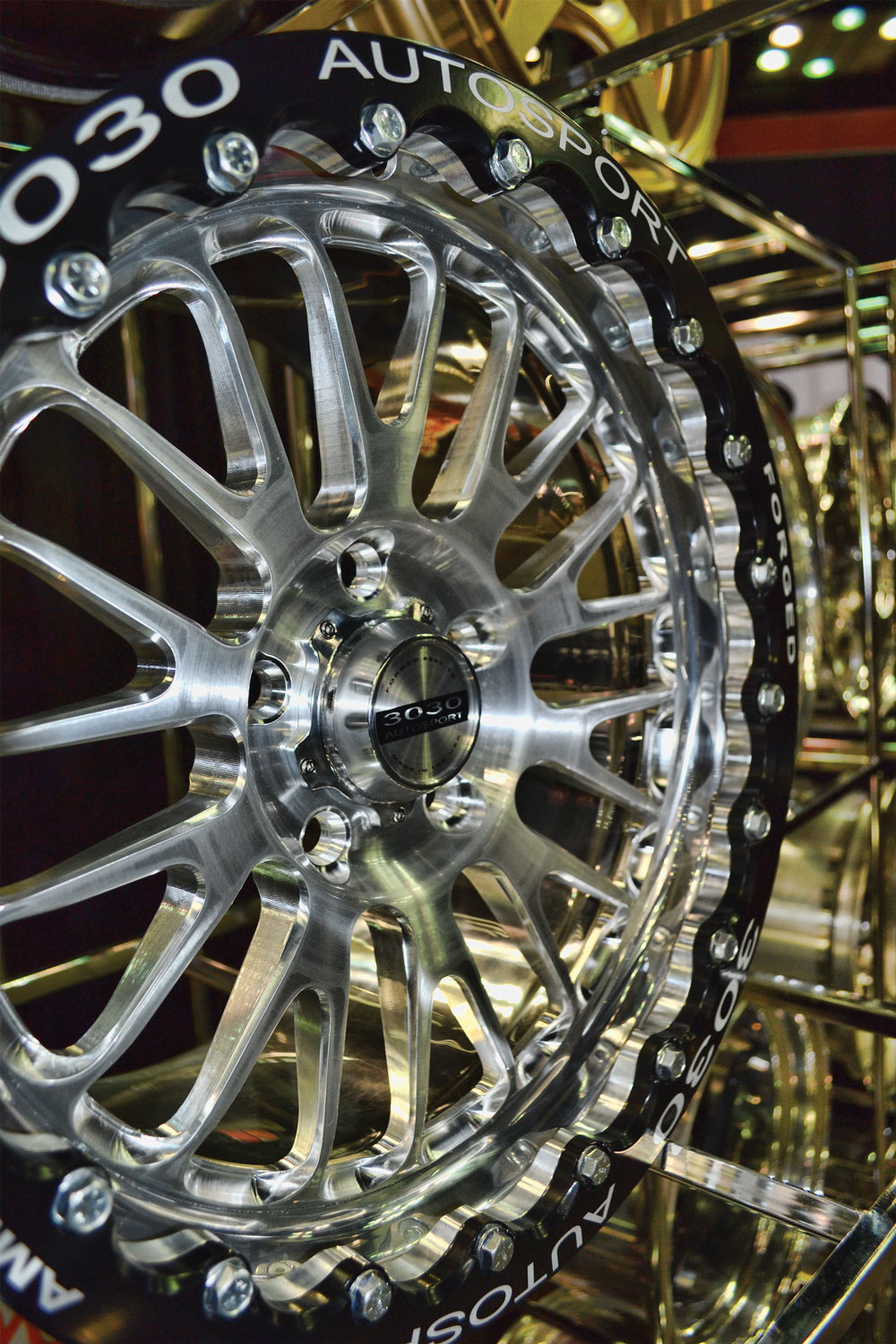
“A lot of these drivers just want to take off the OE 20s and put on drag wheels for some track fun,” said Kern. He explained that the company’s 17x4.5 and 18x5 monoblock FrontRunners and Drag Ops Modern Muscle 17x10-inch wheels are designed so customers don’t have to change the big OE brakes.
Kern described the company’s Series G wheels as an outgrowth of Drag Ops for street/strip drivers who want the OE wheel sizes, up to 20 inches. The Mod3 is a three-piece modular wheel line for street and track, including road racing and autocross. Kern said these wheels, which use a spun outer rim, forged centers and ARP assembly bolts, are tested to an equivalent of pulling 1.2G in a 4,600-pound car for 250 miles.
BBS of America
BBS Wheels, which became famous for its iconic cross-spoke aftermarket and OE wheels in the 1970s, has won more than 250 series championships in Le Mans, IndyCar, Formula 1, IMSA, World Rally Championship and more. For 2022, the company will supply new wheels for F1 and the NASCAR Next Gen (Gen-7) car. Each of these wheels is made with different materials and processes, reflecting the specific needs of its mission.
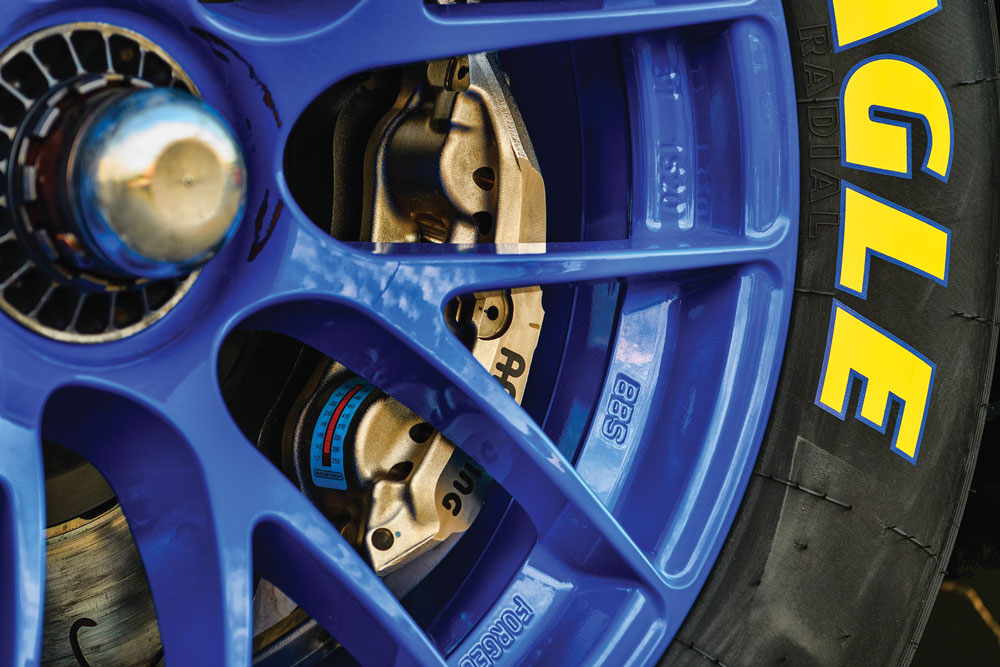
After decades using 13-inch wheels, F1 has switched to 18-inch wheels with lower-profile tires. The new F1 wheel is forged magnesium. “We brought forged magnesium wheels to F1 in 1991,” said Craig Donnelly of BBS of America, Braselton, Georgia, explaining that the material’s light weight and ultimate stiffness were critical in the new, larger wheels.
NASCAR’s radically new Next Gen race car will use 18x12-inch forged aluminum wheels replacing 15x9.5-inch steel wheels used before. They are made with the company’s die-forged manufacturing process. The NASCAR Next Gen chassis is the first in the sanctioning body’s history to use independent rear suspension and center-lock wheels. It will also have more braking power than in the past.
“NASCAR needed a wheel that was lighter and stiffer, yet durable and would withstand the abuse and forces these big, heavy cars generate,” Donnelly said. “It’s a much larger contact patch for the tire, and more mechanical grip. BBS worked closely with Dallara in the area of clamping loads.”
Even while going to an 18x12-inch center-lock configuration, NASCAR wanted the new wheel to be lighter than the previous 15x9.5 five-lug steel wheel. Donnelly said the new BBS wheel came in a pound and a quarter under that. As for durability, BBS is offering a five-year service life on the wheel.
The company’s net-shaped die-forging process, which is used for OE and high-end aftermarket products, was key to achieving NASCAR’s objectives, including its cost target and production volume for all teams. The multi-stage process uses up to 18 million pounds of pressure, according to BBS.
“Most of the shape is created in the forging process, with minimal processing, machining, and heat-treatment,” said Donnelly. “Die forging forces the material to take the shape of a spoke, so the grain structure in the material is more in alignment with where the stress is. It’s just slightly better than with a solid-milled fully forged 6000-series aluminum wheel.”
Critically for cost, the die-forged wheel requires less than 30 minutes of machining time versus several hours per wheel with traditional forging and four- or five-axis machining, according to Donnelly. “We would not have considered any other technology or process for this.”
Donnelly described the project as a unique international team effort, with BBS engineering expertise in Germany and strength in die-forge manufacturing in Japan. Finally, he added that testing for the new NASCAR wheel went “above and beyond the SFI spec.”
BelaK Industries
Marking its 10th year, BelaK Industries in Miami, Florida, emerged from founder Damian Borroto’s experience in drag racing, which began in his teen years. As a racer, he knew the frustration of waiting for wheels to arrive before a race. With 10 employees in three buildings in South Florida, the company specializes in building customizable forged three-piece drag wheels and forged front runners with quick turnaround, Borroto said.
“When we got into the business, we saw a weakness in the market for an ability to meet exact customer needs,” he said. “We’re a smaller company, which allows us to be nimble and flexible. All of our wheels are made to order.” Customers can specify the backspacing and bolt pattern they need and can also choose custom powder coating for a unique look.
All of the company’s wheels are SFI certified and for track use only. Critically, Borroto said the company’s nimbleness has allowed it to identify and move into niches before larger manufacturers do.
“We want to provide wheel packages for customers with brand new cars,” he said.
As examples, he cited the market for drag racing and roll racing the V10-powered Lamborghini Huracán and its corporate and mechanical cousin, the Audi R8. BelaK Industries has an exclusive contract supplying T1 Race Development of Royse City, Texas, with drag wheel packages for these cars.
“We are the only manufacturer that offers an 18-inch wheel with single beadlock that will work on a Huracán or R8,” Borroto said.
In another example of catering to a specific car, Borroto said his company was the first to make a drag wheel package for the new Toyota GR Supra. A brake change is not required to install the drag wheels on this car.
“We listen to the racers and do everything we can to meet their needs,” he said. “We get a car into the shop and tailor the fit. If there’s a clearance issue, we can machine the wheel to fit.”
In addition, Borroto understands his customers’ desire for style and customization. “We want them to look at their car in a new light and love the way it performs with our wheels,” he said.
Forgeline
The supercar and modern muscle car markets have created a strong demand for even more choices in track-only wheels as well as street wheels with true dual-purpose capability. Forgeline Motorsports of Dayton, Ohio, caters to both with a line of forged monoblock wheels.
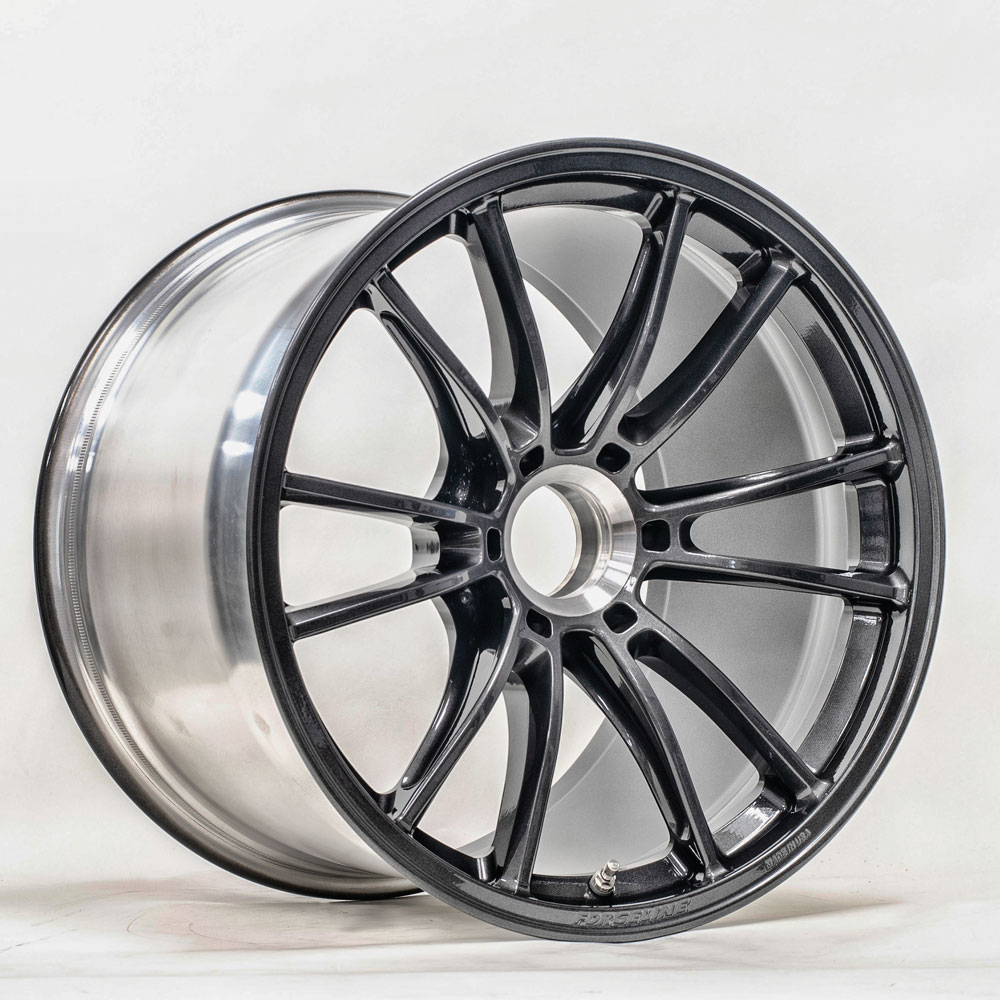
Race wheels are available from Forgeline for the Ford Mustang and Chevrolet Camaro GT4. At the extremes of “street” cars, Forgeline supplies wheels for the Hennessey Venom F5, which has a claimed top speed of 310 mph, and the SSC Tuatara, which set a record of 282.9 mph in January 2021.
“Most of our high-end wheels are tailored for a specific car or chassis—built for specific car weight and downforce,” explained Dave Schardt of Forgeline. He highlighted the new SS1R GT wheel developed for IMSA and WEC GT3 racing as the lightest, stiffest, and strongest wheel the company has ever made. A street-certified SS1R version is engineered for road and track. Both are forged monoblock wheels. The key differences lie in machining, according to Schardt, who said, “The milling process for the true race wheel takes about five hours, and the SS1R takes about two.”
While touting the light weight of both wheels, Schardt addressed a critical trend in road-racing wheel development that may surprise some, especially in the street camp that does track day driving: It’s not always about ultimate light weight.
“Teams would accept more weight for increased stiffness,” he said. “That trend started about seven to eight years ago. With aero producing so much downforce, the stiffer wheels can yield faster lap times. There’s less flexing, better reaction. Suspensions are so good, and tires are getting stickier all the time. Drivers can actually tell stiffness in the wheel.”
Material choice and the manufacturing method are key to getting that stiffness with very low weight. Schardt explained that all Forgeline race wheels are 6061-T6 forged, using a proprietary mixture that he said is 20–25% stiffer and stronger than regular 6061-T6. “We pay a higher premium for that,” he said. “It is all sourced in the US.”
Schardt added that achieving maximum stiffness with low weight also depends on cutting-edge finite element analysis (FEA). “We have so much data from 20 years, including our wheels and others, along with wheels that broke,” he said. “Using FEA, once we have the wheel stiffness we need, we’re able to take out material where it’s not needed. For example, we’re not the first to do I-beams in spokes, but it’s a great way to increase strength with less weight.”
Real Racing Wheels
Frustrated with the way somebody else makes something? Do it yourself. Troy Boubin said Independence, Iowa-based Real Racing Wheels began in 1992 when his grandfather, a tire distributor for American Racer, became dissatisfied with delivery times from a large wheel manufacturer.
“His goal was to provide racers with a quality race wheel and a minimal delivery time,” Boubin told PRI. The business organically grew into a niche to provide wheels exactly to racers’ individual specs.
“We can make pretty much any off-road type of wheel, including for dirt track, tractor and truck pulls,” explained Boubin. “We have the tooling to make large and small orders. We do not mass-produce. We have no minimum quantity.”
The “Real” in the company name stands for “Racer Engineered Aluminum.” While most of the wheels are indeed aluminum, the company also makes 15x8-inch steel wheels for modifieds. Street wheels are not offered.
Product development is driven by what customers ask for, according to Boubin. He said racers come to Real Racing Wheels seeking specific backspacing and bolt patterns they cannot get elsewhere. Other needs are driven by changes in brakes, suspension, and tires required by racing series. “For example, when a new tire comes out in pulling, everybody calls needing a wheel for it,” he said. “We also keep our ears to the ground on trends in the market.”
Most the company’s wheels are spun by hand, except for some of the larger-diameter wheels that are CNC-spun. Boubin cited advantages to hand spinning, including quick changeover for making different wheels.
“It really is a disappearing art,” he explained. “It is very labor intensive, but our guys can see if there’s a defect in material, or if something is not right in the heat-treating. Quite a few have been with us for more than 15 or 20 years.”
Likewise, the polishing is laborious. “It’s a tough, dirty job but is so critical,” said Boubin.
Expertise in short runs of specialty wheels has attracted customers to Real Racing Wheels from around the world. Boubin said the company has made wheels for sand-drag racers in Dubai and the United Arab Emirates, ice racers in Iceland, and for military all-terrain vehicles in Alaska.
He revealed that the most unusual request came from NASA, which needed development wheels for the Mars Rover early in the program. “None of our wheels went to Mars, though,” he said. “They were used for the mock-ups.”
Vahlco Wheels
A relatively new name in the racing wheel market, Vahlco Wheels of New Egypt, New Jersey, emerged from race team owner’s Fred Vahlsing’s purchase of Valken Wheel company in 2014. The company has focused on oval track racing—dirt sprint, dirt late model, Northeast modified, and asphalt sprint—and recently expanded into drag racing.
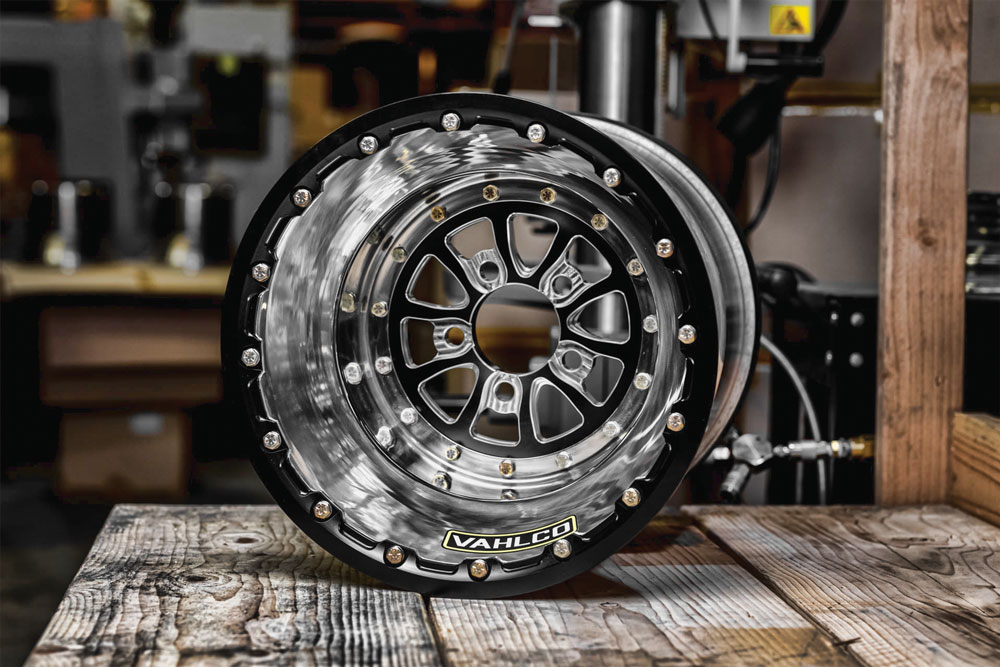
specialize. Vahlco Wheels focuses primarily on oval track, but has recently launched
a drag-racing line.
Dave VanHorn, who runs operations at Vahlco, is a third-generation dirt racer who currently drives a Northeast dirt modified, including at the local 7/16-mile dirt track, New Egypt Speedway.
VanHorn said that, while always seeking light weight and high strength for its wheels, the company makes durability a top priority, no easy feat for such brutal race conditions.
“Most dirt oval racers are racing 100 times a year, and the wheel has to hold up for that,” he said. “The Saturday night guy needs a wheel to last three to four years with no issues.”
Vahlco’s wheels use CNC-spun 6061-T6 rims and forged centers. “They are within 20 thousandths true,” said VanHorn. Emphasizing the company’s attention to heat-treatment, he added, “The temper part is the secret to all wheels for getting the correct stiffness.”
VanHorn said the company is always seeking to give racers the best product possible, with good value and durability. For example, the sprint car wheel centers were recently upgraded to 2024 alloy, known for its high strength-to-weight ratio. For its 10-inch midget racer wheels, Vahlco now uses a magnesium center. “We have a lot of teams in Australia and New Zealand using those, and they have been very successful,” said VanHorn.
Vahlco engineers wheels in the US and sources forged centers from California. The CNC-spun rims are produced by a manufacturing partner in South Korea that VanHorn said has 30 years of experience. “We work closely with them on the processes,” he said.
Beadlock rings are made in Vahlco’s New Jersey home base, where wheels are assembled, packaged and warehoused. VanHorn said the company is doing more in-house manufacturing than before, which helps to get orders out more quickly.
For drag racing, VanHorn said Vahlco saw a need for a certified wheel in amateur divisions, and now the company is also seeking SFI 15.1 certification for faster classes.
He explained that the key for the drag wheels is getting the weld-on beadlocks correct, depending on the weight and horsepower of the class. In oval racing, he said the company has become renowned for its fully machined billet beadlock system, using its own bead grip technology.
Sources
3030 Autosport
3030autosport.com
BBS of America
bbs-usa.com
BelaK Industries
belakindustries.com
Forgeline
forgeline.com
Real Racing Wheels
realwheel.net
Vahlco Racing Wheels
vahlco.com