Beyond the Anvil
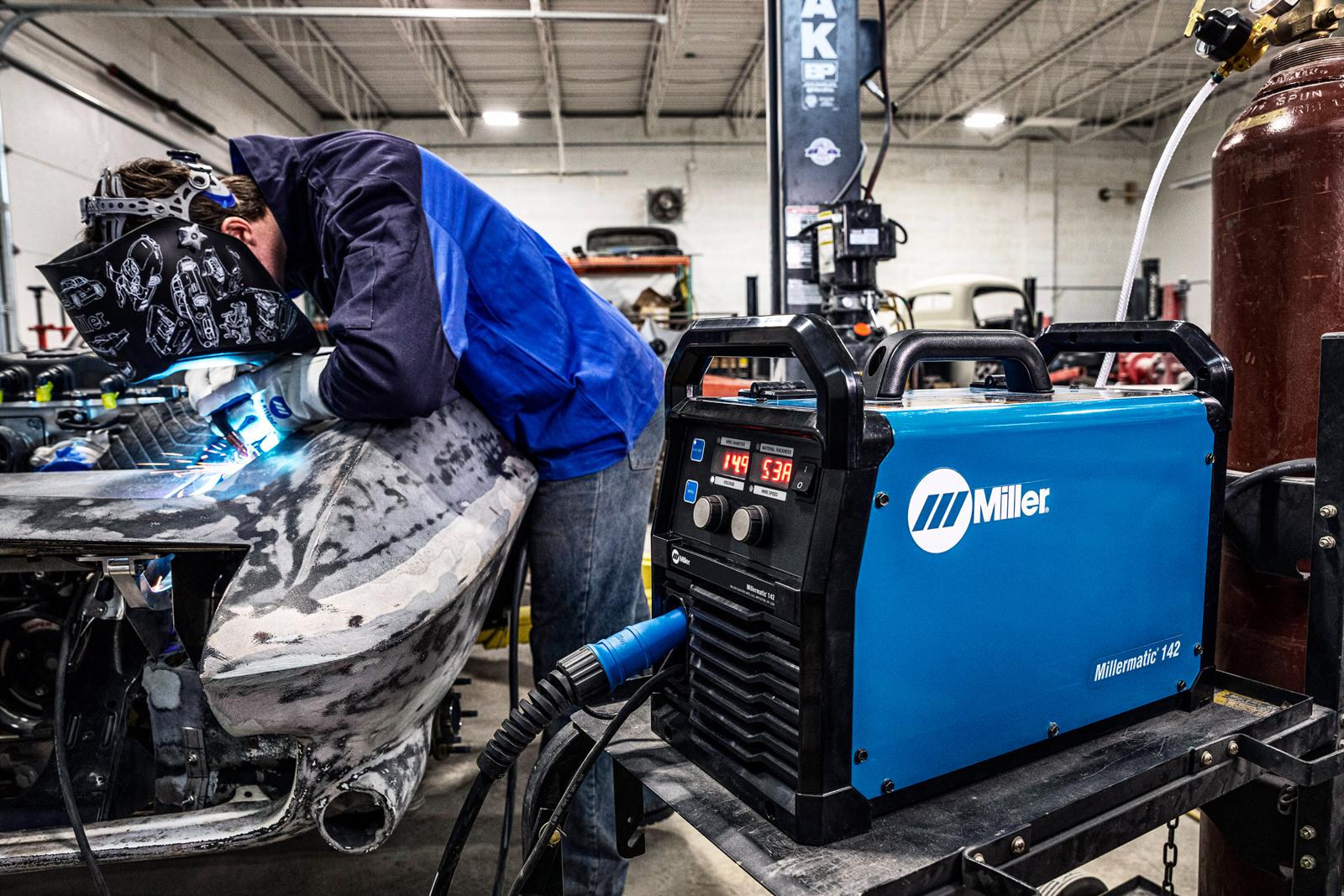
Photo courtesy of Miller Electric
Current cutting-edge trends in metal fabrication and welding are focusing on more compact designs, automation, and improved efficiency.
If there appears to be a rekindled interest in metal fabrication around automotive custom shops and race garages, especially from younger want-to-be craftsmen, then consider the prominent role of social media.
“You’ve got these old-school guys like Gene Winfield who didn’t mind sharing their skills,” explained Phil Heck of Woodward Fab, a division of Heck Industries in Hartland, Michigan. “But he’s rare. Most of his generation were pretty secretive about how things got done in the shop. They didn’t leave the doors open so people could wander in and see what they were doing. Now everything’s being shared on YouTube. What might have been a secret years ago is now common knowledge. There’s just so much stuff on the Internet that demonstrates how easy it is for anybody to do this work.”
In following this promising renaissance within the industry, Woodward has released two new English wheels, including a benchtop model that reflects one of many noticeable trends that’s promoting smaller equipment in fab shops.
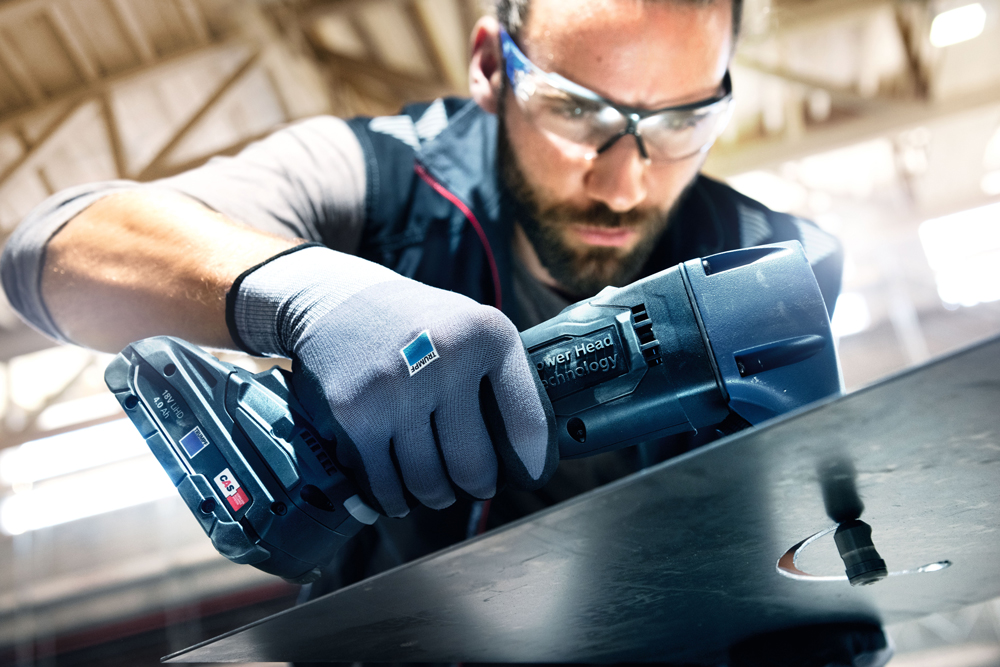
“It’s actually designed in Australia. Originally, we thought it was a silly thing, but my customers explained that getting into tighter spots sometimes required the need of two English wheels,” said Heck. “I know we’ve had some customers that travel conducting classes and seminars, and I think they put this in the trunk of their car.”
Woodward specializes in metal fabricating and forming tools, offering products from $15 up to $15,000. While many factions of the industry are moving toward automation, Heck said his customer base is different.
“They’re working on a prototype or one-off basis most of the time,” he said. “For some of our tools, they can be manual or power. Manual is often preferable because it’s more controllable. Also, it’s impossible to make an English wheel or planishing hammer automated.”
Increased Automation & Robotics
Increased automation and the growth of robotics in the fab-tool industry is being driven by numerous factors, including the need for increased production at some shops in addition to continuing struggles in the labor market.
“As technology becomes more available and affordable, and labor becomes harder to come by, you can drive those two points closer together. So, automation is something that a lot of people are looking for, especially from bigger shops where they do a lot of volume,” said Bruce Van Sant of Trick Tools and Van Sant Enterprises, Pella, Iowa. “We’ve been selling more in the line of CNC tube benders, and this year we have a full three-axis CNC bender because there’s so much interest in that type of equipment.”
Manufactured in Germany by Transfluid, the CNC bender can churn out headers, roll cages, and other tubular parts up to 3.000-inch OD in 10-foot lengths. One of the keys to implementing such an expensive machine in any shop is proper training of the employees who’ll operate it.
“We’ve seen improvements in software and programming. There’s even collision-avoidance simulation. It will show a simulation of the bending on a screen to make sure you don’t have any problems or conflicts,” said Van Sant, adding that the ROI can depend on many factors. “We’re not trying to replace humans, but there’s more need for automation because of labor shortages and less availability for hiring people.”
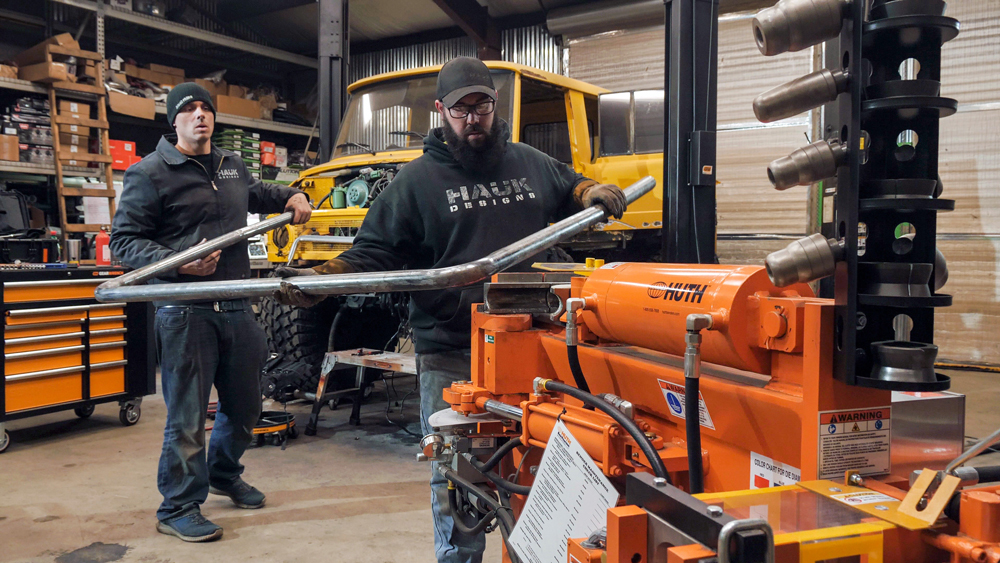
Bend-Tech in Osceola, Wisconsin, helps shops improve build times with its CNC tube and pipe plasma cutting machines. They can fabricate designs with holes and end cuts, plus mark all bending locations, rotations, and degrees on the pipe.
“Our product assists in automating the shop’s processes,” said Kyle Merry. “Our CNC tubing pipe processors are able to cut out all of your profiles, mark your part identification and your fit-up locations, and also give you all of your bending information as well.”
Models include the Dragon A250 that can handle four-inch-diameter round tubes up to 21 feet long, or there’s a smaller model designed for tubes up to 12 feet. The Dragon A400 handles 24-foot materials—including square, rectangle, angle, and channel—up to 6 inches in diameter and has a maximum capacity of 400 pounds.
“One of our shops recently said they took their projects from a three-week build to a one-week build,” added Merry. “We’re actually able to calibrate a bender and die in our software and give you your real bending instructions. For example, a 12-inch leg with a 90-degree bend in another 12-inch leg—that’s not a 24-inch part, right? Material stretches and it springs back. We actually take all that into the calculation and put the real bending information on the tube for you.”
Tubing benders are a specialty at Hartford, Wisconsin-based Huth Benders, which offers Huth and Ben Pearson models in a variety of sizes and capabilities to meet the demands of different metals, intricate bends, and new end-forming proficiency.
“Stainless steel is always an area of interest, because it can be tricky and kind of a bear,” said Ken Murray. “But we’re also doing the tube forming to help them put tubes together. A shop may source mandrel bends from somewhere else, but they still have to put them together, and they need a tool that works really fast.”
One popular tool is the 1674 broad-range tube expander that can produce 25,000 pounds of expanding power through the 3.5-inch cylinder and 49,000 pounds through the 5.0-inch cylinder.
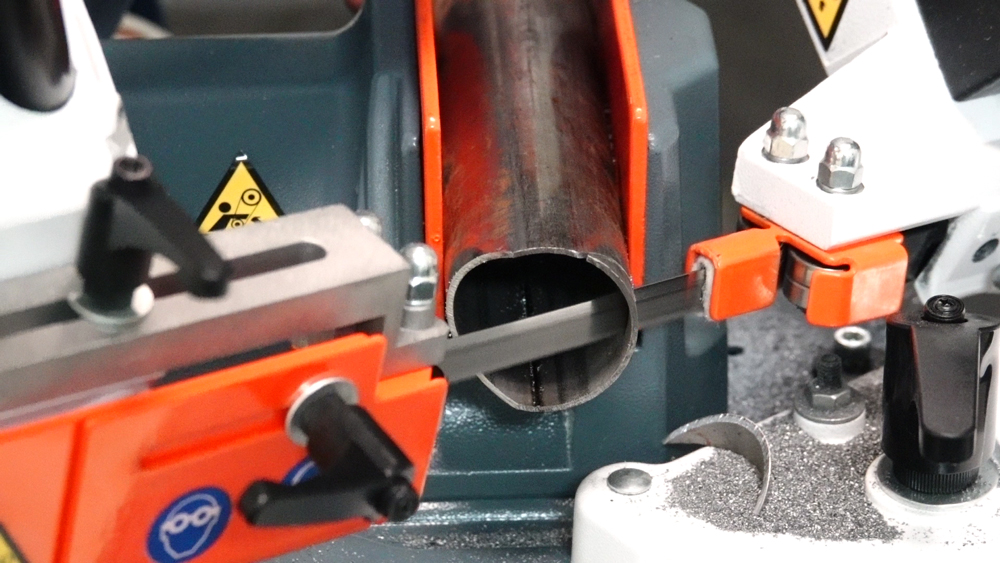
“It has two heads. Guys might be working with bigger stuff or a couple of different sizes, and they don’t want to do tool changeovers,” said Murray.
While saving time and money is on the minds of Murray’s customers, his product development strategy may seem cautious in an industry where technology is driving forward at a fast pace.
“How can I do it quicker and better depends on who, right? It depends on whether it’s a small manufacturer who’s looking to produce more efficiently, or an operator who’s actually doing his own stuff. Those are different worlds,” explained Murray. “We might be a little slow on the automation because we’re dealing with smaller guys, not the huge shops that need a CNC approach. We do have some models that incorporate PLCs [programmable logic controllers], and we’ll be doing more of that as we go forward.”
Robotics is another advancing technology edging its way into the industry to help counter labor shortages and improve production. Training and programming are also key considerations in those purchase decisions by a fab shop.
“We’ve come out with a new robot called the Copilot that is very user-friendly,” said Andy Weyenberg of Miller Electric, Appleton, Wisconsin. “People may shy away from automation because it’s expensive, but the big problem is trying to find somebody who can program it.”
The Copilot’s advantage is that programming time can be as little as 15 minutes. In the past, programming for a run of five or 10 parts could take longer than the actual production.
“You can teach it simply by moving its torch to the piece. When you’re in the learning mode, you can press a button to set a start point, you can move the torch down and set another point, and that would be your ending point. I mean, basically an 18-year-old kid and a 68-year-old man could have the thing programmed in the same amount of time. It’s just super user-friendly,” explained Weyenberg.
Another company promoting advanced welding stations is TRUMPF based in Farmington, Connecticut. Its TruArc Weld 1000 is a fully equipped tool that includes an exhaust system and other critical safety equipment.
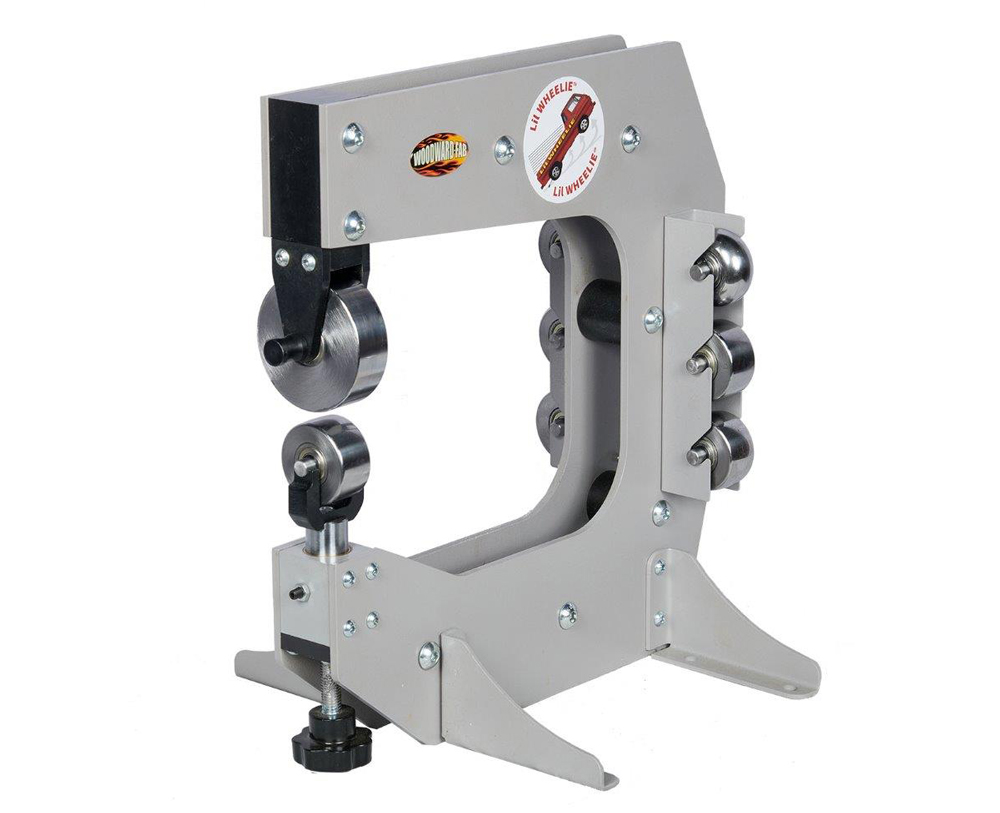
“Two of the biggest benefits for a performance race shop are speeding up high-quality production and freeing a shop’s skilled welders to focus on more complicated tasks,” said Tommy Zoladz. “The TruArc Weld is so easy to use that anyone on the shop floor can program the machine and run it, even without much welding experience.”
Zoladz also said automation helps create consistency in welds, which is a selling point in the aftermarket. The station is also designed to allow the operator to load or unload one side while the other side runs production. On the smaller side, TRUMPF offers a cordless 18-volt TruTool N 200 nibbler.
“It’s probably our most popular tool at PRI,” said Grant Fergusson. “Race shops can make templates and easily do repeats on regular parts. They can also make cuts outside the shop since the tool is cordless and fast. Also, it does not create sparks or dust, which makes it safe for working around fuels or oils.”
Time Savers
There are other trends in the industry that suppliers are noticing. Miller Electric has a new Millermatic 142 welder that features an inverter engine, which has been a staple in the larger units, yet it is small and lightweight, runs on 120 volts, and still offers a 60% duty cycle.
“So it’s not just a hobby machine with that kind of rating. Inverter engines open you up to a lot more versatility in your welding processes,” added Weyenberg.
Welders at race and fab shops are getting a lot of love these days, and not just from advanced technology. Miller has the ArcStation series of tables, including a small folding unit with a thick metal top and larger models with wheels that can easily be moved around the shop.
“It’s very relevant to our industry because it’s hard to have a nice, sturdy platform with 500 pounds capacity at the race track that doesn’t take two men and a small boy to move,” noted Weyenberg.
Over at Trick Tools, modular fixture tables have grown in popularity. “We saw a lot of welding tables where everybody used to have dedicated jigs for each part they needed to build,” recalled Van Sant. “Now the systems are much more modular and can be reformatted and repurposed for different things. So you can have one table that gets quickly changed over from one part to another. This allows for more customization and personalization for chassis builders.”
As a result of COVID-19, some shops had to downsize, whether due to loss of sponsorship or lack of racing opportunities during the pandemic. That prompted some fabrication equipment manufacturers to offer versions of their products with a smaller footprint.
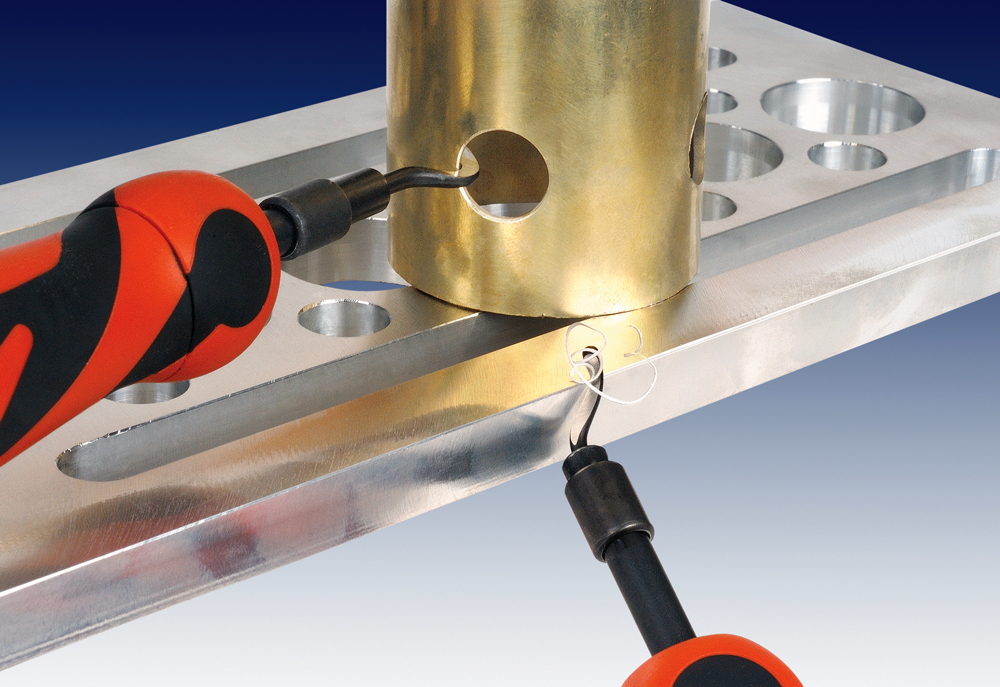
“They’ve had to utilize their space more efficiently, because maybe they’ve brought multiple race cars in one program and had to combine shops. So space is always a consideration,” explained Paul Beha of HE&M Saws, Pryor, Oklahoma. “That’s where our bench-top saw series comes into play. They don’t take up much room, but they have a lot of benefits.”
Just in the portable bench-top series, HE&M has eight models available. “It’s basically what fits the customers’ needs. The 782, which is the smallest model, will stand upright and can be utilized as a vertical saw. Some people have that need,” said Beha. “The other thing would be capacity. Some saws there have a 6-inch capacity, some have a 4- or 3-inch.”
The small saws also have dry-cutting ability, so there’s no mess, and they can be utilized at the track where there will not be any environmental problems with the fluid. At first, the small saws were not a hit with the company brass, which was happy selling larger industrial saws. However, at automotive venues, the big saws were not an easy sell. Beha then tried out a line of smaller saws made in Italy.
“I couldn’t believe how fast you can cut a solid piece of steel in under 20 seconds,” he recalled. “The blade doesn’t even get hot. The two things that fatigue a blade are vibration and heat. And the design of these saws, for example, the NG120 and several of the other models, have 10 roller guides surrounding the blade on two sides and the top. So they’re securely held, they’re dry cutting. And the precision is amazing. We can cut slices .005-inch thick, and they’ll remain true top to bottom.”
Not all advancements in fab tools have come in big-ticket items. Bad Dog Tools in Bristol, Rhode Island, recently released 5.0-inch flat and 7.0-inch flange versions of its HDII line of Endless flush grinding and cutting wheels.
“DeWalt just came out with a new 7-inch FlexVolt angle grinder, and it’s a super-cool combination with our Endless cutting wheel,” said Ann Strong. “It has cordless ability, and you have 6 1/4 inches of cutting depth. You can do frames, body panels. It’s great for metal, carbon fiber, fiberglass, Plexiglas. Even if it’s concrete and you have to grind down the apron in front of your garage.”
The flange version allows for flush sanding and grinding. For really tight spots, Bad Dog has cutting wheels down to 1.25-inch diameter.
“I have a mid-engine Porsche 914. Once I had to cut a bolt off the engine. I don’t know if you’ve ever seen the engine compartment on a Porsche 914, but it’s not for the faint of heart,” recalled Strong. “We used the inch-and-a-quarter to reach down and cut that bolt. You could not do that with a larger blade because it just would not fit. So, each of the versions of the HD2 has its own sort of niche, tools that it works on or operations that it can do. We always advocate using the right tool for the job.”
Finesse
While hardcore cutting and grinding may seem like very aggressive and heavy-handed actions in the shop, there are elements of finesse required for some racing operations. Richard Orlikowski of Goodson Tools and Supply in Winona, Minnesota, pointed to clutch grinders who are looking for more accurate products to help them maintain consistent launches.
“They want to keep all of those things the exact same, so they need a grinding wheel that’s going to give them the same finish for each and every pack that they have,” said Orlikowski, noting that Goodson sources a very specific CBN abrasive stone in two sizes just for that market.
Recently, Goodson has expanded that focused strategy for the wide-open market of sanding belts. The company now purchases jumbo rolls in bulk and then cuts them down to specific sizes for each customer base.
“If they have some weird, old size that they’re looking for, we make them custom in-house, so the belts are usually out within two to three days,” said Orlikowski. “Everybody wants the brand-new stuff. But some of the older tools and machines still work great. The problem is everybody’s discontinuing the product lines for those machines. So, we are still able to make the grinding and sanding belts for those machines, because we don’t have stock sizes. We make whatever size you’re looking for. It’s benefited those guys because they don’t have to spend the money to buy new machines and new supplies.”
As noted earlier, many factions of the industry are seeing the need for more compact or miniaturized products, and Goodson is trying to keep up with many of those demands from race and fab shops.
“The newest stuff in machining seems to be getting smaller. You’re not seeing a lot of the three-eighths and eleven-thirty-seconds stuff anymore. Everything’s going to five mil or four-and-a-half mil. Some of the equipment needing to be repaired is all smaller dimensional,” said Orlikowski. “It’s making it harder for us to try to find those specific tools that the customers are looking for.”
Even with automation and more precision in the fab shop, there remains the need for simple hand finishing with basic traditional tools. Shaviv USA in Bolingbrook, Illinois, offers a wide variety of deburring tools that have been used for decades.
“Over the years, there have been plenty of advancements in the cutting of metals and other materials directly from machining. Unfortunately, no matter how precise the fabrications seem to get, no one has yet to perfect machining to a degree where our tools have become obsolete,” said Nick Prohl. “On brand-new production parts, even the slightest burr can cause fittings to misalign. Rather than redo these parts from scratch, we offer the quick and cost-efficient solution that many shops rely on.
“You also have to take into account that a lot of fabrication and work takes place not just on newer builds, but older rigs in the automotive sector,” added Prohl. “There has always been a great restoration aspect that goes hand-in-hand with what we do. We help ‘finish’ that workpiece.”
Sources
Bad Dog Tools
baddogtools.com
Bend-Tech
bend-tech.com
Goodson Tools & Supplies
goodson.com
HE&M Saws
hemsaw.com
Huth-Ben Pearson
huthbenders.com
Miller Electric
millerwelds.com
Shaviv USA
shavivusa.com
Trick Tools (Van Sant Enterprises)
trick-tools.com
TRUMPF
trumpf.com
Woodward Fab (Heck Industries)
woodwardfab.com