Head Knowledge
Advances in design, materials, and construction methods are producing helmets that are safer, more comfortable, and more versatile than ever before.
Like many aspects of motorsports, helmet design is largely a balancing act between features, function, and cost. If one of these aspects is allowed to run wild, it typically comes at the detriment of the other two, and that makes breakthrough innovation a tricky proposition.
But thanks to advances in development and production technologies, helmet manufacturers are finding ways to innovate that simply weren’t feasible a decade ago. As a result, racers are getting advanced protection that’s increasingly dialed in to their specific needs.
“Today we’re using software like Fusion 360 and Solidworks for development, and 3D printing tech for prototyping,” said Gary Peters of Simpson Race Products, New Braunfels, Texas. “It really speeds up the development process, but we also still use clay modeling for some ideas. Sometimes that ends up being a quicker way to create something or make a change. The construction materials have evolved significantly in recent years as well, and those have led to improved manufacturing methods with more consistent results. For example, in the past we used composite fabrics, and we would coat in the resin by hand after each piece of material was installed. Now we’re using more pre-preg materials, and that reduces excess resin in between the layers, which results in lighter shells with better fit and finish.”
Technical advances have also ushered in other improvements in aspects like aerodynamics and visor sealing, and that in turn has allowed manufacturers to put a greater focus on comfort and modularity while still ensuring that their products meet the latest safety standards.
Plush Appointments
While safety is ultimately the top priority in helmet design, comfort is also a core development focus. Because of racing’s physical demands, and the inherent need for a snug-fitting helmet to provide effective protection, manufacturers are continually on the hunt for ways to make wearing a helmet a less cumbersome affair for racers. Over the years, that’s brought features like air venting and interchangeable cheek pads into the fold, and as Steve Russell of Pyrotect in Redmond, Oregon, explained, manufacturers are now taking those concepts a step further.
“We’ve now designed the inner liner of the helmet into a four-pad system, so you can essentially re-size the helmet to get an absolutely perfect fit,” Russell explained. “You can change any one of those pads, or all four of those pads, with different thicknesses to essentially tighten or loosen the helmet as needed to better fit the shape of your head.” Separate from the interchangeable cheek pads, this four-pad system focuses on the crown of the head to additionally improve fitment.
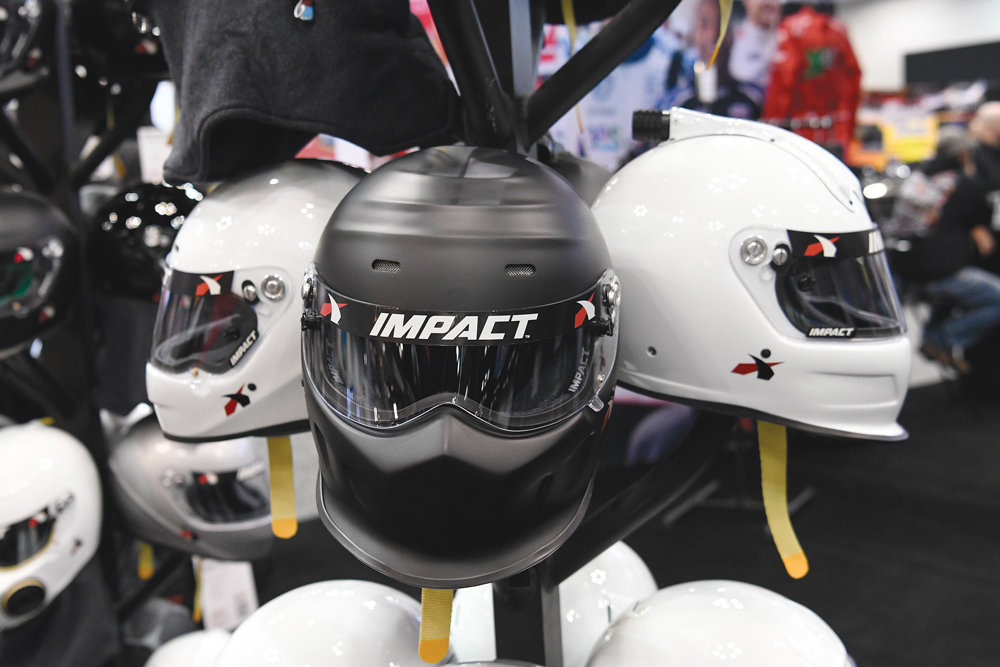
Danilo Oliveira of G-Force Racing Gear in Acworth, Georgia, noted that the company has adopted a similar approach across its helmet lineup. In an era when the majority of helmet purchases are made online rather than in-store, this adjustability made it much easier for racers to purchase a helmet that feels custom-made.
“Someone might find that a medium-sized helmet is too tight, and a large helmet is too loose, so they don’t really have an ideal solution either way,” he said. “With a system like this, we can suggest trying the large helmet with more padding or using the medium with a little less padding. Sometimes it’s not the shell of the helmet that is the issue, it’s the padding inside. If we can provide the opportunity to the customer to make those small adjustments, it can really improve things if they’re in between sizes. Two millimeters can make a difference when it comes to comfort.”
Russell said that while Pyrotect was developing its crown pad system, it also took a closer look at how air flowed into and out of the helmet to further improve comfort.
“Years back, at the very top of the inside of the helmet, you’d have a smooth crown pad and a smooth headliner, and some manufacturers would pump in air through a couple of ports at the top of the head, but the air had nowhere to go,” he explained. “You’ve got to have air movement in order to have a cooling effect, so we spent a lot of time looking at that. Our design utilizes a double inner EPS core: Air blows in through certain ports and is routed through channels in the liner and the head pad. We also use exhaust vents at the back of the helmet to ensure that the air has to go over the top of your head and then out of those vents. Creating a place for the air to go provides that flow.”
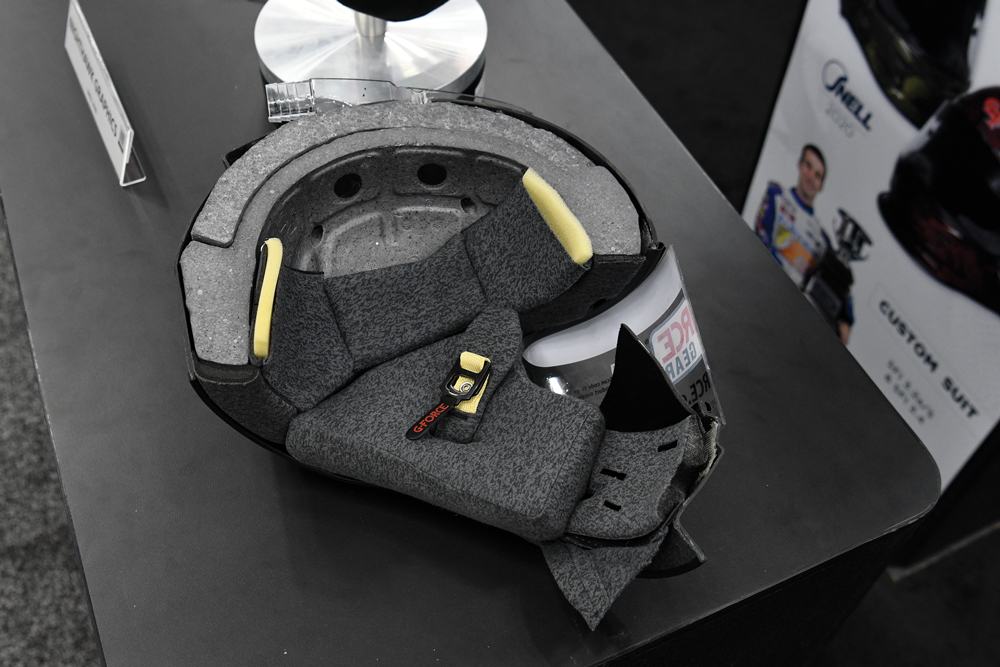
Ben O’Connor of Impact Racing in Indianapolis, Indiana, said that comfort is being improved through weight reduction as well. “The size of the helmet affects that. We don’t want a large helmet, and ours is significantly smaller in diameter than the majority of what’s on the market today while still achieving the same safety certifications. Anyone can pass those tests if they build a big enough helmet. The challenge is achieving those safety targets while keeping the helmet small.”
Oliveira told us that material improvements have been the key to bringing that mass down. “When you reduce a helmet’s weight by, say, 100 grams, it’s going to make a noticeable improvement in driver comfort,” he explained. “The driver’s head is being subjected to significant G-forces in a race car dozens—or even hundreds—of times during a race. So, if you can reduce weight by even that much, it’s going to make a difference in fatigue, and in turn overall comfort, throughout the race. For us, the materials are still primarily fiberglass and carbon. The difference is that, in the past, a carbon helmet might have actually been 70% carbon. Now we have helmets that are 100% carbon. Before you had to have some fiberglass involved in order for the helmet to provide enough protection, but with the latest materials that are available, we’re able to provide that protection entirely with carbon. That makes the helmet much lighter as a result.”
Tailored To The Task
Manufacturers typically offer a range of different shell types to provide racers with a helmet that’s specialized for a given application, whether that’s the aerodynamic needs of open wheel racing or the environmental concerns of off-road competition. While these design elements address some of the key requirements of various use cases, recent development efforts have seen an increased emphasis on modularity as well.
“The goal is to get these helmets to accept a wider range of electronics, and more ear-cup capable,” said Peters. “There’s got to be room in there to make ear cups work, so you’ve got to have cheek pads of different shapes, and relief in the EPS to provide that space. And, of course, all of that has to be tested to ensure that the helmet still provides proper protection.”
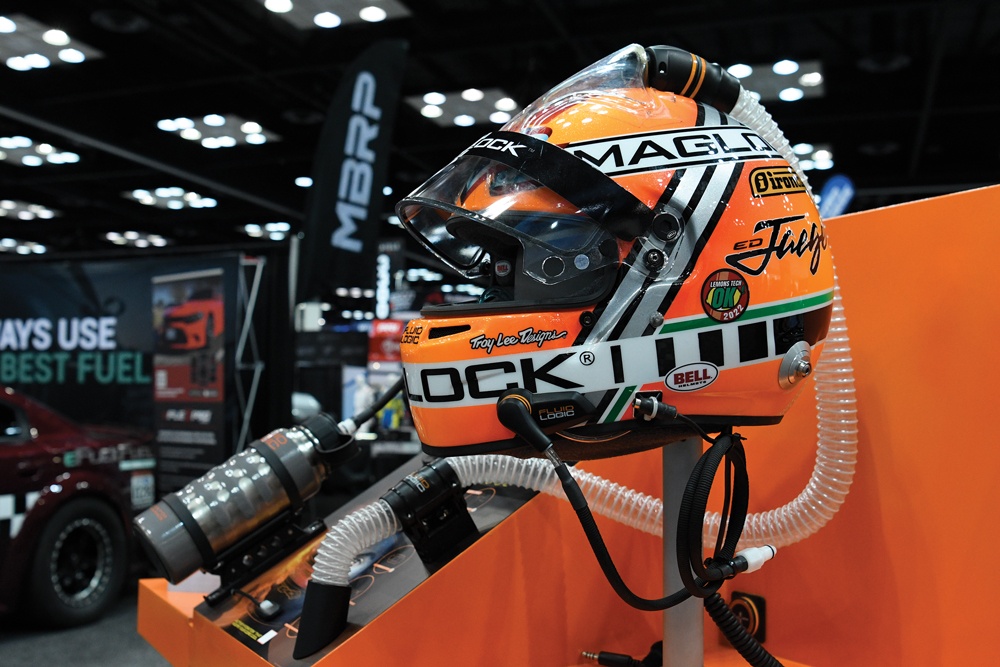
With the array of different accessories that a helmet can be outfitted with, and racers’ potential concerns about compatibility and aftermarket installation hassles, O’Connor said that manufacturers are now making a stronger effort to offer these options right out of the box.
“The big thing for us is that we want to offer all of that in one turn-key package,” he explained. “So if you’re racing in the Baja 1000 and you want to have a helmet skirt, FHR posts for a HANS device, and you’re planning to run PCI wiring in the helmet with ear cups as well as a FluidLogic hydration system, we can send you a helmet that’s immediately ready to go. That means you don’t have to send it out to five different companies for retrofitting, or risk your safety by doing it yourself, which could potentially create a dangerous situation if the helmet is modified in a way that it shouldn’t be.”
Greater modularity is being designed directly into the helmet shells as well. “We make a helmet that has a mid forced-air attachment, and it also comes with a side forced-air attachment,” said Russell. “So if you’re driving a car with low head clearance, you can take the top air piece off, put the cover on that element, and use the side port instead. It also comes with a communications and drinking tube cover, which can be utilized to plumb your radio and hydration system. All of these attachments and covers come alongside the helmet in the box, and that allows the customer to configure the helmet to their preference once they’ve decided how they want to use it.”
Upping The Ante
While the safety of modern racing helmets is largely dictated by Snell and FIA certification requirements, each manufacturer takes a slightly different approach in its mission to reach those targets. For its part, O’Connor said that Impact Racing’s emphasis on minimizing weight with reduced shell sizes also provides safety benefits alongside enhanced comfort.
“The lighter a helmet is, the safer it is in terms of preventing secondary injuries like whiplash,” he explained. “Some of the big differences with today’s helmets are in the composites, along with different fabrics, resins, and different ways of laying the materials up. There are now more advanced techniques that ensure better penetration into the matting with the resin. That’s not only going to help it absorb energy more effectively, but it’s also going to allow you to create a stronger shell overall with less resin, which results in less weight.”
Meanwhile Peters said that reaching these safety standards without compromising other aspects of a helmet’s design requires some deliberate strategy. “The new standards force manufacturers to make changes. If they change the impact requirements, you may need to stiffen up the shell, or you may need to make the shell more flexible in combination with a certain density of the EPS foam. Weight is always one of the biggest concerns, so we’ll take different materials and produce different layups for the shells, and we’ll try various combinations of materials placed in specific areas. There’s a bit of trial and error to it; the testing doesn’t always go the way you think it will. With some products, we’ll work with aerospace construction companies to get their insight regarding the kind of strength we need in certain areas to reduce weight while still reaching those safety goals.”
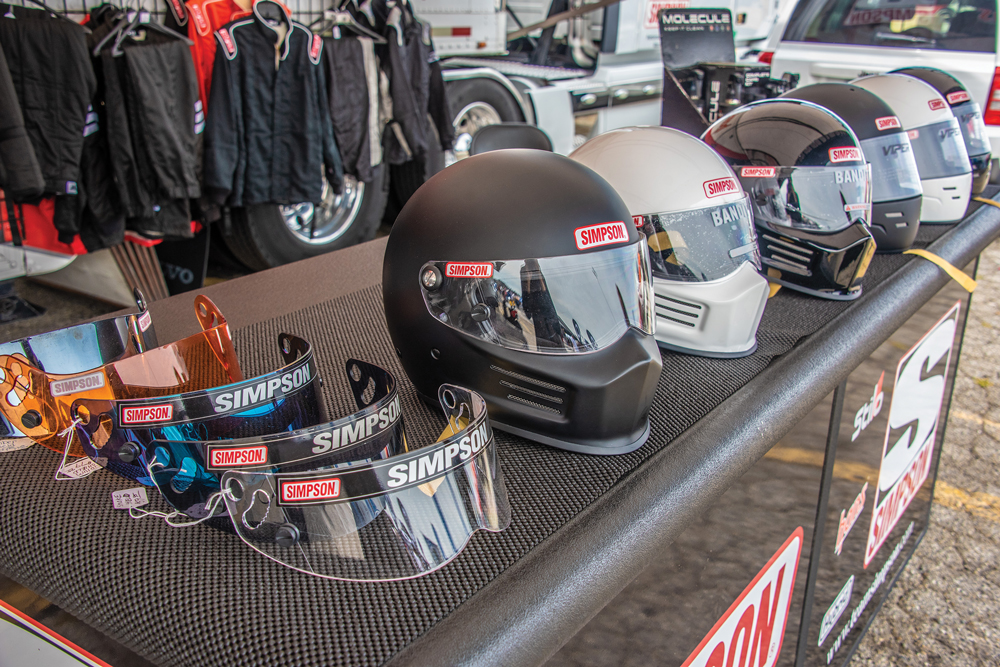
As the new Snell 2025 certification standard approaches, manufacturers like Impact Racing are now working to find ways to meet the elevated requirements without making sacrifices elsewhere.
“The idea is that each standard results in an incrementally safer helmet than the previous one,” said O’Connor. “But there are always trade-offs in whatever you do. For example, maybe you need to bump the impact resistance by 20% but the only way to get there is to make the helmet 10% heavier. This time around the main focus is on reducing the G-forces that the head is subjected to in an incident. It’s not a huge jump, but it’s significant enough that there’s going to be a little bit of development work involved. Some of the stuff we have is already beyond that standard, so it’s just a matter of re-testing it, but we like to stay ahead of the curve.”
Looking ahead, Oliveira also expects more sophisticated technological integration in the helmets that we’ll see a few years down the road. “A lot of companies are looking to improve radio integration at the moment. And there’s a lot of discussion around headphones with noise cancellation features, so you hear the radio rather than the noise inside of the car. Bluetooth is also something that I expect to see more of in radio systems in the coming years. The technology hasn’t been perfected for this type of an application yet, but there are benefits in terms of reducing the wiring that has to be hooked up to the helmet, so I think we’ll see more development there, too.”
But as Russell noted, the pace of innovation in the helmet world is heavily influenced by the safety standards that all manufacturers must adhere to. “If you’re going to come out with a new helmet design, you want it to be something that will suit the market for a 10-year period. This is why some manufacturers don’t make a XXXL helmet, or a larger shell helmet. If the market isn’t there in the five to 10 years of the standard, you may not be able to recoup the development and production costs. That’s why we try to do our big design changes every 10 years. I think that with the 2025 standard being more of an incremental change, the biggest leaps in design will probably be aimed at 2030.”
Sources
G-Force Racing Gear
gforce.com
Impact Racing
impactraceproducts.com
Pyrotect
pyrotectstore.com
Simpson Race Products
simpsonraceproducts.com