CUTTING EDGE DEVELOPMENTS
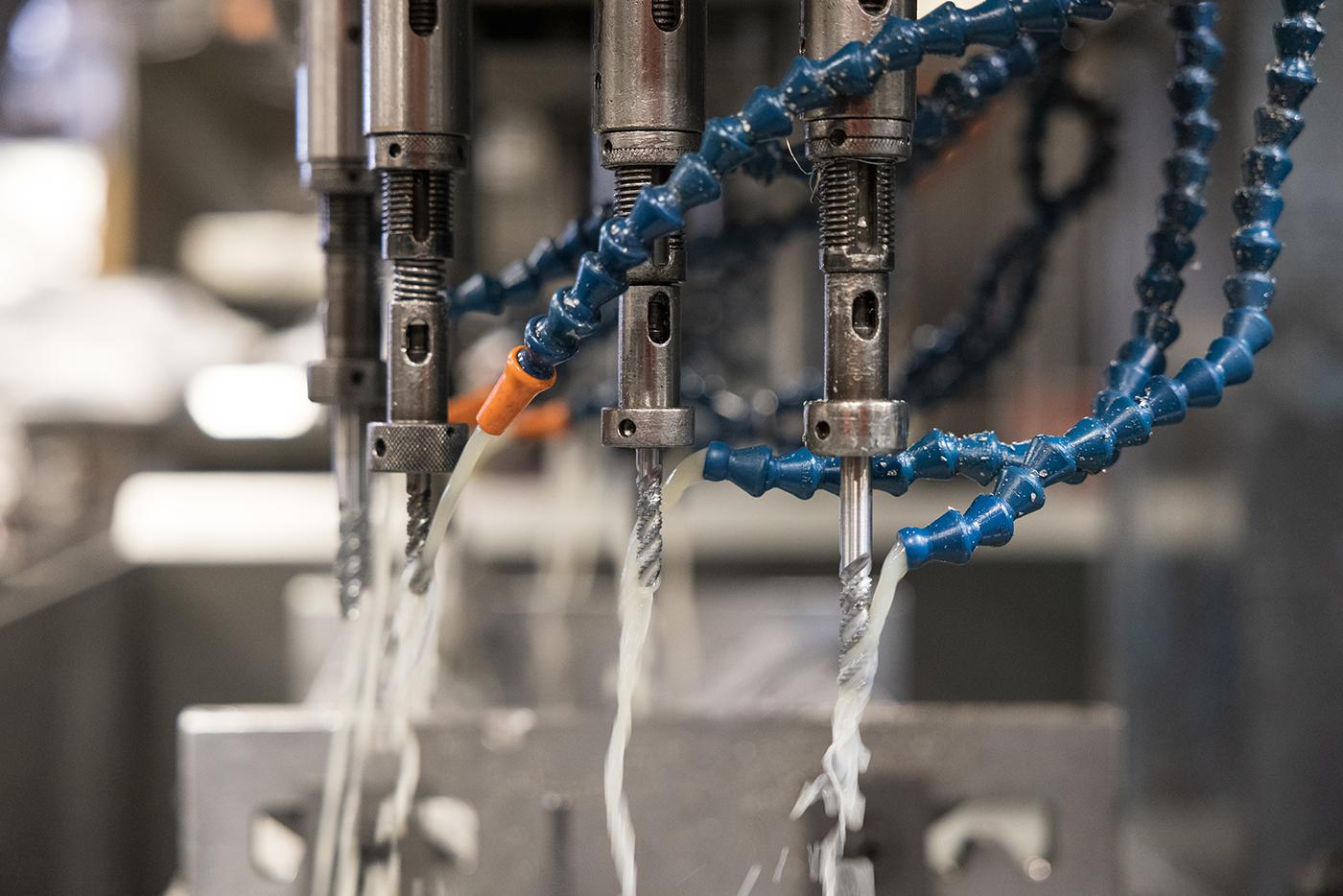
Keep engine building productivity on pace with these new cutters, tooling, and abrasives solutions.
The year 2020 will certainly go down in history as one with no shortage of challenge and compromise. But folks in the racing industry have always been a resilient bunch. And while much of the year saw teams in a holding pattern rather than out on track, many decided to turn their attention back to the garage to make the best use of the down time.
“Business is up—we’ve been busier than ever, it’s staggering,” said Christine Lowe of Cylinder Head Abrasives, Orangevale, California. “I think people have had more time to port cylinder heads right now. They either couldn’t go racing or chose to take the season off, so they’ve been in the shop putting more development time into the cars and the parts they’re using.”
So with that in mind, we decided to take a closer look at five of the latest products and technologies in machining cutters, tooling, and abrasives to see how innovation continues to point the way toward lower costs, greater efficiency, and better results.
PGE6000 PRECISION ELECTRONIC BORE GAGE
SUNNEN PRODUCTS
ST. LOUIS, MISSOURI
Sunnen is in the midst of a brand refresh of sorts, having launched a new, more comprehensive website (sunnen.com) in 2020; a new e-commerce site is also scheduled to go live later this year. “We’re definitely targeting the engine rebuilder marketplace,” said Tom Dustman. “We look forward to providing access to place direct orders any time, day or night, for our US customers, along with pricing and availability of the products in our catalog.”
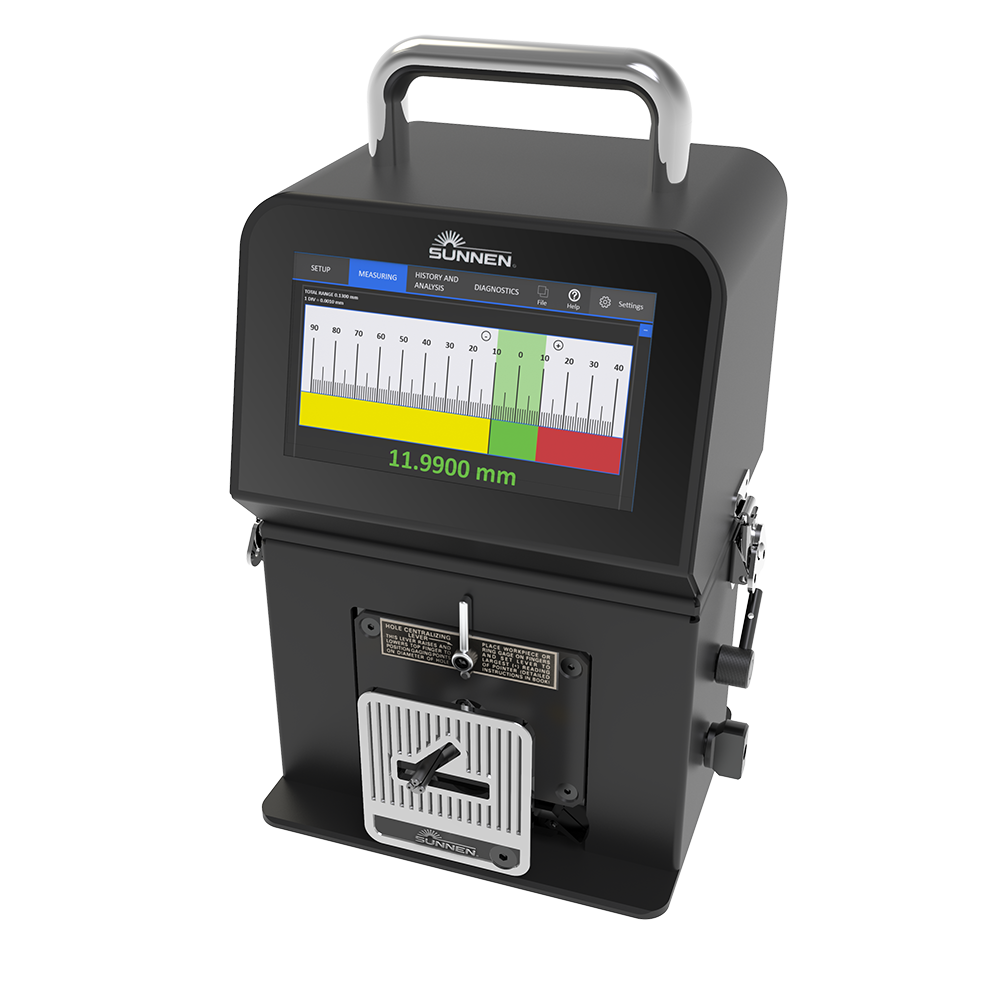
Alongside this new online effort, Sunnen is busy developing tools that are designed to yield more accurate measurements—and in turn, more reliable parts production.
The latest is an electronic version of Sunnen’s benchtop PG800 precision bore gage, the PGE6000. “The PGE6000 is a benchtop unit that will allow a machinist to see an electronic display of the actual diameter that’s being measured,” Dustman explained. “It will be available in 110v 60Hz as well as 220v 50Hz single-phase and will offer a diameter range from 0.37 inches up to 1.5 inches. It’s designed to be user-friendly and will withstand variations in shop floor temperature and the vibrations of a typical shop environment.”
“It also allows you to collect data and interface with statistical process controls,” he explained “We’ve been seeing a trend in the industry that’s moving toward documenting high-precision performance measurements, and it’s driven by the end-user who wants to ensure that all of the components on the engine have been produced to an accuracy that’s equal to OEM standards. There’s peace of mind in that. It should also confirm to the machinist and management that the work has been done right—it prevents someone from coming back and claiming there was a quality issue when there wasn’t one.”
Dustman added that the PGE6000 should also be of interest to larger engine shops who are, for instance, producing connecting rods. “They might be doing a ton of rods at once, and they want to make sure every one of them is the same—with this built-in statistical process control, it makes it much easier to confirm that,” he concluded.
BLG-1000 Bucket Lifter Grinder Assembly
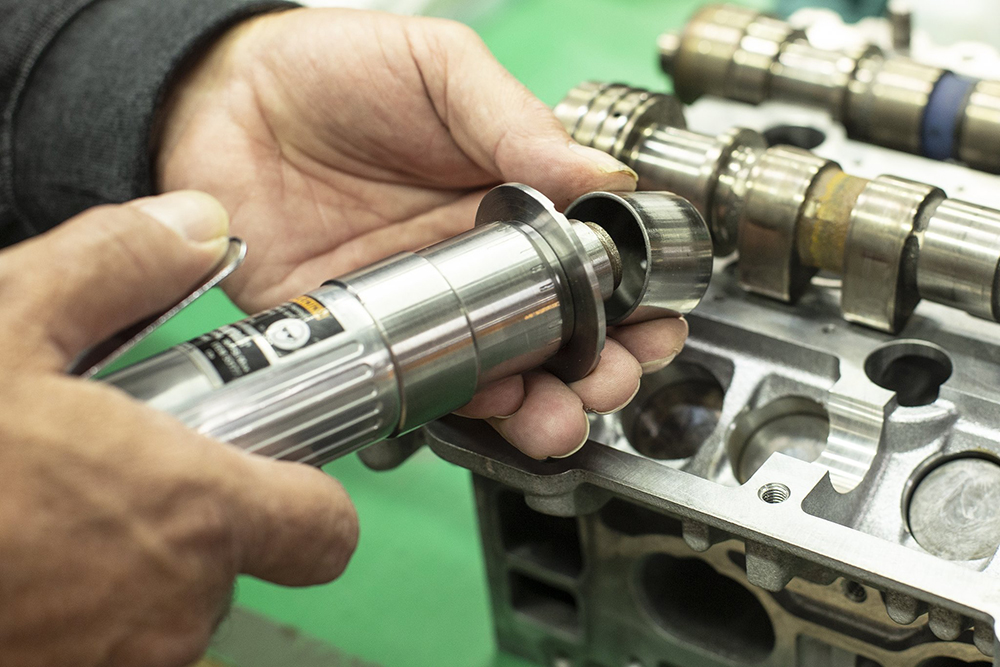
GOODSON TOOLS & SUPPLIES
WINONA, MINNESOTA
“This is, in my opinion, the neatest thing we’ve launched recently,” said David P. Monyhan. “This bucket lifter grinder was designed and patented by an engine builder here in the US. He came to Goodson because of our position in the marketplace and asked us, ‘Hey, do you think this is a good idea that we can run with? If so, I’ll get it patented, but I want you guys to bring it to engine builders worldwide.’ And that’s exactly what we did.”
The BLG-1000 is designed to work with multi-valve overhead cam cylinder heads, which all have a commonality in the bucket lifter, and inside that bucket lifter is a small tab or machining point. “We use a CBN button grinder to actually affect a dimension on that boss and then set the clearance or cam lash, as it were,” Monyhan said. “Once you’ve assembled one of these 20-valve or 30-valve engines, you have to measure cam lash. If cam lash is not correct according to specification, you’ve got to completely disassemble that cylinder head and then you’re left with three choices: tip the edge of the valve, grind the valve face itself, or actually grind or cut the valve seat once again.”
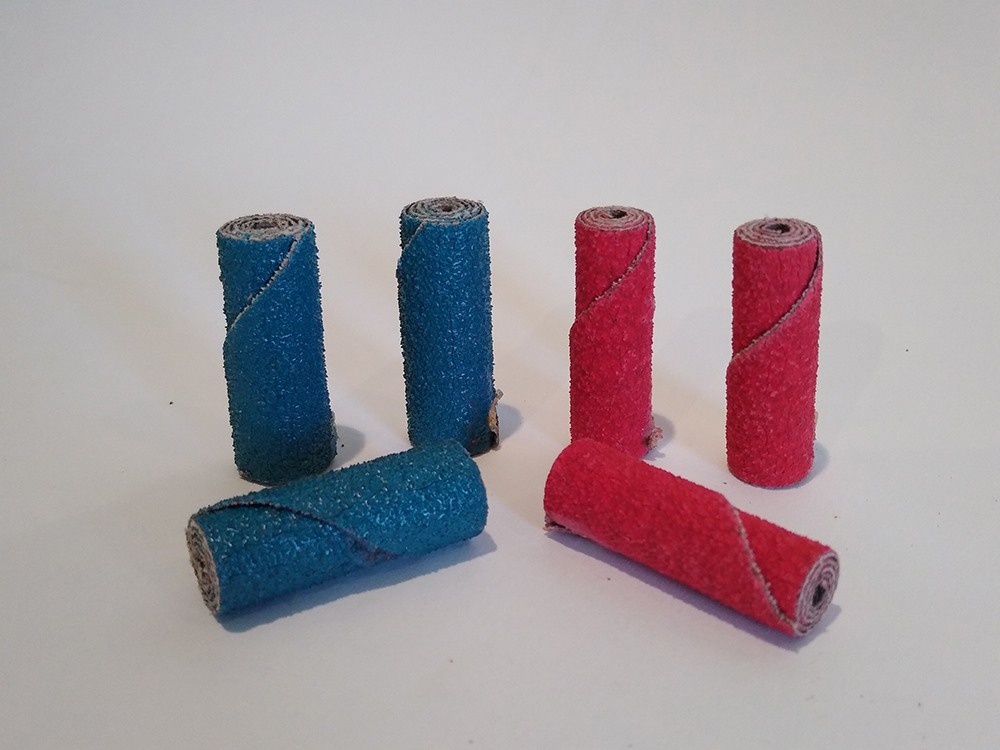
Monyhan said that by just affecting that same tolerance dimension on the bucket lifter, the BLG-1000 cuts an hour to an hour-and-a-half out of the assembly time on each multi-valve overhead cam cylinder head, saving shops a ton of time (and money) in the process. A micrometer feed shows how much material is being removed, and the included dial indicator and bridge allows the machinist to check their work.
PREMIUM CARTRIDGE ROLLS
CYLINDER HEAD ABRASIVES
ORANGEVALE, CALIFORNIA
Christine Lowe noted that demand for more specialized tools has picked up significantly over the past year. “We have the ability to do short runs of custom product, and there’s definitely been an increase in requests like, ‘Can you make this carbide, or can you make this porting stone with this specific grit?’ Or maybe they need a certain shape and a certain flute count. Folks are getting a little more knowledgeable about what they need and are calling out for specific characteristics that fit their particular application. Those types of orders have gone through the roof recently.”
And as the customer demand becomes more refined, Lowe has sought to expand Cylinder Head Abrasives’ catalog with a wider range of on-the-shelf options to meet those needs in a timely fashion.
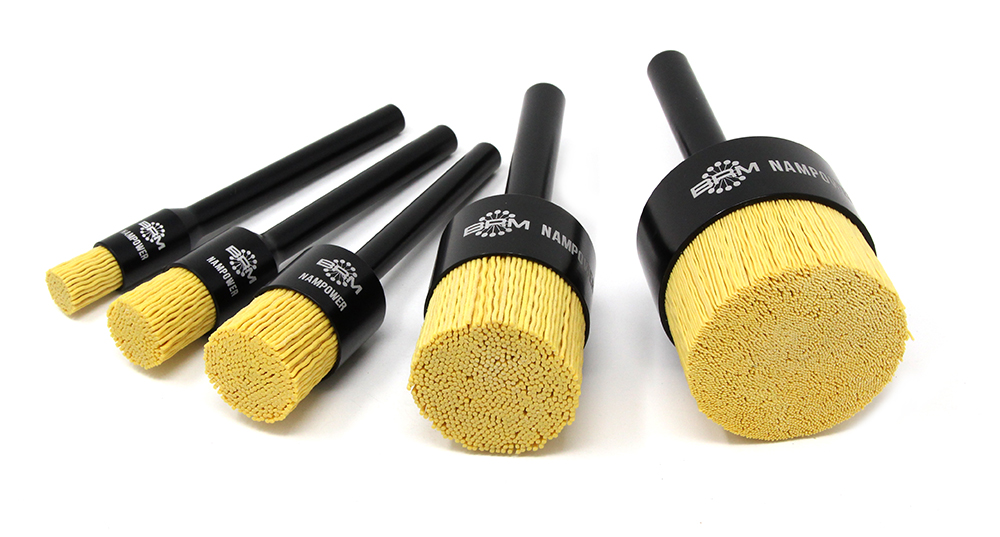
“These brushes work well for OD or face applications for deburring, finishing, and removing rust and corrosion from the outer surface of parts and inside pockets,” said Elysha Cole. “You can use it on aluminum, stainless steel, cast iron—it is very multi-purpose.”
Cole explained that wire brushes are typically used on the outside surfaces of parts, and while that works fairly well, there are some notable drawbacks. “The wire does fatigue eventually, and that can cause it to break off,” she said. “That can get into the components you’re working on and pose a risk to the machinist working on that part. Abrasive nylon is a much more flexible material, so as you use them they abrade down. It’s similar to sandpaper in that way—you can keep using them as it wears without having issues like filament snapping and breaking off.”
That equates to longer brush life and a safer working environment, and with the range of grit levels that BRM offers, machinists can get the specific type of surface finish they’re looking for from a brush design that performs like a wire brush while also decreasing costs. “If you’re deburring, edge break, or removing rust, we have a grit level for that; and if you’re polishing, we have something for that as well.”
The development of Nampower nylon brushes come as part of a response to an industry trend that’s seen shops work toward keeping these processes in-machine whenever possible. “They generally don’t want to move stuff to that secondary, by-hand operation,” Cole added. “Often it’s a situation where the facility doesn’t want to move the part off of the machine and to a different location to deburr it—everyone seems to be moving toward keeping these processes in-house wherever they can.”
EMUGE’S CIRCLE SEGMENT
END MILLS
MSC INDUSTRIAL SUPPLY CO.
MELVILLE, NEW YORK
“At first glance, you may think this is a tapered ball nose end mill, but it’s not,” said Scott Lowe of Emuge’s Circle Segment End Mills for five-axis machining, one of the metalworking and maintenance, repair, and operations (MRO) products and services offered by MSC Industrial Supply Co. that recently caught our eye.
“This end mill design uses a large profile radius, or circle segment, to machine the part,” he continued. “In many cases, it replaces stitch or pencil milling with traditional ball nose end mills when finishing milling part features in five-axis machining.
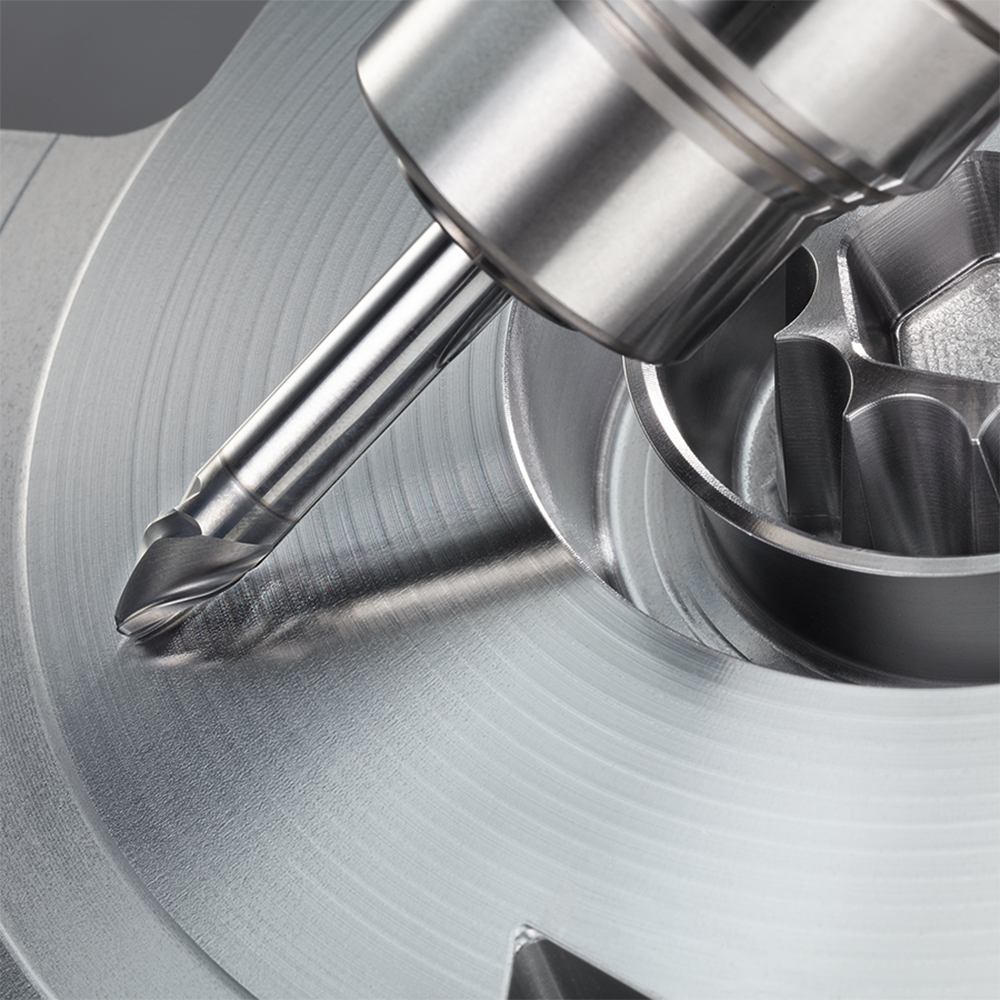
“Circle Segment End Mills require the full capabilities of a true five-axis machine where complex toolpaths are generated using the right CAM software (Hypermill and Mastercam, for example).”
These end mills are designed to significantly reduce billet-to-finish part time due to their ability to increase stepover length up to 30 times greater than a traditional ball nose end mill without increasing cusp height.
“This translates to significantly faster machine time without sacrificing component surface finish,” Lowe added. “The large profile radius of the Circle Segment End Mill is held to an extremely tight tolerance of +/- .01 mm (+/- .00039 inch), thereby ensuring that critical features are machined with precision.”