DEFEATING TURBO LAG
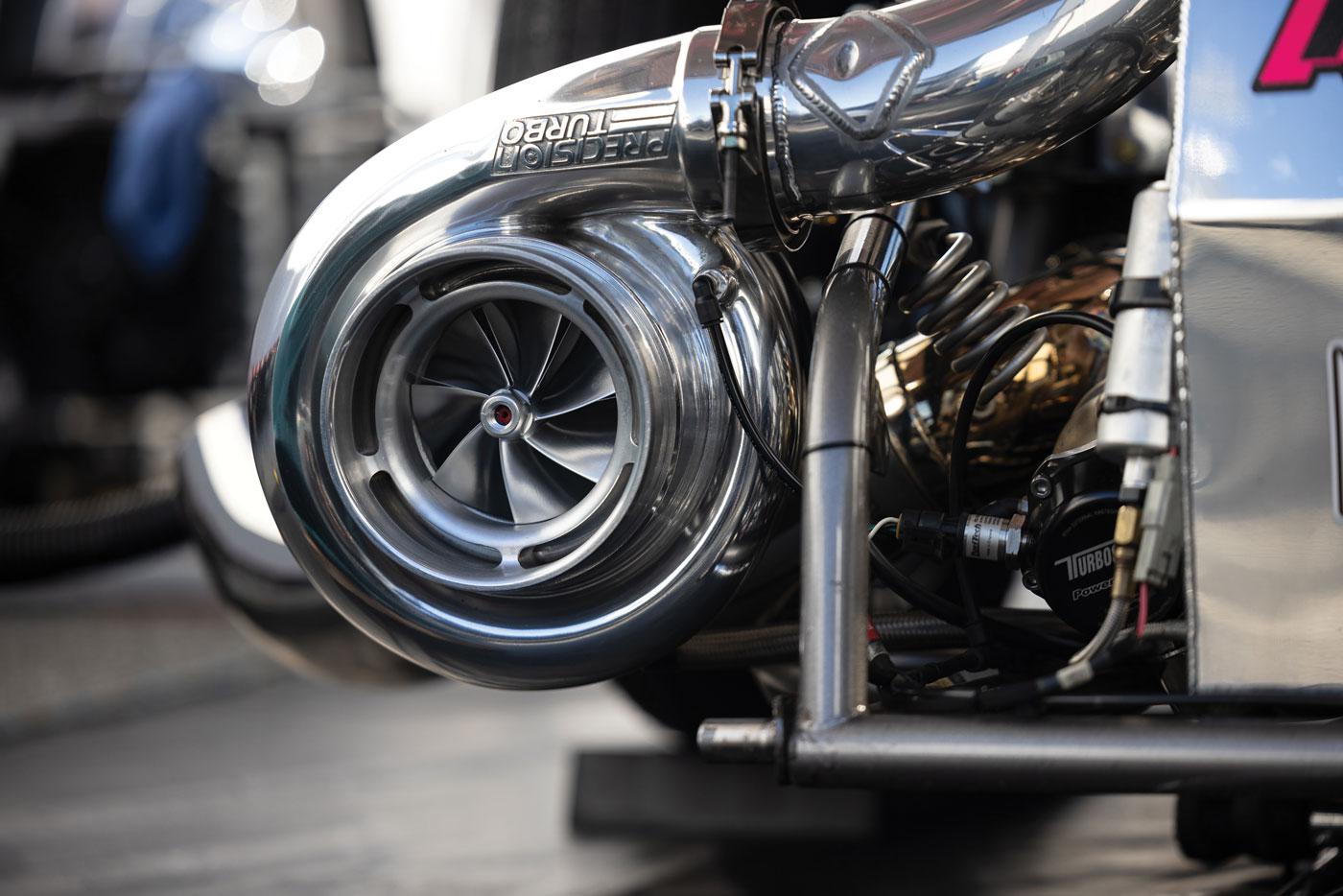
Problems arising from system design, parts selection, and inexperience can lead to performance left on the table—or even the failure of critical components. Here are some of the most common trouble spots seen by turbocharging experts and how they can be resolved.
Whether the weapon of choice is a high-winding four pot or a big displacement V8, turbocharging has become the name of the game when it comes to making big power. Turbo technology has come a long way in recent years and its popularity has increased in turn, but that doesn’t mean it’s foolproof.
“It can be trickier to work with versus a supercharger, for instance,” said Reggie Wynn of Precision Turbo & Engine, Hebron, Indiana. “There are more things that can go wrong along the way, but they’re generally simple issues that can be easily corrected. But without knowing what those are when going into it, it might not be so simple.”
Those issues can be exacerbated by factors that have nothing to do with what’s under the hood. “Sometimes it’s just pride,” Wynn said. “Some people don’t want to ask for help, or they’re not willing to heed advice from people who’ve done it before. They might have a lot of experience with other types of engine combinations and assume that what works in one situation will apply to another, but that’s not always the case.”
Ernie Munoz of Comp Turbo Technology in Pomona, California, pointed out that turbocharging is a very different game when compared to other power adders, and some folks might not know what they’re getting into initially. “People get fixated on the horsepower numbers or displacement, but there are a lot of other variables that need to be considered when putting a turbo system together that can affect what kind of power it makes and how reliable it’s going to be.”
Performance and reliability are the core goals of just about any combination built for competition, and the inherently complex nature of turbocharging means that small problems can have a significant impact on both. Yet as the experts attest, most problems stem from common mistakes that can be easily avoided—provided the racer knows what to look out for.
1. WASTEGATES SHOULDN'T BE AN AFTERTHOUGHT
“From a boost control standpoint, the location and proper mounting of the wastegates is key,” said Marty Staggs of Turbosmart, Ontario, California. “All of the wastegate manufacturers provide diagrams and guidance on this, but it often gets overlooked when people are building their headers or designing their systems. A lot of times it’s the last thing that gets taken into consideration, so folks will just try to stuff them into any spot where they’ll fit. Folks need to take into account the size and location of the wastegates when they’re building that system, because otherwise they’ll get bit. They should be mounted in the flow path because we need to control that exhaust drive pressure. If the gates aren’t installed properly, they will have a hard time controlling the boost.”
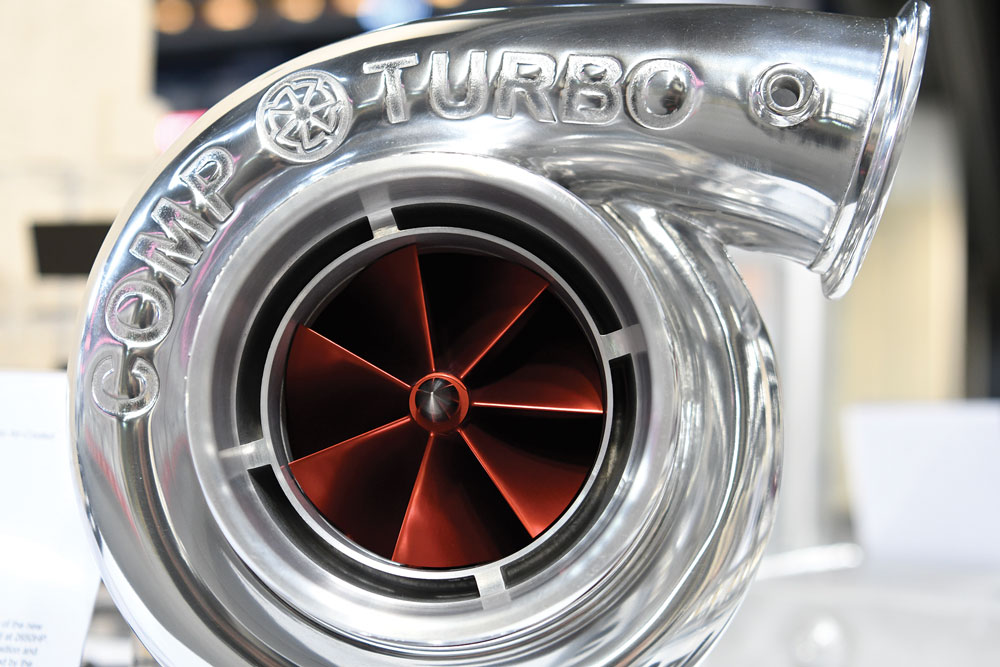
2. AREA OVER RADIUS SIZING
“If the A/R [area/radius] is too tight, it’s going to over-spin the turbo, and that causes a lot of failures,” said Deena Salenbien of Apex Turbo, Maybee, Michigan. “When it comes to the turbine housing, it’s one of the few aspects of the design where the builder has to make a choice. The tighter the A/R—or the smaller the number—the smaller the opening into the turbine housing is, and the quicker the turbo will spool up. But the larger that area is, the more top-end power it will make because it’ll flow more air through the scroll of the turbine housing. An A/R that’s too tight runs the risk of spinning up the turbo beyond its operating range, and that can potentially damage the turbine or the bearings. In a racing application, where low-rpm engine response isn’t a big concern, loosening up the A/R provides some headroom to get a reliable sense of the turbo’s desired rpm range. Then tighten up the A/R from there if necessary.”
Wynn agreed that a less restrictive housing is ultimately a safer bet. “A compressor cover that’s too small will kill the turbo sooner. Keep over-speeding a turbo, and at some point, it’s going to fail,” he explained. “Make sure that the compressor housing is the right size to match the compressor wheel size. If someone is stuck between two different sizes, I would recommend going with the larger housing. A lot of people will go with the smaller one because of packaging concerns, but the restriction can potentially affect the turbo’s longevity.”
3. FOREIGN OBJECTS
“If the turbo isn’t shielded in some way, that risks causing damage every time the car is run,” explained Munoz. “That turbo is spinning very quickly, so it’s like a jet engine that will just pull in any kind of debris that it comes across.”
Salenbien said problems that can crop up from debris entering the turbo system aren’t always immediately obvious. “That could be a foreign object from the road surface, or it could be a situation where something like a valve seat comes loose and goes through the turbine side,” she said. “If that causes a chip, or a blade comes off, it’s going to cause an imbalance and that will eventually lead to a bearing failure. It might not show up right away, but in a short amount of time they’re going to start seeing a lot of issues. It’s probably the biggest reason that turbos come in for repair. Those types of problems can be tough to detect right away, though, so it’s important to pull the downpipe off and inspect the turbo regularly. Just spinning it isn’t going to indicate whether or not something is damaged.”
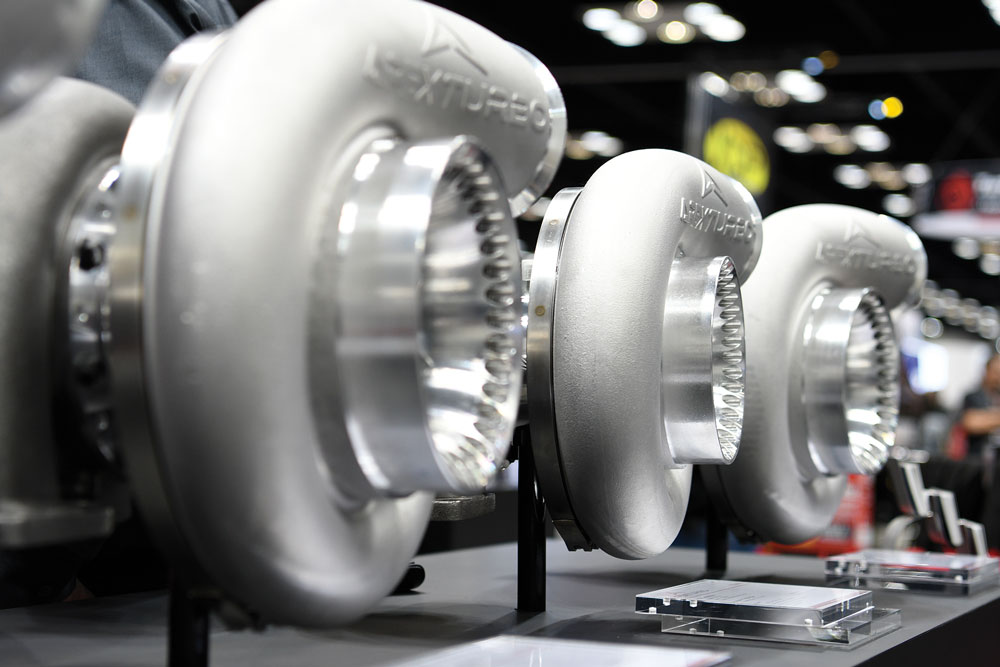
Wynn said that the best way to avoid foreign object damage is to run a filter or guard of some kind, but he noted that this approach comes with its own compromises. “A filter will protect the turbo against a lot of that, but a lot of racers won’t use them because they don’t look as nice aesthetically, they restrict airflow to a degree, and they take up more space,” he explained. “But if debris gets into the compressor side of the turbo, it’s just a matter of time before that turbo is toast.”
For those who want to make sure their turbos can live long and healthy lives in racing environments, Munoz recommends dialing in the system with a filter on right from the get-go. “Get a filter that’s going to have very high-rpm flow so it can actually hold up in that environment. Otherwise, it becomes a very big restriction. And it would be a good idea to do dyno sessions with the filter on if the plan is to run one,” he advised.
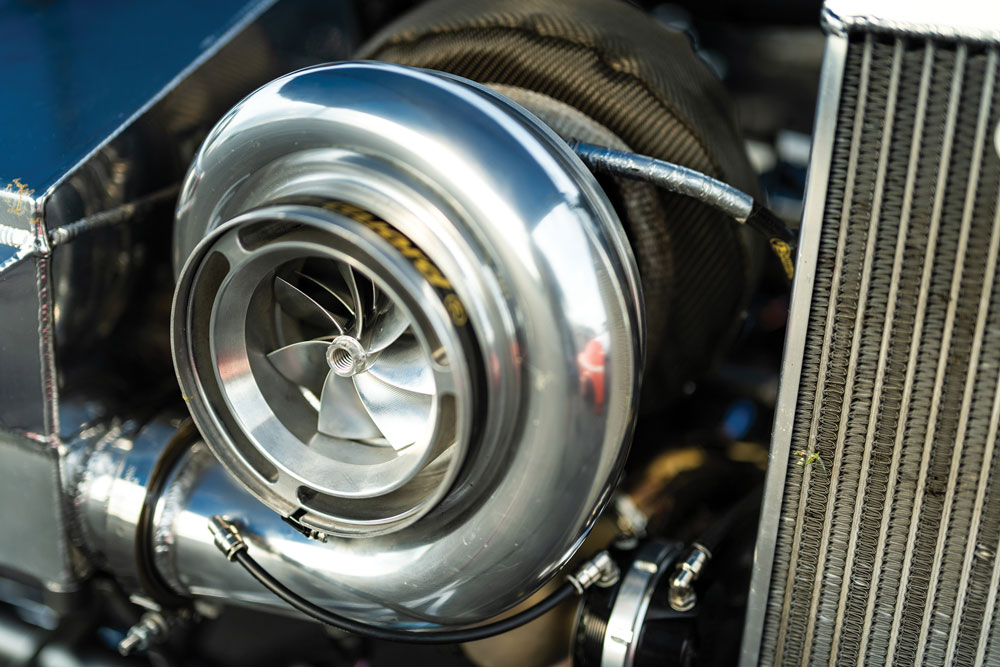
4. IMPROPER OILING
“One of the biggest problems I see is with turbos smoking, and that generally happens because of improper oil draining or scavenging,” said Staggs. “The oil backs up into the turbo, and that’s not good for the system’s efficiency or longevity. In those situations, it often ends up pumping oil into the intake, so that can cause problems there as well. Proper draining of the turbo and scavenging of that oil line is critical.”
Wynn said that the issue is often caused by mistakes in the design of the plumbing. “I see a lot of folks using too small of a drain line to go back into the engine, and that will cause smoking. You need to use a -10 or larger, depending on the size of your turbo. But the biggest no-no I see in this realm is 90-degree fittings. With that oil being gravity-fed out of the turbo, any abrupt change in direction of the flow is going to cause the oil to back up into the turbocharger. It’s better to use two 45-degree fittings to achieve the same goal instead.”
Munoz noted that low-mounted turbo systems can see other oiling challenges, too. “Best practice is to mount the turbocharger above the oil pan so it can drain properly and avoid leaking issues,” he said. “Some folks chose to mount them really low in the car and run a scavenge pump system to compensate for it, but that can cause serious problems. That pump is trying to replicate gravity drain, and any time it doesn’t pull fast enough, it risks causing damage. That’s why we recommend air-cooled or oil-less turbochargers in those situations to avoid the issue entirely.”
5. BIGGER ISN'T ALWAYS BETTER
“If what’s needed is good response across the rpm range, going with one huge turbo is not going to be the best option,” said Wynn. “When the turbo is too large, it’s going to take a long time for it to spool up and make power. That might work in certain racing applications, but if the engine is going to operate in a wide rpm range, the better choice is often running two smaller turbos with more boost rather than one bigger one with less boost. But for someone working on a budget and who needs to stick with a single turbo, sizing it to their needs is going to produce better results than just buying the biggest one they can afford.”
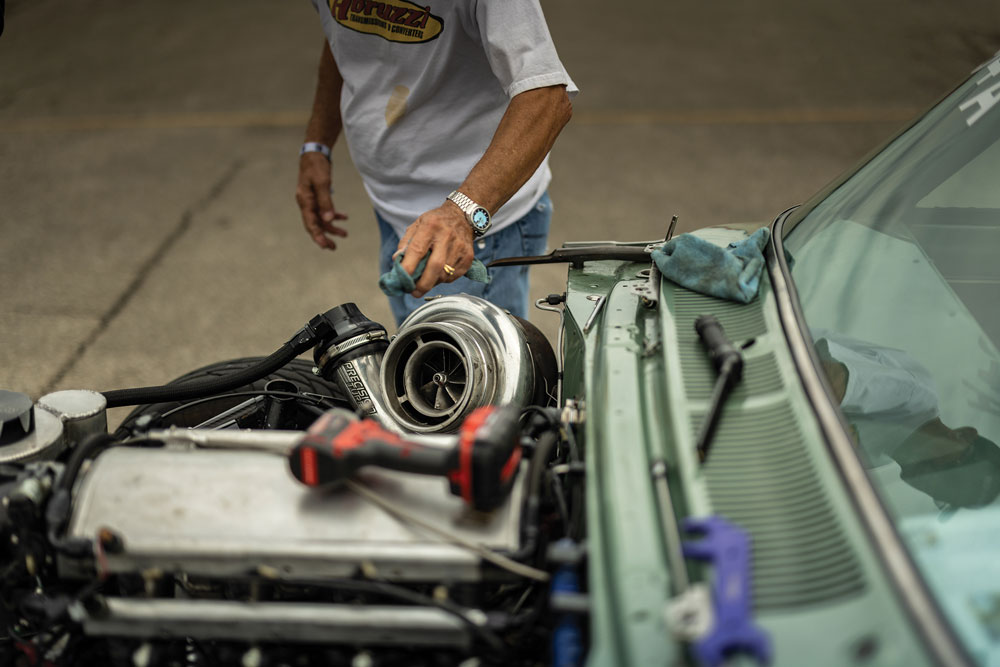
6. AIMING FOR 1:1
“Typically, the best horsepower results we see happen when the inlet pressures and outlet pressures get close to being the same value,” stated Salenbien. “That can be tough to achieve because of the differences in wheel sizes or the rule restrictions in certain race classes. Racers who run similar sizes for the compressor and turbine will probably never see a 1:1 ratio like that, either. They’re always going to see way more turbine pressure than compressor pressure in that situation because the turbine’s too small to be able to achieve those kinds of numbers. But to really optimize the system, 1:1 is the target. It could take some trial and error along the way with turbine housing sizes, wheel sizes, and the engine combination itself. Cylinder head flow and camshaft profiles can change that dramatically.”
7. BUILD STRATEGICALLY
“There is a lot of, ‘monkey see, monkey do’ going on out there,” explained Turbosmart’s Staggs. “People see someone else’s turbo setup and assume that it is going to yield the same results for them. But this is not a situation where one size fits all. The system should really be built around what the specific goals are. Just swinging for the fences is not going to provide optimal results. The application, the engine combination, the fuel used—all of these elements factor into how a turbo system should be built to maximize results. Usable power is the real goal here. Four-thousand horsepower isn’t worth much if it can’t be controlled, so the setup needs to be manageable under the specific circumstances in which the car is used. Given what’s available today, we’re seeing more and more people who are interested in actually turning down the power to make it more controllable. The guy who is focused on making as much horsepower as possible isn’t going to go rounds. The guy to worry about is the one who is dialing it in to be manageable.”
Salenbien said the engine combination itself is a crucial component in that equation. “Turbo systems take a lot of unfair blame because they’re an easy target when the combination isn’t doing what someone wants it to do. But the cylinder head design, the camshaft, the fuel delivery—all of it factors into the end result,” he explained. “Racers need to open up a line of communication between their engine builder, their tuner, and their turbocharger manufacturer together to make sure that the build will make not only the performance needed to win, but also the longevity.”
SHOW PIECES
While race product innovation is a 24/7/365 endeavor, no event captures the sum total of these developments quite like the annual PRI Trade Show. Each December, this marketplace of motorsports brings tens of thousands of buyers to the Indiana Convention Center and Lucas Oil Stadium in downtown Indianapolis to survey the latest go-fast parts and discover solutions to help unlock their race programs’ performance potential. Front and center at our most recent Show were some dazzling displays of turbo-equipped engines designed to elevate both horsepower and pulses. Here’s a closer look at three builds from the Show floor that we found particularly eye-catching.
MOUNTAIN MACHINE
Mountain Machine owner and engine builder Steve Ortner combined an H1 Hummer with a turbocharged 6.7L, 1,500-horsepower Cummins engine that has a highly modified 12-valve cylinder head and a pair of ApexTurbos. The manifold charger is an 88-mm s400 and the big turbo is a custom 110/114 charger with Apex’s patented billet center section with triple ball bearings and billet wheel. The rest of the engine features a Hamilton wet race block, Wagler rods, Diamond billet pistons, Farrell Diesel Service 14-mm pump, a competition Fluidampr damper, and several billet parts from Mountain Machine’s shop. This truck is primarily run at the Silver Lake Sand Dunes in Mears, Michigan. The custom cut paddles from Duneland Off-Road Center on the Raceline wheels helps it fly through the sand.
CIVETTE LSX
The Civette LSx, owned by Renegade Racing’s Thomas West, is a 2,200+ horsepower rear-wheel drive LS-swapped 1996 Honda Civic with a Corvette C5 drivetrain. It features twin Precision Turbo & Engine 76/78 ball bearing turbos with dual wastegates and dual blow-off valves as well as a Nitrous Outlet direct port nitrous system. The entire turbo kit was custom made for the one-of-a-kind car. Top End Fabrication built nearly the whole car, including the chassis, turbo kit, fuel system, etc., and Tommy’s Auto Machine & Parts built the engine. The driveline, including the transmission and clutch, was built by Tick Performance while Scott Bowen from In Tune Motor Sports tuned the Civette. West races in Stick Shift Outlaw.
BLUE TURD
Zach Wright’s 1995 Ford Taurus SHO features a custom billet block V6 from Bullet Race Engineering that’s based off the original Taurus SHO engine. The car has a chassis built by Bill Draghis’ Chassisworks, is wired by Ryno Wiring Solutions, and tuned by FuelTech with jazTUNING. It makes 1,400 horsepower with a Precision Turbo & Engine 7285 turbocharger (but will soon have the new 7685). Wright mounted the turbo all the way forward, literally sticking out of the front bumper, for a weight ballast. He’s using all the weight and leverage he can to plant the power through the front tires. Blue Turd competes in XFWD (Xtreme Front Wheel Drive), which is open to front wheel drive imports only.
SOURCES
Apex Turbo
apexturbo.com
Comp Turbo Technology
compturbotechnology.com
Precision Turbo & Engine
precisionturbo.net
Turbosmart
turbosmart.com