Game Changer
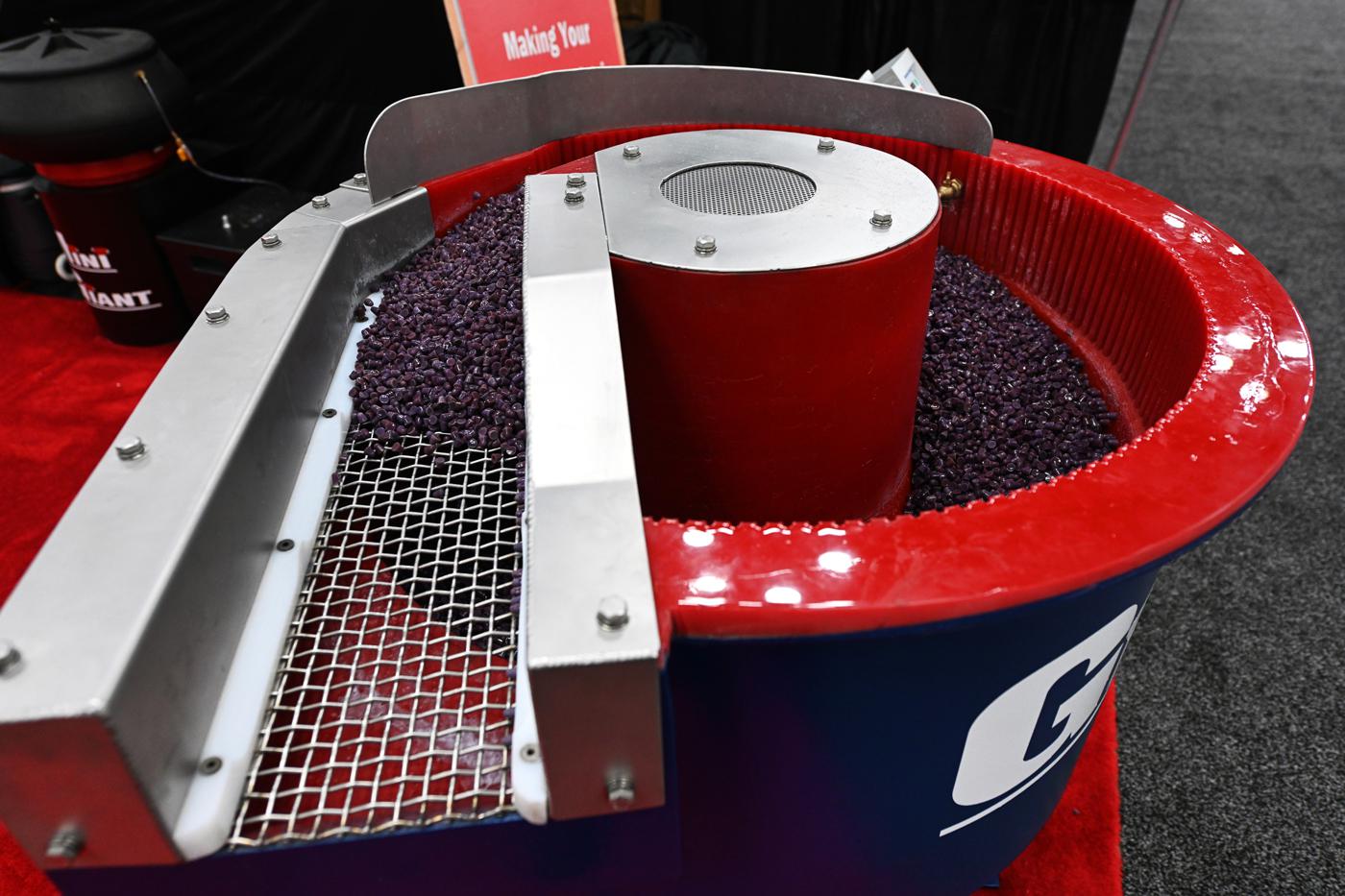
Having the right parts cleaning equipment and using it correctly “will change your life,” said an expert in the industry. He and others share tips for getting the best results.
To Perry Crabb, who has worked at AXE Equipment of Council Grove, Kansas, since 1985, the importance of clean parts is obvious. “Everything starts with the cleaning department.” No shop is going to “put a filthy block in their honing cabinets, or on their boring table, either. You don’t start anywhere until you get it clean.”
Mark Haworth of Temco Parts Washers in Edmond, Oklahoma, agreed. “Everybody in the automotive world deals with cleaning parts. I don’t care if it’s a race car or an everyday driver, if you take something off, you’re going to clean it before you put it back on or rebuild it.”
That being the case, these sources and others we spoke to in the parts cleaning industry remain surprised at how many automotive-related businesses don’t have the proper parts cleaning equipment. Or, if they have it, don’t use it for maximum effectiveness.
Before he worked at UltraSonic LLC in Amelia, Ohio, Jason Shaw used to “spend hours busting my knuckles in a mineral spirits parts tank scrubbing nuts, bolts, parts, valvetrain, all that stuff,” he said. “When I got here and saw what these machines can do, I was kicking myself wondering, ‘Why have I not seen this before?’ Once you see how much time and effort it will save you, it can be an absolute game changer.”
But, Shaw added, “it’s not magic. It’s science.” To get the most out of a parts cleaner, whether it’s an ultrasonic machine, a blast cabinet, a water-based parts washer, or other piece of equipment, there are processes and formulas to be followed.
Multiple Steps
Depending on the parts being cleaned, the job may require several steps using multiple types of equipment.
Mark Oryszczak of Giant Finishing in Addison, Illinois, pointed out that a shop doing remanufacturing will have parts “with heavy greases and oils on them, so they may have to go into a parts washer first, and then they’ll need to scrub the parts afterward. Then there are times, like to get into little nooks and crannies, they’ll want to do that in a dry blast cabinet. But you can’t put wet, greasy, oily parts in a dry blast cabinet, so that’s when you have to use something like a slurry cabinet.”
“A good cleaning system combines different kinds of equipment working together, which can dramatically reduce the amount of time needed for cleaning,” Shaw said. “For example, instead of putting something in a jet wash or spray cabinet for a half hour or an hour, put it in there for five or 10 minutes just to knock off the heavy, thick stuff. Then put that part into an ultrasonic cleaner for precision cleaning. It will get down into the angles, the blind holes, the places you can’t see or touch. If at that point you’re going to machining, you may need a little media blasting, but the ultrasonic machine may have eliminated the need for that, or at least reduced the media blasting time.”
Time, Temperature, Detergent
While different kinds of water-based cleaning equipment may not function the same way, they all have one thing in common: To get the best results, “it’s all about time, temperature, and concentration, and the concentration is the detergent,” Haworth said.
Temco’s parts washers don’t use spray nozzles, “so for us it’s about gallons per minute and pressure. We want to flood the part with as much hot, concentrated detergent as we can to get it as clean as we can.” The ideal water temperature is “around 180 degrees or hotter,” Haworth said.
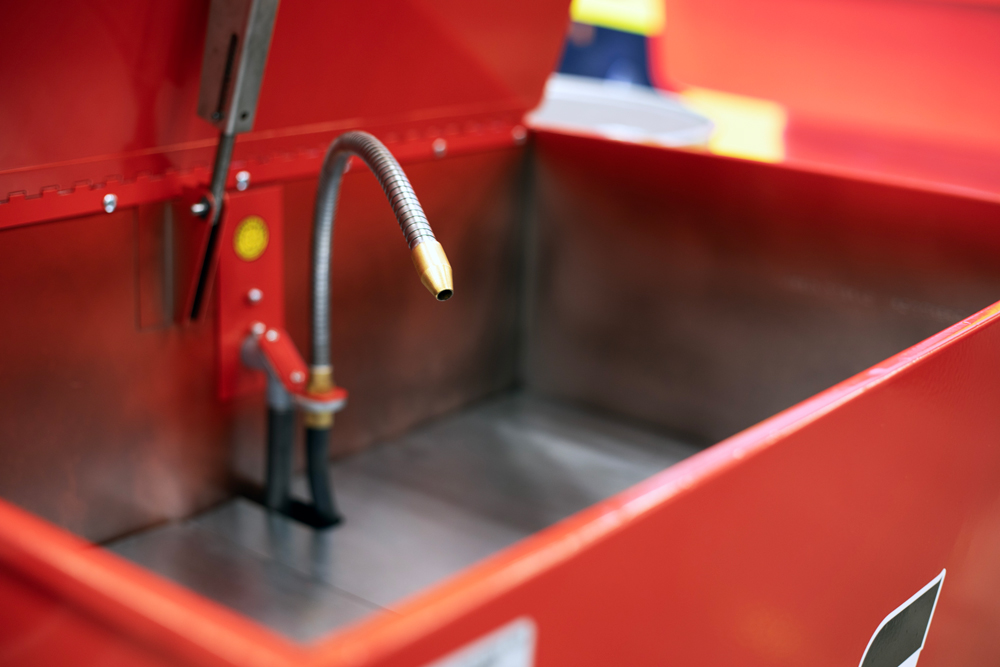
“You’ve got to have hot water,” Crabb agreed. “We set parameters where you can’t get any colder than 140 degrees, because with anything under 140 you’re just wasting your time.” However, “you can’t go over 200, because above 200 water starts to boil, and the pumps don’t want to pick up the water.” Cast iron parts, he said, “respond well at a higher temperature, like 180 or 190.”
Because AXE cleaning equipment does use nozzles, Crabb added a good pipe system and filtration to his list of must-haves. “Without the filtration you risk plugging your nozzles,” he said. “If you’re running this big, 10-horsepower pump with 20 nozzles, and 11 of them are plugged, you’re running all that energy and not getting anywhere.”
One more ingredient Crabb included was a good drive system for the parts turntable. “Our turntables are very slow, like two-and-a-half times per minute, because we have to have contact time coming out of those nozzles.”
Time is a critical factor when using an ultrasonic machine, Shaw said. “Start with short cycle times, especially if you’re dealing with aluminum. If you leave it in there too long, it can etch or discolor the part. You will want to do some testing, as there’s a bit of a learning curve with this equipment. All too often people put parts in the tank and crank on the time for, say, 15 minutes, when the part was actually done in 3 to 5 minutes.”
The “science” aspect of parts cleaning figures most prominently when it comes to detergents.
“Monitoring the pH of your water is important to every parts washer,” Haworth said. “It’s all about monitoring the pH of the detergent and mixing it correctly.” Most detergents come with a Safety Data Sheet (SDS) that indicates what the pH of that detergent is when properly mixed. Ideally, “you want a high pH, but not above 12,” he said. “You’re getting more alkaline as you go higher on the pH scale, and if you go above 12, you can damage the cabinet if it’s a steel cabinet. We’ve seen people who have had a machine for a few years, and they complain about it rusting out and things falling apart. It’s mostly because they’re using a chemical in their machine that has a high pH. It may clean the part better, but it’s also damaging the cabinet.”
Rust, though, can form for another reason.
“A lot of people who buy these spray washers think, ‘All I’m doing is final wash. I’m washing completely clean blocks. So I’m just going to put some Simple Green in my spray washer. It smells good,’” Crabb said. “But that machine will rust up within a week. If you don’t run a detergent with a built-in rust inhibitor, you’re going to have problems.”
The hardness of the water used in the machine—the water’s calcium content—can also affect the detergent, Haworth said. “You can’t achieve the pH you want if the water is really hard. If you can’t get your pH up above 11 with a detergent that says its pH is above 11, then you probably have very hard water.” There are ways to treat hard water, he said, “and none of them is extremely expensive. You don’t have to buy some elaborate water softening system. There are chemicals you can add to your tank to reduce the hard water and its impact on the detergent. The detergent will last longer, the pH will stay higher, and the parts will get cleaner.” To determine the pH in their washers, “people can go to Amazon and get a digital pH tester for about $12.”
Cast Iron vs. Aluminum
Another factor in choosing a detergent is the makeup of the parts to be washed.
“What are they going to be cleaning, cast iron or aluminum?” asked Crabb. “If they tell me strictly cast iron, they should ask for a chemical with a high concentrate of sodium hydroxide, meaning it’s caustic. That will eat at that paint and that baked-on sludge on those blocks. But then they can’t put aluminum in it.”
“There are products on the market that do very well with steel, but most of those products can discolor aluminum,” Haworth said. “They will turn an aluminum part dark gray. There are specific chemicals that you want to use for aluminum. Those have a different chemistry. They can create the same pH, but they don’t have such a harsh effect on aluminum.”
He acknowledged that, for shops that do both cast iron and aluminum in a single parts washer, “it doesn’t make sense to drain out and waste all that detergent. You can get by with running shorter cycles using an all-purpose detergent with aluminum. It can minimize the impact of the discoloration. But if you run it for a long wash cycle, you’re going to get discoloration. It’s a challenge when you’re trying to use two different base materials in a parts washer.”
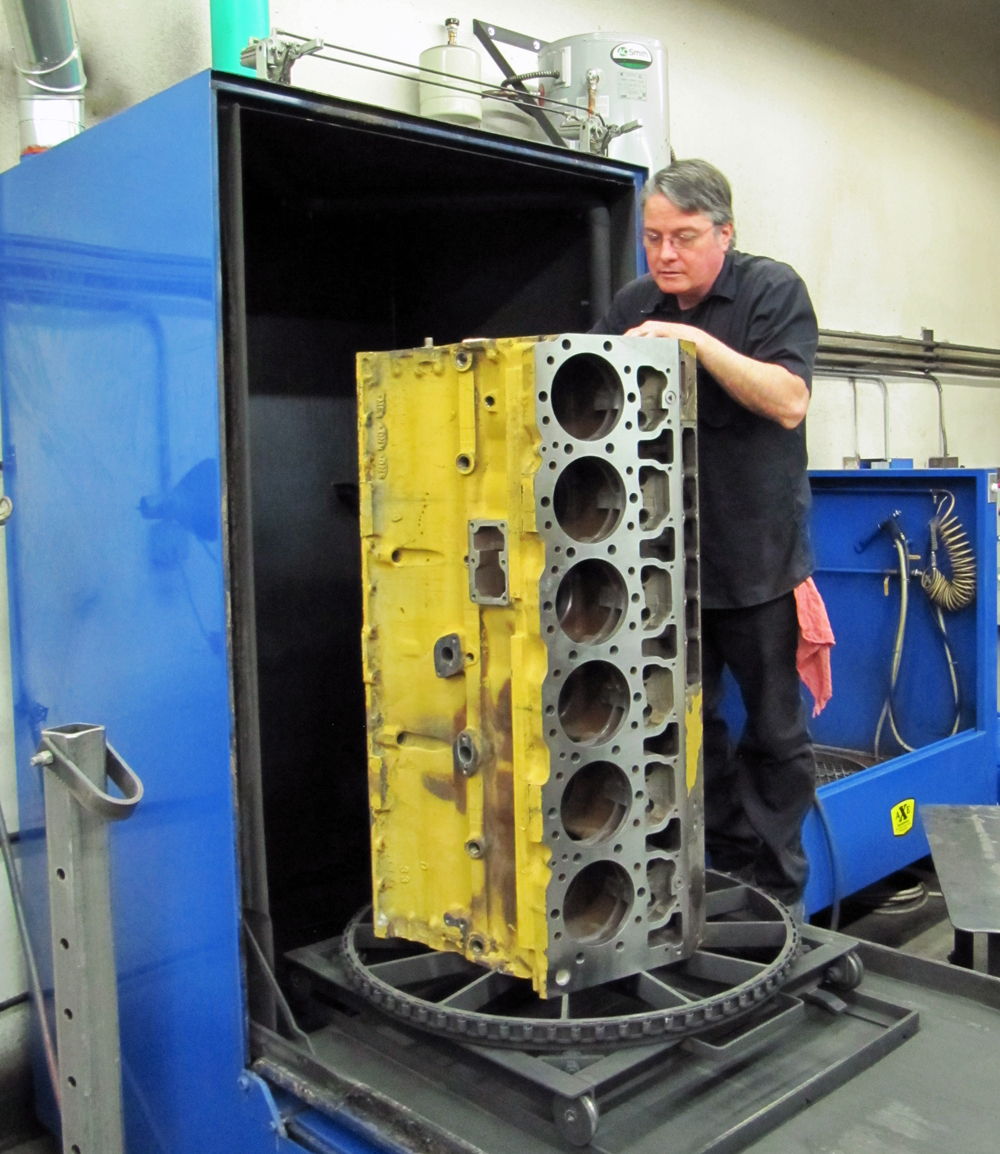
In an ideal world, Crabb said, a busy shop would have two machines, one dedicated to cast iron, the other to aluminum. For those shops that can’t afford that, he recommended using aluminum cleaner for both cast and aluminum parts. “That aluminum cleaner with high heat and good pressure will clean probably 70%, but it’s not going to cut any carbon, not going to take off any paint, not going to really cut that heavy sludge.” In those instances, “they should do a little bit of hand massaging before they put the part in there, scraping off some of that big stuff.”
To help in these situations, AXE manufactures washers “with a built-in hot tank in the front,” Crabb said. “You can soak a block or a pair of heads in our hot tank while you’re spray washing up in the top.”
These same kinds of detergent choices apply to ultrasonic washers as well, Shaw said. “We offer several different detergents depending on the kinds of parts they’re cleaning. Anybody who’s dealing with billet and racing parts exclusively should use our Ultra 3. It’s definitely the safest for that kind of thing. If you’re cleaning diesel reman and dealing with cast iron, ferrous metals, and old school parts coming out of a junkyard, Ultra 1 is the most aggressive. Ultra 2 is our mid-grade, for people cleaning a variety of parts.”
“There’s always new chemistry and new media coming out,” Oryszczak said. “It uses our same style of equipment, but there are options that make using that equipment more user-friendly.” One example he cited was a chemical mixing system “that automatically siphons the correct mix of chemistry and water. The best analogy I can think of is this: Do you want to be the fifth person in line for a bath with the same water after me and four other guys? Just recirculating the water? Or would you rather take a shower where you’re not recirculating the water? Where are you going feel clean? Same with your parts.”
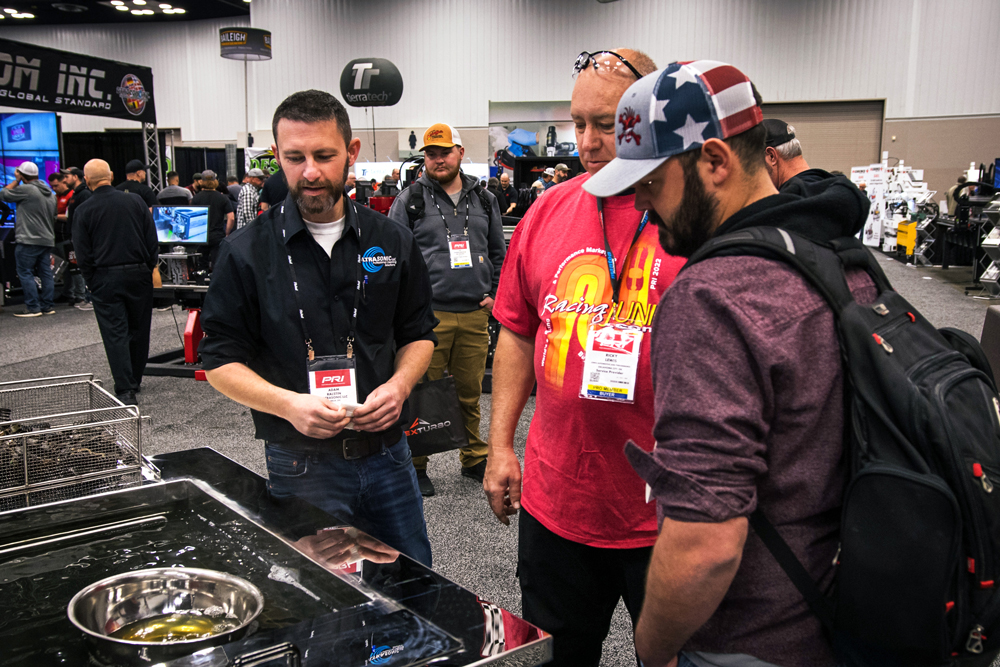
On the subject of recirculating cleaning water, depending on how busy the shop is, cleaning solutions should be changed about four times a year, Crabb said. “But I’ll bet many rebuilders only do it twice a year. Nobody wants to clean these things. They’re filthy.” What happens more often is the water that naturally evaporates due to the high temperatures is replenished. “When they lose 10 gallons, they’ll add 10 gallons and more chemical.
“But there’s risk to that,” he continued. “When they go home on the weekend, and that water gets cold, all that stuff gels together, and it falls on the bottom. It’s not coming back up until you take it out. If they’re not mindful, they’ll get a big sludge buildup down there, which is going to insulate the heater. Now it’s not going to heat up right.” Fortunately, there are service agencies, including Safety-Kleen, which will “come in and suck that sludge and the water out of there and take it away for you.”
Environmental Impact
Mentioning washer water removal brings up another aspect of parts washer ownership that shops need to consider: the environmental impact of the machine.
“When you buy these water-based cleaning products like ours, there’s some responsibility that comes with it,” Crabb said. “What are you going to do with all the mud that’s collected down in the bottom? There’s lead content in all the stuff we’ve washed out of the engine block. If you’ve stored it out in the backyard, it’s all going to leach down into the ground, and the EPA doesn’t like that. It’s something to be mindful of when you’re buying these things, even ultrasonics.”
Having an agency like Safety-Kleen remove the wastewater and sludge is a good first step, Crabb said. AXE also manufactures a Rinse Booth that retains and recycles the rinse water inside the booth’s reservoir. “It’s a closed-loop system. We call it ‘No drain, no EPA pain.’ We take them to the PRI Show every year, and we sell them all the time.”
Crabb also suggested that shops add a line for waste disposal fees in their invoices, much like tire stores and oil-change stations do, to offset the costs involved with properly disposing of the water. “Otherwise, they’re cheating themselves. And I wouldn’t bury it in the price of the product. I’d put it on a separate line just like they do with tires.”
Return on Investment
“You don’t make money cleaning parts,” Haworth admitted. “It’s a process, but it’s not a profitable part of the process. It’s something you have to do. But I’ve done so many ROIs, and there has never been a case where a parts washer didn’t pay for itself in less than a year. Do the math: You pay a kid minimum wage to stand out there with a pressure washer. Or you waste the time of a technician who’s bent over a wash tank trying to clean a part. Within a year, a $10,000 parts washer pays for itself. You can’t hire a person and pay an annual wage of $10,000. Well, not in this country. It just pays for itself. You put a part in it, you turn it on, you walk away, you come back, and your part’s clean.”
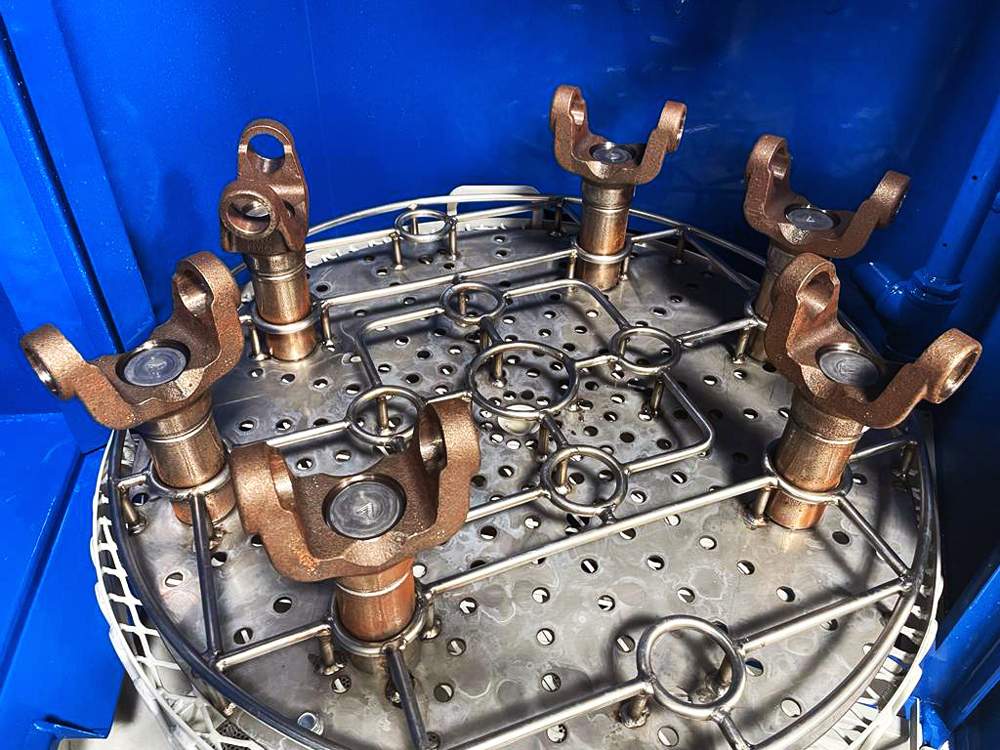
“An UltraSonic machine never takes a break. It doesn’t take a vacation. You get the same precision cleaning job every single time,” Shaw said. “Even a tabletop cleaner has merit and value. Then, depending on what you’re doing, you can move up to a larger unit. Now, instead of spending half your day cleaning heads, it’s doing that for you, and you’re on to assembly or machining. You’re increasing your volume, and it will increase your profit. It will change your life.”
Haworth called a parts washer purchase a “100% get what you pay for” situation. “When you’re making an investment in a parts washer, a few thousand dollars can make a difference between a two-year machine or a 20-year machine. I have machines still running, that run every day, which were built in the 1990s. You want to make a solid purchase, a one-time purchase if possible, and have a machine that will be around a long time.
“I rarely replace the machine,” he added. “If I sell a repeat to a customer, it’s because they’ve added on, and they need more machines. It’s not because their machine wore out or fell apart. They’ve grown, and they need another machine.”
Final Thoughts
“How can someone get the best results from their parts washer? Pick up the phone and call a metals finishing expert,” said Oryszczak. “There’s a lot to be gained by talking to an expert. There are minor details that you may divulge in just general conversation that could be key to helping figure out what you’re doing. We can help figure out if they need equipment. Do they just need to tweak their process? Are they using actual chemistry, or are they using Dawn dish soap? Seriously, you can’t make some of this stuff up. Do they need heat? Are they doing this in a parts washer? Are they doing this in a vibratory, a tumble cleaner? Are they doing this in a blast cabinet, a slurry blast cabinet, centrifugal barrel, ultrasonic cleaner? There are so many methods to do this.”
Giant Finishing will even accept sample parts, “and we’ll process them free of charge” to help solve a cleaning problem, Oryszczak said.
“These machines are a lot like air compressors, in that people put them up, and when they stop working, that’s when they take care of them,” Crabb said. “Nobody cares about them until they’re broken. The performance people are better than most, but the engine rebuilding businesses in general don’t take care of them very well. But this is our 40th year. We rolled out the first machine in July of 1984. And we still have machines out there. If you take care of them, these things will last you 25 to 30 years. No problem at all.”
Sources
AXE Equipment
axeequipment.com
Giant Finishing
giantfinishing.com
Safety-Kleen
safety-kleen.com
Temco Parts Washers
washparts.com
UltraSonic LLC
ultrasonicllc.com