Tech Transfer
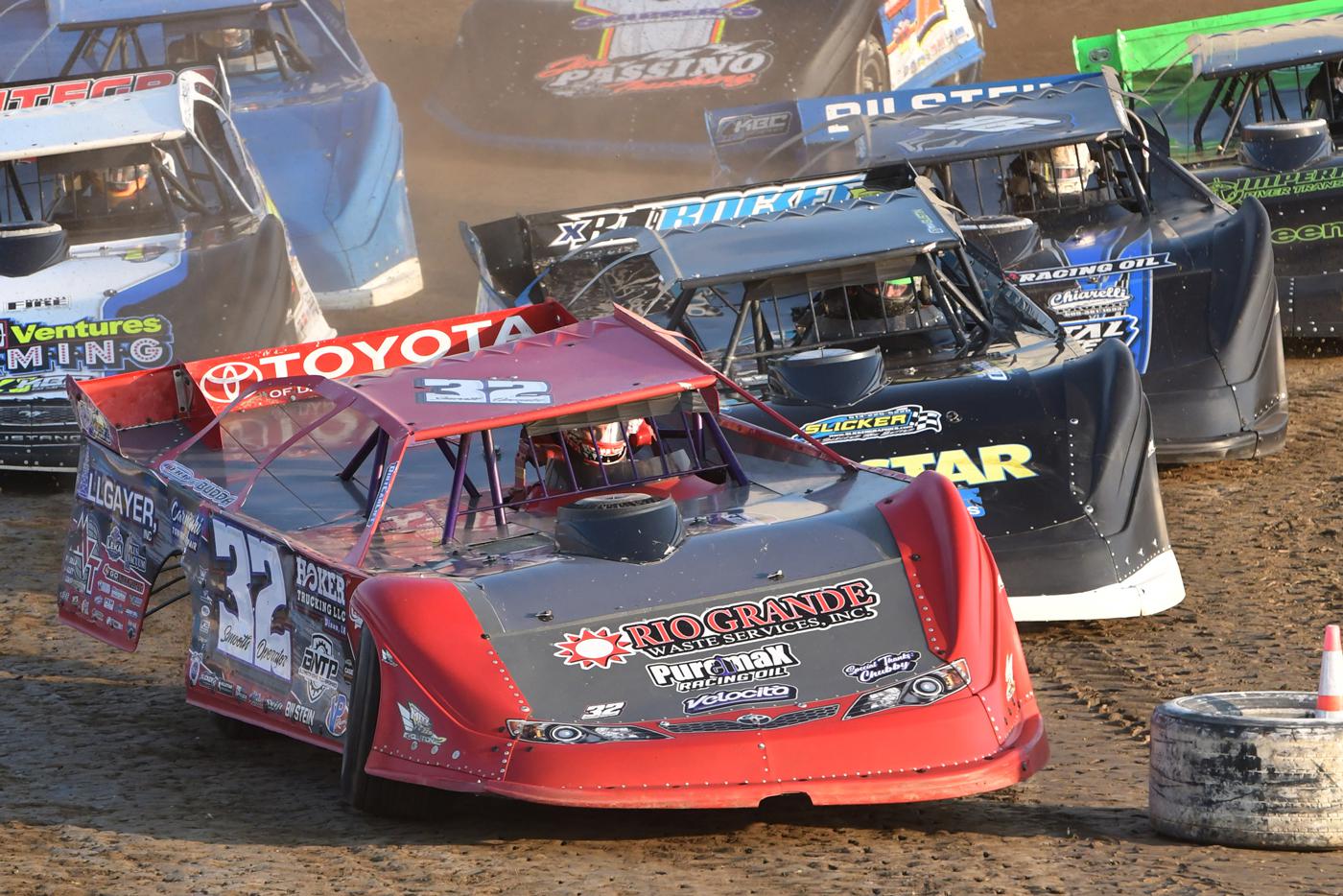
On-track validation is still an important aspect of race car development in dirt late model racing, but data acquisition, wind tunnel testing, and simulation have also taken on increasingly pivotal roles.
While the overall design of the cars has largely remained constant, over the past decade or so, the setup of dirt late models has taken on an increasingly sophisticated approach. Rather than focusing on extracting every last ounce of power from the engine, these days most teams are more concerned with grip, and how suspension, aero, and other tuning strategies can affect it.
“I think that if you look at a 10-year-old car compared to today’s car, the chassis are very similar,” explained Aaron Lambert of Penske Racing Shocks, Reading, Pennsylvania. “The bigger changes are happening in the technologies that are being used—how data is collected, and how we do testing. As more folks come in with experience from NASCAR, and other forms of racing where aerodynamics plays a big role, it has definitely affected where dirt late model teams are focusing their efforts. If you can find an aerodynamic advantage over your competitors, it can be a game changer. Mechanically, everyone is running very similar equipment. So if you can gain a 10% or 15% improvement in aerodynamic efficiency, it’s nearly impossible for your competitors to overcome.”
Finding these aerodynamic advantages—and replicating them in a predictable, repeatable manner—is easier said than done, though. Whereas the surfaces in pavement-based disciplines tend to stay fairly consistent throughout a race weekend, in the dirt world surfaces not only vary widely from venue to venue, they also often change considerably throughout the course of a race.
These changes affect the car’s mechanical grip levels as well as its posture at speed, which in turn affects how the car’s aerodynamics function. Suspension setup, chassis flex, and even the proximity of other cars can also significantly impact the effectiveness of the aero, making it difficult to pin down strategies that will yield repeatable improvements. As a result, many manufacturers and teams are leaning more heavily on technologies that will allow them to account for these variables. While these solutions often require significant up-front investment, they can actually end up keeping costs down in the long run.
Getting Scientific
“We used to scale the car on the ground, and kind of guess to where it was going,” said Mike Nuchols of Warrior Race Cars, Seymour, Tennessee. “If it hit the ground during the suspension’s travel, we would just add spring rate to the corners to make changes. These days we know exactly where it goes to, and we’re really not changing spring rates much—we’re manipulating cars with 1/16 of an inch packers. The window of adjustment is much smaller now, and there’s not a lot of guessing anymore.”
The use of data acquisition systems over the past few years has provided teams with a wealth of proven information to pull from, which has in turn reduced the amount of time and effort required to establish a solid baseline setup for these cars. These systems can also provide the insight needed to further refine the setup with smaller changes, Nuchols explained. But that is only part of the process.
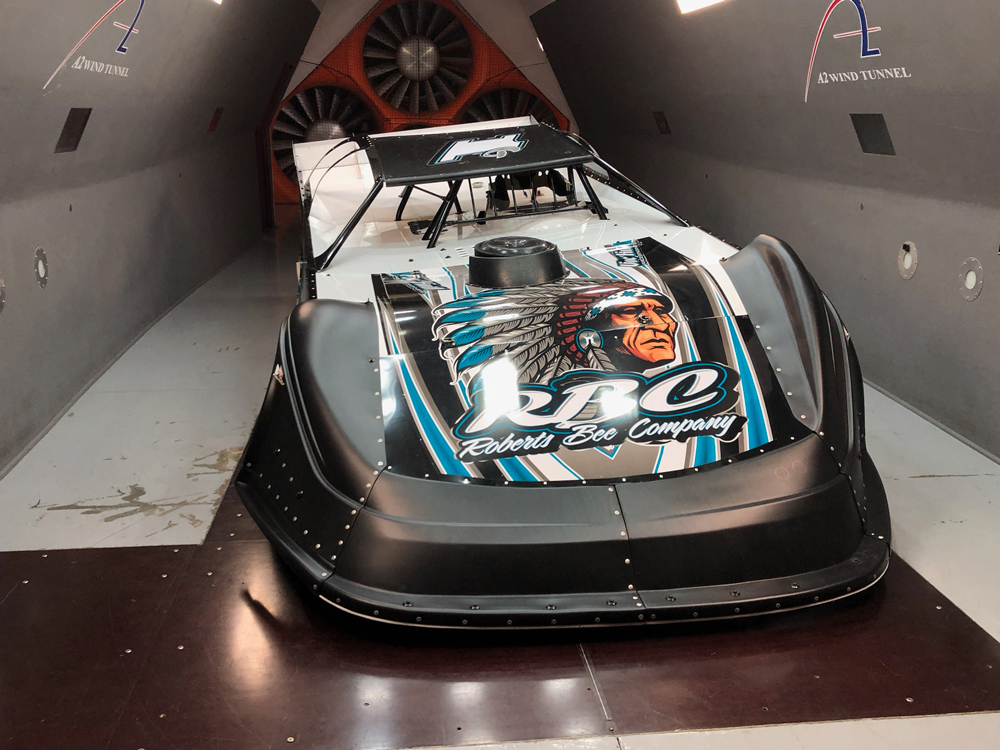
“We’re still in the early stages of figuring out what body manipulations we can do to the car to make them better,” he said. “The first time we went to the wind tunnel, we tried a lot of old school tricks that were suggested to us, and we didn’t see changes with a lot of it. There were some other things that we initially didn’t think about doing that ended up making huge changes, like air cleaner deflectors. If you have an air cleaner that’s 90 degrees to the hood, it immediately shoots the air over the deck, and over the car. Just changing the way the air rolls over the top of the air cleaner can keep the air stuck to the car for longer across the deck and get it to the spoiler. A minor change like that can make a big difference.”
But he’s quick to note that wind tunnel testing has its own limitations. “We can put the car in attitude as far as rake front-to-rear, and we could yaw it out about three to five degrees at the wind tunnel we went to. The problem is that our cars run at about 15 to 20 degrees of yaw on corner entry, so we’re still not getting a full picture of what’s going on in terms of side force and air blowing across the car.”
While there are wind tunnel facilities that can replicate those on-track yaw angles, Nuchols said they can cost up to $2,000 an hour, making them prohibitively expensive for routine testing for most teams.
“That’s where CFD [computational fluid dynamics] testing comes in. It requires a big investment up front—probably $20,000 to do initial scanning and things like that. But in the long run, simulation is probably going to be a lot cheaper,” Nuchols noted.
As Steve Arpin of Longhorn Chassis in China Grove, North Carolina, pointed out, leveraging simulation technology can also potentially speed up development. “For example, let’s say you have a new left rear suspension configuration that you want to test. If there are 10 steps involved in vetting whether or not it’s going to be beneficial, simulation can fast-track the process because you don’t have to go through each one of those steps manually. You might already be at step five before you have even hit the race track. That has really revolutionized the development process. The math doesn’t lie. If you can work through the numbers ahead of time, it takes a lot of the guesswork out.”
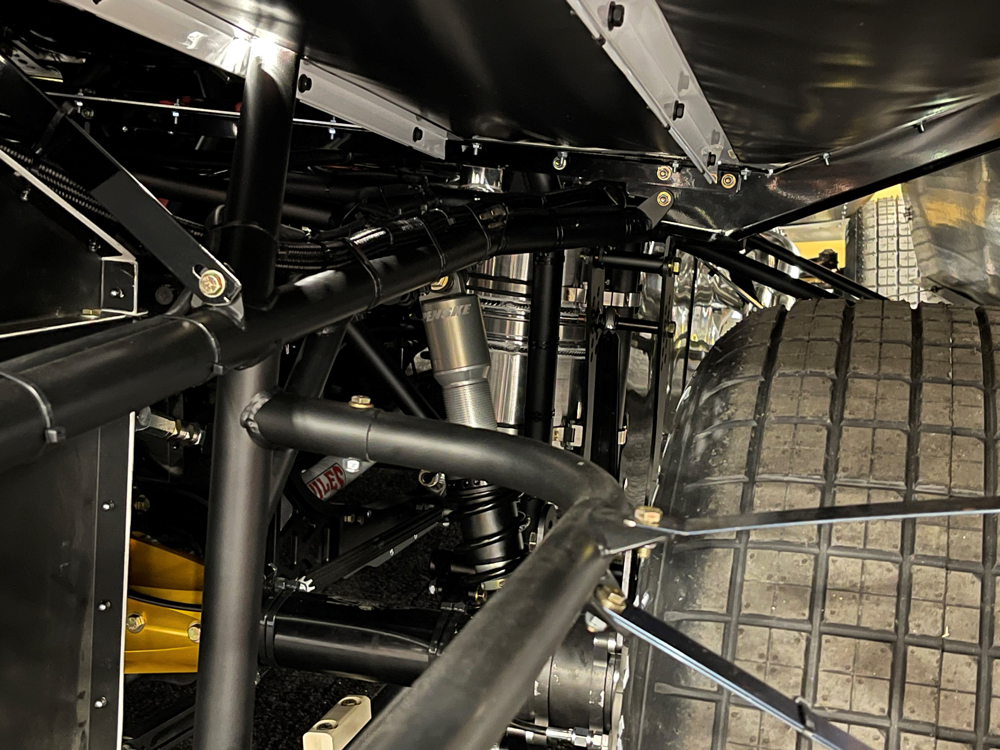
Simulation’s usefulness extends to many other aspects of dirt late model car design as well. “Teams are starting to realize that the brake packages have evolved, too. It’s not just the same old technology,” explained Travis Gorsuch of Gorsuch Performance Solutions, Chanhassen, Minnesota. “Today we have a lot more tools to work with to help these racers fine-tune the car, and brake system adjustments can affect the whole setup.”
The company has used finite element analysis (FEA) simulations to help guide the design of the vanes in its brake rotors, which Gorsuch reported yielded improvements in airflow through the disc as well as more consistent heat absorption throughout the rotor, the latter of which reduces the occurrence of hot and cold spots that can cause cracking.
“A lot of our calipers have gone through FEA simulations for strength,” Gorsuch continued. “If a caliper flexes when you step on the brake pedal, it’s going to feel spongy. At the same time, we want to keep the weight down as much as possible. So this allows us to optimize the design by determining where we need material in the caliper and where we don’t. If we can design something that allows the driver to modulate the brake pedal with more precision, it’s going to give them better feedback about the car’s setup on the whole.”
Purpose-Built Solutions
Lambert noted that computational fluid dynamics simulations that also helped Penske develop position-sensitive shocks encourage the car to stay in its ideal aerodynamic posture. While many position-sensitive shocks are designed to stiffen as the shock compresses, these are designed to provide more compliance through the middle of their travel, which takes some of the burden off the tires to absorb the energy from cornering loads and inconsistencies in the race track surface. Lambert admitted, though, that there are still limitations to this type of technology.
“You really need a race atmosphere to see where you’re at. Once you get 10 or 15 other cars on a track you get dirty air, you get cars running different lines, and the conditions really change,” he said.
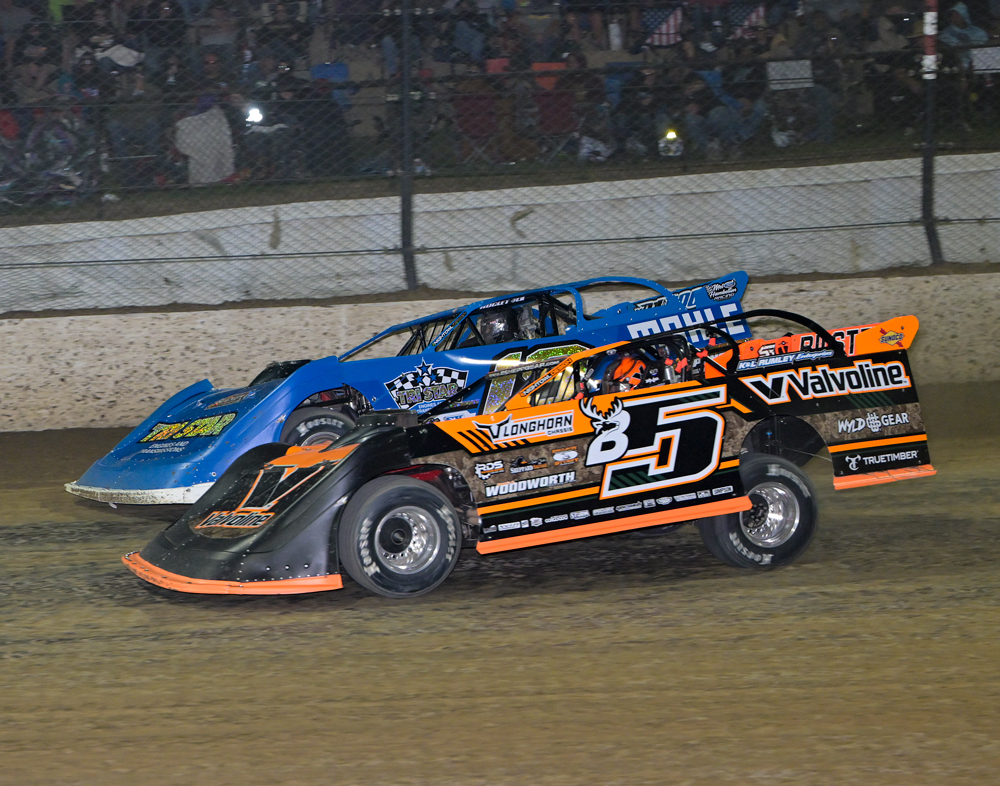
Penske is working on an answer to that as well. “We’re developing a simulation program that will allow us to import parts of the race car—the chassis, all of the suspension pieces, and so on—and apply inputs to them,” said Lambert. “That will allow us to run virtual laps around a track, make changes, and get immediate feedback about how that alters the performance of the car. So if we change the load by X amount on the left front, it also shows us how that affects everything else and gives us a theoretical lap time. It’s similar to what we’re seeing in NASCAR, IndyCar, and Formula 1. Simulation is the world they live in. It’s expensive initially, but when you look at it from a dollar-per-lap perspective, it’s much cheaper.”
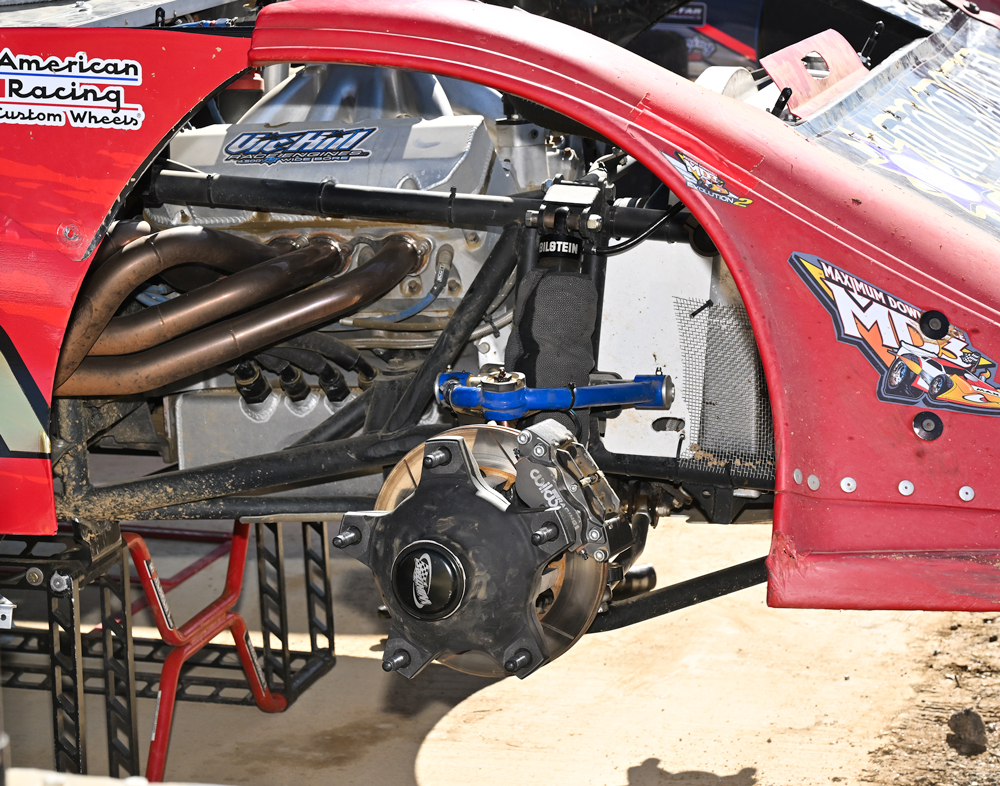
He added that while the software currently looks at the radiuses of the corners and angles of the banking on a given track, future versions are expected to include track surface condition data as well. “Characterizing the condition of the dirt is probably the hardest part. What is a heavy track with a lot of grip, and how is that different from a slow track that’s really slick? Fortunately, we have a lot of feedback and data to work with from teams and drivers. Once we have a really good race track in simulation that correlates to the real-world data, we should be able to say, ‘OK, let’s degrade the track condition 15% and see how that affects the car.’”
Meanwhile, Arpin told us that achieving repeatable results is one of Longhorn’s primary objectives with its chassis. Since the chassis’ flex is effectively a part of the suspension system, he said it’s crucial that the design yields a consistent spring rate.
“As you go into the corner, your right front tire is the first thing that gets there, and the load comes into the chassis from there,” he explained. “As you leave the corner, the load is being transferred back to the race track through the left rear tire. So it is about figuring out what is happening in that chassis during that time. That is all spring rate, and we want to make sure that is consistent on every car we build. That way when we make an adjustment on one car, that same adjustment is going to create the same effect on another one.”
In order to ensure that the adjustments they make will yield beneficial results, Longhorn Chassis has partnered with two different companies to develop two simulation models, one focused on the mechanical elements of their cars, the other on the aerodynamics.
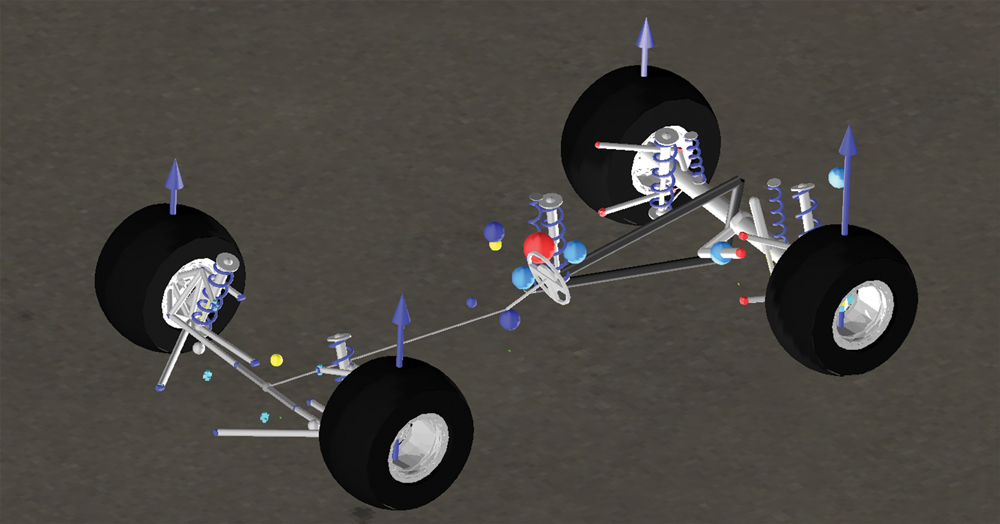
“The models are independent of each other, but the information does transfer back and forth between the two camps,” Arpin said. “For example, if we find that we can make more mechanical grip in a certain posture, we’ll then go to the aero side, put the car in that posture, and measure how it affects the aero. That can go a couple of different ways. We might gain 8% mechanical grip with this change, but the posture reduces the aerodynamic grip by 10%. Assuming that in this scenario the mechanical grip and aero grip are equal to each other, we actually have a net loss. So you have to work them back and forth with each other to find a good balance.”
Like Penske, Longhorn Chassis is also working to bring greater accuracy to the simulations it’s using in order to develop and test its products more precisely.
“When you go to a wind tunnel, you can only measure one race car. The problem is that you’re basically just simulating being on the track by yourself for qualifying, and we don’t win trophies for qualifying,” stressed Arpin. “So we’ve chosen to invest in CFD technology that allows us to digitally place five or six cars in the wind tunnel together, and we can measure how that turbulent air is affecting the cars.”
Although dirt late model chassis haven’t seen dramatic changes in recent years, Nuchols said that as these development methods continue to mature, that may be poised to change in the future.
“Over the past few years, the rule makers have started to clamp down on some of the shock technologies, so the focus may shift down the road. If we want to go faster, it may require a whole different type of frame. The chassis rules are pretty vague right now—they are mainly focused on safety. So it seems like there is still a lot of room to innovate there.”
SOURCES
Gorsuch Performance Solutions
gorsuchperformancesolutions.com
Longhorn Chassis
longhornchassis.com
Penske Racing Shocks
penskeshocks.com
Warrior Race Cars
goddardwarrior.net