Controlling The Flow
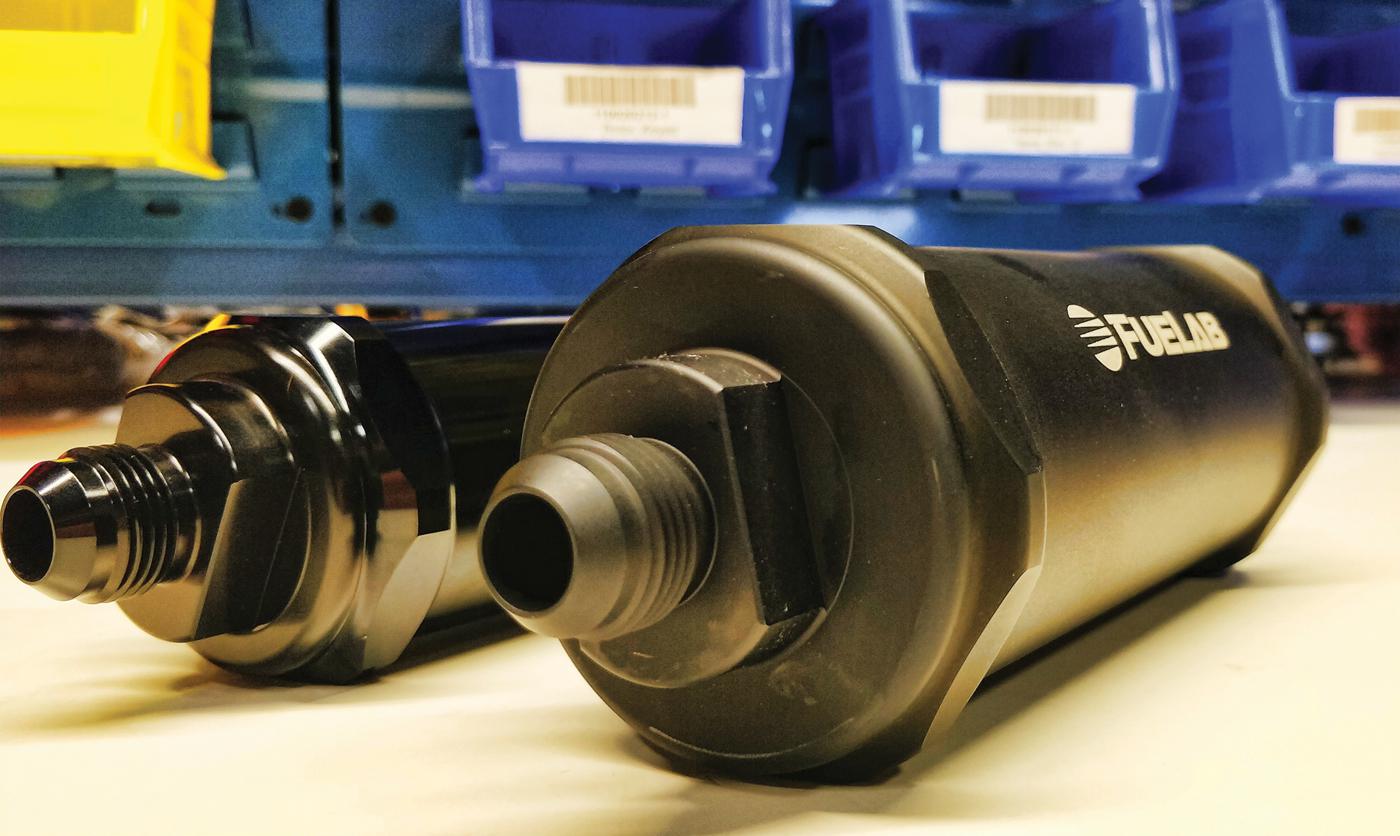
Considering the different types of pumps, fuel choices, induction systems, car styles, and intended applications, parts selection can be complex. Fortunately, our experts are here to help clarify and simplify the process.
Fuel pumps aren’t supposed to be sexy. They’re like a pair of work boots, or a trusty hammer, or a good helmet. They’re there to do a job. If you notice them, there’s probably something wrong.
But without fuel pumps nothing happens in a race car—instead of the sweet music of internal combustion, you’re left to absorb the deafening sound of silence.
What’s more, the work of fuel pumps is actually more complicated than it might first appear, with a demanding array of criteria driving the choice of which one to use. And if you get it wrong, you could not only lose races but destroy expensive components in the process.
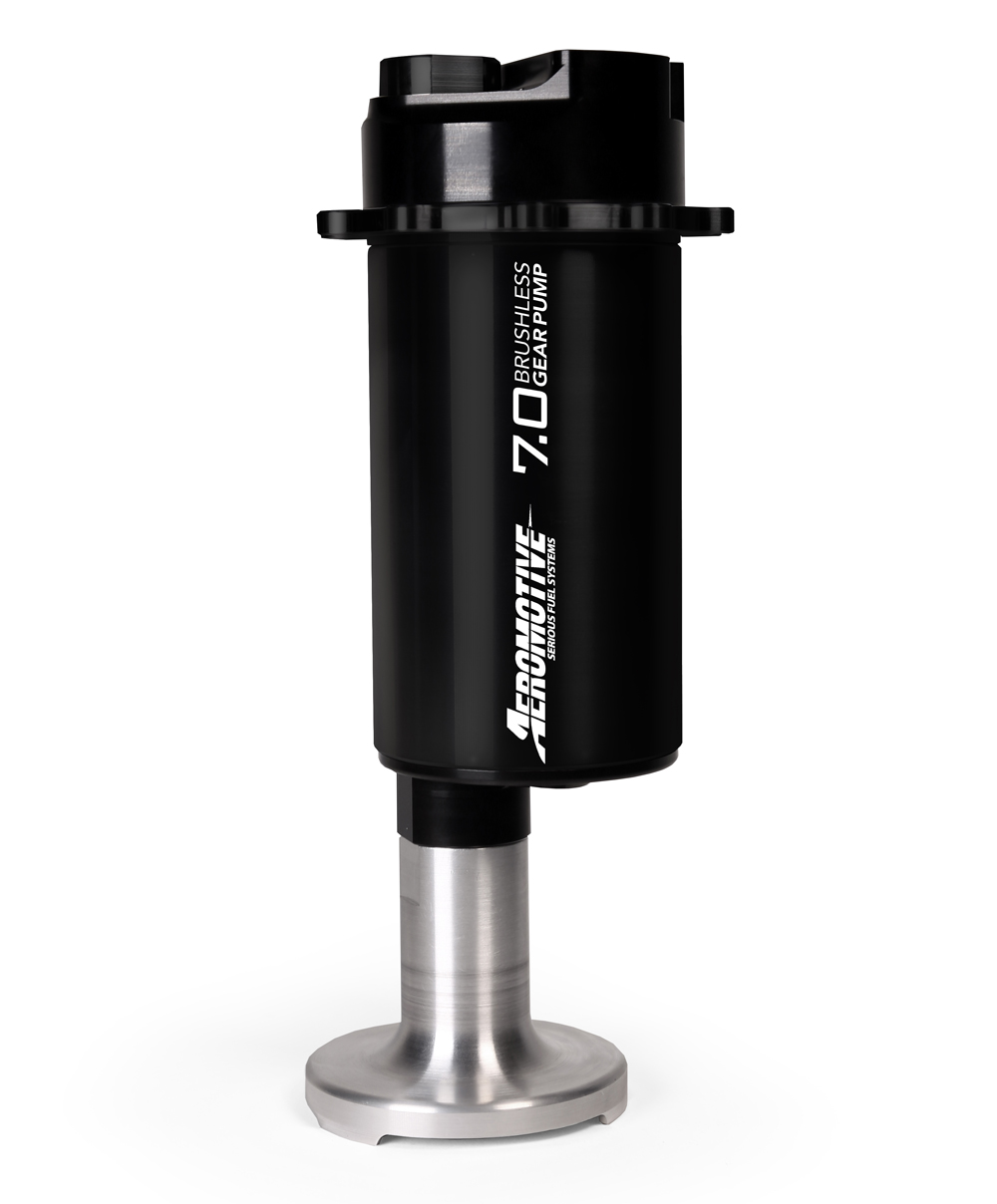
To learn more about these essential unsung heroes of the motorsports world, we talked to leading fuel system experts for their insights and recommendations on the subject. They took us through the different types of pumps, best applications, and the pros and cons associated with each one.
Electric Pumps
Of all the fuel pump types being used in motorsports today, electric pumps are the most common. They’re found in everything from simple carbureted bracket cars to 3,000-horsepower, twin-turbo, fuel-injected beasts. Much of the popularity of electric fuel pumps stems from their sheer versatility. Name almost any imaginable combination of car, engine, or induction system and there’s probably an electric pump for it.
Electric fuel pumps fall into two broad categories: inline and in-tank, based on where the pump is mounted. Each configuration has its own advantages and disadvantages.
Inline pumps are mounted outside of the fuel tank. One of the primary advantages of this configuration is its adaptability. Locating the pump outside the tank removes many of the space considerations imposed by mounting a pump inside the tank or cell. Because there are fewer size restrictions, a wider array of flow ratings and pump configurations are available. In addition, racers can even run multiple pumps in series if necessary.
That said, inline pumps can take more work to install. They need to be mounted below the bottom of the tank, and no further than two feet away from it so they can draw sufficient fuel into the pump. This can pose challenges in some cars, which can lead to compromised installations that reduce the fuel system’s effectiveness.
In-tank pumps are mounted inside the fuel tank or fuel cell. This configuration offers several significant benefits. “The advantages of an in-tank mounting system are one, you exclude the pump from environmental heat,” said Brett Clow of Aeromotive, Lenexa, Kansas. “That way it isn’t a target from external sources like exhaust or the pavement. And two, in-tank installations are cleaner and easier, because when you install the tank, you’ve installed the pump and pre-filter and everything. You don’t have to worry about how you’re going to get the pump low and close to the outlet of the tank and clear the wheelie bar or the suspension or whatever else may be going on in the back of the car.”
Another advantage of in-tank units is that the pump is submerged in fuel, which keeps the pump motor cooler. This can allow the pump to run more efficiently and extend its life. In-tank installations also tend to run quieter, which can be particularly important for dual-purpose race cars that do significant amounts of street driving.
One of the few downsides to in-tank fuel pumps is that they can be more challenging to install on OEM fuel tanks or on fuel cells that weren’t designed for the particular pump being fitted. In these cases, some fabrication and adaptation may be necessary.
Although the terms “in-tank” and “inline” seem straightforward enough, Clow noted a recently introduced wrinkle that could prove confusing. “The term ‘inline’ is kind of a misnomer,” he said. “It’s generally considered to mean the pump is outside the tank. But from our perspective at Aeromotive, we use the term ‘inline’ very specifically to define a pump in which the electric motor is in the fuel flow path. It runs wet.
“It’s a distinction with a difference in it,” added Clow. “When the motor is in the fuel flow, it can run continuously and not have the motor overheat. It’s cooled and lubricated by the fuel flowing through it.”
This brings up the subject of efficiency, a crucial concern for any fuel pump. The quest for greater flow in a smaller unit has led to the emerging trend of brushless electric motors for fuel pumps. “With a DC brushless motor, you typically get greater power for the given size of the package,” explained Rob Scharfenberg of Fuelab, Collinsville, Illinois. “It also gives you the ability to control the speed of the pump, so you don’t have to have it going full-out all the time. You can actually control it by your ECU. So, for example, we could have an electronic regulator that’s capable of controlling the fuel pump’s speed based on the sensed demand within the system. So if you have a really high-horsepower application, you don’t have to pull so much fuel pressure. You could make it more streetable.”
That said, not all manufacturers are on board the brushless bandwagon. “We don’t follow the buzzwords,” said Jim Craig of Weldon Pump, Oakwood Village, Ohio. “A growing faction out there are using brushless fuel pumps. But we don’t offer a brushless pump. Our pumps are the most efficient fuel pumps on the market. We draw the lowest amount of amperage but provide the most amount of fuel flow. Some of these brushless pumps are putting 18–20 volts to them to get them to spin enough just to keep up with one of our midrange fuel pumps.
“And you can only reduce the fuel flow out of a pump so much until you get to where you can’t maintain fuel pressure,” added Craig. “A lot of brushless guys are saying, ‘Well, my ECU can ramp it in and start from nothing.’ But you still get to a point where you can’t maintain pressure. So it’s only reducing volume so much.”
Mechanical Pumps
At the basic level, fuel pumps that are powered directly off the engine are considered mechanical pumps. At the lower end of the mechanical pump range are legacy OEM-style pumps. These are generally diaphragm-style pumps mounted to the engine block in the factory location, fueling carbureted engines. Although most forms of motorsports have abandoned OEM-style mechanical pumps, they’re still required by many stock-car sanctioning bodies and in some stock classes of drag racing. For most street-stock dirt-track racers, these pumps are the only approved choice.
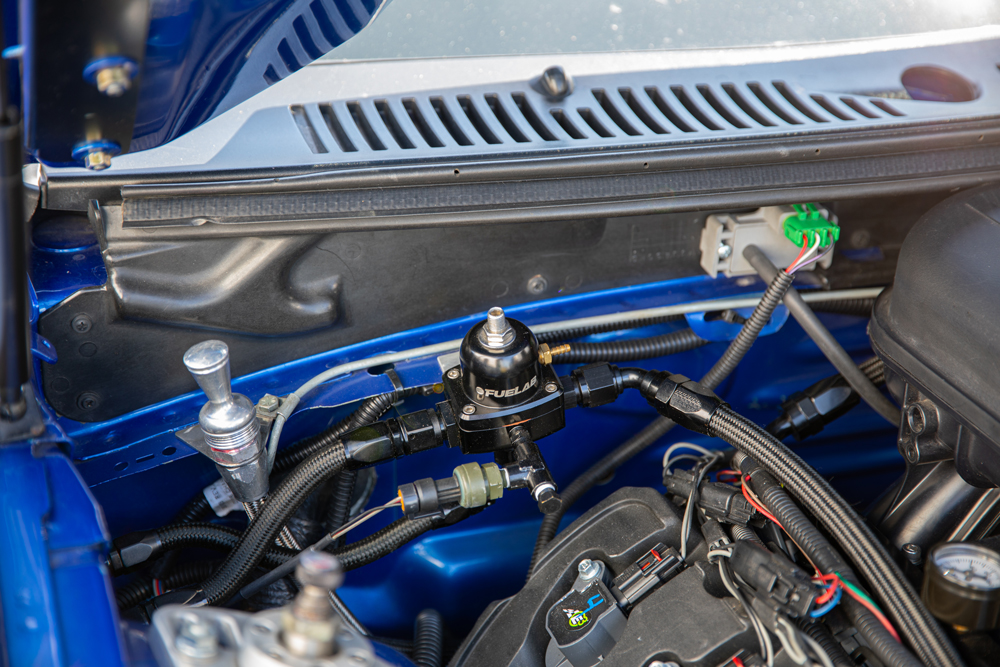
The fundamental advantage of OEM-style mechanical pumps is their simple, proven design. No external fuel regulator is required, there’s no additional work to mount them, and the technology itself is durable and reliable. As the mandatory choice in several extremely popular types of racing, these pumps still see widespread use. And so, despite their limited flow capability and complete unsuitability for EFI applications, many suppliers still offer a full product line to serve racers that are required to run them on their engines.
Also commonly used in motorsports are direct-drive external mechanical pumps. These can be driven by a dedicated belt-and-pulley system, mounted to the back of an external oil pump, or run directly by the camshaft through a timing cover adapter. Direct-drive pumps are typically found on dirt-track sprint cars, late models, and modifieds, as well as engines using mechanical fuel injection.
But perhaps the most dramatic application of this technology is in moving torrential amounts of fuel through high-horsepower, boosted drag cars. “The escalation of power was just outpacing the development cycle on electric fuel pumps,” explained Clow. “How do we make more power with a given engine? We just throw more boost at it. We get bigger turbos, bigger blowers, the boost goes to 25, 35, 45 psi, and your total fuel pressure numbers are exceeding 100 psi. And it’s really in that area where a mechanical pump’s advantage is going to start to reveal itself.
“All fuel pumps have an efficiency factor,” Clow added. “They all have internal leakage as pressures go up. As the pressure increases, that leakage increases incrementally with it. It’s not a tremendous amount of fuel. But when you look at the flow curve on an electric pump, you see a more dramatic decline from low pressure to high pressure. What’s going on there is you’re seeing the electric motor with a fixed amount of torque slow down as the pressure increases. So you’d have both the flow losses across the pumping mechanism and the reduction in pump rpm. That’s going to result in reducing the flow available as pressures go up. But if you put a mechanical pump on the engine, that pump isn’t going to slow down.”
Despite their efficiency and high flow, direct-drive pumps have a disadvantage in that they can’t be used with a fuel cell mounted in the back of the car, unless a cumbersome cable drive is used to run a mechanical pump in the back. If a front-mounted mechanical pump is used with a rear-mounted fuel cell, vacuum will go so high at the inlet of the pump that cavitation can occur. This high vacuum flashes the liquid fuel to vapor at the inlet of the pump. The resulting interruption in fuel flow could put an end to a pass and possibly damage the pump at the same time.
Even with this limitation, direct-drive mechanical pumps have found a solid niche in motorsports. But, like so much else in racing, that position is in a state of flux, as continuing development of electric pumps moves the point at which a mechanical pump’s advantages outweigh the disadvantages. “We’ve been progressively increasing the capabilities of electric fuel pumps with our brushless gear pumps,” said Clow. “These pumps have come along to facilitate supporting these higher horsepower combinations on exotic fuels, without having to relocate the fuel cell to the front or put a big cable drive system in for a mechanical pump.
“But regardless of how much electric pumps evolve, there will always be a place for mechanical pumps,” admitted Clow. “They’ve earned a spot. With mechanical injection, that’s where you traditionally run a pump like that. And there’s also a small part of the marketplace, alcohol carbureted, where a mechanical pump and its variable flow characteristics allow us to cheat our fuel pressure a little bit, running low pressure at idle and higher pressure down track. And those markets will continue to be there.”
Choosing the Right Pump
When looking at the choices of fuel pumps, one thing quickly becomes very clear: It’s complicated. If you take into consideration the types of pumps, fuel choices, induction systems, car types, and the intended usage of the vehicle, there are many ways to get it wrong. And the results can be catastrophic. Besides losing races, improper fuel delivery can instantly ruin components or even grenade entire engines.
And unfortunately, the choices aren’t getting any simpler. With forced induction and EFI adding greater complexity, the stakes have gotten mighty high with regard to fuel delivery. “There’s a lot greater complexity that’s occurring today,” observed Scharfenberg. “So the challenge is navigating through a lot of that. The one thing that I think a lot of people need not be shy about is understanding that they need to learn something new. Unfortunately, I think there are a lot of guys out there that are going, ‘Ahh, I already know it. So I’m just going to forge ahead.’ And I think that that’s sometimes where they get into trouble.”
According to Matt Henson of DeatschWerks in Oklahoma City, Oklahoma, that kind of attitude often leads to common mistakes. “First off, many people don’t realize how fuel system pressure affects fuel pump flow—flow decreases as fuel pressure increases. People don’t understand that even though a pump is rated for 1000 hp, it may not support 1000 hp for them, because their particular system might be running different fuel pressures. Second, they don’t see how OEM fuel system designs affect fuel pump output. Modern OEM fuel systems use fuel flow from the pump for slosh control and fuel tank delivery issues. This robs fuel flow from the pump, lowering the amount of power it can support. Some guys will also undersize lines on the inlet side and they’ll kill the fuel pump. Or they’ll use excessive filtration or too tight of filtration on the inlet side, and they’ll kill a fuel pump, because you’re going straight to cavitation. So you have to size the lines, the filters, and the pump so that everything works in conjunction with the motor horsepower.”
Many racers try to give themselves some margin for error by intentionally choosing a pump that’s larger than they need. But this too has significant complications. “Let’s say, for instance, you put a fuel pump in your car that’s moving 200 gallons an hour, but your motor is only making 1,000 horsepower,” said Craig. “That means you’re constantly returning to the tank half of what that pump is putting out. That will start to heat the fuel. You’ll end up elevating the fuel temperature and turning fuel to vapor, which results in cavitation, erratic fuel pressure, and erratic performance.”
Manufacturers have plenty of information available online to help racers choose the correct pump for their specific application. But this can quickly become overwhelming, as racers grapple with factors like fuel weight, brake specific fuel consumption, and the relationship between flow and pressure. Fortunately, some manufacturers also provide far easier methods of choosing a fuel pump. A number of suppliers, including Aeromotive and DeatschWerks, have online search systems on their websites that guide customers to the correct pump choices, just by answering a few simple questions.
And all suppliers we spoke with agreed on one point: It’s always best to call the manufacturer’s tech line if you’re not sure of something. “Most guys will look online, because there’s a lot of information out there,” said Craig. “But 90% of them will end up just calling me. And then I walk them through it. I’m an educator of fuel systems.”
Fuel Cell Considerations
Fuel pumps are a central element of a cohesive, effective fuel system. But without the right components to complement them, they can’t perform the way they were intended.
Foremost among those components that must be carefully considered in a fuel system is the fuel cell. Designed to optimize fuel flow and reduce hazards in crashes, fuel cells are a vital part of a racing fuel system and are therefore required by sanctioning bodies for most types of competition.
There are three primary elements to a fuel cell: enclosure, bladder, and foam baffling. Enclosures are typically made of plastic, steel, or aluminum. This material serves as an outer shell to resist punctures in the event of a crash. For greater protection, many fuel cells have rubber bladders inside the enclosure. These soft inner containers are designed to absorb impacts without puncturing, by stretching and conforming to sharp edges during a crash.
Not all fuel cells have rubber bladders—they aren’t required for some types of racing.
But whether or not they have a bladder, fuel cells today are all generally filled with safety foam, designed to prevent fuel from exploding if it ignites. At the same time, the foam also limits fuel sloshing to ensure more consistent fuel delivery.
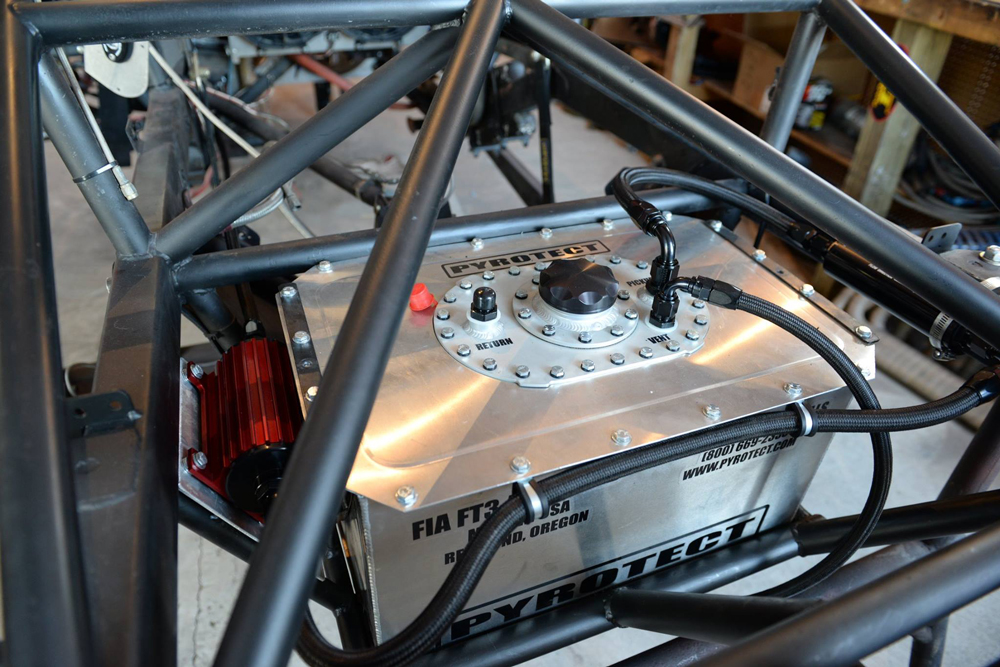
Ultimately, fuel cell choices are largely dictated by the sanctioning bodies. Therefore, the rulebook is the first place to start when considering a fuel cell. That said, many manufacturers feel there is still considerable room for improvement over what’s specified.
“Some rulebooks are extremely lax on fuel cell requirements,” said Dave Dack of Aero Tec Laboratories (ATL), Ramsey, New Jersey. “We always encourage racers to make sure the cell is equipped with check valves for both the fill and the vent, and most importantly that they choose a cell with an approval from a reputable, world-renowned organization like the FIA.”
Other manufacturers point to the importance of the mounting position and the risks a vehicle is exposed to when choosing a fuel cell, regardless of what’s required by the sanctioning body. “A good rule of thumb is that if the fuel cell is in a high-risk area, such as behind the rear axle, or in the side pod of the vehicle, you really need to have a certified rubberized bladder type cell,” noted Steve Russell of Pyrotect, Redmond, Oregon. “There are also circumstances, like in high-powered off-road race trucks, that carry anywhere from 80 to 120 gallons of fuel. For those we typically build in the next higher standard, even though it’s not required, just because of the sheer speed and impacts they can take.”
Beyond safety concerns, practical considerations like line size and mounting points are crucial in choosing a fuel cell. Given the complexity and nuances of fuel systems in general, this unfortunately leaves plenty of room for mistakes. “I see this all the time where guys will have a 3/8-inch or 1/2-inch standpipe for a pump that needs a 5/8-inch or a 3/4-inch pickup tube,” observed Brett Clow of Aeromotive, Lenexa, Kansas. “And the pump is going to suffer for that because it’s going to be starving for fuel, producing a lot of vacuum, and cavitating. And it can boil fuel, because of the restriction created by the suction side of the pump.”
To simplify the choices, there’s a growing trend in offering preconfigured pump and cell assemblies, which come already set up with the correct enclosure, pump, fittings, lines, and filter. Although the cost may appear to be higher than it would be when sourcing individual components, it can be nearly the same when everything is factored in.
“If you look at one of our fuel cells with a pump in the cell, on the face of it, it may seem kind of pricey,” said Clow. “But take and buy a fuel cell, some lines, hose ends, and a 100-micron filter, then compare it to the price of one of our cells with the pump already in it. There’s really not much difference.” —David Bellm
SOURCES
–
Aeromotive
aeromotiveinc.com
Aero Tec Laboratories
atlinc.com
BLP Racing Products
blp.com
BOOSTane
boostane.com
DeatschWerks
deatschwerks.com
FiTech
fitechefi.com
Fuel Safe Systems
fuelsafe.com
Fuelab
fuelab.com
Hot Shot’s Secret
hotshotsecret.com
Jones Racing Products
jonesracingproducts.com
Kinsler Fuel Injection
kinsler.com
MagnaFuel
magnafuel.com
Pyrotect
pyrotect.com
Schaeffer Manufacturing
schaefferoil.com
Weldon Pump
weldonracing.com