Core Competencies
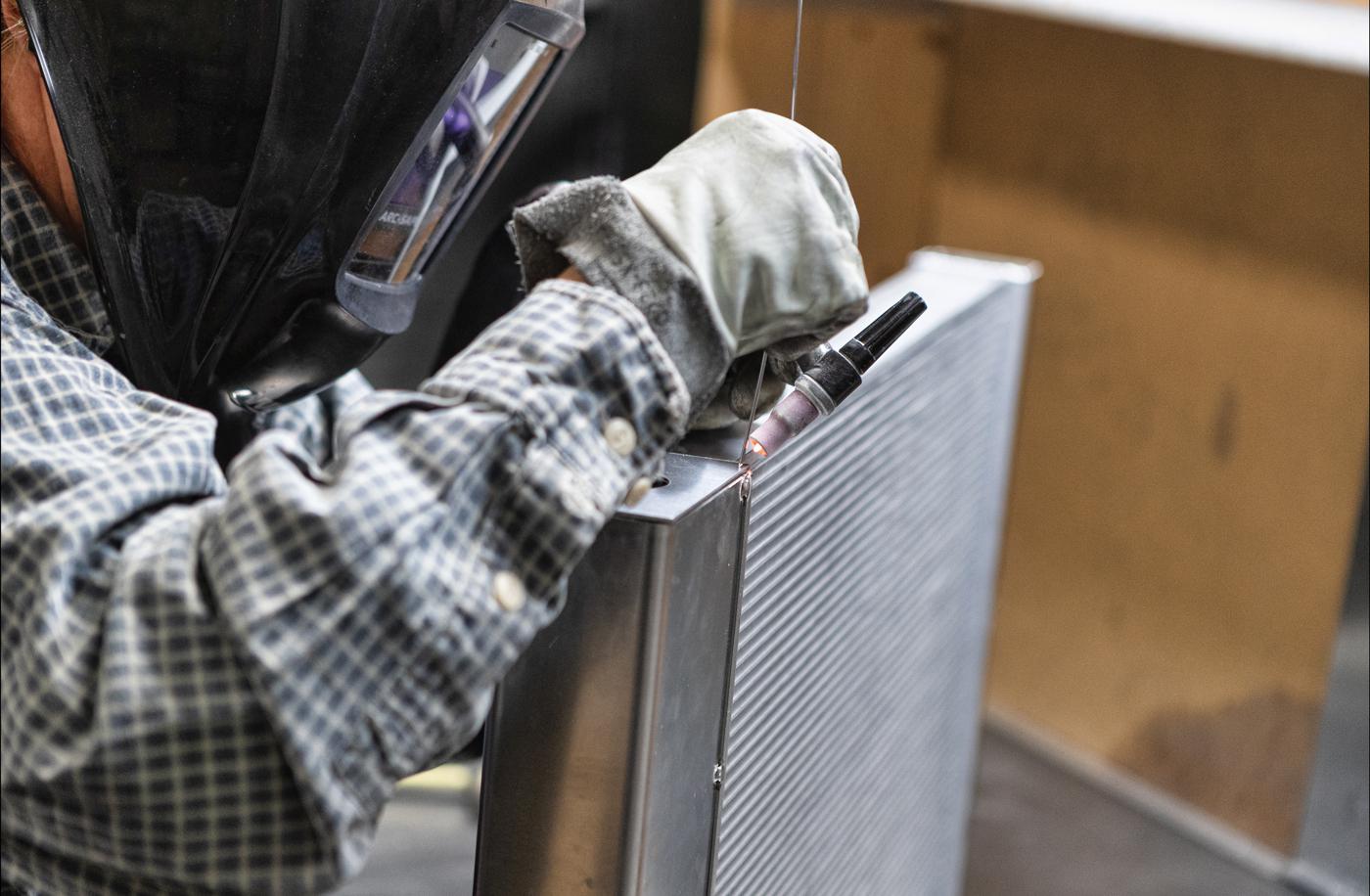
Our expert sources are here to troubleshoot temperature increases, size up (or down) expansion tanks, break down the differences in radiator type, and more.
One of the fundamental properties that all internal combustion engines share is the need to maintain a proper operating temperature. Run an engine too hot, and the resulting parts failure could prove catastrophic. Run an engine too cold, though, and it won’t operate as efficiently as it should. Now, take that bit of Auto Shop 101 knowledge and put it in the pressure cooker that is racing, and the risks—and rewards—of proper cooling rise dramatically.
It may be fundamental, but proper engine cooling practices require a knowledge and experience base that’s distinct from other engine functions. For that reason, we reached out to experts in engine cooling and asked for their most frequently asked questions from the racing community, as well as their answers.
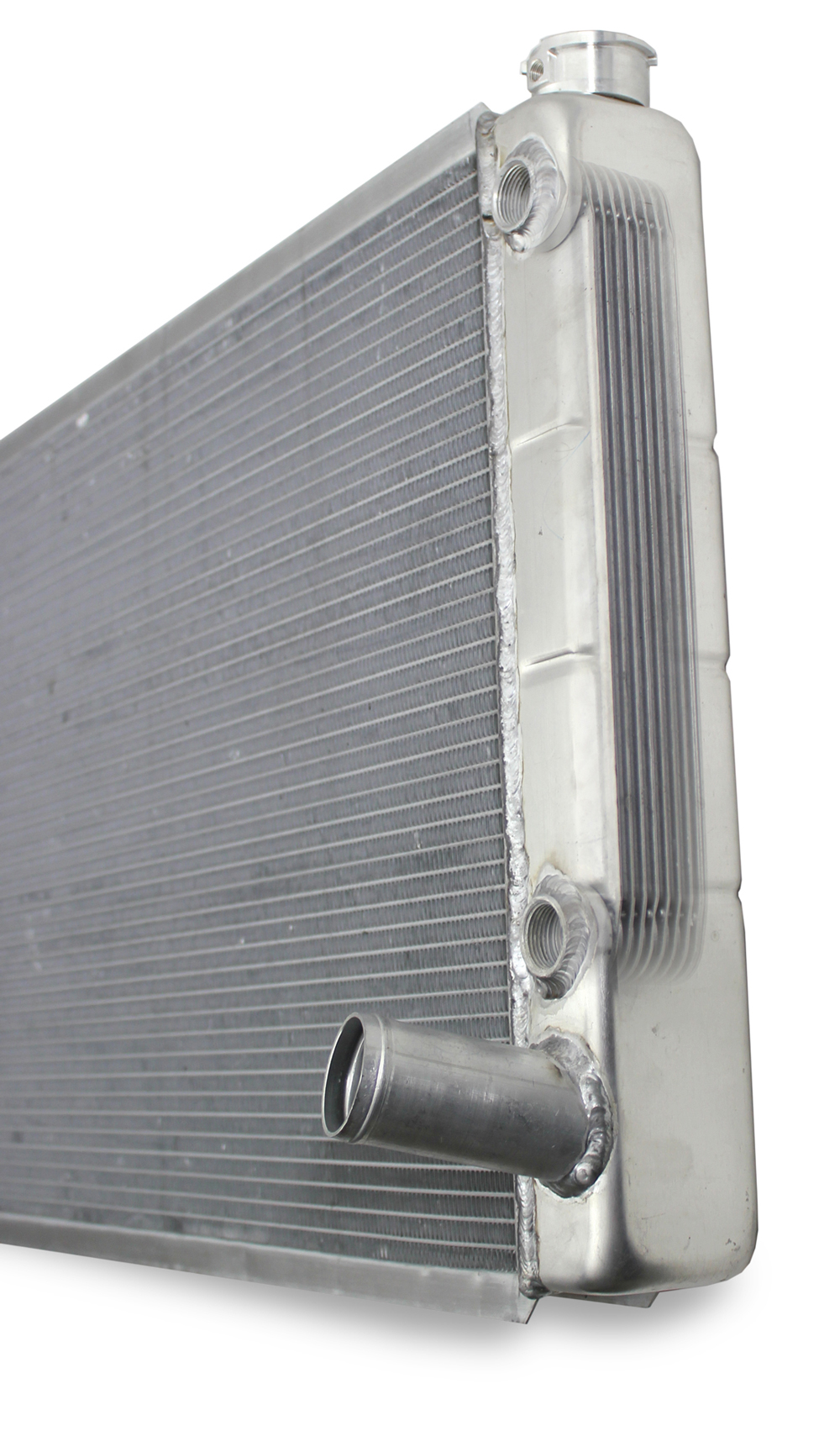
What are the differences among the variety of radiators available in the market?
The two main considerations when comparing radiators for racing applications are airflow and coolant/water flow and turbulence. Airflow technology is dependent on the core tube size and configuration, and on the fin size and configuration. Our sister company, Tube Wright Inc., developed several different cores that Power Cool uses to build radiators for racing applications: a 52-mm Ultra-High-Performance Core and 36-mm and 26-mm High-Performance Cores. These cores provide maximum heat transfer with or without the addition of a high-performance fan to deliver more cooling performance under extreme racing conditions.
The other factors that determine how effective your cooling system will be are the water flow rate and turbulence of that water as it passes through the tubes. Higher flow rate and high turbulence both work together to achieve faster and more efficient cooling at the extreme engine temperatures that racers need to be competitive. We advise teams to look for dimpled-core tubes, which maximize surface area of the water flowing through the radiator, thereby increasing the radiator’s cooling capacity. Power Cool’s Ultra-High-Performance and High-Performance radiators use this dimple technology. —Earl Lemley, Power Cool Systems, Indianapolis, Indiana
Is there a difference between a radiator used for racing and one used for another application, like a restoration?
Not necessarily. Most of our radiators have two rows of 1-inch aluminum tubes. They’ll cool your 1968 Camaro and your small block or big block modified circle track car that you take out on Friday or Saturday night.
But we do have a difference in our race product that other manufacturers don’t: an eight-plate oil cooler we call the Northern Super Flow Oil Cooler. Some manufacturers will put in what’s called a barrel cooler, a tube that sits in the tank. While barrel coolers are high flow, they have poor cooling efficiencies. The eight-plate design is the largest cooler that will fit in our race radiator tanks, and the plate design is highly efficient in heat transfer. It can also handle either a wet-sump oiling system or the higher pressure and volume of a dry-sump oiling system.
We also have single-pass, double-pass, and triple-pass radiators, all designed to help the racer dissipate heat based on whatever his issues might be. Sometimes a single pass through the radiator is not enough. A double-pass radiator gives the coolant two passes through the core, and a triple-pass radiator gives it three passes through the core. With a double-pass you’ll typically get an extra five degrees worth of cooling, while a triple-pass will give you 7% to 10% more cooling. Most double- and triple-pass radiators work well when you have limited airflow at the front of the car and you need that extra time in the radiator to help dissipate heat. —Chuck McKaige, Northern Radiator, Willmar, Minnesota
Is a thicker radiator core better than a thin one?
Let’s start by defining “better.” In a radiator, better would be defined as exchanging more heat under similar conditions. Heat is transferred from the engine coolant to the radiator fins, and then to the air that has been pulled through the core by the fan or a positive pressure area in front of the radiator. This air then travels to a low-pressure area out of the hood or into the engine bay. The job of the radiator is to remove as much heat as possible from the coolant.
Many assume that thicker radiators are automatically superior in cooling, but that is not the case. The most efficient core would be thin, but tall and wide, which allows the most amount of heat exchange. When you start adding extra rows, they get less efficient as you stack them. There is a point where too thick becomes a problem, as the incoming air becomes turbulent and the path of least resistance is no longer through the core. As technology progresses, we will evolve into cores that remain thin but contour to the chassis, providing maximum heat exchange in a previously unusable area. —Ryan Williams, FLUIDYNE, Mooresville, North Carolina
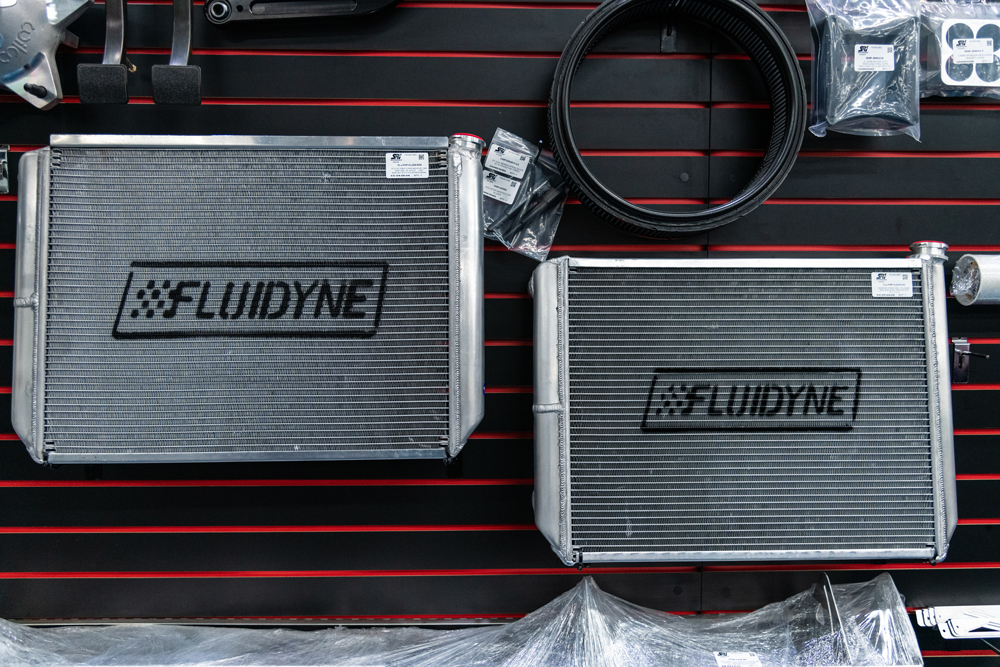
With the advancements in core technology, such as cooling tube and fin design, improvements have been made in heat rejection. This has allowed us to utilize thinner cores for a given application, and the thinner core gives us a more efficient core where airflow is concerned. With all things being equal, the thinner core will have less pressure drop from the front side to the back side of the core. This allows the velocity of the air to be higher, which in turn creates another positive situation in heat rejection. Within reason for the application, a thinner core is just more efficient with the given amount of airflow it’s seeing.
For example, where we previously used a lot of 55- to 68-mm cores, we can now use a 42-mm core and see better cooling. We also end up with a lighter part and less fluid weight. Obviously, there is a point of diminishing returns when it comes to using thinner cores. There will always be a minimum thickness that is desirable.
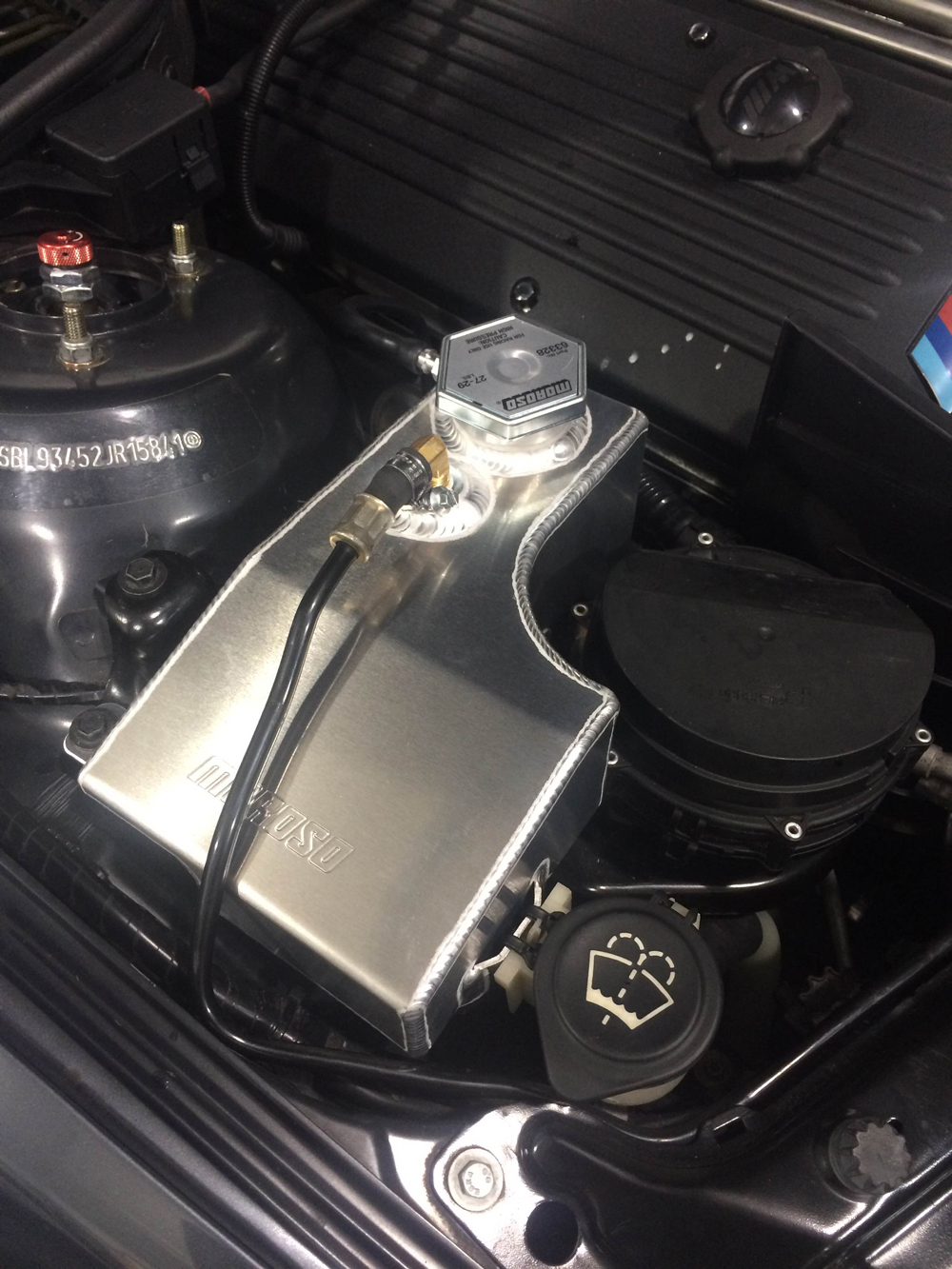
Another interesting point about core thickness: The thicker the core, the more the air heats up as it passes through it. Thus, the thicker core will have higher temps on the back side of the core, which can have a negative effect on water temp.
With [our partner] PWR building its own cores in-house, it gives us great latitude when it comes to core thickness, cooling tube and fin type, as well as fin density, where we can tailor a core spec to a specific set of parameters for a given application. —Herb Engelhart, C&R Racing Inc. (part of PWR Advanced Cooling Technology), Indianapolis, Indiana
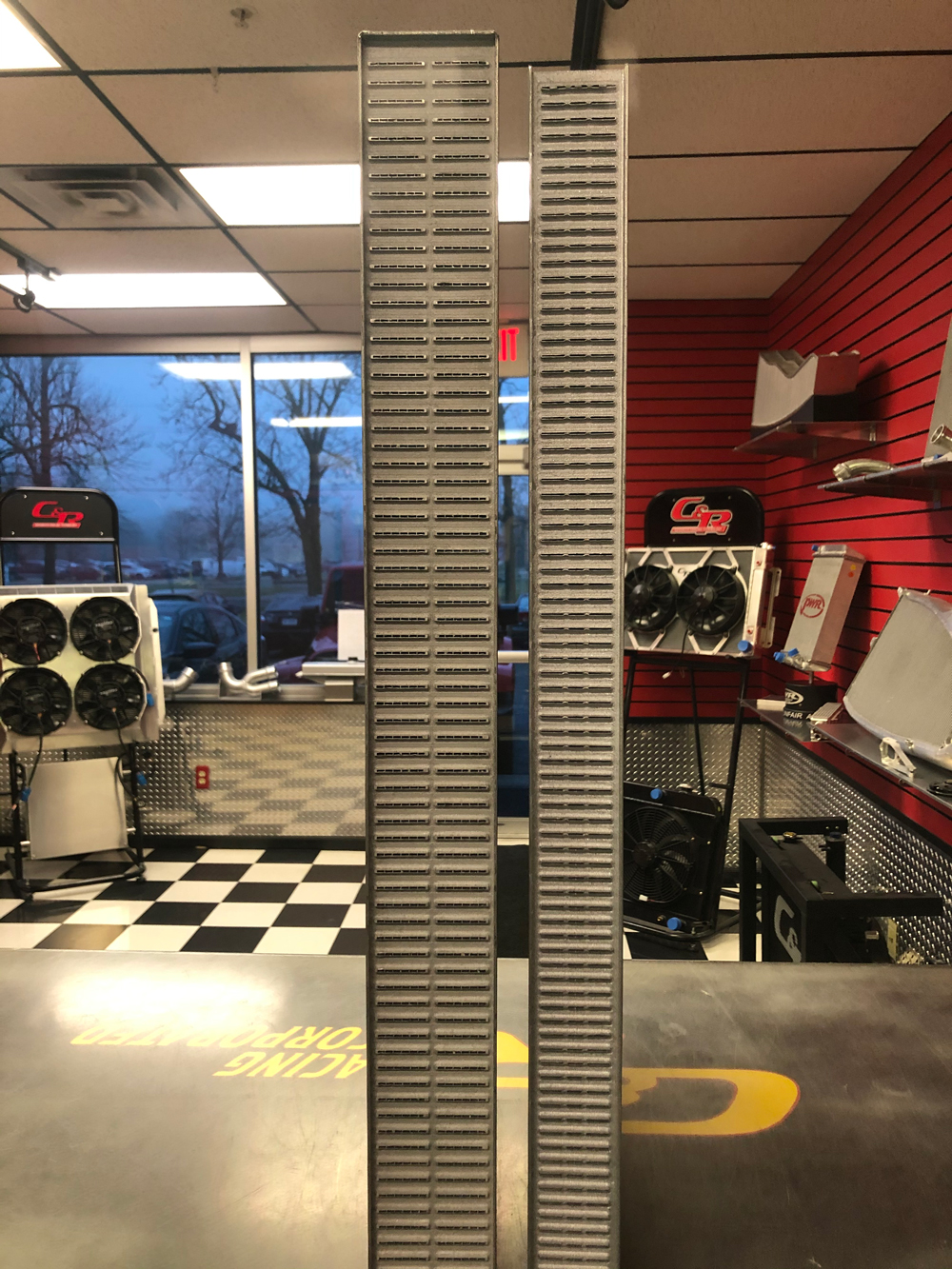
Should I install smaller lower radiator hoses or restrictor plates to slow down the coolant and keep it in the radiator longer?
No. A cooling system is closed-loop. The more time the coolant is in the radiator, the more time the coolant is in the engine. Reducing coolant flow will only expand the temperature difference between the inlet and outlet temperatures. That’s bad for a whole bunch of reasons.
The inlet and outlets on the engine usually are attached to separate components—the block and heads. If the temperature of one is significantly different than the other, you’ll have a problem with thermal expansion. Though it might not be immediately apparent, that poor head gasket is being sheared to death. The heads are growing larger than the block. Your head gasket problem could be a cooling system problem.
There are situations where lower flow has benefits, and others where max flow is required. Too fast or too slow are both problematic for proper cooling. Having the engine’s rpm determine coolant/airflow makes it nearly impossible to maintain ideal operating temperatures. That’s why Delta PAG manufactures variable-speed brushless water pumps and fans. They’re powerful [and] efficient; and because of their ability to operate at variable speeds, they can increase or decrease flow rate from 5 to 60 gallons per minute as needed via a one-wire signal PWM. It has a huge 1.75-inch inlet and dual 1-inch outlets and only weighs 4.60 pounds. —John Pairaktaridis, Delta PAG, Astoria, New York
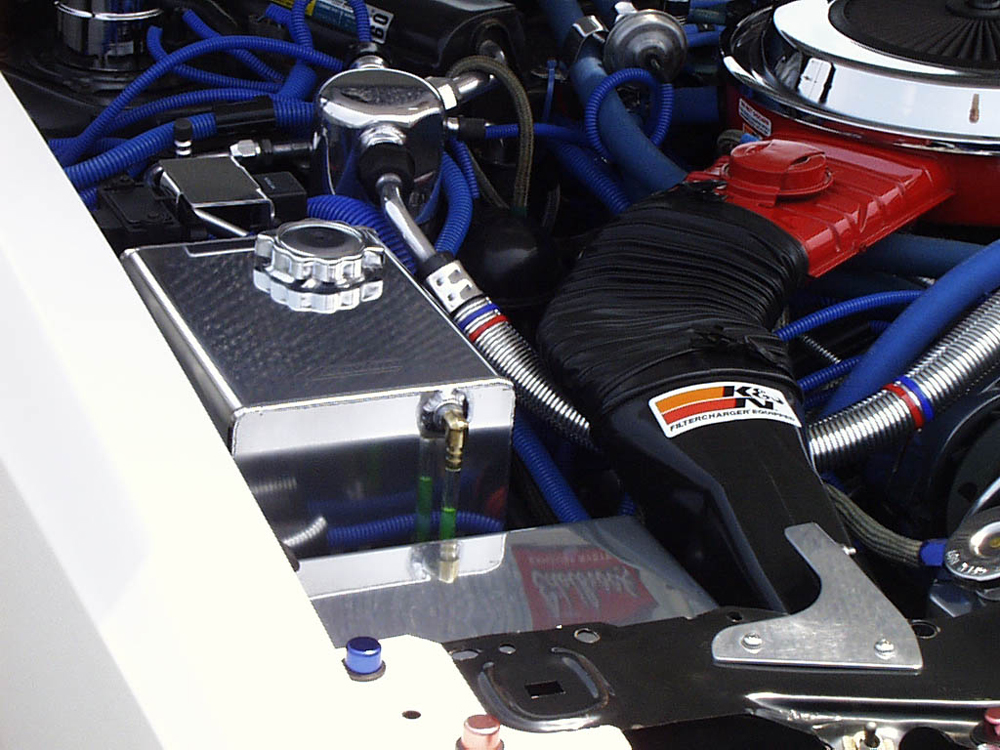
I put in a new motor and radiator, but the engine is running hot. What should I do?
95% of the time, a correction of one or more of these issues will solve the problem: Set the proper timing of the distributor; properly jet the carburetor; and/or replace an improper thermostat. If the engine’s timing is too far advanced or retarded, that causes the motor to run hot because it’s working harder. The same is true if the engine is running too rich or too lean. And if you replace a 180-degree thermostat with a high-performance, 160-degree thermostat, that usually immediately cures the problem. —Rick Hobbs, PROFORM, Warren, Michigan
How does using a high-pressure cap improve performance?
Two important facts here: One, cooling systems like the one in a production vehicle generally work with pressures less than 19 psi. Two, water boils at 210 degrees F.
These two facts are important because they define the need for pressurized caps. One thing we do not want is to boil the water. This will create pockets of air, which greatly hinder cooling performance. As we increase the pressure, we are able to increase the boiling point of the water in our cooling systems. Every pound of pressure is equal to 2–3 degrees F increase in the boiling point. In the top tiers of racing the engine cooling system operates at pressures over 50 psi. They can then tape off the front end, increasing the downforce on the car. Taping off will increase the water temperature, so they are able to run the car at 250 degrees F without having cooling issues. These types of temperatures would overheat a standard production car, possibly leaving you stranded. —Ryan Williams, FLUIDYNE
What is the difference between an expansion tank and a recovery tank?
To properly function, a pressurized cooling system needs a fill, expansion and air-bleed area when filling or topping off coolant. That area needs to be the highest point in the system. In older vehicles, the top of the radiator was the highest point of the cooling system, and it was accessed through a pressurized radiator cap. New vehicles are designed with aerodynamics, styling, pedestrian-protection, and a host of other factors that place the vehicle’s radiator lower than the engine in many cases. The expansion tank, then, is located at the high point in the cooling system and serves the same function as the radiator cap in older vehicles. Expansion tanks are valuable in helping the cooling system operate properly in race cars as well, as race car designers and builders mount radiators lower—or even at different ends of the vehicle—than the engine. Performance retailers can sell direct-fit aluminum expansion tanks that replace the prone-to-cracking plastic expansion tanks under the hoods of most modern vehicles.
The function of a recovery tank is to contain the system’s expanded hot coolant. This happens when the internal thermal spring of the radiator cap is tripped and sends the expanded fluid out the side bleed hole port of the radiator neck. Sanctioning bodies require race cars have a place for this expanded coolant to go, so a recovery tank should have a vented cap and be plumbed close to the side bleed hole port of the radiator cap neck. As the coolant cools down, the spring in the radiator cap will go back to its normal position, and the cooling process will create a vacuum that sucks the coolant back into the system. —Thor Schroeder, Moroso Performance Products, Guilford, Connecticut
What size expansion tank do I need for my coolant system?
The general rule of thumb for proper capacity of expansion is 12% of total coolant volume for drawdown and 6% of the total volume for thermal expansion.
Drawdown capacity is the amount of coolant that can be lost before air reaches the water pump and is introduced into the system. Air bubbles in the coolant system can cause inconsistent cooling and can also prevent the thermostat from opening if an air bubble gets trapped underneath it.
Thermal expansion occurs as coolant accumulates heat from the engine. The 6% of the expansion volume is calculated from the amount that the coolant level will rise at 212 degrees F. This takes into account the density change of the coolant itself and all the components that are in the coolant system. If the volume is calculated incorrectly and an inadequate expansion space is provided, coolant will be discharged from the system at operating temperature. To prevent the possibility of spilling coolant, a catch tank or a recovery tank can be used.
To get the proper expansion tank volume, add together the drawdown capacity requirement and the thermal expansion requirement for an additional 18% total volume required for the expansion tank. As most coolant systems are designed to operate with about 13 quarts in the system, these calculations serve as an example:
Drawdown = 12% of 13 quarts = 1.56 quarts
Thermal Expansion = 6% of 13 quarts = .78 quart
Expansion Tank Size Required = 2.34 quarts
In a situation where a large enough tank isn’t available, a recovery tank can be used to make up some of the expansion volume needed. A recovery tank will collect any coolant that is expelled from the pressure relief. In a setup with a recovery tank, it is important to make sure that the coolant system is still full enough to allow for drawdown. —Iann Criscuolo, Canton Racing Products, North Branford, Connecticut
How much horsepower can be gained by converting to an electric pump?
Since an electric coolant pump works at a steady rate and a belt-driven pump is rpm dependent, it is hard to give an exact number as far as horsepower gain is concerned. As a general reply, we tell our customers what we have seen on various dyno tests, which is somewhere between 7 and 14 horsepower maximum. The details matter greatly when trying to discover what the true number will be for your build. Important factors include the design of the factory pump, most especially the stock impeller diameter, shape and internal clearances. Also important is the target rpm where the power will be used. If that rpm is beyond where the factory pump begins to cavitate and become horribly inefficient, greater horsepower gains may be realized. —Don Meziere, Meziere Enterprises, Escondido, California
Are CVR Proflo Extreme water pumps interchangeable?
Yes. The pumps are designed for use with all of CVR’s other (non-LS) mounting kits, so they are interchangeable. Simply change out the mounts/legs and you can move between a Ford 351, a small or big block Chevy, or a big block Ford. That’s one of the advantages of a universal pump. It makes it easy for the racer to change from one application to another, and it also reduces overall inventory costs for the dealer.
Our Proflo Extreme water pumps flow 55 gallons per minute (GPM). That motor, coupled with the CVR elliptical billet impeller, provides the maximum benefit to the racing industry. —Ron Thomas, CVR Products, Arnprior, Ontario, Canada
SOURCES
–
C&R Racing
crracing.com
Canton Racing Products
cantonracingproducts.com
CVR
cvrproducts.com
Delta PAG
deltapag.com
FLUIDYNE
fluidyne.com
Jones Racing Products
jonesracingproducts.com
Maradyne High Performance Fans
maradynehp.com
Meziere Enterprises
meziere.com
Moroso Performance Products
moroso.com
Northern Radiator
northernradiator.com
Power Cool Systems
powercoolsystems.com
PPE
ppepower.com
PROFORM
proformparts.com
Ron Davis Racing Products
rondavisradiators.com
Summit Racing Equipment
summitracing.com
Top Street Performance
topstreetperformance.com