Digging Deeper
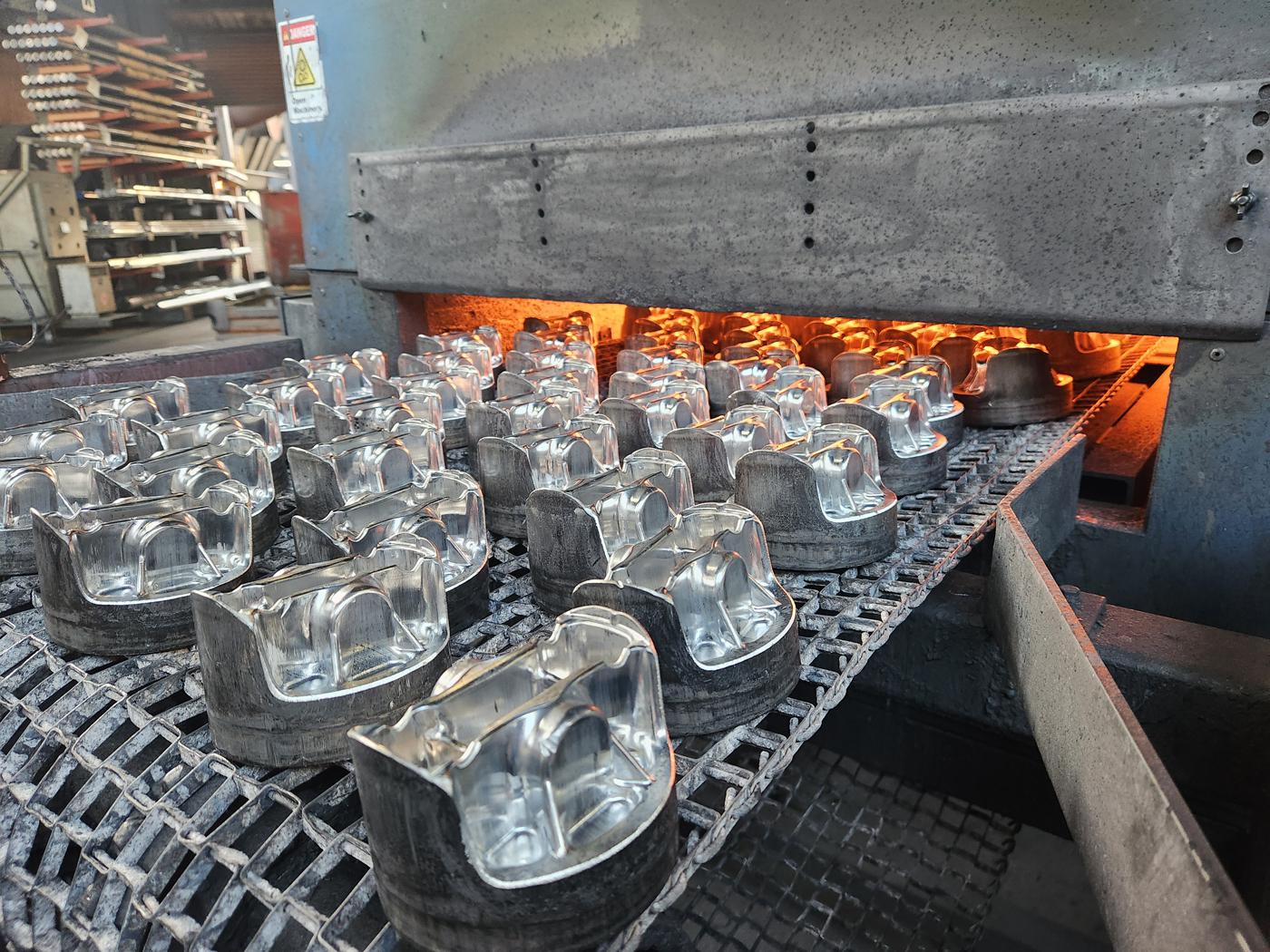
Forgings with intricate tooling requirements may have to be struck twice. Here the initial forging is being preheated to 800 degrees F at Performance Forge before going back to the press to be hit with a finish die. Tooling will last longer when using this process, and the forging is more refined before going to the customer.
It’s not always the piston’s fault. Analyzing piston failure can expose other problems in a race engine.
In a presentation at an AERA conference one year, Eric Grilliot of MAHLE Motorsport, based in Fletcher, North Carolina, led with a slide that simply stated: Rule No. 1: It’s never the piston’s fault!
“Then I had to convince a room full of engine builders to agree,” he quipped. “A lot of times the piston takes the brunt of what’s happening, whether it’s faulty fueling or detonation. The piston is literally right there in the line of fire.”
Analyzing piston failure has become more of a priority for manufacturers that supply product to the racing community. As boost levels and compression ratios increase for many race engines, failures also escalate. While the piston may not be the initial source of the failure, it bears the scars that can be examined and evaluated to uncover the root cause of the breakdown.
Race piston design, materials, and manufacturing haven’t really changed much in the past decade or so. Several new and promising alloys have been tested, but the negligible performance or durability gains are heavily outweighed by the increased costs. Only a few well-funded independent teams are trying these exotic materials. There’s the promise of 3D-printed pistons and those forged from composite materials, but those pistons are very rare in the aftermarket. Forged aluminum—mostly 2618 alloy—is still the preferred recipe in most motorsports segments, with some teams machining pistons from billet aluminum to address complex objectives.
Engineers are constantly making small design adjustments to meet the needs of racers, including working with thinner ring packages, modifying the skirt design, and playing with the barrel shape. However, there has been no significant design breakthrough that has disrupted the piston industry. On the manufacturing side, CNC machines are more precise, so more delicate designs can be attempted.
As for piston rings, they are getting thinner, and there is more attention to coatings. However, the biggest emphasis is on how the rings interact with the cylinder wall to maintain cylinder pressures. (See sidebar below.)
“There are numerous factors that can cause piston damage,” noted Jack McInnis of PBM Performance Products, Louisville, Kentucky. “Detonation puts tremendous mechanical stress on the engine and transfers a lot of heat into the piston. This can cause pistons to deteriorate, fracture, or even melt in extreme cases.
“For drag racing engines using power adders, we frequently upgrade to stronger heavy-duty wrist pins,” he continued. “Pistons for power adder applications are designed with the top ring groove set lower to prevent the ring land from fracturing. This often means the pin must also be located lower to keep it out of the ring grooves.”
“Bad tune-ups are the single biggest reason that leads to piston failures,” added Kirk Peters of Howards Cams, Oshkosh, Wisconsin. “If the engine has a detonation problem, no matter what the reason, it will lead to piston failure.”
“Tuning errors and/or chance circumstances leading to uncontrolled combustion [detonation] are the leading causes of piston failure,” said Trey McFarland of RaceTec Pistons, Huntington Beach, California. “Improper pin selection is also a common issue. We’ve seen failures due to both overly stiff, heavy-wall pins and too light, thin-wall pins.”
RaceTec tells the story of a customer supplying his own DLC-coated wrist pins. “The pistons were sent in for analysis due to an unrelated concern, and the evaluation showed the pins were distorting heavily,” recalled McFarland. “Due to the DLC coating, they had not yet pushed the pistons to failure. The customer was using the same pin his competitors were because the class was under the impression this was the cure for a galling issue that all were experiencing. We suggested a slightly longer pin to increase bearing area that would also not require DLC coating. This reduced costs as well as increased build intervals.”
Analysis Beyond the Piston
When a failed piston is returned to the manufacturer, each company has a procedure in place to inspect the product and find the cause of the problem. Sometimes that means analyzing more than just the piston.
“The biggest thing about analyzing is experience,” observed Chris Madsen of Ross Pistons, based in El Segundo, California, noting that in some failures the biggest piece of aluminum to examine is no bigger than a nickel. “Typically, if there is a failure, we like to see all the pistons. Sometimes you can find ones that are on the verge of failing and get an idea of what is really happening in the engine.”
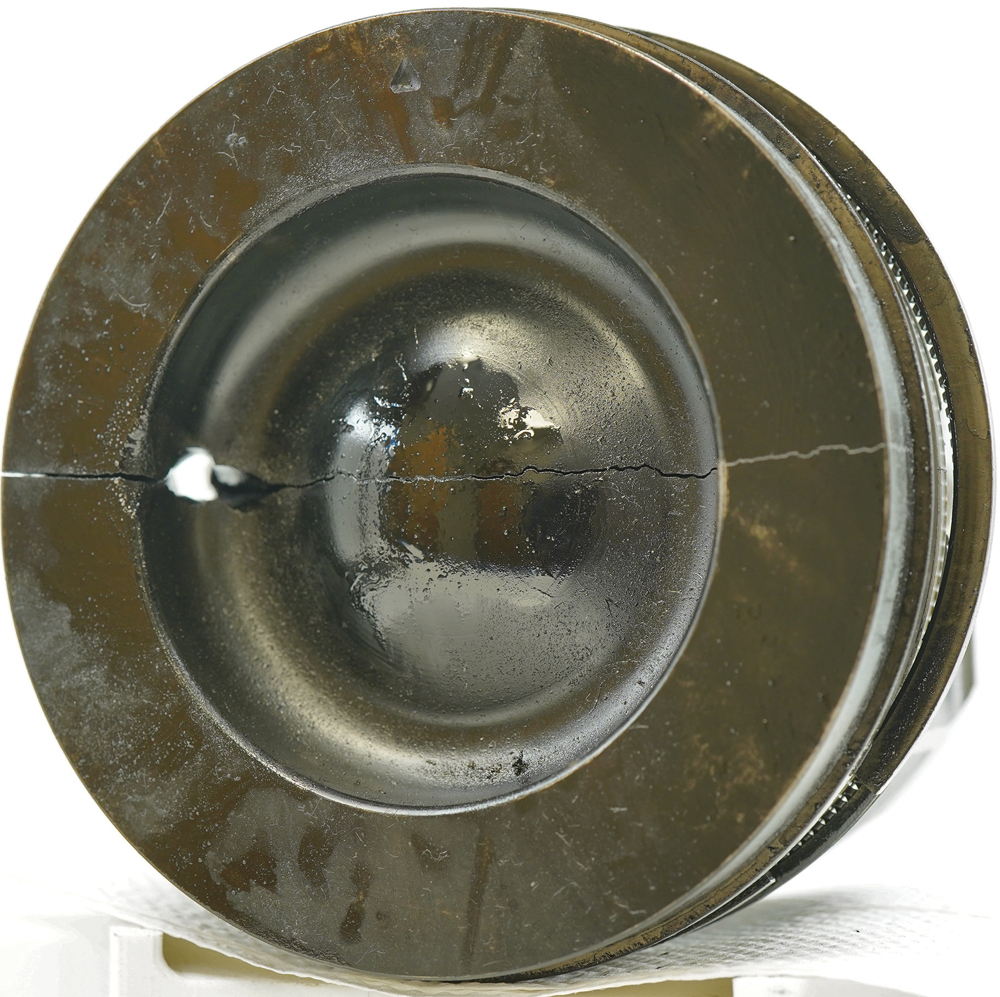
In one example, a customer had a new set of pistons for a rebuild and lost the engine on the first burnout. “Again, we need to look at everything. He had less than 20 seconds on the motor,” said Madsen, adding that the customer claimed the valve reliefs were not in the same location as the previous set of pistons. He sent only two pistons back, and both measured fine. Madsen then asked for the connecting rod from the failed piston. “We found two spots where it was cracked.
It was an NA motor, and they were going
too light.”
The rod hadn’t come apart but allowed enough flex that the piston rotated slightly and lost all radial clearance around the valve. Most likely it hit the back of the valve first, and the forces kept compounding with every rev until the piston was destroyed.
“Yeah, we like to see all the related parts, too,” agreed Bryan Moreland of CP-Carrillo, Irvine, California. “Wrist pins, locks, connecting rods, bearings, and parts from cylinders that didn’t fail. Sometimes you really can’t tell from the piston itself because it’s in such bad shape that it won’t give you a good read.”
CP-Carrillo has a rigorous action plan when analyzing a piston failure that starts with establishing a folder for data and detailed photos. The piston is inspected under a stereo microscope and sent to an in-house laboratory for even more intense evaluation.
“We have the ability to check hardness on all the parts that need to be evaluated. We also have cold saws so that we can section parts without changing the material properties,” said Moreland, who noted that the company’s OEM projects have led to a massive database that can be leveraged in piston failure analysis.
CP-Carrillo recently worked with a Top Fuel team that was suffering scuffing on the pistons. Engineers looked at changes in the oil selection, oil dilution, and differences between the cylinder blocks used by the team. They also checked a number of pistons for machining accuracy.
“Once we verify that the dimensions of the parts are all accurate, then we can start talking about what steps we can take to make the part different or better for that particular customer,” explained Moreland. “In this particular situation, we had a variety of concepts for pin-bore machining, skirt design, the areas around the oil ring, and
so forth.”
CP-Carrillo worked with the team to adjust clearances on the skirts. Attention was also focused on the ring-land diameters, piston taper, piston crown, and even the diameter of the holes in the oil-ring groove. Since there is limited Top Fuel testing, the team may try different piston designs in the same engine.
“That is the benefit of a Fuel car. They are pulling the pistons out every round anyway,” explained Moreland. “We have the ability to put one piston with one change in one cylinder, and one piston in with a change in another cylinder and try multiple changes at one time. It costs a lot of money to run those cars, so you have to test multiple things at once.”
Over at Mentor, Ohio-based Race Winning Brands (RWB)—which is the parent company for JE Pistons, Wiseco pistons, and Diamond Pistons—the customer bases and marketing efforts are separate for each brand. For example, JE continues to promote the Ultra Series with its unique Aligned Grain Flow forging technology, and Wiseco is putting the spotlight on its new Red series with some 150 new applications coming to market. Diamond is working on its 2K line with new offerings for the LS engine family and the 2.0-liter TDI architecture.
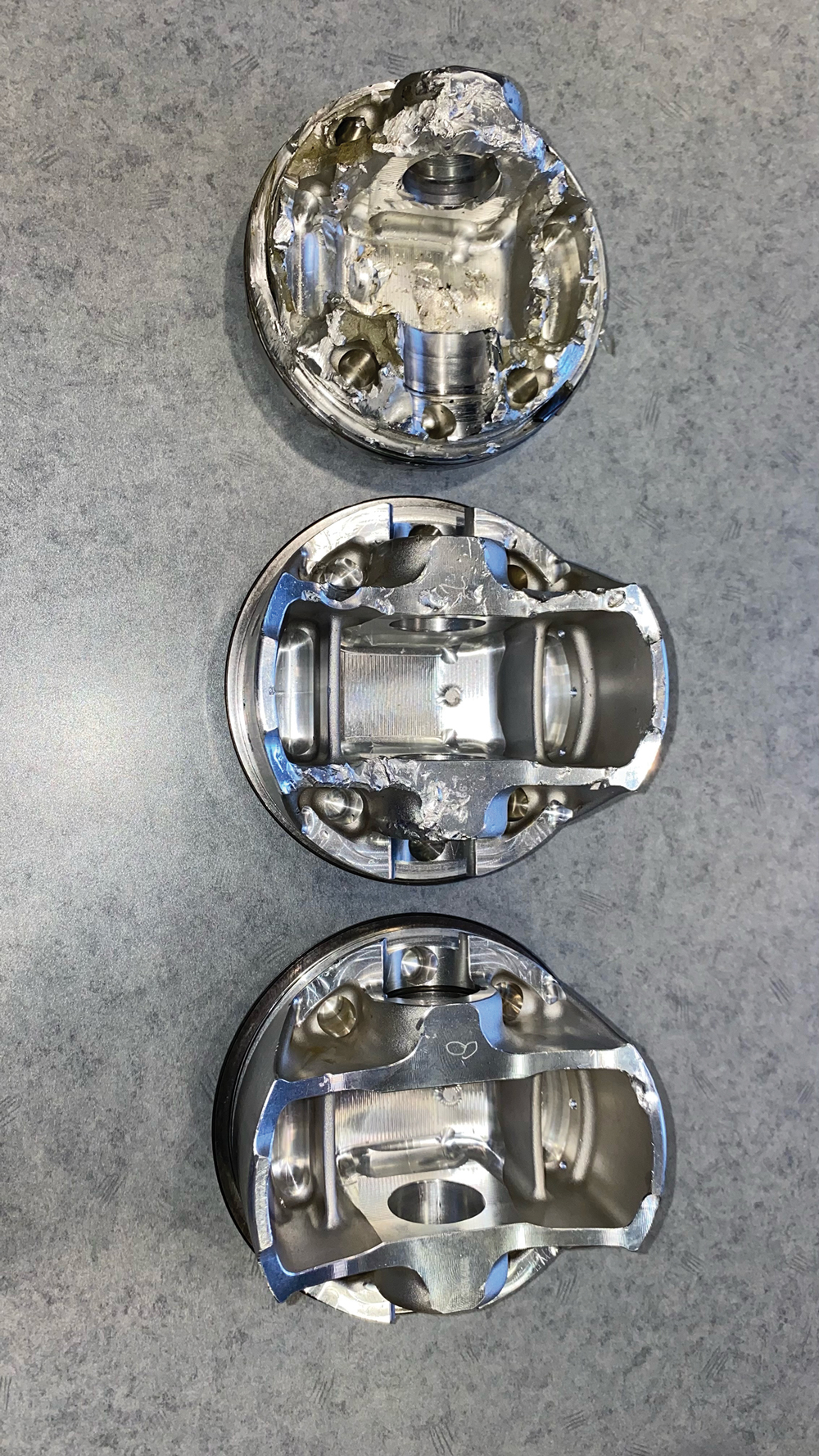
The company, however, will share engineering expertise for improving manufacturing as well as analyzing piston failures. As with other companies, it collects as much information as possible about the application and inspects the parts.
“Things like the color of the dome will tell us the heat range running in the motor. The color of the undercrown tells us how much heat saturated through,” said David Back. “Also, scuffing on the ring lands or the skirt, or signs of detonation. Those are all signs that jump out to you in the beginning and give you an indication of how the engine was running and what the tune-up was like.”
Engineers will then check material hardness against a large database on file at the companies to help determine running temperatures. Sometimes this step requires sectioning the piston to obtain multiple check points.
“That’ll basically tell us how heat was coming into it, how it was exiting, and whether heat was transferred appropriately,” said Back, adding that additional tests include examination with a Zyglo dye under a black light to check for hairline cracks. “And we usually will back that up with FEA simulation to see where those hot spots are on the piston and make sure that lines up with where we see cracks. That tells us that maybe we can improve those areas where those cracks are starting.”
RWB sees oil contamination from dirty environments and butting of the ring end gaps as two of the leading causes of failure. “Contamination is probably 50% of the failures. It seems when people send in the pistons, they don’t do a good job of trying to hide it. It’s pretty clear you have dirt or metal going through the oil,” said Back. “A lot of times they might have had the right intention when setting the end gap. But because of the tune-up, they had excessive heat and butted the rings. Through our internal testing, we always tell people to lean on the side of too much gap rather than too little gap.”
Coatings are also being emphasized at RWB, especially with the increased popularity of boost and with ring packages getting thinner, which affects the heat transfer.
“The vast majority of heat going into the piston has to come out of that top and second ring,” explained Back. “As the rings get smaller, that heat has to go somewhere else, so you definitely have to design accordingly. We’ve evolved a lot of different coating options to help combat that. Specifically, our thermal crown coatings help reflect heat away from the dome of the piston. We have anodizing, electrolysis, and nickel plating that also help that piston live a little bit longer in heavy-boost environments.”
Robotics’ Increasing Role
On the manufacturing side, there haven’t been too many changes of note. Wayne Ramay of Performance Forge in Montebello, California, a leading supplier of raw forgings to piston manufacturers, said robotics is playing an increasing role because of struggles in the labor market, and piston weight is always a concern with customers.
“Robotics help us in a number of ways—consistency of product, and consistency of labor,” said Ramay. “With regards to tooling, customers keep designing weight-reduction pockets to be deeper. Unfortunately, I can’t always do that. My tooling won’t last. A long, deep weight-reduction pocket takes a little finger on the forging die. When it hits the metal, it just puts so much side force on those little fingers that it can break them off.”
New materials are also being tested. “We’ve played with a couple of them, but they’re so expensive,” added Ramay. “We’ve been trying some with additional nickel, and they hold up really good. But with the cost, we can’t justify the benefit.”
UEM-Icon/KB Pistons in Carson City, Nevada, however, expects to introduce an exotic new composite forging for the wrist pin. “We’re working as a distributor with AWA Composites for a lightweight wrist pin,” said Christopher Sulprizio. “The wrist pin itself is about 40% lighter than a standard wrist pin. You’re looking at reducing upwards of 4 pounds from the rotating assembly.”
UEM’s strategy in analyzing piston failure is similar to other companies. Its team requests as much data from the customer as possible and also seeks to inspect the parts.
“Sometimes we ask for the rod and bearing, so we can see what kind of load that bearing was also seeing,” said Trevor Cleveland. “If it was a detonation condition, you start seeing that wear on that bearing, not just the piston. There are a lot of good resources in terms of identifying certain failures just by the damage on the piston.”
One such reference source is the “Failure Analysis Manual” from AERA. “It’s an encyclopedia of piston failures,” noted Cleveland. “You take your part, look in there, and can almost always figure out what your problem is. MAHLE also has piston failure books, and Kolbenschmidt, too.”
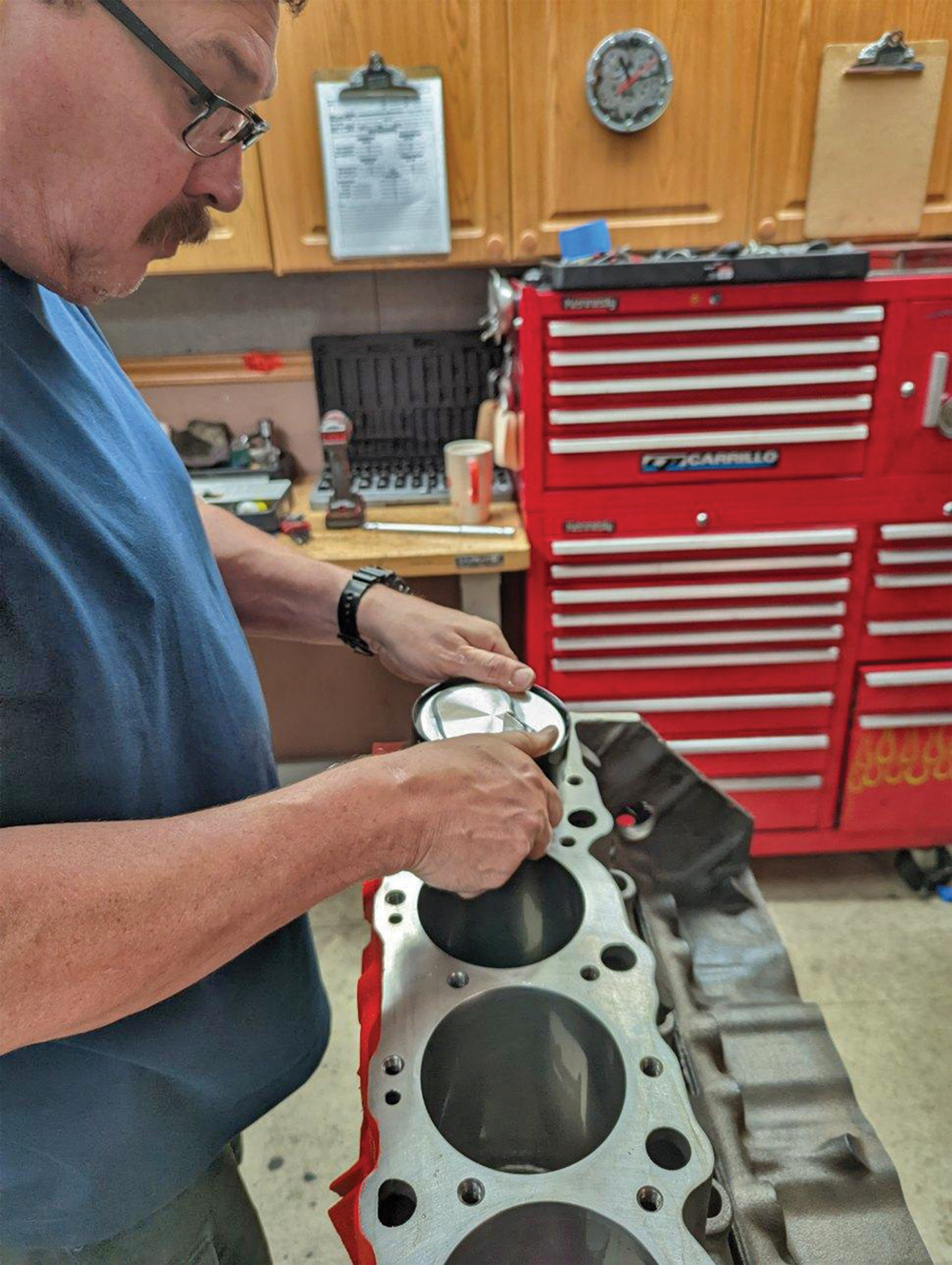
A little more than a year ago, UEM licensed Speed of Air (SoA) technology to offer pistons with dimples on the crown. While dimpled pistons have been around for some time and often tried by race teams, SoA has patented the technology based on specific dimple diameter and depth, along with location on the piston crown. So far, it is showing promising results in the diesel market.
“We continue to partner with them, pushing new applications,” said Sulprizio. “We’re starting to find that Speed of Air has nothing less than spectacular results, especially on turbo applications, and some of our diesel applications are where this product shines. We’re working with SEMA for certification, and then we’ll have our first SEMA-certified diesel motors for the GM Duramax and potentially some others.”
Still a Place for Castings
The discussion so far has focused on forged pistons, but cast pistons still have a place in the market. MAHLE recently upgraded its castings for the LP5 Duramax.
“We make it a more robust part, and because we’re building for the performance versus all the restrictions that the OEM manufacturers have,” explained Grilliot. “We try to build reliability into the part for the guys pushing it into performance applications, like tractor pulling. Where they see weak points, we tweak and redesign the casting to accommodate them. These tweaks include modified bowl geometries, compression ratios, using our skirt coatings, and just trying to offer an overall more robust part, but still in a cast piston. That’s important for diesels because you can keep the steel insert for the ring groove, and they have the cast-in cooling channel on the inside of them—things you can’t do with a forging.”
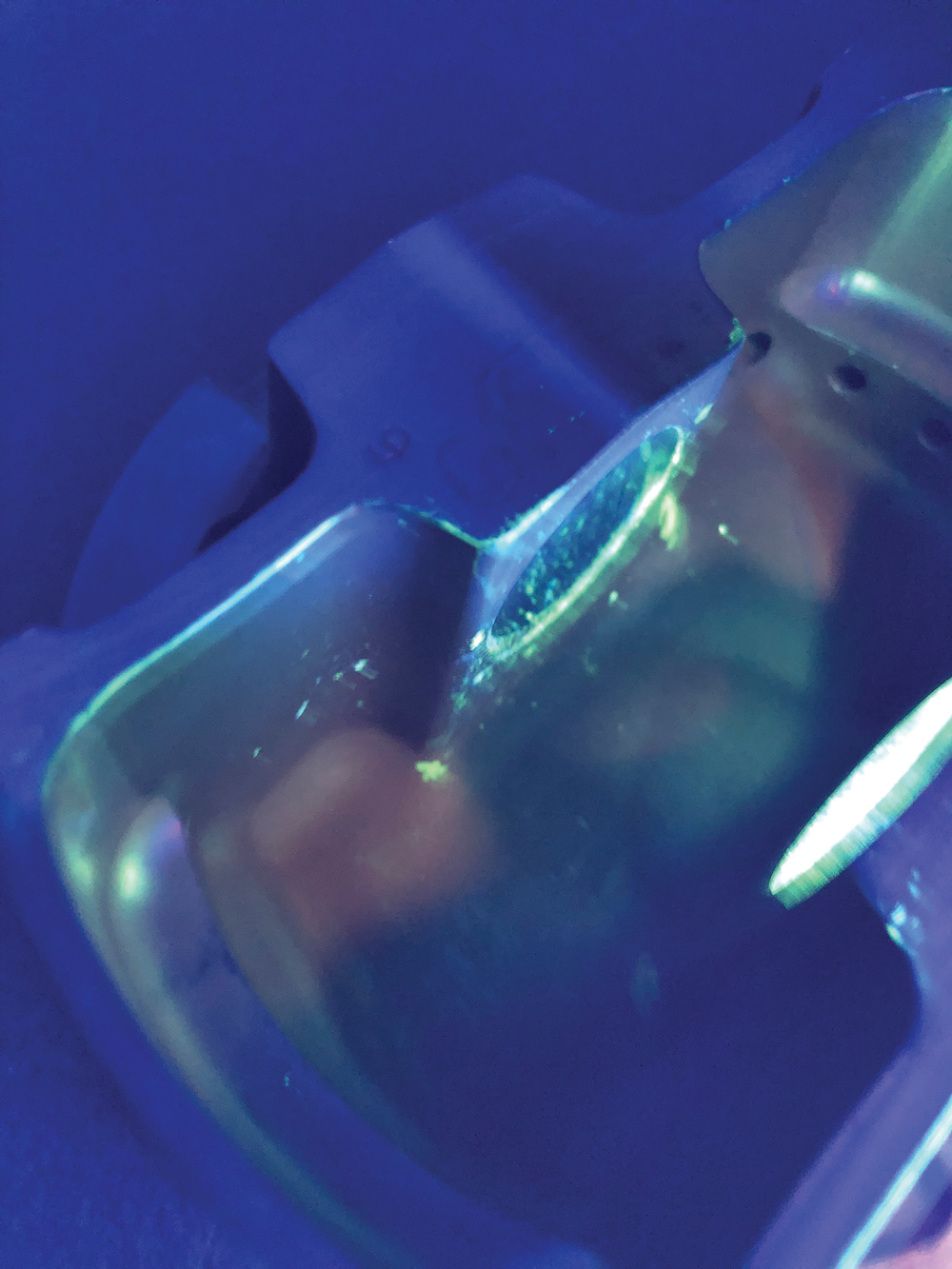
MAHLE’s failure analysis practices are among the more robust in the industry, often leveraging lessons learned developing and testing pistons for OEM customers.
“If I made up a statistic, I might say that half the time we can’t ultimately tell you why something failed, but maybe we can tell you how it failed,” explained Grilliot. “We can see whether it overheated and melted and how that failure came about. But we couldn’t say it was because the spark advance was wrong, or because it went lean. There was something in that combustion event that led to the consequences that we saw on the piston.
“If there was one sentiment that I could share, it’s that being able to look at the entire picture is extremely important. All too often somebody will get a failure, and the knee-jerk reaction is to send in this one broken or failed part and have someone tell me what went wrong,” continued Grilliot, adding that inspecting as many parts of the engine as possible is key to identifying the root cause of the failure. “The reality is you may have one bad piston and seven good pistons, but seven good pistons to you isn’t necessarily seven good pistons to us. Those other seven usually tell the story or provide insight.”
In summation, a piston rarely fails on its own. More often than not the expectations of the piston are far too bullish. Said McFarland, “On custom pistons—not that the piston manufacturers cannot make a mistake when designing a piston—but in most cases, pistons are designed with a level of additional strength for the intended application. It is not uncommon that, despite recommendations, we are pressured to design to unrealistic goals with an improbable outcome.”
The Great Divide: Check Those Ring Gaps to Avoid Failure
Performance engine builders are moving away from iron and trending toward PVD-coated steel piston rings these days. For many applications, especially naturally aspirated, thinner is better. NASCAR and Pro Stock engines are reportedly in the 0.5- to 0.6-mm range for the top ring. High-boosted engines are known to be safe with 1.0-mm or a more traditional 0.043-inch top ring.
“With steel, you’re getting a better-quality material. It’s stronger and more malleable. It can be thinner and not break,” said Lake Speed Jr. of Total Seal, Phoenix, Arizona. “It can conform to the movement of the pistons.”
Speed said there’s often a misconception that the piston ring is comparable to a structural component within the piston. “The wrist pin is 100% a structural component. A piston ring is not a structural component. It’s a seal, and it needs to be able to conform to the movement of the piston. The thinner the ring is, the more it can conform.”
Which begs the question: If rings keep getting thinner, aren’t they more vulnerable to failure? “Not necessarily,” said Speed, noting that ring failure is often traced to the wrong end gap. “People are obsessed with trying to run too little end gap. There’s an idea that if I’m a couple thousandths too wide, I’m going to have a blow-by problem and my engine won’t run. That is absolutely wrong.”
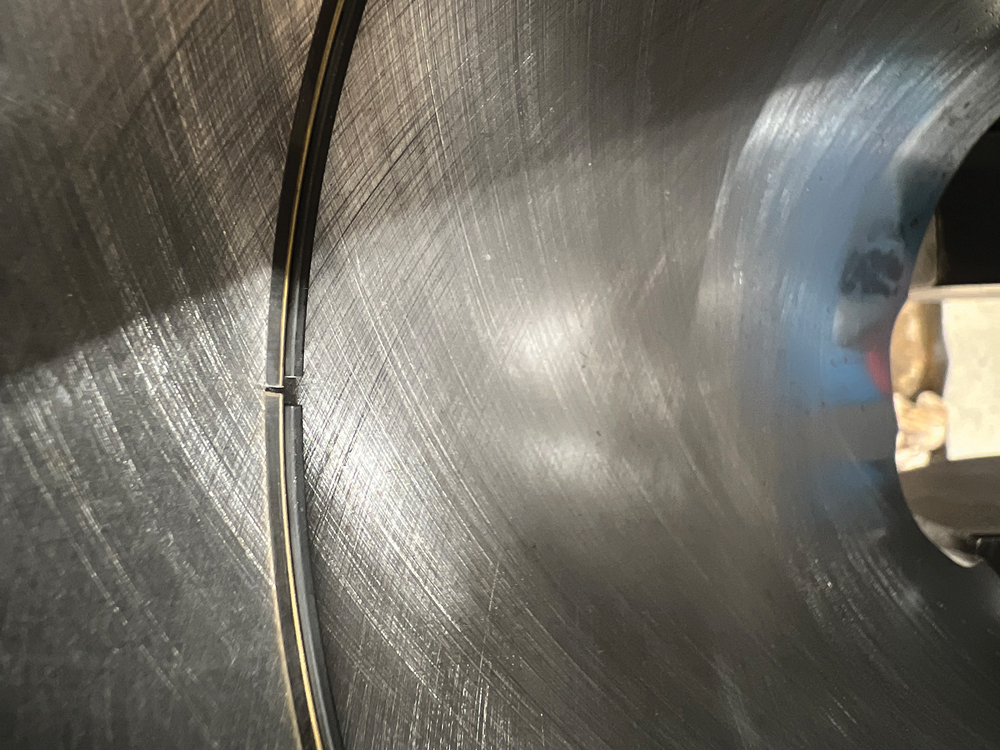
Speed said that while running a smaller end gap “makes sense on paper,” the reality is that on a 4.00-inch bore engine, a 0.012-inch gap won’t run any better than a 0.024-inch gap.
“In fact, I’ll say this: I can make that 24-thou gap probably run better than your 12-thou gap because I can use that little bit of blow-by to push oil out of my oil ring,” added Speed.
Of course, every engine is different, and dry-sump, boosted engines have different ring packages and clearance suggestions than wet-sump, NA engines. Thinner rings will expand more because they will get hotter, so stepping up from a stainless-steel ring to a tool-steel material may be necessary if the engine builder wants to run a very thin ring and maintain durability. Either way, end gap is the first defense against failure.
“What will normally happen when you have a problem is you’ll see some witness marks where there is butting of the ring ends. It might just be tiny, but whenever that ring butts, nothing good happens. Only bad things happen if the rings touch,” warned Speed. —Mike Magda
SOURCES
CP-Carrillo
cp-carrillo.com
Howards Cams
howardscams.com
MAHLE Motorsport
mahlemotorsport.com
PBM Performance Products
pbm-erson.com
Performance Forge
performance-forge.com
Race Winning Brands
racewinningbrands.com
RaceTec Pistons
racetecpistons.com
Ross Racing Pistons
rosspistons.com
Total Seal
totalseal.com
UEM-Icon/KB Pistons
uempistons.com