Nuggets of Innovation
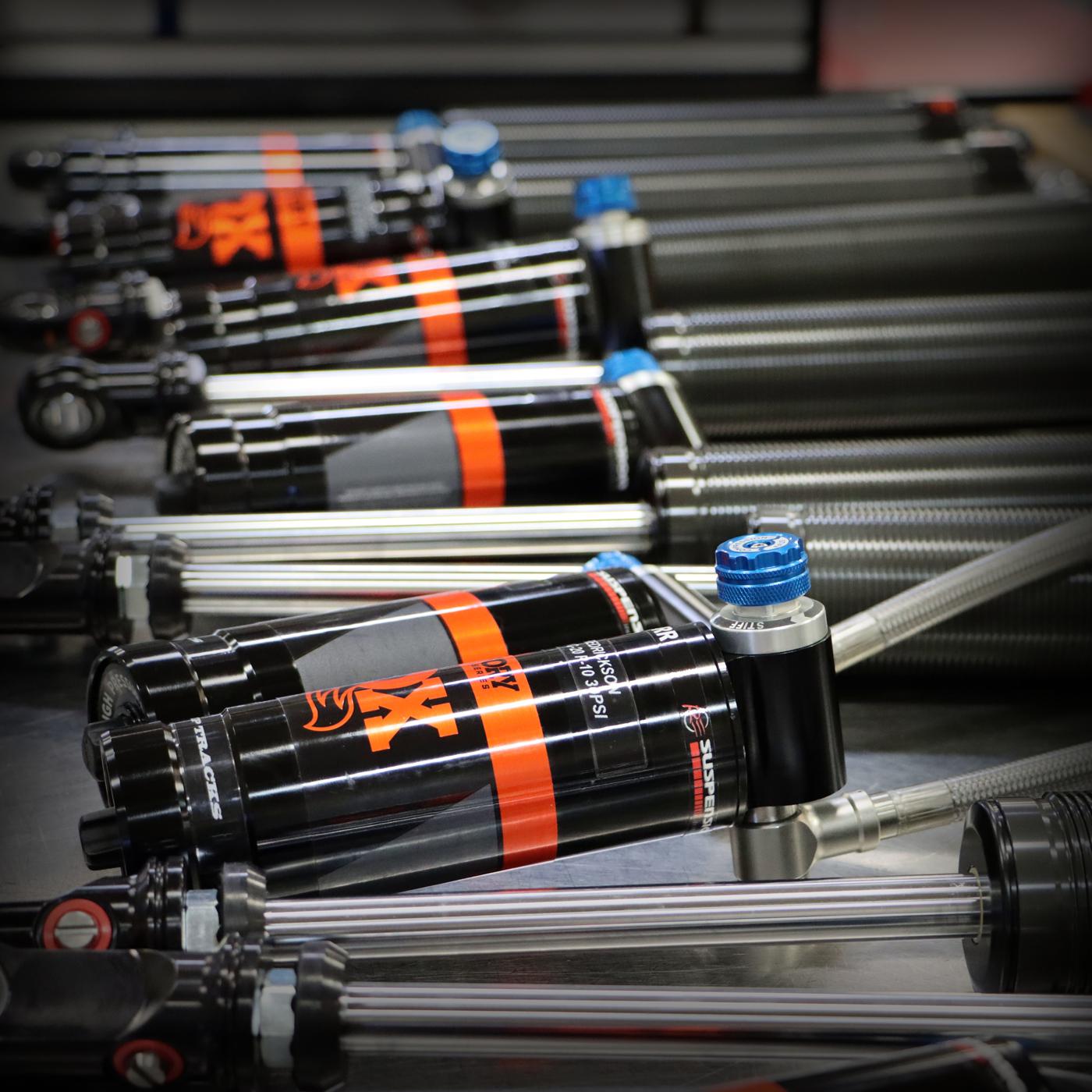
Using input from sources as diverse as rulebooks, team requests, and computational fluid dynamics, shock absorber manufacturers continue to develop new products to meet racers’ needs.
Traditionally, racing drives innovation. Developments in the quest for greater speed, handling, safety, and reliability are typically born in race shops and on track and then eventually find their way to the transportation sector.
To a certain degree, the reverse is happening in the realm of shock absorber development. Cutting-edge damper technology—electronically adjusted shocks, active aero shocks, composite shocks—are found on some of the world’s most advanced sports cars but are not allowed by most race sanctioning bodies.
“Honestly, some of these hypercars are more advanced than the race cars,” said Aaron Lambert of Penske Racing Shocks, Reading, Pennsylvania. “They have the adaptable suspension that can be controlled electronically. You can interlink them front-to-back, side-to-side. But Formula 1 and other racing series have pretty much banned all interlinked suspensions, so you lose that advantage.”
With OE and aftermarket divisions, Bilstein has “extensive experience with electronic dampers within those lines,” said Keith Robertson with Bilstein’s US division in Mooresville, North Carolina. Yet “since the circle track market prohibits them, we do not have applications active or planned with the capabilities. Bilstein saves that technology for the cars spectators drive to the race tracks.”
“Much of this technology is just not legal” in racing, added Josh Slade of RE Suspension, Mooresville, North Carolina. “We don’t really see that on the motorsports side until you get to the Formula cars and higher tiers like that.” Slade, in fact, characterized recent shock absorber development as “pretty stagnant. The last thing that was really revolutionary and ground-breaking was more than 10 years ago, with Penske and the Inerter.”
“That was the last big development,” said Lambert of the Inerter shock. Engineered by Penske with McLaren for Formula 1, it contains an internal flywheel that creates energy as the main shaft is displaced. “Essentially, the flywheel is forcing the suspension to continue to work, kind of like a supercharger for your suspension,” he explained. “Formula 1 banned it when the new car came out, which forced teams to find other ways to get that advantage. IndyCar and drag racing still allow them, so we do some development there, but it’s very specific for those markets.”
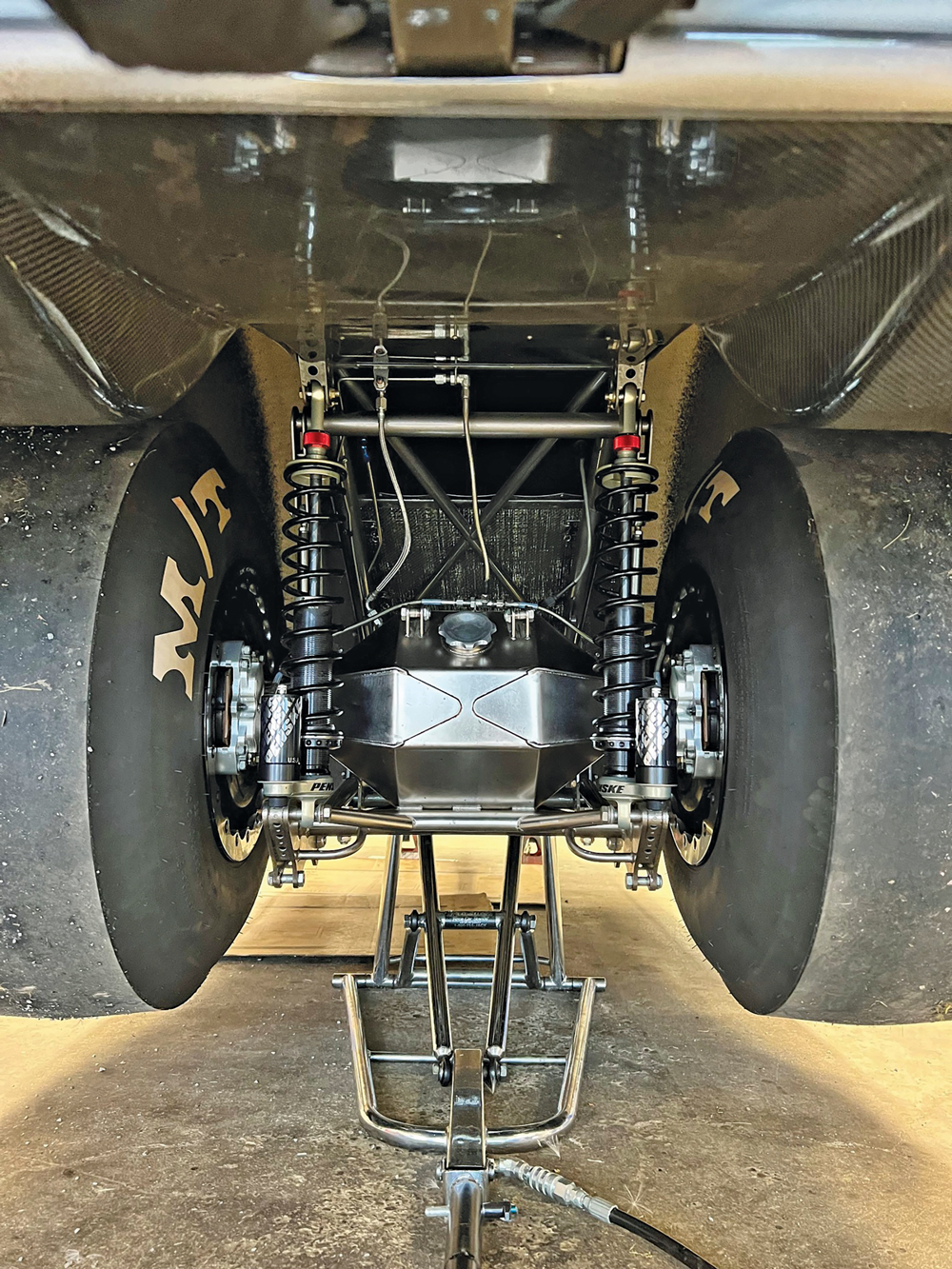
“At least in the circle track side of the racing industry, there’s a general stability in the ‘footprint’ of the dimensions of the shocks,” Robertson noted. “Car builders may play around with the mounting points and angles, but generally your lengths and mounting styles tend to be similar. As such, more of the focus can be on the tuning capabilities. That’s often a ‘cat and mouse’ game, since the chassis builders are constantly evolving their product as well. Sometimes we can hit the moving target with a simple valve stack adjustment, and sometimes it takes some new technology. We need to be willing to try both.”
Shock makers may feel stymied by the limitations put on them by sanctioning body rulebooks, but those rules “are simply a framework,” Robertson added. “The key to success is finding those nuggets of innovation within the details not specified in the black-and-white print.”
Product Innovation Trends
Ben Baker of AFCO Racing Products in Boonville, Indiana, agreed that “as a whole, in the last 10 years, there’s been very little difference between all the different shock manufacturers, both in piston design and valving. Everybody’s gotten smarter, and we’re narrowed down in a pretty small box right now.” The changes that are made can be driven “by the racers, and what we see as market trends, issues we run into in the field. Some ideas come from the shock tuners we work closely with.”
But, he added, “trends in chassis setup influence us more than anything.” In the dirt late model world, “15 years ago, if you traveled the right front 3 inches, you had more than enough travel than you could ever want. In today’s world, if you don’t have 5 inches, you’re in the way. We have to accommodate springs, two-stage kits, bump stops, and all these different things that we do today. All of that goes into the whole shock design.”
Slade, too, said dirt late model racing “is the market that is driving the most changes, as they need different things to get all the travel they’re looking for. But they’re asking for a lot of different things than what they have had in the past.” For example, RE Suspension developed dual-spring sliders and lock-out nuts in two different heights for all the major shock brands “based on racer demand,” he said. “This is one of many products we developed with the racer to help accomplish what they are trying to do.”
For AFCO, keeping up with the changes in drag race chassis setup has also spurred new thinking, Baker said. “We used to run a lot of drag cars in what we call squat—the car would squat when it would launch. In today’s world, we put a lot of anti-squat in them to where we try to make them really separate hard. As traction ramps up, and horsepower ramps up, and as the tires get better, and the track prep gets better, we have to get more aggressive with shock valving and shock design to accommodate that kind of power and that kind of force separating the car apart.”
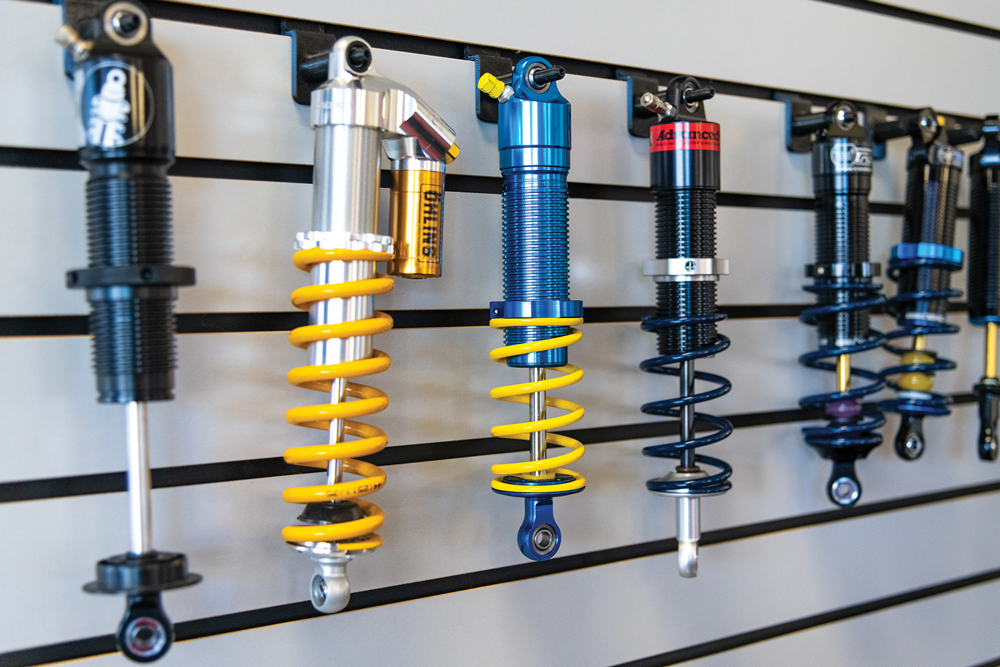
“Drag racing in general has been a big learning curve,” said Lambert. “The Pro Mod and Pro Stock clutch packages have become quite a bit different. The way they deliver the power is much more efficient, which means your suspension’s working even harder. That’s a constant change between what they’re doing with motors, how efficient they’re making them power-wise, to how the drivetrains transfer that power. Every time a team finds ways to get power more efficiently to the rear wheels, it ends up changing what you’re doing with the shocks and how to adjust them.
“That’s where the shock setups really come from,” he added. “As these chassis builders continue to evolve and change things, we just try to keep up with what they’re after.”
The Name of the Game
For those markets that drive design innovations, “adjustability is always the name of the game,” said Robertson. “Manual adjustments on the shocks have been around for a long time, but the offerings with more distinct tuning capabilities, like the Bilstein EVO RT and EVO RX five-way adjustables, are setting new standards.”
There’s no question that external adjusters have made shock tuning easier. But, cautioned Christer Lööw of Öhlins USA in Hendersonville, North Carolina, “in a lot of race series, as you go down in the classes, a lot of them are limited to using two external adjusters.”
Öhlins had a situation where it needed to adapt an existing damper to fit the TCR touring rules. The damper had compression and rebound adjusters “and a blow-off valve as an additional adjuster for when they’re hitting curbs.” In some series that was considered a three-way adjustable damper and not allowed, “so we had to develop a new blow-off that was not externally adjustable just to meet the rules.”
Robertson also noted that “there’s been a lot more market interest in ways to optimize the damping characteristics at different points of shock travel. It’s no longer just thinking about the velocity of the shaft, but also where the shaft is in its range of travel and what it’s being asked to do at that point.”
Penske, too, is developing new ways of affecting damping forces along the shaft’s travel. “Regressive technology is big for us,” said Lambert, referring to internal shock components “that allow us to tune a regressive curve a little more freely and apply that to different forms of racing.”
By regressive, Lambert is referring to a damping curve that is what Penske calls “the next level” beyond a digressive-style curve (and the opposite of a traditional progressive damper). The regressive tuning enhances a digressive shock’s ability to offer firm low-speed damping while reducing high-speed forces to not upset a chassis over high-speed bumps. Per a technical blog Lambert authored, the regressive shocks “become even softer at higher velocities than at low velocities.”
Penske introduced this technology “in Formula 1 years ago,” Lambert said, “and then we redesigned that packaging and came out with different pistons so we’re running it in dirt late model, sports cars, Indy cars, even motorcycles.”
Trickle Down
Many of the manufacturers we spoke to take higher-end technological advancements and apply similar strategies to lower-tier racing series. The technology behind Öhlins’ TTX product line, a sophisticated twin-tube system that completely separates compression and rebound adjustments, “was designed for Indy car racing at first, back when it was CART,” Lööw said. “That technology has since trickled down, and now you can buy it for everything from track-day cars to motorcycles.”
Bilstein’s AS2-R Series shocks “were designed parallel to when we were breaking into the dirt late model market,” Robertson said. “As triple-adjustable reservoir shocks, these took a significant amount of testing and research to dial in the valving setups. With the working knowledge that was gained during that process, we did an analysis of our applications offered for the lower divisions that use the non-adjustable shocks, like the SZSL and SMX Series, and revamped our valving options to give the best options available.”
Bilstein also has the advantage of an OE division that can sometimes influence race damper design, Robertson said. “Our 46-mm digressive piston is a staple piece in many of our applications. It utilizes a check valve system that allows for a larger, regulated flow on one side of the piston, usually compression, but then restricts it on the opposite movement. Our OE division created this design to give a new level of comfort to street vehicles, but on the motorsports side it gave a totally new range of tuning. That same check valve system is now utilized in our linear/digressive motorsports piston design, and we also have another piston in the works that will share the same technology.”
Computer Tools
As with everything in the racing and performance industry, computerized design and production tools are taking on a bigger role in shock development. For example, every one of the companies we spoke with utilizes additive manufacturing in its design and R&D processes.
“It allows us to do different flow paths and things that you normally can’t machine,” said Lambert. “We haven’t seen it cross into the majority of our other markets, but I would say in the next three to five years you’re probably going to see a big push on the additive side. As it’s becoming more and more available throughout markets, it’s bringing the costs down and making it more readily available.”
To date, these companies are using additive manufacturing just for development and prototyping. “We typically won’t race them,” said Baker, as “the materials we use aren’t strong enough to do that. But there are certainly cases where a 3D-printed part helps fast-track an idea.”
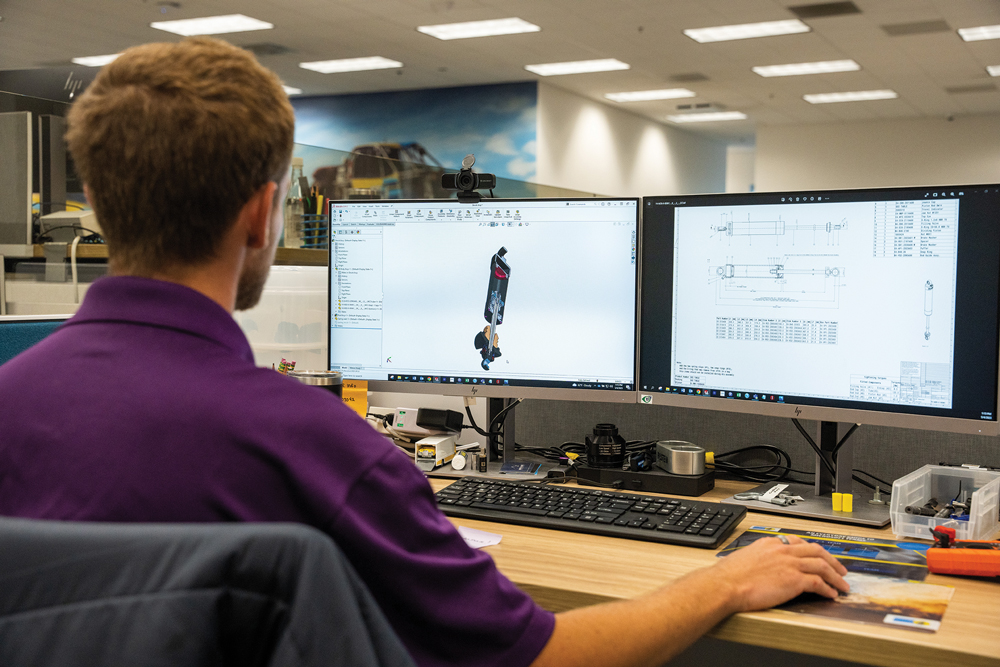
Lambert, though, predicted “there will be parts we’re actually going to be racing. Possibly by 2024 there will be some additive manufacturing parts that are out in the racing world. And usually, a few years after that you see them trickle down into the vast majority of racing markets, whether that be a piston or an actual structural piece.”
Beyond additive manufacturing, “we have way more computer tools easily available now, like FEM (finite element method) and CFD (computational fluid dynamics), that we’re using when we’re designing the internals of a shock,” Lööw said. “We can use CFD to simulate the flow of the oil within a damper. That’s driving a lot of the design work.”
The manufacturers aren’t the only ones using computers more often. Lööw said race teams “are more educated about what they want. They do more computer simulation work,” which results in “more specific requirements. Maybe that, in turn, is driving the want for more adjustable dampers to meet their needs.”
These teams are also asking for more data from Öhlins “that they can feed back into their simulations. We have the VRP, Valving Reference Program, which is software that predicts what kind of damping forces you would get for a certain valving. You put in what valve combination you have inside a damper, and where you put your clickers, and it would produce a theoretical damping curve. They can then feed that into their simulation to see if a clicker setting would be any good for a particular simulation. They can run sweeps on the clickers from this software, feed that data into their simulation, and take which clicker setting they should start the race weekend. It’s driving the damping design to be more flexible, for them to be able to run through all this stuff in a simulation, and match what they feel would be the best.”
Computer simulation only goes so far, Lööw added. “In the end we have to test it.” Among Öhlins’ verification tools is a seven-post shaker rig, “kind of between pure computer simulation and going on the track. We can put a car on there and simulate any given track, simulate downforce, roll, braking forces, all that. Then we can, let’s say, run a perfect qualifying lap, run that hundreds of times over a test in the exact same way. That way we can pick up tiny improvements in damping.”
By “tiny,” he means changes that might shave five-hundredths of a second from a lap. “You wouldn’t be able to detect that on the track with everything that’s changing—tires wearing, temperatures, and fuel levels changing—but you can find that here.” Add up a few of those tiny changes “and now all of a sudden you have a tenth or two of improvement. Keep doing this and before you know it, you have gained a second or more. Some of these changes would have been hard or impossible to verify on the track individually.”
New Products
Several of these companies had just or were about to release new racing shock products.
As we spoke with Baker, he was assembling some new AFCO 81 Series shocks, which were released in April. These are “stock-mount gas shocks that are internally gas pressurized. You can fill the gas chamber through the floating piston. IMCA Hobby Stock rules don’t allow any external fill ports, and they have very specific length rules as well, so these have been tailor-made to their length rules.”
A second new shock series, due out in June, consists of “steel-body, take-apart shocks, bearing-to-bearing, kind of like our 74 or 84 Series,” Baker said. “This particular shock is going to have a base valve internally, so we don’t have to run exceptionally high gas pressures to make the shock not cavitate. The gas pressure typically takes feel away from the driver, so we’re trying to minimize that gas pressure.”
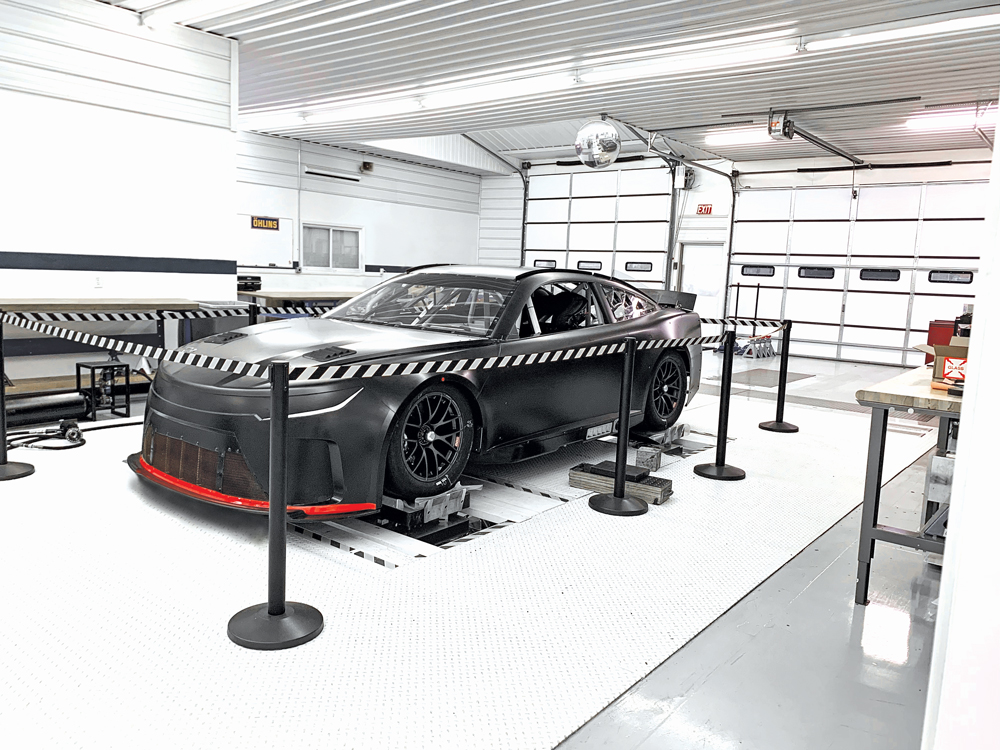
For the asphalt late model market, Bilstein just released “seven new shocks based on our AS2 and XVA Series offerings that are developed for the Late Model stock/LMSC market,” Robertson said. “For Northeast modifieds—big block, 358, and sportsman—we’ve released 16 new race-ready shocks based on the AS2 (for big block, 358) and SN2 Series (for sportsman).”
Robertson explained that “each new part release can have its own unique scenario based on the market we’re trying to reach. In the case of the modifieds, there’s both a series variation (XVA and SN2) to meet the rules specifications of different divisions and then also two sets of shocks within each of those series that are valved up specifically for each corner and ready to race. This gives our catalog dealers race-winning options they can sell right off their shelf. On the late models we also have two different series to meet rules requirements, but those are actually dry kits (no oil, nitrogen, or valve stacks) that are geared toward the shock tuners so they can build to their customers’ specific needs.”
Öhlins has just released a new two-way adjustable TTX Advanced Trackday kit for the Porsche 992 GT3, Lööw said. The aluminum, two-way adjustable shocks are upgradeable to three- or four-way adjustability, and they utilize the factory top mounts. “The nice thing about it is, we have a version of it where they can retain their nose-lift system so they can still pull over a curb without hitting the ground.”
Final Thoughts
“One of my biggest pet peeves in racing in general, not just shock related but parts in general, is that a lot of people today think you buy speed,” said Baker. “If it costs more, they think it has to go faster, and that is definitely not the case. If the car is not right in general, I don’t care if you put a $100 or $10,000 shock on it, it’s not going to go.”
As a company, AFCO “has always taken a lot of pride in having good, reliable, fast parts, but we try not to strangle a racer to death with pricing,” Baker added. “That’s something we definitely battle. They think we can’t be as fast as another shock because it’s $100 cheaper.”
Looking at the racing shock market as a whole, RE Suspension’s Slade believes “it’s getting harder and harder to make any big changes. When you look at where we started, with an old-school emulsion shock, to where we are now, that’s a huge advancement. But the products that these companies are releasing for the most part are really good, really reliable. You can take shocks from any one of the big-name manufacturers and win races with them on a regular basis. That’s different now compared to years past. You used to have one company that was pretty dominant, and it would kind of go in waves. It does a little bit still, but on a weekly basis, you see a much wider variety of what’s winning. Right now, everybody’s on their A game.”
SOURCES
AFCO Racing Products
afcoracing.com
Bilstein
bilsteinus.com
Öhlins USA
ohlinsusa.com
Penske Racing Shocks
penskeshocks.com
RE Suspension
resuspension.com