Supply & Demand
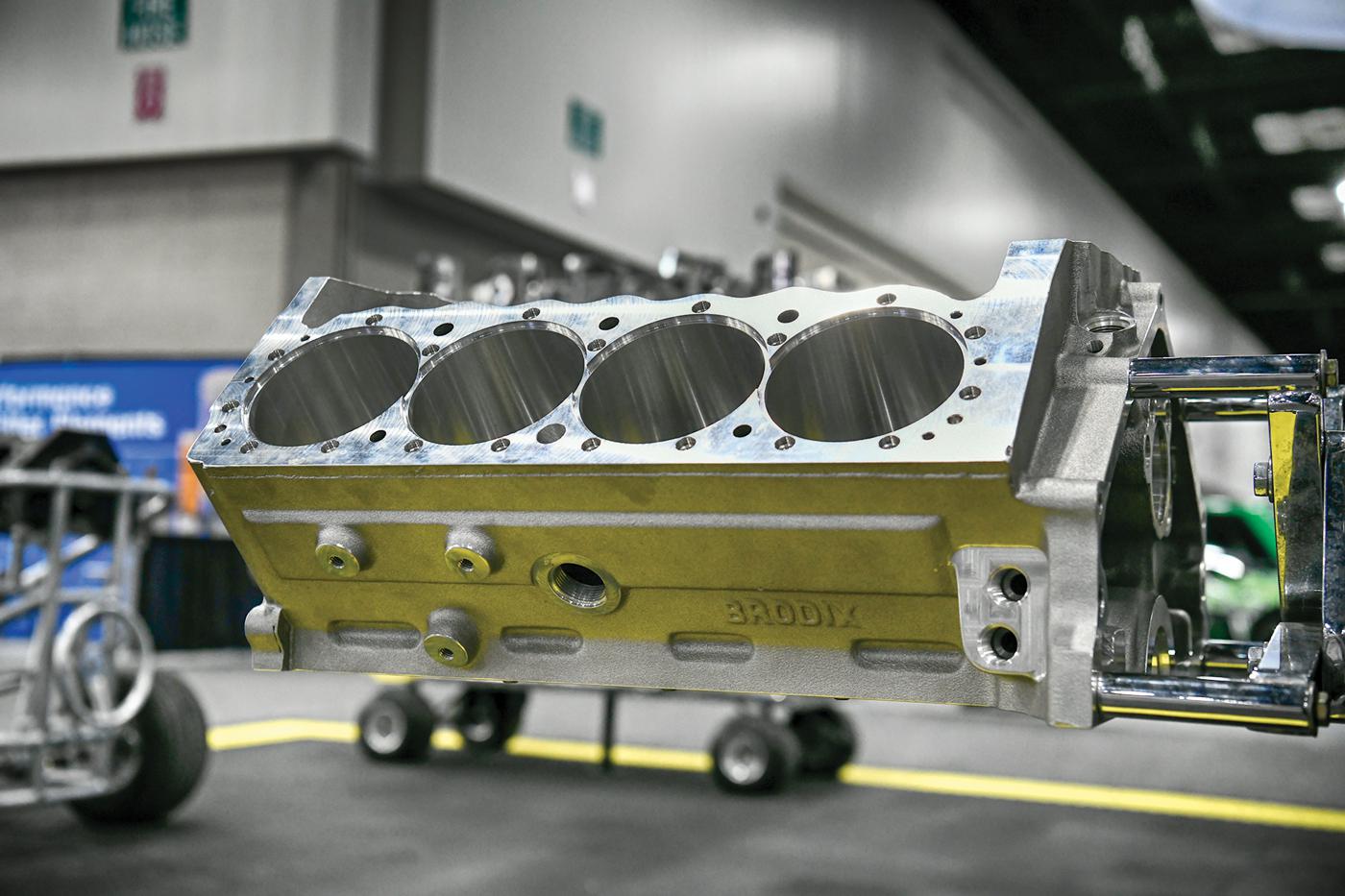
As the engine block industry recovers from the pandemic hangover, sales to racers are strong due to increasing performance options and robust construction.
One consistent takeaway can be drawn from talking with cylinder block manufacturers, engine builders, and race-industry observers this year: There is a significant demand for blocks. That statement can also be interpreted to mean there’s an undeniable shortage of cylinder blocks in the performance market. It just depends on who’s talking.
“There’s definitely a shortage of blocks,” said Carlos Inocencio of Concept Performance, Indianapolis, Indiana. “In fact, we just created new tooling for a big block Chevy because we have customers who cannot get BBC blocks. They’ve been hounding us to make a big block Chevy.”
“We’ve had some blocks on order for over a year,” added Ken McCaul of Borowski Racing Engines, Joliet, Illinois, adding that availability of many popular blocks is returning to near-normal status. “But the specialty blocks that used to be four or five weeks out, well, I’ve had one order in since May 2021. Thankfully, I have customers who are understanding.”
McCaul had the resources to plan ahead and make a six-figure purchase of blocks at one point. “We could see that the supply chain was becoming unpredictable,” he explained. “It got worse than we thought, but fortunately, we still have 50 or 60 blocks on the shelf. It was very fortunate that we were able to do that. Otherwise, I don’t know how you can make engines without engine blocks.”
Aftermarket manufacturers are rebounding from the industry turmoil created by the pandemic. First, many foundries were shut down due to COVID-19, and some didn’t go back online or they severely reduced certain services following supply chain and labor challenges. Even if another foundry could be sourced, all new tooling had to be developed to work with that foundry’s system.
At the same time that COVID-19 hit, thousands of racers and street enthusiasts were motivated to start new projects. Heavy demand was there, but product was hard to find. Many manufacturers had to put R&D projects on hold just to free up resources to fill orders.
“We’re at about 110% capacity right now. We’ve had no time to develop new product because we’re making blocks as fast as we can,” said Mark Fretz of Brodix, Mena, Arkansas. Brodix has its own foundry for aluminum blocks and used to source a limited number of iron blocks from an outside supplier. “We suspended all sales of iron blocks until further notice. We’re working on a new deal, but it’s probably six months out.”
“We don’t have anything new right now. I wish we did,” confirmed Jack McInnis of World Products in Louisville, Kentucky, noting his company did experience problems sourcing a foundry during the pandemic. “We’ve remained committed to getting our castings US-made and doing all the machining and finishing work here. I don’t think we have every part number available right now, but that’s probably true at any given time for anyone.”
Over at Dart Machinery in Warren, Michigan, the recovery is also bullish. “Supply is back with an increase at a minimum of 10% across all fronts,” reported Steve Rhodey. “Probably more like 20% on the iron.”
Resourcefulness
The demand for new cylinder blocks comes after a long period when racers actually sought out used, or “seasoned,” production iron blocks. Conventional wisdom at the time was that a used block would reveal any problems with core shift or porosity from the casting process before it was put into racing.
There’s the folklore of BMW Formula 1 engineers in the 1980s selecting only blocks that had been driven 100,000 miles in a production vehicle. They were building the legendary 1.5-liter turbo four-cylinder M12/13 engines that reportedly hit 1,500 horsepower in qualifying trim with 80 pounds of boost. Once a suitable block was found, it was then left outside in the elements so that the hot-and-cold cycling would stress relieve the iron.
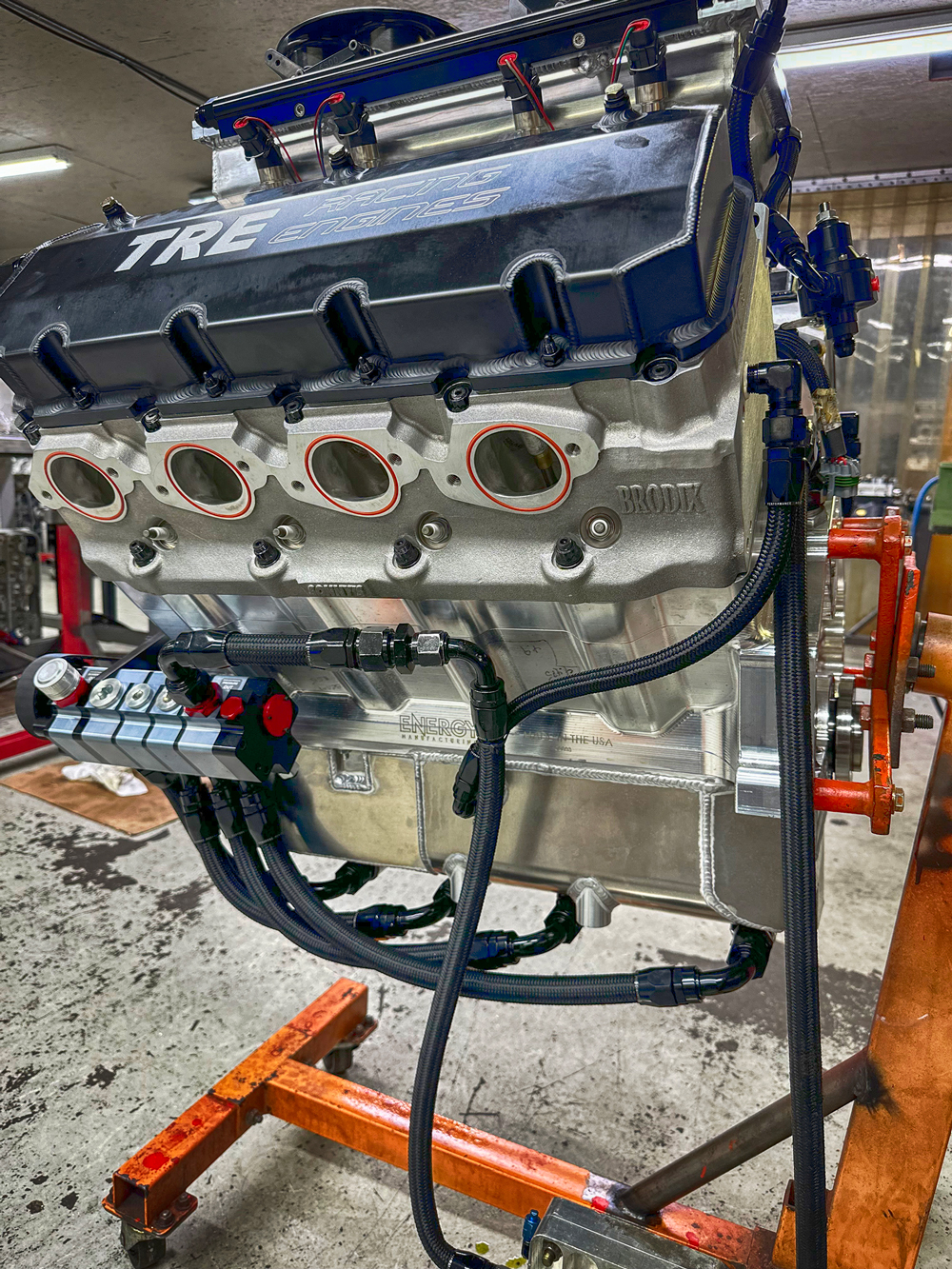
Mythbuster rationale aside, even the best of seasoned blocks will eventually fail, and then availability diminishes quickly. That scenario led BluePrint Engines of Kearney, Nebraska, to develop its own block-manufacturing program.
“When we started pursuing more horsepower, we needed blocks stronger than those made in the 1980s by GM, Ford, and others. That really led us down the path to do our own engine blocks,” said Johnny McDevitt, noting that the company either manufactures or tools many of the parts that go into its engines. “It just helps us control our own quality.”
The thought of not having blocks for his specialty engine business led Tim Banning to purchase Keith Black Racing Engines, which traces its history back to the legendary engine builder Keith Black—who also eventually had to manufacture his own blocks to keep up with increasing horsepower demands.
“Now we operate the business to produce blocks for a dealer network that assembles engines,” explained Banning, who runs the Hemis Only engine shop and the KB operation out of Clearwater, Florida. “We also sell to a lot of independent engine builders in addition to the dealer network. One of the reasons I purchased KB was to have a good supply of blocks.”
One-Off Blocks
Designing and producing a one-off cylinder block is hardly an uncommon practice. All you need is an inventive mind, CAD software, and a big CNC machine. New clean-sheet designs with wider bore centers, taller or shorter decks, massive camshaft diameters and relocated lifters are available from numerous sources. One such pioneer is David Visner, who has an engine development shop in Kentwood, Michigan, and purchased a CNC horizontal milling machine a few years ago.
“We had some ideas that we wanted to try and prove out,” recalled Visner. “We thought we could build a better block and thought it was an opportunity to fit into our program.”
Visner’s first project was a solid, 4.600-inch bore center small block Chevy. At the time, only one other company offered a similar block. Some drag racing rulebooks permit such a wide bore spacing but limit boosted engines to 500 cubic inches.
“So, we did a combination that had a 4.250-inch stroke. That put it just up right under 500 cubic inches. Then we did a taller deck deal for nitrous,” said Visner. “These were popular for grudge racers, no-prep, and so forth.”
Word of the block got out, and soon other customers with different needs approached Visner. “One of our first customers was Alan O’Brien with an AMC V8. People laugh when I tell them that we have an AMC billet combination. But it’s simply a customer who wanted that, and it was an opportunity,” said Visner. “With the late-model Hemi, they were having troubles. Tony Bischoff and Rob Goss were in X275, so we did those blocks. There again, it filled in the need, right?”
Visner used reverse engineering to develop the blocks, relying on measuring arms and laser scanners to gather the dimensions. “Then we modify it from that point to make it stronger, better,” he continued. “Most of the blocks are for power-adder applications. The goal is always to make the block better—designing the mains in a way where it has more positive registers to eliminate cap walk and give it a lot of strength in the crankcase. It’s all about reliability.”
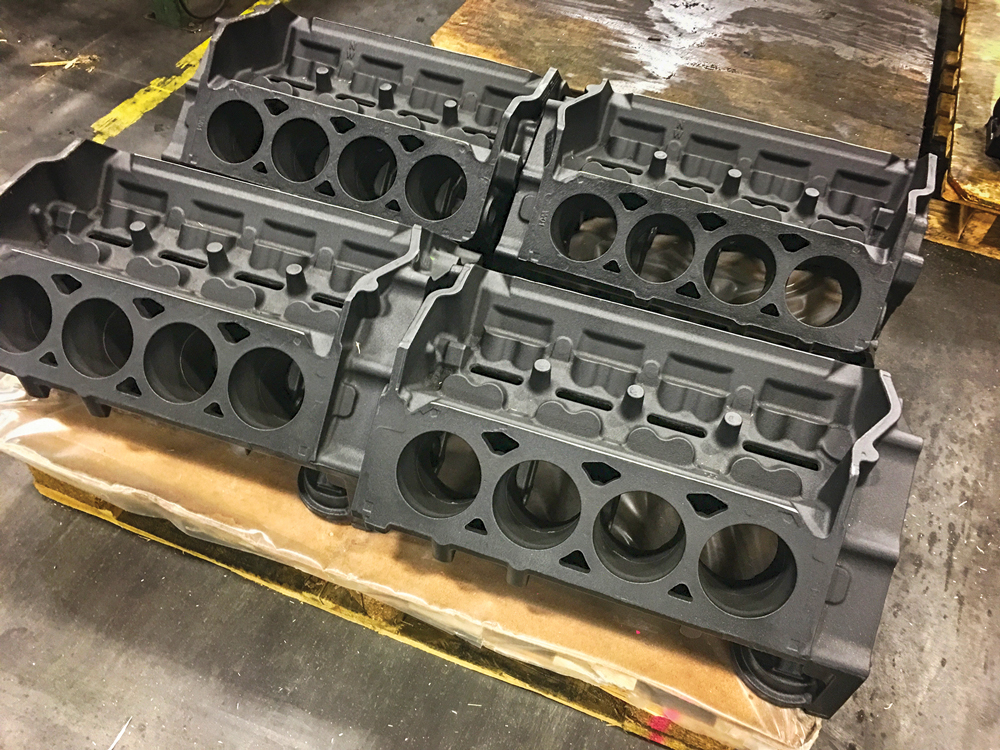
Another manufacturer of solid billet-aluminum blocks is Energy Manufacturing in Fremont, Ohio. The company currently offers big block Chevy, small block Ford, and LS blocks, each with standard or raised-cam options and a choice of aluminum or steel main caps.
“Now we’re working on an alcohol Hemi block and a Top Fuel block,” said Heath Norton. “We had started the Top Fuel but put it on the shelf to collect more data. We’ll be relaunching it later this year with both 2.750- and 3.000-inch mains. A Hemi variant of that block will be for Top Alcohol/Pro Mods.”
Norton admitted the Top Fuel block was delayed due to increased demand for the existing lineup during the pandemic. The Pro Mod block will likely come out in Q3 this year followed by the Top Fuel in Q4.
“The Top Fuel block has been tested in the field with great results. COVID hit and the program stalled out because of other priorities,” said Norton, adding that there are new priorities in developing blocks. “We’re seeing a lot more horsepower across all platforms. This hockey-stick horsepower curve is changing how people look at engine builds and development. Everything we’re doing now regarding parts is, how do you make it last? If you look at it from the 1990s when everything was naturally aspirated for the most part or a blower, everything lasted. Now it’s less about weight reduction, more about stability.”
Complaints from racers dealing with block problems motivated Concept Performance to develop its own blocks, according to Inocencio. The company first produced the aluminum LSR with considerable reinforcements, upgraded A356 T6 aluminum alloy, and plenty of performance options. Concept is now releasing the LTR for the Gen V racers.
“A lot of basic dimensions are the same, but the accessory bolt holes are different,” explained Inocencio. “We’ve taken the same priority oiling system from the LSR and put that into the LTR. We see these blocks making 2,000 horsepower, and the LSRs up to 2,500 horsepower.”
The LTR blocks do not have active fuel management capability, so they are more suited to stand-alone race builds. They are poured in the company’s foundry, which also serves many race teams and other manufacturers needing castings. That experience is helping Concept design the new BBC block mentioned earlier.
“The good thing about us is, all we’ve really done throughout the years is high-performance racing,” said Inocencio. “I mean, we’ve made parts for tons of race teams, so we have the knowledge, and we have the foundry to do so. We’re only limited by the hours of the day that my guys are willing to work. And we’ve not seen a cap on that so far.”
The BBC project started in late October 2022 by researching the competition, asking racers what they liked and didn’t like about specific blocks on the market.
“We then came up with our own plan,” said Inocencio. “We started on the tooling around the PRI Show and had the first block at the end of April. The first blocks will go to selected builders. We have some very high-end builders who build large-horsepower engines, and that will be the testing phase.
“This block should be a beast,” added Inocencio. “We’re hoping to hit closer to 4,000 horsepower by the time we’re done. Eventually, we’ll have a tall deck and tall deck with a raised cam.”
New Life for a Brand
Reinvigorating the Keith Black brand started with all-new tooling that will be used at a foundry in Michigan. The goal is to eventually produce 300 blocks a year.
“We had to make new tooling,” said Banning. “The tooling and whole infrastructure hadn’t changed in 30 years. Everything was worn and outdated.”
KB offers the Street Hemi in 4.240- and 4.490-inch bores, and it can be ordered with either 7/16- or 1/2-inch head studs. There’s also a Race Hemi block in both bore sizes with 1/2-inch studs and a raised 60-mm cam tunnel. Finally, the company offers Street and Race versions of blocks for Mopar wedge-head designs.
“We’ll be reintroducing a solid blown-alcohol block soon,” added Banning. “Also, we have CAD work done for the KB600, which is popular with offshore racers and truck pullers. It’s basically a big block Chevy with Olds racing heads. We’re getting a lot of calls on that.”
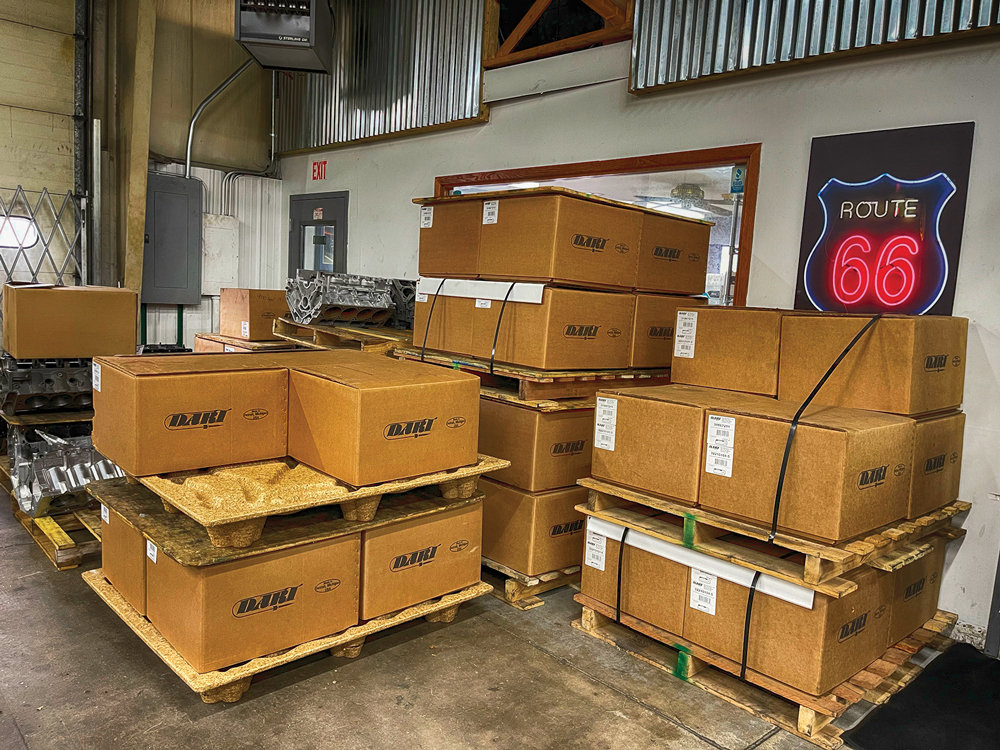
KB is also considering a Gen III Hemi block, but as with the KB600 block, the market has to be evaluated to see if the sales numbers will justify the new tooling costs.
“Right now, the biggest demand is the alcohol guys wanting a solid block,” noted Banning. “We’re doing that as a casting. The castings are super strong. We have guys making 4,000 horsepower with the water-jacketed blocks. I’m not too concerned about the strength of those blocks at all, but if the class rules don’t allow it, there’s obviously a limit of where you can race it.”
BluePrint Engines can produce 100 engines per day, and almost all of those engines will start with a BluePrint Engines’ designed engine block. However, such a volume could not be filled by US foundries alone, especially after the COVID-19 turmoil. So the company also works with a state-of-the-art foundry in Germany to meet demand.
“We found those facilities met our standards,” said McDevitt, noting that working with different foundries requires a strict quality control program when the blocks arrive at the plant for machining and assembly. “Everything that comes in the building goes into quarantine. They go through numerous inspections, both before we get them and after. Probably our smartest quality control movement is dyno testing every single engine. Even the long blocks get dyno tested.”
BluePrint’s block lineup covers all the popular platforms, including LS, and soon a Gen III Hemi will be added. Designing its own blocks allowed BluePrint to alter its business direction away from remanufacturing.
“We are a performance-based company—there’s no reman content at all. As a performance engine company, we start with a brand-new block. Everything is new,” said McDevitt, adding that all the engines currently sport an iron block but that an aluminum program may be explored in the future.
Delays are Ending
New block projects that were delayed by the pandemic are now close to release. For example, the Dart Iron Eagle Gen III Hemi block shown at the 2021 PRI Trade Show is a current priority.
“We are close. We’ve had to do some tooling, some engineering revamps a few times over from the original design, but we are on task to do sample trials by the end of May,” explained Rhodey. “When we get about a dozen samples in, we’ll get them machined, we’ll cut them up, and make sure everything lines up where we want, and the cross sections are correct. We are working with a couple of engine builders in the market to build them and test them for us. We should be filling orders by the fourth quarter this year.”
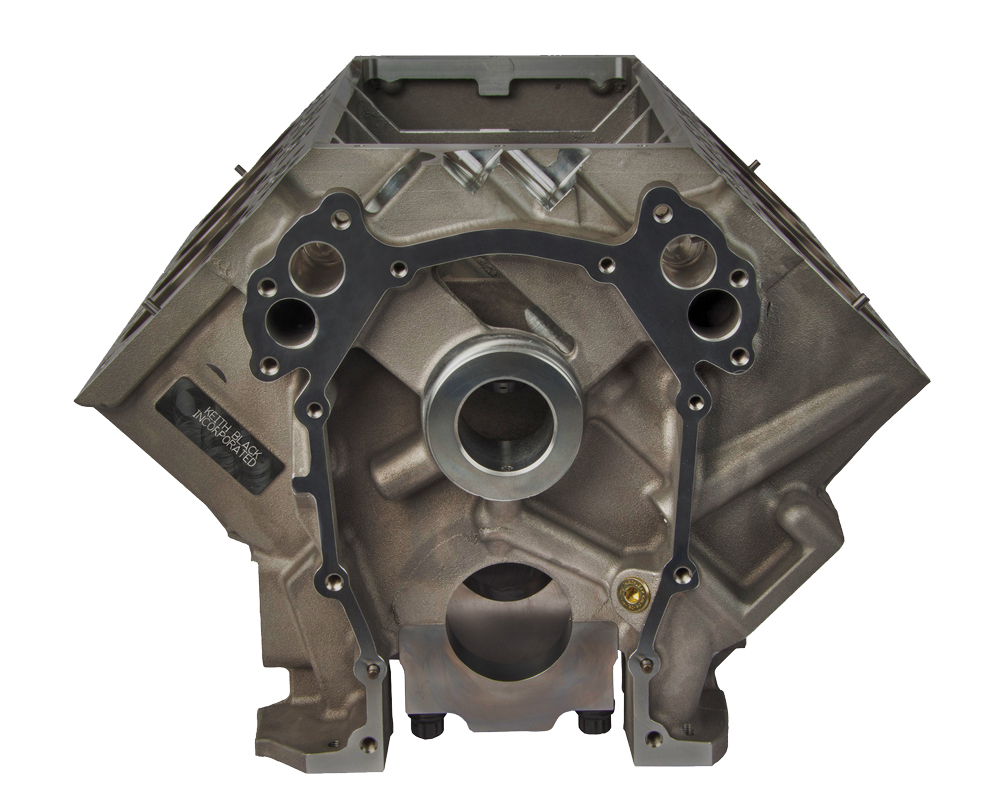
Another new block already drawing heavy interest, especially in social media, is Dart’s version of the 2JZ. “We have a few different renditions of the block. We have the solid billet, we have a water billet, and we’re taking pre-orders on it right now,” said Rhodey. “Then we also have a cast-iron revised from the OE that we are actually in the final stages of getting the tooling operational now.”
A few years ago, Dart created a new approach to block design with the LS Next—a block that would support LS heads but use traditional SBC components. The concept has been expanded through a number of LS Next iterations that offer a wide range of options and features. One of the latest versions is the cast-iron LS Next SHP Pro. It’s constructed from 220 BHN iron and has many of the features favored by engine builders, such as priority main oiling, thick-wall siamesed cylinder bores, splayed outer bolts on the center mains, available 1/2-inch head holes, and it’s clearanced for up to a 4.100-inch-stroke center-counterweighted crankshaft with steel rods.
Also new is the LS Next2 in both iron and aluminum. “These blocks offer a few options like Cleveland mains (2.750-inch diameter) and come with blind 1/2-inch mains and head-bolt holes,” said Tony Hornak.
Other features of the LS Next2 block include extending the cylinder barrels .375-inch at the bottom, priority main oiling with two lifter crossovers, choice of 4.000- or 4.125-inch bore, and scalloped water jackets. The aluminum version will be offered in three deck heights: 9.240, 9.450, and 9.750, while the iron version comes in either 9.240 or 9.450.
Drag and Drive
Although the total number of participants is relatively low compared to most motorsports, the expanding drag-and-drive movement is generating new product technology and upgrades that allow high-powered engines to survive in a daily driving environment. Solid billet blocks are great for all-out drag racing but have limitations where engine cooling is required. There are a few water-jacketed billet blocks on the market, but they are expensive due to the extensive machining involved. That doesn’t mean a solid block can’t be used in drag and drive.
“With the block, most of the heat is trapped in the top end of the engine,” explained Hornak. “The bottom really only has the frictional heat that’s being created and which the oil typically removes. I know of a few street cars, true street cars that are driven hundreds of miles a day that use a dry block and water heads, and they get away with it. I’m not saying that’s for everyone. I’m just saying it’s feasible.
“Aluminum is a pretty good heat sink. If you put an oil cooler in and have water in the heads, you can probably cool the engine pretty well,” said Norton. “Drag and drive is fraught with peril because it’s usually a war of attrition, not necessarily a war of performance. It’s who can get to the end, not who is the best.
“Everything in this business is trial and error, and that’s one of the things we’re looking at,” Norton said. “With cast heads and a billet block, you get the stability on the bottom half and still maintain cooling around the plugs and the top of the cylinder. I’m not saying it’s bulletproof, but some people are trying it.”
Ready to Race?
Just how finished do engine builders want to see their cylinder blocks from the supplier?
Advancements in CNC machining allow manufacturers to offer more options in cam-bearing size, lifter-bore size, fastener sizes, and more. In theory, a customer could have a race-ready block except for finish honing and final cleaning. In practice, however, some engine builders want to have full control over block preparation work, including advanced machining procedures such as O-rings.
“There are too many variables,” said Brad Lagman of QMP Racing Engines, Chatsworth, California, one of the country’s leading block machinists. “As far as race-ready blocks, there is no such thing.”
“It’s all relative to the goal,” added Nicky Fowler of SDPC Raceshop, Lubbock, Texas. “Is it race ready for 1,000 horsepower or 2,500 horsepower? It’s not just little things like fasteners that have to be up to par. It’s the design of the block. Blocks, in general, by all manufacturers, have garnered the development over the years of what has made blocks better.”
In other words, the actual fastener may be robust enough, but if there isn’t enough metal in the block to support the threads, then a quality, high-priced fastener is no good with 30 pounds of boost.
Lagman agreed and pointed to the factory LS block as a perfect example. “The bulkhead underneath the deck is designed for a certain bore and 7/16-inch stud,” he said. “So these guys try to put a half-inch bolt in, and you’re really compromising that structure.”
“Then there’s the problem with turbochargers today,” Fowler added. “The customer said he’s only going to make 1,100 horsepower. But it’s like the dial on a speaker—it’s that easy to turn it up, and then they want to know why they lifted a head gasket. Well, there’s not enough clamping force.”
Many engine builders have reservations about running high power levels in a cast-aluminum block and may set an arbitrary limit of 1,500 horsepower.
“It’s tough to have that conversation because we’ve had customers making close to 3,000 horsepower and have no issues,” explained Steve Rhodey of Dart Machinery, Warren, Michigan. “Then again, we’ll have guys making 800 horsepower and they’ll shoot the crank clean out of the oil pan. So it’s hard to put a power number on a block because everyone is wanting max effort.”
“That’s a tough situation as a manufacturer, where the block failed because the tune-up was not correct, and it was pushing the envelope with the product in the first place,” added Dart’s Tony Hornak. “We continue to make upgrades where we see a failure and incorporate changes in either the way we machine an area or the way we cast it. We’ve made plenty of running changes throughout the history of all of these aluminum blocks.”
The majority of leading engine builders would prefer to see more options or features for a block, as opposed to more finish machine work.
“Most of our resellers are machine shops, so they’ll do all the final work,” said Jack McInnis of World Products, Louisville, Kentucky. “We will have some customers that don’t have that capability and ask about it, but at the moment we can’t offer it.”
“Most of our customers are high-end engine builders, and they want to do all the fitments themselves,” agreed Mark Fretz of Brodix, Mena, Arkansas, noting that all the blocks are custom ordered at Brodix. “We keep nothing on the shelf so that everything we build is specific to the customer’s needs.” —Mike Magda
SOURCES
BluePrint Engines
blueprintengines.com
Borowski Race Engines
borowskirace.com
Brodix
brodix.com
Concept Performance
conceptperformance.com
Dart Machinery
dartheads.com
Energy Manufacturing
energymanufacturing.com
Keith Black Racing Engines
keithblackhemi.com
QMP Racing Engines
qmpracing.com
SDPC Raceshop
sdparts.com
Visner Engine Development
visnerengine.com
World Products
pbm-erson.com