Hold Fast
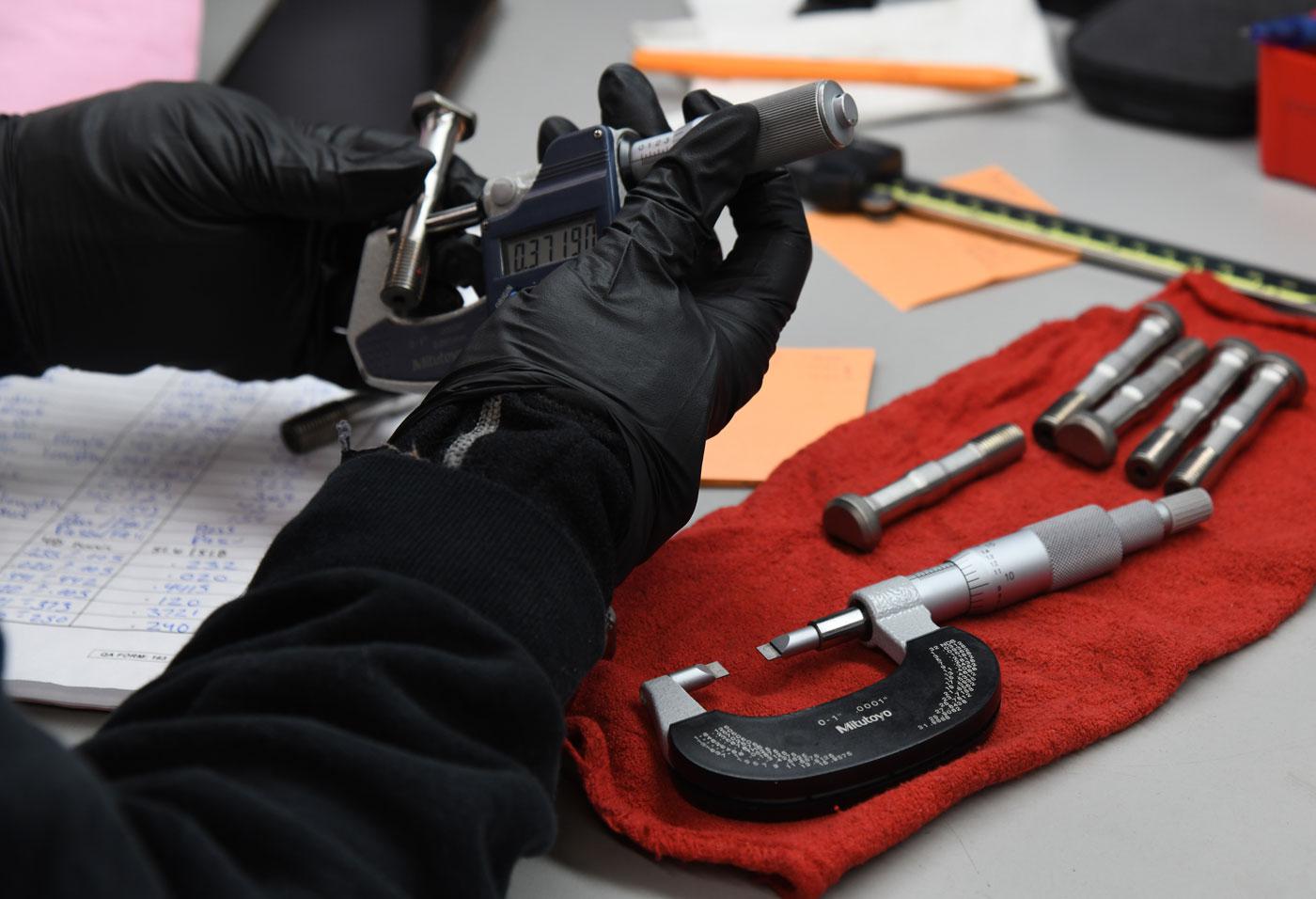
Photo courtesy of ARP
How fastener technology translates from the highest tiers of motorsports to amateur and grassroots racers.
Chris Brown of ARP in Ventura, California, recalled what the fastener business was like “in the glory days of Formula 1, in the early 1990s, when we got into that space. It was crazy. The budgets were about the size of a small country’s GDP. It was a free-for-all. You’d have a room of 30–40 designers just drawing whatever they needed. They would come up with some great designs, but often they were expensive to produce.
“We’re not in that world anymore,” Brown said. “It’s cost-capped, in an attempt to try to keep the cost of racing under control.”
Yet at the same time, the demands put on fasteners, particularly those that are engine-related, have exploded, pun intended.
“There’s probably nothing on earth that’s harder to seal than a Top Fuel motor,” noted Mark Campbell of P1 Manufacturing, Rogersville, Missouri. “Especially when things go wrong.”
Fastener manufacturers are challenged to find sealing and connecting solutions that strike a balance between cost and strength, while also factoring in weight and durability, always seeking less of the former and more of the latter.
Design Principles
At ARP, fastener development is based on a set of design principles, Brown said, which “really haven’t changed over the years. When it comes to fasteners, there are certain do’s and don’ts that you incorporate into design. Many of the same ideas and principles that are used in the top levels of motorsport have also been used in the grassroots, in parts in our catalog, for many, many years.”
As an example, Brown pointed out that “when an engine designer is designing a joint, they want to use the lightest, highest strength thing that they can so they can keep the weight down. That is when those principles kick in as far as, for example, where you can neck the stud down in diameter to keep the weight down, but also maintain the joint integrity with the clamp load.”
Or in another example, a connecting rod bolt, the ideal basic design principle would be a bolt “that would be like a piece of steel rope—something very strong in tensile strength, but also something flexible, that will allow the bolt to bend slightly without cracking,” Brown said. The material used to execute that design principle would vary from application to application depending on the “duty cycle, the load that the fastener is going to see in service. We know there’s going to be a force generated on the cap when the rod and piston get to top dead center. We can calculate what that force is with that rod, piston, stroke, and rpm combination, and then we select a material from our palette of materials that will exceed those requirements with a very healthy
safety factor.”
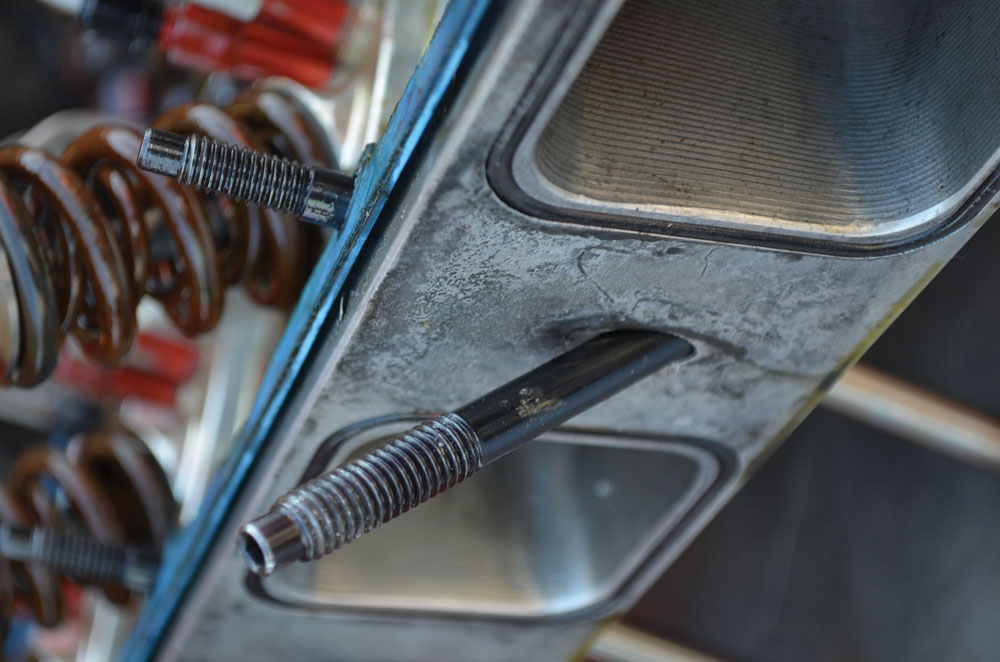
When developing a new fastener for a customer in motorsports’ top ranks, ARP collaborates with the team to develop fasteners for each specific use case. Teams will provide basic parameters, ARP will get back to them with recommendations, and once they agree, ARP executes the fasteners to spec. “Or, customers will send us a drawing, knowing exactly what they want,” Brown explained. Either way, the fastener design is proprietary.
“We are involved with lots of NDAs,” Brown noted, adding that ARP is “in an unusual position of making parts for several engine manufacturers that compete head-to-head, and yet we make their parts here. It’s a position of great trust that we take very seriously.” As one would imagine, those proprietary parts don’t trickle down or wind up in the catalog.
Interestingly, Brown has noticed something of a trickle-up situation happening “with the push to reduce the cost of racing. A lot of the top-tier racing engines now are somewhat cost capped. What a lot of designers who have worked with us over the years have recognized is that the quality that we offer with an off-the-shelf catalog part is much higher than it would be for, say, a commercial grade socket head cap screw that they might have been using previously. So a lot of our off-the-shelf designs and part numbers are being incorporated into the design of some very cutting-edge modern power units.”
A Different Approach
P1 Manufacturing entered into the fastener business much differently than most would expect, Campbell said, “because one of the first products we made was a billet Top Fuel block and then the fasteners for it. We learned a lot about fasteners doing that, and we have taken a lot of that knowledge and technology and applied it to our regular, everyday stuff.”
As an example, Campbell said P1’s heat-treating process “is quite different than any other fastener manufacturer out there. We do vacuum heat-treating, which eliminates any of the particulates in the air that could contaminate that part while we’re heat-treating it.” The process and its related equipment are “very expensive,” he said, “but we started doing that when we were making these extreme high-end fasteners, and we’ve had very good luck with it. So today, literally every single fastener that we make, whether it’s an 8740 or a 625 Plus or anything in between, is vacuum heat-treated to increase their reliability.”
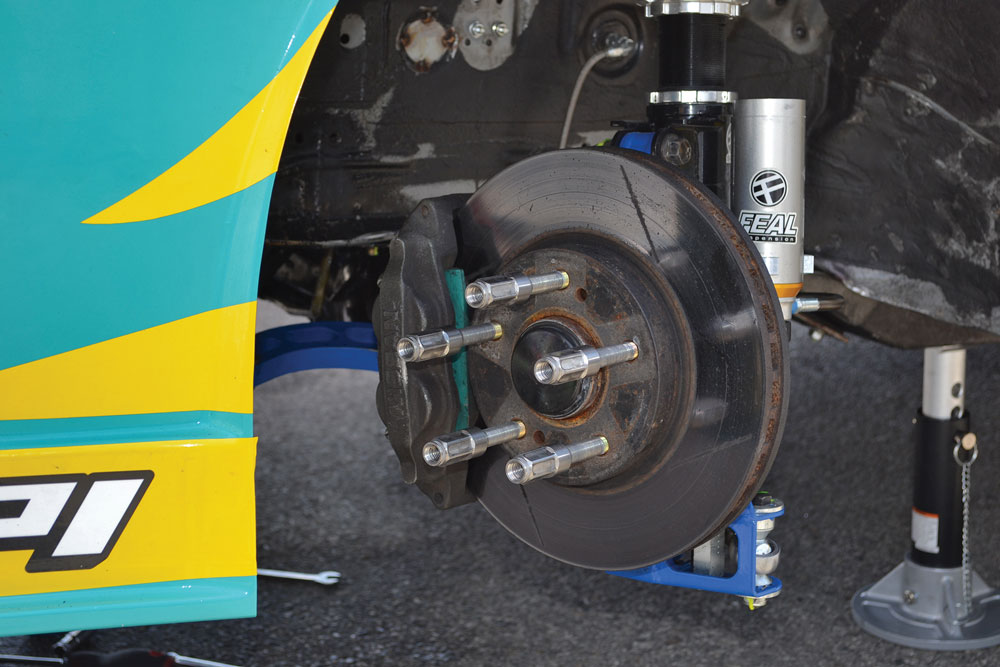
The 8740 material Campbell referred to is a chromoly used for fasteners that is often treated with black oxide to improve its durability. He described 625 Plus as “a very unique material, some of the best material you can use” with properties similar to tool steel and tensile strength in the “270,000–300,000-psi range.” It’s used in P1’s highest-end fasteners—including those for Top Fuel engines—because “it’s about the only thing that will live in an application like that.”
Developing a fastener using a material rated for 270,000-plus-psi tensile strength is “really a matter of coming up with a fastener that obviously has a lot of strength, but also does have some pliability or is a little bit ductile,” Campbell said. “Because no matter what, the stud does have to stretch to create the load you want, but it has to come back as well. Otherwise, you’re getting into a torque-to-yield type fastener, a one-time use. These guys don’t want to just use this once and throw it away.”
Some of the fastener knowledge P1 shares across motorsports disciplines is about how to properly torque fasteners, “and the lube that they use on the fasteners, all those things to get a very positive clamp load and an equal clamp load across the entire cylinder head to make sure that they stay sealed up,” Campbell said. Many in the racing industry have been torquing fasteners for a long time and are a bit set in their ways, he acknowledged, “but we’re trying to show them different ways, better ways. We have a metrology lab here, which is the science dedicated to measuring stuff, and we’re trying to help them understand the properties of the materials and how they react to loads.”
Panel Fastener Evolution
To diversify our fastener discussion a bit, we spoke with two companies that manufacture and/or distribute panel fasteners. Clarendon Specialty Fasteners of Long Beach, California, distributes fasteners of all kinds “to just about every sanctioning body in motorsports, whether it’s Formula 1, IndyCar, NASCAR, Top Fuel, even endurance racing and drifting,” explained Caulin Anderson. One of the company’s most popular panel fastener lines, Live Locks, “started in Formula 1, but now they’ve moved over to endurance racing, and you’re starting to see them more, not just on DTM or GT3 cars but also filtering into GT4s.” That includes the GT3 and GT4 Mustangs Ford released earlier this year.
Several factors set Live Locks apart from other quarter-turn fasteners, Anderson said. “They’re a little bit smaller and more aesthetically pleasing. And unlike the quarter-turn fasteners that give you one click, these can be ratcheted down for the perfect fit. They’re also offered with different styles of heads, including one that’s countersunk, one that’s protruding, and the one used on the Mustang GT3 cars, which has like a mushroom-shaped head for a little more clamping area around the body panel.”
Because Live Locks are “at a higher price point,” it may be a while before they reach the street car market, Anderson believes. “It’s really going to come down to how much the OEMs are using it. The more they use, the more stock we’re going to buy, which means a lower sales price we can give the average motorsports guy.” Right now there’s “something of a disconnect” between the price of the studs and the receptacles, he said, “because a lot of people need the receptacles, but they’re not using the same size stud. All the studs go in the same receptacle. It’s kind of like nuts and bolts. Everyone can use the same nut, but not everyone can use the same size bolt.”
Behrent’s Performance Warehouse in Florida, New York, has specialized in quarter-turn fasteners “for the dirt market for the last 20 years,” said Jon Lynch. “Our Panelfast fasteners, which now have more than 200 variations and sizes, started with the Northeast modified market and now have pushed into national tours such as Late Models, sprint cars, IMCA, and UTV/off-road applications. We see new growth every year with different purposes. The expansion trickles down to karting, mini-sprints, Legends, quarter midgets, and other beginner racing classes. Most recently we have seen an influx from the drag and street market as well as niche markets like rock climbing and monster trucks.”
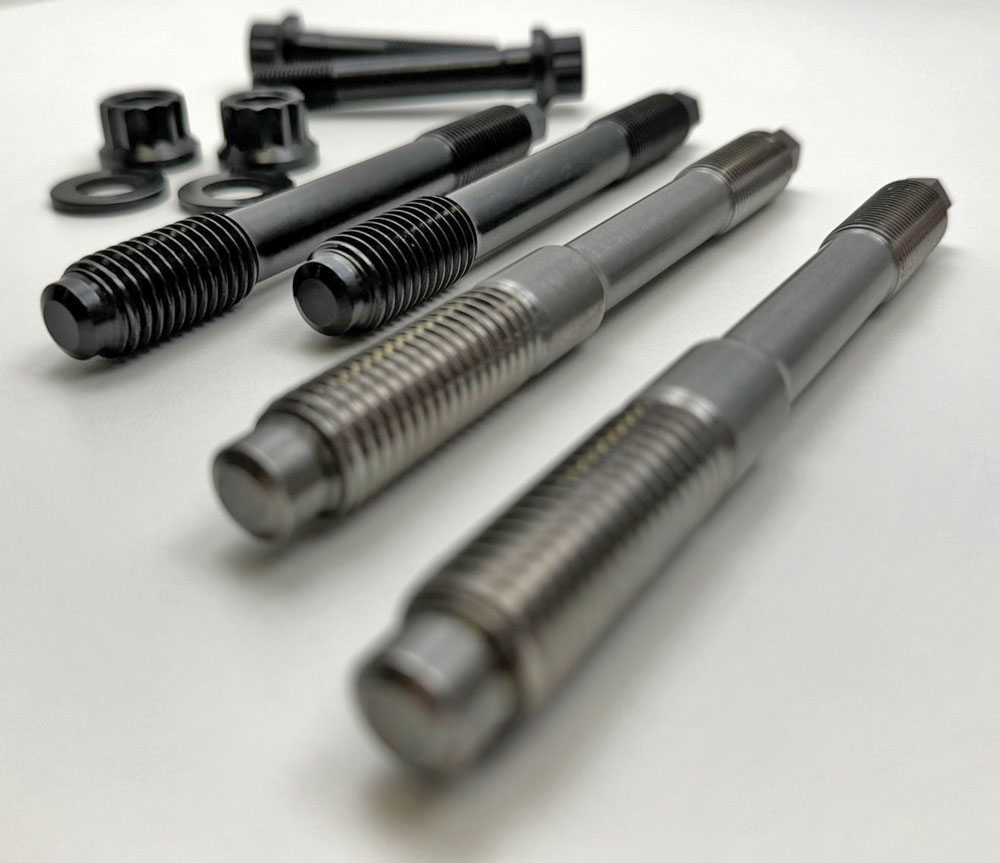
Lynch said that newer design machinery, “such as 3D printing and scanning, has made making new items and prototypes easier and more efficient in the design stage, which enables us to make products more accessible to the end user quicker.”
He noted that the fastener industry has “recently seen a bigger push toward aluminum fasteners compared to steel. Between strength of material and weight savings, it provides racers with an advantage without sacrificing durability.”
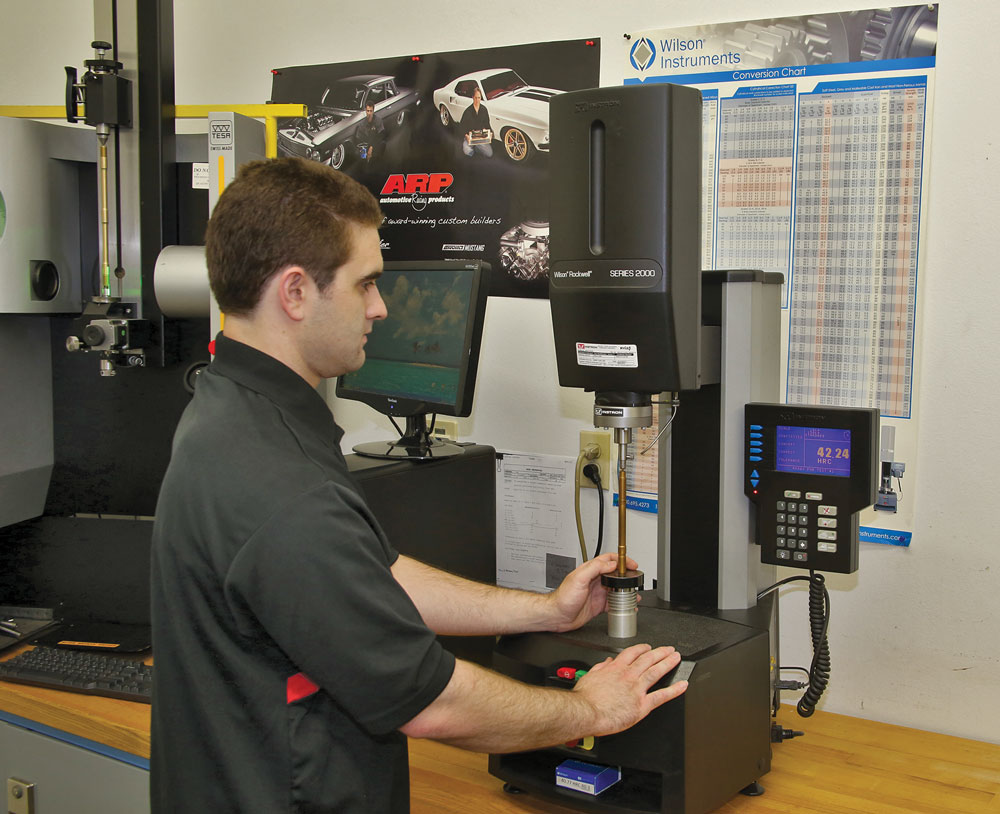
What drives the decision to choose one material over another? “It really depends on the customer,” Lynch said. “In crate engine classes for example, where every car has the same motor and parts, they tend to try and find the lightest option. Whereas short track racers still tend to use steel buttons, as they are more cost efficient when the possibility of damage is higher.
“Changes in head styles, color, and material options have given racers and manufacturers the ability to offer more options and tailor-make what fits each customer’s needs,” Lynch concluded.
THE RIGHT STUFF?
Should racers use aerospace-quality fasteners? The term would seem to indicate a fastener of the utmost quality and strength, one good enough to keep airplanes or spacecraft in one piece in the harsh environment of extra-terrestrial travel.
“Generally speaking, people hear about a part made to aerospace or aircraft or military specification, and they automatically assume that it’s better,” noted Mark Campbell of P1 Manufacturing, Rogersville, Missouri. “But really, it’s similar to making something to an ISO standard. Aerospace has certain standards that they want you to abide by when you’re building a product. Typically, it means that it’s a better product, but it doesn’t necessarily mean that it’s right for what we’re doing in motorsports. What we do for a Top Fuel engine can be crazy compared to the fasteners we create for the aerospace industry. ‘Aerospace’ definitely doesn’t mean that it’s better.”
Just because an aerospace fastener is designed to meet a particular specification “doesn’t mean it’s the strongest fastener,” added Chris Raschke of ARP, Ventura, California. “It was designed for a certain area of the aircraft. They’re all designed around a spec, and every one of them went out to meet the minimum bid at the minimum standards. In our world, we make fasteners to the highest standards at a good quality price for good value.”
“In aerospace there is quite often a degree of redundancy,” said ARP’s Chris Brown. “If it takes 10 bolts to hold a joint together, aerospace might use 15 or 20 to have an extra level of safety. We don’t have that luxury in motorsport. The joints are really critical and a lot closer to the edge. So the materials, design, and quality of that part have to be that much higher.
“We don’t want to demean the term ‘aerospace quality,’” Brown continued, noting that ARP has held an AS 9100 aerospace quality credential since 2009, “and we were compliant before we became accredited. It’s a very, very stringent set of rules. By the nature of what it is, aerospace has to be very tightly controlled because of safety. So it gives you a high degree of confidence as far as consistency from one part or one batch to another. Whereas in the commercial world, that can vary quite a bit because the rules are much looser.”
With an aerospace fastener “you are certainly getting more strength than your run-of-the-mill product,” said Caulin Anderson of Clarendon Specialty Fasteners, Long Beach, California. “But with the way cars are developing, you may need something more. Previously, automobiles didn’t see the same kind of stresses as a plane. But nowadays, you’re seeing more stresses on certain components.” —Drew Hardin
SOURCES
ARP
arp-bolts.com
Behrent’s Performance Warehouse
behrents.com
Clarendon Specialty Fasteners
clarendonsf.com
P1 Manufacturing
p1mfg.com