TECH SUPPORT: OIL PUMPS & FILTERS
Industry experts weigh in on how to best care for an engine’s circulatory system.
Racers, engine builders, and other members of the performance industry tend to talk about engines as if they were living things. An engine “breathes” through its cylinder heads and exhaust system. Its “brains” are the ECU and other electronic systems. And its “blood” is the oil, pumping vigorously thanks to the beating “heart” of its oil pump.
The analogy is apt, said Thor Schroeder of Guilford, Connecticut-based Moroso, which is why we shouldn’t view “the oil pump as just an oil pump, and the oil pan as just the oil pan. Every year in racing we want to go faster and do it in less time than before. With these increased expectations come greater demands on our equipment. Most racers today realize that they will have to run a quality oil pump to get the performance and reliability they are looking for. The wrong pump selection can result in the engine having poor performance or a diminished life expectancy.”
In this installment of our ongoing Tech Support series, we asked several companies to share the types of questions most frequently asked of them by racers and engine builders, along with their answers. Judging by the responses from our industry experts, racers who continue to hunt for constant and reliable oil pressure may be a bit confused by the difference between high-volume and high-pressure oil pumps, and wonder if the engine’s beating heart could be a source of power.
OILING BASICS
Why does my oil pressure drop at high rpm?
“It’s most likely an oil pump cavitation issue, and this is a common problem when you spin an oil pump past its design parameters,” said Bill Baroody of Dailey Engineering, Temecula, California. “Cavitation is the formation of voids (vapor bubbles) within a liquid, caused by a rapid decrease in localized pressure on the liquid at the pump inlet as the pumping cavity opens. As the fluid passes through the pump the pressure increases, causing these voids to implode [and] resulting in a shockwave. These shockwaves are powerful enough to cause pitting and erosion to the surface of the pumping gears, decreasing its performance and longevity. As cavitation worsens, the pump outlet pressure can no longer be maintained.
“The local pressure drop that causes cavitation is a factor of both fluid restriction and pump speed,” Barody continued. “Restriction can occur at the pump inlet due to an undersized feed line, restrictive fittings, or high oil viscosity. As pump speed increases, it is harder for the oil to fill the pumping cavities quickly enough to prevent a local pressure drop.”
“Cavitation is related to the high-speed operation of any oil pump,” added Mike Osterhaus of Melling Performance, Jackson, Michigan. “Cavitation will occur in any pump as the speed increases to the point where the oil can no longer fill the internal pumping chambers. If the inlet pressure drops below the vapor point of the oil then cavitation will occur, as oil vapor bubbles will form in the oil. The pressure regulation valve is designed to redirect some of the output flow back into the inlet port of the oil pump. The bypassed high-pressure oil increases the local inlet pressure to push back the onset of cavitation. This is referred to as supercharging the inlet, and it allows the pump to effectively operate at higher engine speeds. It is important to know that modifications made to redirect the bypassed oil to the sump (oil pan) instead of the pump inlet will negatively affect the oil pump’s operation and allow cavitation to occur at lower engine speeds.”
Osterhaus said that Melling’s Shark Tooth oil pumps for small block Chevrolet engines “utilize a helical asymmetrical gear set that improves the operation of the pump by significantly reducing the pressure ripple produced by spur-gear oil pumps. The helical-gear design provides more time for the oil to fill the gear set, resulting in improved performance and delaying the onset of cavitation.”
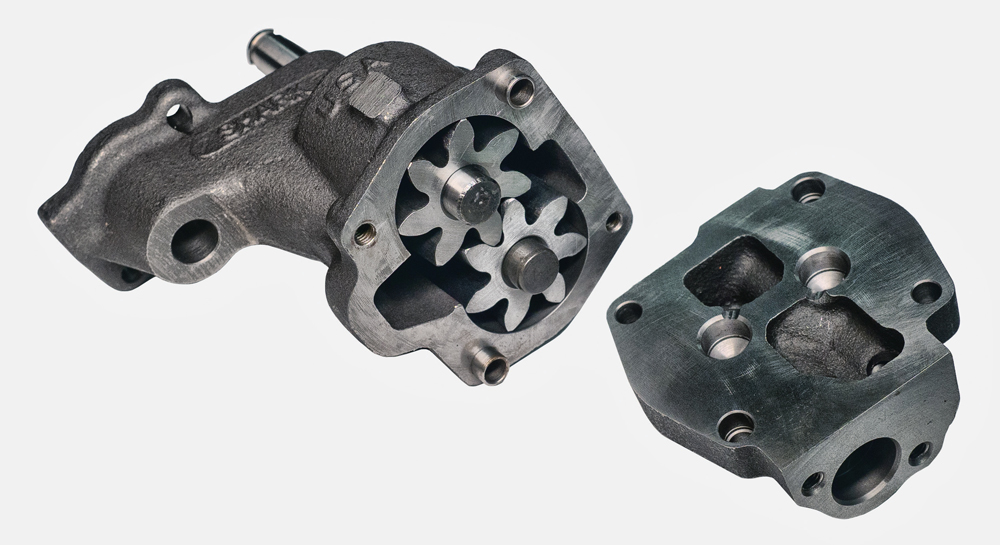
What’s the difference between a standard-volume, a high-volume, and a high-pressure oil pump?
“Standard volume relates to the volumetric flow rate matching the original oil pump for the engine,” said Osterhaus. “A high-volume oil pump produces more flow rate than a standard pump. This is accomplished by changing the rotor or gear set, typically by increasing the thickness of the set. A high-pressure oil pump indicates that the oil pressure required to open the pressure relief valve is increased relative to the original design. To do this, the design of the pressure relief spring is changed to apply more force to the pressure relief valve. This means an oil pump can be both high-volume and high-pressure.”
A high-volume oil pump, Osterhaus said, “will provide more oil flow to the engine across the engine’s operating range. Any modifications that will increase the engine’s demand for oil—larger bearing clearances, higher flow-rate lifters, adding piston and/or valve spring oilers—will require a high-volume pump. A high-pressure oil pump will supply additional oil flow at higher engine speeds due to less oil passing through the oil pump’s internal pressure relief circuit. Many factory stock performance engines came with standard-volume high-pressure oil pumps.”
Osterhaus also pointed out that “the oil demands of performance engine blocks with priority main lubrication are less than factory blocks, so a stock-volume oil pump is recommended. A high-volume oil pump will supply too much oil and result in high oil pressure across the engine’s operating range. In the case of GM’s LSX and Dart’s LSNext blocks, a stock-volume pump can provide too much oil. As a result, Melling has developed a low-volume oil pump for aftermarket LS engine blocks with priority main oiling systems.”
When making pump recommendations to customers, Schroeder uses these guidelines: “If the customer has a rear sump, where the deepest part of the oil pan is toward the back of the vehicle, like 1979–1995 Mustangs, and the oil pump is in the front of the engine with that big long oil pump pickup tube, I would recommend strongly that a high-volume oil pump be used. If the vehicle has an oil cooler, remote filter, and an extra-capacity oil pan, [and] is a street/strip car that also might see an autocross or go on a road course, I recommend a high-volume oil pump. If the vehicle is being used for drag racing, or is a street/strip car that will only be raced in a straight line and has to run a stock capacity oil pan, then I would recommend a standard-volume oil pump. For the vehicles that have the luxury of being able to run an extra-capacity oil pan, and are being used in a drag race application in which the operator of the vehicle is less inclined to watch their gauges, I would recommend a high-volume oil pump. If the last horsepower is trying to be freed up in a drag race car, even those with extra-capacity oil pans, then I recommend a standard volume oil pump, but stress that the operator has to be aware of what the gauges are telling them and to act if there is a severe pressure drop.”
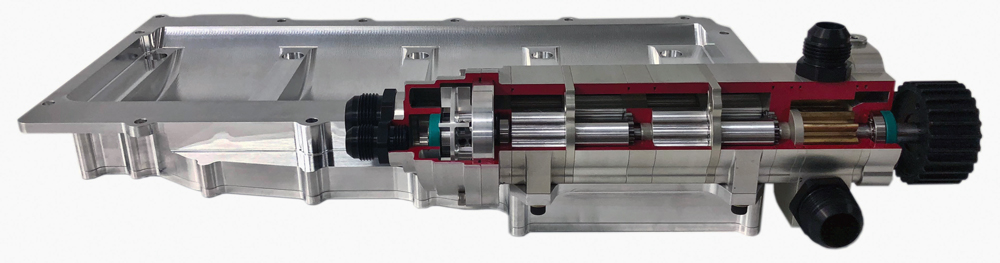
I put a vacuum-pump system on my car and now I don’t have the oil pressure I used to. What happened?
“Vacuum pump usage relative to oil pump functioning is the least understood thing with the racing public and even many engine builders,” said Verne Schumann of Schumann’s Sales & Service, Blue Grass, Iowa. “If you put a vacuum system on it, you’ve taken away the whole life-support system of priming the pump. Ninety-nine percent of oil pumps in the automotive world are vented to the atmosphere. The atmospheric pressure pushes on the oil reservoir pool in the oil pan and helps push the oil into the screen. Once the oil gets up to the gears, then it’s self-sustaining.
“Our Energy Recovery Engineering System takes the extra oil, commonly called the bypass oil, and pressurizes it to whatever the oil pump is set at, to send it back to the intake tube of the oil pump system. You’ll have the normal oil pressure and volume with the vacuum pump system operational,” Schumann added.
Do clearances and oil selection affect oil pump recommendation?
“They have a huge effect on the oil pump’s performance, so much so that we recommend the customer work with us directly,” explained Schroeder. “Other variables are the intended rpm range of the engine, if the engine is normally aspirated or has a power adder, and what fuel type the engine uses. From this information we can recommend which of our pumps be used, be driven at what speed, and even come up with a custom dry-sump pump specifically tailored to that application.”
What is the functional difference between a rotary (aka gear rotor or gerotor) and geared oil pump for a performance engine?
“A gerotor-style pump is a good slow-speed pump, but once it gets past about 4,500 engine rpm, it can’t pick up any more oil, or increase the volume or pressure of oil going through the motor,” said Mark Mittel of System 1 Filters, Tulare, California. “At System 1, every pump we make is spur-gear style. Our pumps will go up to 8,800 rpm before they start to nose over and cavitate. The spur-gear stuff is what you want if you’re going to set your engine on kill every time.”
“Gear rotor has been the OEM choice since the 1960s because it is more efficient,” said Schumann. “The exit speed of the oil—how fast it comes out of the pump, in feet per second—can be double that of a gear-to-gear pump.”
But in the performance industry, “two engines that constitute a big chunk of sales, the small block Chevy and big block Chevy, have gear-to-gear pumps,” Schumann added. “And they’ve gotten outdated by OE thinking and engineering of the gear rotor pumps.”
To help level the playing field, Schumann developed the Paddle Wheel oil pump, a gear-to-gear pump with scallops machined into each gear tooth.
“In a gear-to-gear oil pump, when you turn it over it squeezes the oil, and that oil oozes out of the gearset,” he explained. “With a Paddle Wheel pump, the oil oozes up to the paddles, and the paddles catch it and accelerate it. The net result is that the Paddle Wheel gear-to-gear oil pump is no longer obsolete.”

Can an oil pump make horsepower?
“Cars driven on the street today have oil pump systems that are roughly 30 percent larger than what the engine needs,” observed Schumann. “If you run a stock or super stock car with a typical old-school high-volume racing pump, it’s 30% bigger than a stock pump, and the stock pump is 30% bigger than what the engine needs. Add those up and now you have an oiling system that’s 60% larger than what the engine needs to survive. Racers and engine builders have figured out they can run a standard-volume oil pump because it’s still 30% bigger than what the engine needs.
“General Motors has told some of the best engine builders in the country that you can’t go less than their half-inch gear rotor pump for the LS engine (or the optional, non-warrantied 0.420-inch pump used for the COPO Camaro only),” he continued. “But we have people running 0.325-inch gear thickness in our drag strip pump, and they’re picking up 10, 12, up to 16 horsepower, depending upon how much overkill the system had before. And the bearing life has held up for the entire race season, no issues.”
DRY SUMP
What are the advantages of a dry-sump oiling system?
“With a dry-sump system, the oil pan is not used for oil storage as it is with a wet-sump system,” Baroody explained. “Instead, the pan is specifically designed to be as thin as possible while still effectively scavenging the oil that is suspended in the windage generated by the crankshaft. Oil is stored in an external reservoir, eliminating the risk of oil pump starvation caused by the extreme G-load effects during racing. With the use of a thin dry-sump oil pan and remotely mounted oil tank, the engine can be lowered in the chassis to improve the vehicle’s handling characteristics.”
“The primary advantage of a dry-sump system is its ability to make more power,” added Schroeder. “With very little oil in the pan, the rotating assembly is not burdened with the weight of excess oil (commonly referred to as ‘windage’). And because there is no internal pump, the windage tray or screen, which isolates sump oil from the rotating assembly, can run the full length of the pan. Keeping the rotating assembly free of windage allows it to spin freely and make more power. In addition, the extra crankcase vacuum created by the dry-sump pump helps to improve ring seal for additional power gain.”
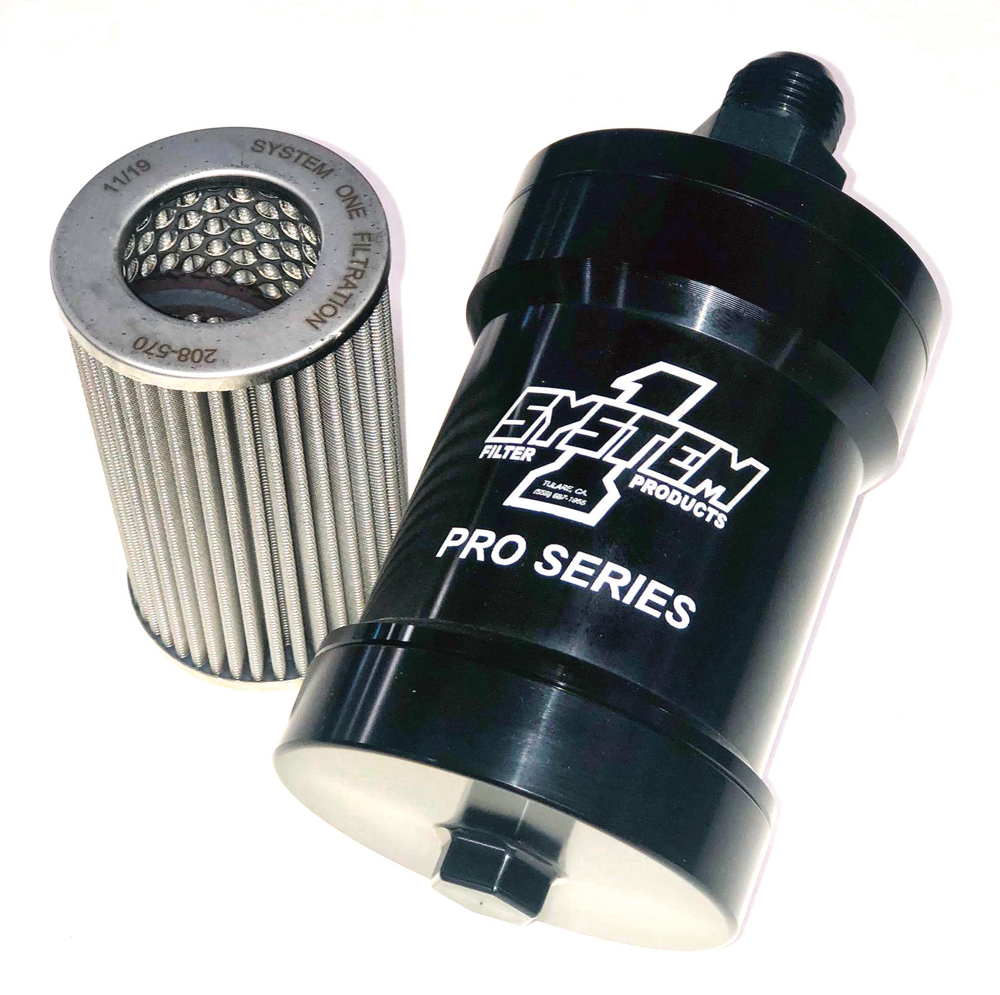
What issues come up when converting from a wet-sump to a dry-sump oiling system?
“Customers forget that engines equipped with a dry-sump oiling system must be sealed so they don’t pull in outside air,” said Schroeder. “That means no open valve cover, lifter valley, or crankcase vents.”
Can I adapt a pre-owned racing dry-sump pump to my engine?
“Buying pumps from used NASCAR engines and trying to adapt them on different racing cars is a big problem,” advised Stefan Verdi of Auto Verdi, Söderbärke, Sweden. “The pump will not work for them because the specifications of the pump will be wrong for their engine. The NASCAR engines often have a very small oil need compared to the engine’s size. A privately built engine will need a lot more oil, so the NASCAR pump’s pressure section is not big enough. Also, the fittings are custom made specifically for each NASCAR team, so they are not easy to find on the open market. If you do, they’re very expensive. The brackets that fit those pumps to NASCAR engines often won’t adapt to another engine. They will put the pump too far forward or too far backward. The whole thing will be wrong.
“In the future, some of the NASCAR teams will stop selling these pumps to the buyers who put them on eBay,” he continued. “They will destroy them. The latest generation of pump can never be used on another engine. It was too complicated to make and too complicated to adapt. The teams understand that people buy these pumps and then get angry because they won’t work on just any engine. So, they have started to destroy the parts rather than selling them and getting in trouble.”
What size dry-sump pump should I use?
“Initially we base the flow rate on what the factory pump’s GPM was and use that as a starting point,” explained Gary Armstrong of ARE Dry Sump Systems, Loomis, California. “There are other factors, too, so we always base our decision on the size, use, modifications and objective of the racing engine. We use a minimum of two, up to four scavenge stages, also depending on use.”
OIL FILTERS
Can an oil filter make power?
“With a free-flowing oil filter, the oil pump doesn’t have to work as hard to push oil through the filter, and the motor is not laboring to drive the pump to push oil through something that’s a little restrictive,” said Mittel of System 1 Filters. “I’ve heard our filter can make anywhere from seven to eight horsepower all the way up to 10 or 15 horsepower on the dyno. Now, there will be guys who say those numbers could be in the margin of error, or there were air changes in the dyno room—like if they went to lunch, came back, and there was better air quality in the room. So, we kind of stay out of that war, but we are freeing up the system, and it could possibly make more horsepower. We know it can give you better pressure because it’s less restrictive.”
Is there a rule of thumb about filter micron size and oil weight?
“System 1 makes 35-, 45-, and 75-micron filters,” responded Mittel. “The 35-micron filters are for the new kinds of lighter-weight oils, 0-weight or 10W20. When you get into a little bit heavier style oil, like a 20W50, or a straight 40-weight or 50-weight, we like to bump up to the 45-micron filter, which is a basic performance-style element. Anything over 50-weight you should go to the 75-micron filter, especially if you’re using a Lucas Oil additive, because that bumps up oil by 10—your 50 becomes 60, or your 60 becomes 70. The 75-micron filter has larger diameter wire where the cloth is woven, so it’s more robust.”
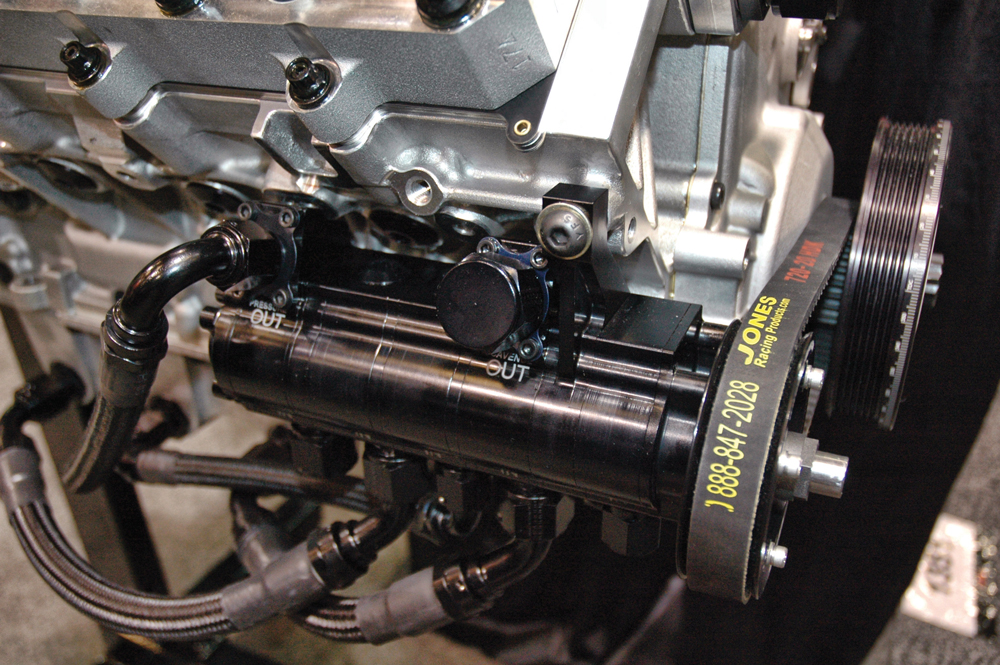
Where do the filters need to be in a dry-sump system and what micron size should they be?
“To properly filter the system you need three stages of filtering,” Baroody explained. “The first stage is a 730-micron filter in the oil pan that captures any large debris before it gets sucked into and damages the scavenge sections of the oil pump. The second stage is a 75-micron scavenge filter placed after the scavenge pump and before the oil tank. This keeps the tank clean and ensures the pressure section of the oil pump will be in good condition. If debris passes through the pressure section causing scoring, then the performance of the pump will be compromised. The third and final filter is the standard engine oil filter. This will be anywhere from 15–35 microns and should be the last component before the oil enters the engine block.”
How can you use an oil filter as an engine diagnostic tool?
“A cleanable, reusable filter is an excellent tool,” Mittel stated. “You can actually look inside the motor without taking it apart. You can tell what’s going on in the motor by the color of the debris in the filter. For example, the difference between a rod bearing and main bearing: A main will be more copper looking, where the rod bearing will have an aluminum look to it. You can pick out the bronze distributor gear, too. If the distributor gear is too far down, or not far down enough, the gear isn’t fully engaged where it runs on the camshaft. The gear starts to get eaten up, with material shedding off the gear. In situations like that, with the different kinds of materials in motors today, you can just about pick out what’s what in the filter. And in most cases, problems can be fixed before they become major.”
SOURCES
–