Custom Combinations
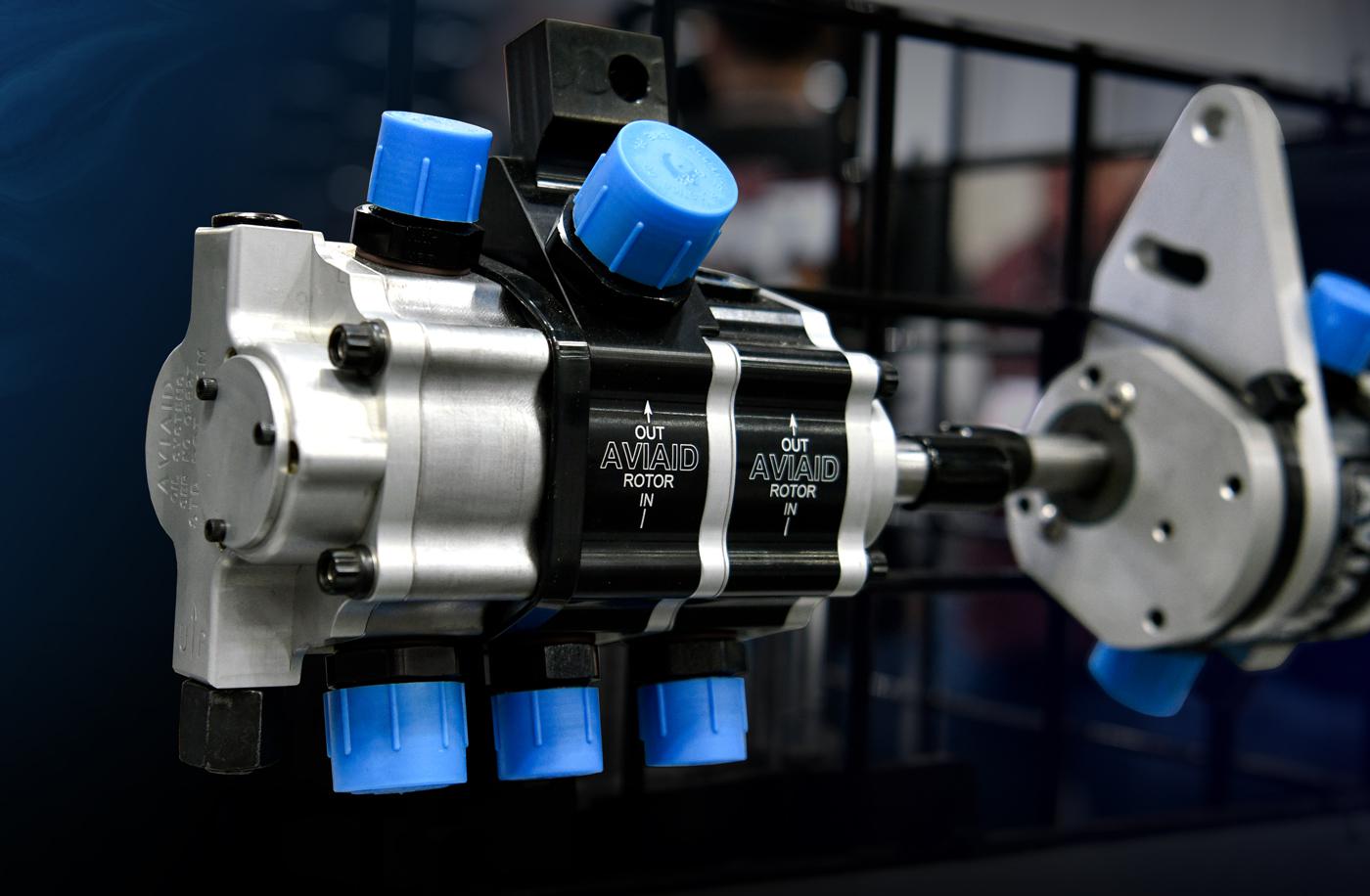
Oil system component manufacturers work painstakingly to provide tailor-made solutions to complex lubrication scenarios.
Amid all the bromides and sloganeering directed at the world of racing engines, this much is an unshakable truth: Inadequate oiling, for any reason, is going to invariably result in a dead engine and a lost race. Keeping the engine sated with slippery stuff is paramount. Doing so in an environment where physics, or simply rules, restrict the available room to package an engine’s oiling system is a crucial challenge.
Fortunately, the racing industry is well-populated with manufacturers who have been thinking about customized lubrication applications for a long time. The variety of components they offer to provide proper oiling in a tight space, or a constricted regulatory environment, is impressively broad and effective.
“We used to be more involved in custom oil pans, but now, it seems, we’re mostly advising other people on how to build their own because everybody seems to have their own CNC machines,” said John Schwarz of AVIAID, Chatsworth, California. “Typically, engine builders, chassis builders, people who are trying to package a dry-sump system into a vehicle are already making a lot of their own parts. What we do are basic lubrication system components.”
AVIAID’s entrée into customization is actually a very basic part, called a builder core, which is an unfinished oil pan stamping that’s 4.5 inches deep at the bottom, just like a small block Chevrolet V8’s wet sump. “If you’re building a dry-sump pan, with typically three or four different pickups, right or left side, the pan core becomes the framework that we build our features into to accomplish our goal,” Schwarz said. “Nobody runs wet sump unless they’re required to. Basically, someone will tell us where they have suspension components, crossmembers, transaxles; and the core is minimum displacement, as shallow and narrow as can be, and we add from there.”
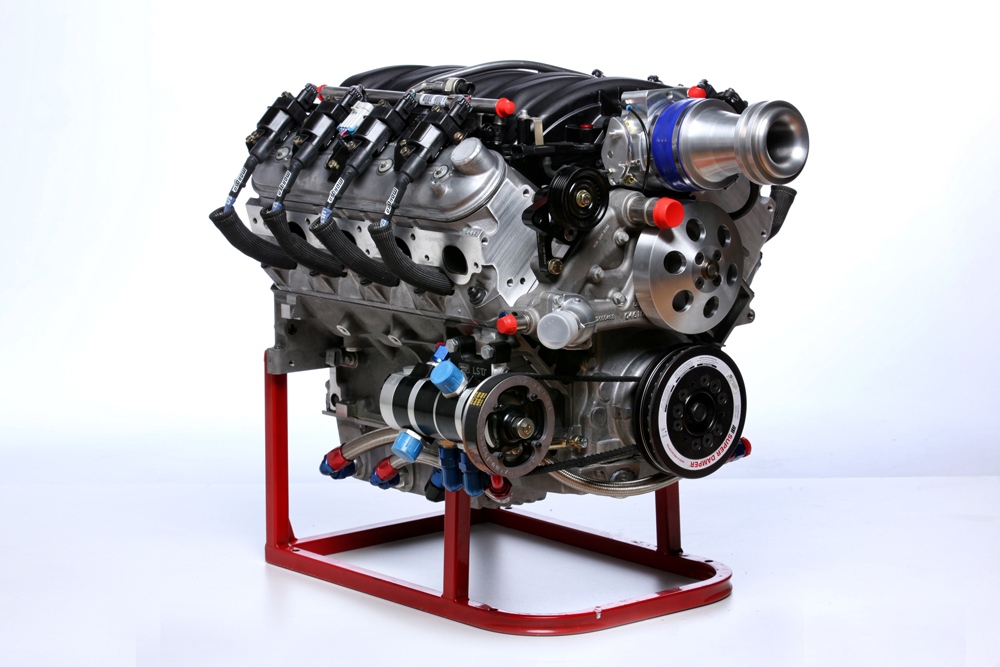
AVIAID currently offers a series of wet-sump oil pumps utilizing both belt and camshaft drive, with a variety of diameters and flow capabilities. AVIAID’s wet-sump pans are designed from the start for road racing applications, with the appropriate pickup locations for race cars turning left and right. The pans are fabricated from steel and cadmium plated. One application covers American Motors engines, in addition to the more common Chevrolet and Ford parts. ARP fasteners and Fel-Pro gaskets are standard with AVIAID installations.
Schwarz said that most US customers are using Chevrolet or Ford engines, which eliminates much of the dimensional guesswork. AVIAID also does extensive work with import-sourced engines and will have customers request an oiling solution for a turbocharged four-cylinder engine that has to fit tightly into a specific chassis space. “We also do a 5,500- to 6,000-horsepower John Deere engine with 5 pounds of turbo boost for tractor pulling. When I look at my catalog, I have 40 different ways to mount an oil pump.”
Working with a Legend
Melling Engine Parts of Jackson, Michigan, doesn’t offer custom-designed oiling systems per se, but Mike Osterhaus said that research with longtime customers can result in the kind of innovation that leads to custom packaging, or performance parameters.
“One such example is our 10294 low-volume performance LS oil pump. The idea for that oil pump originated from a conversation at the SEMA Show a number of years ago with Richard Maskin, the founder of Dart Machinery,” Osterhaus recalled. “At that time, Richard was developing Dart’s LS Next engine and needed a solution to an oiling issue he encountered. The LS Next design incorporated priority main oiling that supplied oil to the main bearings first before the camshaft, lifters, and valvetrain. In early testing, Richard found that the flow rate of the original Gen III oil pump created high oil pressure across the engine’s operating range. He had installed a variety of different pressure relief springs, but the oil pressure was still too high, and he needed a solution. The answer was in reducing the amount of oil flow provided by the pump.”
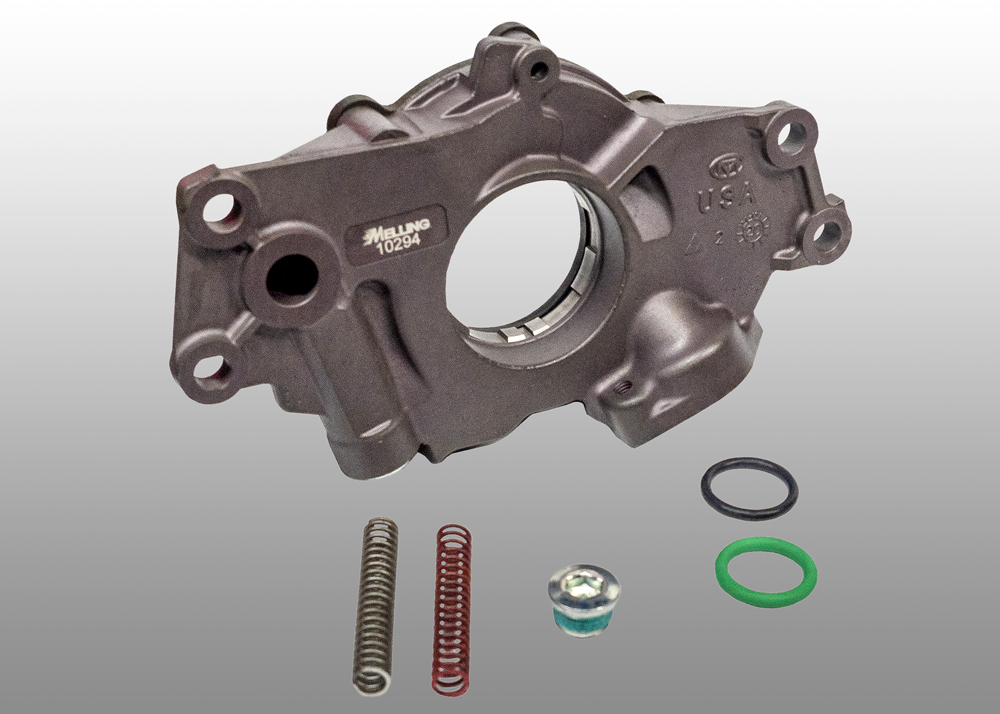
The LS oil pump is designed for use with performance aftermarket Chevrolet LS engine blocks with priority main oiling, and without variable valve timing or Displacement on Demand features. With 15% lower volume than stock, the high-pressure LS pump has a cast-aluminum housing, an anodized hard-coated body with phosphate-coated cover, and it utilizes standard steel rotors. A high-pressure spring is optional. The pump uses a 7/8th-inch bolt-on screen.
Melling built up a series of prototype oiling assemblies with stepped drops in oil flow for dyno testing. “We found that reducing the flow by 15% was the best solution,” Osterhaus explained. “With validation testing completed, we then moved to the production phase and added the pump to our performance oil pump product line. The 10294 low-volume performance oil pump comes with all the features that make the Melling Performance wet-sump oil pumps best in class. Features include a hard-coat-anodized housing, coated cast iron cover plate, exclusive rotor design, and optional springs to increase the pump’s original bypass pressure setting by 10 psi and 25 psi.”
Demanding Environment
Quantifying oil flow in customized applications was the same sort of research undertaken at Schumann’s Sales & Service of Blue Grass, Iowa, which currently has 13 patents applied for, pending, or issued for designing oiling solutions. Company founder Verne Schumann—who calls himself a tribologist, after the physical study of interactive surfaces in motion—said that much of his research and product development is aimed at race classes that require wet-sump systems due to rules.
“The most demanding oil-pump application in the country is 305 sprint cars because of their rpm potential, plus the fact that they’re mostly fuel injected and pushing out almost 2 horsepower per cubic inch these days,” Schumann said. “With promoter’s restrictions, such as flat tappet camshafts or compression ratios, they’re doing it the hard way. It is the most demanding because you have to use 305 bore and stroke and the 42-pound crankshaft. The oiling system on a 305 is just as demanding as a 360 or a 410 Outlaw motor.”
The research led Schumann to develop a $400 oil pump for wet-sump applications, and to develop a new way of measuring oil flow, in feet per second. Schumann’s specialized solutions include the patented Paddle Wheel configurations for common gear-to-gear oil pumps, which result in higher flow rates at both GPM and feet per second at the same engine rpm, requiring less horsepower to move the oil. The firm also produced the ER-VAC wet-sump pump system that allows for maximum energy recovery while being unaffected by G-loadings, a key consideration for rock crawlers and Monster Truck teams. Schumann’s has also developed its 140 Ball Valve, which reacts in a fraction of the time needed by conventional OEM-style cup valve systems, allowing surplus oil to vacate the sump at lower oil temperature and with no impact on ignition timing.
Conventional gear-to-gear oil pumps essentially squeeze the oil to move it via the curvature of the teeth in the gears as they rotate against each other. The Paddle Wheel gearing incorporates cup cavities in the pump’s idler gear that aim high-velocity oil at the outlet of the pump. While the meshing of the gears is the primary means of moving the oil, the Paddle Wheel adds a secondary level of oil transfer within the same pump housing.
Schumann’s offers performance wet-sump oiling systems for truck, circle track, and drag applications, the latter including atypical engine applications such as the big-block Oldsmobile. The same “dimple tech” gear design incorporated in the Paddle Wheel is also utilized by a high-performance wet-sump pump created for the 2.5-liter Subaru engine.
“What makes the Paddle Wheel work is when oil oozes up through the idler gears, the gears are parabolic shape, but the cavity cup is exactly the opposite, spherical,” Schumann said “Each tooth on the idler gear has a cavity cup machined into it. So we came out with feet per second measurement.”
Customizing Off-the-shelf Components
Peterson Fluid Systems of Longmont, Colorado, offers several options for custom components, ranging from single, one-off custom pieces to engineered parts ordered in limited quantity. The firm expects to resume fabrication of custom sump tanks shortly. Typical custom parts are oil pumps, as Peterson works with engine builders on specific requirements regarding flow rate and the type of scavenging needed for a particular application.
Peterson pumps can range from one to eight stages, with multiple sizes of rotors and different shaft designs and lengths for the pump drive. Since the pump is modular, most custom pumps utilize off-the-shelf components. Due to the unique design of the R4 l pump, it allows for a solid foundation from which a plug-and-play type construction can be built. The combination of off-the-shelf components allows a custom application with minimal additional custom machine work. In most cases, the custom components are centered around the shaft assembly, such as a male hex key for the installation of a front-mounted ProCharger supercharger.
Dry-Sump Offerings
When it comes to dry-sump oiling for performance engines, two of the industry’s pioneers are Gary and Sandy Armstrong, who founded Armstrong Race Engineering in 1974, and first began fabricating dry-sump oiling systems after getting their start building race engines. Gary Armstrong started making dry-sump pans out of cast alloy 356A T6 aircraft aluminum, the same material used for oiling systems by numerous Formula 1, Indy car, and Le Mans racing teams. Within 10 years, ARE Dry Sump Systems was building products for competition Corvettes and Formula 5000, as well as NASCAR teams, and was no longer building racing engines.
The Armstrongs are now in the process of selling ARE Dry Sump Systems to Kragen and Rachel Faulkner of Oroville, California, and their business, Advanced Race Engineering Inc. The company still lives up to the Armstrong standard of comprehensive dry-sump solutions, with more than 55 different dry-sump pans currently produced, mostly CNC machined. As Gary Armstrong explained, “The state-of-the-art designs led us to contracts with GM, Chevrolet Racing, TRD, Honda, and so on, which carry on to this day. Our desire to build high-tech, dyno-proven dry sumps by working directly with the factories and pro engine builders has always kept us up front.”
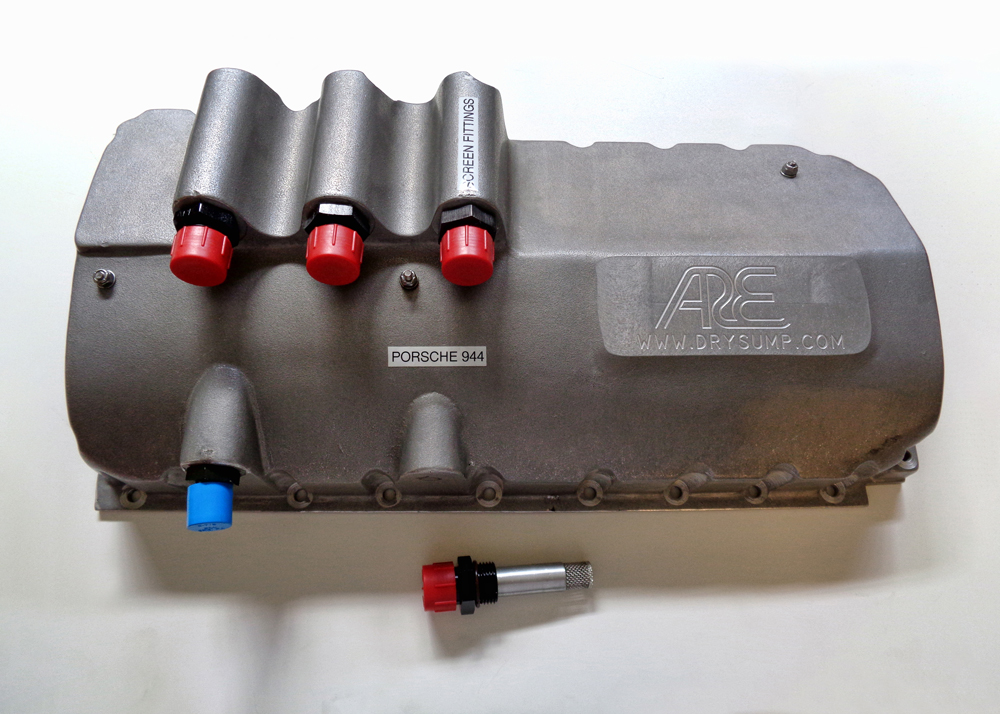
The Armstrongs aren’t ready to retire, not by any means. In 2011, they formed Spintric Technologies, which created and continues to market an inline air-oil separator for dry-sump systems. “As most dry sumps scavenge out two to three times more air than oil out of engines, this invention separates as much as 80% of the air on the return to the pan,” Gary explained. “Now, there are 10 patents on Spintric products, including our dry-sump tanks, atmospheric vent cans, air-oil separators, filter adapters, screens, and more.”
Gary Armstrong received a patent in 1983 for a mechanical separator for air and oil incorporated within the pump of a dry-sump oiling system, using the physical concept of centripetal force. The Spintric, as designed, has no moving parts and is mounted separately from the pump. The separation force is generated by the internal channels of the Spintric as oil passes through the assembly. The percentage of air varies with pump rpm, oil temperature, and flow volume.
Packaging Requirements
At FLUIDYNE High Performance in Mooresville, North Carolina, Gary Johnson said the firm’s oiling answers are largely determined by the space and packaging requirements dictated by customers.
“FLUIDYNE makes a wide variety of oil coolers, which are available in different shapes and sizes in an effort to accommodate our customers who present us with various types of oil cooling challenges for aftermarket applications,” Johnson said. “These challenges are normally resolved by offering packaging solutions where we help the customer place the right-sized oil cooler in the best location available in his vehicle to achieve maximum cooling performance.”
Insurance Protection
Some oiling solutions can be made applicable to both dry- and wet-sump lubrication systems. At Canton Racing Products in North Branford, Connecticut, engineers have developed an intermediate component that ensures the crucial bearings are properly fed under all rpm and loading scenarios. “Our Accusump oil accumulators, which we’ve been producing for more than 35 years, would be the best fit for a custom application,” Iann Criscuolo explained. “Accusump stores pressurized oil from a canister with oil on one end and air pressure on the other side. When oil falls below [the oil level] in the Accusump, it pushes the oil to supply the engine bearings under high-performance applications in any kind of racing you can think of, for both wet-sump and dry-sump systems.
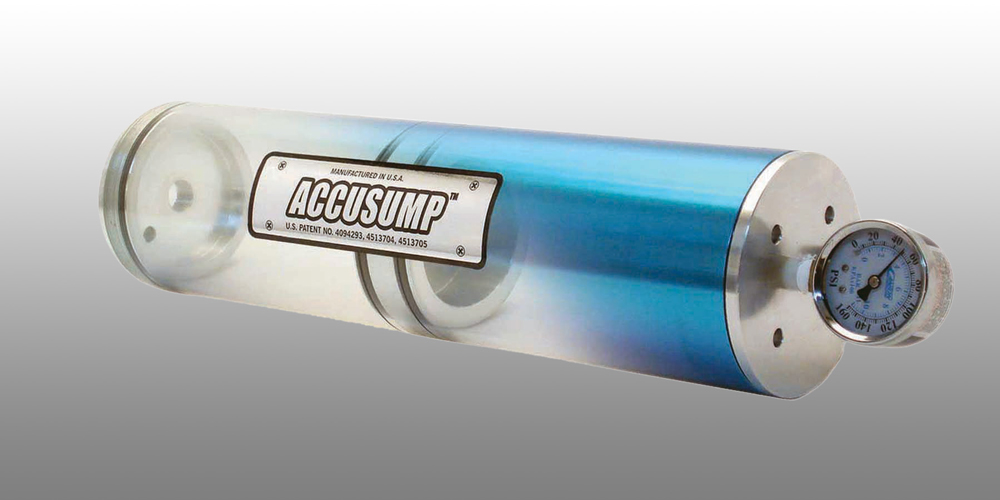
Canton markets the Accusump system as one of the most original designs of automotive oil accumulators on the market today. Each Accusump accumulator is precision fabricated from heavy-wall, roller-burnished aluminum tubing, with a Teflon hard-coated interior. Each accumulator uses a billet aluminum internal piston with screw-in end caps and is equipped with an internal pressure release valve. For turbocharged applications, Canton also produces the Accusump Turbo-Oiler, which supplies a pressurized flow of oil to hot turbocharger bearings during spool-down, making bearing failure less likely. The turbo after-oiler prevents heat-related coke buildup, which can limit oil flow to the turbocharger bearings.
Variations in ambient air pressure and oil viscosity determine how quickly the oil dumps from the Accusump, with Canton engineers recommending 5 to 7 psi. Canton is primarily focused through its product lineup at budget-minded racers, so the majority of its catalog deals with wet-sump systems, which have broad applications including oval track, road racing, autocross, off-road competition, and even aircraft.
“There are only a few things that can really be customized, one by purchasing the size of components they really need for their type of engine, or that need pre-oiling to stop dry-start scuffing inside the engine,” Criscuolo added. “The Accusump is more of an additive to someone that has an oil system already. It can improve the longevity of the race engine, as well as being a little insurance that the oiling system isn’t going to be an issue.”
Sources
ARE Dry Sump Systems
drysump.com
AVIAID
aviaid.com
Canton Racing Products
cantonracingproducts.com
Champ Pans
champpans.com
Clear View Filtration
clearviewfiltration.com
FLUIDYNE
fluidyne.com
Jones Racing Products
jonesracingproducts.com
Melling Performance
melling.com
Moroso Performance Products
moroso.com
PBM
pbm-erson.com
Peterson Fluid Systems
petersonfluidsys.com
PWR Advanced Cooling Technology
crracing.com
Schumann’s Sales and Service
schumannssalesandservice.com