Driver's Cocoon
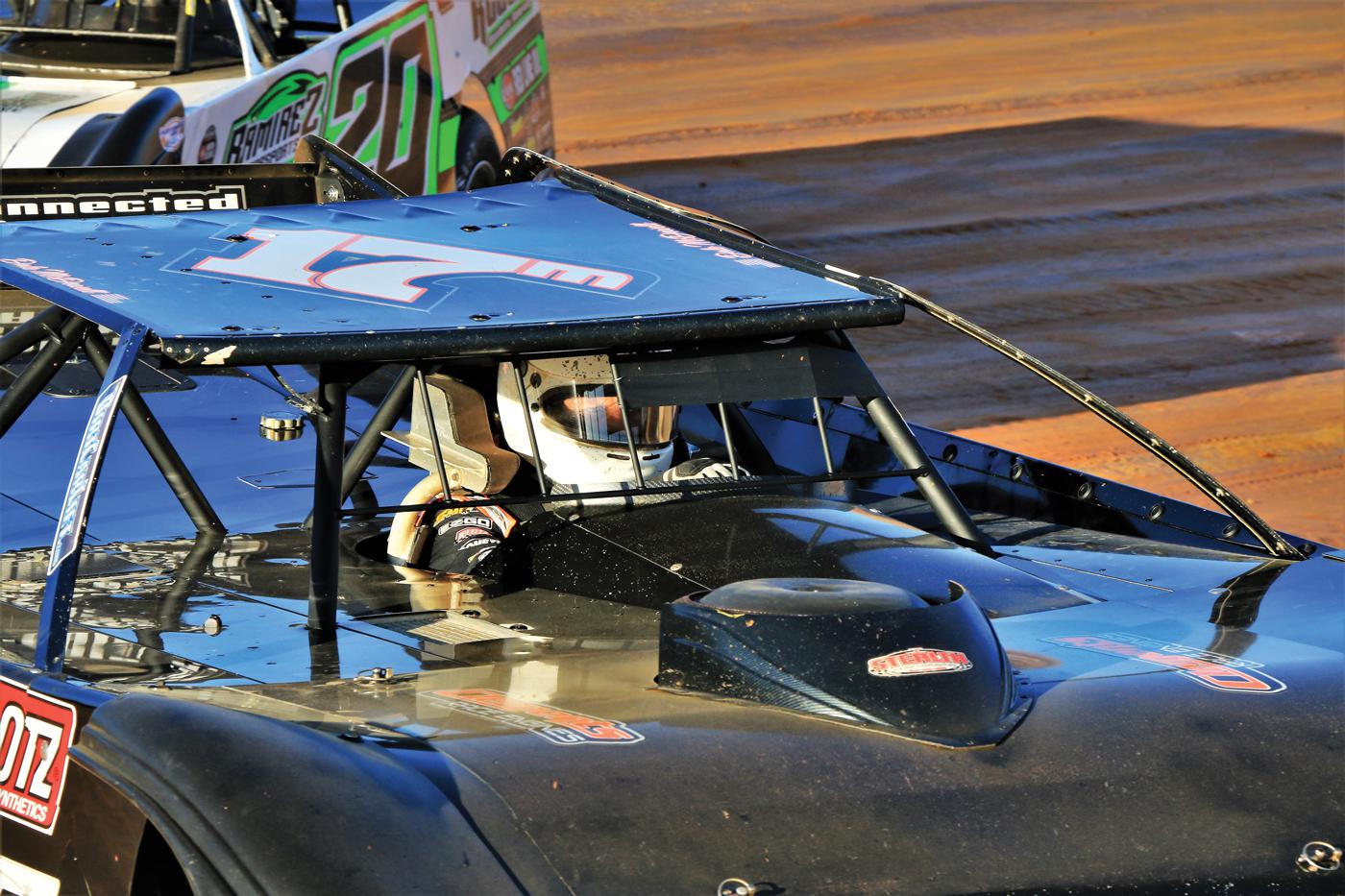
The science and innovations that are creating safer seats in motorsports.
In 1984, Randy LaJoie snapped loose coming out of Daytona’s fourth turn during a qualifying race for the Daytona 500. His No. 07 Chevy went into a long slide, and then a short flight, before finally smashing the inside wall—bottom-side of the car first—and rolling end-over-end.
Miraculously, LaJoie was left relatively unscathed beyond a concussion. When recounting the story, the two-time NASCAR Xfinity Series champion believes his seat kept him safe that day.
“I had a Mark Donohue-designed fiberglass seat that my dad purchased from him in 1971,” said LaJoie. “My dad was a racer and Hall of Famer in New England, so good enough for him, good enough for me. But I had to sign a waiver before I went out to qualify [at Daytona] because [NASCAR] had never seen a seat like that. It was a bucket seat, it had a frame around it, no padding in it, it was painted white. It looked like a damn bathtub.”
NASCAR allowed LaJoie to keep using the seat—until it banned fiberglass seats in 1992. Unwilling to abandon his rounded seat and disappointed with the absence of rounded aluminum seats on the market, LaJoie founded The Joie of Seating in Concord, North Carolina.
After 30 years in business, LaJoie continues to learn and innovate. “We’ve learned the less the occupant moves, the better they’re going to be.” As a self-described “test-dummy” for his first decade in business, LaJoie applied the lessons of his past hits to provide better safety for today’s racers.
“We’ve gone the strong seat route. I started that probably 25 years ago with putting tubing around the seat. When I hit stuff hard, the Monday and Tuesday were a lot nicer when I didn’t move so much.” According to LaJoie, the rounded seat design only further bolstered seat strength. “It’s a very strong seat because of the shape. You fit the body 50% better because of the round butt, whereas there’s lots of voids sitting in a square.”
Selling seats is LaJoie’s business, but educating local racers about safety is his passion. Every year, LaJoie takes his safety sermon on the road. In 2007, he launched the Safer Racer Tour and visited local tracks to spread knowledge to grassroots racers about safety innovations.
“I’ve been to 185 race tracks, but when I first started going on the road, it was 20% good seats and 80% bad ones, maybe even under 10% good ones. Now I go and it’s 80% good and 20% bad.”
Significant innovation in seat technology has elevated safety in all forms of motorsports, giving today’s drivers the best chance of surviving even the most horrific crashes. As LaJoie pointed out, there’s still work to be done at the grassroots level, where unsafe seats still result in preventable injuries and death.
As an industry, our challenge is less about figuring out how to make seats safer, and more about convincing every racer that their lives are worth the investment.
Specs Save Lives
Not long ago, race seats were unregulated and up to the racers’ discretion. Racers are notorious for cutting costs in the safety department, but thankfully a rise in sanctioning bodies requiring certified seats has significantly increased safety outcomes.
Two main organizations set safety standards, while also testing and certifying that seats meet appropriate safety specifications: The SFI Foundation, Inc. (SFI) oversees safety standards for prominent North American sanctioning bodies including NASCAR, NHRA, and World of Outlaws, while the Federation Internationale de I’Automobile (FIA) oversees safety standards for international racing series including Formula 1, World Rally Championship, World Endurance Championship, and more.
“[SFI] came up with a 39.1 spec, which is a 100G hit,” said LaJoie. “The seat cannot flex more than half of an inch, and it must come back within 1/4 inch of where it started. NASCAR mandated that in 2011. SFI also made a 39.2 spec for all the short track series, which is half of the spec of the big guys. It’s half as strong, but that’s still a push load of 2,000 pounds for the head, 3,000 pounds for the shoulder, and 4,000 pounds for the hip. It’s a great spec.”
While the SFI 39.1 spec is required in NASCAR’s top divisions—Cup, Xfinity, Trucks, and ARCA—the adoption of the 39.2 spec seat has been slower, though progress is happening.
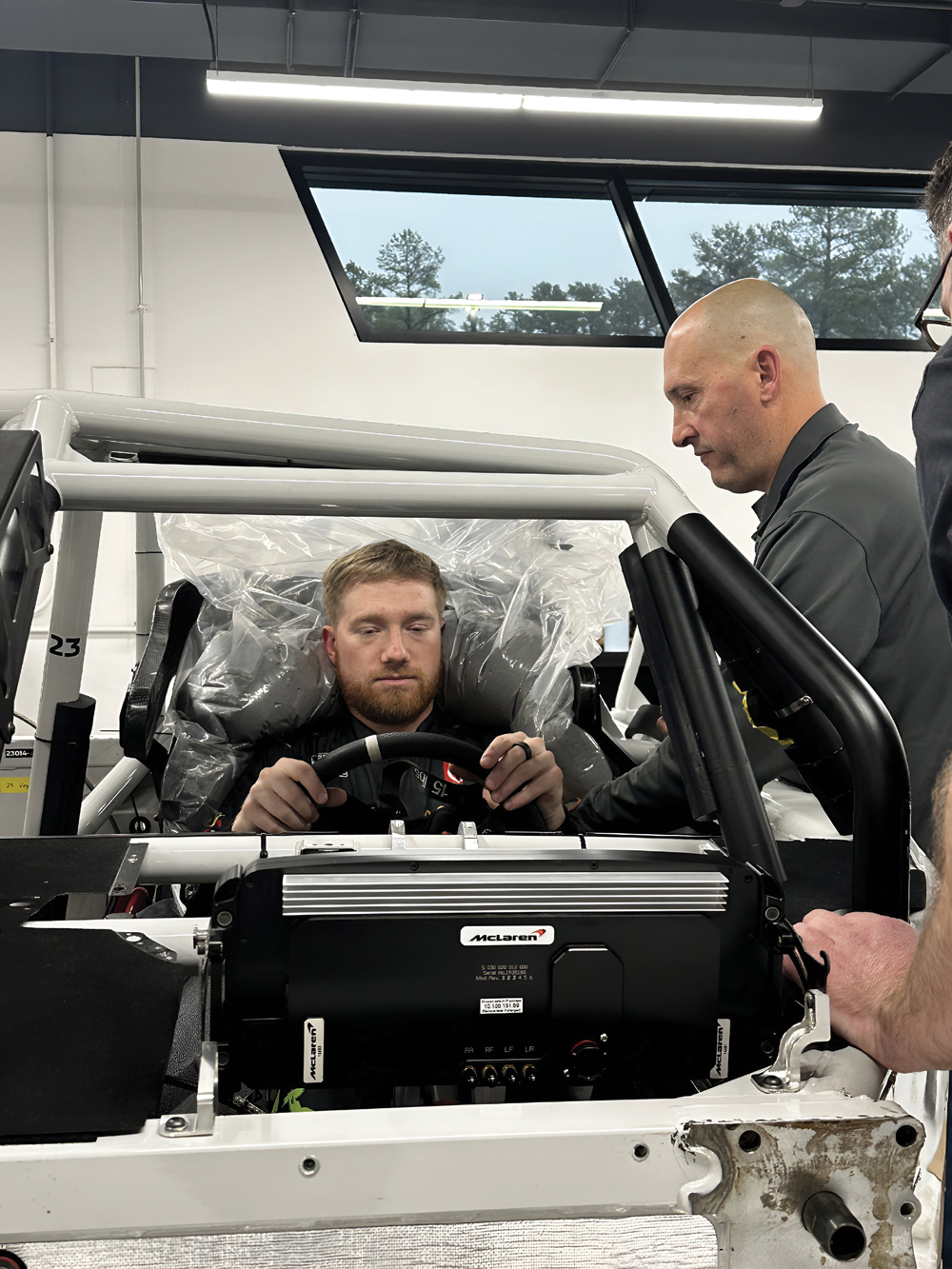
“World of Outlaws picked it up, Lucas Oil Late Model Dirt Series picked it up, and next year all traveling dirt series teams will need to have a certified 39.2 seat,” said LaJoie. “That’s still 14 years after NASCAR mandated a certified seat, and a lot of guys got hurt in between those 14 years, just because they move too much.”
FIA seat safety standards have been around longer, with the FIA 8855-1999 spec ratified in 1999.
“FIA 8855-1999 involves sled testing of the seats with a Hybrid II dummy strapped into the seat,” said David Black of Racetech Manufacturing, Seaview, New Zealand. “20G rearward [first impact], 15G sideways, and 10G rearward [second impact]. The shell of the seat must show no signs of cracking or delamination. Rules around padding and brackets are quite loose. This standard still has its place in a number of forms of motorsport and is certainly a big improvement over no standard.”
The FIA made a significant improvement upon that standard with its 8862-2009 spec, one that Black described as a “huge leap forward in race car safety.”
“The FIA 8862-2009 was ratified in 2009 after many years of development and testing to prove the concept,” continued Black. “This is a quasi-static test, which is more repeatable and provides a rough equivalent load of 70G lateral and rearward. It also requires the energy foam to be in place, along with the fire-resistant cover. Plus, the seat must be mounted into the car with the brackets it was tested with. The loads applied equals about 3 tons at one time and must hold for 60 seconds, with specified deflections at each part of the seat—the head, shoulders, and pelvis. Most GT racing, V8 Supercars, British Touring cars, and WRC rally cars all use 8862-2009 seats.”
Ultimately, the right spec depends on the race vehicle and its usage. But even a basic spec will be a quality seat. Fred Bickford at ButlerBuilt in Concord, North Carolina, offered straightforward advice for racers in the market for a quality seat: “There are lots of ‘crash’ products out in the market today. But I would advise consumers to request test data or have a certified spec with the product.”
The Foam Frontier
Rapid developments in impact-absorbing foams are making a big difference for racers across a variety of disciplines.
“Padding has evolved greatly over the past quarter century,” said Matt Ray at Impact Foam Solutions, Cornelius, North Carolina. “Most seat foams were nothing more than furniture foam in the late 1990s. Through research and development, superior foam products were developed specifically for motorsports. The SFI 45.2 specification was introduced in 2002 to create a minimum standard for impact padding.”
The adoption of the SFI 45.2 spec helped standardize and propagate effective impact padding to drivers in all forms of racing, significantly reducing head and body injuries. Just as important is how teams and manufacturers layer padding to maximize impact absorption.
“The benefit of the foam materials depends on the seat structure it is installed into,” said Ray. “A rigid seat structure allows the foam to perform more of the energy management it was designed to do. Different density and stiffness foam materials are used in areas of the seat and head surround.” For example, Impact Foam Solutions created a new rear head foam that is “lighter and softer” than the SFI 45.2-approved foam it produces.
Several sources discussed the importance of layering multiple different foam densities, particularly in their headrest designs.
“In [Racetech’s] 119 range of seats, there’s two different foams in it—an FIA-approved energy foam and then a layer of EVA, which is just a little bit softer for taking the vibration out of rough roads,” said Black. “Obviously, it’s quite important to absorb energy at different rates. General driving, where [your helmet] is bumping against the headrest, is one thing, but when you have an impact, you need to have that much harder energy absorbing foam there to accept that impact.”
Different foam densities serve different purposes, but layering them together protects drivers from both small and large impacts. RECARO Automotive in Clinton Township, Michigan, has used this same approach to lessen impacts drivers feel.
“We developed technology where you take a foam that’s harder, and then we layer it up with softer foams,” said Nicole McElroy of RECARO. “The hard foam has a lot of cells to it, so the energy dissipates when it goes through that foam. By the time it gets to the top layer, all that energy is not getting put through the body.”
Sprint car racing—where crashes often involve wild barrel rolls—is a discipline where foam plays a critical role. However, it’s not the rolling that scares drivers so much as that final landing.
“The concern for the sprint car driver is that last four-wheel, bottom-out smackdown after a tumble,” said Bickford. “This is a literal back-breaker crash and, in extreme cases, paralysis.”
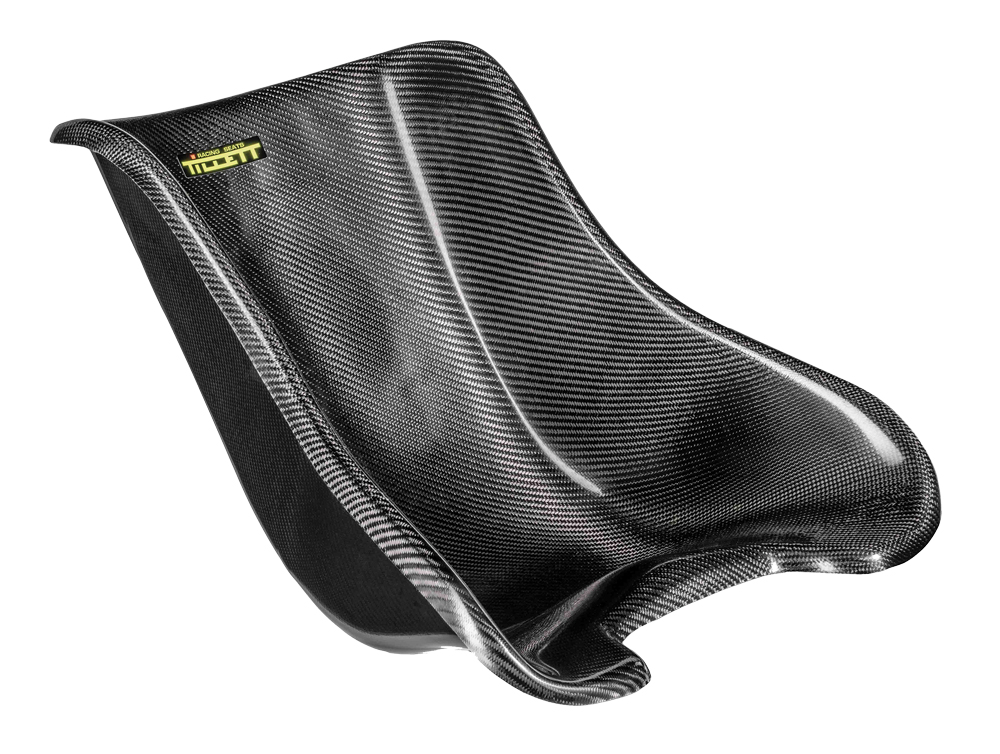
This exact scenario happened to NASCAR Cup Series driver Alex Bowman in 2023, resulting in a fractured vertebrae that forced him to sit out multiple Cup Series races. While ButlerBuilt does not produce foam, it is constantly working on ways to develop both seat design and foam placement to improve outcomes for drivers.
“We used CNC-cut custom scanned inserts from the 45.2 foam with increased thickness to absorb more energy in high-impact wrecks,” said Bickford. “We also changed the head-and-neck device clearance points to take pressure off the back and shoulders at the point of contact, securing the driver back in the seat for a tighter fit. [World of Outlaws driver] David Gravel has been testing sprint prototype seats and foam over the last two years for real-time feedback.”
Necessitated by the stiffness of the Next Gen Cup car, NASCAR teams have also been experimenting with foam layups in headrests to improve safety outcomes.
“[NASCAR] used to mandate 3/4 of an inch [of padding] behind the head, because the older cars had so much crush in them, they had 6 feet of crush behind the driver,” said LaJoie. “With this [Next Gen] car, you only have 2 feet of crush, so now there’s 3 inches [of padding] behind your head.”
Fit is Function
During on-track battles, the last thing drivers should worry about is their seats. While the safety and strength of a seat are critical during a crash, the fit and comfort of a seat make a difference each lap.
One size does not fit all when it comes to race seats. “Make sure you get the right size seat to fit your body. That’s part of the reason we have four sizes of most seats,” said Black. “Every human is a different size, so it’s crucial that the body is supported at the right level, the right height in the car. The eye is about the center of gravity of the head, so that should be within the head restraint of the seat.”
Another consideration is ensuring the seat aligns body positioning and provides secure support, not distracting aches. At RECARO, McElroy said each seat design starts with a focus on comfort and body positioning.
“We start with the curvature and body positioning in a seat, and then use that as our basis for formation of the seat. That allows us to make sure we’re holding the body correctly at the right angle,” she said.
Not only does this improve comfort during the drive, but research has shown it also reduces fatigue. “We just did a study with Michigan State University (MSU) with female drivers, and it showed they’re using less energy burn in our seats, which is good,” said McElroy. “That means they’re probably having less fatigue.”
Improved comfort and reduced fatigue allow drivers to focus their full attention on driving the car—increasing both on-track performance and overall safety.
“We’re constantly working on the next way to increase safety and comfort together,” said McElroy. “If you’re not comfortable, you’re never going to be safe, because it’s a distraction.”
Based in Kent, United Kingdom, Tillett Racing Seats made its reputation by manufacturing hand-crafted kart seats. The brand gained popularity due to its carefully sculptured shapes, providing drivers with comfort and feedback from the kart, while at the same time having the rigidity for speed.
“Through many years of karting experience, we learned how to hold a driver comfortably without padding,” said Laura Tillett. “We develop the shapes millimeter by millimeter feeling every pressure point, then scraping it away until the body is loaded evenly. We do not use CAD to initially design the seats, everything is done by hand. That way we can provide the perfect feel from the vehicle and give superior support, without hindering the parts of the body that control the vehicle.
While its origins are in karting seats, Tillett has also expanded its “perfect feel” seats to road and track cars. The copyrighted shapes, some of which are FIA approved, allow the foam to be minimal, giving better feedback from the car and enhanced support during longer stints.
“The seats are incredibly compact, which means the driver can sit lower with superior leg room,” said Tillett. “Our seats are very popular in cars with space restrictive cockpits, such as Lotus and Corvettes. In the UK, the seats are a common aftermarket choice for the driver who wants high quality, safety, weight savings, and extra headroom. We are looking to offer these attributes to the US drivers, too.”
Life-Saving Investments
From setups to engine components, achieving success in racing requires access to trusted information. The same is true for safety in race seats.
“Really do your research and make sure you get somebody with the right expertise and experience to give you the right advice,” said Black.
A friend at the track may swear by his favorite old-school seat, but if put to the test, the laws of physics may not agree. Buying a seat with an official SFI or FIA safety certification is the safest way for protection in a hard crash, keeping in mind the type of racing where the driver competes.
“It’s just understanding the usage of your vehicle and what your intention is,” said McElroy. “You can spend as low as $300 for an FIA-certified seat, but is it the right seat for what you’re using it for, and is it going to meet the requirements that you’re expecting?”
Still, the final hurdle is to convince every racer and every race series to prioritize safety and require their competitors to use race seats that meet certified standards.
“I hope that [local] racers will push toward certifying their seats,” said LaJoie. “Because a guy’s life on Thursday, Friday, and Saturday is no different than a guy’s life on Sunday.”
Inside Dallara’s Mission to Build a Safer Cell
The Indianapolis 500 is the Greatest Spectacle in Racing: 33 IndyCars battling wheel-to-wheel, reaching speeds approaching 240 miles per hour. This annual spectacle is riveting but filled with danger. Spectacular crashes are a common occurrence.
To protect drivers at Indy and during every race on the schedule, IndyCar’s exclusive chassis supplier, Dallara in Speedway, Indiana, has created a “cocoon” within the car to protect drivers. Commonly known as a monocoque safety cell, it has been refined and strengthened over the years to better protect drivers.
“The chassis monocoque itself is carbon fiber with aluminum bulkheads,” said Dominic Coffey of Dallara. “Above that there is EPP [expanded polypropylene] foam below the driver, on the driver’s back, and on each side of the driver. Then on top of that is the custom-made, driver-specific seat. We don’t manufacture the [seat]; that’s up to the teams to either pour a seat or have one machined of similar EPP foam.”
Over the years, Dallara has continued to make safety updates. For example, the headrest is now constructed with multiple foams in a single bonded assembly, where in the past those headrests could be multiple separate pieces.
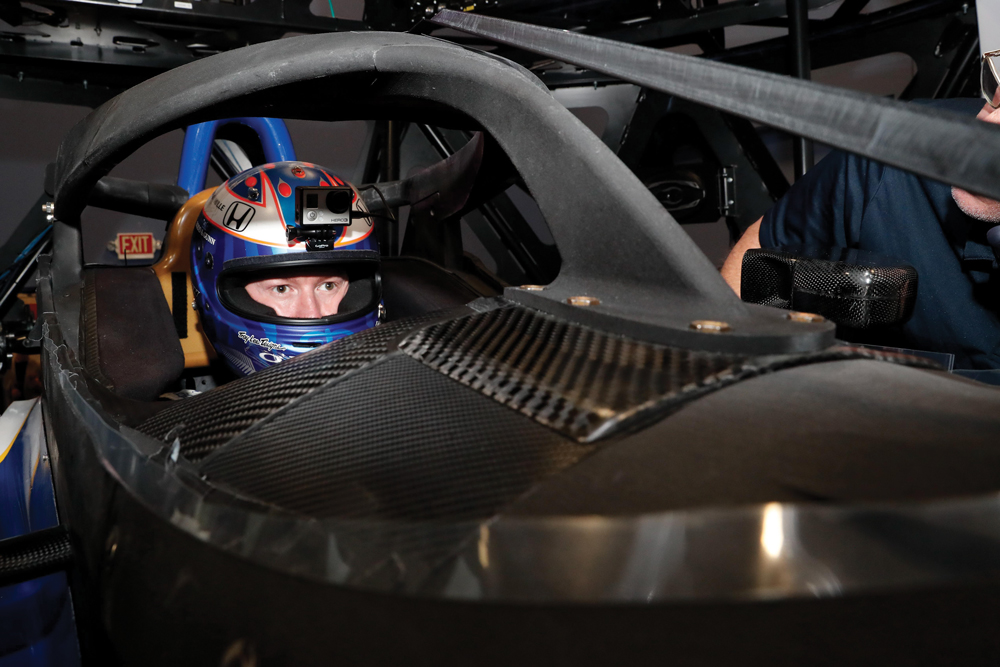
The monocoque’s most significant recent safety development came five years ago with the addition of an aeroscreen. This innovative safety device provides complete driver cockpit protection, with a ballistic windscreen from PPG anchored by a titanium framework produced by Pankl. While other open wheel racing series commonly use a Halo to protect drivers from cockpit intrusions, high-speed oval track crashes and their expansive debris fields necessitated a full coverage option.
“We started in roughly March 2019 with IndyCar and Red Bull Advanced Technologies,” said Coffey. “There was a lot of CAD design work and a lot of analysis of crashes that had already happened. We developed something called the Helmet Exclusion Zone, which is an area behind the windscreen where there can’t be any ducting or any fairings, because that’s the accepted area where you could expect the helmet to be in a big crash. The aeroscreen and the upper titanium frame do not intrude on this Helmet Exclusion Zone.”
After a few months of development, the team was confident in the safety and integrity of the aeroscreen. But before taking it to the track, they tested the concept on Dallara’s world-class driving simulator.
“We got a rapid prototype dummy version of the titanium frame and the aeroscreen profile to put it in the simulator. Then we had a driver, Scott Dixon in that case, get in there and define if the sightlines were good and if he was happy with what he was seeing,” added Coffey.
By the start of the 2020 season, the aeroscreen was ready to use during all races. Dallara has continued to make tweaks in the last couple of years, including raising the sides of the headrest to provide enhanced lateral support. This season, Dallara introduced the second version of the aeroscreen, which is lighter and includes 3D-printed TPU rubber air vents.
“The benefit of these ducts is one, that it pushes as much air to the driver as we can, but also that the rubber acts as a good energy absorption area,” said Coffey. “If the driver’s hand gets thrown into this rubber duct, it’s going to absorb quite a bit of energy, rather than just being thrown right into titanium.”
For the Dallara team, safety developments are a constant pursuit. While the monocoque dates to 2012, continual upgrades have pushed the overall safety and strength of the car to new levels.
“The structure supporting the titanium frame added a lot of stiffness to the monocoque,” said Coffey. “With the new bodywork for the car in 2018, the structural sidepods have crash structure inside that’s immediately next to the driver, that also provided a big increase in the strength and stiffness of the car. So those two things together were quite a big jump in a very short amount of time for the safety of the car.” —Jack Haworth
SOURCES
ButlerBuilt
butlerbuilt.net
Dallara
dallara.it/en/dallara-usa
Impact Foam Solutions
racetech-usa.com/shop/impact-foam-solutions
Racetech Manufacturing
racetechseats.com
RECARO Automotive
recaro-automotive.com/us/
The Joie of Seating
thejoieofseating.com
Tillett Racing Seats
tillett.co.uk