Forged Innovations
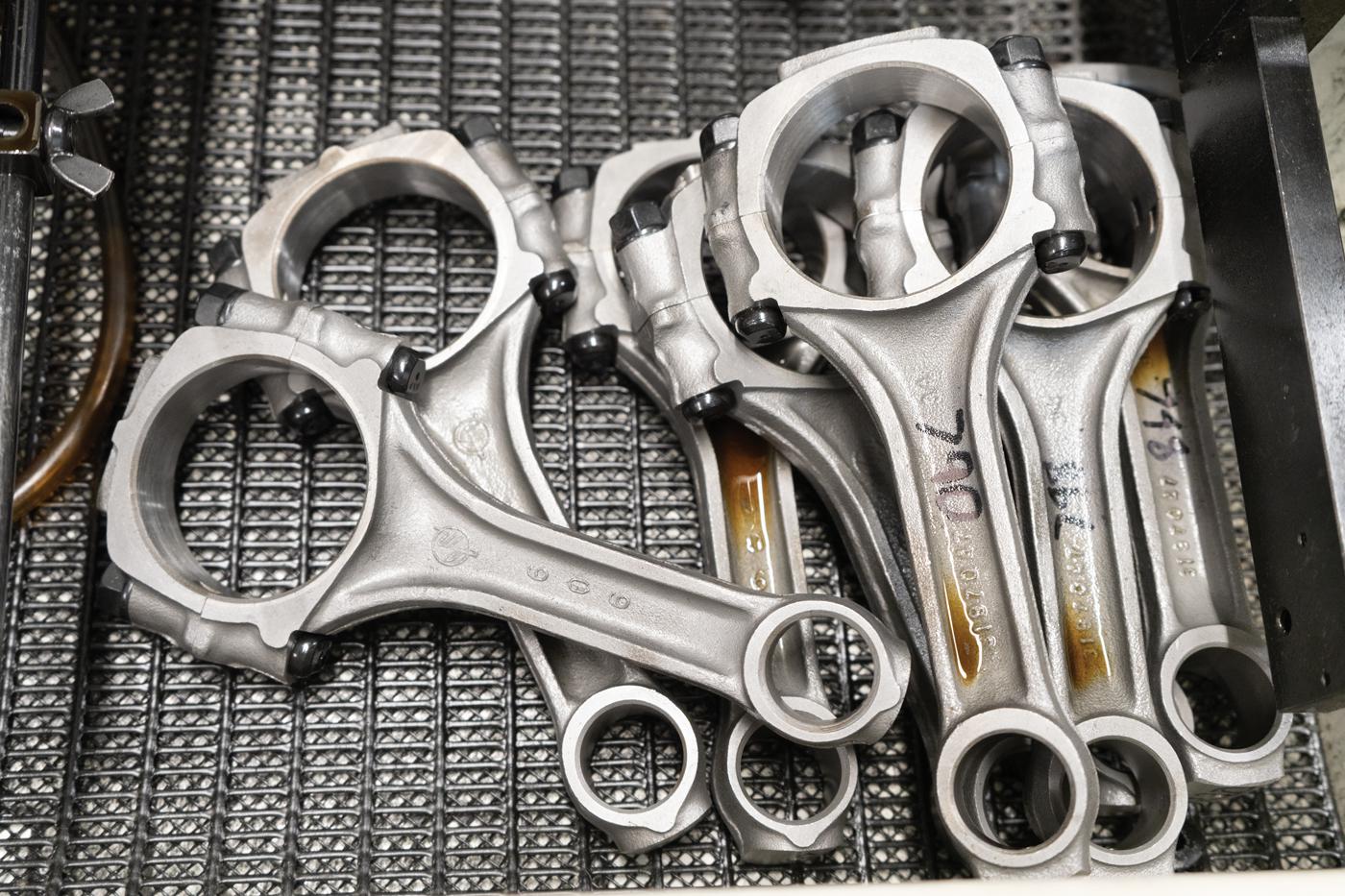
Development often comes at a glacial pace in the connecting rod industry, but there are a few current talking points of interest to racers.
If there’s a segment of the performance-engine market where the excitement level is tantamount to sleep inducement with a double shot of melatonin, it’s the connecting rod industry. There just hasn’t been many news flashes that boast about updated designs, materials, or manufacturing methods in the past decade.
“Essentially, there are only so many ways you can make a rod,” confessed Tom Molnar of Molnar Technologies, Kentwood, Michigan. “Our rods, of course, are a little different than the other guys, but a rod is a rod, for the most part. When it comes to cranks, it’s sort of the same way. There’s only so much real estate that you can put in metal without it affecting everything else, and it’s tough.”
“Yeah, we’re still using the same steel, and racers really aren’t asking for anything different these days,” agreed Richard Batchelor of CP-Carrillo, Irvine, California. “They just want a rod that’s strong and not excessively heavy. That’s the battle, isn’t it?”
A sampling of connecting rod manufacturers revealed a continued assessment of the market to address new applications, but not much else. With regards to new materials, steel suppliers have always dropped into the offices of the manufacturers to pitch a new alloy that is stronger and lighter. There’s only one snag.
“My particular customer base is not ready to pay for that kind of steel,” stated Roger Friedman of Dyers Top Rods, Forrest, Illinois. “Plus, there’s the hassle with adjusting your heat-treating. I mean, you’re probably going to add $500 to $1,000 a set. I’m also getting price increases from UPS, from our electrical company, and all my dry goods like sandpaper rolls. I mean, prices have gone out of sight.”
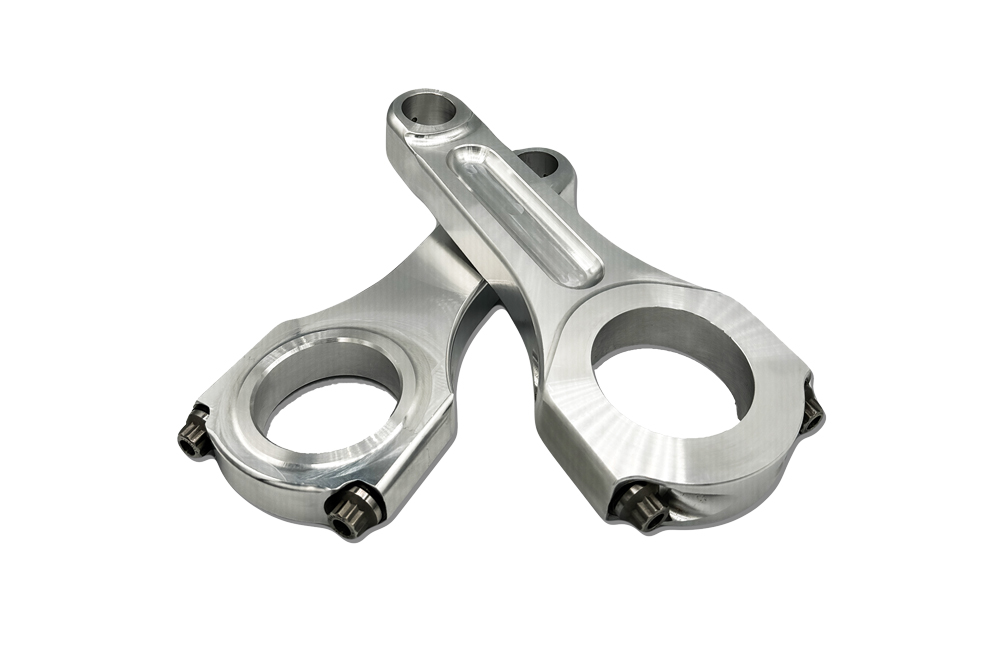
There is one success story in the rod market that illustrates this Catch-22 storyline, and it involves technology trickling down from NASCAR. Callies of Fostoria, Ohio, built a special set of rods for the Spinal Tap 2.0 engine project created by EFI University in Lake Havasu City, Arizona, that is a viral sensation within social media.
“Nick [Norris of Callies] exposed me to the PremoMet materials that had previously been used successfully in NASCAR, so we decided it might be a good fit for this engine, given the extremely high-rpm requirements,” explained Ben Strader of EFI University. “The goal is to have power peak up near 11,000 rpm with nearly 1,000 more rpm for overhead protection.”
“The material is really expensive, and the processes are actually quite difficult,” added Norris. “The challenge is that in its final state, it has to be vacuum hardened, so the parts become very hard at that point. We can’t actually machine the pin-end bore with normal cutters. We have a special machine with small grinding wheels on an oscillating shaft, and even the threads have to be cut with special mills.”
Strader said the material strength is about 10 KSI (kilopounds per square inch) stronger than 300M steel.
“Given the extra headroom, we decided that we could either have more strength in the same rod dimensions, or the same strength in a smaller cross section to save weight,” explained Strader. “In the end, we were able to add some material to critical areas around the rod bolts and under the pin eye, while reducing cross sections in other areas to achieve a lightweight and very strong result.”
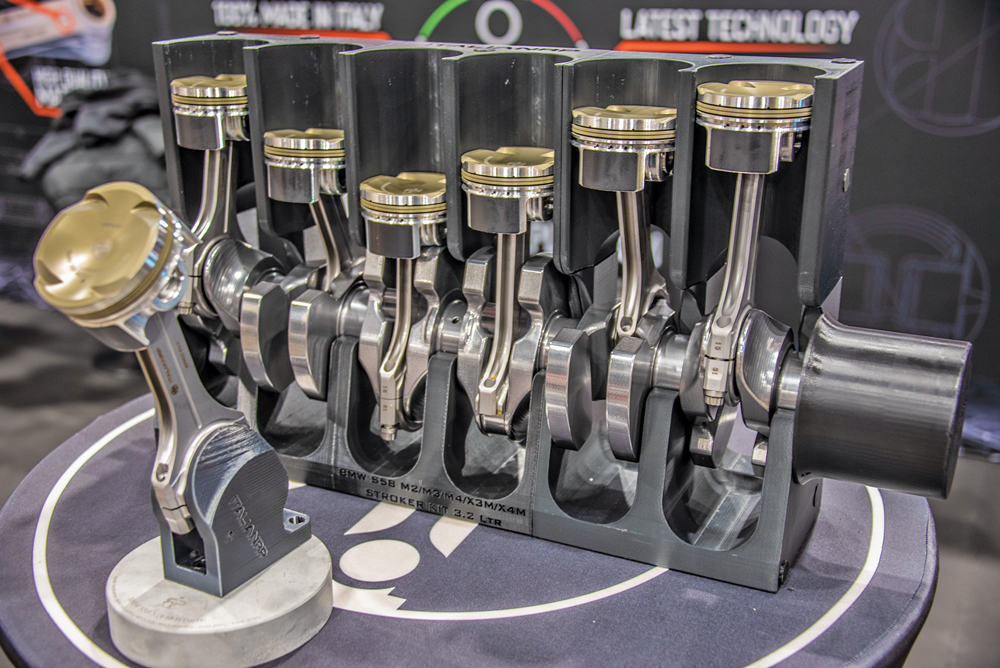
The team called in P1 Manufacturing in Rogersville, Missouri, to develop custom bolts from an exotic alloy called MP35N. The H-beam rod uses a 1.850-inch bearing and a short, 0.708-inch DLC pin that is some 45 grams lighter than a more typical 0.866x2.125 pin.
“We purchase the material from Carpenter Technology and then have Trenton Forging make the forgings,” said Norris. “We can forge only so many parts before the dies have to repaired. It’s a really robust material with good fatigue life.”
The estimated cost is $4,500 for a set of these connecting rods, so there is a limited market. On a more traditional note, Callies continues to develop its Ultra Dirt H-beam as a supporting component to the company’s Ultra Dirt crankshafts. “They are not made out of exotic material, but they are not necessarily lightweight. We know that in sprint cars and dirt late models, you can’t be light anymore. But we try to keep the mass down on the pin end, and then we do some really nice work around the big end to keep it round,” said Norris.
That “nice” work includes reversed radius instead of a chamfer. “Basically, there’s no downside to it, and it’s actually easier to machine,” added Norris.
Aluminum Gaining Momentum
While steel connecting rods make up the majority of performance applications, aluminum rods are drawing more attention with the increasing popularity of boosted applications.
“We’re seeing more demand for aluminum on the sport-compact side, too,” said Batchelor. “We recently released 1,600-horsepower rods for K24 Honda engines. One of the sales guys asked if we could start making them for his customers. We got all the parameters and had engineering design them.”
The rod actually measures 0.010-inch shorter than stock, which allows customers to use standard compression-height pistons. It’s also a solid-beam design that is “maxed out” as far as dimensions will allow. Two lengths are offered: 5.462-inch for the K20 and 5.974-inch for the K24.
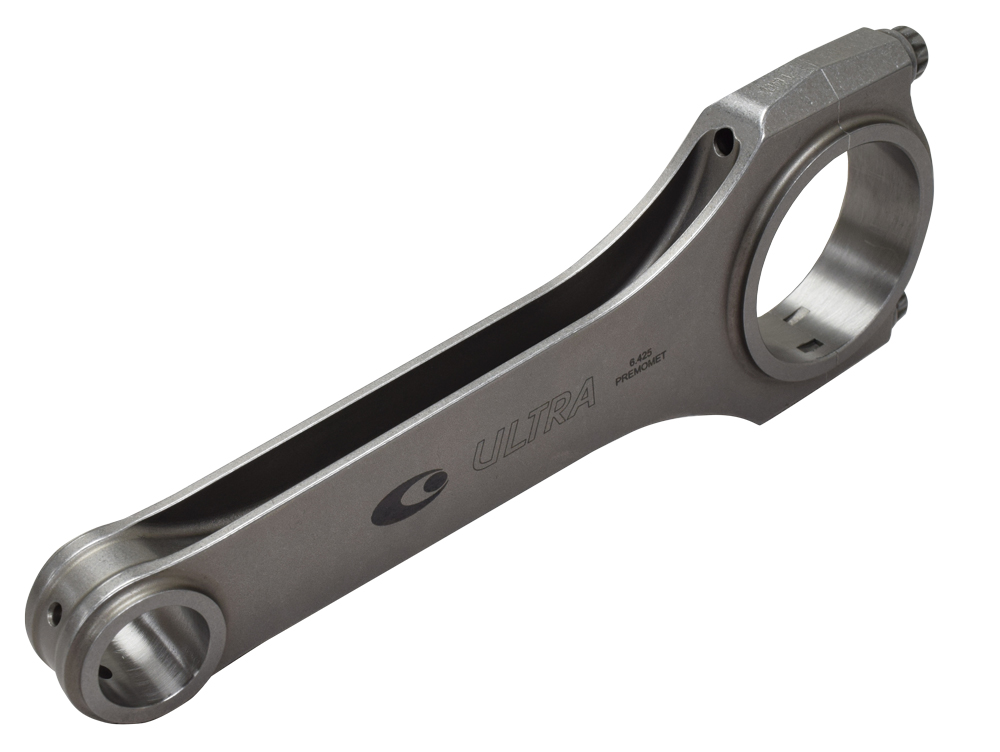
“We had a rod before and just really beefed it up before we started running out of real estate,” said Batchelor. “These are from a forging and not machined from billet. We like the grain flow of a forging. And it comes with 7/16-inch H11 steel fasteners.”
CP-Carrillo also has aluminum rods for Top Fuel and blown alcohol applications, and there are two options for materials—but that’s a topic for more discreet conversations.
“We try not to talk about aluminum materials because of the competition on this side,” Batchelor said.
Over at ItalianRP, a rod manufacturer based in Italy with an office and distribution center in Phoenix, Arizona, longer-than-stock rods are being developed for BMW S58 engine architecture.
“We’re also doing considerable development for motors in the Can-Am side-by-side market,” said Nico Pouyoukas. “It’s such a growing market right now. Guys are making 900 horsepower with these three-cylinder engines.”
The company offers three different lines of connecting rods, and all products are designed and manufactured in Italy. The Silver and Gold lines are machined from 34CrNiM06 steel forgings. The Silver line weighs less than a comparable 4340 design, and the Gold is about 15% lighter in weight than the Silver line. The Gold is also designed to be stronger and harder than the Silver. The Platinum line is machined from 35NCD16 billet material and undergoes two “deep freeze” treatments. The weight of a Platinum rod is 20% less than a comparable Gold model, and the strength and hardness numbers are also significantly higher.
“Obviously the Platinum material is very expensive,” said Pouyoukas. “It’s a memory steel that’s used in Formula 1. We also do a lot of rods for LMP3 cars and WRC teams.”
The company offers a catalog of parts, and custom applications are designed, engineered, and manufactured in Italy, then shipped stateside. The design will depend on the application, with ItalianRP offering I- and H-beam styles along with a hybrid.
“The owner is an engineer, and he does a lot of research and design. We have in-house simulation programs that are very spot-on. Most important is to be lightest but strongest. Our pistons and rods can handle 2,000 horsepower, yet they’re not the same weight as OEM,” said Pouyoukas.
H-Beam vs. I-Beam Continues
Many companies will offer both an I- and H-beam style rod. The debate has many proponents on both sides, and for most customers it is simply a personal preference.
“Our normal game is making H-beam rods,” said Friedman. “But we can make I-beams. We picked up a customer at the PRI Show last year. He wanted I-beams, so we made them I-beams. Their customers are used to seeing I-beams in their engines. I don’t believe the rod is any stronger than an H-beam. It’s just more of a customer preference.”
Durability is a concern for racing customers, and Friedman is always in education mode when working with teams to set fatigue limits. “In dirt late model, there’s a big variation because some customers use Honda journal rods. Those rods weigh less than 600 grams, and they use 3/8-inch bolts. They’ll run them 2,500 to 3,000 laps and take them out,” explained Friedman. “The guys with 7/16-inch rod bolts have rods that weigh in the 620-gram range, and they think they should last forever.”
Advancements in camshaft and valvetrain components have led to engines running close to if not over 9,000 rpm, and that puts enormous strain on the rods.
“They’re racers, and they’re going to run as hard as they can,” continued Friedman. “When you get into calculating loads on bolts and the clamp loads needed to hold these rods together, you’re good up to about 8,500 to 9,000 rpm. When you go over that number, bad things start to happen. Your loads start increasing by huge amounts. Some racers don’t want to hear about it, but facts are facts.”
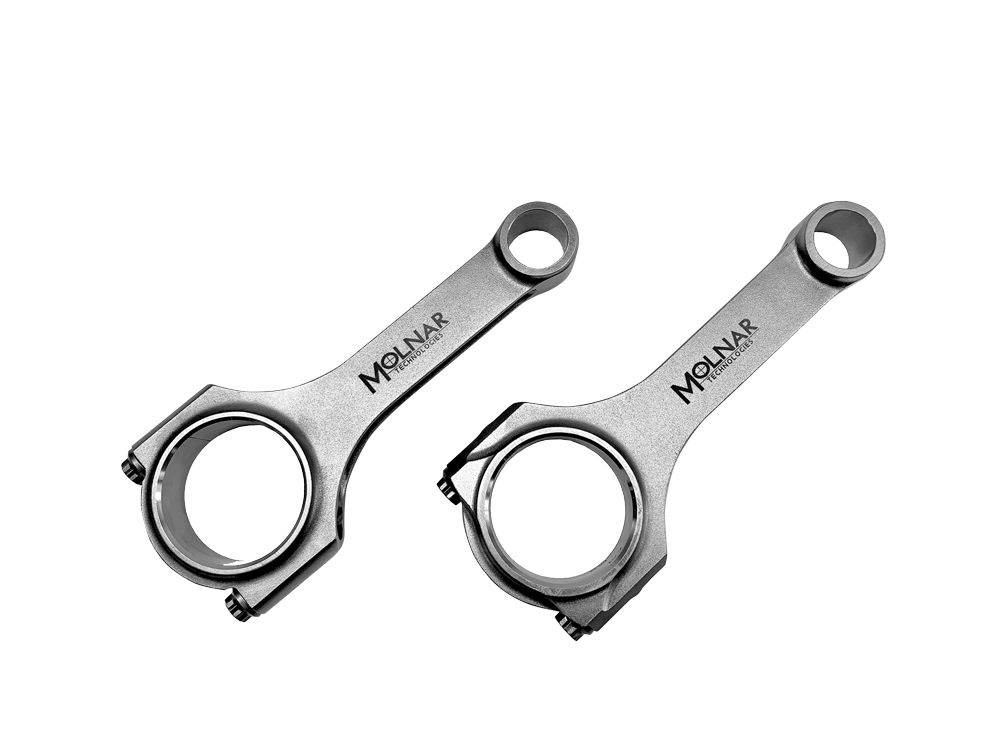
The connecting rod must work in harmony with the crankshaft and the piston assembly. The pressure to keep removing weight from the rotating assembly—including using a smaller wrist pin, which requires changes on the little end of the rod—can lead to conflict in balancing that harmony.
“I like heavier wrist pins because they deform less, and when they deform less you have less load on the pin into the rod,” said Molnar. “Getting pistons and pins too light can be a problem. The really, really light parts, I won’t make. I’m looking at some 3D models of parts and thinking, boy, we can buy a lot of bad advertising with this deal.”
Molnar has experience with customers returning broken rods and noting that the rod pulled the pin right out of the pin bosses on the piston. “If you break a rod, you can’t pull the pin out. There’s no force on it. That was a piston problem,” said Molnar. “But they thought the rods were breaking until someone tore a motor down and discovered there was cracking on the bottom of the pistons. That’s when the light went on for a lot of these racers.”
Molnar doesn’t like to rate rods by horsepower, but he does offer different series that are built to engine configurations. For example, there’s a standard LS rod, LS engines with a power adder, and LS engines with an even bigger power adder. Basically, the differences are more metal in strategic areas of the rod.
For example, a 6.125-inch LS standard rod will weigh 602 grams, while the PWR ADR version will weigh 654 grams. There’s also a slightly lighter version at 642 grams that’s clearanced for high-lift cam lobes. The PWR ADR PLUS will be much stronger at 737 grams. All are designed with Molnar’s experience, which started with the early H-beam rods in the 1960s.
“It has changed, but a lot of the stuff on the market today is a copy of a copy of a copy, and they don’t understand why they’re doing something—they’re just copying it,” he said.
The connecting rod lineup at Howards Cams in Oshkosh, Wisconsin, has been fine-tuned with some models discontinued. The Sport rods are forged 4340 I-beam design with ARP 2000 fasteners. They are stroker clearanced and forged in the USA.
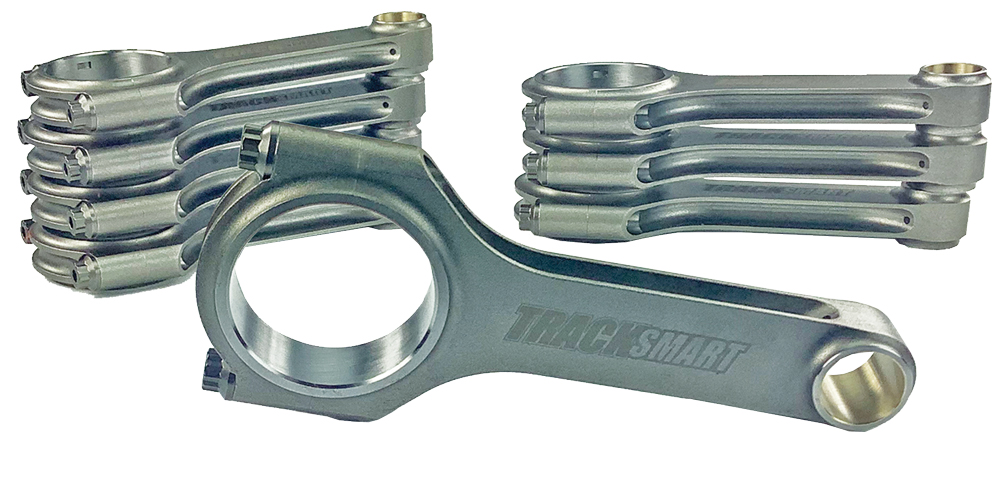
“It’s for the guy who wants to run a stock-appearing I-beam but can run cap screws instead of the old bolt and nut,” said Kirk Peters, noting they’re popular in many dirt-track classes. “We’re a grassroots company, and that’s where our bread-and-butter products are, whether it’s dirt track or bracket racing.”
Then there’s the Ultimate Duty “forged billet” rod made from high-nickel 4340 and put through a multi-phase heat-treat process. The rods are fully stress relieved and shot peened, and the design profile helps reduce weight while accompanying long-stroke applications.
“They’ll take upwards of 750 to 850 horsepower,” said Peters.
Howards also has the Ultimate X rod for Duramax engines. The latest offering is the Track Smart forged H-beam rod. It’s constructed from 4340 high-tensile steel and heat-treated. Other features include stress relieving, shot peening, and double-ribbed caps for extra bearing support. They are available for small block Chevy, LS1, Chevy big block, and Ford small block. All rods come with 7/16-inch ARP 2000 bolts.
“These are computer designed with the professional engine builder in mind,” added Peters.
In conclusion, while connecting rods don’t seem to be generating exciting new designs or shifting to new materials, there is considerable development to keep pace with the increasing boost and horsepower levels in today’s competitive engines. Subtle design changes can make a big difference in improving strength while keeping weight to a minimum.
Some racers, however, need to help themselves when considering a parts strategy for high-stress engines. Oftentimes, the connecting rod isn’t changed after its lifecycle is exceeded.
“Everyone is trying to get as much life out of a set of rods and think they can last forever,” said Friedman. “Does your crankshaft last forever? What does a set of titanium valves cost for an engine today? New lifters? New pistons, rings, and pins? When you start adding these parts up, you’re comparing apples to oranges. Why don’t you change the rods every time? There’s a perception from the engine builder that all this should last, but it doesn’t!”
SOURCES
Callies
callies.com
CP-Carrillo
cp-carrillo.com
Dyer’s Top Rods
dyersrods.com
Howards Cams
howardscams.com
ItalianRP
italianrpusa.com
Molnar Technologies
molnartechnologies.com