CRANKED FOR PERFORMANCE
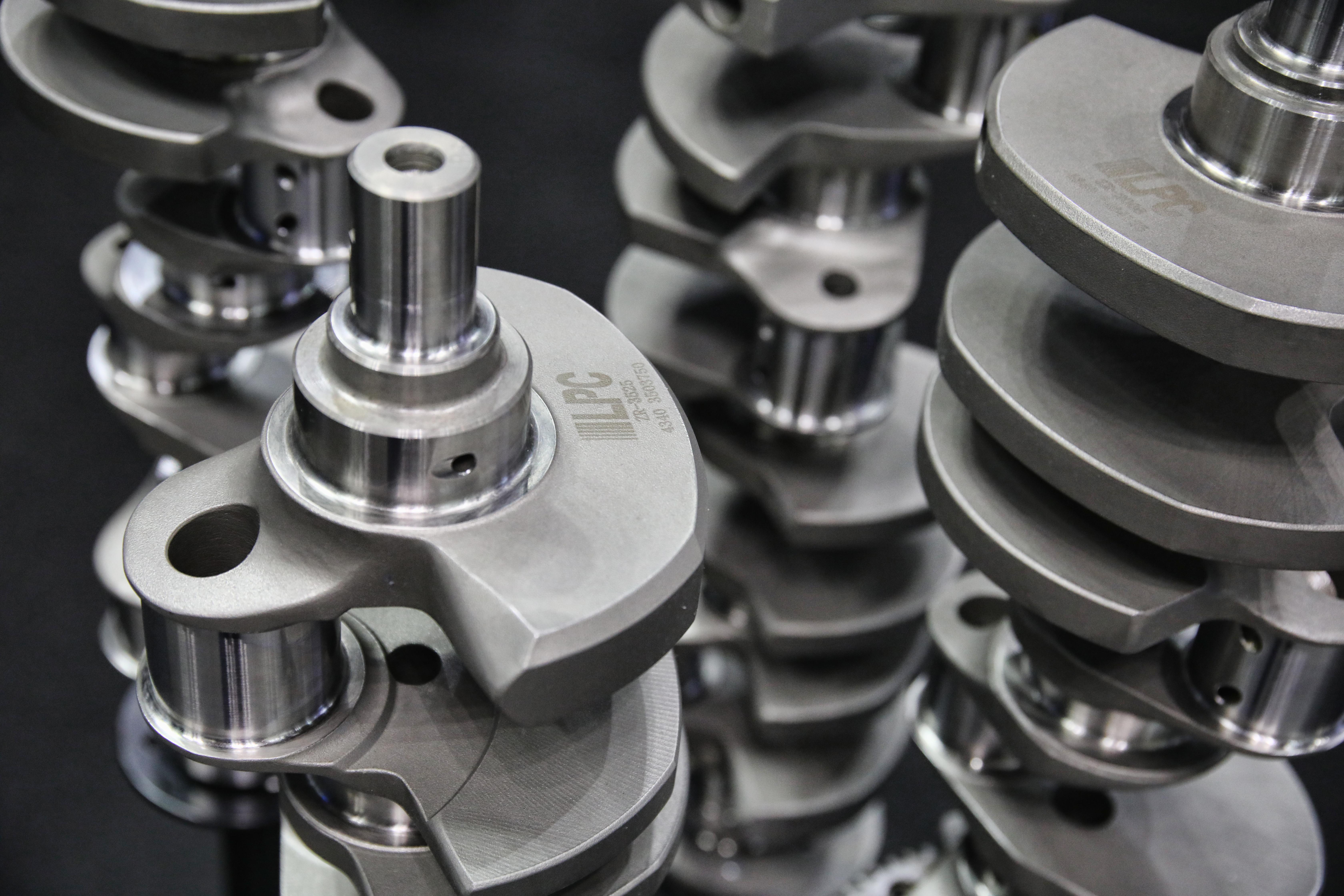
Crankshaft technology is focused on quality control, meeting specific builders’ needs, and keeping race engines humming—no simple task considering today’s almost limitless applications.
As the simplest, yet perhaps the most robust component in a race engine, the crankshaft may still not have reached its technological paragon. Still, with no clear design breakthroughs on the horizon, manufacturers are doubling up on quality control and working directly with builders to provide the appropriate product—since the wrong choice usually leads to disaster.
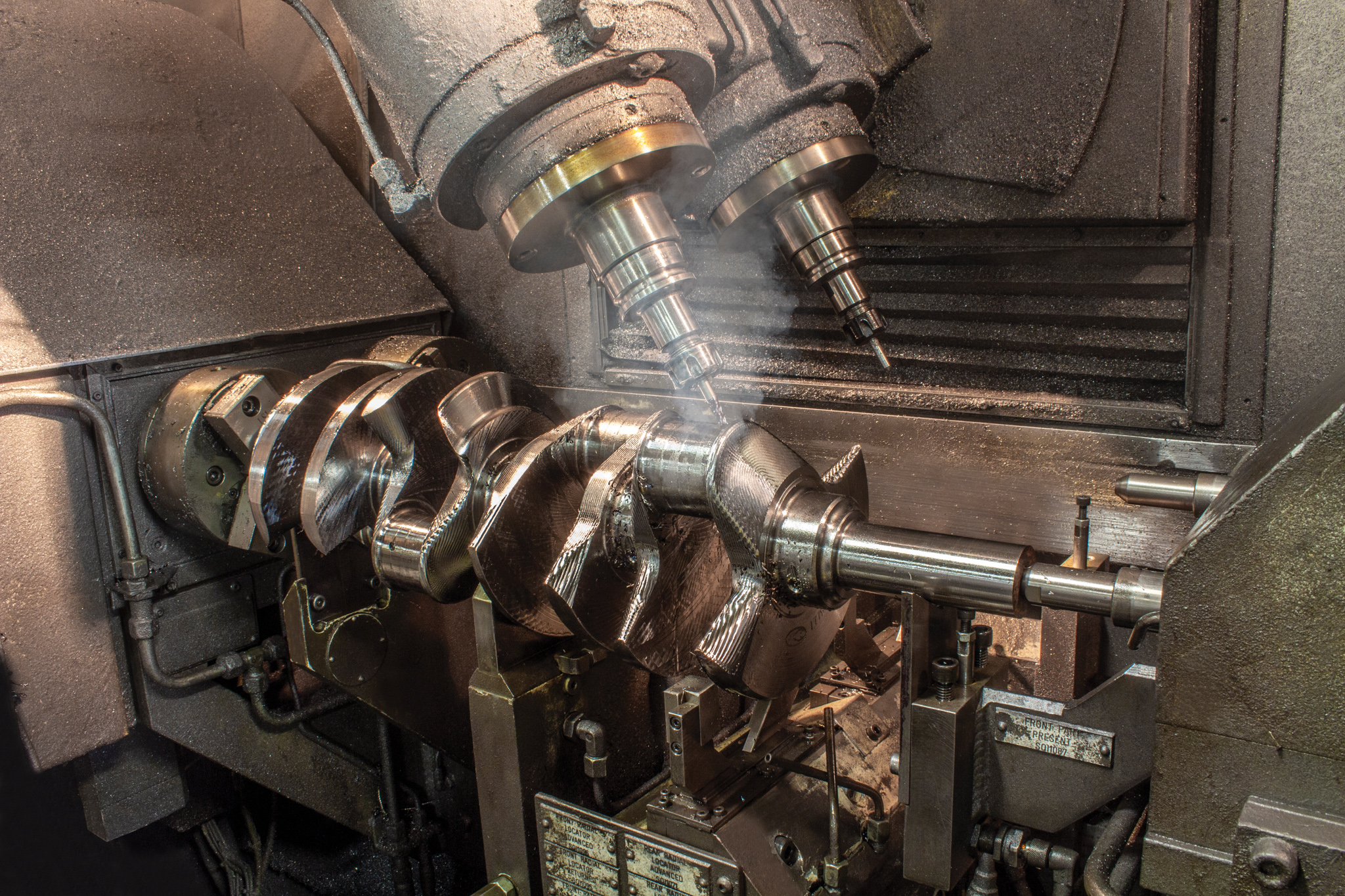
“We haven’t changed much in the past five years,” said Peter Harris of Crower Cams & Equipment Co., San Diego, California. “It’s attention to detail, making sure the grinds are right.”
“Crankshaft and rod technology have sort of peaked, to some degree,” added Tom Molnar of Molnar Technologies, Kentwood, Michigan. “You make a crankshaft…. It’s got to fit in the block and clear everything. The stroke and indexing have to be right. There are some people doing funny things to cranks to make them appear to be better from a marketing standpoint. Is it a better crank? Maybe, maybe not. But nobody is coming out with something revolutionary.”
Driving basic improvements in the crankshaft market are the surge in horsepower levels, increased rpm, and specialization.
“A lot of this stuff has now become niche markets,” explained Tom Lieb of Scat Enterprises, Redondo Beach, California. “You have guys that specialize in Ford FE engines, and those that specialize in LS engines. It’s not a general marketplace, like it used to be 10 or 20 years ago. You go into an engine shop back then, and there would be 10 or 15 different types of engines. Although there are still some shops like that, an awful lot of shops now specialize in certain things. So, that can dictate that we have whatever they need.”
That’s not to say there aren’t blue-sky aspirations to revolutionize crankshafts. It wasn’t that long ago that non-twist forgings became the industry standard. Originally, forged cranks for V8 engines were pressed out in a single plane by multi-ton presses, then the second and fourth main journals were re-heated and twisted 90 degrees to correctly position the second and third crankpins. Modern tooling dies and manufacturing processes now forge crankshafts with the rod pins in the correct position in a single operation to achieve a stronger product.
COUNTERWEIGHTS
Racing crankshafts in the future may be assembled, not unlike some types of crankshafts found in radial engines. Formula 1 teams have experimented with designing crankshafts piece by piece and then welding them together. The benefits could never cover the cost and complexity of such a move, so the idea was reportedly scrapped. Today, however, some high-end race engines will use bolt-on counterweights—often made of heavier metals than the rest of the shaft—to achieve the delicate balances desired for high-rpm operation.
The topic of counterweights, however, is still very much alive today, as more V8 engine builders request fully counterweighted crankshafts, or those crankshafts designed with eight counterweights instead of the conventional six.
“Anytime we can get a forging with center counterweights, we push the customer that way,” said Brook Piper of Callies Performance Products, Fostoria, Ohio. “We’re seeing more and more demand with all the high-rpm engines going on now.”
While machining a fully counterweighted crankshaft from billet stock is rather straightforward, an eight-counterweight forging requires considerably more investment in tooling.
“It takes a really big press to twist a center-counterweighted forging,” noted Piper. “There are limited guys out there with presses big enough. Everyone started with a six-counterweight die. To change dies, you’re looking at hundreds of thousands of dollars. That’s why there might be some hesitation to do it.”
Nevertheless, racing dynamics and market demand are encouraging manufacturers to offer these crankshafts.
“As power numbers continue to rise to levels thought unimaginable 10 years ago, the need for stronger, more stable crankshafts has been a result,” said Alan Davis of Eagle Specialty Products, Southaven, Mississippi. “Center counterweighting is one of many ways a crankshaft can be made stronger and more stable at higher loads and rpm. We are seeing a shift from large-displacement engines to more moderate displacement with forced induction. We have had requests for center-counterweighted, shorter-stroke crankshafts for these applications. They have been engineered and should be hitting the shelves soon.”
“We are certainly seeing more requests for eight-counterweighted crankshafts,” added Mike Sanders of Dart Machinery, Troy, Michigan. “When rpm and power levels rise, the crankshaft starts to flex and destabilize in the middle. Think of it like a jump rope. You have your flywheel and clutch-pack weight on one end and your balancer, pulleys, and timing-component weight on the other end. Under rpm, the crank will start to flex in the middle like a jump rope, so you need to add weight back to the middle to counterweight the effect.”
Most emerging trends in motorsports come with a word of caution, and eight counterweights is no exception.
“Eight counterweights make everybody’s dampers’ lives easier,” noted JC Beattie Jr. of ATI Performance Products, Gwynn Oak, Maryland. “I’ve always been a proponent of fully counterweighted crankshafts. Some people have different concepts of what that means. They think anything in the center means fully counterweighted.”
Meantime, Molnar warned us that some eight-counterweight cranks on the market today “are just simply wrong. They are putting eight counterweights on so they can be marketed as an eight-counterweight crank.
“In fact, there are cases where a good six-counterweight crank is better at reducing the bending of the crank than some of these eight-counterweight cranks I’ve seen.”
Improving crankshaft durability and lifespan are certainly goals when considering a fully counterweighted crank. It’s a topic that can puzzle even savvy industry veterans.

“One of the most interesting things I’ve learned with crankshafts is the different life requirements for some race classes,” said Christoph Wachmann of Pankl Racing Systems, Kapfenberg, Austria. “For example, if you expect a crankshaft in NHRA Top Fuel to last 15 races at four seconds each, this would mean approximately only 10,000 full-load cycles for the total crankshaft life. In most of the other race classes as well as OEM engines, the minimum cycle target is 10 million cycles, which is 1,000 times more than the Top Fuel. The big difference is the load acting on the crankshaft. In a nitro engine with peak cylinder pressure in the 1,000- to 2,000-bar area, it’s extremely high. We would call that ‘low-cycle fatigue,’ and this understanding requires a completely different approach in design and manufacturing processes.”
“We make adjustments based on input we receive from engine builders and race teams using our cranks,” said Sanders. “For instance, we adjusted counterweight placement and added material in critical areas to improve overall strength.”
CRANKSHAFT GRINDS & REPAIRS
Specialty crankshaft grinding is another area of growing interest. There are subtle tricks that can be applied to crankshafts that take advantage of certain class rules.
“In NHRA Super Stock, they allow up to .015-inch longer stroke,” said Dave Olsen of Mile High Crankshafts, Denver, Colorado. “We’ll have guys send us a crank and we will grind the strokes to achieve that. We can modify the counterweights if there’s a clearance issue with the pistons hitting, or do profile cutting on the counterweights.”
“For example, you can’t center gun-drill a Stock crank, but you can a Super Stock crank,” added John Partridge of Bullet Racing Cams, Olive Branch, Mississippi. “You can’t do excessive lightening on a Stock crank, but we can lighten the Super Stock to whatever weight we want it to be. Another thing: In Super Stock we can run any journal size.”
Precision repairs are also in high demand from these specialty shops.
“We are not a rebuilder shop. Our stuff is all done in a specific fashion for race cars,” continued Partridge. “I have one really talented guy that grinds the crankshafts, and he’s done nothing but racing crankshafts. We have a special welding process that when we get through, the journal is harder than it was originally. We can repair one journal and not have to re-heat-treat the whole crank.”
Preventative medicine can help keep a crank out of the repair shop, and Olsen reminds racers to watch their tune-ups, even if it may confront their egos.
“There are times when guys have bearing issues. The one thing that is really kind of difficult to do is suggest that they have got a problem with their tune-up—like it’s detonation that’s creating this problem,” explained Olsen. “It can get the guys to thinking that, ‘Yeah, they did switch fuel.’ The other thing is guys that might run components like harmonic balancers longer than what they should, and that can create crankshaft problems.”
QUALITY CONTROL
While crankshaft design hasn’t changed much in the past few years, manufacturing and choice of materials are improving to keep up with power demands and quality control.
“In racing, we have introduced the use of highest-strength steel alloys with deep nitriding up to one millimeter,” said Wachmann, whose company supplies crankshafts to NASCAR, IndyCar, and IMSA teams along with select vintage racers and high-performance tuners. “And for the OEMs, we have introduced technologies such as the combination of induction hardening with overlaid fillet rolling in the crankshaft radii for higher strength at a lower cost.”
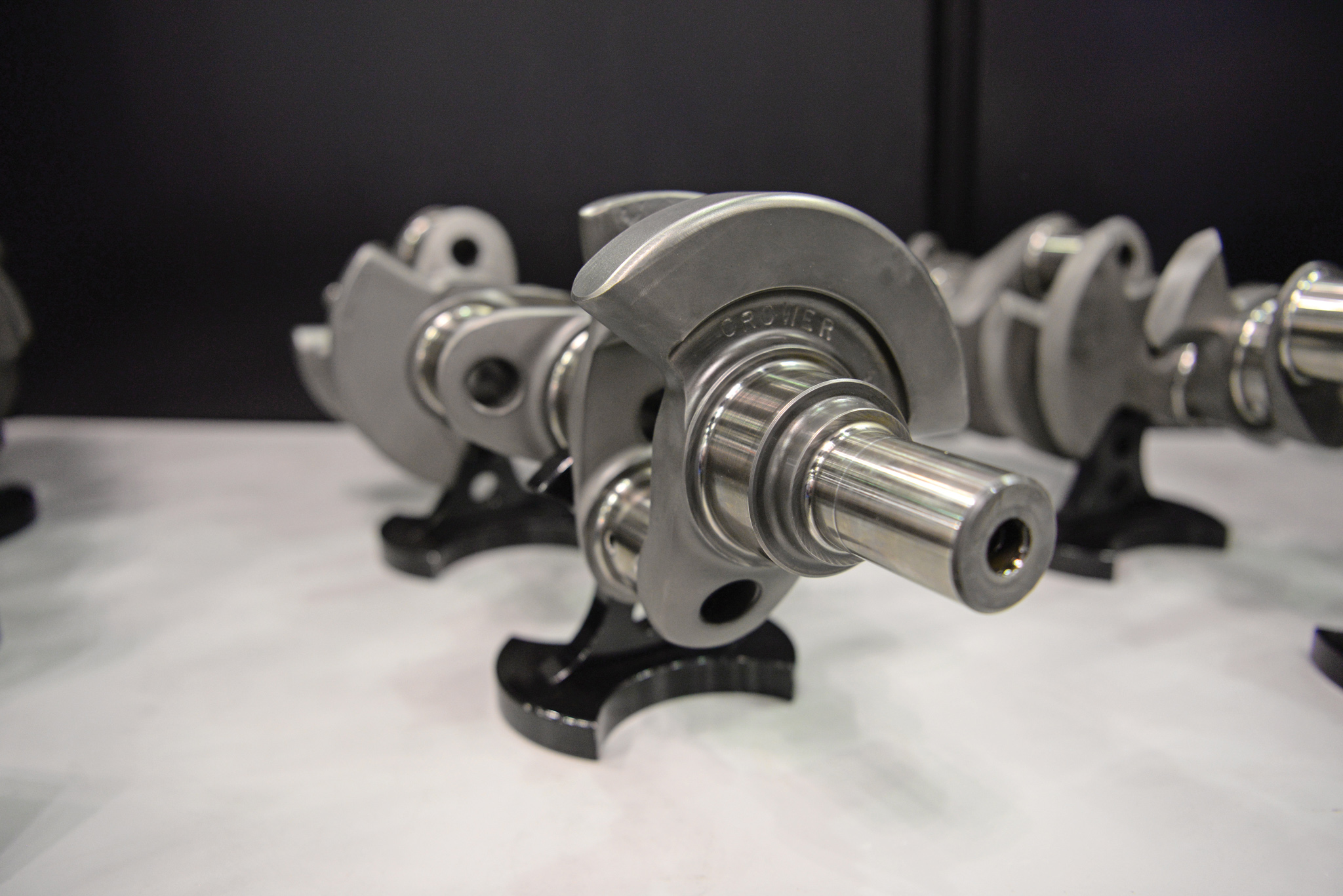
“The 4340 specification leaves a little wiggle room, and we have found that holding tighter specifications for some alloying elements has resulted in a fairly significant increase in strength and other material properties,” said Davis. “Thankfully, we have established a terrific relationship with the foundry we work with, and it has enabled us to make specific requests such as tailoring more exact amounts of alloying elements when we order our steel. Eagle’s steel, while still technically 4340, performs much better than ‘typical’ 4340 steel.”
“CNC technology has come a long way,” claimed Piper. “It’s just like computers; it changes daily. The profiling you can do to the counterweights, the drilling of the oil holes—they can blow through holes and keep a better surface finish on the inside of those oil holes. There are some materials that guys are starting to play around with that are coming to make better crankshafts. The jury is still out on if they’re going to be that much better versus the cost, that’s the big thing. You can spend a lot of money on the material, but at the end of the day is it really worth it that you really gain that much more strength out of it?”
If there’s one big concern industrywide, it’s the reliance on offshore sources for forgings. The majority of forgings come from China. And some companies bring in finished product from China, while others import the raw forgings and handle all the machining, heat-treating, and finish prep in their shops.
For example, Callies has the budget-minded CompStar line of cranks that is fully produced in China but polished, balanced, and finish-inspected domestically. “We actually put our hands on them before they go out the door,” said Piper.
How a company works with China-based suppliers and oversees the machining and finish treatments will dictate the resulting quality.
“We started in China in 1990, 1991, so we have had relationships for all that time with our suppliers. We have only switched factories a handful of times. But basically, the people in China that we deal with, we’ve brought them up through the system,” explained Lieb. “We do not expect a good finished part because we take care of that here. The part of the good finish is the QC on the material, and the QC on the material is the fact that we heat-treat here.”
However, some available products proudly claim, “made in the USA.”
“The best selling point is that our crank is fully American made,” said Harris of Crower. “Forged here and manufactured here. A lot of people really like that. Not a lot has changed in the past five years. It’s just attention to detail and making sure the grinds are right.”
The Callies Magnum and Magnum XL lines start with US forgings. “They’re made 100 percent here in Ohio,” stated Piper.
Forged crankshafts make up the majority of racing cranks; yet, there is still a market for cast crankshafts—which are less expensive to manufacture but don’t embrace the same strength qualities as forging.
“While we don’t recommend using cast cranks in competition applications, it is still common. Most applications we’ve seen are claimer engines in dirt track racing,” said Davis. “You can improve the strength and performance of a cast crankshaft—simple design changes such as larger fillet radiuses, slight counterweight changes, journal polishing, and our ESP Armor process can reduce bearing shear friction and windage to free up some power.”
“The cast-crank market has always been racing, as well as street and hot rodding. We see the market as strong as it’s ever been,” said Lieb. “It isn’t increasing, but it’s not decreasing either. When we look at the numbers, the percentage of cast and forged and billet and so forth, our business model is pretty much the same as last year. It has not changed much.”
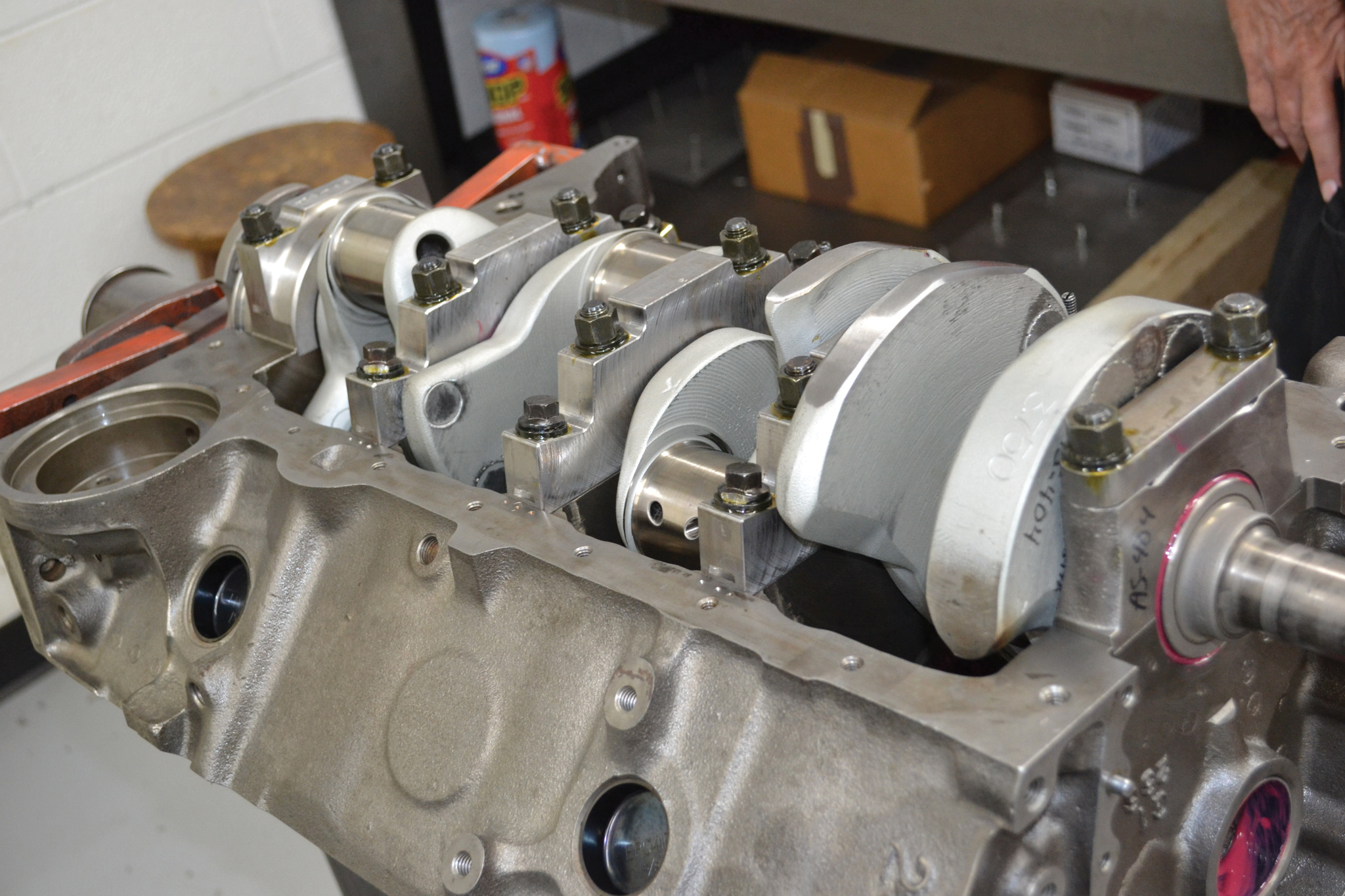
Billet cranks are favored mostly by racers with unique setups, or those who need special features on a crankshaft.
“When we ask an engine builder their application, we would try to steer more toward a forging, unless the application [is] so unique that you have to make it out of billet—such as a 5.3-inch bore spacing,” said Piper. “Nine times out of 10 a forging will do the job because the forging is going to be stronger.”
“The big push for us is the Reaper billet line,” said Eric Bolander of Howards Cams, Oshkosh, Wisconsin. “They’ve been surprisingly good and taken a lot of abuse. We’ve had customers really lean on them.”
Currently the Reaper line is limited to big and small block Chevy, with the next target market being the LS customer.
“They’re made overseas, and that’s the easy part. Getting them shipped here is the problem,” added Bolander. “The new offerings have been evolving.”
“The increasing popularity of high-boost systems and high-rpm builds make it even more important that our crankshafts are built to the most exact standards using the best possible materials, heat-treat, and surface finishes,” said Sanders. “With this in mind, we use 4340 billet machined from solid bar stock and incorporate full counterweighting for added strength and stability.”
Providing a range of crankshafts is helping manufacturers meet the budget needs of some racers. Lunati of Olive Branch, Mississippi, uses 4340 forgings for both the Voodoo and Signature Series, but separates them by price and strength through different heat-treatments.
“The Voodoo is nitrided. The Signature series is pulsed plasma heat-treated, which goes deeper for a stronger crank,” said Will Vance. “Also, the Voodoo has what is known as bull nose cut on the front edge of the throws, while the Signature is finished with our exclusive wing cut to better cut through the oil and reduce windage. The main customer for the Voodoo is the average guy wanting a good crank at a reasonable price up to a racer who needs a solid bottom end. The Signature customer is the top engine builder trying to make as much power as possible.”
NEW MARKET TERRITORY
For the future, many manufacturers are looking into new markets.
“I could see expanding into the diesel tractor market, but it would be a huge investment. These are really large crankshafts, and they’re larger than the machinery we have here,” said Harris, adding that he recently received a phone call asking about cranks on the other end of the size spectrum. “Snowmobile engines. It’s something smaller than maybe I want to deal with.”
Scat is also looking at big tractor crankshafts to expand into the pulling market. However, there are challenges to developing a racing crankshaft for an engine originally designed to putt around a farm field.
“Tractor engines are designed to operate at a certain low speed 10 or 15 hours a day. Now they’re taking them from 1,700 rpm to over 6,500 rpm. And they’re taking tremendous torque from the low end to the upper end,” said Lieb, noting that counterweight design and material choices become increasingly critical. “It’s all about keeping it together.”
Whether it’s for a John Deere tractor or an Outlaw 275 Camaro, racers will need a solid block-and-crank foundation to support their massive power goals.
“The future will always see more racers pushing the limits of what’s possible and playing that balancing game even tighter than they ever have,” said Davis. “The margin for error will shrink, and we must keep pressing for better ways of doing things: better materials, better manufacturing processes, better quality control, all while keeping costs reasonable.”
SOURCES
–
ATI Performance Products
atiracing.com
Bullet Racing Cams
bulletcams.com
Callies Performance Products
callies.com
Crower Cams & Equipment Co.
crower.com
Dart Machinery
dartheads.com
Eagle Specialty Products
eaglerod.com
Fluidampr
fluidampr.com
Howards Cams
howardscams.com
Lunati
lunatipower.com
Manley Performance Products
manleyperformance.com
Mile High Crankshafts
milehighcranks.com
Molnar Technologies
molnartechnologies.com
Pankl Racing Systems
pankl.com
Scat Enterprises
scatcrankshafts.com
TCI Automotive
tciauto.com
Dampers: Harm Reduction
“A damper can’t fix a major underlying problem,” stressed JC Beattie Jr. of ATI Performance Products, Gwynn Oak, Maryland. “It can be a Band-aid, but eventually every Band-aid will fall off.”
Dampers—sometimes referred to as harmonic balancers—are designed to reduce harmful harmonics generated by crankshaft bending and twisting during operation. Currently, there are four types of dampers common in the automotive racing industry: elastomer, viscous, pendulum and friction. All have their pros and cons, and today’s damper manufacturers are not only improving and expanding their lines, they’re locked in an informational campaign to explain the technologies behind their products.
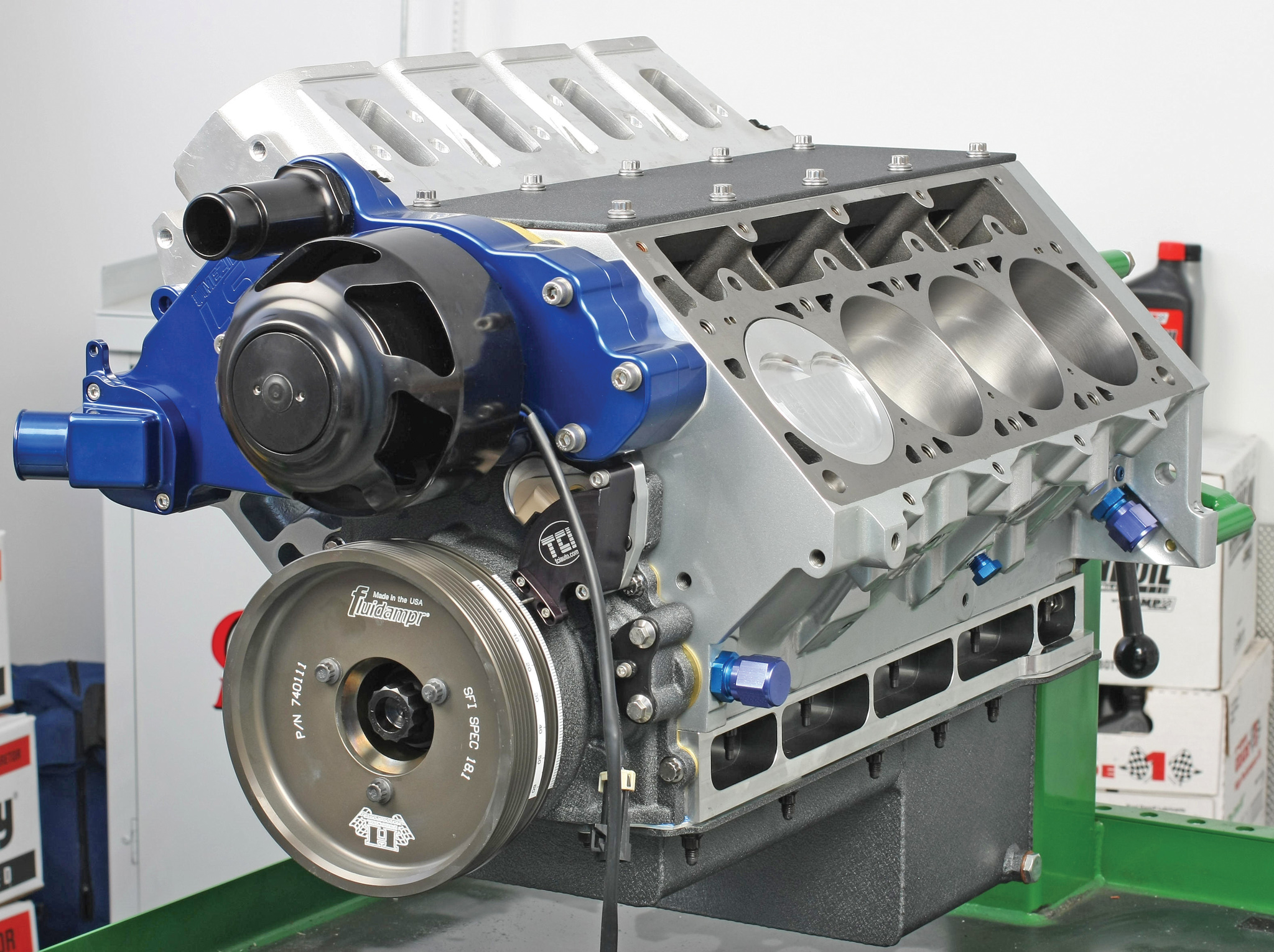
“It’s really education about torsional vibration control and how we can improve the efficiency in the durability of the engine,” said Brian LeBarron of Fluidampr, Springville, New York. “Once we educate the science behind it, some of the dampers are pretty straightforward.”
Fluidampr promotes a viscous-style damper, and its suitability for high-rpm is often a misconception associated with that product. “That’s just not true anymore. We’re up over 11,000 rpm with Cosworth. So the ability to make a viscous damper that works on high-rpm, high-performance engines is certainly there—and we’re supplying at the OE level,” said LeBarron, adding that viscous dampers are noted for durability, especially in high-temperature situations.
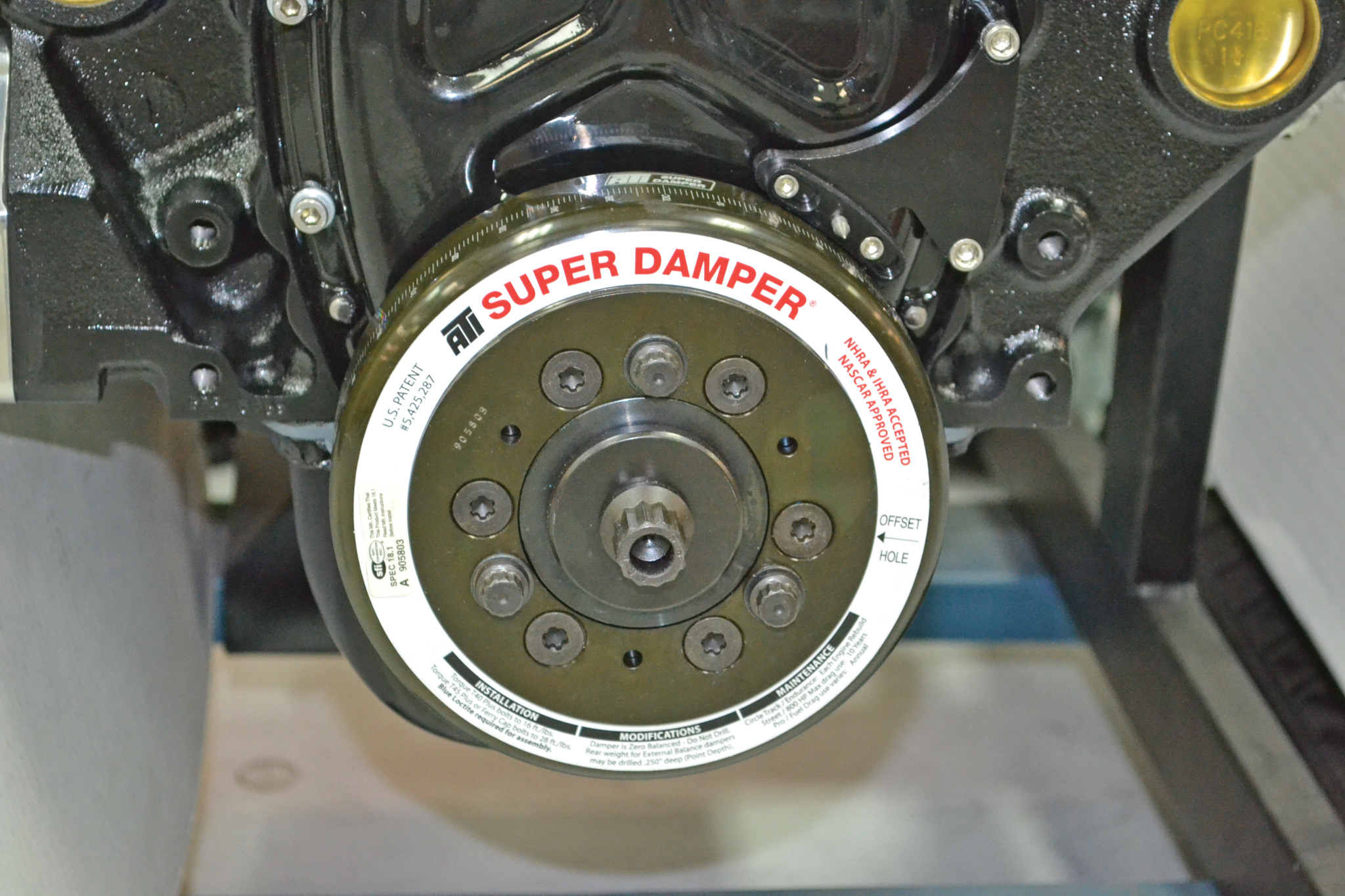
TCI Automotive in Ashland, Mississippi, builds a pendulum-style damper that may be a little heavier than other styles, but also has unique selling points.
“It is a true vibration absorber,” said Scott Miller. “Others on the market are dampers, which only reduce the vibrations. The Rattler absorbs the vibration within itself, thereby extending the life of engine parts.”
Very little has changed about the TCI damper since its introduction, and its top selling point is long-term cost savings. “The initial testing took several years because we wanted to make sure that every aspect of engine vibration was looked at. We wanted to make sure that it was 100% perfect before releasing it for sale,” added Miller. “Even though it might cost a little more, you will save money because you can see longer intervals between engine freshen-ups.”
ATI is another company that hasn’t changed its elastomer-style damper in recent years, but rather has promoted the product’s modular benefits.
“It’s hard to change something that already works well and does exactly what we say it will,” said Beattie, noting that there are 450 different part numbers for the components that can be used to build an ATI damper. “We can engineer it to fit all the different engine packages, such as diesel, race, show, and so on. We can change it on the fly and still get the best performing damper while working with that particular engine package.”
Educating the consumer is also a priority for ATI, as its damper has a reputation for working only in high-rpm applications.
Beattie said, “When we first came out, we were fixing OEM dampers that failed at high rpm. A lot of people thought it was just for that, but it works through the full rpm range.” —Mike Magda