MANIFOLD CHOICES
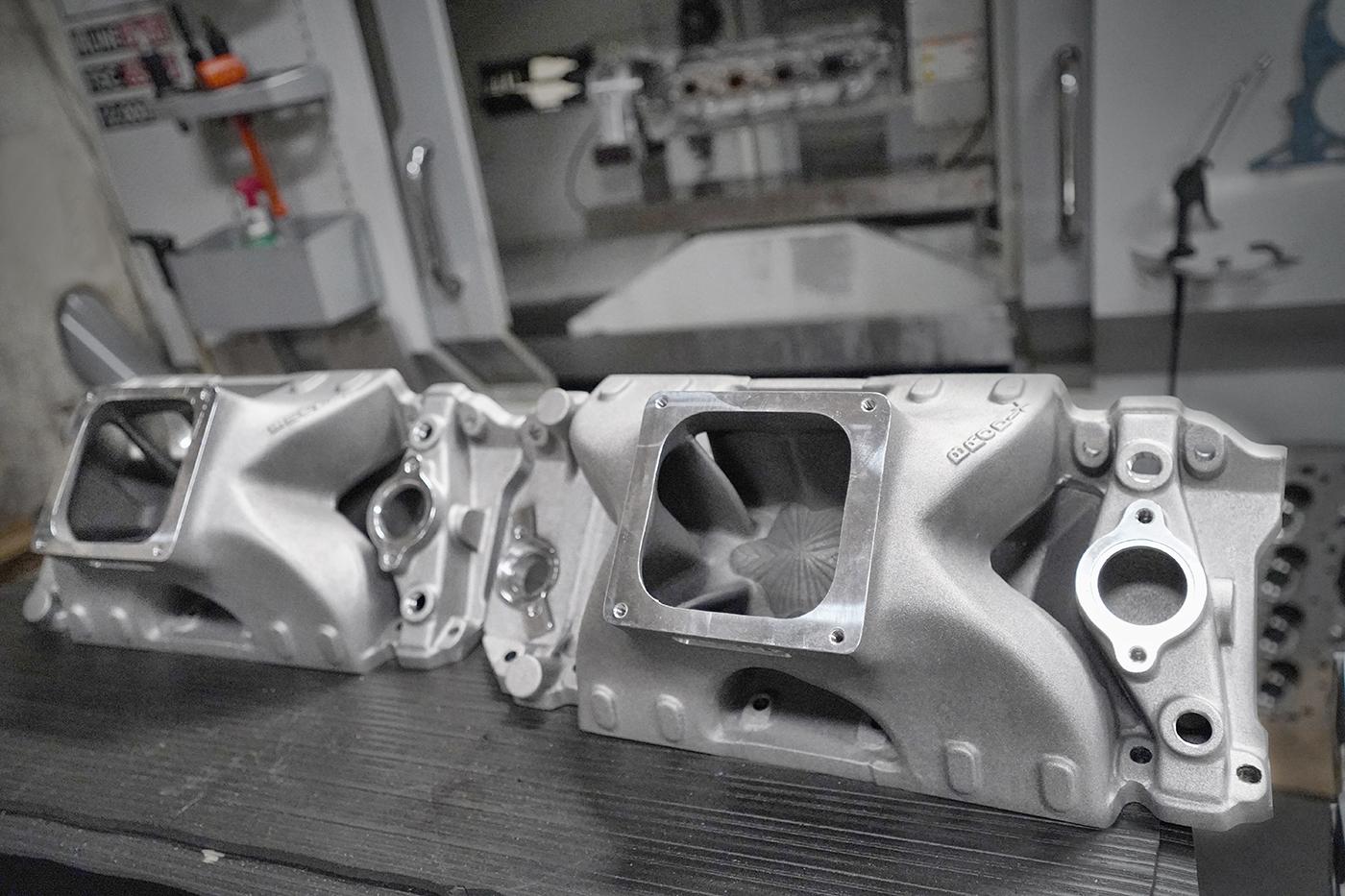
Every racer will eventually face the decision: off-the-shelf or custom? Fortunately, our expert sources are here to help retailers and engine builders point customers in the right direction.
Assembling a racing engine is always a series of choices and compromises. Some parts, either because of the rulebook, deadlines, or budget constraints, are bound to be readily available off-the-shelf items. For other parts, only custom pieces will do.
To examine those trade-offs, consider the intake manifold. Every engine needs one, and the variety in the market is staggering. The manifold is one of those engine parts that perfectly illustrates the factors that must be considered when deciding between off-the-shelf or custom. Both types of intakes have their plusses and minuses, and helping retailers and engine builders guide racers to the right choice is no small challenge.
There are several steps along the way to piecing together the optimum induction package. Asking the right questions is the start. “The biggest or first question that I normally try to get our guys to ask is drivability—what style of driving they’re going to have,” said Mark Fretz of Brodix, Mena, Arkansas. “If it’s going to be a stoplight-to-stoplight, pump gas, power brakes-type engine, or is it going to be something that they’re going to rip on a little more? Or is it an all-out drag race car, or circle track car, or road race car? Try to get the style of driving that they’ll be judging the performance from. And at that point, then get them the style of manifold, or fine-tune it down to which exact manifold will work best for them.
“The main thing is, you can build two identical engines, and two guys are going to evaluate them completely different if they have two different driving styles,” Fretz continued. “If one guy gets in and wants to drive it to the grocery store or drive it to the drive-in diner to go get a milkshake, he’s not looking for power at 7,000 rpm. He’s wanting power from off-idle to 4,500 rpm. Where, put his grandkid in it and he wants to go show off to his buddies, all he wants to do is see how far he can spin the tires. And they’re going to evaluate it differently.”
At Frankenstein Engine Dynamics in Weatherford, Texas, Jesse Meagher noted that ultimate performance is not always the deciding factor. “Every engine combination is unique in one way or another, so a custom manifold will almost always outperform an off-the-shelf version,” he said. “When we design a new manifold, we factor in induction type, cubic inches, rpm range, fuel delivery, and a few other things. The only real difference between one of our higher volume production manifolds and a custom piece is how wide the range of those factors is we accommodate to. In practice, however, that advantage can be negligible, and often budgetary concerns outweigh small performance gains.”
M&M Competition Engines in Franklin, Indiana, mostly offers custom manifolds, and knows well the considerations racers take into account. “Correct intake manifold choice results from a combination of several key factors,” said Scott Patton. “The questions a retail sales staff and engine builders alike need to ask include, but are not limited to, what type of racing will the end user be participating in? What cylinder head is being utilized? What size is the engine? What are the horsepower goals of the combination? What is the budget of the end user? What type of fuel delivery system will be required (EFI, single carb, dual carb, mechanical fuel injection, etc.)? Are there any rules that govern the use of a cast intake versus a sheet-metal intake?
“For example, a bracket racer that is wanting to make 200–300 passes per year would be fine with an off-the-shelf intake manifold in most instances because budget and simplicity are the driving principles behind intake choice, not all-out horsepower,” Patton said.
OFF-THE-SHELF (MOSTLY)
Buying a manifold that’s a regular catalog item has several advantages that will strike most people as obvious. For one, it arrives quicker than waiting for custom work. For another, it’s usually less expensive.
But there are plenty of reasons racers choose an off-the-shelf intake manifold that aren’t always as apparent. “One thing that’s going on in the manifold world, at least for our product, where our product really shines, is hood height—cutting the hood, cutting the cowl,” said Brian Tooley of Brian Tooley Racing, Bardstown, Kentucky. “There’s a lot of people who don’t want to cut up their cars to install an intake manifold. And a lot of the intake manifold choices out there would require cutting a hole in the hood, or getting a custom hood, or at minimum, cutting the cowl with a custom hood. A lot of guys don’t want to do that to their car.
“You have so many customers running boost now, whether it’s a centrifugal supercharger, turbo, twin turbo—boost just gets cheaper and cheaper, and easier and easier,” Tooley said. “So a lot of those guys want something that is going to make power up over 7,000 rpm, and they don’t want to cut their car up.”
The sanctioning body rulebook often plays a role in limiting custom pieces. “Some classes say, ‘No billet or sheet-metal intakes,’ simply from a cost perspective,” Tooley said. “So it must be a cast-aluminum intake. From that perspective, our cast-aluminum intakes fit the bill there.”
Intake manifolds, of course, have to work in concert with carburetors or fuel-injection systems, as well as cylinder heads. It’s not unusual for high-volume off-the-shelf intakes to have been designed to work in concert with popular, readily available parts both upstream and downstream of the manifold. Collaboration between companies is common in the industry.
“We do a lot with APD (Advanced Product Design) up in Ohio,” explained Fretz with Brodix. “As they develop carburetors, they work with us on intake development as well.”
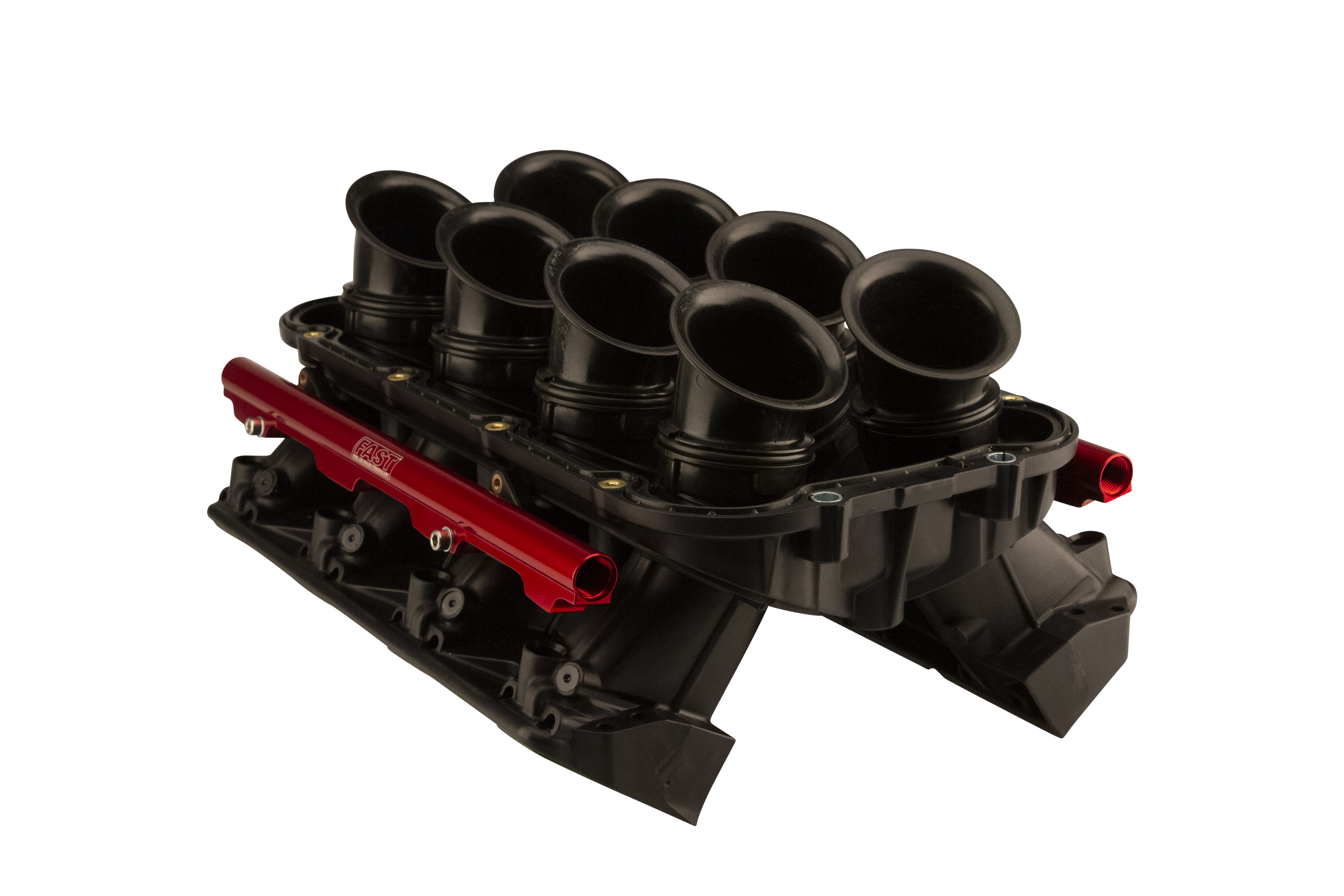
Brodix manufactures its own cylinder heads, and updates and optimizes its intake manifolds to maximize package options. “When we do an intake manifold, the design we’re looking for is to get optimal power for a specific style of engine, or specific size of engine range,” Fretz said.
“And then once the cylinder heads become better and better over the years, then the demand outgrows what intake manifolds we have. And then we look, and we try to redesign and get ahead of the game again with the manifold. We start with an existing manifold that we have and then evaluate, and then engineer what we think it needs to do.”
COMP Performance Group in Memphis, Tennessee, is a manufacturer with many brands in its portfolio, such as COMP Cams, Racing Head Service (RHS), and Fuel Air Spark Technology (FAST). Intake manifolds from FAST have been engineered to work with other COMP Performance Group parts, making it easy to put together a well-matched package. “Those products have all been tested together,” said Matt Patrick.
“Any new manifold is always designed as a kit, working in conjunction with the throttle bodies, fuel rails, airhorns, mechanical or electronic actuation,” added Mike Jenvey of Jenvey Dynamics in Bridgnorth, Shropshire, United Kingdom. “Jenvey throttle bodies are modular in design, allowing engine builders to fine-tune intake systems to best match their engine specification.”
To say that a product is “off-the-shelf” doesn’t mean it’s a pedestrian item, or a second-best choice. Modern tools and design processes mean that many off-the-shelf manifolds are not far off from what was a leading-edge custom just a few years ago, capable of hitting a performance bullseye in many racing applications.
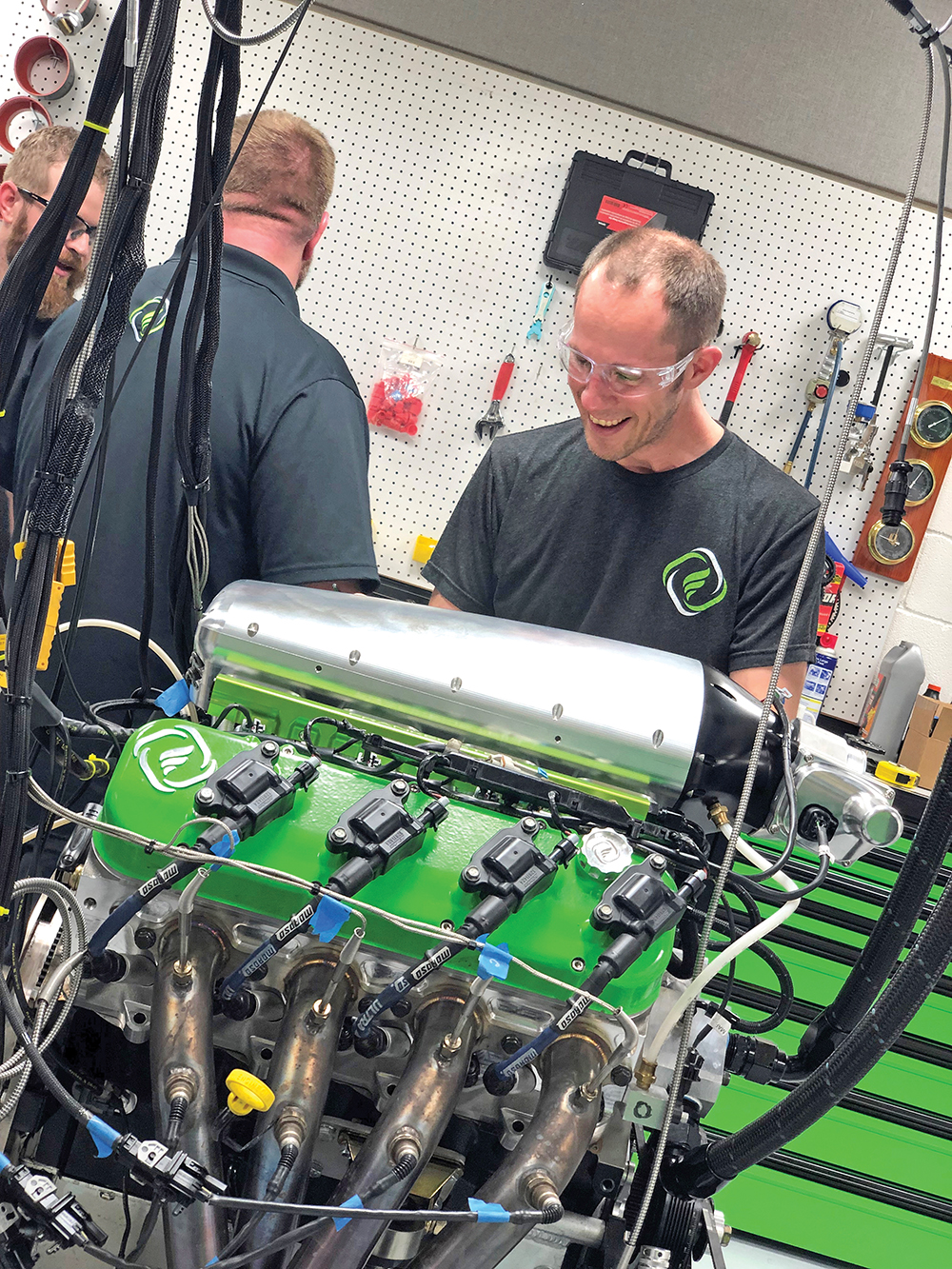
At Brian Tooley Racing, the latest generation of manifolds are the Equalizer 1, for the GM LS1 series, and the Equalizer 3, for the LS3 family.
“We call them our Equalizer series because of how the air is introduced low, below the runners, and flows up into the plenum,” Tooley said. “When you look at most of the race intakes out there, you have the runners running up into the plenum, the throttle body is affixed right to the front of the plenum, and the air from the throttle body runs right across the opening of those runners. And what most people assume is the front runners are going to get the most air, and the rear runners are going to get the least. What actually happens is just the opposite. As the air rushes past those front runners, it actually kind of shears some of the airflow off the front runners. The airflow then basically stacks up in the rear of the plenum, and feeds more air to the rear cylinders. We have eight wide-band O2 sensors on our engine dyno, so we’re able to look at that air/fuel ratio per cylinder,” citing the air/fuel ratio per cylinder at 7,500.
At the COMP Performance Group, FAST’s new LSXHR manifold straddles the line between off-the-shelf and custom capabilities. “[This] intake manifold took us a full three years to develop,” Patrick said. “A tremendous amount of R&D went into it. It is the industry’s first polymer, tunnel-ram style manifold that has some key features. One, it’s really rated for boost. This product works great for naturally aspirated applications, but the boosted market was first and foremost in our minds. It’s very strong, very heavy-duty, very thick polymer. It’s rated for 45 pounds of boost continuous. It’s a very strong structure. From the beginning, from the clean-sheet design, it was designed for boost. There’s a lot of reinforcement, and a lot of material thickness to make it very strong.
“It’s got replaceable stacks that come in different lengths,” Patrick continued. “So you can have a short-runner for very high rpm, a mid-length runner for something intermediate, and then we have the longest runner, which really is optimized up to about, I would say, 7,200 to 7,500 rpm.”
Citing additional “neat features,” Patrick told us the fuel injectors were “very strategically aimed…and it’s really a compound angle. Much like the OE intake, ideally you want your pencil-stream injectors to aim right at the back side of the intake valve. It’s a very hot surface, and it’s a really nice way to get really solid fuel atomization.”
That ability to “custom outfit” an off-the-shelf manifold has become increasingly easy to find. “Jenvey specializes in cast-aluminum manifolds. All design work is completed in Solidworks with CNC machines dedicated to creating patterns (moulds) for the on-site foundry. All subsequent machining is carried out in our CNC shop,” Jenvey said. The company’s newest MF20 Ford Coyote downdraft manifold was designed for use in rear-engined Sports Prototypes, as well as cars such as front-engine Cobra replicas, requiring maximum flexibility.
“A number of customers approached us about supplying a downdraft manifold for the Ford Coyote engine,” he continued. “This is our own product, but careful consideration was given to performance and allowing fine-tuning of the system length as well as offering multiple injector positions, one of which can allow the use of the original loom. Using our modular components, it is possible for engine builders to specify the system to their own requirements.”
Frankenstein Engine Dynamics makes readily available intake manifolds that pack the visual punch of a custom, along with multiple options to tailor them for specific applications. “With the Freakshow, we wanted to build a manifold better suited to either larger cubic inch engines or high-boost forced-induction applications. Freed from the tight constraints of our LowPro manifold, we increased the plenum volume and runner length significantly to work better with these larger, more powerful engines,” Meagher said.
“As for the Iceman, it was all about packaging with a bit of cool factor thrown in for good measure. We weren’t the first to come up with the idea, but instead of adding the intercooler as an afterthought to an existing manifold, we decided to design one from scratch without compromise, and using the largest air-to-water core we could,” Meagher added.
CUSTOM TAILORED
Any number of factors could trigger the need for a custom intake manifold—moving the ports in a cylinder head, dialing in power in a particular rpm range, or simply seeking a competitive edge, to name a few.
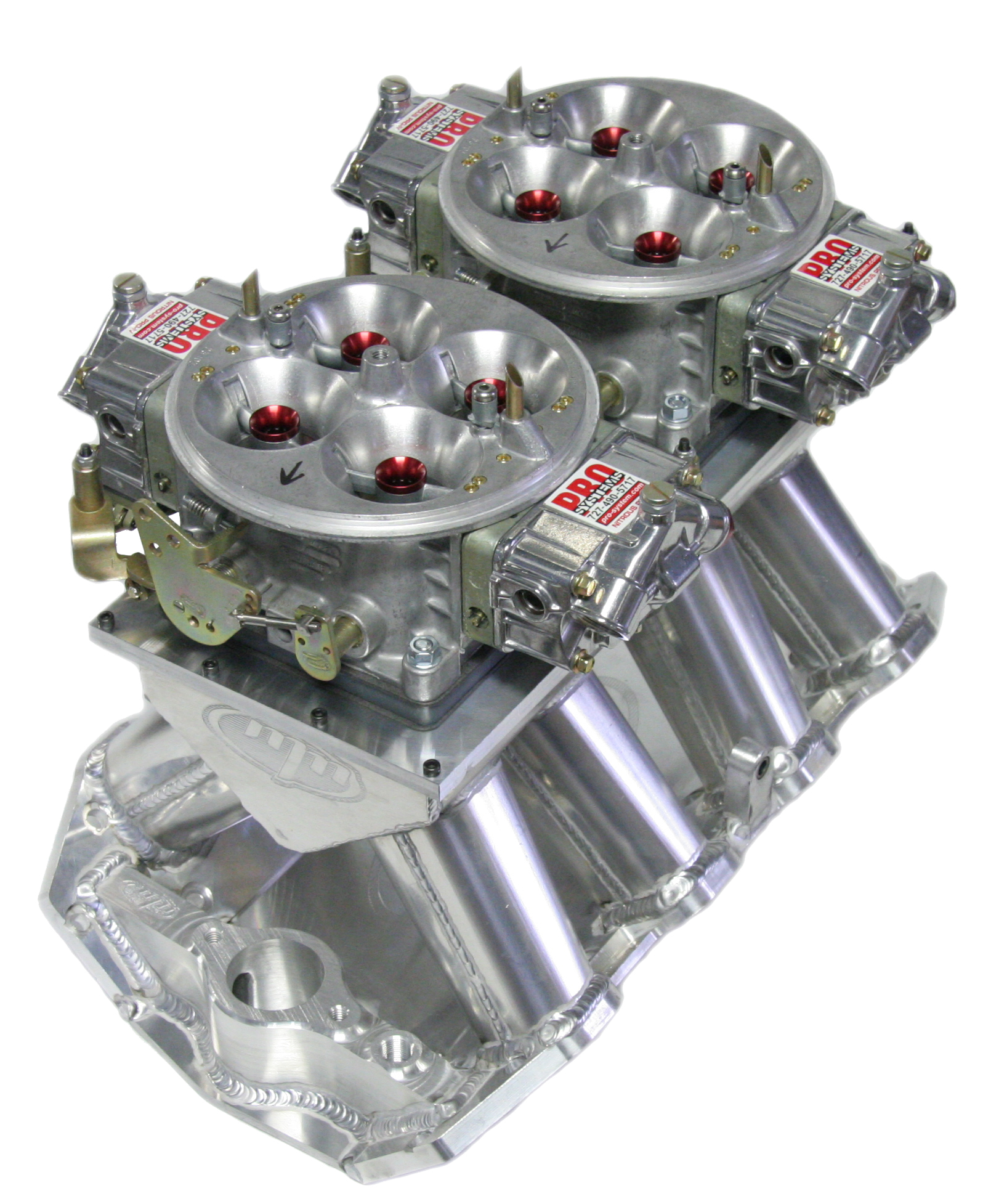
A racer may have to search a bit to find the ideal source for a custom manifold, but the options are plentiful. “We specialize in prototype and low-volume production, one to 500 parts a year,” said Mike Miller at Cunningham Precision Group, Columbus, Indiana. “We do this with tooling that is a reasonable price range for the normal racer or smaller speed shop to afford. Most foundries are not interested in these low quantities, and their tooling is very expensive. It is hard for a customer to find a casting house that’s interested in making low volume; however, a lot of customers have unique designs and applications that do not lend themselves to high production. This is our niche.”
Cylinder head evolution drives a good part of Cunningham’s manifold business, Miller said. “In today’s industry, intake manifold designs are not keeping pace with the cylinder heads they complement,” he explained. “Cylinder heads are becoming much more advanced and are capable of producing more horsepower than ever before, and they are doing so at a rapid pace. Unfortunately, the intake manifolds that are available for said heads are not allowing the racers to take full advantage of the advancements made in the high-end cylinder heads they purchase.”
This is a trend the team at M&M Competition Engines has also encountered. “Most of what we offer the market from an intake manifold perspective is custom, whether it be our sheet-metal or cast-intake programs,” said Patton.
“Our sheet-metal intakes are purpose built for the customer’s specific needs,” he continued. “All components are made in-house, and are designed and machined once all of the engine specifications and customer desires are finalized. We have the unique ability to go as far as making our own dies for our die-formed runner sheet-metal intakes.
Patton further noted that “even the cast intakes we sell are what we would consider custom. They are not custom from the same standpoint that our sheet-metal program is, but all of our cast intakes are derived from a void in the marketplace. With the sudden spike in cylinder head development in the past several years, the availability of improved cast intake manifolds has not progressed along with them.”
At M&M, the process involved in a new intake manifold casting project “typically begins with us heavily modifying an existing cast intake manifold (so much so at times that it does not even resemble what it began life as),” Patton told us. “There could be many factors that lead to us producing a new casting, but they all stem from there not being anything in the market that fills that specific need. For example, it could be something as simple as current intakes not being able to fit various deck heights, to something as complex as designing an intake with the correct runner taper, runner length, port entrance angles, plenum volume, line-of-site variables, etc. What it simply comes down to is that if we cannot drastically improve upon an existing platform or application, then we just do not go to the financial or time-consuming expense to produce a new casting. Why make something that someone else already makes? We do not just make intakes to make them. If there is not a true superior design advantage to be had in making a new product above and beyond what is already offered in the marketplace, we do not manufacture it,” Patton said.
Creating a custom or hybrid intake manifold based on off-the-shelf raw material is also common in the industry. “A popular class we have done a lot of work for lately is Ultra Street,” said Frankenstein’s Meagher. “This class requires a mass-produced cast manifold, but significant modifications are allowed. We often begin with a cast carburetor-style manifold, then whack the top off and build a billet elbow to allow for better airflow and distribution, along with larger throttle bodies and charge pipes.”
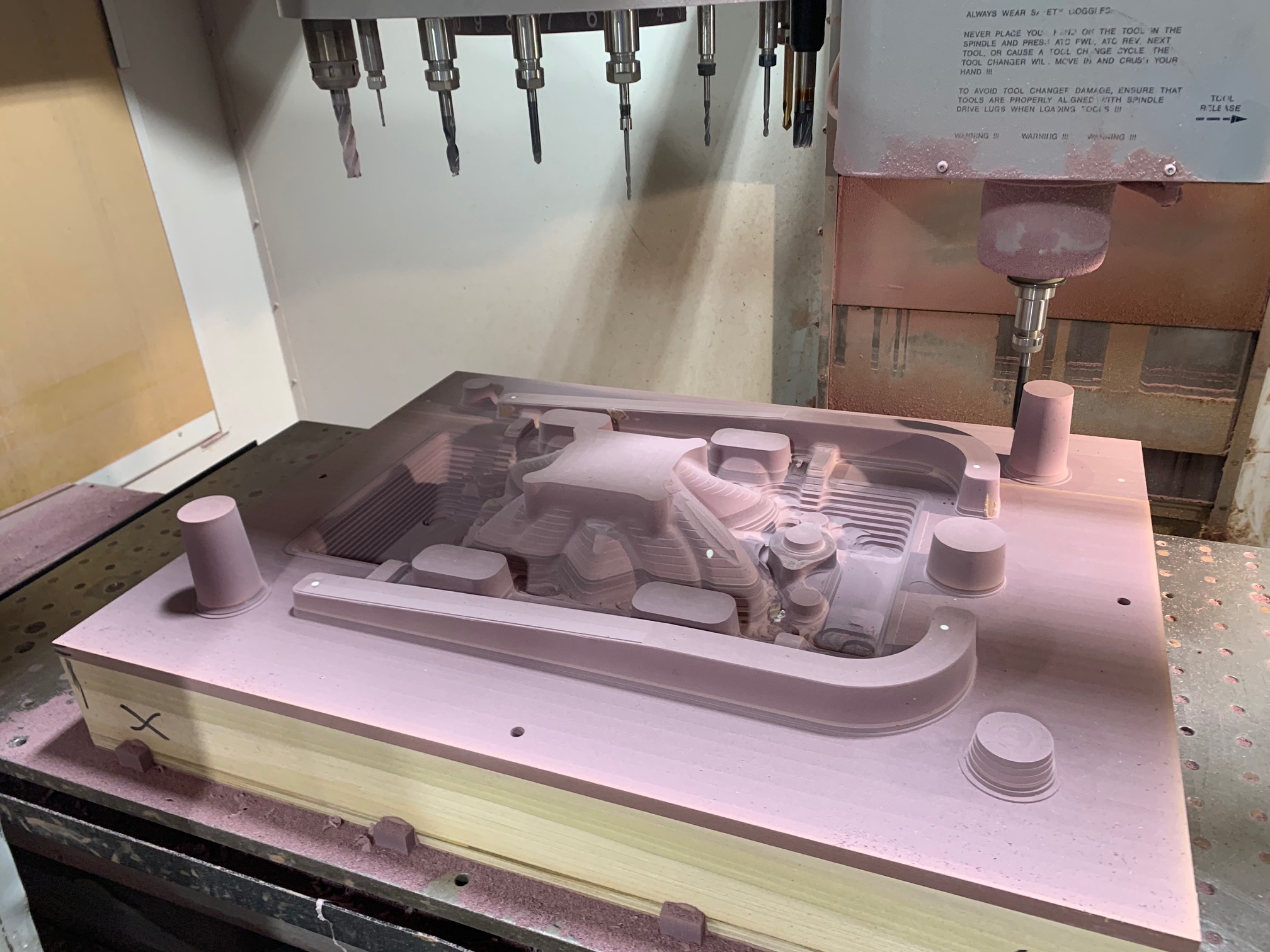
The new generation of advanced tools accelerates the process of producing low-volume manifolds. “We have our own 3D laser scanner where we can actually reverse engineer a customer’s manifold that they have modified an off-the-shelf manifold to their own design,” said Cunningham’s Miller. “This technology speeds the process up greatly and eliminates a lot of hand work to produce the foundry equipment.”
Those tools have led to remarkable advances in both custom and regular production intake manifolds. “By far the biggest improvement to manifold design has come from CAD. Long gone are the days of cutting and trimming and welding together pieces to get everything to fit, even the first time,” said Meagher. “Now a complete manifold can be designed, fit, tested, and even placed on an engine or in a car virtually before the part is made. The other, possibly more significant technology to revolutionize manifold design is Computational Fluid Dynamics (CFD) and Finite Element Analysis (FEA). CFD allows us to not only refine the shape by dynamically simulating the conditions of a running engine including airflow and distribution in relation to compression, vacuum, cam timing, etc., but also simulate heat exchange, and other factors such as intercooler efficiency on our Iceman. FEA can then be used to make sure the manifold can deal with the physical stresses of heat, pressure, and vibration that could lead to premature failure of the manifold.”
At some point, every racer will have to choose between custom and off-the-shelf. Fortunately, in today’s market, good choices are everywhere.
SOURCES
–