TECH SUPPORT: CHASSIS SETUP EQUIPMENT
Proper training and an understanding of the data are essential to maximizing the benefits of these precision tools.
Even within the racing world, chassis setup is a bit of a dark art. While gear ratios, boost levels, and horsepower are easily contextualized, metrics like cornering loads and camber angles can be a bit more nebulous. But make no mistake—when it comes to road racing, circle track, and even drag racing, proper chassis setup is a crucial element of a competitive program.
“Chassis setup tends to be more experience-based rather than data-based,” said Lynnie Doughton of DRP Performance, Rocky Mount, Virginia. “So for most tuners, the settings that they input are largely based on what they’ve done in the past, not necessarily what is considered ‘optimum’ for the vehicle.”
While the sweet spot tends to be harder to pinpoint, there is a science to it. “You’re going off of what’s essentially an emotional reaction—driver feel,” he explained. “But with the right equipment used properly, you can actually put numbers to all of that, and make logic-based decisions based on the data you have, just like you would when tuning an engine.”
Part of what makes chassis setup such an arcane enterprise is the specialized equipment required to do procedures like corner balancing, damper valve adjustments, and motorsports-spec alignment tweaks, along with the fact that changes made to one element of the setup have the potential to affect other aspects of chassis behavior. Together, it’s a situation that can create a steep learning curve for both the uninitiated and seasoned veterans alike.
“None of it is particularly complicated,” Doughton emphasized. “But it’s a challenge we run into a lot—folks get a new piece of equipment and they don’t know exactly how to use it, and they’re not really sure how to analyze the data they’re getting. That complicates things for them tremendously versus just doing it the old-fashioned way. The key is really just proper training.”
With that in mind, let’s explore some of the challenges most often faced by teams and shops related to their chassis setup equipment, and how best to address those matters.
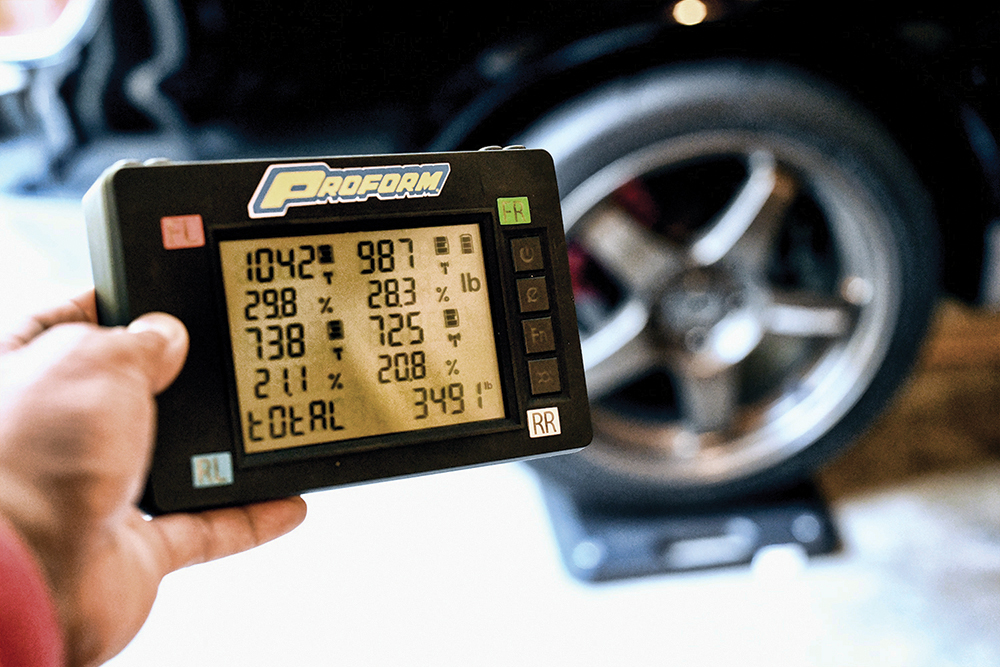
How often should I recalibrate my vehicle weighing system?
Corner balancing a car is a fool’s errand if the equipment you’re using to measure the weight carried by each wheel isn’t yielding reliable data. With road racing cars, the typical goal here is to distribute the weight of the car as evenly as possible among all four corners to provide predictable and balanced handling when turning in either direction. Adjusting that balance can also be a useful tool for drag racers who are looking to fine-tune their setups for optimal weight transfer at launch. And as such, the accuracy of these systems can be a concern for some racers.
“There are folks who have owned our scales 10 or 20 years and have never had to recalibrate them once,” said Chris Berg of Intercomp, Medina, Minnesota. “Then there are other folks that like to have their scales calibrated every year, or more, for their own peace of mind.”
Berg noted Intercomp recommends to have race scales professionally calibrated yearly if used frequently.
Ryan Salata of PROFORM Parts in Warren, Michigan, added, “Generally speaking, you’re not going to fall out of calibration—you’re not in danger of being out of calibration at any given time. That being said, things happen, and enthusiasts do love to tinker with things.”
If a scale’s calibration is in question, both Berg and Salata suggest that the best way to get things back in order is to send the system back to the manufacturer to ensure it’s recalibrated to the highest accuracy level possible. However, if a racer is pressed for time or simply trusts their own work, most systems can be recalibrated by the user if they’re walked through the process—provided they have what’s needed to create an accurate baseline measurement.
“With our equipment, calibration can be done over the phone or online with the calibration guide on our website,” Salata explained. “But it’s important to note that the calibration will be to the weight you use, so you have to ensure that you have an accurate calibration weight, and you’ll need to place a minimum of 200 pounds on the pad. So if you have scrap metal or old parts lying around, put 200 pounds or more of it into a container, get it weighed at a junkyard or recycling center, and use that number as your calibration number.”
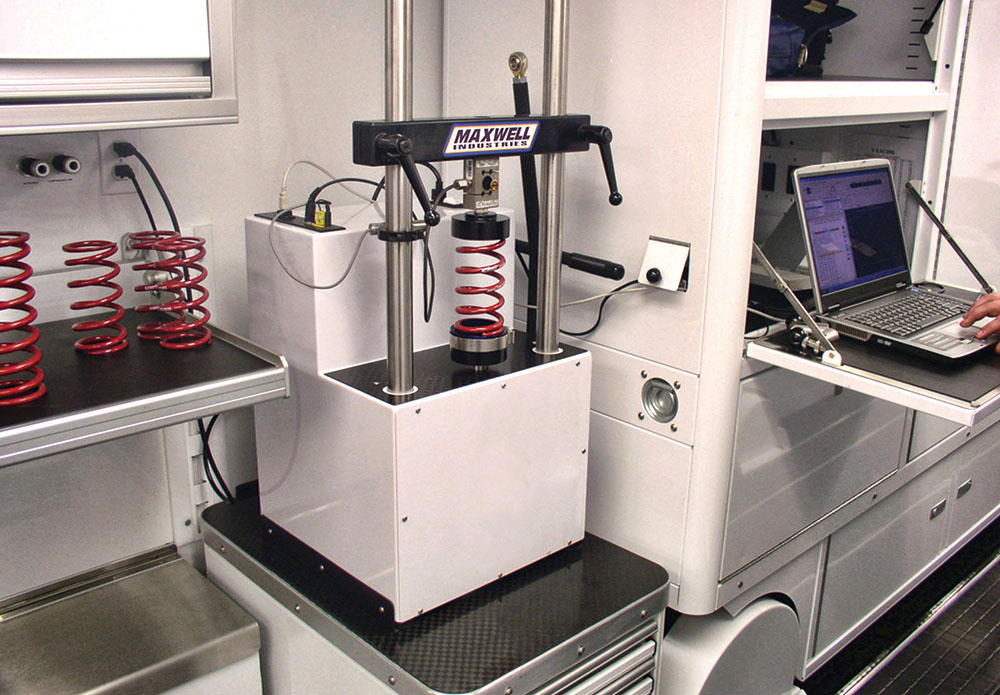
What should I use as a baseline for my suspension adjustments?
Suspension tuning is a delicate process largely due to the fact that small changes tend to have a significant effect on the vehicle’s overall dynamic behavior, and that means that too many tweaks in short succession can easily lead to a situation where you’re struggling just to get back to where you started from.
“Most of the top teams in World of Outlaws and other circle track series are all in the same realm when it comes to shocks and torsion bars—there’s only so many manufacturers, so most of the teams have already been through the gamut of what’s available,” said Steve Watt of Maxwell Industries, Ventura, California. “So the general mindset is to find a combination that works and stick with it, because the more you switch, the greater the chance you have of losing that baseline.”
For that reason, it’s important to know if your initial settings are within similar numbers of what most racers in a particular series or class are using before you start making more adjustments, and that kind of data is usually acquired the old-fashioned way.
“If you can get a general idea of what the top teams are running, that’s a good place to start,” Watt said. “First, folks usually ask about torsion bars—what rate they should be using on all four corners. That’s pretty straightforward stuff. Shock valving is a little more complicated because you have to consider compression and rebound at each corner—they’re looking for the numbers. Once we know what they’re currently running, and we have some data that’s already been proven by other teams, we can tell them whether they’re close to where other competitive cars are, or if they’re way off.”
All scale systems are basically the same, right?
While the primary job of a scaling system is to determine specific pieces of data—how much weight is resting on each wheel of the car—these days racers have some options when it comes to the additional data a system can provide, which can have a significant effect on a team’s overall approach to tuning.
“Any worthwhile system is going to give you information like the weight distribution between the left side and right side, the front and rear percentages, the cross, the wedge numbers—all those different scenarios,” said Ben Baker of Longacre Racing Products, Boonville, Indiana. “But there are different levels of complexity in terms of what you can do with that data. For instance, with our basic scale system you can save one data point, whereas with our tablet systems you can save up to 50 data points. With the tablet system that allows you to, for instance, keep a record of the data from a specific day, a specific location, and a specific setup so you can reference that later when making adjustments or compare the changes when testing. It adds a lot of flexibility.”
Baker also noted that racers have some considerations to make with regard to the technology involved. “We have both wired and wireless scaling systems,” he said. “With any wireless system, one thing you need to keep in mind is that most of these systems use a Bluetooth signal to communicate. Because of that, it’s important for each scale pad to have a clear line of sight to the tablet—they shouldn’t set down into pull down rigs or some kind of concrete opening where the signal can get trapped. So with a wireless system you need to be mindful of how the pads are placed under the car, or it may have trouble getting data from the scales.”
Beyond the obvious benefits of cabled scales versus wireless scales, what other benefits are there?
“Other than the convenience of not having to run cables to each scale pad, Intercomp RFX Wireless Scales provide the most options to view and analyze your scale data,” said Berg. “Display options include a traditional wireless handheld indicator, RaceWeigh PC software, and Bluetooth communication to a mobile device. An added benefit of the PC software option is the ability to plug into a flat screen TV for easier viewing. Bluetooth communication from a handheld RFX indicator to any mobile device with the iRaceWeigh app is a standard feature beginning in 2020.”
What is the difference between spring load and wheel load, and why should I care?
“A lot of teams will get data from spring and shock load machines, and they’ll assume that’s all that they need,” said Doughton. “But the wheel load is important data, too—that’s what the tires are actually feeling on the track.”
He noted that there’s a significant difference between the two, and the buck ultimately stops where the tread meets the surface. “As the car is traveling down the track, it’s going through pitch and roll motions that will change the needed spring load. It’s something we see a lot—people think that because they have their spring loads correct that the car should be sorted out, and they don’t understand why the suspension is over-traveling once they get it out on the track.”
That extra layer of wheel load data is provided by a pull-down fixture. “It’s a piece of equipment that measures how much force is on each wheel while it’s in a corner, and the confusion tends to come from not understanding how it works independently of a spring load machine,” he continued. “A spring load machine is a great tool—that’s what we’d use to make spring changes at the track, but it’s not really a ‘setup’ machine. It’s only looking at one individual element among myriad different things that are happening. A piece of equipment like a pull-down fixture is going to give you more of the total picture of the entire setup.”
So, why wouldn’t a tuner just use a pull-down fixture from the get-go, then? Doughton said it often comes down to sheer simplicity. “A lot of people are looking for the easiest way to get from Point A to Point B,” he explained, “and there’s this hope that they will get where they want to be just using spring and shock load data. That stuff is going to get you to a certain level. But for those who want to get their setup to the next level, you need to take a more advanced approach, and that’s where things like pull-down fixtures come in.”
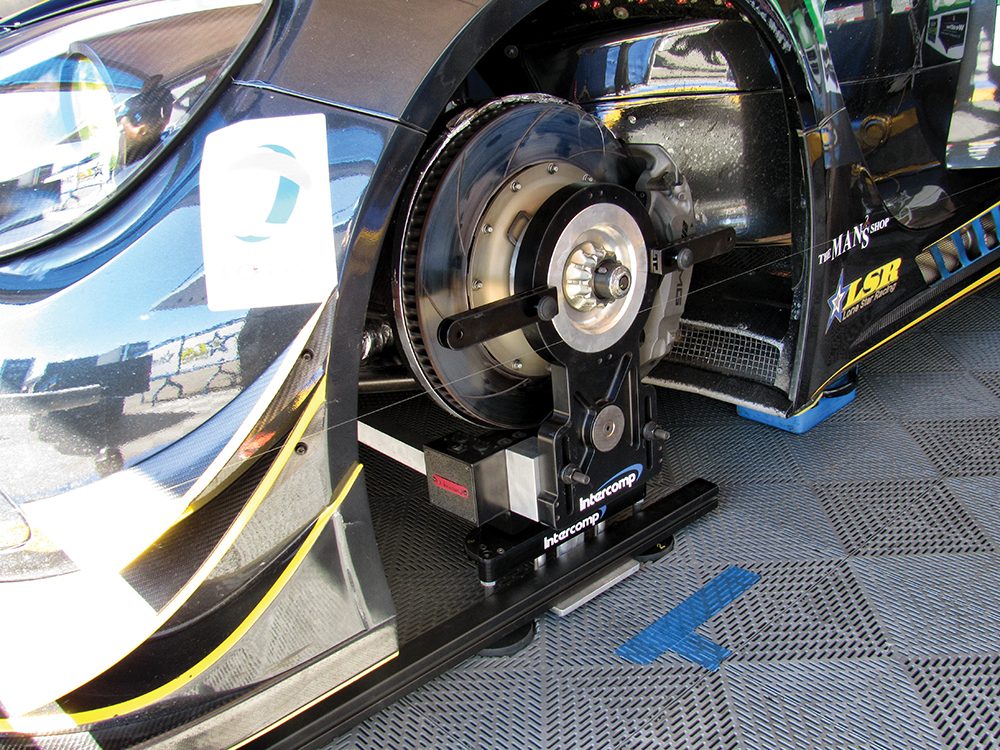
Is there a reason to upgrade from an analog caster-camber gauge to a digital one?
Caster-camber gauges are one of the primary tools used when adjusting a car’s alignment, and “bubble vial” analog designs have been the industry standard for decades. However, digital gauges have become more affordable in recent years, and there are clear benefits for those who decide to make the switch.
“The thing with an analog gauge is that you’re really only as accurate as your eyesight is,” said Berg. “If you go the digital route, it gets you down to tenths of a degree, so you’re able to get that much more exact, and know exactly where you’re at.”
Baker shared a similar perspective. “As people have started running more and more camber and caster in cars, the analog-style caster-camber gauges are becoming obsolete,” he explained. “A digital gauge has essentially infinite range, while an analog one might cap out at 15 or 20 degrees, so the flexibility is limited. And digital is basically foolproof—whatever the number is on the gauge, that’s where you’re at. Analog is more the user’s interpretation of the readout—two people can read the same gauge and one might see 13.2 while the other sees 13.0.”
And while a tenth or two of a degree might not seem like much, Doughton reminded us that it can mean a lot on race day. “Minutiae is the difference between finishing third or first, or tenth and fifth. Modern chassis tools allow you to get close to perfect right off the bat, and that means you can focus more time on the small stuff to get the car to run just a little bit better, rather than spending it just getting the car initially dialed in.”
SOURCES
–