New To Market
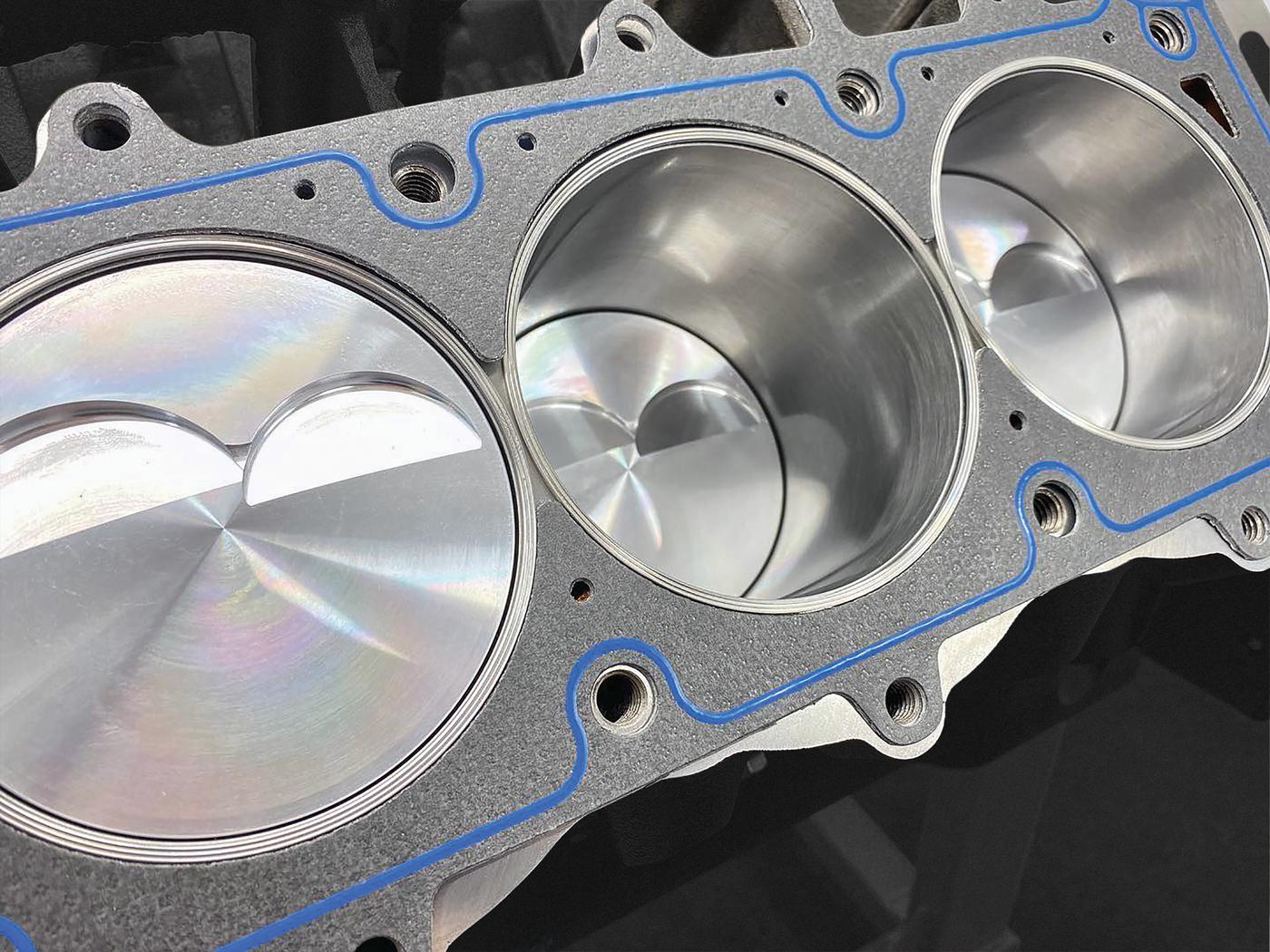
SCE Gaskets photo courtesy of ACE Racing Engines
Rising power levels and a growing diversity in engine components make gasket development more important than ever. Here’s how top suppliers are keeping pace with racer demands.
While they have always been a key component in making an engine work properly, never before have gaskets—especially those tasked with sealing the business end of a high-powered, boosted powerplant—been asked to do so much.
Today’s four-cylinder engines, like the Ford EcoBoost, can make 250 or more horsepower from the factory, “which is pretty good for a four-cylinder,” said Ryan Hunter of SCE Gaskets, Mount Pleasant, Tennessee. “Then our customers in the aftermarket ask, ‘How can I make it produce 1,200 horsepower?’ At 1,200 horsepower we’re moving that block, deck, crankshaft, and cylinder head all over the place under load, and problems begin to occur with an OEM head gasket.”
“We run into problems with applications that have been power added,” noted Tim Golema of MAHLE Aftermarket, Farmington Hills, Michigan. “Now that the intake charge is at such a high volume, we have to be concerned with maintaining the seal. It’s no longer the motor alone sucking it down the cylinder head. Now you’re blowing it down the hole with 30, 40, 50, 60 pounds of boost. Now the act has become more complicated.”
How do gasket makers keep up with this ever-moving horsepower target? We spoke with several leading manufacturers in the performance automotive space to find out.
Seeing a Need
The first step in staying abreast of racers and their engine development is recognizing that a need for new gaskets exists.
Flatout Gaskets of Mundelein, Illinois, recognizes those opportunities “partly through industry need and partly through customer calls,” said Tony Gillig. “Often when a company produces something new like a cylinder head, it doesn’t make the gasket. We hear through the industry that, say, Brodix or Dart is making a new head, and we get with them to find out what the head looks like so we can create a gasket for it. Or we’ll get a customer calling and asking, ‘Do you have a gasket for this?’ If we don’t, we do some digging and go to the manufacturers for a way to generate a gasket for that product.”
Cometic Gasket of Concord, Ohio, takes a similar approach. “We may get requests for a certain part, or we’ll see what’s being developed in the market,” said Micky Hale. “When we see more of something being developed, we’ll talk to the engine builders and the piston manufacturers. That’s usually where it starts, when they start modifying something.”
“The ideation process can come from anywhere,” said Nick DiBlasi, Race Winning Brands’ director of product management in regard to Pro Seal of Cypress, California, a brand born from the performance experience of JE Pistons. “Our staff is just like our customers and engine builders. Every one of our sales guys is a racer. So we’ll often hear about opportunities internally first. And we talk on a regular basis with our customers and engine builders.
“For what we do, in most cases it’s an OEM engine that someone built that is now exceeding the factory gasket capabilities,” DiBlasi added. “We need to understand the application to understand what is failing. We’ll speak with the people blowing out the factory gaskets and ask what they’re doing. We’ll look at the gasket, drill out the rivets to find out what is it about this factory gasket that’s failing. Is it the design, is it an OEM flaw, or are they actually pushing it way past its limits?”
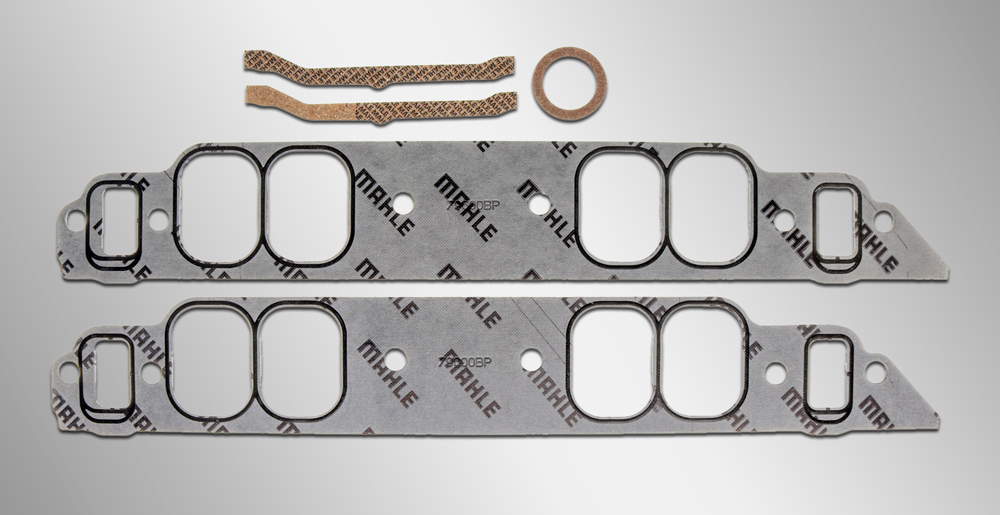
A relative newcomer to the gasket market, at least in the US, is ElringKlinger in Plymouth, Michigan. Over more than 140 years of business in Europe it has become a major OEM supplier, but it launched its US aftermarket efforts just within the last five years, offering performance gaskets through a select distribution network that includes Engine Parts Group (EPG) and Brian Tooley Racing. “Our vision is to bring this brand awareness in the US with the right distribution partners, best-in-class products, and supported with effective marketing,” Jeff Guenther said.
While ElringKlinger manufactures gaskets for Formula 1 through its OEM channels, here in the US “we like to operate through our distribution team,” said Harald Reinhardt. “They know better their customer range and what they want to serve.” EPG, for example, gets its LS gaskets through Elring.
“We have a full-range engineering department,” said Reinhardt. “Whenever we put a gasket out, we collect the requirements from the customer, so we make sure we know about what kind of sizes they need, what kind of horsepower they’re running. Then we do our full R&D with all the OE knowledge in the background.” When the gaskets get to the customers, “either they do some dyno tests or test runs or they use it immediately. Whatever feedback we get, we use to improve and get better.”
At MAHLE, “we need to determine if there truly is a need” before developing product, Golema said. “There are many applications that are very, very limited. It would be difficult to justify putting all the effort into making a new gasket if only six guys in the country would be using it.”
He said the PRI Trade Show is among the “first places we look” to gauge the need for new gaskets. “We get to see new blocks, new cylinder heads, new intake manifolds. If someone has created hardware, chances are someone will want a gasket to fill that gap.”
The situation is different at Clark Copper Head Gaskets of Blaine, Minnesota. “Right now, most of the stuff we’re doing is custom,” said JR Clark. “Most new motors are using MLS gaskets. They’ve become so good they don’t need a copper gasket.” Most of the gaskets he makes, then, are for older engines, including race motors based on “small and big block Chevys, 351 Fords, 440 Chryslers, some 429/460 Fords, motors that haven’t been updated to where people use enough of them to keep gaskets on the shelf.” He’s also doing a brisk business with tractor pulling engines. “We’re making a lot of gaskets for Internationals, Farmalls, Olivers. They’re making so much horsepower now, they can’t use the old gaskets, and a lot of the tractor pulling motors are so old, nobody’s made anything for them in years.”
Custom Gaskets
While it may not be their mainstay, several of these companies offer custom gaskets for low-volume engines or specialized projects.
Custom gaskets “are a big part of our program,” said Cometic’s Hale. “Almost every major engine builder across the country comes to us and says, ‘We’re doing this to this cylinder head or we’re CNC’ing this cylinder head and we need intake gaskets to match.’ We get their DXF [drawing exchange format] file in here, then we have a gasket to match what they need. We can change the gasket thickness or the port sizes, or anything that they’re doing. And we’re good at keeping secrets. If it’s their spec part, it won’t be going out the door to a million people.”
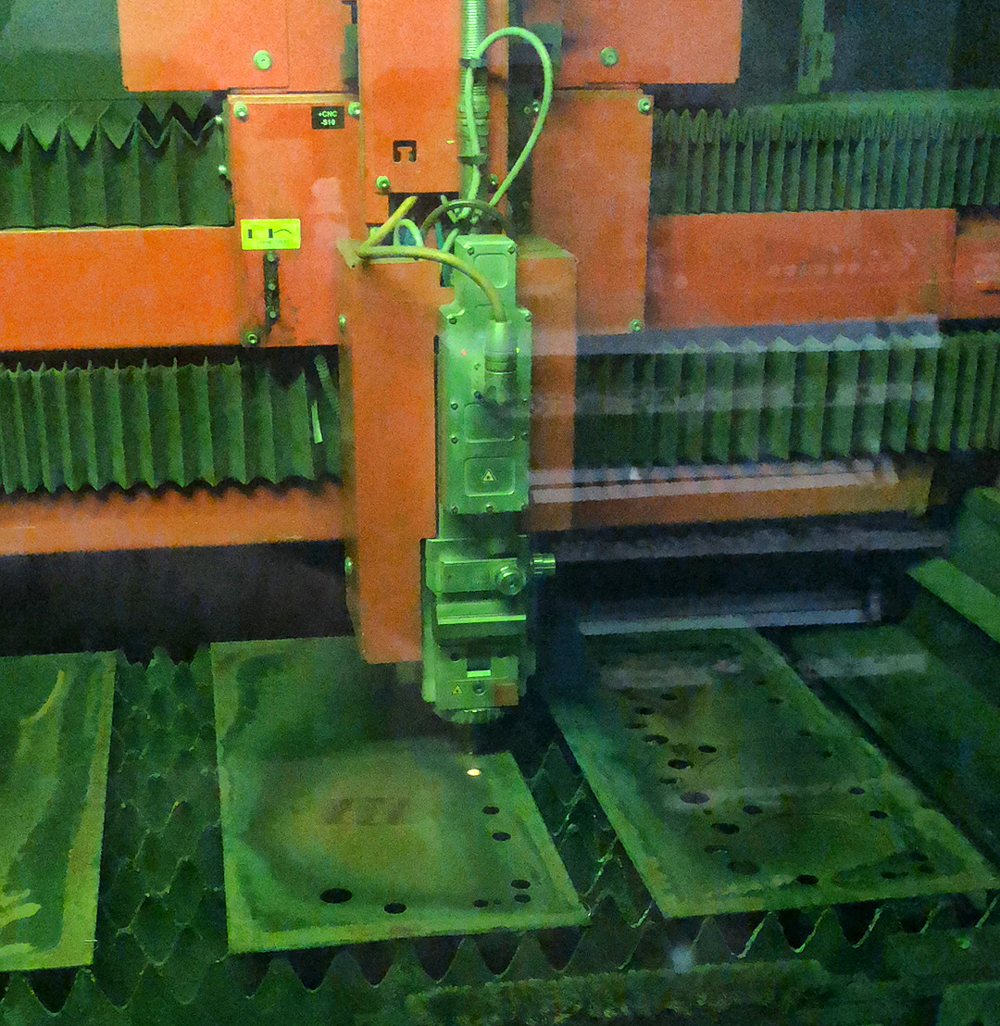
Elring, too, has a prototype shop that can produce custom gaskets “for any kind of car, any kind of specs,” Reinhardt said. “As long as we can get the old gasket or some specs, we are able to rebuild those gaskets.” Prototype shop requests can be submitted via Elring’s website (elring.com).
“We offer all the basics, but we can make a custom gasket for any application,” said Flatout’s Gillig. “We cater to our customer’s needs, whether it’s an individual racer or an engine builder. One guy might want to order a hundred, one guy might want 20 sets, or a guy calls and needs one for his motor. No problem, we’ll get them out today. We can fill that empty hole and get it to somebody in a hurry. You can make or break some guy’s season that way.”
Manufacturing
Few of the companies we spoke to were willing to provide details of their manufacturing processes due to their proprietary nature. Those who did share had some interesting details to discuss.
“Back in the day—and this is a terrible thing to hear—but gaskets were literally made out of centers laying around because the material was cheap,” said MAHLE’s Golema. “That’s not how we operate. We use a virgin sheet of material per application, and every gasket is designed per application. That makes it sound like there’s one choice of material to use, but there’s a litany of materials we may use depending on that specific application.”
He cited a case where a potential customer at last year’s SEMA Show “saw a gasket made for a big block Chevy. But this particular engine was made for a Brodix head, which has a machined surface and a machined valve cover, so the gasket was relatively thin and dense. That gasket would not work on a stamped cover with an as-cast head. It was designed for perfectly flat surfaces with the best bolt load you could get. Just because it’s performance doesn’t mean it fits.”
When Clark is manufacturing a custom copper head gasket, “we request that they send us the old gasket if they have one in decent shape,” he said. “That makes it easier to make a print from, and we can go right to copper and send it to them. If the gasket is bent up or not in great shape, we’ll make them an aluminum template and send it to them to make sure it fits the motor the way they want. When they verify it’s what they want, then we’ll make a copper one. Especially nowadays with the price of copper, we don’t want to be ruining it. If we can even get it.”
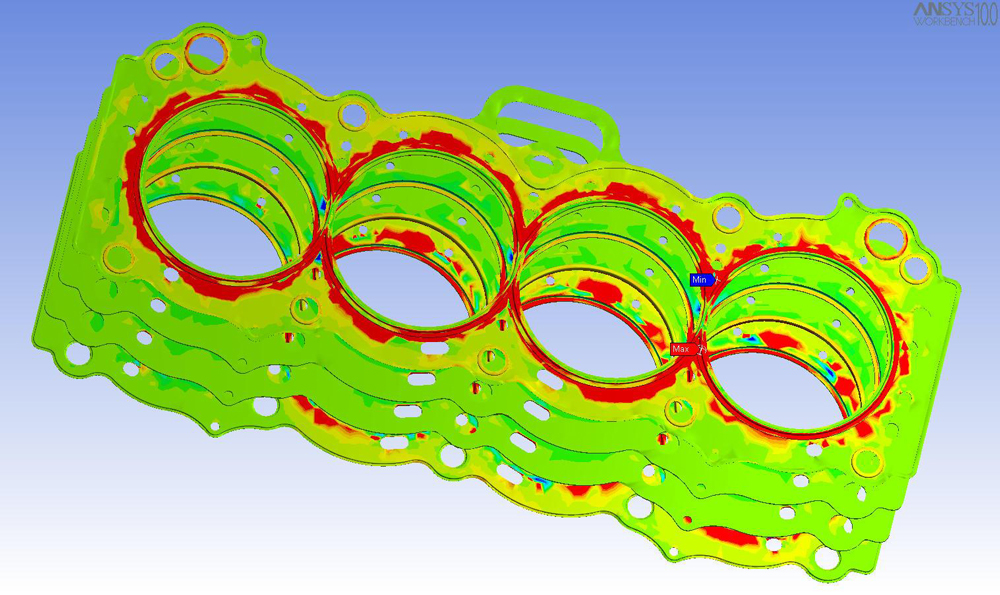
At Pro Seal, “one consistent design aspect we follow with our MLS gaskets is that you want all the layers of the material to be the same,” said DiBlasi. “All the layers in the gasket are of the same exact grade of stainless steel. Then instead of a one-hit process that embosses it, we form it over multiple hits and presses. What that does is build a nice, smooth radius for all the bends and embossment. You don’t want to stamp it too hard, because that makes a lot of ridges and stress risers. You want to slowly stretch the metal, and then stress-relieve and heat-treat it after that process, which normalizes it in an embossed state.
“That’s really critical,” he added. “Probably the most important thing in creating any sealing type of gasket is the process by which you emboss it and then treat it after that. It creates the memory in the metal by processing it after. A lot of companies take a gasket that’s pre-coated, then emboss it or laser cut or water cut it. The problem is, because it has a coating on it, you can’t heat-treat it. That will melt the coating. But when you heat the gasket back up, and it’s not heat-treated, it wants to normalize back into its original state. Any time you can heat-treat it, that’s the new normal, its new living state for the rest of its life.”
Hunter said SCE has “engineering capabilities here, drafting and drawing, fitting up to the component whatever it may be. We’ll plot it, make sure that it’s properly dimensioned, and then we produce a tool. There are various types of tools—some are as simple as a steel rule die, which is very much like a glorified cookie cutter. There are limitations to those tools, so they’re used in certain areas and not in others. They can’t cut steel core material very well, for example, as they tend to leave kind of a pucker. There are tools that are well suited for an intake gasket that wouldn’t be well suited for a head gasket, for example.
“Then it comes down to, if we have the fitment right, how does it perform in the field?” Hunter continued. “We can get very close to knowing how the gasket will perform based on the gasket design and our knowledge of the raw materials selected for it, and then we put it out to the customer base. Because we cannot, even on a dyno, duplicate what takes place in motorsports.”
Research, Development & Testing
While many of these companies get new product ideas from their engine builder customers, it’s also common for them to work with their customers to get real-world research, development work and testing on those new products.
“We have what we call select development partners all over the country,” said Hunter. “There’s Dale Meers Racing Engines in Kentucky, David Butler at Butler Performance near us in Tennessee, and Kenny Duttweiler out in California. We’ll go to them and say, ‘Here’s a new product. Try it, flog the thing, tell me what breaks.’ They’re happy to do that because they know that we’re pushing the envelope trying to get them a product that seals more than what’s available now.
“I don’t want it to sound like we’re just taking our best guess and letting the customers do our testing,” he added, “but in some respects that’s actually true. Customer input has often helped us with the final degrees of refinement.”
“We have customers who will let us use their engines for some testing,” said Kristen Damberger of Cometic Gasket. “They’ll come in and want to see what power they can get out of their engine. We’ll ask if we can use some of this data for ourselves, or can we run this test a little bit differently so we can get what we need out of it?”
At the same time, Cometic Gasket also has “a full-service engine shop and dyno in our facility,” Hale added, with LS and small block Chevy mule engines in-house. “It is a great supervised, controlled environment, where we know the consistency and how things are put together. We’ll know what will work and what’s not going to work.”
Pro Seal, DiBlasi said, has “multiple companies, with decades of experience, that specifically manufacture to our requirements. Utilizing their OEM experience, we lean heavily on their in-house development and testing. We work in collaboration with our suppliers on requirements for the engine and operating conditions to mutually understand the specifications needed for success. They also do a lot of physical testing, including follow up with FEA [finite element analysis] and validate with real-world engine dyno testing. We perform surgical inspection post dyno testing, or work with a customer we’ve partnered with to ensure sealing is optimized and performance targets are achieved.”
Chemical Gaskets
Beyond the world of MLS, cork, rubber, and copper gaskets are the silicones and other chemical gasket makers. Eric Seibold of Permatex in Solon, Ohio, said these gasket types are becoming more prevalent due to evolution in engine manufacturing.
“The biggest change we’ve seen over the years has been in the quality of the machined surfaces in domestic automobiles. With computers and laser cutting, the surfaces are so fine that they need less gasketing material to form a seal. That has led to an increase in the use of chemical gaskets like ours, and the ability for us to use thinner formulas. You don’t need to cake in a bunch of silicone to create a physical barrier; you’re looking to glue or adhere two surfaces together.”
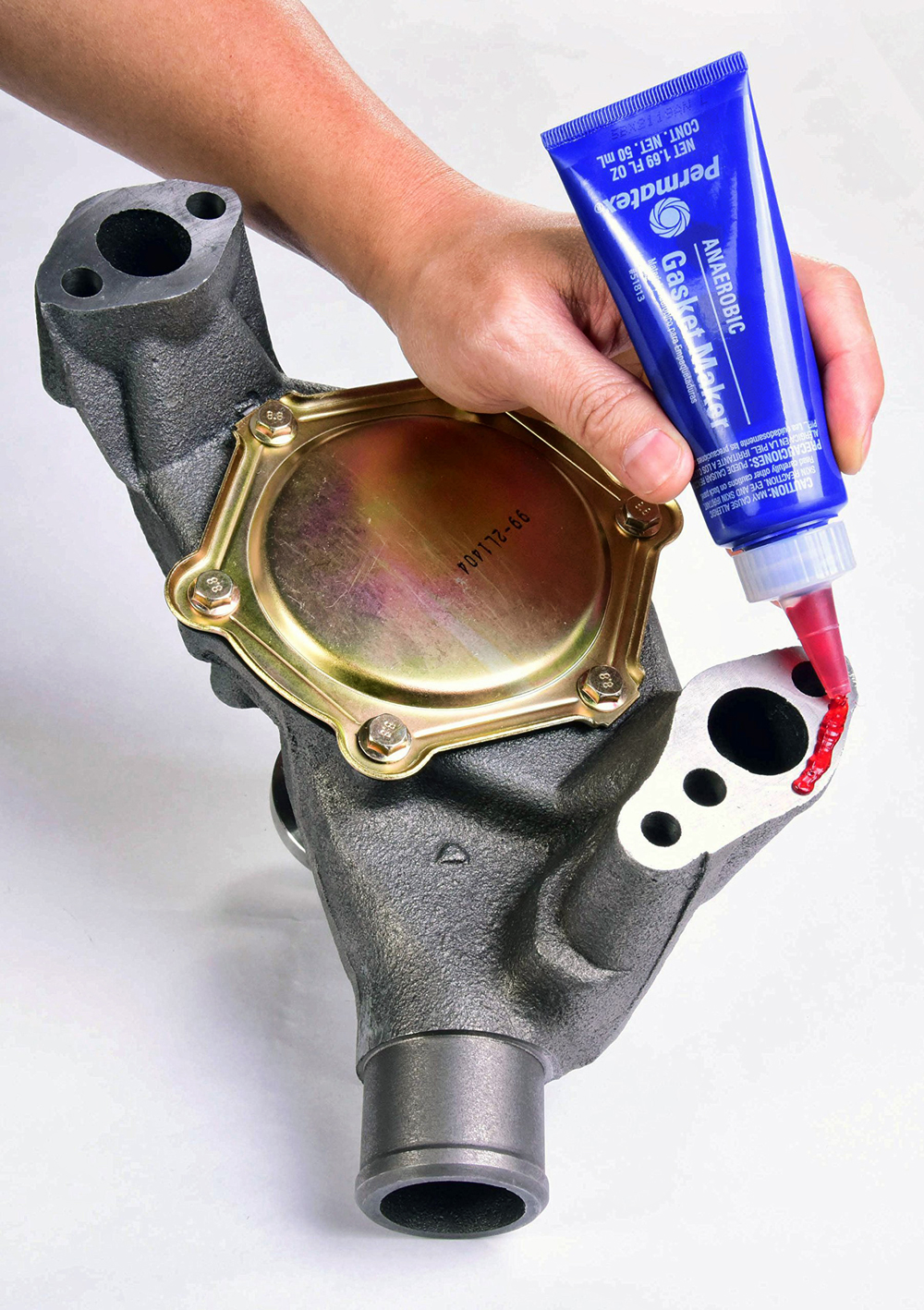
Permatex is a fixture at chain auto-parts stores and DIY centers, but Seibold said racing is “our testing and proving ground. We have relationships with a lot of different race teams. We will send them product that is either new to market or in development, ask them to use it on test-and-tune days, and if they have a lot of success, then use it on race tracks. If it functions for them, in extreme conditions that they’re under as far as pressures and temperatures go, we know it’s going to work on a street vehicle.”
Though he couldn’t share specifics about products in development, Seibold said a Southern California professional drift team is currently testing “a new experimental gasket maker.” That same product will “replace all the gaskets” in a Mini Cooper that is entered in a 24 Hours of LeMons race in October.
“We can do all the lab testing in the world to get our quantitative numbers and confirm a product is within spec for a silicone, meets a certain ASTM test, or meets a certain OEM specification. But the real-world, qualitative use by mechanics or race teams is arguably more important,” Seibold said. “We can be fairly confident in the lab, but that doesn’t necessarily mean it’s going to perform in the harsh conditions that race teams put them through.”
Carburetor Gaskets
The carburetor gasket niche is wholly different than gaskets in the rest of the engine, noted Dave Braswell of Braswell Carburetion in Tucson, Arizona. “It’s not an application like a head gasket where motors are making significantly more power every year, and the loads on the gaskets are quite a bit more severe.” That doesn’t mean, though, that the carb gasket landscape isn’t changing.
“Carburetors originally were an OE application, and the lowest bidder was the one who sold the carburetor,” he explained. “That meant the quality of the product and castings weren’t normally the best because there wasn’t the profit margin to keep the tooling fresh, so gaskets were really important. Now, with CNC machining, the overall quality of products is much better, so the sealing of the products is much less of an issue than it used to be.”
Braswell uses “premium materials in our gaskets,” with applications available for all race cars that use carburetors.
Braswell has gone beyond traditional gaskets for sealing applications. “Whenever we can put an O-ring in a product, we do. Probably 10 years ago we put an O-ring where the power valve goes into the metering block instead of using a gasket. That’s been really successful. The power valve seats on aluminum on the metering block instead of on a gasket, so you don’t have to worry about the gasket drying out and the power valve coming loose.”
Braswell also machines sealing beads “in all our castings. If there’s not a sealing bead in the casting on a machined surface, like on float bowl screw washers, we’ll machine a sealing bead into it to ensure that they seal. A lot of the sealing issues can be eliminated with proper design work of the component part that you’re trying to seal.”
Sources
BLP Products
blp.com
Braswell Carburetion
braswell.com
Clark Copper Head Gaskets
clarkcoppergaskets.com
Cometic Gasket
cometic.com
ElringKlinger
elring.com
Flatout Gaskets
flatoutgroup.com
MAHLE Aftermarket
us.mahle.com
Permatex
permatex.com
Pro Seal
auto.jepistons.com/proseal
SCE Gaskets
scegaskets.com