Power By Numbers
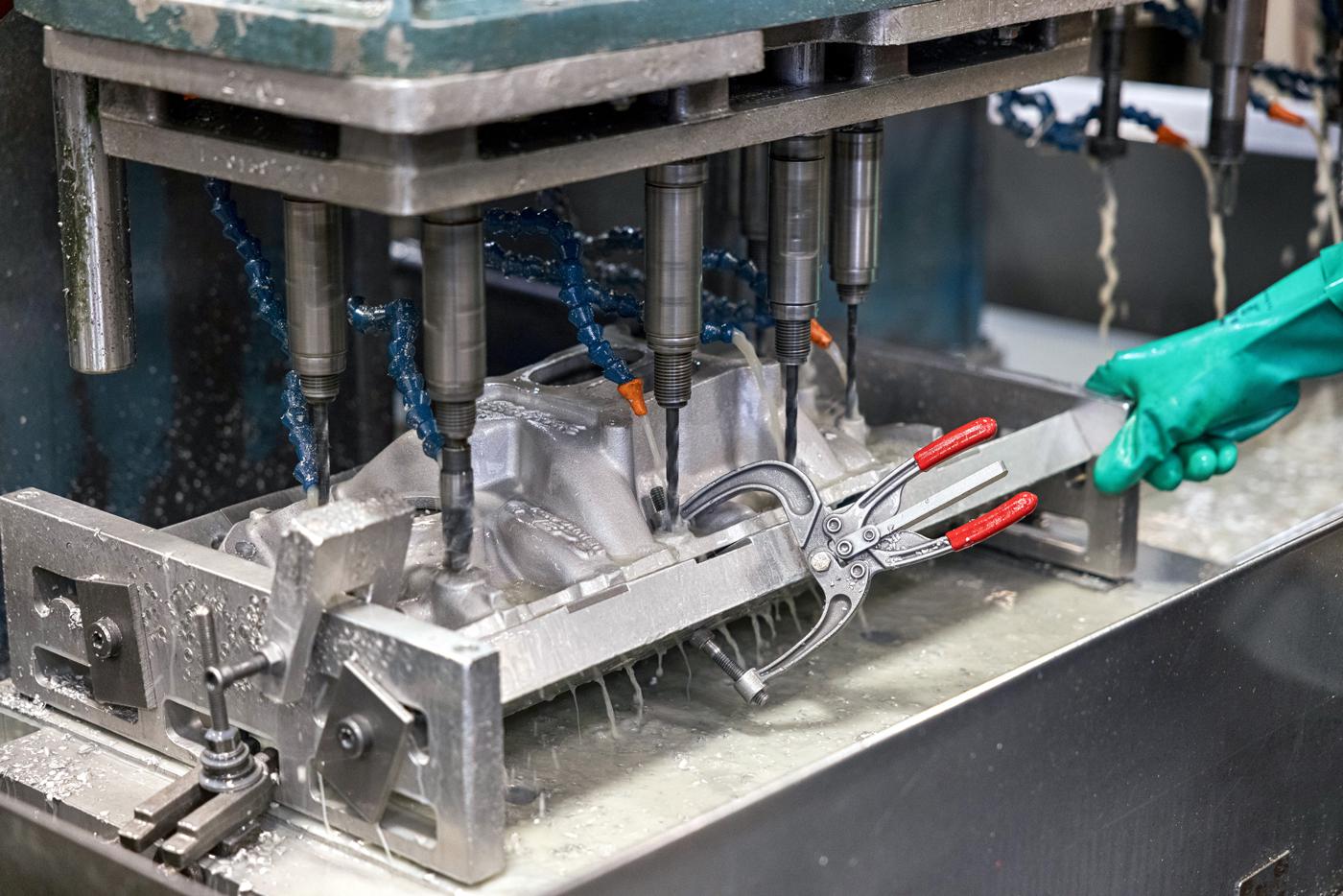
Intake manifold designers rely on a variety of tools when developing new products, whether using complex math formulas or simple gut instinct and experience.
Even with considerable technology and computing power available to the aftermarket, some companies still prefer to develop new intake manifolds or improve on existing manifolds by leveraging practical knowledge gained over the years.
“We’re actually old school,” said Mark Fretz of Brodix, Mena, Arkansas, explaining how the company is working on a new 18-degree cylinder head for the big block Chevy, with a dedicated intake manifold to soon follow.
“We still take each individual piece out of the core boxes in our foundry,” said Fretz. “We may take the center spider from one manifold, and we’ll build new core boxes for the inrails and the side rails. We can build a new valley, add material to the intake face, and then machine for that specific cylinder head.”
“It’s a lot of seat-by-pants work,” agreed Tony McAffee of Dart Machinery, Warren, Michigan. “There were some formulas we used in the past with carburetors—they came into play because of a gear change, and you don’t want to lose all your signal to the booster. So you kind of have to keep that plenum volume at a percentage of cubic inches.
“Now, with better carburetors with much improved venturis, that’s kind of going away,” continued McAffee. “Then, with fuel injection, there is no signal needed to the venturi. Some of the rules are tossed in the garbage.”
“We’re still using what we’ve proven in the past while verifying new ideas through testing,” said Corey Spainhoward of Holley, Bowling Green, Kentucky, which recently introduced two new intakes for the Ford Coyote platform.
With advancements in CAD software, CNC machining, and 3D printing, new and exciting designs are appearing in the racing market, but often for select customers or even the designer himself.
“The newest things I’m building are for my own cars,” reported Mike Weinle of Weinle Motorsports, Cleves, Ohio. “I’m building a billet Pro Stock manifold and I’m building a sheetmetal manifold for a late model dirt car engine with a 4.5-inch bore space. Both are something new that I’ve never built before.”
Optimizing Designs
Regardless of the methods or design theories, today’s intake manifold engineers have similar goals: improve runner and plenum design to optimize airflow to the cylinder heads. High-end race shops and the OEMs will utilize advanced computational fluid dynamics (CFD) computer simulation to test different designs. Often these programs validate the old-school approach that still leads to improved power numbers.
“It does seem like the higher horsepower and higher rpm range are where most of our customers are interested,” said Spainhoward.
The increased emphasis on boost has also shaken up the intake manifold industry, introducing new sets of challenges to distribute air effectively and equally to all the cylinders under high pressure. Conventional wisdom once boasted that a plenum under pressure shouldn’t have distribution problems; however, that thinking just hasn’t been proven completely true. Designers are still toying with throttle-body location and mounting angle in addition to experimenting with different plenum shapes to better control air distribution. Often the front cylinders miss out as the air rushes in on a manifold with a front-mounted throttle body.
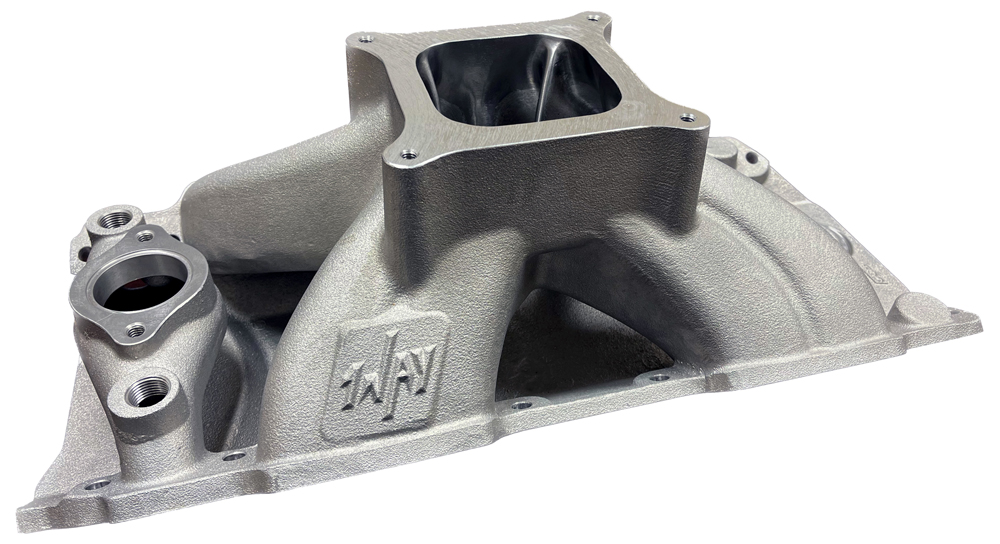
“The more you give the air a chance to actually make that turn and not starve the front two cylinders for air, the better the design,” said McAffee, who recalled a story about equal distribution to the runners when working for the late John Lingenfelter. He would switch between EconoDragster and A/Dragster classes by changing between single- and dual-carb tops on his tunnel-ram intake.
“With the single four-barrel we would have trouble with the outer four cylinders running lean, while it was perfect for the center four cylinders,” continued McAffee. “We had tried air dams in the roof and started playing with shear plates, and it wasn’t until we and other people started playing with the pent-roof design that we started making serious power.”
As noted earlier, cylinder head development is driving much of the intake these days, as are sanctioning body rules. 1 Way Technologies in Washington, Indiana, is developing a package to work with big block modifieds that run on Northeast dirt tracks.
“We have a cast four-barrel intake now in production that we developed for that tour,” said Jeff Jones. “We developed this intake around a SR-20 style cylinder head that fits their ruleset.”
Under the rules, the intake had to be cast and limited to a 4150-type carburetor. The heads were also limited on valve angle and other specifications.
“The port placement becomes critical, and then the intake becomes a big factor as far as getting runner shapes and sizes to fit,” explained Jones. “Manifold height wasn’t an issue, but plenum volume was a definite factor as these cars have to accelerate off the corner and require a wide torque curve. That means runner size, taper, and plenum volume all become big factors to develop an intake manifold for that environment.”
For the most part it was a clean-sheet design since there were no intakes available that fit that cylinder head. 1 Way cut up existing intakes, modified the sections, and welded them together to build early prototypes before transferring the dimensions into CAD to develop the tooling.
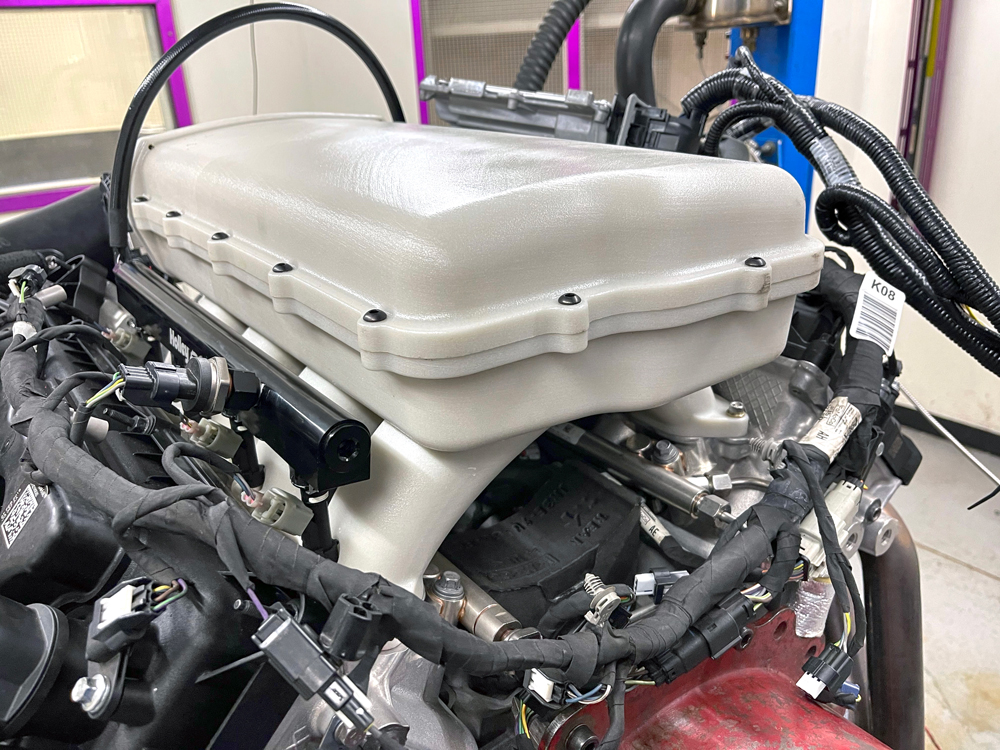
“From concept to tooling probably took six or seven months,” said Jones, adding that the design was driven by a combination of math and experience. “It’s based on the portfolios that we have learned over the years. We have minimum cross sections that we feel like we need and where the runner takes off out of the plenum. We know that if you get outside of certain cross sections, you’re going to have to turn a lot of rpm that may make a lot of horsepower but not be very drivable on the race track.”
Blank Canvas
Much of the intake manifold industry is still recovering from the high product demand experienced during the pandemic, along with the supply chain and labor challenges that disrupted production. Many new product development projects were put on hold or delayed when engineering teams were spread thin.
“We’ve been so slammed just trying to keep up with orders that we really haven’t released any new product in two or three years. The Australian market is really big right now, and in the US market every aspect from street cars to offshore boats, sprint cars—it seems like every segment is staying busy,” said Fretz, noting that the Brodix philosophy tends to design heads and intake manifolds that can be easily modified by head porters and engine builders. “We provide a blank canvas for the guys to finish how they want. We’re not trying to compete with the end user. We provide a good platform that the porting shops can expand on.”
With that in mind, Brodix offers different plenum volumes for standard manifolds. “A couple years ago we did our new big-plenum manifold where we shortened it just slightly and made everything wider, bigger, with more of an open top,” Fretz continued. “That added volume for the large cubic-inch engines, and the new 18-degree conventional head will be on that platform. It will need the large-plenum manifold.”
Over at Bill Mitchell Products in Edgewater, Florida, the emphasis is also on keeping up with demand for shelf-stock items. “We upgrade and make revisions as we go along to make the intakes perform better,” said Bill Mitchell. “The Ford manifolds have gotten popular for us, and some of that is simply because more Ford guys have found out that we have that intake. And the marine guys love our brass water jacket piece. That’s something I don’t believe anyone else has.”
The marine intake is designed for big block Chevy and is available for both the 9.800- and 10.200-inch deck heights. The key feature is an integrated brass water jacket to prevent corrosion in saltwater environments.
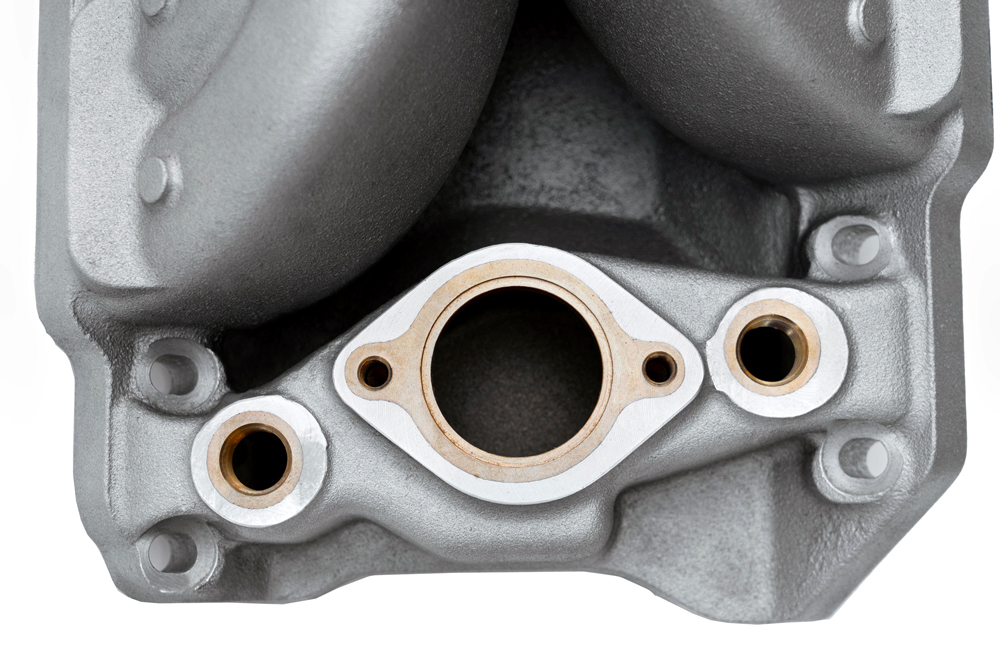
“The 9.800 guys all want a 4150 carb flange. Not very many wanted a Dominator, but they all did on the tall deck,” said Mitchell.
Recently, Mitchell brought the intake manifold machining in-house where the company’s cylinder blocks are finished. “We already had the machines to cover it. The manifolds are a much nicer piece now.”
Not all new intakes recently introduced are cast. Edelbrock in Olive Branch, Mississippi, just released a new XTS fabricated sheetmetal intake for the 7.3-liter Godzilla engine found in Ford heavy-duty pickups. In addition to improving power for racers and engine-swap projects, engineers wanted to ensure customers could fit the XTS under the hood of a stock pickup. Also, camshaft development for the Godzilla coincided with the intake manifold project.
“Because it’s a truck manifold, it was really hard to get torque out of an improved one,” said Jeff Krangnes, noting that the decision to construct it with sheetmetal was driven by time to market and no need for tooling development. “The stock throttle body is 85 mm, but we have the intake set up to run 102 mm.”
The camshaft engineers from COMP Cams were also involved in the project, so there was synergy in analyzing the flow characteristics of runner length and plenum volume.
“We ended up changing the runner lengths two times to get where we were happy, and we have a larger plenum than the stock manifold,” said Krangnes. “It’s definitely more of a race manifold. It’s meant for the guys who drop Godzillas into Fox bodies.”
As with other companies, Edelbrock is working on new cylinder head projects but not releasing details. Those heads will eventually spawn new intake manifolds as well as new carburetors. In addition, Edelbrock may trim some existing intake manifolds to simplify the lineup and avoid consumer confusion. “Plus, we’re trying to push our racing a little bit more,” added Krangnes.
Holley had a head start when developing the recently introduced Hi-Ram and Ultra-Lo Ram intakes for the Ford Coyote platform.
“We were able to get CAD data from Ford through our relationship with SEMA. By using their CAD models, we can optimize the ports,” explained Spainhoward. “We can ensure fitment with all the engine components.”
The modular intakes are designed to share the same base, then the front and tops can be designed to suit the different needs of the user.
“For the Ultra Lo-Ram, we wanted it to fit under a stock hood with stock engine mounts. The modular design also allows engine builders to easily access the runners for porting. A slightly different machining on the Hi-Ram allows people to use intercoolers for their boosted applications,” said Spainhoward, noting that Holley used 3D-printed protypes for dyno testing and fitment validation.
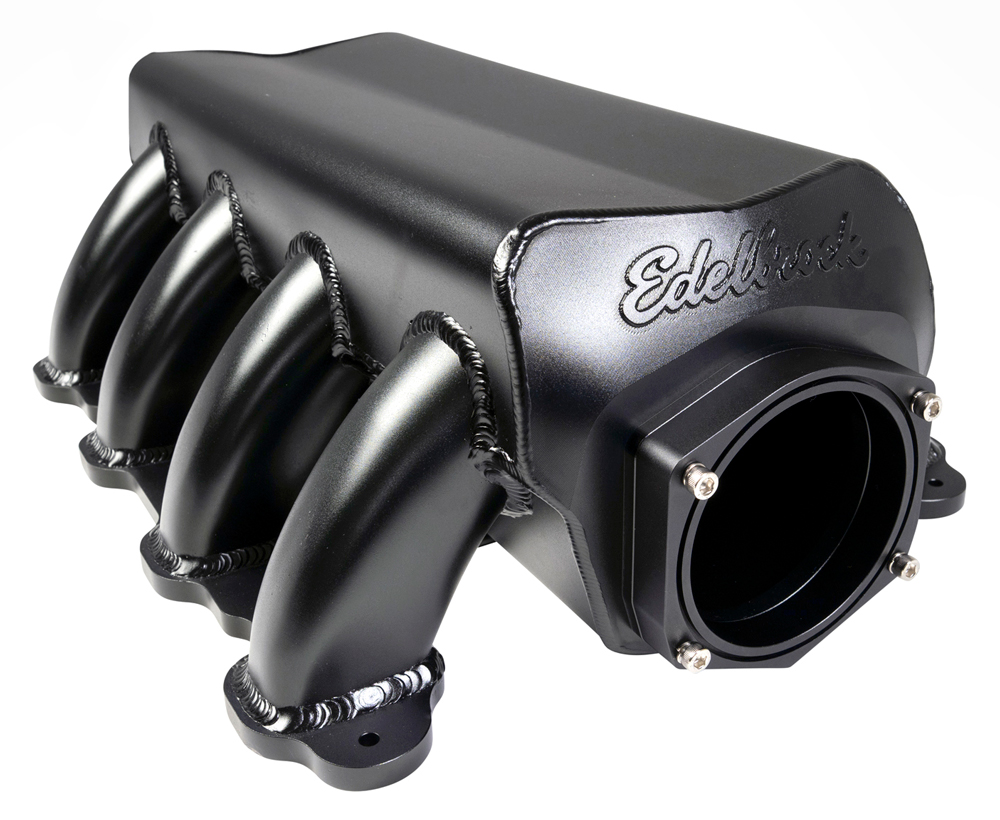
As further testament to the popularity of carburetors, Holley released a low-rise, single-plane intake for the Gen III Hemi. It comes in black or natural cast finish and will support a 4150 carb or self-contained EFI throttle body such as the Holley Sniper system. There is also an EFI version that comes with fuel rails and multi-port injector provisions.
“The single-plane manifolds that we currently offer for LS1 and LS3 do really well. A lot of people like the retro look for swaps with a modern engine into an older chassis and not the plastic manifold,” said Spainhoward. “The runner length is optimized for mid-range, and even though it’s a low manifold, we still have a nice transition into the ports of the Chrysler head.”
Results Driven
While the bulk of intake manifold sales and development is driven by the needs and pocketbook of street enthusiasts and weekend warriors, they will benefit from lessons learned designing new race manifolds. Whether seat-of-the-pants creativity or formula-driven vision, the prime motivation is to try something different with the goal of making more power.
Weinle’s efforts to design a trick sheetmetal, single-four-barrel manifold for a Chevy ROX-style 460-cubic-inch late model engine with 4.500-inch bore spacing will focus on more size.
“I’ve got a billet manifold on there now. I figure my advantage is to build one with a little more plenum and a little bit longer runner,” said Weinle. “Also, I want to raise the manifold up a little higher—more of a drag-race style.”
Weinle is working with a Pro Stock engine builder who is a disciple of longer runner lengths, and that’s where much of the design theory is generated.
“You see more torque with a longer runner. I built a Super Stock intake for a guy in Sweden, and we were definitely able to go longer and bigger and make it work,” said Weinle, adding that equal distribution with the runners is the main challenge. “I’ll be honest, this manifold is not for a short track. You can’t lose three lengths on a restart. You can definitely get away with a bigger manifold on a big track.”
For his Pro Stock intake, Weinle has fabricated the runners and port plates so far. Next comes CNC machining elements of the plenum. “I’m actually building it for myself, and it’s going to cost every bit of five grand, but it’s going to be pretty sophisticated,” promised Weinle.
Bottom line, racers are eager to try new tricks in the area of intake manifolds.
“I’m working with a couple of race teams on Pro Mod and the Outlaw 632 projects,” said McAffee. “A lot of rules are myths. Sometimes you can change those rules, and sometimes you can do nothing more than confirm what they really were to begin with. You try to break the rules often, and most of the time you get spanked. But once in a while, you find that little something and you start picking at it.
“You still have to confirm the myth and the stories, and what you’ve always thought in the past wasn’t indeed the truth. It may have only been the truth up until then,” McAfee noted. “The cylinder head design and camshaft profiles are changing, and now you have to readdress all those myths and the rules. You have to at least test the waters.”
Sources
1 Way Technologies
1way-tech.com
Bill Mitchell Products
billmitchellproducts.com
Brodix
brodix.com
Dart Machinery
dartheads.com
Edelbrock Group
edelbrock.com
Holley
holley.com
Weinle Motorsports
weinlemotorsports.com