Sealing Science
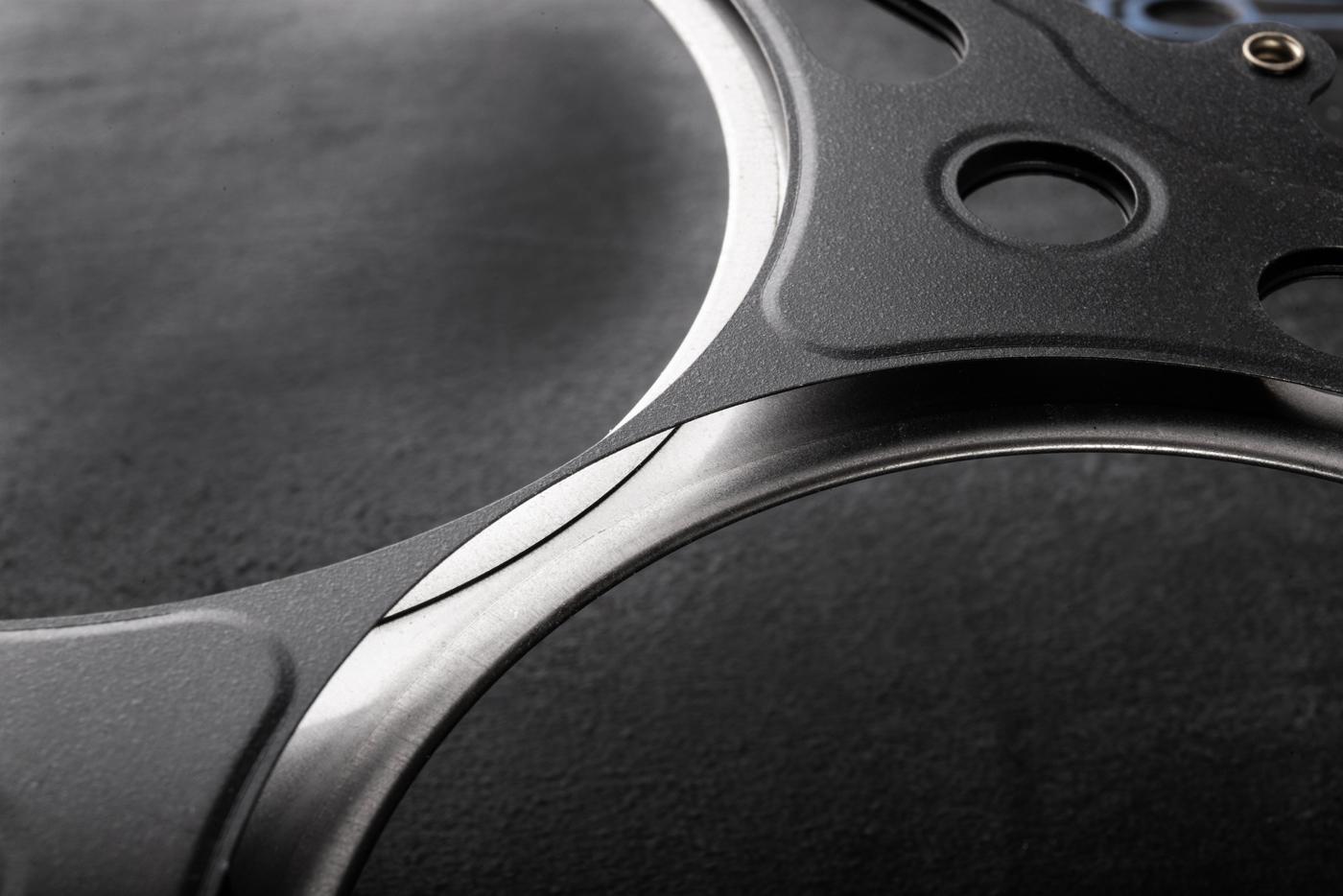
Gasket manufacturers are putting vast resources into developing products that seal better, last longer, and are easier to work with. A big part of that quest starts with the types of materials used.
It’s one of the most tortured components in a race engine. Many racers don’t give it much thought, but when a head gasket fails, it can wipe out an engine, take a team out of a race, and wreck an entire weekend in seconds. And there are dozens of other gaskets in a race car, any of which can wreak havoc in countless ways.
Although these modest-looking parts may seem simple at a glance, that’s deceiving. Sure, gaskets don’t have any moving parts, and they don’t gleam with the eye-candy, jewel-like sheen of a freshly minted set of cylinder heads. But gaskets are, in fact, extremely precise components. They’re the result of a vast army of engineers applying more than a century of collective experience, modern science, and the hard lessons of races gone wrong.
Central to the effectiveness of any gasket are the materials that go into it. On everything from oil pans to cylinder heads, gaskets are a meticulous blend of different substances, all carefully selected by engineers to deliver optimum performance. Although the basic functions of gaskets may not change much, development is never-ending nonetheless.
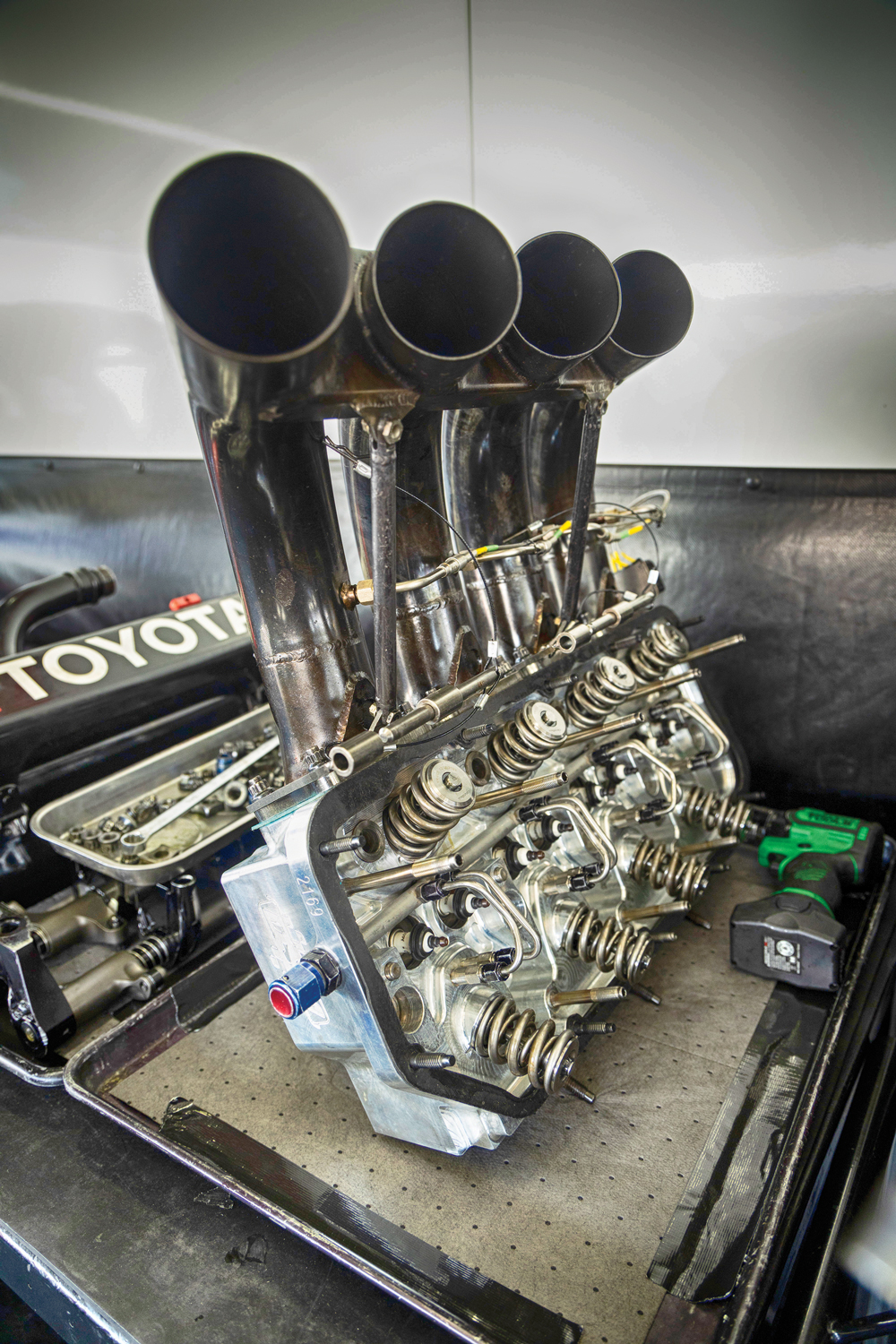
Many of today’s racers are pushing the limits of power to sky-high levels, so gasket manufacturers see their products hammered to the limits day in and day out. As if the never-ending quest for more power isn’t enough, racers and ordinary drivers alike nowadays expect that everything on a vehicle will be a tightly sealed unit, free from leaks, drips, and fluid losses.
To cope with these demands, gasket manufacturers are in constant development mode, seeking new materials and new ways to use them, in the quest to deliver the most effective products possible. The results are new, innovative ways of using materials and steady, constant improvement in the science of sealing.
Head Games
In the world of gaskets, head gaskets generally get the most attention. When something goes wrong with a head gasket, it tends to cause big, dramatic failures, compared to something less demanding like a valve-cover gasket. Even more significant, head gaskets are the sole barrier separating combustion, coolant, and oil from each other, an extremely demanding role unlike that of any other gasket.
In general terms, the primary materials used for head gaskets aren’t anything new. The most popular head gaskets for most engines nowadays are multi-layer-steel (MLS) gaskets. These sophisticated components are designed largely around dealing with cylinder-head lift. In all engines, cylinder heads lift off the deck surface as much as several thousandths of an inch in every combustion cycle. This places obvious demands on the gasket, which must maintain a perfect seal every cycle, thousands of times per minute, despite the clearance that it sits in changing as much as .003-inch along the way.
Making this phenomenon even more challenging from a gasket-design standpoint, cylinder head lift doesn’t occur consistently across the head and deck surface during combustion. The amount of lift can vary considerably depending on proximity to head bolts, clearance between cylinders, and a wide range of other factors. Presented like that, it might seem almost impossible to seal such a thing effectively. But that’s one of the fundamental advantages of the MLS concept.
“Each and every combustion event is unloading the gasket,” said Aaron Hunter of SCE Gaskets, Mount Pleasant, Tennessee. “The beauty of MLS gaskets is that they act like a spring that tracks with that. But it varies. Take for example a Ford Coyote. They’ve got four bolts per cylinder, and the bolts are relatively close to the cylinders. The LS is a little bit further out from the cylinder, the Subaru is really far out from the cylinder. So you have to look at the right gasket materials for each application based on the position of the clamp load. And then also how much clamp was available, but we also try to make sure that we can get all the clamp load we need.”
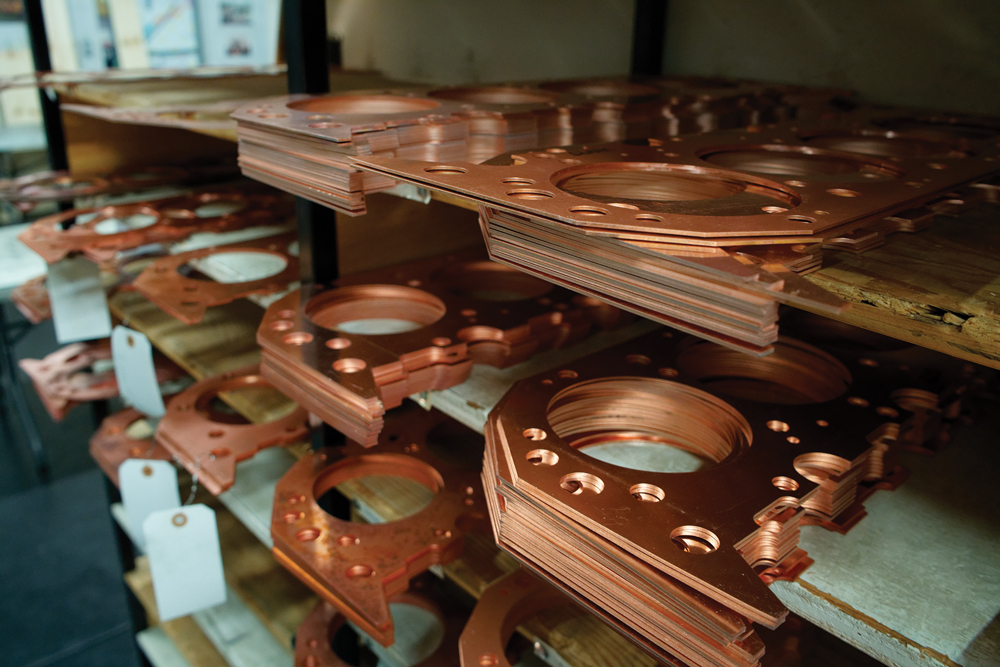
As the name implies, the primary ingredient in a multi-layer-steel gasket is steel. Each of those steel layers is designed for a specific purpose. Some layers have embossing that allows the steel gasket to take on the spring action needed to compensate for the head lifting off the deck during combustion. Along with this, stainless steel is used for its ability to resist corrosion in the harsh environment head gaskets are subjected to. That isn’t just a matter of longevity. The ability to resist corrosion enables the head gasket to control coolant pressures effectively.
“The reason that stainless is typically chosen comes down to impingement,” said Tim Golema of MAHLE Aftermarket, Farmington Hills, Michigan. “In the olden days when they made metal gaskets, they had problems with the
tin-plated steel they used when you would run the coolant. Back then, in many cases, the coolant was just water. When you would run it through the gasket, that hole would corrode and get larger and larger. Eventually, you had a problem with coolant distribution. You’d overheat because you weren’t able to put the coolant where it actually needed to be. Now we use various grades of stainless steel to prevent that. While today we don’t use much water in production cars, a lot of guys in the race car world use water, and then they put the conditioner in there so they can get the temperature higher.”
Although the use of stainless steel in MLS head gaskets is a given nowadays, from there, the choices get rather complicated for engineers. To achieve the requisite amount of sealing, clearance, and compensation for head lift, engineers carefully choose the number of layers, the grades of stainless steel, the heat-treating of those layers, and whether or not those layers are folded over to double them. These measures are all chosen in an effort to control the load that cylinder-head bolts put on the gasket, so combustion, oil, and coolant are all sealed effectively.
“We’re trying to balance the load on the head gasket so we, for sure, have 50% of that load sealing combustion,” said Golema. “You don’t want to leak that—it’s exploding and it’s hot. That way you’ll also have load left to maintain the seal for the oil and the coolant. If you waste all your available bolt load at sealing combustion, you’ll end up leaking coolant or oil. So the various grades of the stainless steel are that way in an effort to distribute that load evenly across the cylinder at the given amount of bolt load.
“Different grades of stainless steel are typically used,” continued Golema. “Some of those layers are just a spacer layer. So it may be .006 or .007 thick. Now you may have another layer that has two mechanical beads on it, or maybe four mechanical beads on it. Those mechanical beads are what does the load distribution. In addition, there are some layers that are folded upon themselves, in an effort to create, we’ll call it a double stack. So if that layer was .006, it overlays upon itself again, and makes that .012.”
Of course, much of this exotic, complex engineering is completely hidden from view. That’s not only because the layers of an MLS gasket are thin, and they’re welded or riveted together, but because they’re also typically coated over their entire surface. Like the layers that lie beneath, this coating gets vast amounts of thought put into it, too.
“The coating on an MLS gasket can almost be in somewhat of a fluid state,” said Hunter. “You can see on the MLS gasket after they’ve been clamped down and used. In some spots, there’s no coating left—it’s been scrubbed off. On other spots the coating is there, but it’s actually been pushed away. So it’s interesting to play with different coatings, because you have different levels of hardness, different viscosities, and different resistance to chemicals. That can help to get the clamp load exactly where we need it in the right amount so we can seal the most power, while also maintaining a solid fluid seal.”
MLS gaskets have become the de facto standard for most performance applications, and our sources say there’s still a lot of room for continued development with this technology. But alongside MLS gaskets, there’s still demand for copper head gaskets in motorsports, particularly for extreme applications.
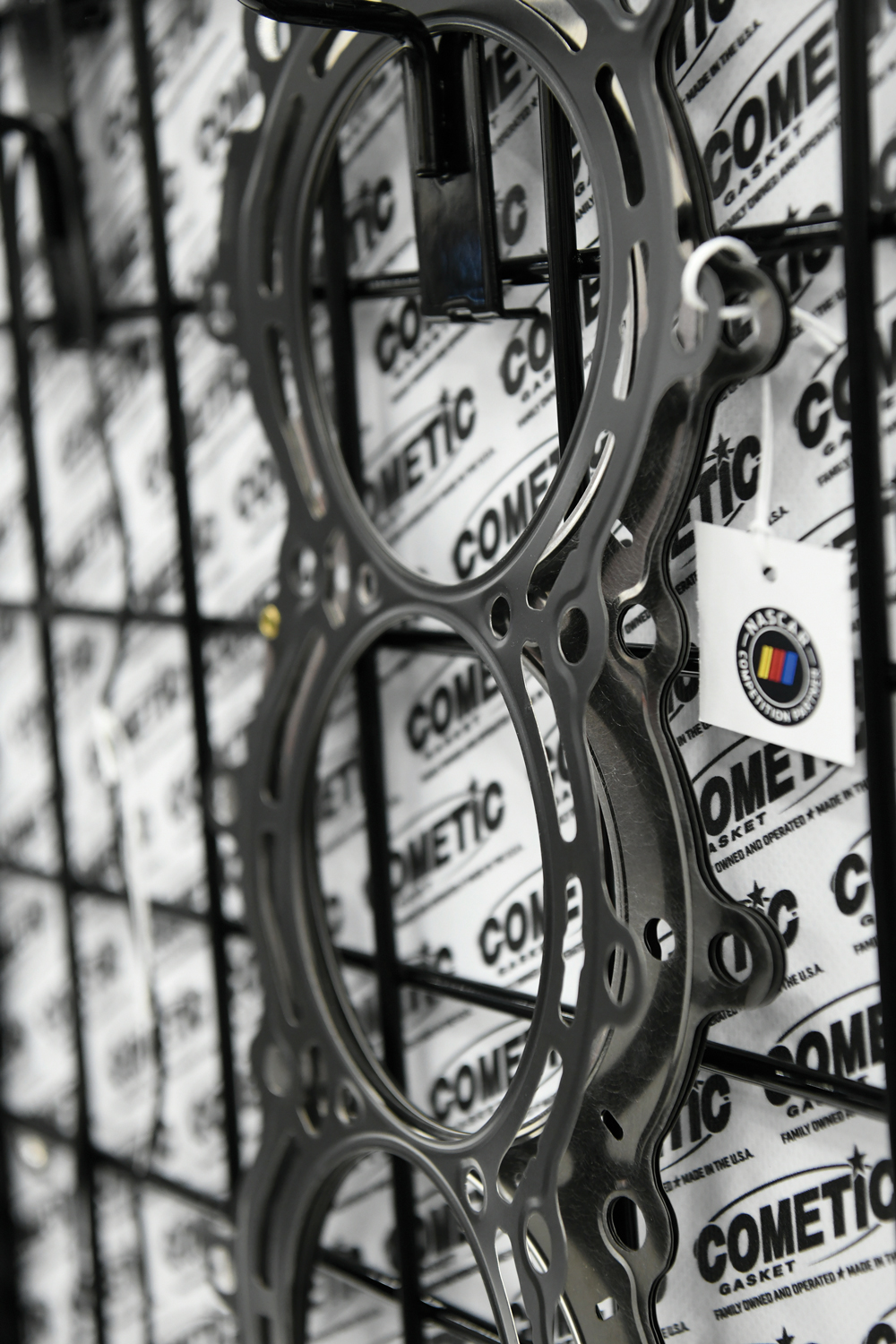
Copper head gaskets offer a unique combination of strength and malleability. This allows them to withstand brutal combustion-chamber pressures, while still being able to conform tightly to deck and cylinder head surfaces for good sealing. Copper head gaskets are also sold in a wide range of thicknesses, which allows racers to make relatively quick adjustments to the engine’s compression ratio simply by switching to a different gasket. In addition, copper head gaskets can also be reused, unlike other types of head gaskets, which are typically designed for one-time use.
Yet there are a number of disadvantages to copper head gaskets as well. One veteran supplier in the industry noted that he spends plenty of time talking potential customers out of using his copper head gaskets, simply because he doesn’t want the potential issues and backlash of dissatisfaction from customers who don’t know what they’re getting into with them. Foremost among copper gasket’s disadvantages is the additional machine work and prep required to run them; a groove must be machined into the deck around each cylinder bore to allow the use of an O-ring.
“Honestly, there are more disadvantages than advantages to copper head gaskets nowadays,” said Richard “JR” Clark of Clark Copper Head Gaskets, Blaine, Minnesota. “You wouldn’t really want to run copper on the street. Besides the fact that you have to have an O-ring and a receiver groove on the deck, copper is also very temperamental toward water. So you can’t run as much water pressure. The other thing with copper is it isn’t going to take up the little voids other kinds of gaskets will. So you’ve got to have a pretty flat surface to get it to seal properly.”
That’s not to say that copper head gaskets don’t have their place. Copper is ideally suited to the harsh environments such engines are routinely subjected to in the most extreme forms of motorsports. “There’s still a very large demand for copper head gaskets,” said Clark. “Mostly in tractor pullers, or in drag racing, for fuel cars.”
New Ideas for Old Challenges
Although head gaskets face the toughest demands of any gasket in a vehicle, engineers and manufacturers aren’t ignoring the rest of the engine. For instance, a failed oil-pan gasket probably won’t cause the immediate destruction of an engine like a head gasket can, but it can still sideline a car in certain situations.
One way manufacturers are preventing such problems is with one-piece gaskets. Many classic engine designs that are still being modified and raced extensively today were originally designed with multi-piece gaskets. These were difficult to seal completely even when the proper use of sealants and installation techniques were carefully heeded. Nowadays, racers generally prefer simpler, faster methods, so they’re increasingly receptive to single-piece gaskets designed to replace these trouble-prone legacy designs. “It’s just about using up-to-date technology to make these engines seal better. It makes a difference,” said Sergio Duarte of Flatout Gaskets, Mundelein, Illinois.
Although elastomeric materials made from silicone and other similar materials are becoming increasingly the norm, classic composite “paper” gaskets are still used in many applications, and the technology continues to be developed. “Composite gasket material is still a very relevant material,” said Hunter. “For lack of a better term, it’s called a ‘paper’ gasket material. But it’s not paper. It’s actually full of all sorts of really sophisticated technology. There’s a whole recipe for each and every material blend, and it all depends on what you’re trying to achieve.”
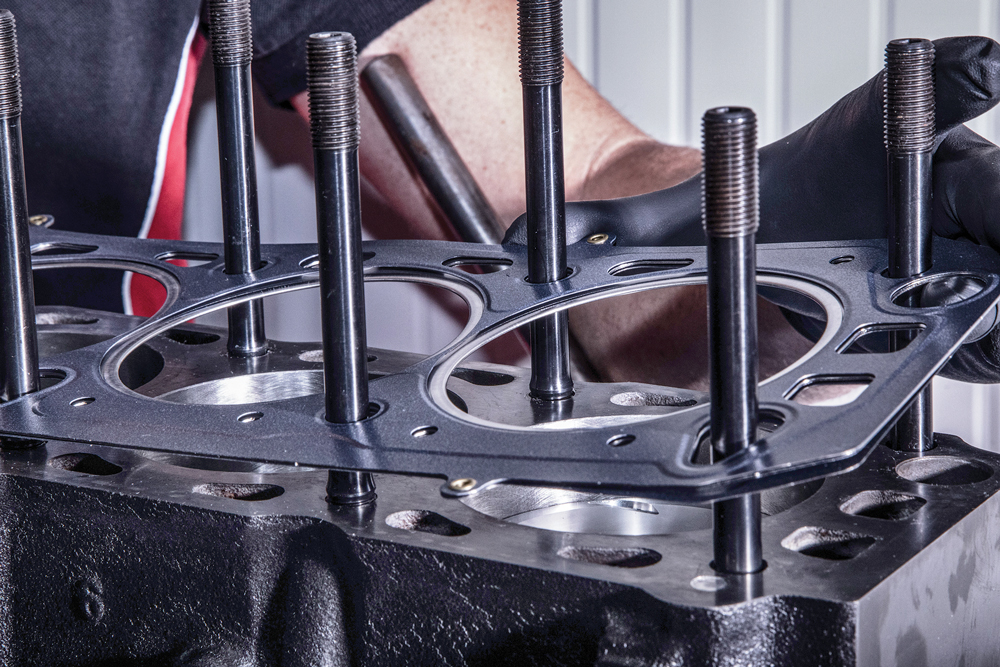
Many of the developments in all types of gasket materials come from OE manufacturers. With the billions of dollars they collectively spend on engineering and development, gasket technologies have improved considerably thanks to their work. The performance aftermarket often builds upon these designs, improving them or borrowing and reappropriating them to other applications. “The OEs are teaching us,” said Hunter. “And it’s not wrong, because they have R&D budgets that are way larger than the biggest gasket suppliers.”
Nonetheless, two aspects in particular of OE gasket designs are largely shunned by racers and the gasket manufacturers that supply them—built-in gaskets and factory engines that are ‘glued’ together with liquid sealers instead of gaskets. Although these make sense for bottom-line-obsessed automakers, they don’t work well for performance applications, in which users need to disassemble and reassemble engines with complete confidence that parts will stay sealed.
“Gaskets make the engine serviceable in a friendly manner,” said Hunter. “When stuff is glued on, you’re sitting there working with a razor blade, shaving stuff off. And you’re probably gouging the surface. At the same time, you’re so focused on what you’re trying to clean off the surface that you’re not paying attention to what you clean off. You can end up putting debris, including metal shavings, down into the crankcase or the timing area, which should be a cleanroom environment.”
At the same time, better components are increasingly being used by racers, according to our sources, which is greatly improving the sealing of engines in general. Although flimsy, thin stamped-metal components are still used by some racers, the poor sealing surface and inconsistent shapes are relegating them to stock restorations, for the most part.
“You see a lot of guys are going to a higher quality oil pan material now, whether it’s a cast aluminum pan or it’s got a nice, thick, welded flange,” said Hunter. “I’m a fan of that. It means my gaskets are going to seal, and people will quit blaming the gasket for leaking on an oil pan that’s been put on 30 or 40 times and over-torqued each time, to where the bolt hole is all stretched out and it doesn’t distribute clamp load properly.”
Keeping up with what’s happening in the field is said to be one of the vital keys to developing gasket materials and designs more effectively. Manufacturers continually work closely with engine builders and racers to get their input. Although this tends to be done with an eye on developing parts that have the potential for high production numbers, engines of all types are of interest to gasket manufacturers, as they seek to learn the nuances of different powerplants and the needs of the racers who field them.
One important aspect of these partnerships is the ability to examine used gaskets after engine builders or racers are done with them. This post-mortem investigation can yield vital information regarding the performance gasket materials and where they can be improved.
“We ask for gaskets back so we can take a look at them,” said Hunter. “Because a lot of these performance guys, especially street performance, burn up pistons all the time. Some of those used gaskets are in perfectly fine condition and they performed well. But it’s still very interesting to look at the gasket, study it, and ask, ‘What happened here? Can we improve on it? Is it doing everything we expected it to do? Are we satisfied with its performance?’”
Whether it’s a relatively simple valve-cover gasket or the endlessly complex head gasket that resides just inches away from it, gaskets are an unseen world that many racers take for granted. The fact that these unsung components work as well as they do is a testament to the vast amount of engineering, study, and thought that goes into their design. Much of that starts with the materials they’re made from.
SOURCES
Clark Copper Head Gaskets
clarkcoppergaskets.com
Flatout Gaskets
flatoutgroup.com
MAHLE Aftermarket
mahle-aftermarket.com
SCE Gaskets
scegaskets.com