The Coating Question

Photo Courtesy of Tech Line Coatings
As parts-coating types proliferate, what kind of real-world benefits can racers expect from these treatments?
“Coatings have grown up.”
That’s how Richard Tucker of Swain Tech Coatings, Scottsville, New York, summed up the current state of the coatings industry compared to, say, 20 years ago. “Folks who oversold what they could do, or who didn’t apply the right coating to the right application have fallen by the wayside on a large scale. There still could be coatings that will be misapplied or over-promoted, but it’s not part of mainstream coating anymore.”
In other words, the old myths surrounding coatings are mostly gone. “Don’t dismiss it as snake oil until you try it,” said Jason Arbogast of Tech Line Coatings, Rutledge, Tennessee. “There is science behind it. There is data behind it. There are a lot of guys using coatings that you may not think are using them, but that is why their stuff is holding together and working. And they may not tell you that.”
Any concerns that engine builders and race teams may have about coatings these days will have more to do with their proliferation than their performance. “People don’t understand what this myriad of coatings is capable of doing,” said Carl Benton of PolyDyn Performance Coatings, Houston, Texas.
“The gap that we see, from an end user’s point of view, is that it can be hard to tell the difference among coatings and suppliers, why one may work better than another,” said Carrie DiMarzio of Industrial Hard Carbon (IHC), Denver, North Carolina.
There also can be a tendency of end users to view coatings as some sort of magic bullet, that “if a coating was applied to any surface, it would improve that surface or system,” said IHC’s Gokhan Yildiz.
That’s why IHC, and other companies that contributed to this story, spend time educating their customers as to the realistic benefits they can expect from coating performance parts. “We’re not just a coating supplier, we are a solution provider,” said DiMarzio. “It’s not, ‘Do we use coatings?’ It’s, ‘How do we use coatings?’ Where in the system is the coating used? How do we design a system using coatings? Because everything is a system.”
What follows is a deeper dive into how engine builders and racers can best use coatings, and what they can realistically expect from coated parts.
Basic Properties
The variety of coatings available to racers goes far beyond the oft-used lubricants and thermal barriers. There are coatings that attract oil and others that shed oil. Some coatings disperse heat, while others trap heat. There are dry film coatings, diamond-like coatings, hard-anodized coatings, polymer-based coatings, ceramic coatings, thin- and thick-film coatings, coatings with a jewel-like finish, and coatings that one manufacturer promotes as “ugly.”
There are single-purpose coatings, but there are also coatings that serve multiple purposes. “For instance, our thermal dispersant coating dispels heat, is oil shedding, and is corrosion resistant,” Arbogast said. “Guys will use that on connecting rods to keep heat out of the rods and help them last longer. That gives you more life expectancy in drag race applications, especially with aluminum rods.” That same coating can also be used “on water pumps, oil pans, valve covers, carbs, alternator housings and so on,” he added. “We have coatings that literally go from the carburetor to the oil pan. How far do you want to take your coatings?”

In some cases, a single component may receive several different coatings. “For example, different coatings can be applied to the head, stem, and tip of a valve depending on the specific engine design,” Yildiz said. “We have to consider environmental factors such as temperature and lubrication and look closely at the type of interactions present with the countersurfaces, the valve guide and seat, prior to providing a coating solution. For instance, the head of a valve can be coated with DLC [diamond-like carbon film], while the stem and tip are coated with CrN [chromium nitride].”
Go from the simplicity of a valve to a complex component like a turbocharger and the coating options grow even further, said Benton.
“On the hot side, which drives everything, putting on a ceramic coating that can tolerate the heat will hold more heat in the turbocharger, which will drive the compressor wheel better and protect the compressor wheel, so it doesn’t melt. We can protect the exhaust housing so it doesn’t turn into a rusty mess. We can do the same thing with the center section, coat it so it doesn’t turn into a ball of rust. We can do some really trick things with the compressor. If you put our PD-14 Silver on the inside of the compressor housing, it will flow 7%–9% more air because the coating alters the boundary layer of air.” (PolyDyn has also used PD-14 Silver on carburetors to achieve the same effect.)
When it comes to the turbocharger’s bearings, “because of the way my coating holds oil on the bushing bearings, they last and last,” Benton said. “When you keep the hydrostatic layer of oil in place, you have no friction at all, so the turbo spools like crazy.”
Line2Line Coatings of Clarkston, Michigan, offers abradable graphite coatings that are used to minimize running clearances between components. These are “thick, fuzzy, abradable coatings based on graphite and resins” that can be used to restore parts from pistons to oil pumps, explained Andy Suman. “We can build up components so they fit better than when they were new.” The graphite-based coating is applied thicker than traditional solid film lubricants, often creating a line-to-line fit at assembly. During initial operation, the coating safely hones itself to the ideal operational fit. The final geometry accounts for machining tolerances, assembly torque distortions, thermal expansion, and kinetic strains, because they are all present during the break-in. During the wear-in, tiny coating particles (mostly under 5 microns) are released into the oil. Suman said there is no need to change the oil after break-in, “but it could have a gray hue from the graphite. After the initial run-in, the wear stops, so future oil changes look normal.”
Fundamental Coatings
With so many options available, where does the selection process begin?
“People will ask, ‘If you were going to coat something in the motor, what would you start with?’” Benton said. “Pistons and bearings. Those would be the first two things, because if you’re going to hurt something in the motor, it’s usually one of those.”
Tucker called those “the fundamental coatings, like coating the rod main bearings with a lubricating coating as a backup form of lubrication for cold-start situations and oil starvation, or situations where your oil film can’t perform the role it’s intended to. With a more aggressive tune, when it’s more likely that a tuning error, or bad fuel, or something else could damage the piston from a heat standpoint, then you might consider adding a thermal barrier to the top of the piston.”

“We study each application very closely from a tribological standpoint,” Yildiz said, defining tribology as “the science of interacting surfaces in relative motion. If you have two surfaces or components that are in contact in a certain environment, you have a tribosystem.”
When IHC designs a coating, “these are the things we have to hone in on to provide a suitable coating for that specific tribosystem,” he said. “What is the substrate material of the two components that are in contact with each other, and how well are the surfaces prepared? What is the working temperature? Is it a dry or lubricated environment? Is it a high load or sliding application? Or both? There are lots of tweaks we can do, or that people can choose, keeping the goal in mind to serve the tribosystem as best as possible.”
Proper Prep
Other than coating choice, probably the most important—and sometimes overlooked—factor in a successful coating application is the preparation of the parts prior to coating. “It’s like painting a car,” Benton said. “When I talk about preparation, 85% of the time a part is in PolyDyn’s shop, it’s in preparation.”
Tech Line Coatings puts so much emphasis on proper pre-coating preparation that it has shifted its marketing focus almost exclusively to professional engine shops and away from retail and DIY enthusiasts, Arbogast said.
“A lot of engine builders put their stuff together in a clean room, take the time and make sure it’s right because with those guys, their name stands behind it,” he explained. “Like our name stands behind our coatings. We want it to go to a guy who’s going to put it on the right way.”
Surface preparation is critical, Yildiz added, because the thin film coatings that IHC applies are “typically 3 to 5 microns thick. Five microns is about 0.2 thousandths of an inch, a very minimal dimensional change to the component. If you have a component with certain surface roughness, or peaks and valleys on the surface, the coating is not going to cover those up or smooth the surface. Because it’s only 3 microns thick, it will conform to the surface.”
Those peaks and valleys can lead to what Yildiz called abrasive and/or third-body wear. “A rough surface can limit the frictional gains and wear-reducing properties the coatings are designed to provide and will act as an abrasive in most cases,” Yildiz explained. “That’s why we have to look at the mating surfaces at a microscopic level and, if necessary, take appropriate steps to improve the surface finish prior to applying coatings to ensure favorable results.”
Coating Appearance
“Guys have asked me for a particular coating because it looks the prettiest,” Arbogast said, “but it may not be right for their application.”
For the most part, our experts said, a coating’s appearance is not necessarily indicative of its performance.
“Sometimes, the materials used inside the coating don’t lend themselves to a high-gloss, high-luster finish,” Arbogast said. “We’re trying to make them prettier, but ours have been more function over form.” Tech Line Coatings’ CBC-1 and CBX piston-top coatings have, respectively, a chalky white and gray metallic finish. “CBX was made for combustion ratios of 12.5:1 and up and supercharged and nitrous applications,” he explained, “while CBC-1 was designed for 12.5:1 and lower.” Tech Line Coatings also offers a gold piston top coating “that a lot of customers want because it looks prettier, and it works well for 9.5, 10.5, sometimes 11:1 combustion applications.” The gold coating will work in engines with higher combustion ratios, “but it may not work as well, and you could lose the gold color.”

“We strive for perfection, because it’s better for the end user to see something that looks like jewelry or a piece of art,” said DiMarzio. “But the looks don’t tell you it’s great or bad. You want to understand the overall systems, the materials the film is deposited on, the compositional performance of the film being deposited, and how it’s going to benefit the application depending on temperature, wear, pressure, what it interacts with.”
“We actually promote our exhaust parts coating as an ugly coating,” said Swain Tech’s Tucker. “When it’s put in use it’s difficult to keep clean, because when it heats up it can get growths on the surface of the coating. There have also been times when the base metal of the exhaust can expand more than the layers of the coating can expand, and that can lead to a fracture of what tends to be the outermost layer of the coating.”
Not to worry, he said. “One of the reasons we put it on in multiple layers is it’s virtually impossible to get all of the layers off,” added Tucker. “And even if you fracture the outermost layers, the remaining layers are more insulated than the coatings that are primarily put on the exhaust parts to improve their look.”
“The beautiful looking, polished ceramic exhaust coating holds the heat inside like it’s supposed to,” Arbogast noted, “but it’s limited in its applications. The outside gloss can handle a surface temperature of up to 1,300 degrees. That’s fine on most applications, but when you start talking about something like a twin-turbo diesel, which is going to put a huge amount of exhaust heat in there, you’re going to lose the finish. The coating is still on the part, but it just doesn’t look as good as it did.” To help slow and even prevent that from happening, he recommended putting a base layer of coating on the exhaust that can withstand higher temperatures and following it with an attractive top coat.
Meeting Expectations
There are so many variables in how race engines (or transmissions, differentials, or other components that can be coated) are built and used that quantifying the benefits of coatings in an exact way is difficult. No one can say, for example, that an engine with coated bearings will make X number of drag strip passes before teardown compared to one with uncoated bearings. Or that the friction losses from coating piston skirts will result in an increase of X horsepower.
In fact, said Tucker, “as we have gone from primarily carbureted motors to fuel-injected motors with electronic management, it’s much harder to get power gains by just doing the coatings. Management systems are so effective at maximizing and getting real information in real time. With a carburetor it was much more blind, so it was pretty common to see a noticeable power increase by coating combustion chambers or piston tops.”
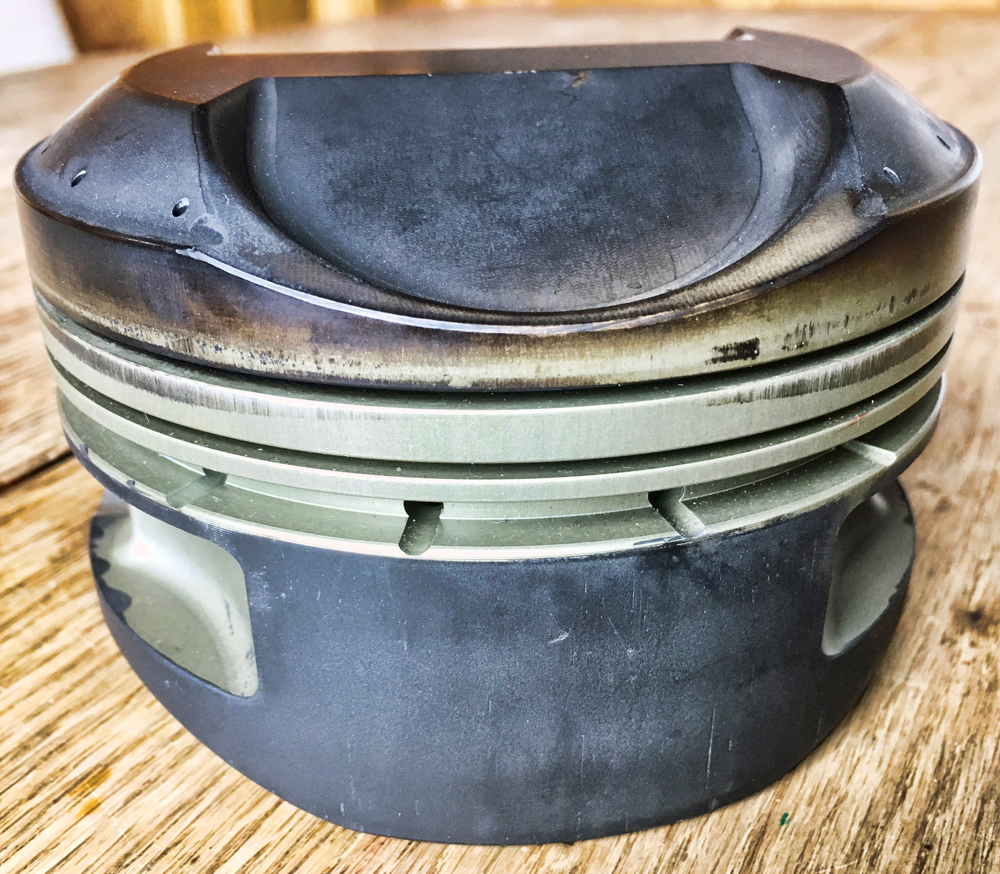
Instead, at Swain Tech, “we’re primarily talking to people about adding a measure of protection in case there’s a tuning error,” Tucker continued. “In the racing world you’re often tuning noticeably closer to the edge of what the parts can take than you would on a street application. When they are adding more power, running the motor under heavy loads for long periods of time, or there are inherent challenges to the motor in general, it makes more sense to add those coatings.”
“What some people don’t realize about coatings,” Arbogast explained, “is that to truly see performance advantages from the coatings, the engine needs to be re-tuned after coating. We’ve had a couple customers call and say, ‘I just spent a lot of money coating all my stuff in the motor, and I can’t see a difference.’ We will then ask, ‘Did you retune it? Readjust your fuel? Readjust your ignition system? Readjust your timing? If not, you’re not going to see those differences.’ By coating the parts, they will last longer, but to get the full benefit, it will take some adjustments to the engine.”
Coating companies may not make sweeping generalizations about horsepower and durability gains, but there are plenty of anecdotal examples of the benefits of these products.
PolyDyn’s Benton said he found using an oil-shedding polymer to coat the crankshaft counterweights in a wet-sump Chevrolet 350 engine—“there’s like gazillions of them in roundy-round cars, right?”—was worth 14 to 16 horsepower above 4,000 rpm. “A coated-up motor comes off the corner like gangbusters, and it also rpm’s smoother.”
When he and his son were racing a NASCAR Late Model with a Windsor engine, Benton coated the car’s transmission and quick-change rearend. As a result, “it only lost 15 horsepower from the flywheel to the tire. When you go out there with that kind of advantage, and you tell your driver that you have a secret weapon, for some reason they drive harder and they’re unstoppable.”
The benefit of Line2Line’s clearance-control coatings is that “everything lasts longer if it’s not rattling,” said Suman. “If it’s not rattling, it’s not piercing oil films, and your parts aren’t rubbing on each other. Pistons are our workhorse. We’ve seen people who would get 15 nights on a set of pistons now run 45 nights because the rattle is gone.”
Added Line2Line’s Mark Gelstein, “One of our customers had a brand-new gerotor oil pump that at idle or low rpm was making 20 to 22 pounds of pressure. We coated all the internals, and now it never drops below 55 pounds with that same hot, thin oil.”
Suman and Gelstein are proud of the fact that “we’re the guys at the PRI Trade Show with the table full of used parts,” Gelstein said. “We love showing off what a 3,000-horse blown alcohol Pro Mod piston that has 40 passes on it looks like. It looks like brand new.”
The most dramatic anecdote we heard came from Arbogast: “We got a chance to help out a local guy doing his drift car engine, a supercharged LS motor. We told him putting coatings on would give him a few more horsepower, manage heat better, and provide longevity for the parts, which was important for him, since while drifting, the car will see constant 6,000–7,000 rpm throughout the run.”
On his first event, while in the middle of a run, “the blower belt shredded, pulled off the boost reference gauge, and the motor went to a full lean condition at 6,000 rpm,” Arbogast continued. “But instead of detonating and blowing holes in the side of the block, the motor stayed together. Some of the parts were scorched inside, some of those bearings were squished, but he did not see the catastrophic failure that would have happened without the coatings. And because the pistons did not seize inside the block, and the bearings were not welded to the crank, he was able to pull the motor apart and put in new bearings, a couple of new rods, and some new pistons. The heads were salvageable, the valves were salvageable, and there was no hole in the side of the block. He was tickled to death.”
SOURCES
–
Calico Technologies
calicocatings.com
Industrial Hard Carbon
industrialhardcarbon.com
Line2Line Coatings
line2linecoatings.com
PolyDyn Performance Coatings
polydyn.com
Swain Tech Coatings
swaintech.com
Tech Line Coatings
techlinecoatings.com