Permission To Speed
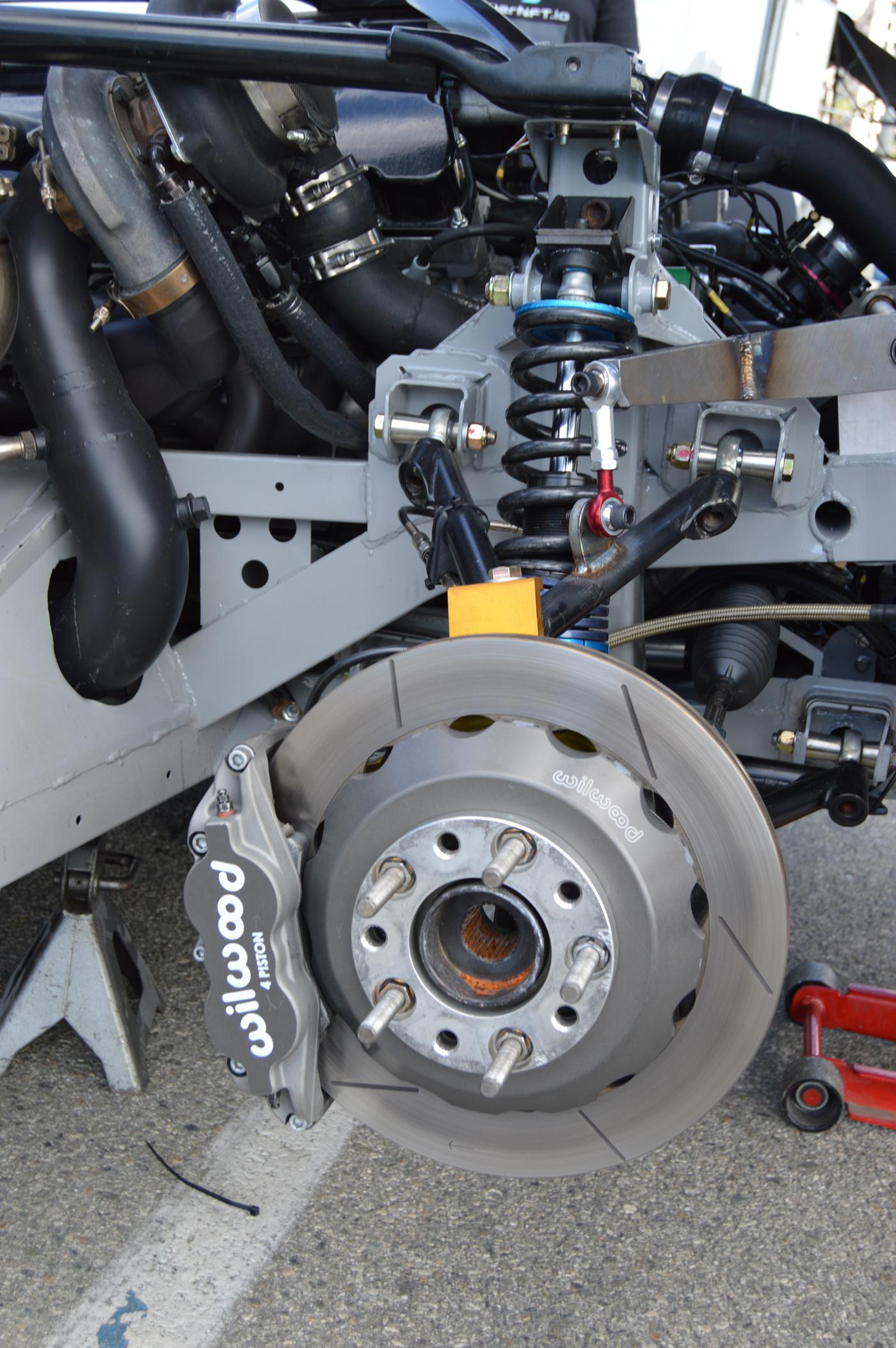
From new materials to advanced computer simulations, the science of brake systems continues to evolve and expand, as part of a never-ending cycle in which these components react to increased speeds and contribute to those speeds going even higher.
Brakes are speed. While the rest of the world thinks of these vital components only as a way to slow down and stop, racers in most forms of motorsports also see them as a means of steering, transferring weight, and driving harder into corners. But what constitutes the ideal race-car brake system inevitably changes over time. New technologies, experimental setups, advanced materials, and revolutionary data systems are being applied to brake system development, bringing racers a range of options that are more effective than ever.
To get a handle on the latest developments in brake systems and components, we talked to leading manufacturers and suppliers. They gave us a deeply nuanced view of brakes, the science behind them, and what that means for racers.
The Big Picture
One trend, more than perhaps any other, that has contributed to brake system development is that today’s street cars carry much more weight and far more power. This is particularly the case with production-based vehicles since many OEM performance-car platforms now tip the scale at well over two tons. At the same time, these behemoth machines are often making 500-plus horsepower right off the showroom floor, with modified cars routinely exceeding 1,000 hp. This combination of hefty mass and brutally strong power places extreme demands on brake systems.
“Many race cars are following the same trend that street cars are following—heavier and faster,” said Paul Rankin of PFC Brakes, Clover, South Carolina. “This increases braking demand, so we are always looking at how to mitigate the heat most effectively. It’s necessary to keep calipers and disc hats/disc bells cool, so we’re designing in thermal barriers when necessary to help keep the heat in the disc, which is the primary heat sink of a braking system. But then we need to effectively manage the heat in the disc to help get it out of the system to keep the pads and discs in their optimal thermal window, so we don’t see reduced performance or other thermal incidents. All of this must be accomplished without excess weight or too much system compliance, so it can be a delicate balance.”
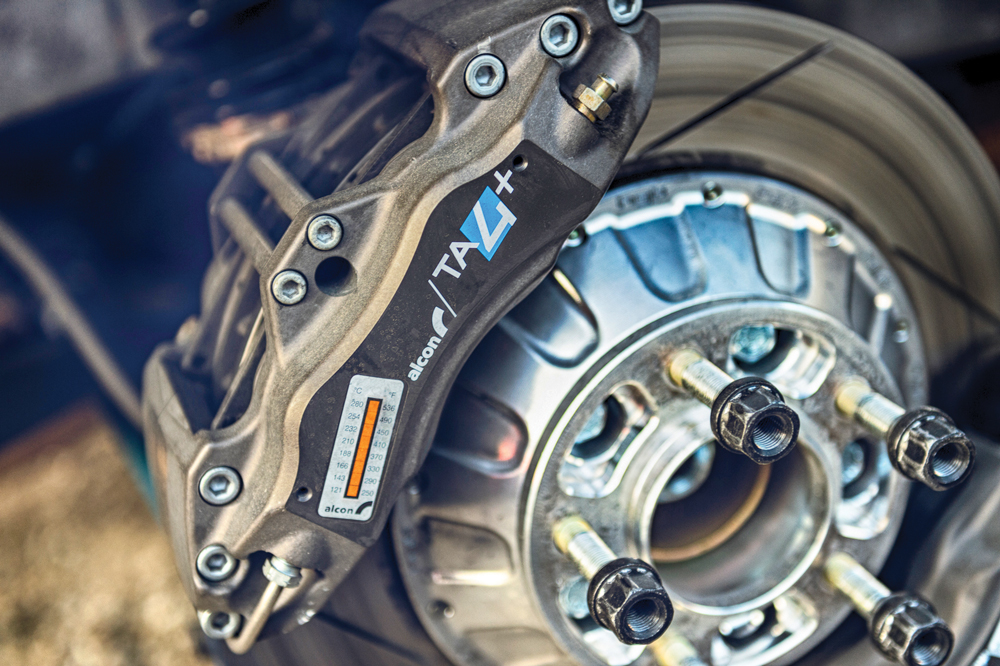
Manufacturers have also responded to this trend by producing new pads, with compounds that are better suited to quickly bring fast, heavy cars down from high velocities. “For years, our DTC-70 was our highest torque, highest temperature pad,” said Edwin Mangune of Hawk Performance, Medina, Ohio. “But because race cars are making more power and are heavier, we realized we needed more brake torque than we currently had. So we produced our DTC-80, and now that’s very successful.”
In the quest to improve performance and respond to racers’ continual needs for more effective brakes, manufacturers constantly look for new materials that can do the job better. “There are always new materials to evaluate for any aspect of a brake system,” said Rankin. “For aluminum components such as calipers or disc hats and disc bells, there’s always a search for lighter and stiffer materials that can handle the thermal and mechanical stress. On brake discs, the iron can be tweaked with different alloys to tune the rotor properties for the environment which they will be subjected to.”
In many cases, brake-system development is a collaborative process between brake manufacturers and racers. Such efforts typically begin as a theory based on observations and measurements. That can start with racers asking manufacturers to develop parts based on new ideas, or by manufacturers going to racers and asking them to try a new setup.
“A good example is a few years ago in NASA Spec E30,” said Mangune. “Everyone was running our DTC-60 pad on the front axle and then our DTC-30 pads on the rear axle, so it was a staggered fitment, with the high-torque pad on the front. But after doing some testing with one of the regulars in that class and monitoring rotor temperatures, we felt he could use a higher torque pad on the rear. So we installed our DTC-70 pads on the rear, which is about a half a step more brake torque than what the DTC-60 offers up front. And it made a big difference. Now, I don’t think anybody uses the old combination anymore with DTC-30s on the rear axle.”
New Markets
Like any other business, brake component manufacturers are always on the lookout for new markets. With the constant ebb and flow of different types of motorsports in America, that tends to be a moving target.
Endurance racing has proven to be one of the healthiest markets for brake manufacturers in recent times, and all of the sources we spoke to point to it as an area of significant growth. The popularity of these series has opened up new possibilities for brake manufacturers, which are generally embracing the segment with open arms and bringing new technical developments to it. Foremost among the new brake products being made for endurance racing are advanced pads designed to withstand the rigors of long events, without requiring excessive brake-pad changeouts.
Traditionally, the US road race market focused on sprint racing, according to Mangune. “But in the last several years, endurance racing has become popular. So we developed our latest release, our ER-1 endurance race pad. We formulated it for grassroots endurance series, like ChampCar and Lucky Dog.”
While the need for longer-lasting pads is obvious in all types of endurance racing, this can come with tradeoffs. In particular, the traditional compromise with endurance pads is that they tend to gain longevity at the expense of initial bite. This typically requires pads to get several laps in them before they work effectively, requiring significant alteration in braking technique early in races.
Now, however, that’s proving to be less the case, as manufacturers are finding ways to create brake pads that last for 12 hours or more while still having good initial bite. “When I was working with drivers on our ER-1 endurance pads, I told them to take it easy for the first lap or two because I didn’t know how this pad comes on,” said Mangune. “I had the dyno data, but that can be different in a real-world scenario. But when the drivers came back, they told me, ‘These pads came on so strong that I just got on them right away.’”
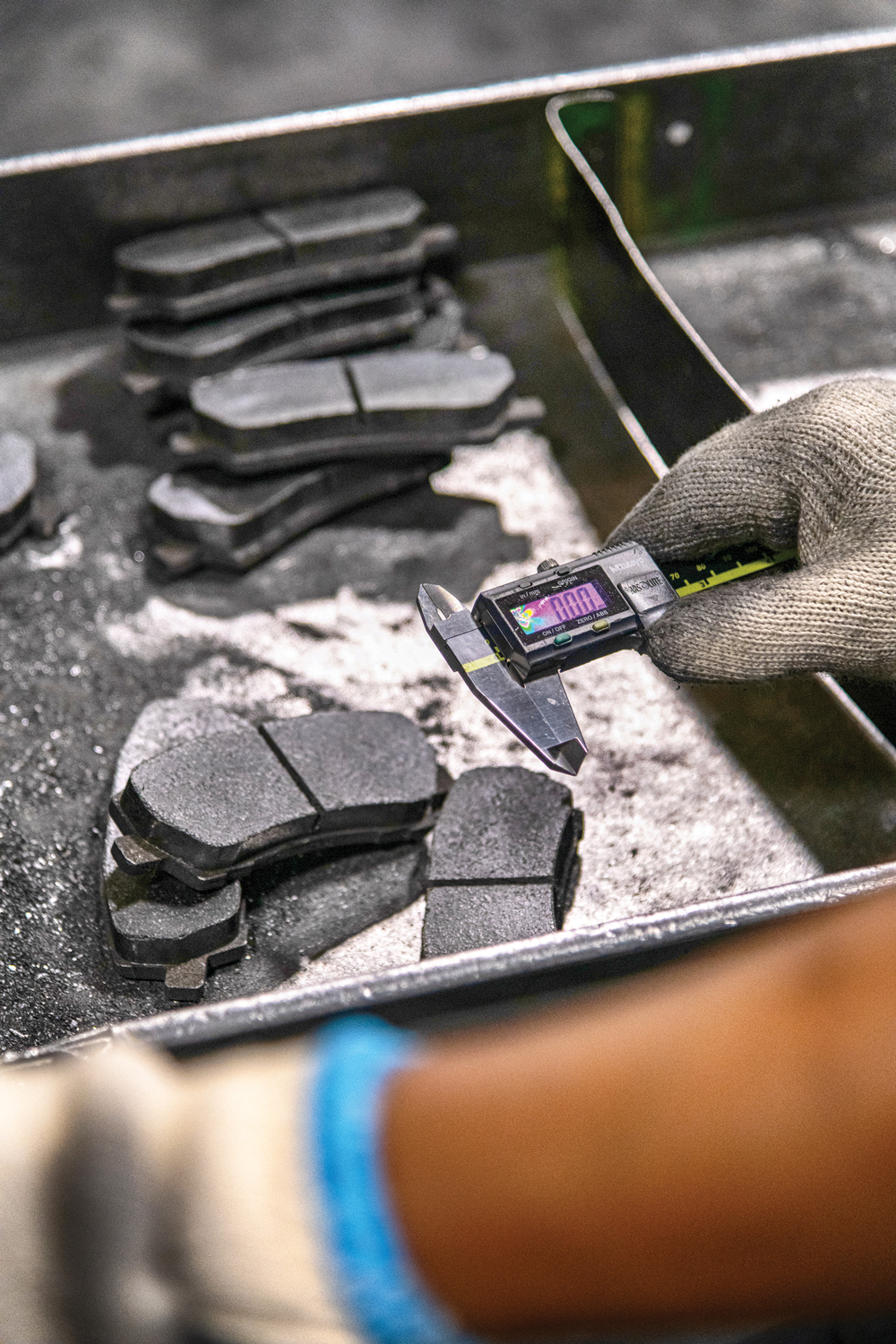
Along with the developments in pad compounds, one of the most profound changes in endurance racing series has been the introduction of antilock braking systems (ABS). This has significantly altered the landscape of brake-system development. On the one hand, ABS has increased performance by giving racers relatively easy access to a much greater percentage of their car’s ultimate braking capability. But it also has brought unique engineering challenges that manufacturers continue to grapple with.
“With ABS, drivers are using more of the brake system through the apex of turns,” said Jim Emerson of PAGID Racing, Troy, Michigan. “In the old days, if you got a little bit of lock-up on the inside tire, you just backed off the brakes a little bit. But now they just drive it. So what happens is some of the less experienced drivers will just keep their foot to the floor and drive through the corner. But that means that the brake pad never comes off the disk—it never has a chance to breathe. So you have to be ready for thermal events over a period of time.”
In terms of specific endurance-racing series, one of our sources noted that World Racing League (WRL) in particular is creating vast opportunities for brake manufacturers. As one of the most popular endurance racing series in the US, WRL’s large number of participants, aggressive tires, and use of proven car platforms combine to make it an appealing market for brake manufacturers.
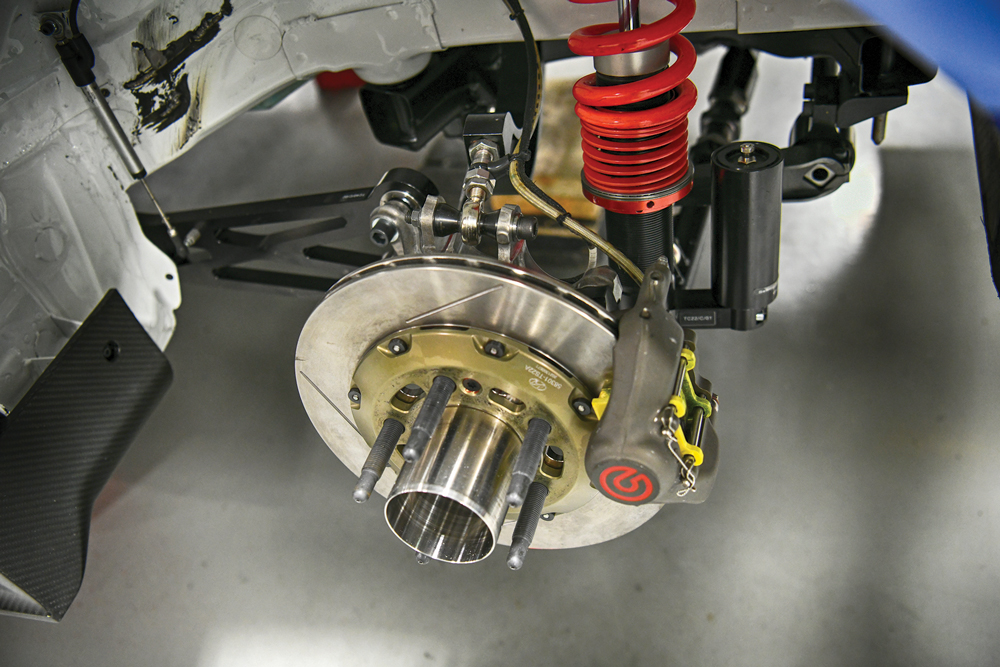
“What’s interesting about the WRL series is they’re on a 200-treadwear tire,” said Emerson. “They’re basically racing on slicks with treads. And because they run previous-generation cars, we have all the stuff. We have the tooling; we have the inventory already in the US. We know what works.”
One brake brand in particular is eyeing this and other similar grassroots series as a means of expanding market share beyond its established clientele in the upper echelons of motorsports. “Traditionally, Alcon is known for being in high-price, low-volume sectors,” said Phil Stubbs of Alcon/Pro-System, Mooresville, North Carolina. “Now we’re getting more and more involved with grassroots type series. We’re having a lot of success with that, be it road racing or oval track. We’ve developed some products specifically for those cars that are working really well.”
Along with more established forms of motorsports, all of the brake component suppliers we spoke to are keeping a close eye on the electric-vehicle market. That said, they differ in how they’re approaching this emerging sector. Some manufacturers are preparing to dive in, while others are holding back and waiting to see how the scene develops. Regardless, all EVs present unique technical challenges for brake system manufacturers.
“Depending on the power of regenerative braking and the budget of the race series, changes in EV brake systems can be minimal or substantial,” said Rankin. “If a vehicle has limited or no regenerative braking, the brake system will remain largely unchanged. Of course, the system must be appropriately sized for the speed, weight, and brake power demands of the specific vehicle. But as more regenerative braking is added to the race car, we can start downsizing discs on the axles that are doing the regeneration, since the thermal load will not be as significant.
“On the brake-apply side of the system, the pedal and master cylinder may no longer be directly connected, in what’s called a brake-by-wire system,” continued Rankin. “This allows for brake blending to occur, where the first part of the brake pedal stroke does not engage the friction brakes but instead activates the regenerative braking—up to a point. At a certain level, the friction brake will engage to assist the motor regeneration. This is all computer controlled and, if well-programmed, it’s imperceptible to the driver.”
Alcon has been extensively involved with EV racing and continues to support it. However, Stubbs noted significant drawbacks that could limit the motorsports potential of EVs. “I don’t think EVs really lend themselves particularly well to racing right now, with their limited battery life,” he said. “So we’re not seeing a huge demand yet. It will probably come in time. Still, I think it’s going to be a while before EV racing is widespread. But we’re definitely involved. We were involved early on with Formula E, and we’ve been involved with electric rallycross cars. And we’ve developed our own brake-by-wire system.”
Although road racing is perhaps the most obvious motorsports segment for brake-system manufacturers to target, appealing opportunities are also coming from the off-road market, according to our sources. In particular, the side-by-side market has come on strong recently, bringing with it new potential for brake system development and new products that complement it. “We’re getting heavily into the off-road market right now,” said Dave Brzozowski of Wilwood, Camarillo, California. “Side-by-sides have taken off like wildfire, so that’s really growing. Our biggest thing has been, of course, the calipers for them. And then we’ve added our lug drive rotor type system for those.”
Other brake companies are taking a collaborative approach in pursuing the off-road market, fostering unique synergies that benefit both companies. “Several years ago, when I was tasked with the off-road market, I piggybacked with chassis builders,” said Mangune. “I was looking for chassis builders to work with, and I found Jamar. At the time, they were one of the only ones that produced a full corner suspension that included the uprights and the brake system. For side-by-sides, they very recently did a full brake system that uses our pads.”
Increasing Sophistication
As all forms of motorsports become more sophisticated and complex, brake manufacturers are keeping pace. Today’s brake suppliers are increasingly taking a comprehensive view of their processes and their approach to problem solving. Among the many benefits of this are improved performance of products, greater cost competitiveness, and a wider range of components.
Alcon has shifted toward a systems approach instead of just focusing on individual components. This puts the company in charge of everything from pads to pedal box. OEM automakers favor this integrated-system approach, according to Stubbs. “We genuinely have control over the whole system,” he said, “so we can do a better job, and it’s a fully integrated package. Whether it’s for the Ford Mustang GT3 or Aston Martin GT3, manufacturers prefer to get as much as they can from one supplier. They know it all works together. Troubleshooting is a lot easier. And during testing and development, they only have one company to deal with—there’s no potential for finger pointing.”
Complementing this approach is the move to more extensive simulation and data collection in brake development. “In the GT market, a lot of it now is coming down to repeatable simulation,” said Emerson. “We’re doing a lot of that, verifying braking characteristics with our dyno simulations to reproduce certain key tracks globally—Spa, Sebring, Nürburgring. The great thing about our team is we’re so global that we have that ability to compare the results.”
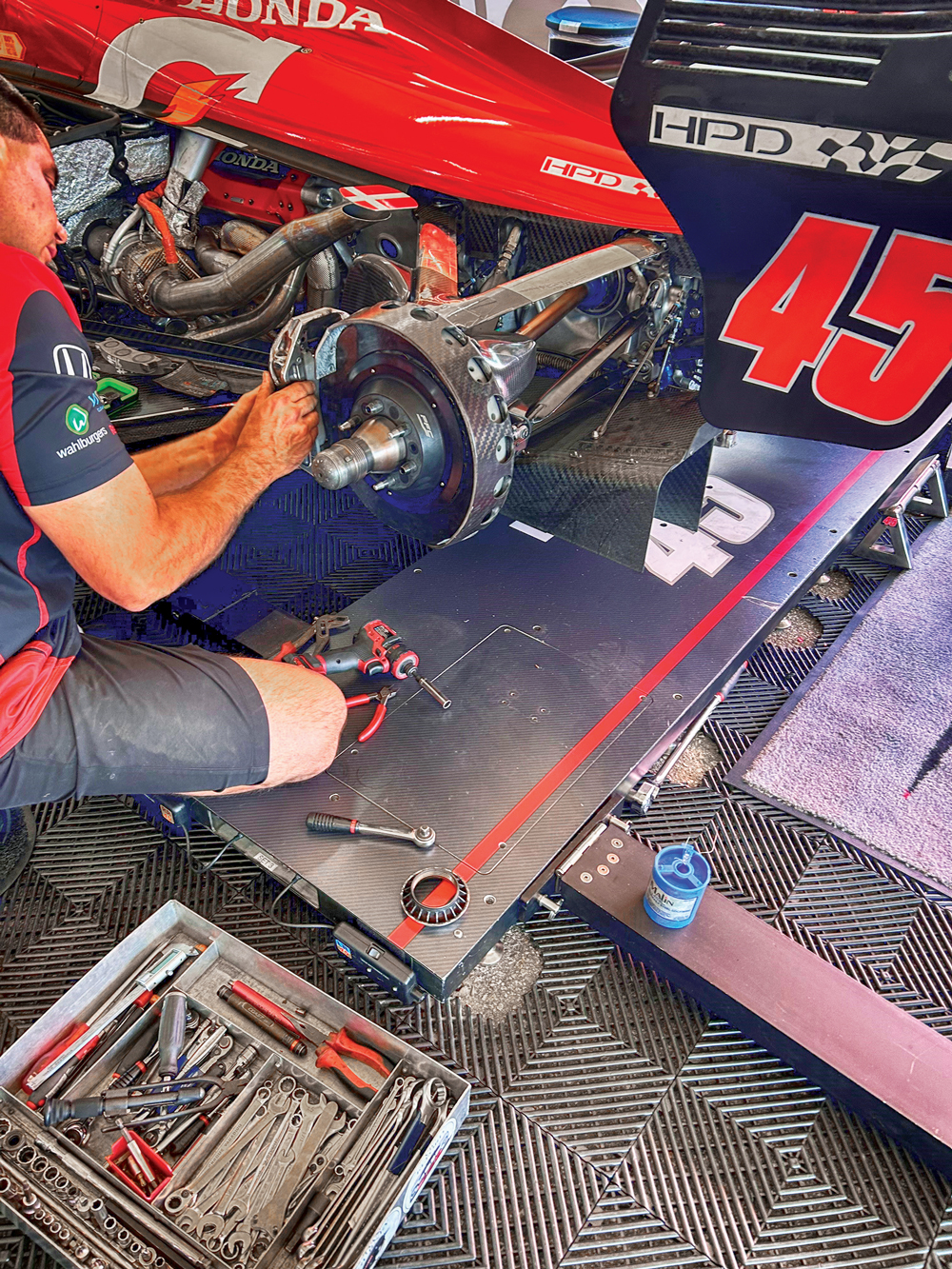
PFC is also doing extensive simulation and has developed a brake-rotor thermal simulation tool, which can predict rotor temperatures at any point on the track for any circuit used by IndyCar. At the same time, it can predict if changes to the car or brake system will affect brake rotor temperature. This has proven to be especially helpful with the carbon rotors and pads used in the series. “With carbon rotors and pads there’s a temperature window,” said Rankin. “If you aren’t in this window, performance can drop off, so our rotor thermal simulation tool is effective in keeping the rotors in the ideal range.”
For all this sophistication, our sources also pointed out that many motorsports market segments remain highly price sensitive. Manufacturers must walk a fine line between creating the most effective, competitive parts, and keeping them at a price their intended market is willing to pay. Because of this, the development process for brake components usually focuses on specific price points from the very start of the project.
One way manufacturers are keeping costs in check is by bringing as much of the manufacturing in-house as possible, thereby creating a more predictable flow of raw materials and limiting potential supply-chain challenges. “We do everything in-house,” said Brzozowski. “We’re in complete control. So we aren’t reliant on a lot of people, which is a game changer. We even went so far as bringing our anodizing in-house. We built our own type III anodizing facility, which isn’t an easy process.”
Another way brake manufacturers are controlling costs is by implementing design-for-manufacture processes, in which the design and development of components is driven from the start by how the part will be produced and what materials will go in it. This allows companies to maximize the inherent advantages of certain methods and materials, while minimizing the downsides.
“We’re very much moving toward design for manufacturing,” said Stubbs. “From the start, we’re designing to make the manufacturing process as efficient as possible. That might mean, for example, that we’re forging parts or casting them rather than machining them from solid billets. You can design the best, most exotic brake caliper, but if it’s difficult to make, then it’s not going to be very successful.”
Whether it’s in the form of new materials, new combinations of components, or the pursuit of new markets, manufacturers are forging promising developments in the science of braking. Regardless of where that journey takes them, the ultimate beneficiaries are racers, who get more choices of parts, improved components, and ultimately better results on track.
SOURCES
Alcon/Pro-System
alconusa.com
Hawk Performance
hawkperformance.com
PAGID Racing
pagidracing.com
PFC Brakes
pfcbrakes.com
Wilwood
wilwood.com