Power Hungry
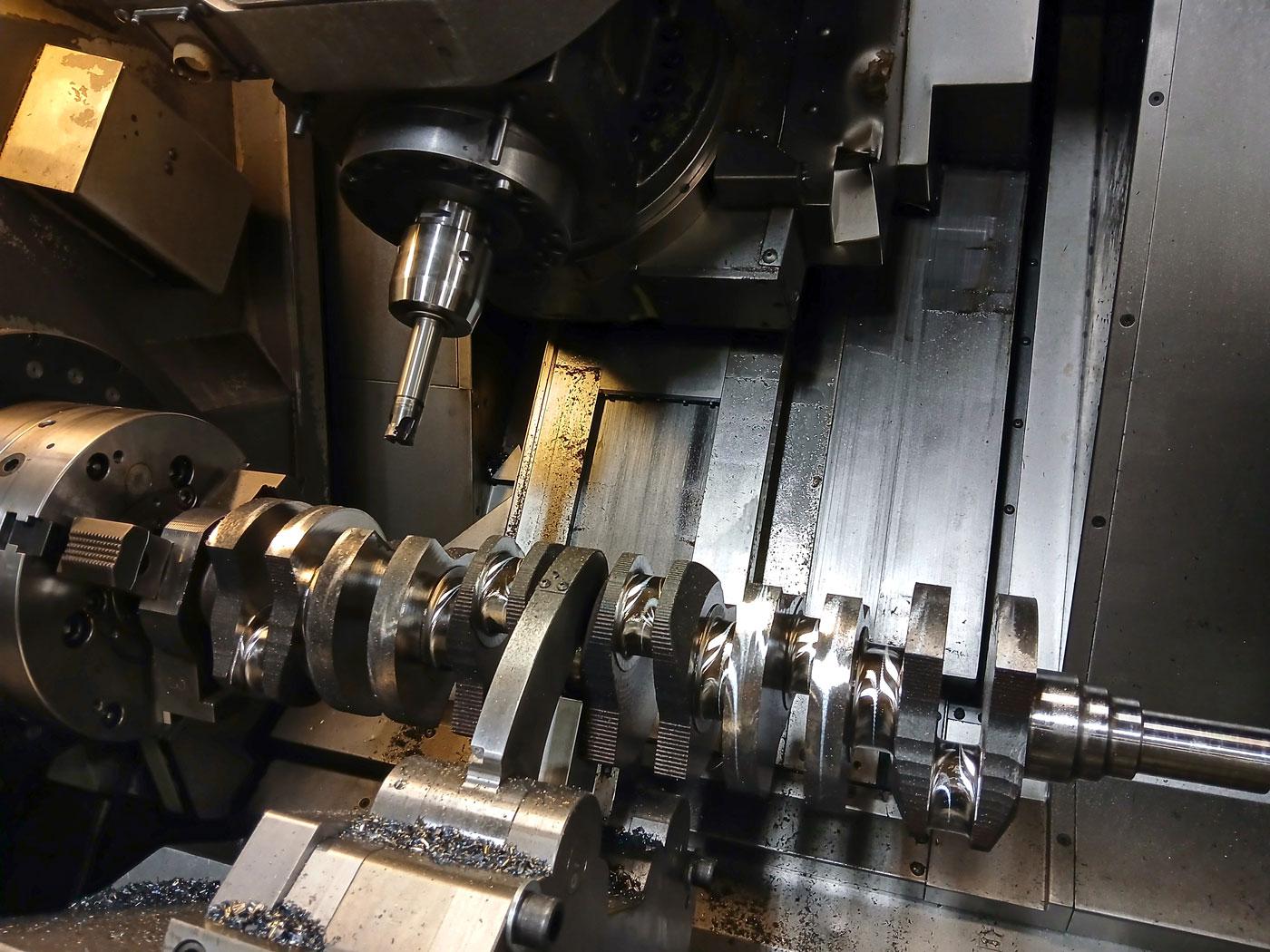
Photo courtesy of Callies Performance Products
As the loads on engine rotating assemblies increase with boost and higher-rpm capabilities, crankshaft manufacturers are responding with stronger products.
Crankshafts, especially custom units, are more robust these days, and there’s a simple explanation.
“One-thousand horsepower used to be a lot. Now, we are hearing 2,000 horsepower more and more,” said Alan Davis of Eagle Specialty Products, Southaven, Mississippi. “Customers need crankshafts that can be the backbone of that kind of powerhouse. Center counterweights play a big role in crankshaft stability and strength at extreme power levels. We are developing more crankshafts with center counterweight designs.”
“Mostly we’re reacting to the needs of the market, and specifically our customers,” added Trip Manley of Manley Performance Products, Lakewood, New Jersey.
Demand for performance parts has yet to soften following the surge in engine building during the pandemic. Manufacturers are now looking at making changes in their manufacturing operations to keep up with customer orders.
“It’s been a lengthy project of making the manufacturing side more efficient,” said Nick Norris of Callies Performance Products, Fostoria, Ohio. “As part of that move, we’ve backed away from some new introductions at the moment.”
Other companies are developing new product. They just can’t talk about it.
“We’re looking at doing some exotic material Duramax cranks,” said Kirk Peters of Howards Cams, Oshkosh, Wisconsin. “What does that mean at this point? It’s hard to say. I can say it will be billet, not forged.”
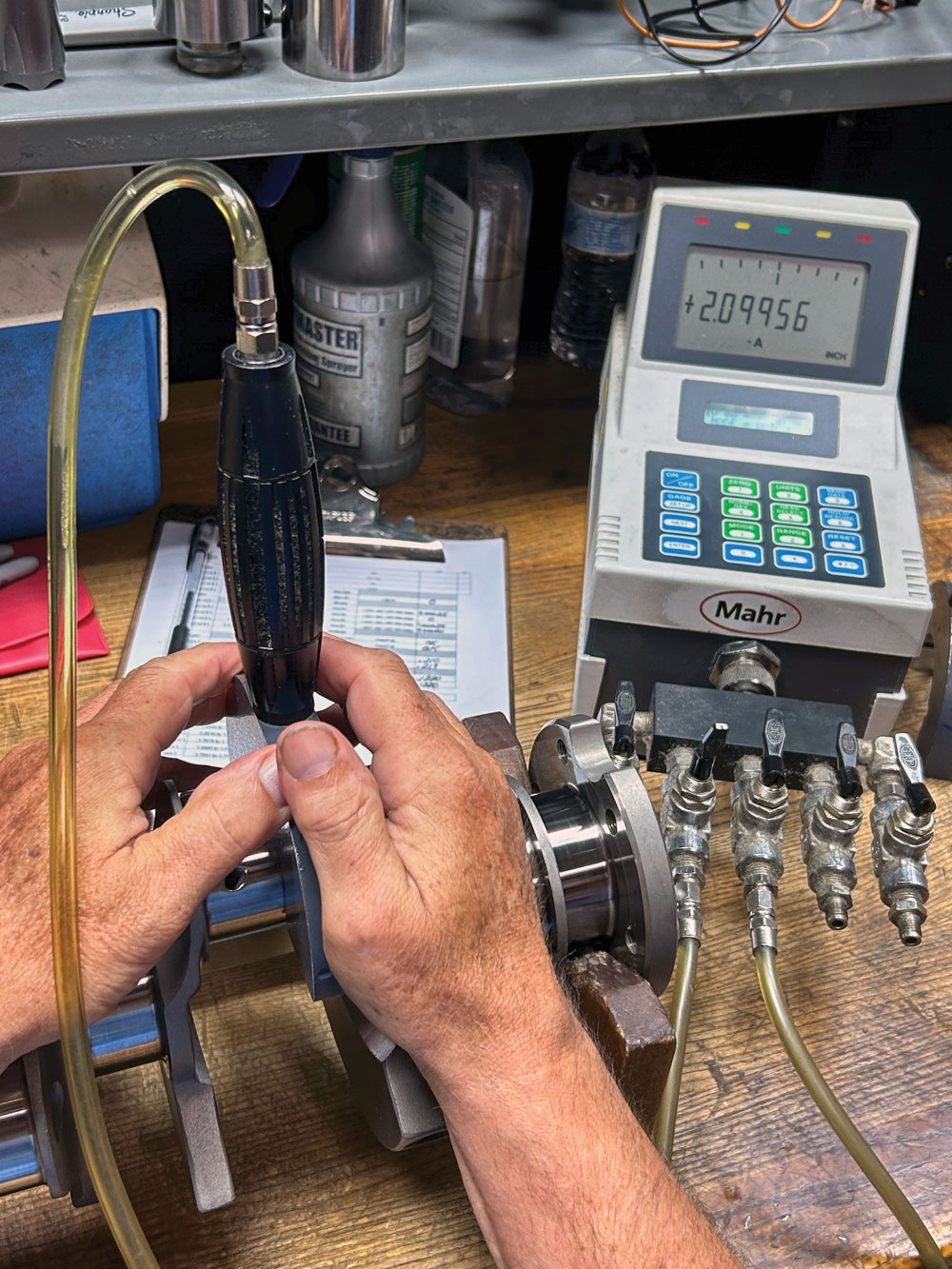
“We’re expanding our billet line,” concurred Tom Molnar of Molnar Technologies, Kentwood, Michigan, adding that the demand for center-counterweight cranks is driving the development. “There are a lot of people who think you need an eight-counterweight crank. In some cases you do. In some cases you don’t.”
Over at Crower, which is based in San Diego, California, there have been some supply problems with acquiring US-made raw forgings. Officials also say heat-treating is taking longer due to labor issues where the process is sourced, and utility prices are challenging. But the dirt late model market is keeping the company busy.
“The small block, 4.500-inch bore center applications—we can’t seem to make enough of those,” said Peter Harris, noting that there were no engineering challenges to designing a crank for the wider bore centers. “Just understanding what the customer wants. They always want the ultimate strength and also light weight. We don’t make them in different weights. We make only one crank for the application. It’s a lightweight billet, center counterweight. But they have to be very strong because of the number of laps on them.”
The number of racers ordering custom crankshafts continues to grow. The debate over which is stronger—billet or forged—will always be spirited. The main reasons that billet is often preferred is flexibility in design. Counterweights can be shaped and located as desired, whereas a forging has limitations in the machining and finishing stages.
“The ratio of billet versus forged has gone higher,” said Norris. “Part of it, I would say, is there are certain forgings that haven’t been updated to eight counterweights. Behind that is the unreasonable cost of changing a forging die to that level. We’re talking six figures to update. At this point, it’s easier to make the billet cranks.”
Computer Simulations
Crankshafts are a specialty at Pankl, which is based in Austria. The company offers clean-sheet design and simulation capabilities for high-end projects and can include connecting rod and piston development in the same program. The customer first sets down the basic requirements including target weight, loads, and packaging considerations.
“We probably start with $10,000 worth of design work just based on experience,” said Christoph Wachmann. “First, you do a fatigue simulation to look into the safety factors in critical positions of the crankshaft, and you do this with a dynamic calculation.”
Wachmann said that anticipated cylinder-block flex must also be included in the analysis. “For NASCAR, it would be a cast-iron block. In other race cars, it would usually be aluminum. So you take into account the deformation of the whole engine and then do an EHD [elastohydrodynamic bearing calculation], where you look into the main and rod bearings. This is assuming that you know the boundaries for the oil viscosities, speeds, and pressures.”
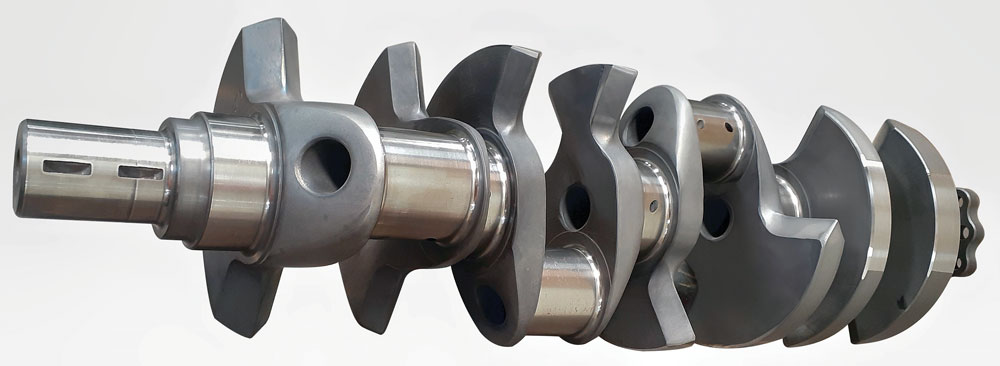
With all the relevant parameters in play, the computer simulation programs can calculate main bearing and rod bearing wear, oil-film thickness, and shear forces. “That’s a quite complex dynamics calculation that is also costly. You easily end up with $150,000 to $200,000 of just crankshaft simulation on the design side,” said Wachmann.
Friction calculations are becoming more important in crankshaft design. For example, a NASCAR superspeedway engine has a very low gradient of rpm change. The driver basically keeps the engine at WOT in high gear around a 2.5-mile track.
“So weight is not the most important factor, but friction is. How can you reduce the friction losses in this engine? In most cases, that has to do with stiffness,” said Wachmann. “You already have a stiff cast-iron block. We learned about 15 years ago in NASCAR that you can’t squeeze all the weight out of a crankshaft because it will start wobbling more, and you’ll have more frictional losses in the bearings.”
Extreme lightweight crankshafts are starting to lose favor with engine builders. There are some race classes where total engine weight may be more important than losing a couple horsepower to friction. Lightweight designs cannot compromise on durability, and many more race classes are demanding that engines live longer to reduce overall program costs.
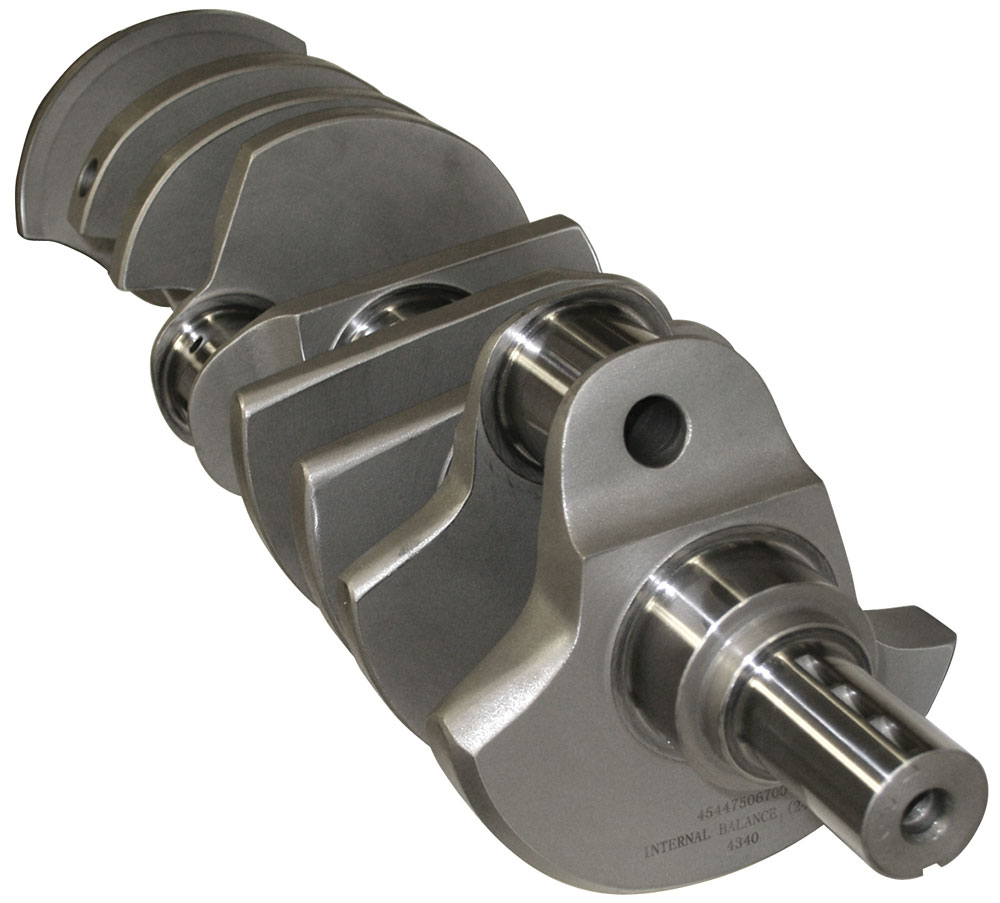
“It comes down to choosing the material and nitriding depths,” said Wachmann. “In Formula 1, where you have a 10-million cycle requirement, or Le Mans endurance racing, people have started to go with very high nitriding depths. I’ve seen crankshafts going close to 1 mm of nitriding depth. That means, depending on the material, that the crankshaft would stay in the nitriding oven for 200 hours.”
Creative Approaches
As noted earlier, the manufacturing side is seeing changes. Callies is revamping the early stages of the production line that includes bringing in new equipment.
“We’ve taken a whole different approach to how we’re making parts from start to finish,” said Norris. “We’ve been making crankshafts for a long time, and we’ve made them the same way. We have some younger, different-thinking people in the production department. They’re changing some things, and some of them are showing improvement. Some aren’t, and that’s okay. If we don’t try, we don’t figure it out.”
With the increasing popularity of eight-counterweight crankshafts, sometimes the manufacturing department has to get a little creative when producing a forged crankshaft. There are two ways to manufacture a forged crankshaft. First is the twist method, where the rod journals and counterweights are forged flat in the dies, then the forging is reheated and twisted to position the rod journals and counterweights.
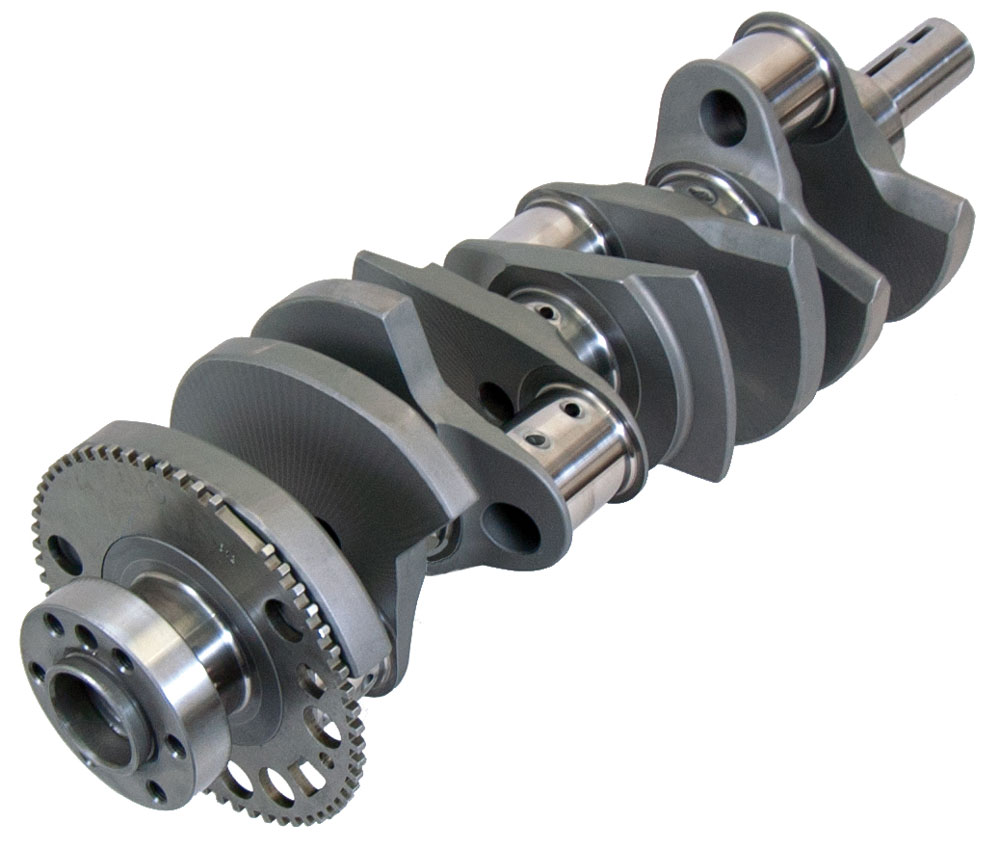
The other method uses the two forging dies that are designed to shape the part in a single operation. These presses required a great deal of power to produce a forging.
“With eight-counterweight forgings, we need what we call a pre-roughing situation where we have to clear out some material similar to what we would have to do on a billet just to get them to the point where they can start running them through our normal production line,” explained Norris.
With some raw forgings, the counterweights can’t be located exactly where the engineers prefer. That’s because the dies are designed with a draft angle so the part can be released.
“When the dies come apart, instead of the part easily coming out of the die, it can get stuck in them,” said Norris. “Probably the best example is our Top Fuel forging. We have the counterweights pretty much where we want them. However, in order to do that we have to put in extra material just so that the dies will accomplish what’s needed.”
Engine Driven
Recent engine platforms are driving new crankshafts. Molnar Technologies is developing both billet and forged crankshafts for the LT series, but one application the company is shying away from is very large displacements.
“One of the things that helps reduce the bending of the crank, besides the placement of the counterweights, is the overlap of the rod and main journals on the crank,” said Molnar. “When you go longer with a stroke, you are reducing the overlap, and the cranks are bending. There’s not that much you can do to help that.
“I’ve seen guys build these big motors, and they’re running eight-plus-thousandths of main bearing clearance,” continued Molnar. “They almost have to, because it’s going to bend, and they’re just trying to help protect the bearings by running thicker oil and lots of clearance.”
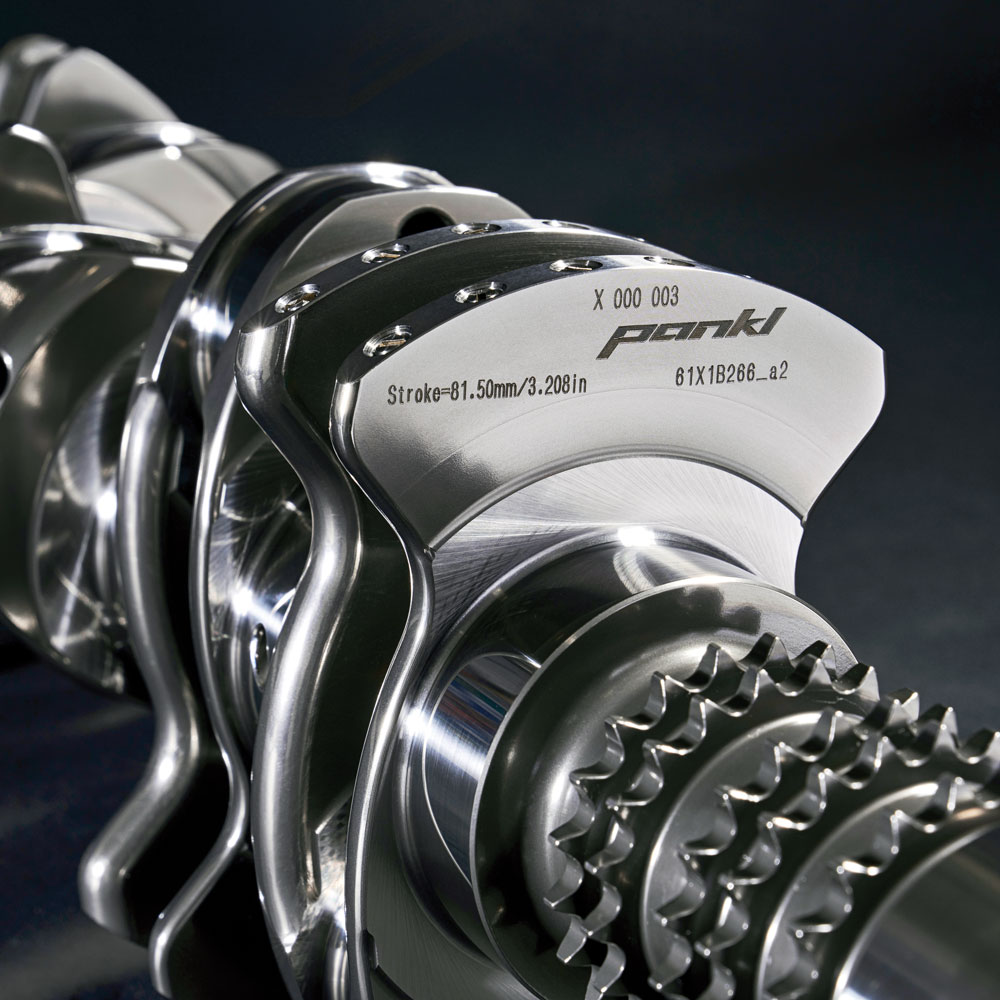
Big block Chevys are drawing attention at Manley right now. Some crankshafts under development include forged BBC 4.500-inch-stroke with center counterweights, profiled for a 6.385-inch rod and 2,250-gram bobweight; forged BBC 4.875-inch-stroke with center counterweights, profiled for a 6.700-inch rod length and 2,300-gram bobweight; and billet Chevy LT1/LT4 4.000-inch-stroke with center counterweights.
“The two new big block cranks will round out an already outstanding lineup of center-counterweighted cranks we offer for these applications,” noted Manley. “The billet Chevy LT crank should enjoy similar success as our billet Chevy LS crank, which has become a staple for many of the top LS engine builders producing 2,000 hp and thus requiring superior internals that can survive in this environment.”
Manley is also working on a new billet 88-mm-stroke crankshaft for the Mitsubishi 4G63/4G64 engine. “The new billet Mitsu is something we are working on to fix a common problem with all Mitsu 4G63/4G64 crankshafts: eventual cracking in the number-four rod journal,” said Manley. “We’ve made some really nice improvements and added necessary cross-sectional thickness in critical areas. This should allow the Mitsu fraternity to gain more confidence when making big power and deliver an engine package that will have longevity. More details coming.”
Rat motors are also a hit with Howards Cams customers. “The big block Chevy guys are going in a lot of different directions. We’ve got ones building Outlaw 632-type motors with either a lot of boost or nitrous,” said Peters. “And then on the LS side, you’ve got a lot of turbocharged applications where guys are pushing the limits. That’s kind of where the marketplace is now with so many people gravitating toward the billet line for the big drag racing horsepower, and it’s getting crazy.”
For circle track racers, Howards has the Track Smart line made from 4340 steel forgings. They feature a larger, 0.125-inch radius on all journals, and the nitriding is a little deeper than normal.
“Since the pandemic, our camshaft business in circle track is really good. In turn, the Track Smart cranks have been increasing in sales,” added Peters.
Over at Eagle, new applications coming include the Ford 7.3L Godzilla engine, the Chevy LT, and Nissan VQ.
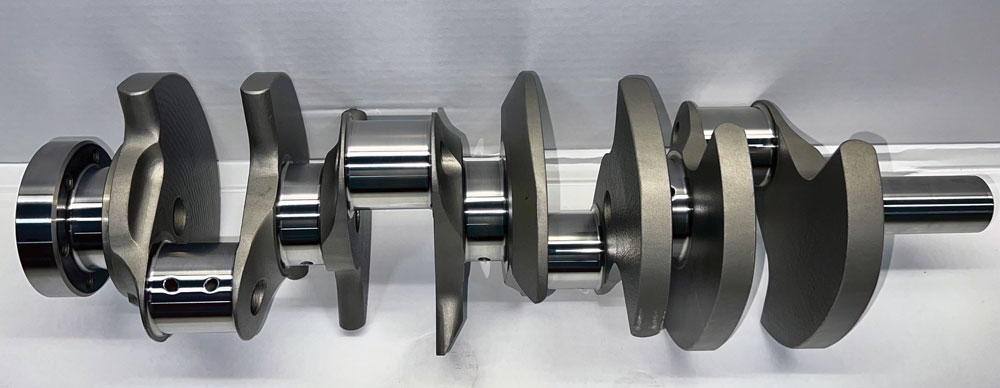
“Along with strength, builders want consistency and predictability. We are well into the changeover to fully automated CNC-controlled journal grinding for unparalleled sizing consistency and accuracy,” said Davis. “In an inflation-riddled economy, Eagle has been working hard to keep costs, and prices, down. Eagle has not had a price increase in over two years.”
Finally, any discussion of crankshafts cannot be complete without mentioning flat-plane crankshafts. Recent factory performance engines from Ford and Chevy with flat-plane cranks have energized engine builders into considering such a move for a future project.
“We get asked about flat-plane cranks quite often. We always ask if they are aware of everything else in the engine that has to change as well,” cautioned Davis. “Usually, people don’t understand that it’s not just the crank that’s different. A flat-plane crank also affects ignition phasing and cam phasing, among other things. As much as people think they want to see it, it will not happen until builders have a firm grasp on everything else that goes along with it.”
SOURCES
Callies Performance Products
callies.com
Crower Cams & Equipment
crower.com
Eagle Specialty Products
eaglerod.com
Howards Cams
howardscams.com
Manley Performance Products
manleyperformance.com
Molnar Technologies
molnartechnologies.com
Pankl
pankl.com