Rock Racing
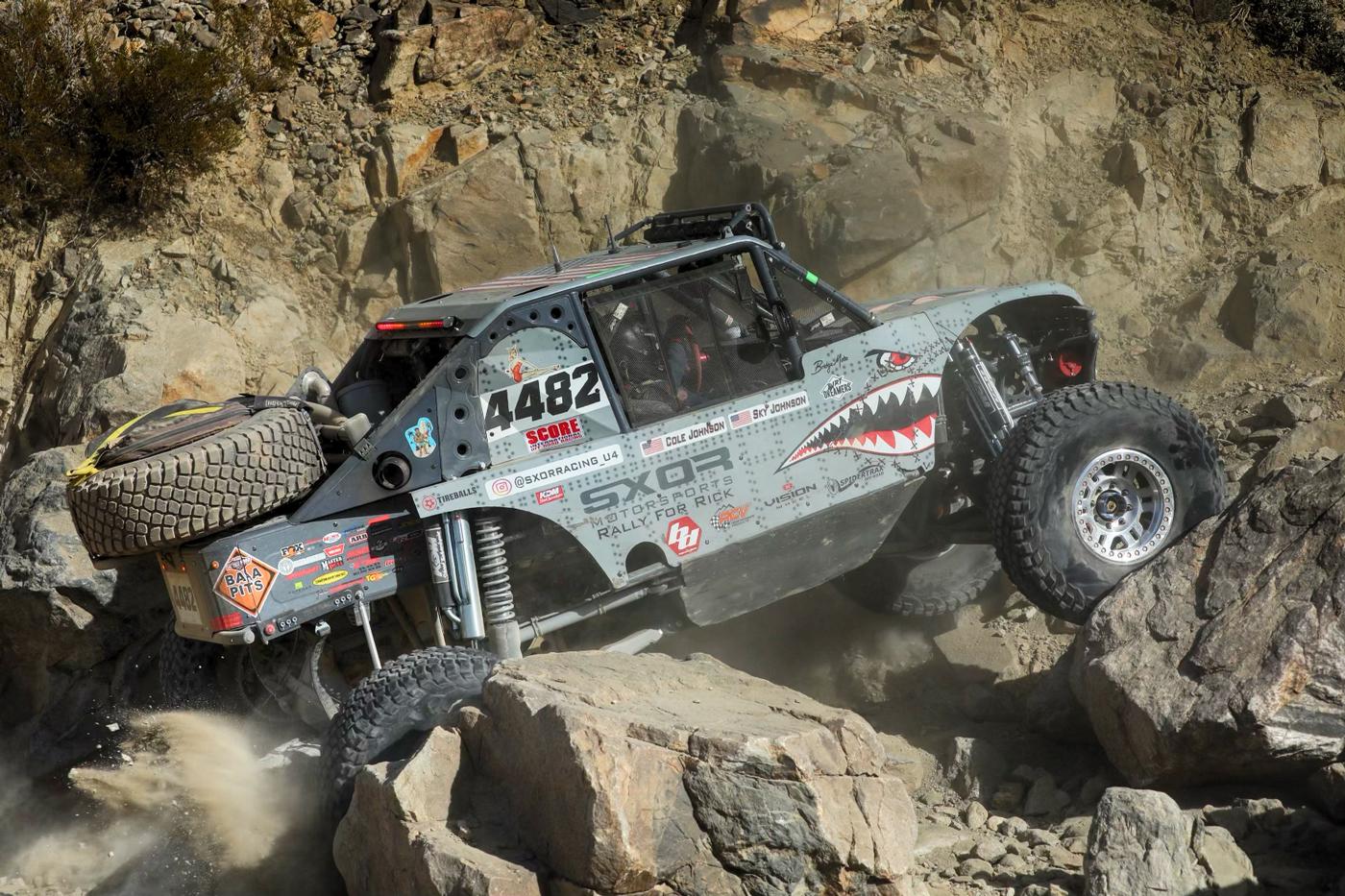
Competing in rocks, whether crawling or bouncing, puts huge demands on components. Here’s how these rigs are built for maximum performance and durability.
Unlike any other segment in motorsports, racing in the rocks can mean very different things and require radically different approaches to winning. Rock crawling is literally that: precisely driving through a set course, with the help of a spotter, to score as few points as possible for things like missing gates or having to back up. Rock bouncers, on the other hand, use all the momentum they can muster to tackle impossibly steep terrain that’s sometimes so slippery it has earned the nickname ‘owl snot.’
“In rock crawling, everything is done really slow and meticulously, because you have traction,” explained Jake Burkey of Busted Knuckle Off Road, Cullman, Alabama. “But when you’re on the slick stuff, you can’t choose your line. You have to bounce up through and over the obstacle.”
“A lot of people would consider [rock bouncing] a car wreck from start to finish,” added Clyde Bynum of the National Rock Racing Association (NRRA), Horn Lake, Mississippi. “It’s hard to fathom the abuse these rigs are taking and the courses they are climbing.”
These polar opposite disciplines have traveled very different vehicle development paths. Yet they do have some needs in common.
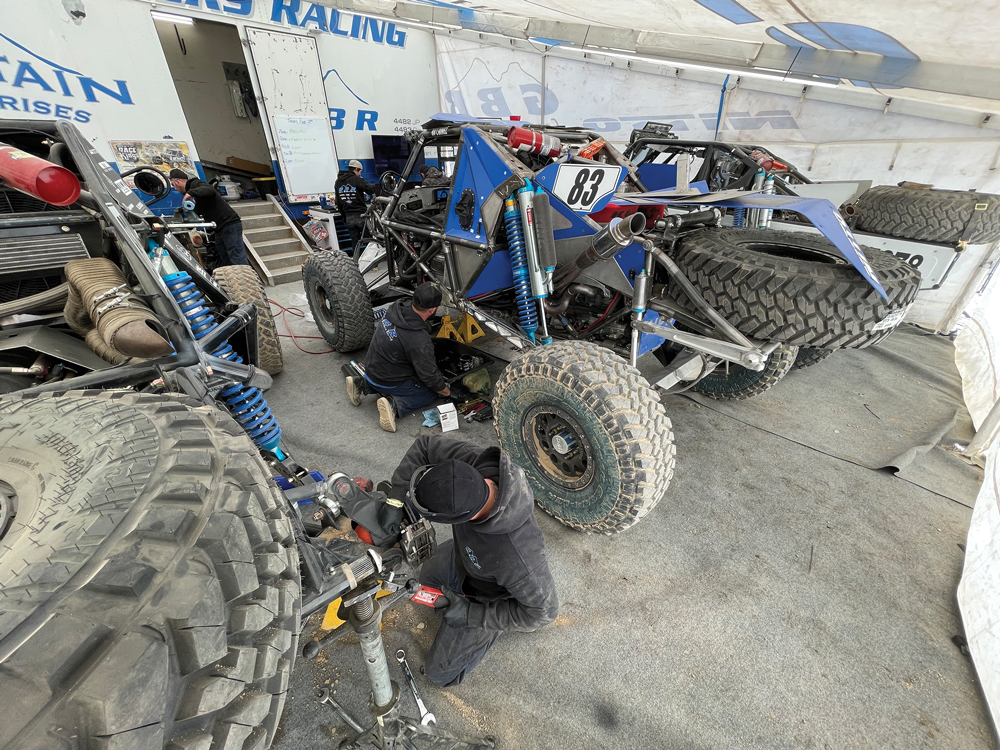
The Might of Light
One trait the rock crawlers and bouncers share is recent movement away from overbuilding their rigs. Or, as Brandon Haynes of Branik Motorsports in Fort Wayne, Indiana, put it, “With light, there’s might.”
In rock crawling, “everybody’s trying to build strong but light,” said Big Rich Klein of the World Extreme Rock Crawling Championship Series (WE Rock), based in Kansas City, Kansas. “The whole idea is to push or pull as little weight as possible over the rock formation.”
The adoption of portal axles (see sidebar on page 80) has enabled builders to “go to a super lightweight, small axle assembly,” Klein said. Many put Toyota center sections in custom Ford 9-inch housings; others have gone even smaller, to Suzuki Samurai axles and diffs.
A lighter rock crawler means “very few people run big motors,” Klein added. “The Ecotec is one of the favorite motors because they can supercharge or turbocharge them. They’re real lightweight, and they’re an easy package to work around because they’re small.”
Likewise, rock bouncers have learned that “a lighter weight vehicle with good suspension actually prevails much better than a lot of horsepower in a heavier vehicle,” Burkey said. “Now we’re seeing people going from what was 1,600 or 1,500 hp down to 900 hp and at the same time reducing vehicle mass by 1,000 pounds. That seems to be a better ticket.”
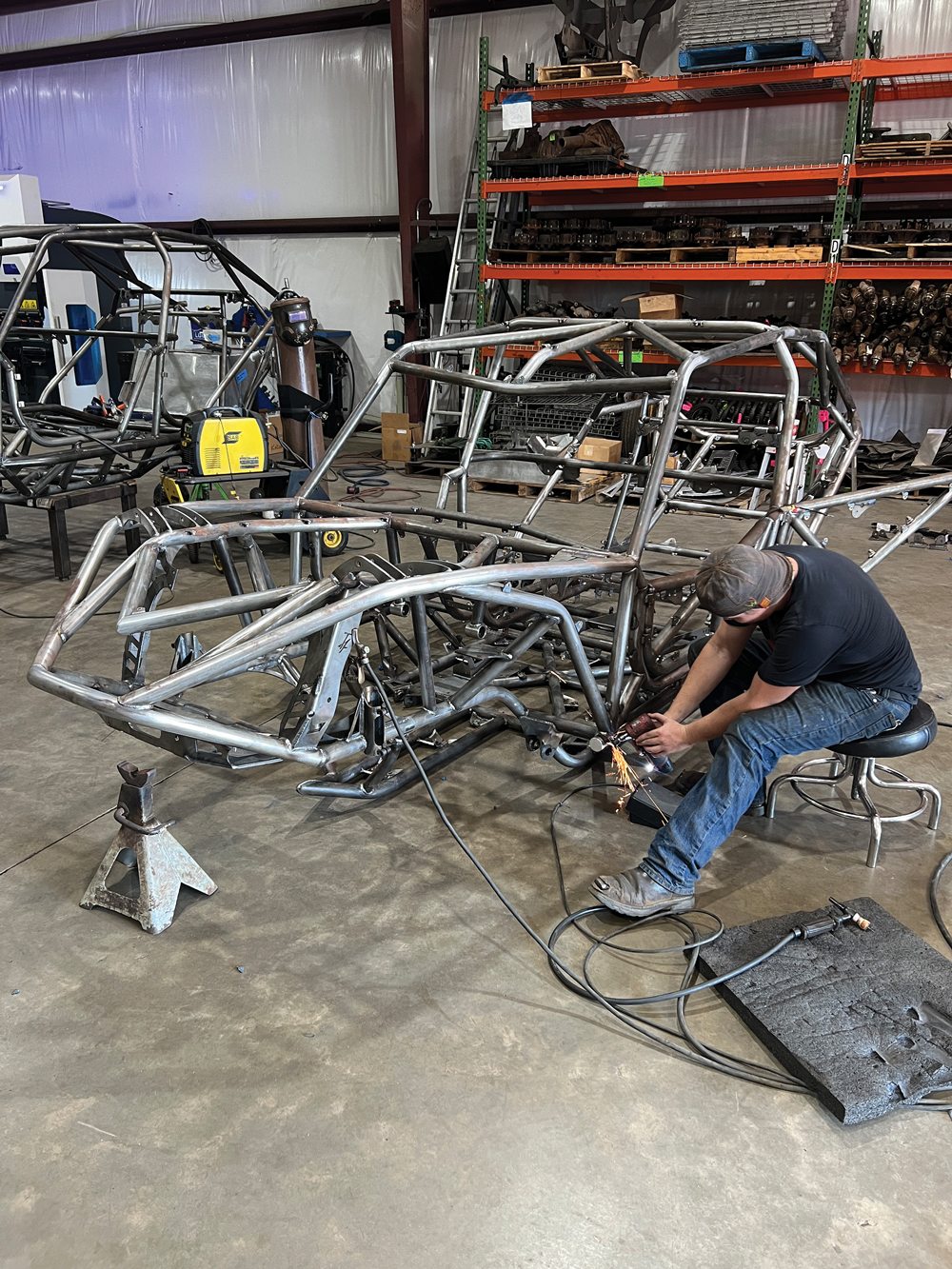
How does one shave half a ton off a rock buggy? Switching from the Dana 80 or Rockwell axles that were commonly used to Ford 9-inch differentials with chromoly housings and 10-inch ring-and-pinions “reduces the weight by almost 300 pounds per axle, so there’s 600 pounds,” Burkey said. Grooving material out of the tires can take “almost 20 pounds off per tire,” and switching from an iron to aluminum engine block cuts another 100 pounds. “Then take out the passenger seat, get a smaller fuel cell, do a few things here and there, and you got 1,000 pounds off the vehicle.”
For those who are building a brand-new rock rig, Busted Knuckle put much effort into designing its tube chassis to be light and strong. “All of these chassis have a triangulated roll cage in them,” Burkey said. “Because of that, we were able to put bars in locations that were in compression or tensile, and we weren’t having to rely solely on the flexural strength of the material, but the compressive nature of it. That triangulation made it to where we can lighten up the vehicles a lot.”
Finding the Balance
Haynes acknowledged that “there’s a balance, for sure,” when building components for lightness but also strength and durability. It’s a balance that applies across the board. “We use the same materials, whether it’s for high speed or rock crawling, because there’s still a lot of strength required for the slow stuff.”
“Stuffing a front tire into a crevice or an undercut and expecting it to climb something that’s taller than the tire puts extreme forces and loads on the axles, U-joints, and stub axles,” said Klein. To stand up to those forces, crawlers are using “more exotic materials than just standard alloy steel axles, from chromoly to 300M. We’ve also increased spline count. We’re running 40-spline axles in a Dana 60 that might have only come with 28 splines from the factory. Plus, the size of the axle goes up from 1 inch to almost 2 inches in diameter. That means the axle tubes are bigger. The U-joints go bigger. A 1310 U-joint is typical in a pickup truck on the street. We’re using 1450s or even 1550s on some of the axle assemblies.”
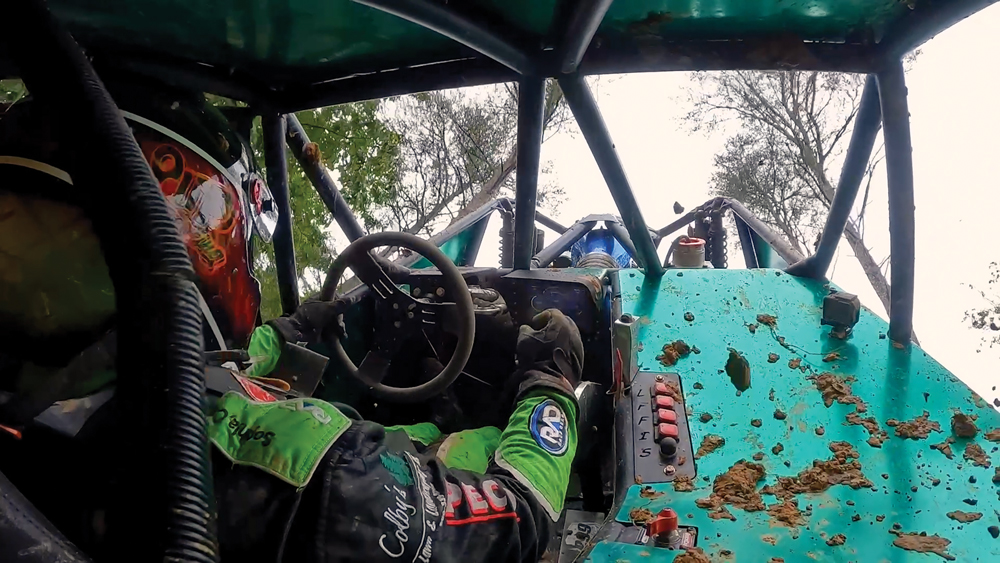
Branik Motorsports has developed its own 1550 U-joints. It manufactures components using 300M alloy “because the way those materials are manufactured and milled, they’re set to a higher standard, and we’re able to manufacture parts that are made not to break,” Haynes said.
Because of what Haynes described as the “point-and-shoot” nature of rock bouncing, where “they use their throttle like a light switch, and it’s all or nothing,” driveline components have to be extremely durable. Not just made of high-strength steel alloy, but big, too. Branik Motorsports turns out axle shafts with spline counts ranging from 40 to 47.
Some of the rock bouncers at the NRRA are using axle shafts from RCV Performance that are 47-spline “and are 2 inches around,” Bynum said. “That’s the same diameter as a Coke can.”
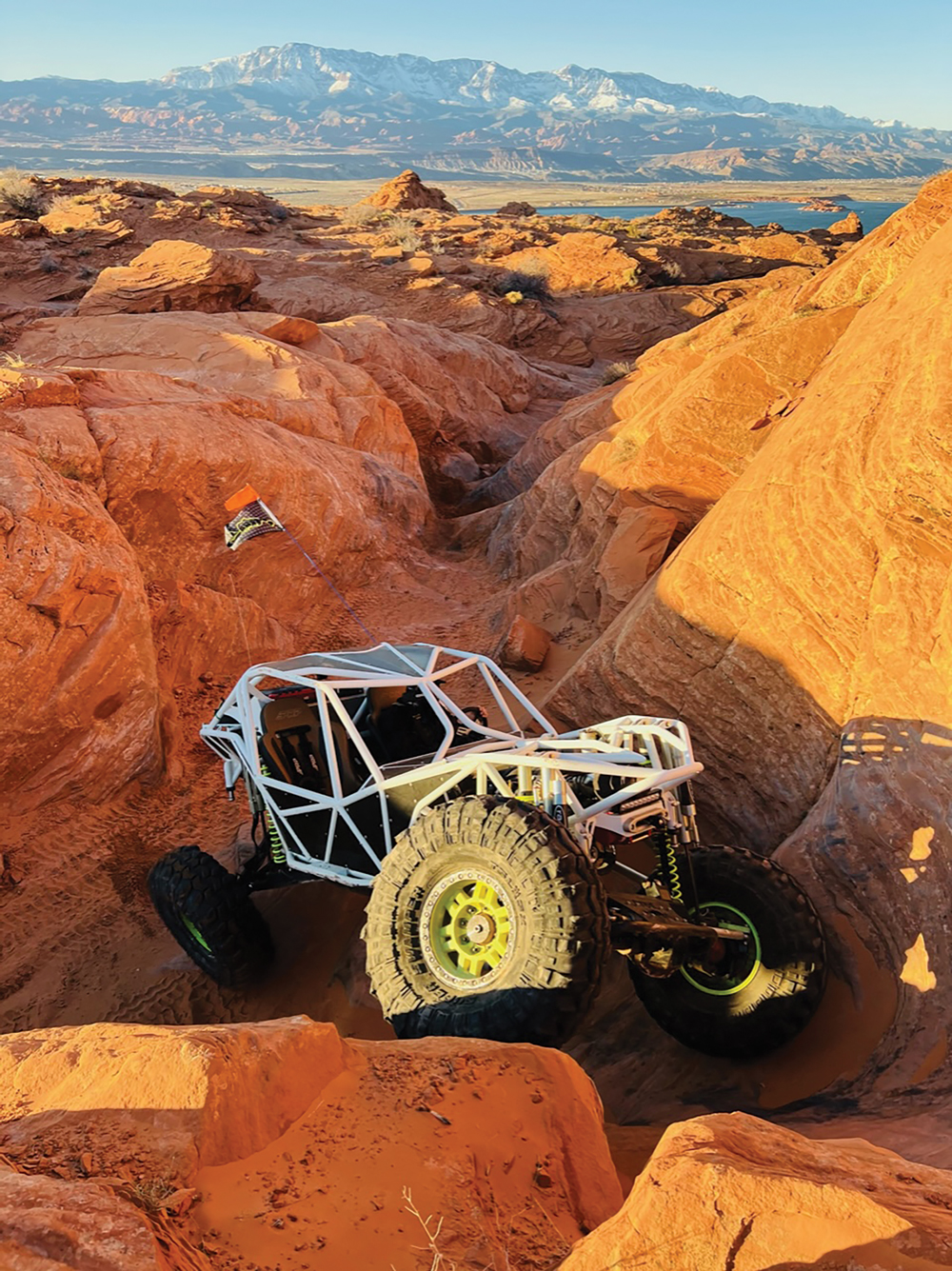
Busted Knuckle uses 300M for its top-tier axle shafts not just for strength but because of “the material’s elasticity,” Burkey said. “It is extremely good for allowing a whole bunch of torsional cycles where you’re getting loaded and unloaded, loaded and unloaded, before any type of cracks start to form.”
Additionally, “we use a lot of high-end aluminum in our designs,” Burkey continued. “The 7075 alloy is one of our favorites. It is extremely strong, flexible, and light weight. We use it on a lot of components that were previously made from steel, allowing us to cut weight in multiple locations on the buggy.”
In terms of axle size, Busted Knuckle makes axle shafts with 40-plus spline counts, though Burkey pointed out that “spline count is not relative to size. It’s relative to the aggressiveness of the spline itself. For instance, our inner axle shafts are 40-spline, 1.75 inches, while our outer axle shafts are 32-spline, but they’re 2 3/8ths inches in diameter. So it doesn’t necessarily correlate. You have to talk diameter, not necessarily spline count.”
What’s the Diff
Variations on Ford’s 9-inch rearend are common on rock racers of all kinds. Among crawlers, the 9-inch is “really popular because if you blow a ring-and-pinion, you can pull the axle shafts out a little ways and drop in a new center section,” said Klein.
The versatility of the 9-inch’s drop-in center section is a “huge factor in how it became so popular,” said Haynes. “You can also build really strong axle housings or aftermarket formed axle housings for the 9-inch, and they’re easy to fabricate off of. You can weld right to the axle housing wherever you need.” Plus, he said, new technology, such as 10-inch gear sets and better race materials, “has put the 9-inch up there as equally strong as the 14-bolt.”
Next to the 9-inch, GM’s 14-bolt and the Dana 60, which were used by the OEs in one-ton trucks, are the most common housings Branik Motorsports deals with, Haynes said.
At the NRRA, “outside of your custom, one-off housings, the most popular are the 14-bolt and the Dana 80,” Bynum said. “A lot of people went to the Dana 80 because of its bigger pinion, but just as many people are running the 14-bolts front and rear because the pinion support in the 14-bolt helps it hold up to what we do a lot more.” The 14-bolt, in OE form, was a rear axle only, but “we’re building them into steer axles front and rear,” Bynum said, as most NRRA racers “are front and rear steer these days to be competitive.”
Rear steer has been popular among crawlers almost since the beginning of the sport, Klein said. “They would take a front steer axle, flip it over, and run it as a rear steer axle so they could get a sharper turning radius. Chassis got narrower so you could turn 40- or 42-inch tires in the rear to an extreme angle. Most pickup trucks or Jeeps you can buy off the showroom floor have a steering angle radius of probably 30 degrees in the front, where our crawlers are getting anywhere from 56 to 60 degrees of angle and making them survive in most situations.”
Where the Rubber Meets the Rocks
Klein credited BFGoodrich with developing the first tire specific for rock crawling. The BFG Krawler T/A is “what we call a sticky tire, which means it has a durometer rating lower than a standard DOT tire.” Other companies have followed, including Maxxis, Interco, and Mickey Thompson.
“We don’t care how many miles they get, and we’re not driving that fast,” Klein said. “If you see a wheel spinning, and it looks like they’re burning rubber, the guys are heating up the tires to get more stickiness out of the compound.”
Tires are one area where the rock crawler push for lightness doesn’t apply. “The lower the center of gravity you have on the vehicle the better when you’re off-camber or climbing because you get more traction the closer your weight is to the rocks,” Klein explained. “So unsprung weight is okay. Axles, wheels, tires, those items can be heavier because they’re below that center of gravity line, or most of it.” Some crawlers add water, or steel shot, or both to their tires to “create more weight in the wheel assembly to hold the vehicle onto the ground.”
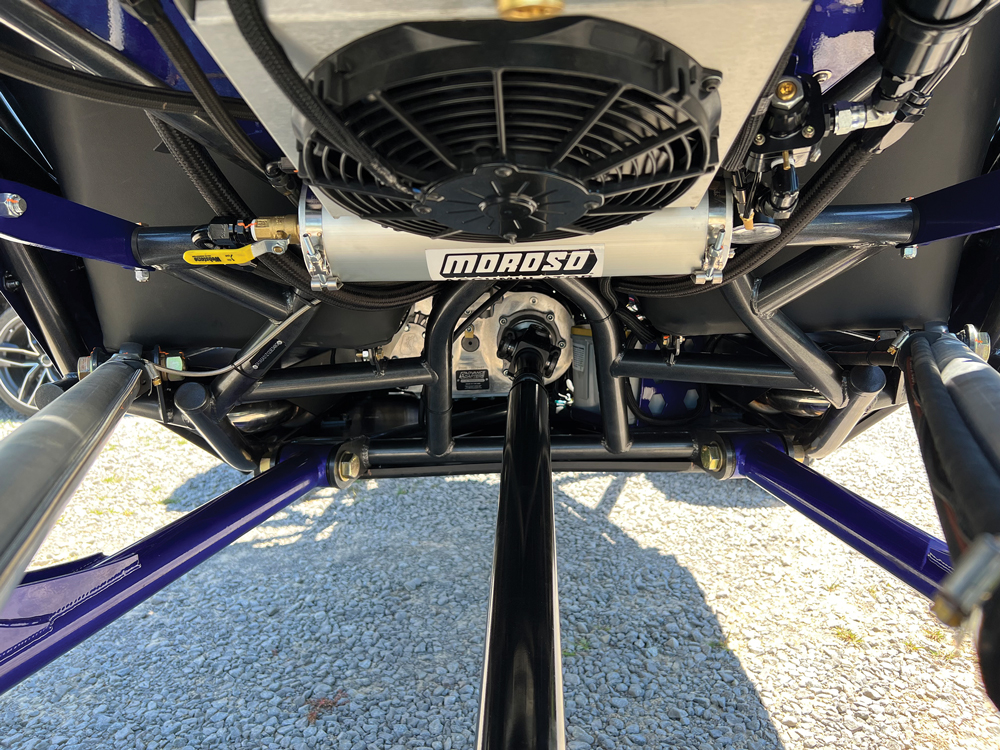
Falken Tires in Rancho Cucamonga, California, is currently testing a race compound, 40-inch version of its Wildpeak M/T01 with select rock crawling teams. “We’re two years out from releasing it in a DOT version. Right now, this is exclusive to motorsports,” said Doug Fletcher. “It has tremendous grip, and they’re doing really well with it.” In addition to the new tread compound, the 40-inch M/T01 is made with Falken’s Duraspec construction technology, in which the tire’s “turn-up plies come up way further than most of the rest of the industry’s products, which gives us additional strength in our sidewall,” Fletcher said. “That means the tire is going to be a little heavier than one that doesn’t have as high a turn-up ply.
“Plus, our tire comes with one of the thickest tread depths in the industry. Depending on size, we go up to 21/32s of rubber,” Fletcher continued. “Again, when we’re talking durability and strength of the tire versus weight, if I have more traction with more tread depth, I’ll sacrifice a little bit of weight to do that.”
On the rock bouncing side, “Mickey Thompson was one of those companies that developed a tire for our market, the Baja Pro X,” Bynum said. Like the BFG Krawler, it’s a non-DOT, sticky-compound tire. Most NRRA racers use the 43-inch-tall version with a 17-inch wheel.
“These guys are hitting, say, a 2-foot rock ledge that’s at a 90-degree angle at 40, 50, 60 miles an hour,” said Bynum. “So the tire has to be very tough for what we do.”
“The invention of the sticky tire allowed us to have the same amount of traction at a higher psi level in the tire,” Burkey pointed out. Conventional off-roading tires are run on the rocks at super low pressures—2–3 psi—for the tires to essentially wrap around the rocks for traction. “But we can run 8 or 9 psi with the sticky tires, which provides the same traction and is enough to keep the tire from compressing when we hit an obstacle at speed and bending the wheel.” Most competitors use beadlocks on their wheels, which bolt the tires to the wheels to secure them at low air pressures.
Burkey said most wheels are 17 or 20 inches in diameter to fit large brake packages and beefed-up steering knuckles and axle shafts. “We’re running huge steering knuckles. It’s kind of hard to fathom just how much bigger these are from even five years ago.”
Desert Race Suspensions
Tuned suspension systems “have become a number-one thing” among rock bouncers over the past three to five years, Burkey said. “We’ve realized that you can make it over an obstacle with less horsepower if your suspension absorbs the impact properly than if your suspension doesn’t. If you combine that with a sticky tire, you have a recipe to conquer all the terrains.”
Rock bouncers have been looking west and borrowing ideas from desert racers, he added, such as trailing arm systems and coilovers with bypass shocks. Desert race shock specialists like King and Fox are in the mix, but many bouncers use Radflo bypass shocks, a company Burkey calls “the industry leader.” Busted Knuckle “tunes the shocks based on the terrain and the vehicle characteristics that we have. Once that’s done, we order the shocks pre-valved from Radflo ready to bolt on the vehicle.”
Bynum agreed that Radflo “is one of the big companies that supports the sport,” and most of the NRRA competitors are using triple- or quadruple-bypass shocks. Trailing arm systems are popular with his bouncers, too, as “that way they get a lot more travel, as much as 24 to 30 inches of travel.”
Branik Motorsports has developed sway bars for bouncers that “keep your vehicle stable and improve the handling going around corners,” Haynes said. “The seat-of-the-pants feel is a whole lot more stable with sway bars front and rear.”
Rock crawlers also turned to desert racers for ideas about shock packages, coilovers, and link suspensions, but Klein said they soon found “all of those items react differently when you’re trying to go slow and gain traction, as opposed to carrying the vehicle as fast as you can over rough terrain.” Crawlers were able to use some of the components, “but the suspension design changed, and the shock valving and setups changed, even though they look identical to what a Trophy Truck or Class 1 car has.”
One innovation that has come to American crawlers from Australia is a shock absorber with the ability to push a tire down into a hole for more traction, Klein said. “It’s a shock with a hydraulic system over the top of the regular shock system. It acts like a regular shock, then at the push of a button it hydraulically pushes the ram to put the wheel where you want it to go. When you release it, it returns to normal ride height.”
Other than components like those hydraulic ram shock absorbers, or tires aired down to single-digit pressures, the vehicles built for rock crawling and rock bouncing “are really no different than any other race car,” Bynum said. “It’s just our sport. I would say it’s probably hardest on parts, but there have been a lot of companies that have stepped up and built custom parts for our industry.” Rock bouncing, he said, “is a sprint of the hardest courses you’ll ever find.”
Hammer Time
Hammerking Productions’ Ultra4 race series and its marquee event, the King of the Hammers in Johnson Valley, California, combine elements of rock crawling and bouncing with high-speed desert running. As such, the cars competing in the unlimited Ultra4 class look like a cross between crawlers and desert racers, and they share some tech with the rock racers.
“Nowadays we’re using portal boxes,” said Dave Cole, “which give you higher ground clearance, the ability to fit bigger tires, better gear reduction, and you can run bigger tires without adding load to your drivetrain. We also get a lot of flexibility out of our differentials, whether they’re selectable or automatic [locking].”
The high speeds put demands on the engines that are unmatched in crawling or bouncing, making “temperature control and oiling a really big deal,” Cole said. “Engine management systems have really exploded. We’re capturing telemetry and managing it at a much higher technological level than you would expect to find in off-road. Ten years ago, you might have found 10 people running a MoTeC system. Now there’s 300. Some people run the old stock ECUs, but you cannot be competitive unless you’re massively changing your entire data management system on your car.” —Drew Hardin
Portal Axles
Whenever portal axles came up in interviews for this story, everyone credited Jesse Haines of Jesse Haines Fabrication (JHF), in Dayton, Nevada, for his pioneering work adapting the system used on military Hummers to the requirements of off-road racing. “It’s old technology, proven in the military for 40 years or so, but a lot of guys are using them. They’re very strong and robust,” said Brandon Haynes of Branik Motorsports, Fort Wayne, Indiana, which worked closely with Haines to develop a Dana 60-sized axle shaft that fits in the JHF portal box.
Portal axles are geared axle hubs mounted on each wheel. Adding gear reduction at the wheels carries some of the driveline torque, “which makes your axle shafts and ring-and-pinion twice as strong,” said Haynes. The portals also increase ground clearance by lowering the wheel’s mount surface relative to the axle and differential.
“A lot of the guys in rock crawling are using smaller, lighter-weight center sections, like Toyota center sections,” Haynes noted. Even when they’re sending 250 to 350 hp to 40-or 42-inch tires, “the differentials hold up well with a portal setup.” —Drew Hardin
SOURCES
Branik Motorsports
branikmotorsports.com
Busted Knuckle Off Road
bustedknuckleoffroad.com
Falken Tires
falkentire.com
Hammerking Productions
kingofthehammers.com
Jesse Haines Fabrication
jessehainesfab.com
National Rock Racing Association
nationalrockracing.com
World Extreme Rock Crawling Championship Series
werocklive.com