REFUELED ENGINE TECH

Power gains come in a variety of packages, and several of today’s top engine builders reveal the advances that are driving developments into 2021.
Mapping engine technology advances in auto racing used to be as easy as following the horsepower improvements year by year. The days when engine builders made power through traditional methods: more displacement, more boost and, of course, more fuel. They also optimized the engine, picking up small but noticeable gains through friction and weight reduction.
Today’s high-tech environment has led to sophisticated powertrains that comprise electric motors, batteries, and vehicle control units. Engine technology now includes lessons in converting kilowatt-hour into horsepower, so people know what you’re talking about. It’s not just about power—the new generation of engine builder is consumed with recharging time, regen braking, and battery cooling. And, instead of wondering when those new titanium valves are going to arrive, today’s EV engine builder worries about sourcing rare earth magnets.
It’s a much different universe, but aside from EV and hybrids there’s still a need to advance technology for the internal combustion engine that’s used throughout most of racing today. In some classes, the power levels are progressing at neck-snapping rates, and engine combinations that were competitive a couple of years ago are now obsolete.
“I get calls from guys who want to go racing in X275, thinking they’ll need 1,500 horsepower and can do that with a turbo and carburetor,” said Ken McCaul of Borowski Race Engines, Rockdale, Illinois. “I’m saying, ‘Guy, I really hate to wreck your dreams of being competitive in that field. But I can tell you I have customers making twice that with computers that can do all sorts of things on the track.’ In other words, I don’t want him spending a bunch of money, not be competitive, and then be pissed off at me about it.”
Educating customers on the level of competition, especially in unlimited-type classes, is becoming more of an obligation in engine shops. While that might discourage some potential customers, honesty is always the best policy—even when it comes to recognizing the limits of current technology.
“If it’s boosted it’s a little bit easier to make power. I mean, you can damn sure make a lot of power quicker than you find some other,” said Jon Kaase of Jon Kaase Racing Engines, Winder, Georgia. “At a PDRA race in Pro Stock, we’re the only cars on the property that are not enhanced somehow with nitrous, supercharging, or turbocharging. Our cars are pretty quick, but we could work for another 10 years and they might just be a tenth of a second quicker.
“The turbocharged cars or the supercharger and nitrous cars are still in a position of making gains,” Kaase continued. “They’re going to be a little bit quicker all the time with those things. We’ve got to the point where our cars are not a whole lot quicker than they were five or eight years ago, but we’re doing all we can.”
In situations where different types of engines compete in the same class, it’s up to sanctioning bodies to balance the power with weight breaks, boost restrictions, or some other handicap to level the field. But even power enhancements can have limitations.
“What happens with nitrous, you start to approach what I call the saturation point,” cautioned Pat Musi of Pat Musi Racing, Mooresville, North Carolina. “There is a graph we use for 350- to a 960-inch motor of how much you can actually get in that cylinder and be reliable. When you get to a saturation point, the nitrous stays suspended in the plenum. Now, you can go over to a certain point, but that’s where the tuning comes in. If you get over center on the saturation point, then you are done. That’s when you see them blow up.”
The sudden popularity of boosted engines where rules allow is certainly driving much of today’s engine development. Even street cars are running 1,500- to 2,000-horsepower engines—a power level that most racers would have salivated over five years ago. Current engine technology is also manifested in more subtle ways that may not make for exciting social media posts. Ask a dozen engine builders what capabilities they have today that they didn’t have five or seven years ago, and the answer is almost always the same.
“CNC machining continues to get better as the years go on. People get a little more efficient and better equipment, and they get more accurate parts,” said Doug Patton of Pro Line Racing in Ball Ground, Georgia.
“The advancements of CNC, robotics, and automation have helped us produce parts quicker and in larger quantities,” confirmed Mark Mazurowski of Mazworx Racing Engines, Sanford, Florida. “A lot of the products we use in our engine builds, we actually manufacture here, which helps us a lot. If something changes, we can make quick changes and not have to worry about purchasing a large batch.”
Mazworx specializes in Nissan four-cylinder engines that have been out of production for 20 years. Many of the OEM replacement parts are no longer available. “We’re now looking at making our own timing-chain sprockets,” said Mazurowski, adding that his shop already manufactures billet blocks and billet main caps.
Billet cylinder blocks represent one of the more significant tech advancements allowing for more boost and big power numbers, the result of factory blocks no longer being able to support the intense cylinder pressures generated by boosted applications.
“The advent of billet blocks is really key,” said Tony Bischoff of BES Racing Engines, Guilford, Indiana. “Billet aluminum is at least twice as strong as cast aluminum. Three years ago, we might have done one billet block, and now we are building probably five to seven engines a year with a billet block. So that is definitely an area where durability has improved.”
In fact, durability is another buzzword that comes up often when talking to engine builders. For the high-stress applications that involve boost, customers just want the engines to stay together. Particularly among budget racers and those with naturally aspirated applications, increased lifecycle seems to be a priority, along with enough power to be competitive.
“With our [drag racing] base we try to get 75 to 100 runs out of these engines before they come in for a freshening,” said Phillip Oakley of Oakley Motorsports, Owensboro, Kentucky. “That’s pretty much a full season for these guys. Basically, all they have to do is service the oil, check the valve lash and springs, put fuel in it and go.”
Another measure of improving engine technology is offering horsepower and durability at a lower cost. In the highly competitive Late Model divisions, purpose-built engines can cost upwards of $50,000 to $60,000. Mullins Racing Engines in Mt. Olive, Illinois, has developed a 430 ci LS7 engine for Late Models that costs just under $26,000 with the same power levels and durability.
“We felt like we needed to run with the big boys and needed to add some extra power,” explained Chad Mullins. “We hit on all the critical areas to get extra power and dealt with the best in the world at every opportunity. It came through pistons, manifold work, carb spacer, camshaft design, and piston design. We just took each particular area, figured out who the best we knew of on each area, worked on that part of the engine, and got the extra power we needed. It’s the same lifecycle as the $50,000, $60,000 engine. You’re not giving up anything, except for saving 40% to 50% of your money.”
Not all technology is limited to the track, however. The COVID-19 pandemic has shut down or hamstrung many racing opportunities, and some shops have made up the difference by building high-powered street engines.
“Honestly, this year with the pandemic, I thought we would really fall off hard, but it’s been the street guys keeping us busy. We’ve done quite a lot of street engine builds,” reported John Benshoof of Freedom Racing Engines, Brownsburg, Indiana, which specializes in diesel performance. “We try to incorporate all of the same technology that goes into our 2,000-plus-horsepower builds—we try to utilize that same technology into everyday stuff. So when you can take a valve seat, for instance, and put it in an engine that is going to make 2,500 horsepower, it’ll surely hold up to 800 horsepower.”
Performance diesel technology is likely advancing much faster these days because it lacked the attention that spark engines received over the past century. There’s a lot of innovation and trial-by-error, as witnessed by videos of some spectacular engine explosions found on social media. Yet the consistent winners seem to focus on the basics while keeping an eye on durability, even when working together with other engine builders on a project. Freedom recently built a 6.7-liter Cummins that Scott Birdsall used to shatter a record in his class at Pikes Peak.
“The technology that went into that was basically build an engine that will live,” said Benshoof, noting that Dynomite Diesel developed unique injectors and Jarid Vollmer handled the tuning. “There were some really neat things that went on with that project. On our end, there wasn’t a lot of time to do development, but what we’ve developed over the years is built a recipe for a foundation that will handle that type of abuse—whether it’s a truck going up Pikes Peak or a daily driver.”
Regardless of the application, most engine builders look to the cylinder head to find more power, especially in naturally aspirated uses. CFD analysis is helping some shops design more efficient ports, while others are analyzing different combustion chambers and valve jobs.
“The best cylinder heads make the best motors,” Kaase said. “The rest of the engine is just along for the ride. If you get a decent short block, the rings are okay and the camshaft is somewhat reasonable—the power is in the cylinder head and intake manifold. We’ve pretty much beat on manifolds to the point we can’t get them much better. It really comes back to the heads and chambers. There’s no big computer program for that. It’s just trial-and-error to find something that is better.”
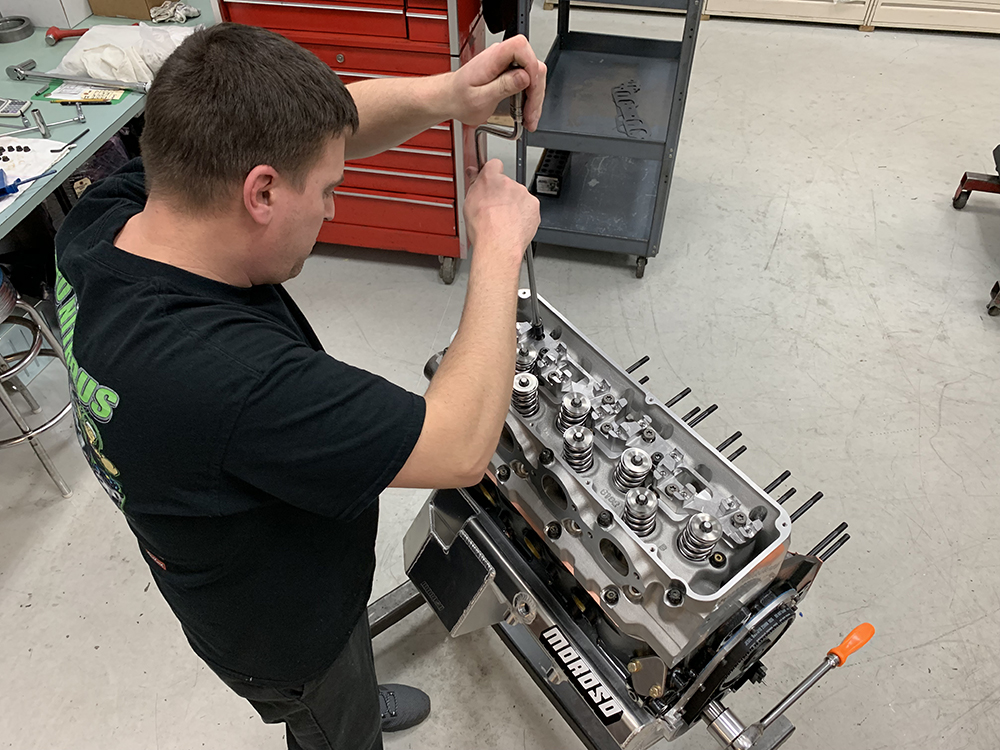
“We’re constantly changing port designs and shapes on the cylinder head,” Bischoff agreed. “We’re finding a little bit, but nothing’s ever huge. In the nitrous world you might think you concentrate more on the exhaust side. I have combinations that run well, including ones where we did the exact opposite and they both run good. With the advent of really big motors, I think our ports are ending up bigger than we ever thought they could be, or should have been, five or six years ago. Naturally, with the advent of better valve springs, rocker arms, and lifters, that all helps you utilize a bigger port.”

From Oakley’s standpoint, “It seems like with cylinder head technology there’s something new every day. Cylinder heads and manifolds have been probably the biggest things that have driven the horsepower increases, along with some of the new cam lobes. Carburetors have also had a big impact. It just depends on what you’re working with.”
Carburetors may seem anachronistic in this new age of computers and fuel injection, but a great deal of the racing community still depends on that simple and easy-to-use method of fuel delivery.
“In my opinion, with EFI there is a huge gain especially in power-adder situations, but a lot of the guys are just scared to death of it,” said Oakley. “It is making its way more and more, but probably only one in 10 are EFI in the sportsman world. In the professional heads-up categories, it’s pretty dominant because of the tuneability. I mean, with my EFI customers I can tune them from my desk.”
“You cannot run a Pro Mod nitrous car without fuel injection,” said Musi, noting that he’s running six stages of nitrous today as opposed to just three stages 10 years ago. “The tunability with nitrous became a big deal. Look, they can still blow them up. It’s like Top Fuel. You give them a window and they are going to push it until they light the fuse and it don’t make it to the other end. What we’ve got is longevity. You’ll never see my cars with the cylinder heads off between rounds. But it’s been a lot of work and trial-and-error. The final component is the tuner.”
“With the electronics nowadays, you’re able to maintain that edge. Back 10 or 20 years ago, it wasn’t easy to ride the edge safely,” said Mazurowski, adding that new computer programs and other advancements continue to improve products before they get to the track. “We have computer simulation, solid modeling, reverse engineering, laser scanning. We can develop a product in the computer, send it to a 3D printer, and verify it before we put it into production.”
TECH FOR SPORTSMAN RACERS
High-line developments are great, but what about new frontiers in engine technology for builders who serve the sportsman racers? Those racing naturally aspirated engines are seeing mostly incremental gains because just about every trick developed by NASCAR and Pro Stock teams has trickled down to the masses. Trade shows, networking, seminars, and cross-pollination of employees has spread the word, and today’s NA engines are more efficient than ever. That leaves boosted engines to lead the way.
“When we first started working with the turbo stuff there was a lot to gain, especially in power management. As the cars have gotten faster, obviously, the amount you are picking up as you go along gets to be less and less,” explained Patton, noting that the improvements have been tremendous with boosted Pro Mod engines. “We bought a dyno in 2011. And at that time, I think the most anyone was advertising for power was in the low 3,000 to 3,200. And that was, say, a 481X or a Hemi with 40 to 45 pounds of boost. That was all anybody had at the time. And now on the hub dyno we have next door, we have seen 5,200 horsepower to the wheels, and that’s a Hemi engine with two big turbos and probably making about 75 pounds of boost.”
Today’s drag cars are making so much power, in fact, that aircraft avionics are necessary to keep them under control.
“We built an engine that incorporated a flight-level indicator out of an airplane. The computer adjusts the boosts to make sure that it keeps the car level,” said McCaul. “We made 3,300 horsepower with a conventional head 427 LS. The heads had water jackets, and we used an iron Dart block with two 83-mm turbos.

“But if I showed up to a drag race and I found out that the guy next to me had a mechanism in his car that came out of an airplane, and that it’s managing torque and traction while I’m trying to pedal it at the finish line, then it is just a different level of competition,” continued McCaul. “You just cannot compete with a computer-controlled engine like that when it is making these adjustments faster than you can blink.”
Which brings us to the one constant obstacle to advancing engine technology at the race track: rulebooks. Sanctioning bodies often put some type of limit on practically every engine component, which can be a subtle way of mandating crate engines in some classes. While the motive is understandable—that is, trying to control costs and maintain a level playing field—sometimes the end result is a dose of clever misdirection.
“As far as crates go, we’re the cheater crate capital of the world. We’re well known for that. We advertise it, proud to announce and tell everybody,” boasted Mullins, who won’t reveal his strategy. “It’s engine stuff they can’t see from the valve covers. We pick them up about 80 to 90 horsepower, and how we get there, I can’t tell you. It’s blueprinting, balancing, and then cheating.”