Burning Questions
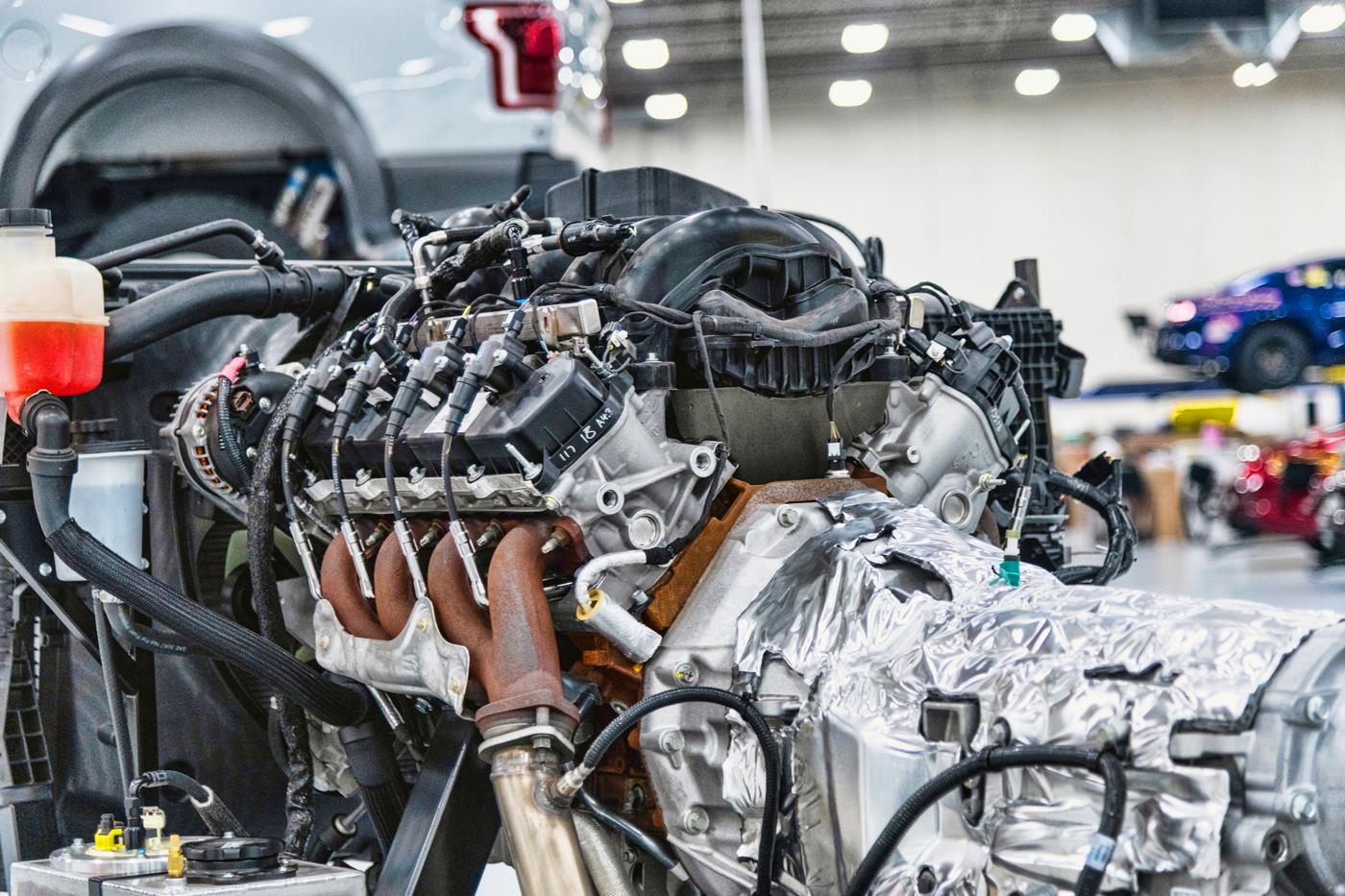
How will the future of performance engine development be influenced by the latest factory offerings from Detroit?
Consumer demand obviously drives performance engine R&D in the aftermarket. Yet today there are companies initiating much more aggressive strategies in building horsepower in new production engines than what was done 20 or 30 years ago with what was then the latest factory powertrain platforms.
The growing popularity of Ford’s Coyote and 7.3-liter Godzilla engines, along with increased attention given to GM’s Gen V LT series and Mopar’s Gen III Hemi, has many engine builders and speed merchants setting up dedicated development programs to improve performance in those engine families.
“We just spent 10 months on our dyno and Spintron developing intakes, camshafts and valvetrain parts for the Gen V engines,” reported Brian Tooley of Brian Tooley Racing (BTR), Bardstown, Kentucky. “We’re just about to start on the Hemi. We actually have a Spintron Hemi built, and we have additional Hemi test engines on standby.”
“We’re doing two versions of Godzilla,” said Jason Youd of Mast Motorsports, Nacogdoches, Texas. “There’s a street car version for Ford swaps and an all-out supercharged engine.”
These efforts and others throughout the industry represent a significant shift in philosophy compared to when the Gen III LS engine first appeared in the Corvette in the mid-1990s. There was no thunderbolt-like reaction from the aftermarket and racing community. Everyone was quite happy building conventional Chevy big and small block engines for both the street and track because there were so many inexpensive but quality parts and options available.
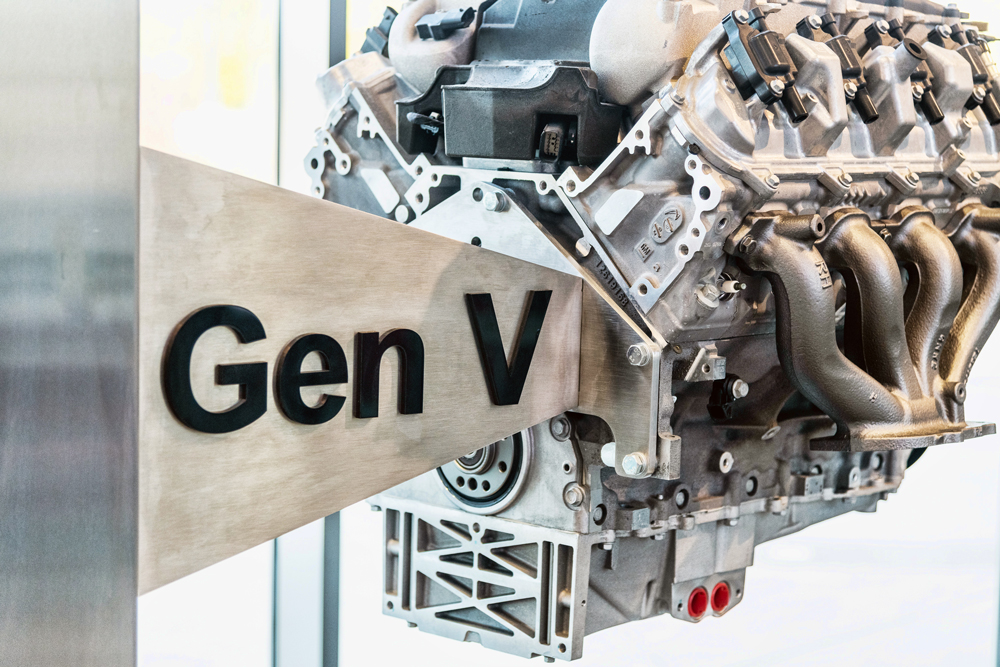
A few GM specialists, like Lingenfelter Performance Engineering, now based in Brighton, Michigan, were able to crack the codes in the factory engine-management computer early on and develop cam profiles to take advantage of the tuning options. Then came a few new intake manifolds and eventually CNC-ported cylinder heads. But the LS really didn’t catch on with the aftermarket until truck engines started showing up in salvage yards.
GM sold more than a million fullsize trucks and SUVs a year that were equipped with variants of the LS architecture. When hot rodders discovered how easy they were to swap into older vehicles, more companies started helping with conversion kits and power upgrades. The rest, as they say, is history. Now the LS engine is available in a variety of crate engines, and there’s a seemingly unlimited supply of aftermarket parts available. Spec versions of the LS are even mandated in some racing classes, including those for which the vehicle bodies are of a different marque than GM.
“Honestly, the same thing is going on with the LT motor as well,” said Lingenfelter’s Mark Rapson. “The LT motor is a better platform than the LS motor, but people have not embraced it like they do LS right now because the direct injection adds another layer of complexity.”
The Gen V LT is a more sophisticated evolution of the LS with direct injection (DI), piston squirters, improved oiling and upgraded VVT. There’s even a supercharged version that’s earned a loyal following in the dirt.
“We specialize in a lot of off-road race cars,” said Chris Bland of CBM Motorsports, Colton, California. “There are still limitations to fuel pumps, fuel injectors and so on, but we’ve done quite a bit with the LT5. We have those going into sand cars. With a typical LT, we’ve had some guys put them into rock crawlers and Jeeps. We even had an overseas customer put an LT1 with an eight-speed transmission into a Land Rover Defender, and it turned out real nice.”
The LT engine was first introduced in 2014 model year trucks, SUVs and Corvettes, and GM has not made it easy to upgrade the most recent performance versions of the LT engine family.
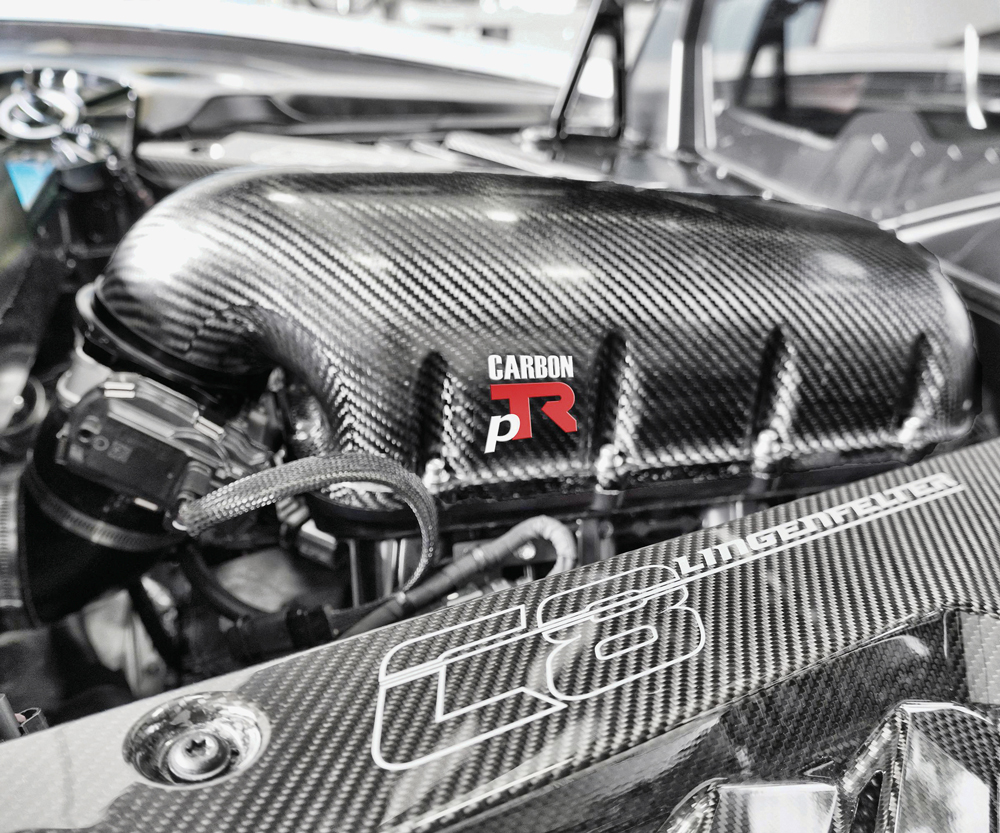
“The biggest challenge on the new vehicles, like the C8 Corvette with the LT2, is the electronics,” said Rapson. “Every year, the ECMs and electronics on the cars have evolved to make it more difficult. Now General Motors has moved to its Global B architecture, which completely blocks any direct access to the engine management system for calibration.”
Lingenfelter’s LT upgrade strategy is to develop advanced hardware that will complement the flexible calibrations programmed into the factory management system. The exhaust system flows a little easier but still provides necessary backpressure to keep the sensors happy. Lingenfelter then worked with Performance Design to develop the Carbon pTR intake manifold. When mated with a Lingenfelter 95-mm throttle body, the C8 Corvette LT2 engine will pick up 25 horsepower at the rear wheels.
“These new systems are wide-band driven,” explained Rapson. “It does give you an opportunity to look at managing the intake and exhaust air in such a way that if the engine sensors are correctly accepting the changes that you make, the engine will, for all practical purposes, recalibrate the air-fuel ratios itself and allow you to add additional horsepower.
“We spent a lot of time trying to really understand what the computer likes and doesn’t like,” added Rapson. “You can get readings out of the computer. You just can’t put information into it like in the old days.”
Aside from being constructed of carbon fiber to reduce weight, the intake manifold features individual runners inside a larger plenum that holds more air.
“We elected to use a taller runner because it allowed the engine to manage the air in the rpm band that the cam was designed for,” said Rapson. “We can’t make more power at a higher engine rpm because you can’t change the rev limiter. But if you change the volume dynamics, then you can make more power within the rpm range that it is operating.”
With the LT platform being one of the most popular of any of the new production engines released in the past decade, there’s more pressure on aftermarket companies to develop upgrades with CARB EO numbers to make them 50-state legal. That takes the pressure off speed shops that deal with the end customer and have had to turn away work that involves installing non-compliant equipment on vehicles still tagged for street use.
“Everything we do is custom-built to the customers’ specifications,” said Bland. “Obviously, dealing with the fact we’re in Southern California and the emissions here are crazy, modifying factory cars is a hard play for us. A lot of what we do is based on what the aftermarket manufacturers come up with that have EOs.”
“Everything that we’ve done and everything that we are doing going forward is designed around CARB EPA approval,” promised Rapson. “The exhaust system already has a 50-state EO, so that’s a no-brainer. The intake manifold is pending. The other things that we’re working on are all targeted around CARB approval as well.”
As more interest grows in the LT and the demand for even more power increases, the challenge will be developing advanced fuel pumps and larger fuel injectors that fit in with the factory electronics and work with boost.
“So far we haven’t exceeded the bandwidth of the car’s capability to add fuel where needed to keep the correct air-fuel ratio,” added Rapson. “When we get into doing other things to the car, whether it’s turbocharging or supercharging, some of the dynamics then change.”
Gen III Hemi
The Gen III Hemi has been used in Dodge and Ram vehicles since 2003, but it didn’t really start drawing serious attention from the aftermarket and hot rodders until the engine was freshened up for the 2009 model year. Chrysler strengthened the block, improved the cylinder heads, increased the oil capacity and added variable cam timing. The automaker also came out with larger displacement versions and supercharged models with wicked monikers like Demon, Hellcat and Redeye. In developing those trendy names and big power numbers, Mopar basically challenged the performance industry to a street fight.
One of the key ingredients in taking the late-model Hemi to 2,000 horsepower and beyond is a stout yet lightweight cylinder block. Keith Black Racing Engines in Buena Park, California, was one of the original innovators in aftermarket cylinder block development when it pioneered the aluminum replacement for the 426 Hemi (also known as the Gen II Hemi) in Top Fuel racing. CNC and billet technology have taken nitro engines to another level, but Keith Black is still casting the venerable 426 Hemi block for nostalgia and marine racing. Now under new ownership since Keith Black passed away, the company is setting its sights on developing a Gen III Hemi block.
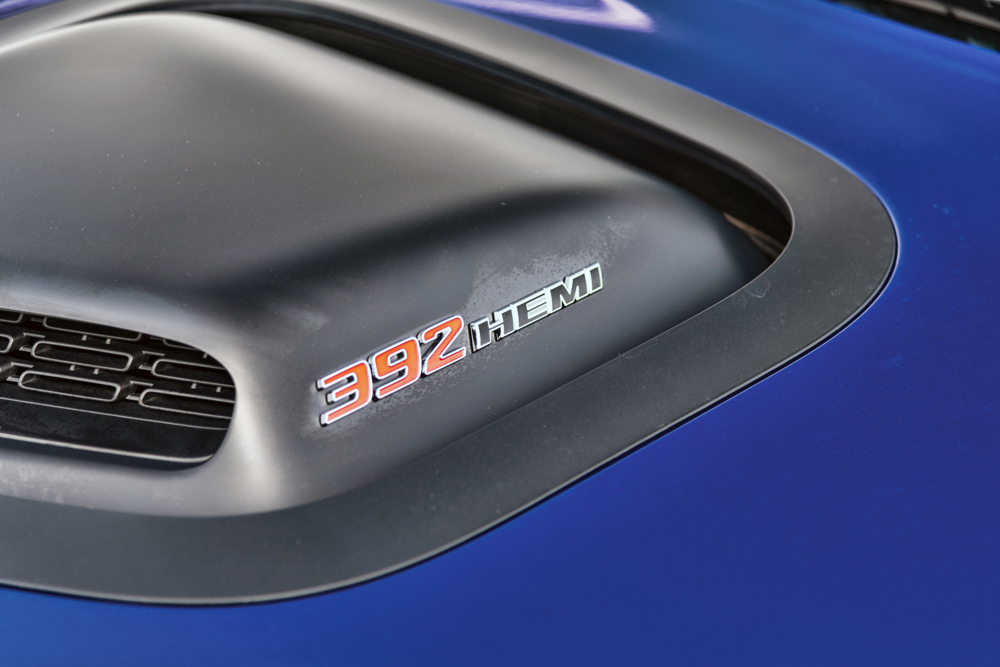
“The Gen III is in development, and it will be capable of 3,500 horsepower,” boasted Darren Beale.
The goal is not to compete with billet block manufacturers, but rather design and manufacture a cylinder block capable of operating in cold and hot weather conditions and will endure thousands of heat cycles.
“We are going to carry over the core principles of engine block design from our Gen II program,” explained Beale. “That is, a very strong and rigid bottom end with a high main-cap-to-block contact area and large clamping lines to ensure there is no cap walk. Because it’s a small block, the only way to make huge amounts of power is by adding lots of boost. Therefore, sleeve design is critical. Also, thick deck and extra head studs with deep thread engagement.”
The block will be constructed from A356 aluminum, and lubrication will be more conventional with full pressure to the lifters and journals along with plumbing options for exotic strategies.
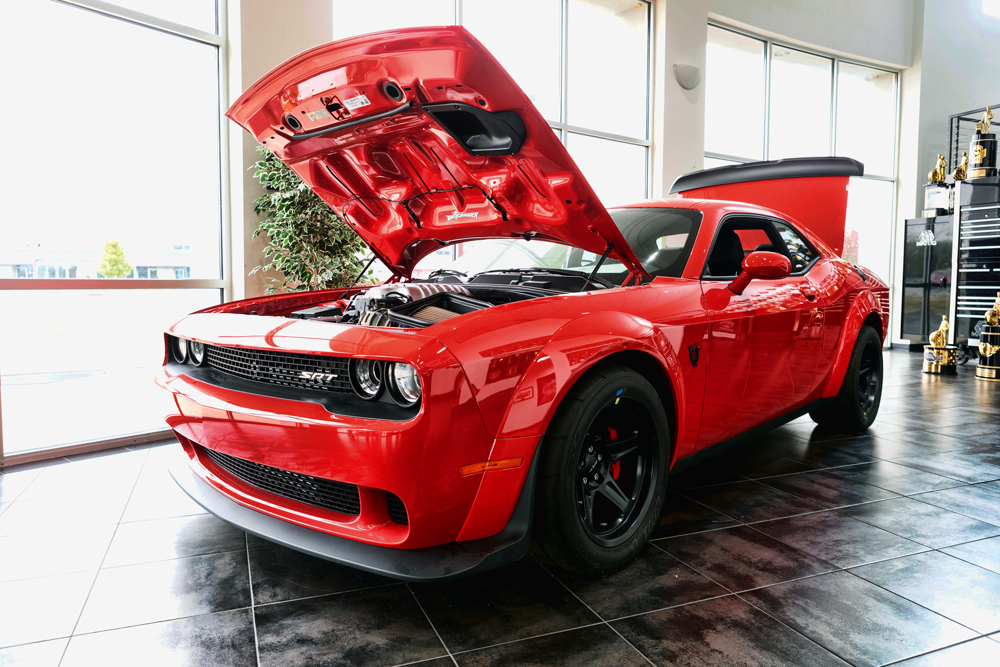
“There will also be a lot of attention on drain back, and we’ll build in features for dry-sump oiling,” added Beale.
Tooley expects his Gen III Hemi development program will follow a game plan like the one that worked for his LT engine program, “because we learned so much with the Gen V program,” he said. “Some of the cams we tested, we were shocked at how much power we made. For example, we sell Stage 1, 2, 3 and 4 cams for Gen IV truck engines. Now we have a new Stage 2 cam, and it makes more power everywhere than our Stage 1, 2 or 3, top to bottom.
“We feel like there’s more opportunity to do well in the Hemi market than what we’re currently experiencing in the Gen V market,” continued Tooley. “Companies that specialize in a specific genre are really elevating the performance.”
Godzilla & Coyote
Perhaps no engine is generating more intense emotional reaction and product interest from the industry than the Ford 7.3-liter Godzilla V8. First released as the base gas engine for the 2020 Super Duty trucks, the 445-cubic-inch pushrod engine is also available as a crate engine rated at 430 horsepower and 475 lb-ft of torque. Since the physical dimensions are not much larger than a LS, the Godzilla is seen as a legitimate challenger to GM’s dominance in the hot-rod engine-swap market.
With that in mind, the aftermarket is serious about developing product for this crate engine. It didn’t take long before Mast Motorsports got one on the dyno for baseline runs. Then the team designed a CNC program for the cylinder heads and came up with different camshaft profiles for testing.
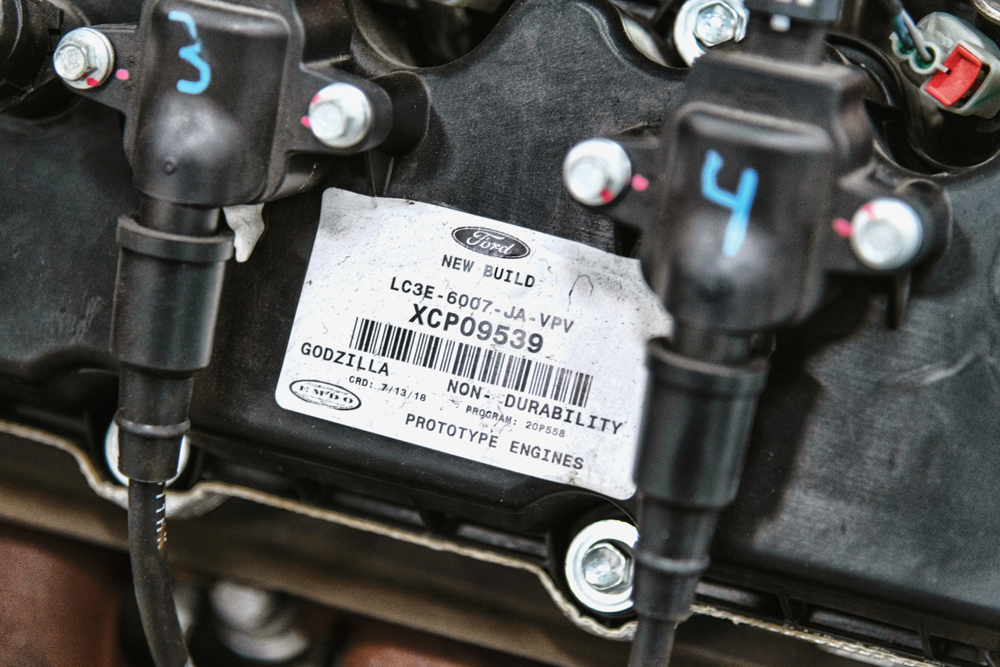
The crate motor baselined at just under 500 horsepower with peak torque at 549 lb-ft. Even with just a Stage 1 camshaft, the engine picked up 125 horsepower. With CNC-ported heads and a Stage 3 camshaft, the engine made 676 horsepower and 610 lb-ft of peak torque.
“To do a sub-700-horsepower engine that people can drop into a Mustang—you know, Ford really hasn’t had a good offering besides the Coyote,” said Youd. ”It’s a pretty big gamechanger, from a horsepower standpoint. The next step is working with Wiseco on a forged piston, and then an aftermarket connecting rod. Now we can put on a Harrop supercharger to test.”
Harrop already has tested its supercharger on a stock Godzilla and made 1,000 horsepower with E85, so there’s certainly potential with internal mods and a dedicated camshaft.
In order to accommodate the engine swappers, different oil pan options will have to be offered. Plus, different intake manifolds will be developed to suit those with carburetor or EFI preferences.
For now, the Coyote is still Ford’s go-to product for hot rodders. The 5.0-liter DOHC V8 has been around for a little more than a decade and first drew attention with the 411-horsepower 2011 Mustang GT. It’s also been available in the F-150 trucks.
Ford did produce a 5.2-liter VooDoo version for the 2016 GT350 Mustang rated at 526 horsepower, and the 5.2-liter Predator version in the Shelby GT500 is supercharged to make 760 horsepower. Ford also released the 5.2-liter Aluminator as a crate engine, but the aftermarket continues to focus on the more plentiful Coyote when developing new product.
Michael Rauscher at L&M Engines in Hatboro, Pennsylvania, has been consulting Coyote owners and dealing with tuning issues since the engine came out. He’ll build engines from scratch or short blocks on an exchange program. Much of his time is also devoted to camshaft development—a direction he took after measuring aftermarket cams and discovering they varied greatly from bank to bank. He purchased graduate-level automotive textbooks from MIT, studied all he could about overhead cam design and found software programs to design cams and understand the manufacturing process.
“Because you can design a lobe nobody can grind or you can design a lobe that shoots the rocker arm through the valve cover, right?” he said. “Next thing you know I’m making power. Poor guy needs 25 pounds of boost to make his power. I’m doing it at 18 or 15 pounds.”
Specializing in overhead cam design has brought Rauscher closer to his customer base than other cam designers might enjoy.
“I take a little bit more of a chance,” he said, noting that due to the small size of the Coyote platform, he must address boost dynamics in many of his designs. “Now all the math is thrown out the window because of the feedback dynamics between the turbo, the turbo piping and the camshaft. That determines whether this is going to make it or not, power-wise.
“The thing I’ve got to stress is feedback,” Rauscher continued. “The blowers are easy to design, cam-wise. Turbos? If somebody calls about a turbo, it puts the fear of God in me. I can design a cam that works great for the same turbo and all these combinations this guy has. And then the next guy doesn’t make any power because of all the losses in the piping system, the heat losses he introduced on the hot side, and it’s ugly.”
Rauscher admitted that the Coyote’s fate is really uncertain as the automaker moves to boosted V6 and I4 engines. “I don’t know what the future is going to be on Coyote, but it’s huge for me right now.”
What’s Next Gen?
Which begs the question: Are there going to be any new engine platforms from Detroit automakers in the next decade or two? Global government mandates are forcing the leap into EVs. Diesel pickups might last longer, but the surprising demand for the Mustang Mach-E may be a glimpse into the future of where production performance vehicles are headed.
One option is designing your own engine. The aftermarket has been busy doing that since Sonny Leonard and others developed cylinder blocks and heads with wider bore spacing to build mountain motor Pro Stock engines. Dart, Brodix, CFE and others have adapted that strategy to small block architecture.
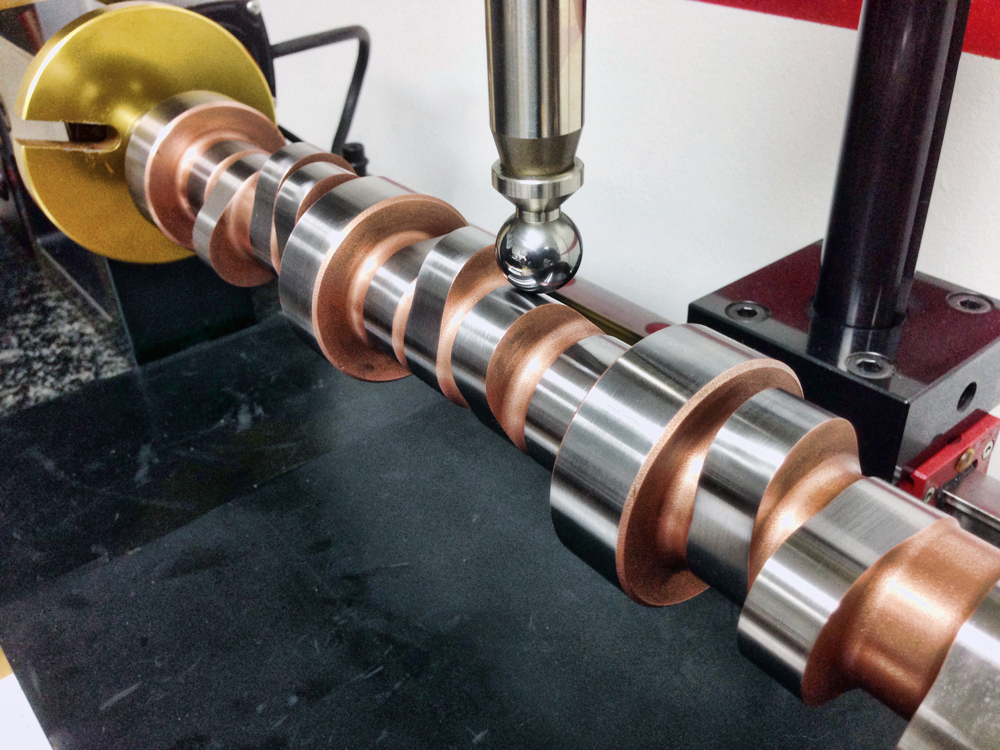
Advancements in CAD software and CNC machining allow innovators to design their own engines these days. Steve Morris developed the SMX platform that’s capable of 4,500 horsepower on the drag strip, yet it can be built for endurance applications if desired. Dan Jesel made headlines at the PRI Trade Show a couple years ago with his Equal 8 engine. Goodwin Competition also designed and built its own engine for truck pullers. There’s even a project underway at Neutron Engines to design a new V8 using Honda K48 cylinder heads.
So, the next great racing engine platform just might come from a little shop in the Midwest!
SOURCES
–
Brian Tooley Racing
briantooleyracing.com
CBM Motorsports
custombuiltmotors.com
Keith Black Racing Engines
keithblack.com
L&M Engines
lmengines.com
Lingenfelter Performance Engineering
lingenfelter.com
Mast Motorsports
mastmotorsports.com