Laying Down Rubber: Supplying Tires for the Indy 500
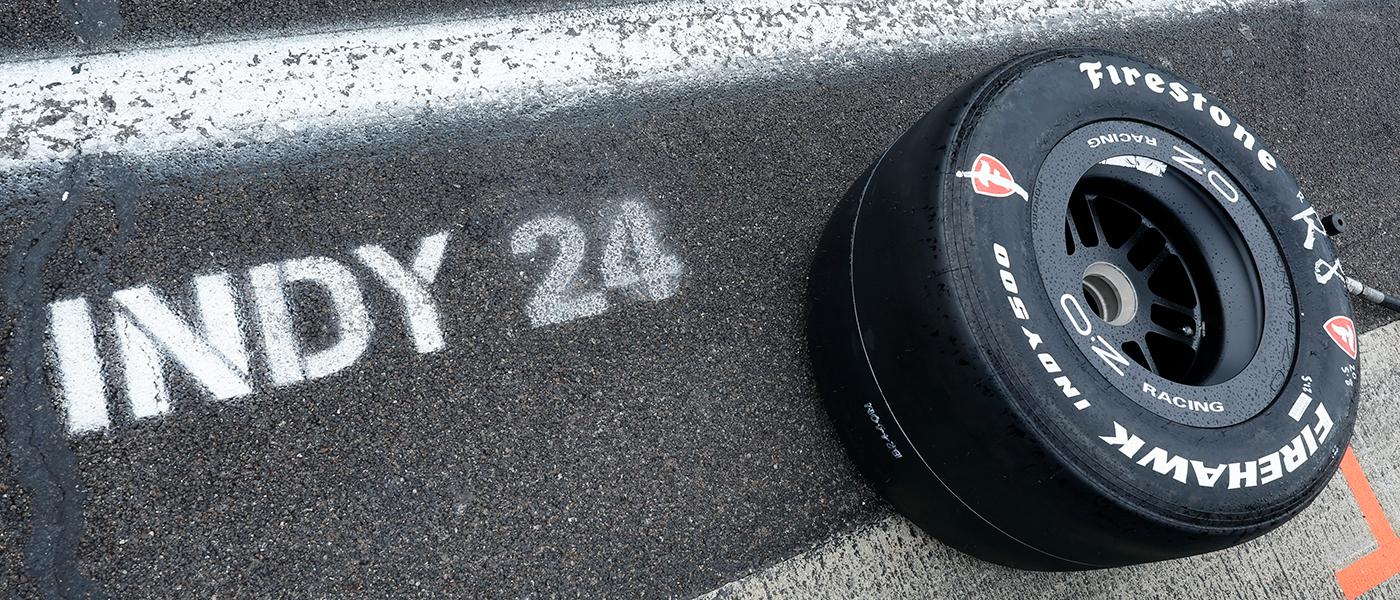
It doesn't need to be said that the Indianapolis 500 is the biggest race of the year for the NTT INDYCAR SERIES. It's the biggest field. The biggest crowd. The biggest purse. The biggest stage.
And with the most on-track time of any race, it means a little more of everything. More fuel, more engines, more manpower, and more tires. A lot more tires.
In a typical INDYCAR weekend, the field of 27 full-time cars uses somewhere between 1,100 to 1,200 Firestone Firehawks across multiple practice sessions, qualifying, and the race. But the Indianapolis 500 is not a typical INDYCAR weekend.
For the four days leading up to qualifying, the track is open for practice for six or more hours, totaling in more than 30 hours of available track time. And that doesn't include the two full days of qualifying over the weekend.
With all the extra running and the expanded grid, the 33-plus entries will use more than 5,000 tires--yes, 5,000--over the course of the month.
To accommodate the extended practice time, larger car count, and increased workload, the tire manufacturer adds four to five members to its usual 14-person service team, according to Mark Williamson, service crew manager. Throughout the day, Williamson and his staff tend to the needs of the paddock, dismounting used tires (dropped off throughout the day by teams), mounting new slicks on each team's rims, and finishing the process by balancing each tire.
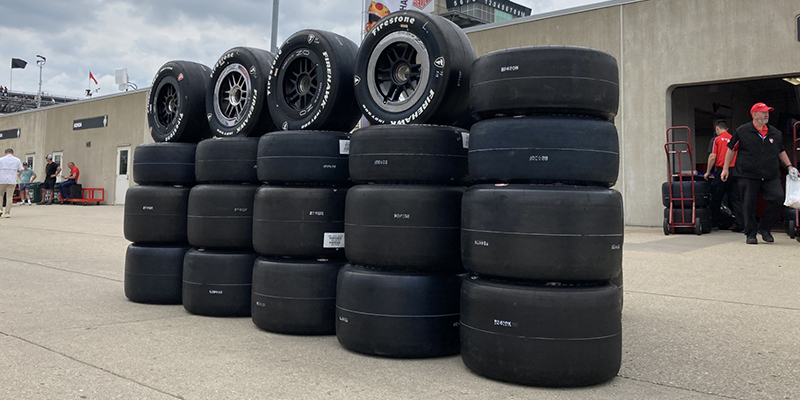
Each step in the process only takes one minute per tire. "Not exactly your local shop," Williamson said.
In addition to preparing each tire, several members of the service crew are also tasked with roaming pit lane while the track is hot, measuring tire temperatures and air pressures from used tires once they come off the car.
Despite the constant and heavy workload, each tire is meticulously tracked, marked with a serial number and barcode, and followed through each step in its life cycle, from manufacture to post-race analysis.
The week begins in anger even before the drop of the green flag on the first practice session, with work ramping up as teams arrive at the track in the days before the opening session. But preparation for the race starts months, even years in advance.
"We're learning right now for next year," Cara Krstolic, executive director of race tire engineering and production for Firestone. "We have an engineering team and at least one chemist at every point to understand what's going on with the tires, working with the drivers on feedback, with the race teams on what they want out of the tire and what they need out of the tire."
In fact, Krstolic and the Firestone engineering team began developing a new tire to better account for INDYCAR's incoming hybrid power unit in October 2022. Originally intended to be in use for the full 2024 season, the hybrid is now slated to debut at the Honda Indy 200 at Mid-Ohio Sports Car Course later this summer. Firestone still had to be ready.
"We started a year and a half beforehand to make sure we had the appropriate tire for whatever the race throws at us," Krstolic said, "whether it's a hybrid, whether it's not a hybrid."
In addition to large, wholesale changes mandated by the sanctioning body, the series' official tire supplier must also be ready for innovations coming directly from the race shops.
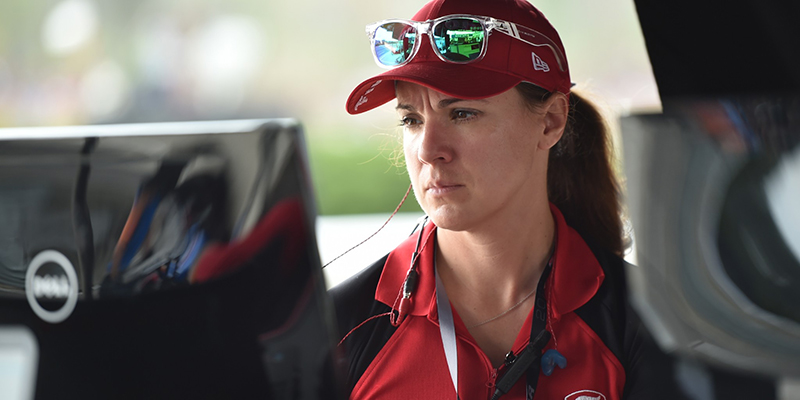
Firestone Executive Director of Race Tire Engineering and Production Cara Krstolic.
"The cars are constantly changing, even if there are zero changes to the cars itself," Krstolic said. "Engineers are finding out new ways to run their cars faster, and that adds new stress to the tires, or adds different conditions than the tires were initially designed for. We're continually learning and that drives our process."
That process includes extensive design reviews and consulting feedback from teams, including year-end debriefs with the full Firestone engineering team. In total, a design review cycle takes about a year, Krstolic said, but the changes always keep coming.
"There's no end of the design or beginning of the design," she said. "We learn as we go."
Changes to the cars and new approaches from the teams are compounded by the unique surfaces of each track. A detailed analysis of the pavement--whether it's a pristine oval like Indianapolis or the winding, weathered streets of Toronto--informs the design process. The engineering team completes a friction analysis and a laser analysis at each circuit to determine the level of grip provided by the pavement, as well as an understanding of how the tire will behave, especially as cars are getting up to speed.
And Indianapolis Motor Speedway, Krstolic said, possesses a very specific challenge.
"What makes Indianapolis unique, other than the amazing history we have here, is the very long straights followed by sharp turns. A lot of people call it an oval. It's really a rounded rectangle," she said. "That provides unique challenges because you have a long time that the tire will cool off, then you enter a turn. Mario Andretti says it's like, 'driving 60 mph down a country road and then turning into your driveway.'
"In some ways, it almost acts like a road course because you don't have a long duration turn, so it's a very unique race track," she added. "We love coming here, we love designing tires for it. It's always a great engineering challenge and it's a great way to showcase our product."