Tech Update: Which Bearing Is Best For You?
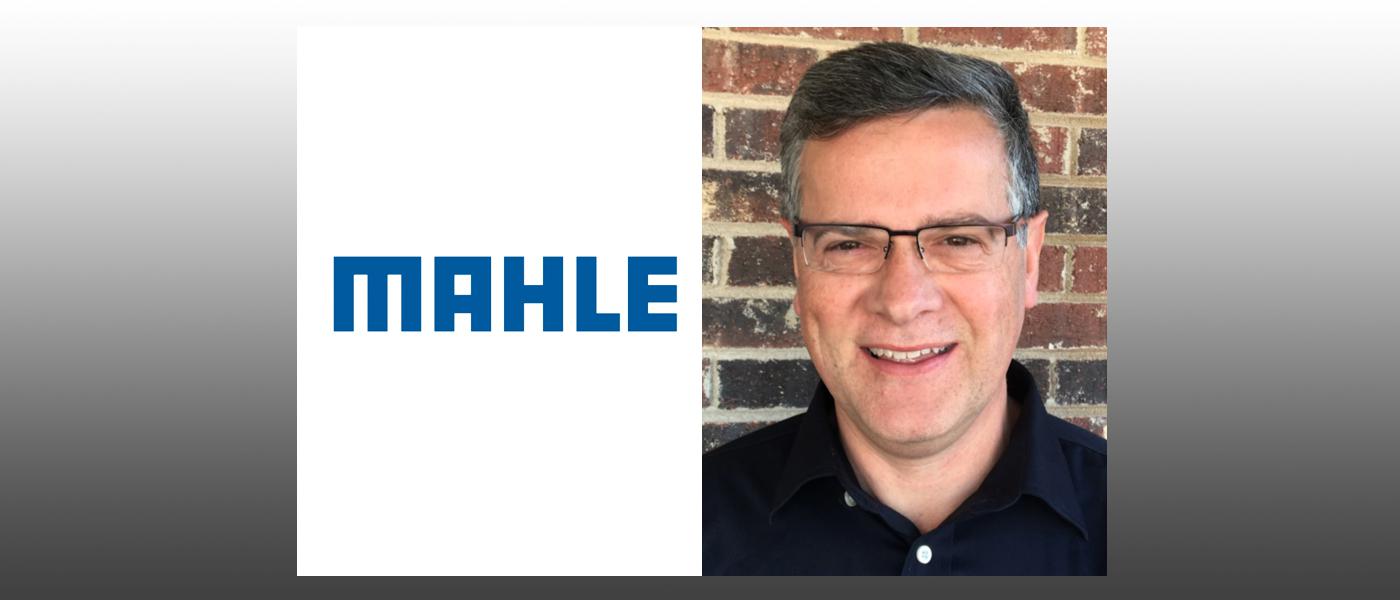
A clearer understanding of design and construction will help you determine the right part for your application.
Performance engines today produce power levels unimagined even a decade ago. Computer-aided flow design, high-lift cams, and boosts from turbochargers and nitrous oxide systems can yield horsepower ratings well into the four digits. This extreme output puts enormous strain on all engine components, but none more than the bearings.
A Holistic Approach
The first key to maximizing bearing life in a high-performance environment is to understand the world they live in. Engine bearings in performance engines must be able to survive extreme pressures, temperatures, and loads. And, tolerances on main and connecting rod bearings are among the tightest of any engine components.
At MAHLE, we’ve developed sophisticated computer simulation software that accounts for the many variables that impact bearing performance: the metallurgy of the block and components, oil flow, temperature, etc. With this tool, we can see how well the bearing will withstand the loads and temperatures, and make changes to improve performance. For example, it helped us determine that the main bearing groove, which feeds oil to the connecting rod bearings, does not need to extend for the full 360 degrees of the bearing shells. In fact, the oil system efficiency can actually be improved by limiting the groove to 180 degrees, or even less.
This software also helped us identify a problem with aluminum versus cast iron blocks that resulted in failures. It allowed us to design bearings that compensated for the different rates of thermal expansion of the aluminum block and the steel bearing backing to enable the engine to operate reliably at the power levels desired.
Bearing Materials
For performance applications, tri-metal bearings are usually the preferred choice. A typical tri-metal performance bearing consists of a steel backing, a substrate usually made of bronze (copper/lead), and the overlay, which can be made of several metals. The two basic types of overlays used in performance engine bearings are copper, tin, lead, or lead indium.
Copper, tin, lead overlay have tighter tolerances than standard bearings and more “crush.” The thin nickel layer is a barrier to keep the tin in the overlay from chemically migrating into the substrate. Copper, tin, lead bearings are the choice for most performance applications, especially when frequent rebuilds are not desired, i.e., bracket racers.
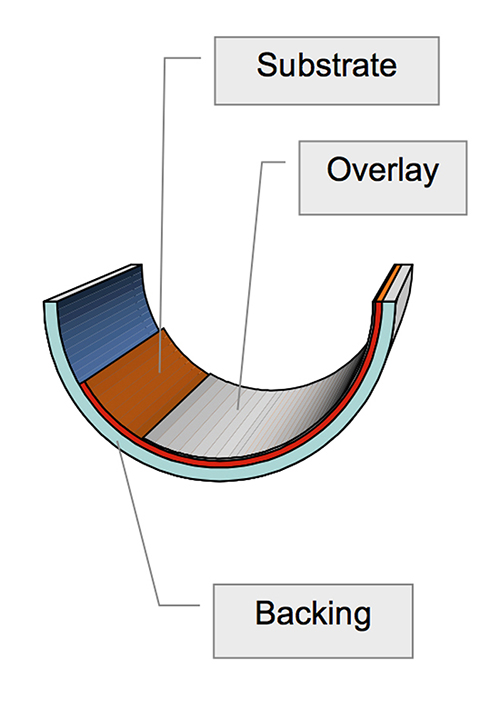
Lead-indium overlay, by contrast, does not need a nickel barrier since there is no tin to migrate. The indium allows for more conformability, bedability, and higher fatigue resistance. This type of bearing is used in higher-end performance applications, but it does not yield as long a service life as copper, tin, lead overlay bearings. But for NHRA and other competition engines where this is not important, lead-indium bearings are the choice for extremely high-pressure resistance.
Bearing Construction
There are two different types of construction used in performance bearings: cast and sintered. A cast bearing is formed with a steel strip with folded edges. The copper/lead alloy for the substrate is heated to 2,000 degrees Fahrenheit, melted, and then poured into the trough formed by the bent steel. The strip is then quenched in oil. The heating enables the copper to adhere extremely well to the steel backing. As it cools from being superheated, the copper forms vertical columns. This gives cast bearings a substrate with a structural load-carrying capacity of 12,000 PSI.
Sintered bearings also use a strip of steel or aluminum, but instead of high heat, pressure is used to bond the substrate to the backing. A powdered substrate material is dumped on the strip, which then enters a sintering chamber where a series of rollers squeeze the strip and powder together. Only enough heat is applied to allow the particles to stick together. The substrate is not melted, nor is the molecular structure altered. The copper and lead have a random pattern with large globules of lead; there are no columns to give support to the substrate. This is because the copper was not superheated and then quenched. Sintered performance bearings typically have a substrate load-carrying rate of 8,700–10,000 PSI.
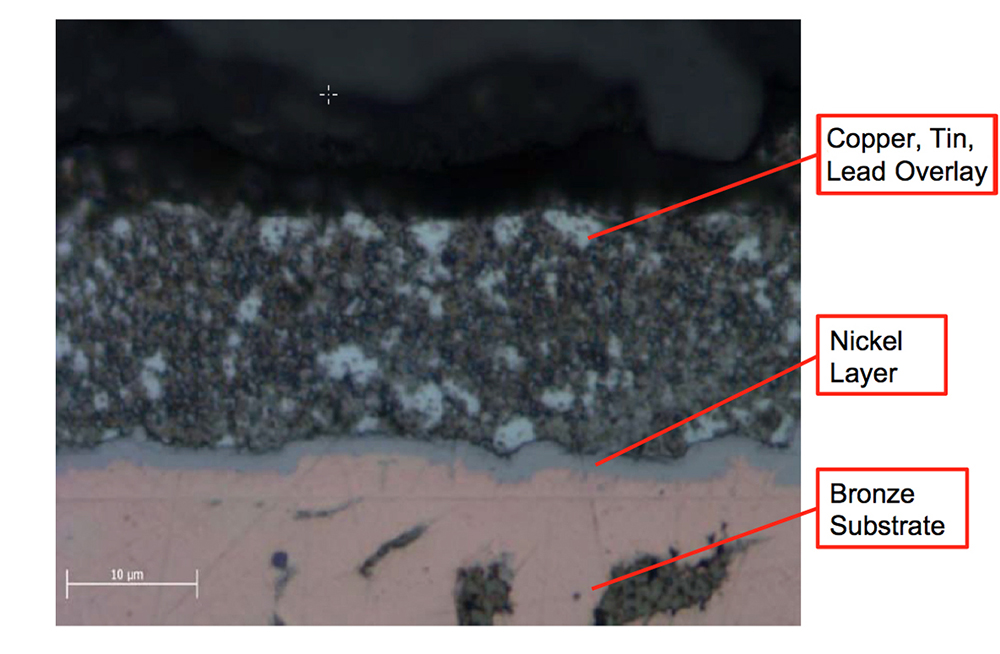
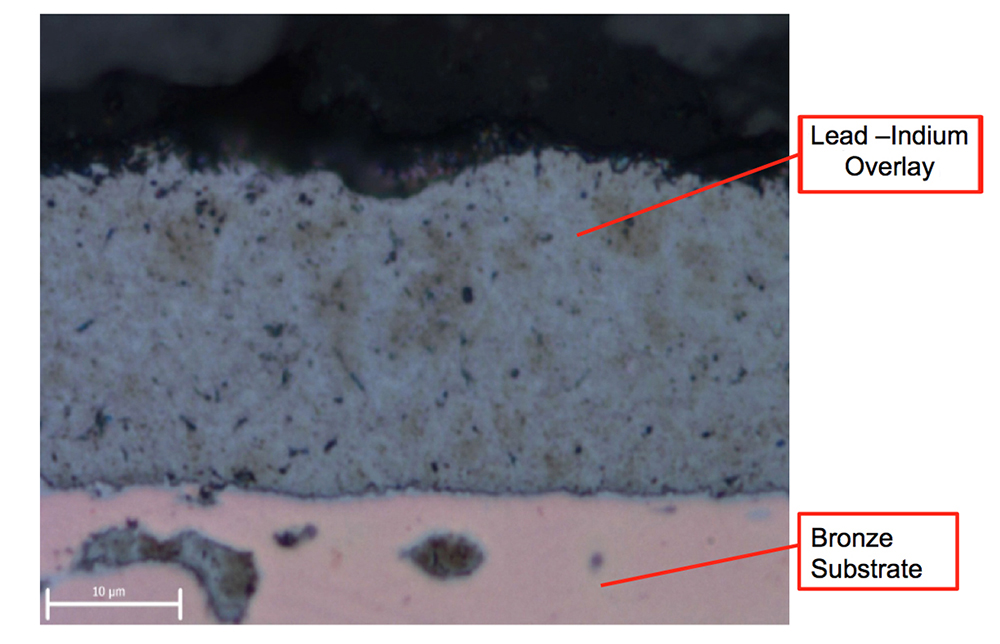
The large pockets of lead give the substrate less strength because it compacts under load. There also can be random fractures within the substrate that are not visible and can result in a loss of adhesion, which in turn may allow chunks of bearing material to separate in performance engines, leaving voids and debris going through the bearing.
Overlay Failure
Bearing overlay failure occurs when bearings fatigue and the substrate starts to move and fractures the overlay. This typically can happen more frequently with sintered bearings. That is why the additional substrate strength of cast bearings is important for performance engines.
Bearings used in high-performance racing engines are subject to greater forces than those in production engines. By understanding the extreme conditions bearings experience, and the different types of bearings available, engine builders can make informed decisions as to which may be best for their particular application.
Dan Begle is the Performance Sales Engineer at MAHLE Aftermarket specializing in performance engine parts. He has over four decades of experience in motorsports, including 27 years in the engine shops of several NASCAR teams.