DATA PROJECTION
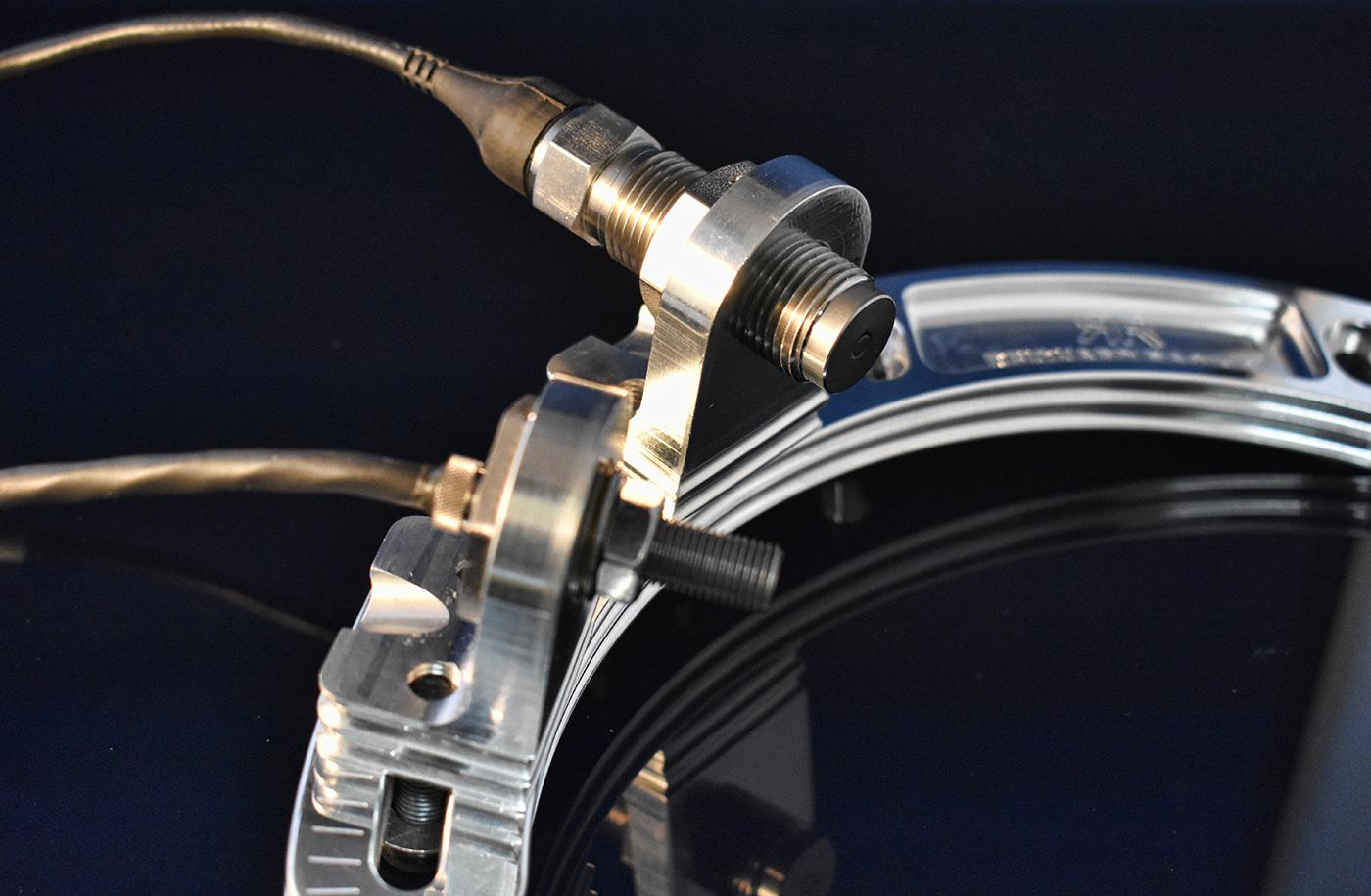
Gain valuable insight into when and to what extent sensors should be upgraded or replaced on a race car.
In the early days of motorsports, it was the duty of master mechanics and crew chiefs to get a “feel” for how the engine was running and tune it to the best of their abilities. These pioneers of the sport often relied on their own senses of sight, touch, and sound to get the most horsepower out of the engines they worked on in order to propel both car and driver into the winner’s circle.
In addition to their tuning skills, these technicians would often conduct extensive tear-downs in an attempt to “read” what was going on inside their engines. In this manner, they could verify if a tune-up was spot on, or see if there was room for improvement as evidenced by breakage, wear, or fuel/oil deposits on any of the various components.
Of course, the industry has changed considerably since then, and high-tech advancements are now made on a continuing basis. Today, race cars are controlled by sophisticated electronics and computers using highly sensitive sensors to provide feedback to help precisely control and measure the air/fuel mixture, suspension position, and timing, among other functions.
Indeed, proper usage, diagnosis, and replacement (when required) of these sensors can mean the difference between coming up just a few inches short and gaining that critical 0.001 of a second needed to qualify for the next round. Conversely, how do you know when your car’s current sensors aren’t getting the job done? Fortunately, our expert sources have the answers.
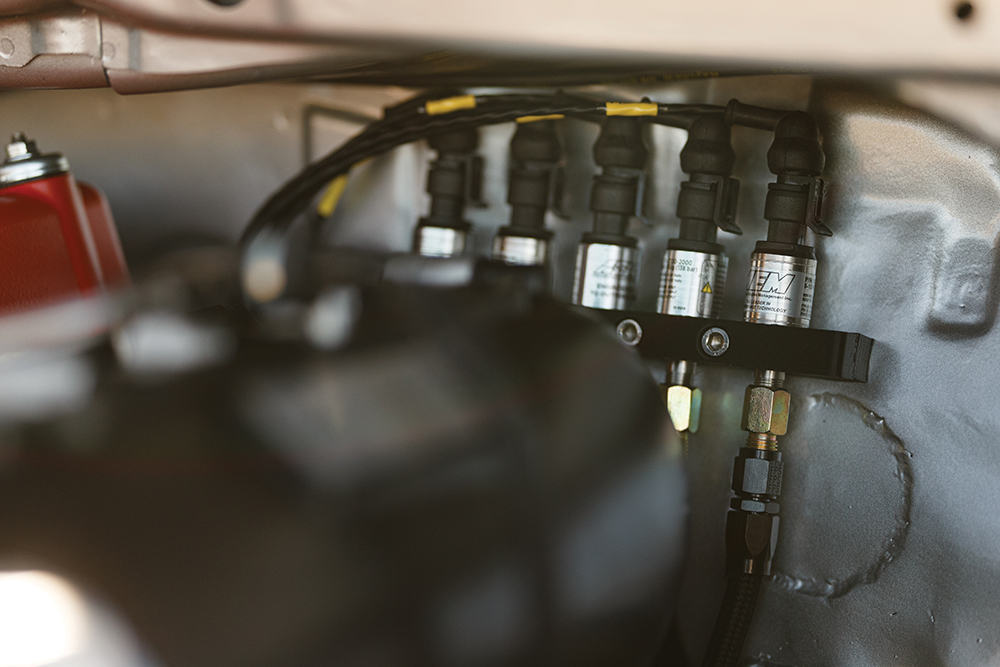
WHEN TO UPGRADE
Racers who already utilize sensors may not realize the benefits to upgrading these small yet important components, or how additional or better sensors can help collect more or better data.
“A customer should consider upgrading their sensors when the use of forced induction is introduced, when improvement in overall engine performance is desired, and/or failures are prevalent,” said Jeff McCants of Smith Systems, Brevard, North Carolina. “We certainly recommend at least upgrading from the plastic OEM sensors to stainless steel versions of most sensors when reliability and performance are essential.”
Transitioning from one material to another can deliver more precise readings, too, as Lawson Mollica of AEM Performance Electronics in Hawthorne, California, explained: “Upgrading from our brass type to stainless sensors are recommended for accuracy when you are using them for tuning and data analysis. We like to say it’s the equivalent of the difference between using a ruler and using a caliper to measure something. Both will measure, but one will measure with a higher degree of accuracy. While our brass pressure sensors are great for looking at something like boost/vacuum on a gauge, you want a stainless MAP sensor when you are using that data for engine tuning.”
According to Skylar Drake of Holley Performance Products in Bowling Green, Kentucky, whose brand lineup includes Racepak Data Systems, “It really comes down to when are they needing more data…. Making the jump from 20 Hz to 100 Hz increases the amount of information recorded significantly (especially if monitoring multiple channels). If moving to a more powerful combination with power adders, it may be a good idea to add a few additional sensors to make sure everything is playing well with one another.”
However, knowing when to upgrade a sensor versus straightforward replacement requires a bit of savvy, according to Todd Paton of Performance Data Systems in Rancho Santa Margarita, California. “In my experience, customers will upgrade sensors once they understand the basic information they are receiving from the sensors and want to look deeper into the information they are receiving,” he said. “A common application of this has been when a customer uses a single air/fuel ratio sensor on the engine to determine if the overall tune-up is rich or lean. Once they start tuning each individual cylinder, they will upgrade from a single air/fuel sensor to a set of four, six, or eight, depending on the type of engine they are tuning.
“We also have customers that start out monitoring the suspension travel of the right rear wheel of their suspended drag race vehicle,” Paton added, “and then call back shortly thereafter to order additional sensors for the other three wheels to help paint a more complete picture of what their car is doing.”
“If the racer is not satisfied with the data observed, or does not see a significant event well-reported on screen, then perhaps newer or faster responding sensors are in order,” offered Dennis Lawler of Exhaust Gas Technologies, Chino, California. “In temperature measurements, the exhaust gas temperatures are paramount to crew chiefs. The closer the cylinder temperatures are, the happier the motor.
“[For example], NASCAR likes to see +/- 50 degrees between cylinders,” Lawler continued. “In drag racing, the fastest exposed tip thermocouple is golden and offers a response time of better than 0.03 seconds. Many teams in the gasoline fuel classes have re-instrumented and use air/fuel ratio measurements and fuel mapping to achieve greater performance.”
POPULAR ENHANCEMENTS
Sensor upgrades run the gamut, but a handful stand out among the crowd, according to our sources.
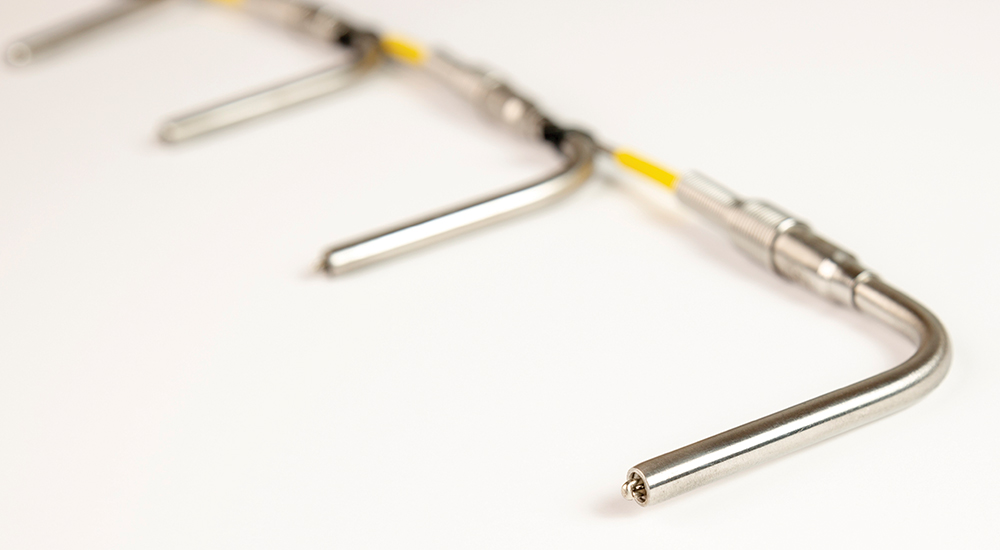
“For tuning, our wideband sensors are a must-have,” stated Mollica, who cited AEM’s X-Series widebands for their especially rapid response time, which “allows tuners to ‘see’ changes that other sensor controllers may miss to create the most accurate tune. It has analog, serial, and CAN bus outputs, too, so it can be adapted for use on many different types of engine management systems, from open source to full standalone units. It also has the ability to use the Bosch 4.9 sensor’s factory resistor calibration, but also free-air calibrate the sensor if you want to. This is a great feature when you have an older sensor and are at the track because you can free-air calibrate the sensor to ensure accurate readings until you can replace it with a new one.”
Most motorcycles and cars come from the factory with narrow-band O2 sensors, according to David Carter of Daytona Sensors, DeBary, Florida, so his upgrade of choice is a wideband O2 sensor.
Paton noted that many of his customers want better monitoring of their suspensions, so they frequently add vehicle ride height sensors. “In cars without a suspension, like Funny Cars and Top Fuel dragsters, we use load cells to monitor pressure on the wheelie bar as well as the front spindles on the chassis, in addition to ride height sensors,” he explained. “There is a fairly recent trend of monitoring tire temperature and track temperature using our infrared temperature sensors as well. We also have many customers looking at monitoring what the driver is doing by adding throttle position, brake pressure, and even heart-rate monitors to their data acquisition systems.”
For temperature measurements, Lawler told us the fastest responses come via “sensors with exposed tips and small gauge elements producing outstanding graphs. They will report a single misfire at 8,000 rpm, and will also tell the crew if the misfire was caused by a loss of ignition or loss of fuel just by analyzing the analog data graph.
“Another important upgrade is intake air temperature,” he added. “By mounting a small 0.092-inch diameter T/C at the top of the carburetor, or air intake on injected motors, or mounted just below the blower, [you’ll get] reliable readings that point the way in fuel mapping. These readings will vary through the day into the evening. The cooler the readings, the more oxygen per cubic foot are revitalized.”
According to McCants, one common—and highly effective—upgrade involves the addition of a crank trigger sensor in coordination with a traditional ferrous reluctor wheel or flying magnet wheel. “This is a great addition when accurate and stable timing is desired. This upgrade can increase performance greatly.”
Other sensors to consider upgrading, according to McCants, are those with open tipped housings, where the coil and magnet are exposed, “due to fluid and or dirt intrusion. Because a vehicle or bike can be subject to many harsh conditions during competition or street use, upgrading to a closed (‘blind’) tipped sensor is a great way to prevent internal damage due to fluid/dirt intrusion. Just a simple change from an open tipped sensor to a blind tipped sensor can make a world of difference when it comes to winning and losing.
“In the case of a turbocharged induction system, users may also find it useful to upgrade their turbocharger by introducing a speed sensor to their unit,” McCants added. “These sensors used in conjunction with an ECM will prevent rpm (over spin), thereby preventing damage to the turbo and/or the engine.”
MAINTENANCE AND REPLACEMENT
So, how to tell when it’s time to replace those helpful measuring tools? What are the early warning signs that precede replacement? And by extension, what sensors should retailers have on hand for immediate sale?
“Most sensors will work until they don’t, so it’s a good idea to carry spares of the important ones you rely on at the track in case they fail,” advised Mollica. “For instance, our stainless sensors have a full 360-degree welded wetted area that makes them impervious to automotive fluids, and their failure rate is a fraction of one-tenth of 1%, but if it happens you will be glad you made the investment in having the spare on the trailer. That said, before you toss the sensor, it’s a good idea to check the connector pins and wiring to make sure they weren’t cooked off or came loose before writing the sensor off.”
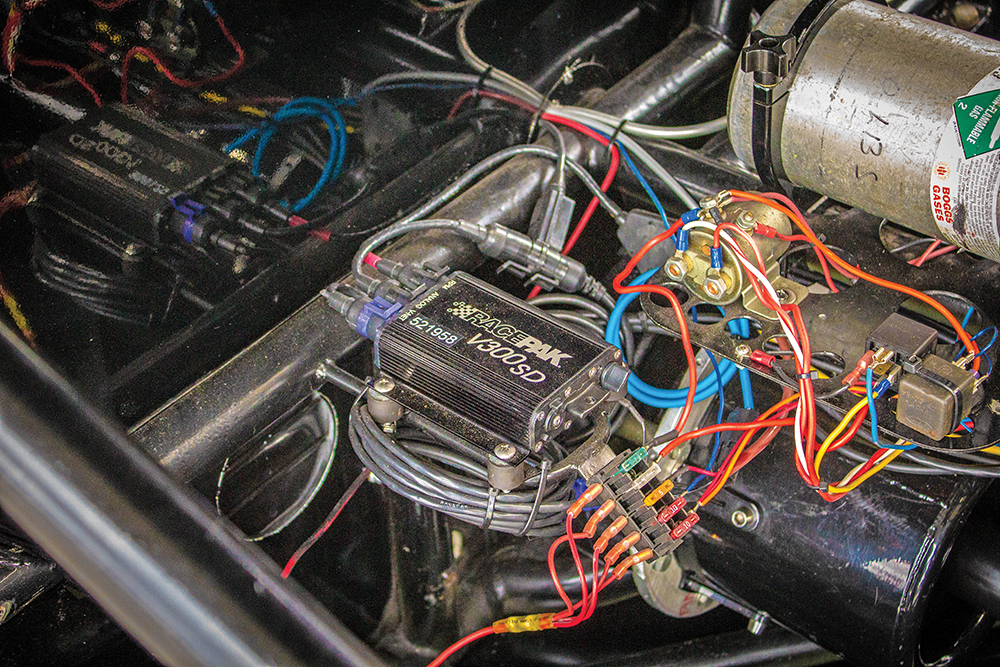
Pointing to AEM’s Infinity ECU and four-channel wideband UEGO controller, Mollica noted the ability to warn users if there are problems with a sensor. “The Infinity has this capability built into the software and you can program it to alert you,” he said, “and the four-channel wideband controller has status LEDs to alert you to a fault condition so you can check the connection to determine if the issue is there or with a sensor that has reached the end of its life.”
Big-picture, McCants told us that key indicators are the system for which sensors are being used and what exactly is being measured: “The broad answer is that a bad sensor will always produce odd readings, [thereby] failing to alert the user of an impending problem and with poor performance soon to follow. Oftentimes your ECU program interface will show undesirable curves, lower or higher than acceptable numbers. In the case of a bad or improperly installed variable reluctance sensor, the sine wave signal will be very weak or nonexistent. The same principle applies when dealing with a bad or improperly installed Hall effect sensor. The square wave will be weak or nonexistent.
“Just to touch on improper install a bit more,” he added, “oftentimes a sensor’s alignment to the target plays a very key role in its performance. Improper air gap can also lead to performance problems.”
Erratic readings, Drake said, such as noise (interference) on the sensor itself can absolutely affect data logging, so the team at Holley recommends moving to remote mount sensor blocks to avoid engine vibration and various harmonics. “There are a large amount of minor vibrations happening in your engine bay, and subjecting your sensor to them will cause false readings and lead to a premature failure. Routing sensor wires away from high-powered ignition components is a must, as plug wires and coils can emit electronic interference that can create skewed data on that particular sensor.
“Don’t forget about heat and its effect on components,” he added, because “heat shielding and wire loom can make all the difference. You are relying on them to tell you what’s happening inside your race vehicle, so treat and mount them like the precision tools they are.”
Carter also advised keeping an eye out for odd readings. “For instance, not responding as quickly as it used to, or not being able to calibrate to free air, or not responding at all to engine change,” he said. “A few signs that the sensor is ready to be replaced would be as follows: Sluggish response from the sensor with engine rpm change, or the sensor is not able to go all the way up to free air (19.5 AFR). We have seen the sensor not even move at all, basically saying the sensor is clogged. You can also test to see if the sensor is heating up properly. About 30 seconds after power-up the sensor should start to feel warm to the touch. After about one to two minutes the sensor should be hot, almost hot enough to not be able to hold in your hand.”
“Yes, in many cases they will get ‘odd readings,’” agreed Paton, “but it depends on the type of sensor, and the failure mode. In the case of thermocouples, we see either erratic ‘jumps’ in the temperature readings if there is damage to the insulating material or the wire leads going to the hot end of the probe, or the reading will be ‘flat’ or steady value if we are getting no output from it whatsoever.
Other sensors fail in similar ways, he explained, noting that shock travel sensors can provide erratic readings if there is damage or debris in the sensing mechanism. “Or [they] may provide no output at all, resulting in a ‘flat’ reading at a certain value,” Paton continued. “Air/fuel sensors may become slower to react or may give a negative value, which is used to determine the source of the failure. RPM sensors usually just return a reading of ‘0’ if they require replacement, while most of our pressure sensors will return a negative value, such as a reading of -15 psi on a sensor that has a range of 0–60 psi.
While Performance Data Systems’ core competency is assisting customers with troubleshooting based on the readings from their data, Paton told us that racers often misinterpret that data as a failure of the sensor, rather than a problem with the component or system itself.
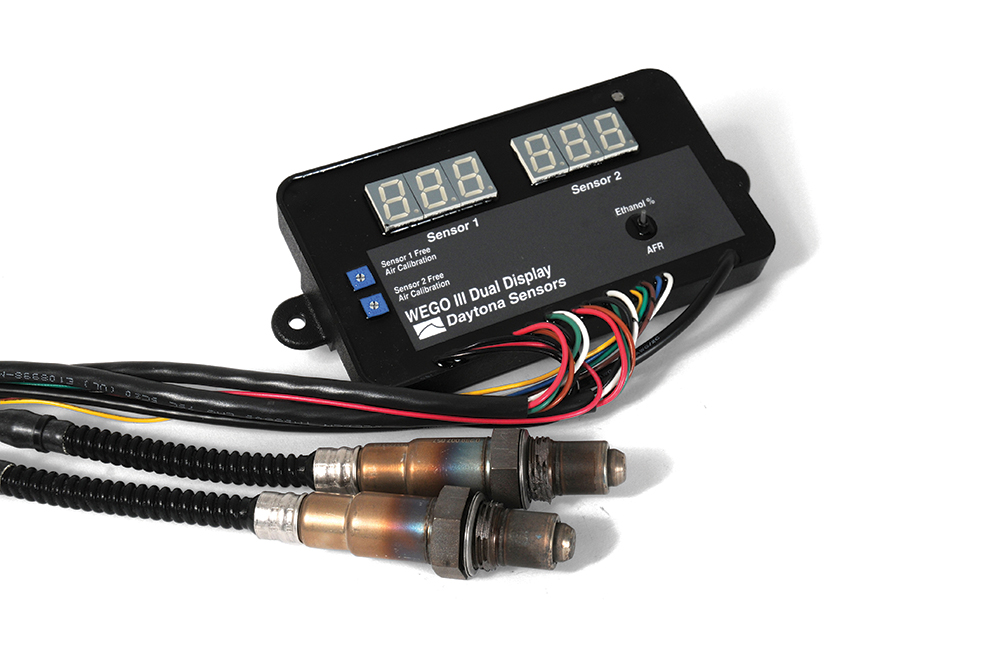
“One of my biggest observations when I started working in the field of data acquisition was how customers install a data system to see if there are any problems on their vehicles, and the minute they spot something, they assume the reading is incorrect,” he said. “Basically, they install the system to find a problem, and once a problem appears, they blame the data system.”
Referencing temperature circuits, Lawler noted a common problem referred to as “multiple or secondary junctions.” A thermocouple, he said, “relies on the single junction at the tip of the sensor only to report true data. Another short in the cable, even a ‘high-resistant short,’ will cause the readings to wander downscale. This problem will show in lead wire twists, pinches, burns, or mild shorts caused by the cable [being] crushed under a clamping device, or pinched under another car component.”
Another question frequently asked of our sources was whether racers should replace certain sensors after replacing specific components. The answer, we discovered, depends on both situation and application.
“Most of the time we’ve encountered individuals, teams, companies, etc. who’ve equipped their cars or bikes with the top-of-the-line, biggest, best, and [most] reliable performance equipment and neglect to upgrade their sensors and cabling,” McCants said. “Typically, when performance upgrades are made, we like to recommend upgrading your sensors as well with sensors that use superior components. Ultimately, this can prevent damage and untimely failures when it counts the most…preventing losses on the track and in the wallet.”
Drake added that replacement may just be the optimal approach in certain cases, such as when sensor wiring melts or gets pinched: “Oxygen sensors can wear over time and prematurely fail when exposed to extreme heat. Whenever possible, remove mount pressure transducers and other sensors to prolong their lifespan.”
Paton clarified that replacing sensors doesn’t necessarily go hand-in-glove with replacing components—that is, “unless it is either financially beneficial, or simply easier to access during the replacement of a particular component.” One example he cited was exhaust sensors, as they are a fairly common replacement when racers swap out the exhaust manifold. “Many professional drag racing teams have a set of temperature probes installed in each of their sets of exhaust headers to help facilitate the quick service between rounds. Often, our customers will replace their driveshaft rpm sensors when they service the rearend in their cars, as the sensors can be hard to access once the center section is reinstalled. Otherwise, I recommend waiting until a slight variation from typical readings is observed.
“The only exception to this is usually when a customer is changing to a new car from another,” Paton continued. “It may seem like a good cost-saving idea to keep the same sensors from one vehicle to the next, but unless great care is taken, the sensors and related cables either get damaged or installed incorrectly on the new vehicle, while the old vehicle gets sold without any of the sensors that, in most cases, helped make it a competitive vehicle.”
Carter pointed to Daytona Sensors’ WEGO systems, for which it carries a line of replacement parts and service options. These units, he said, have a built-in calibration function, and “if the sensor is not able to complete the calibration, then it is either faulty or worn out to the point it cannot be calibrated anymore. This can be caused by several [factors]: dirty gas, race fuels—pretty much any fuel with lead will cause the sensors to not calibrate within just a few hours of use. If the sensor is used on regular pump gas it is possible to get up to 10 years of use out of it. Although, we’re more likely to see anywhere from three to six years on average.
“Leaded fuels are the worst for them,” he noted, “and can take them out in as little as a few hours. We recommend if you are going to use them in a leaded race fuel environment, to just put them in to tune the engine then take them out.”
A WORD ON UPKEEP
Proper care and maintenance of sensors should never be overlooked, as Lidio Patrizio of AvioRace, a sensor and electronic products supplier based in Vignola, Italy, reminded us. “Each sensor has a particular maintenance procedure according to the specific application, what normally requires simply a general check—visual inspection or data acquisition—or directly at the end of each race track session. Obviously, there are measures to prevent malfunctions,” he said. “Let’s consider a linear potentiometer as an example; it’s necessary to clean the stem to prevent dirt residue from affecting the resistive internal tracks’ operation. Another example is the infrared temperature sensor, used for tire temperatures. Here too, cleaning is fundamental to keep the measurement spot efficient.”
He went on to explain that a strategic sensor requires periodic checks and even greater care than an optional sensor. Customers tend to replace a sensor more often if it hinders vehicle performance and functionality, he said, unlike optional sensors, which are more often repaired or substituted upon failure.
“For strategic sensors, a scheduled replacement is based on a ‘usage time’ or ‘mileage,’ although usually defined on statistical data is preferred,” Patrizio said. “Accuracy or reliability upgrades are suggested when customers want to improve the performance of the data acquisition and/or the reliability of the products. For example, to measure the ride height, it is possible to use ultrasonic sensors or laser sensors. These are different technologies for the same purpose; the first ones are less accurate but much cheaper. Accuracy expectation and budget availability are key factors to choose the right product.”
SOURCES
–